Совершенствование интеллектуальных методов управления процессами обогащения на основе визиометрического анализа сортности руды
Автор: Морозов В.В., Шек В.М., Морозов Ю.П., Дэлгэрбат Лодой
Журнал: Горные науки и технологии @gornye-nauki-tekhnologii
Рубрика: Обогащение и переработка минерального и техногенного сырья
Статья в выпуске: 2, 2016 года.
Бесплатный доступ
Для технологического процесса флотации эффективно применение открытых контуров управления, которые используют в качестве входных параметров качество руды. Для определения качества руды проводится оперативный анализ ее вещественного и минерального состава, а также структуры. Основой оперативного анализа являются измерения в рентгеновской и видимой области спектра. Для повышения точности измерения минерального состава руды разработаны новые методики и устройства. При анализе руды на конвейере испытаны специальные системы освещения, использующие чередующиеся фокусированный и плоский световые потоки. Такие системы обеспечивают высокую точность измерений свойств руды на конвейере. Разработана специальная планшетная установка для визиометрического анализа мелкодробленой руды, встраиваемая в существующую систему отбора и анализа проб. Применение планшетной установки позволяет достичь высокой точности минералогического состава руды. Современные системы визиометрического анализа руды создают основу для эффективного автоматизированного управления процессами обогащения, построенного на принципе опережающего контроля сортности руды. Системы, реализованные на обогатительной фабрике «Эрдэнэт» (Монголия), способствовали увеличению извлечения меди и молибдена.
Обогащение руд, измельчение, флотация, автоматическое управление, алгоритм, оптимизация, определение сортности руды, визиомерический и рентгено-флюоресцентный анализ
Короткий адрес: https://sciup.org/140215866
IDR: 140215866
Текст научной статьи Совершенствование интеллектуальных методов управления процессами обогащения на основе визиометрического анализа сортности руды
Новым решением задачи повышения эффективности управления обогатительными процессами на основе радиометрической информации о сортности руды является анализ руды или продуктов обогащения в рентгеновской и видимой части спектра [1, 2]. Важным преимуществом таких способов является возможность оперативного измерения параметров состава руды и продуктов обогащения, в т.ч. массовых долей отдельных минералов.
Ранее российскими и исследователями была возможность оценки перерабатываемой руды зарубежными установлена сортности на основе
результатов измерений вещественного состава исходной руды и продуктов ее флотационного обогащения с использованием рентгенофлюоресцентных анализаторов [3, 4].
Однако адекватная оценка сортности руды возможна только при оперативном измерении параметров минерального состава, таких как степень окисленности руды и соотношение основных минеральных форм [5, 6].
Оперативный анализ сортности руды может быть реализован как на основе непрерывного измерения минерального состава непосредственно в технологическом потоке, так и в результате анализа специально отобранных от этого потока проб руды.
МЕТОДИКА ВИЗИОМЕТРИЧЕСКОГО АНАЛИЗА СОРТНОСТИ РУДЫ
Достоверное раздельное определение минералов в руде возможно с использованием современных форматов распознавания цветного изображения. Для первичной обработки цветового изображения наиболее подходящим является формат RGB, комбинирующий любой цвет в виде комбинации красного, зеленого и синего цветов.
Другие параметры, наиболее важными из которых являются спектральные характеристики, насыщенность и яркость (HSV), определяются на основе этих трех базовых параметров [7].
Первоначально в базу данных созданной системы вносятся видеоизображения всех основных минералов месторождения. На рис. 1 представлены изображения основных рудных грандиорит) и акцессорных (кварц, серицит) породообразующих минералов.
Путем программной обработки создаются компьютерные образы (эталоны) основных минералов. Спектральные характеристики минералов в видимом диапазоне волнового излучения являются источником информации (базой данных) при проведении минералов меди, а также первичных (грансиенит и визиометрического анализа минерального состава руды (рис. 2).
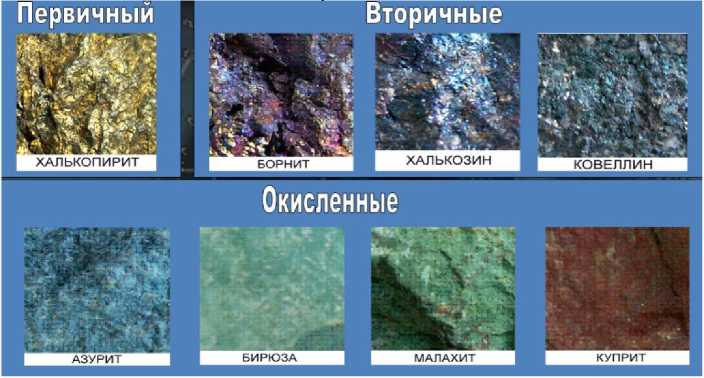
Основные породные минералы
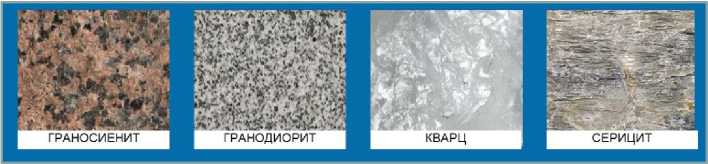
Рис. 1. Фотографии рудных и породообразующих минералов медно-молибденовых руд
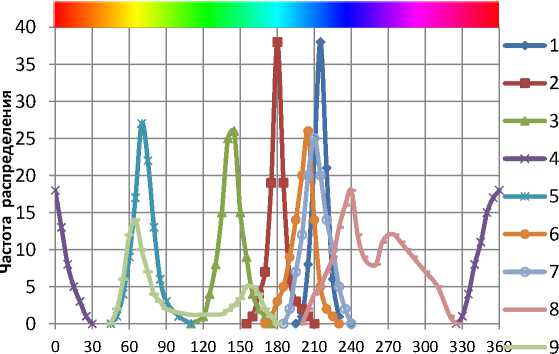
Цветовой тон, град
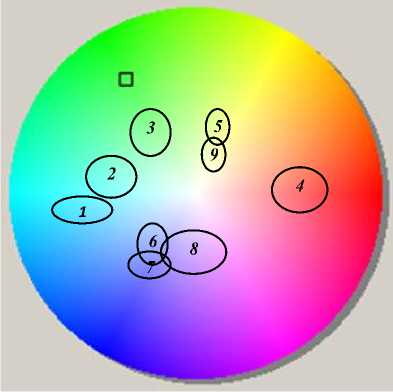
б
Рис. 2. Цветовые характеристики минералов в формате HSV: 1 – азурит; 2 – бирюза; 3 – малахит; 4 – куприт; 5 – халькопирит; 6 – халькозин; 7 – борнит; 8 – ковеллин; 9 – пирит
а
Как видно из рис. 2, б , спектральные характеристики минералов становятся более разрешимыми при использовании двухпараметрической системы распознавания: цвет – насыщенность в формате HSV. При использовании возможностей формата HSV в полном объеме вероятность определения минералов существенно возрастает и достигает 0,95 даже для таких сложных систем, как халькопирит – пирит или халькозин – ковеллин, борнит.
В программе используются простые интервальные ограничения энергий RGB единичного объекта снимка (пиксела). Формируются 3D-области интервалов энергий RGB исследуемых минералов цвета и общей энергии элемента изображения по двумерным вероятностным областям (ареалам) присутствия различных минеральных продуктов в системе HSL. Распознавание происходит по трехмерным вероятностным областям пар цветов единичных пикселов минеральных продуктов в системе HSL с использованием методов нейронных сетей с обучением системы.
На рис. 3 представлены исходное изображение сростка халькопирита с борнитом и ковеллином ( а ) и результаты распознавания ( б ).
Эффективность распознавания велика даже для спектрально близких минералов, таких как ковеллин и борнит. Необходимо отметить, что размер сростка на изображении составляет 2 мм.

Рис. 3, а . Изображение сростка сульфидных медных минералов в медно-молибденовой руде и результаты распознавания: 1 – халькопирит; 2 – борнит; 3 – ковеллин
«ИЙ КАДР
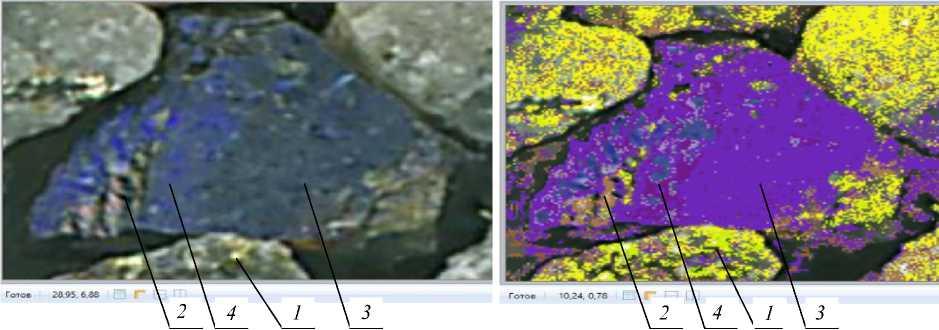
2 4
2 4 13
Рис. 3, б . Изображение сростка медных минералов в медно-молибденовой руде и результаты распознавания: 1 – халькопирит; 2 – борнит; 3 – ковеллин; 4 – азурит
На основе спектрального минералогического анализа производится определение массовой доли окисленных минералов, первичных и вторичных сульфидов меди, пирита, кварца, серицита, слюды и других минералов, присутствие и соотношение которых характеризует сортность руды.
Наиболее эффективен такой подход при оценке степени окисленности руды, рассчитываемой как отношение интегральной интенсивности спектральных характеристик окисленных минералов к общей интенсивности спектральных характеристик всех медных минералов. Степень окисленности руды может определяться как соотношение массовой доли меди в окисленных минералах к общей массовой доле меди. Аналогичным образом на основе спектрального минералогического анализа производится определение соотношения первичных (халькопирита) и вторичных (борнита, халькозина, ковеллина) сульфидных минералов меди. Одновременно фиксируется наличие и измеряется массовая доля талька, слюды, сланцев, серицита и других минералов, присутствие которых оказывает влияние на процесс флотации.
Задача определения сортности поступающей на переработку руды состоит в определении ее схожести с основными технологическими типами руд [8]. В принятом нами алгоритме конечная задача определения сортности руды состоит в определении ее состава - доли в ней основных технологических типов руд. В качестве первичной информации системы анализа используются показания рентгенофлюоресцентных анализаторов вещественного состава и показания датчиков видео-имидж-анализа.
Расчет сортности руды осуществлялся с применением многокритериального метода расчёта принадлежности. Область нахождения искомого решения в нашей задаче представлена образами типовых руд. Руда представляется в виде смеси пяти типов руд, при этом в руде определяется доля каждого типа руды. Математическая часть системы обеспечивает расчет сортности поступившей руды по шести или более значимым параметрам руды (например, по содержанию меди, молибдена и железа в руде, массовой доле окисленных минералов меди, вторичных сульфидных минералов меди в руде, первичных минералов меди и серицита). Можно использовать и другие параметры: например, гранулометрический состав, дробимость или измельчаемость руды [9].
Решение многокритериальной задачи заключается в нахождении доли принадлежности расчетной точки к определённому множеству точек на плоскости (двумерное пространство) или в любом другом «пространстве». Суть расчёта долей принадлежности руды к определённому типу состоит в том, что для поступившей руды можно определить степень «сходства» каждому из известных пяти типов руды, и пропорционально этой степени установить доли, которые каждый из пяти типов руды составляют в поступившей на переработку руде [8]. Для этого сначала определяется удаленность от точки, координаты которой соответствуют параметрам руды, поступившей на переработку, до каждой из точек, координаты которых соответствуют типам, руд, выделенных технологами в качестве базовых (рис. 4).
Затем при помощи расчетных уравнений после проведения операций нормирования и оценки значимости параметров определяются искомые значения массовых долей типовых руд в руде, поступающей на переработку.
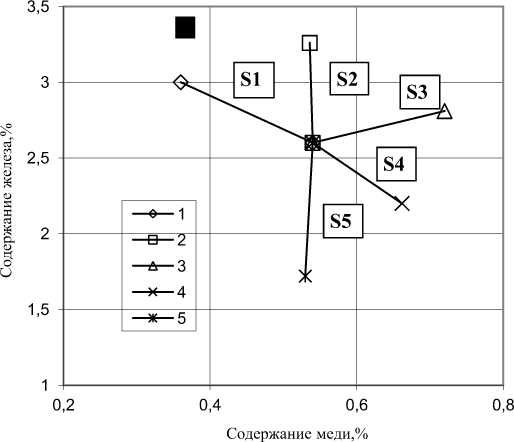
Рис. 4. Пример оценки состава руды в двумерном пространстве 1, 2, 3, 4, 5 – типы руд;
6 ( ) – руда текущей добычи; S1, S2, S3, S4, S5 – отклонения параметров руды текущей добычи от параметров руд типов 1, 2, 3, 4, 5
Нормированная величина отклонения ( Si ) параметров смеси руд ( Zn ) от параметров типовых руд ( Zni ) рассчитывается по формуле:
S i=Vn- Z „\! Z» при i = 1-5. (1)
Нормированные величины схожести параметров смеси руд с параметрами типовых руд рассчитываются по формуле:
D i =1/ S i , при i = 1-5, (2)
где Si – нормированное отклонение параметров смеси руд от параметров типовых руд. Расчет массовой доли отдельного типа руды ( i ) в смеси руд проводится по формуле:
Y i = kD i / 2 kD i . при i = 1-5 (3)
где k – коэффициенты значимости отдельных измеряемых параметров руды.
Коэффициенты значимости отдельных параметров являются адаптивно настраиваемыми параметрами, исходной базой для корректировки которых является проверочная информация о фактической сортности руды, получаемая по результатам анализа проб, отобранных и проанализированных с применением классических методик.
Операция определения сортности повторяется через заданный промежуток времени. Конечные результаты анализа сортности перерабатываемой руды имеют вид временных зависимостей, представленных на рис. 5 и отражающих изменение состава перерабатываемой руды.
Модернизация системы оптического анализа руды на конвейере
В результате совместных исследований ученых НИТУ «МИСиС» и ГОКа «Эрдэнэт» был разработан и испытан новый способ опережающей диагностики руды на базе оптического анализатора минерального состава.
Система видео-имидж-анализа (рис. 6) обеспечивает получение цифрового видеоизображения руды. Она была сформирована с помощью современных телеметрических и программно-технических средств. Система позволяет получить информацию в реальном времени о минералогическом составе руды и о типе руды. Система также позволяет получить данные по гранулометрическому составу руды, поступающей в операцию измельчения, и характеру вкрапленности минералов.
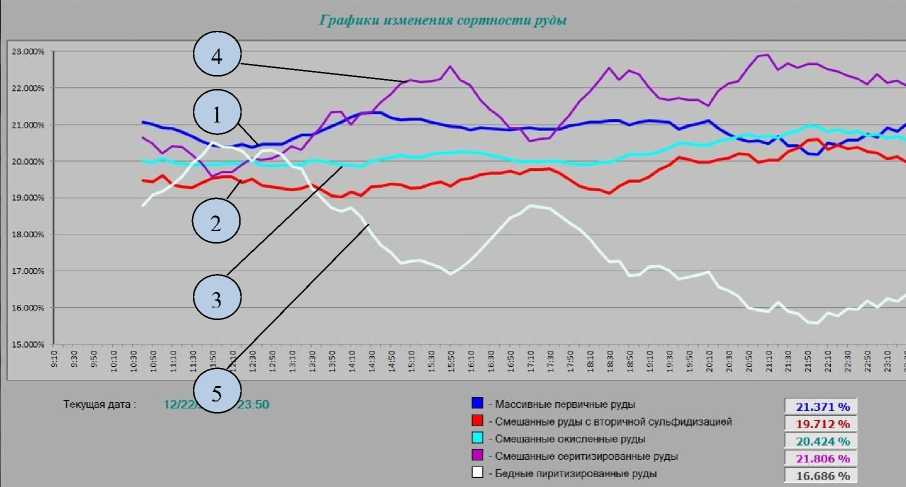
Рис.5. Изменение состава руды текущей добычи: 1 – массивные первичные руды; 2 – смешанные руды с вторичной сульфидизацией; 3 – смешанные окисленные руды; 4 – смешанные серитизированные руды; 5 – бедные пиритизированные руды
<
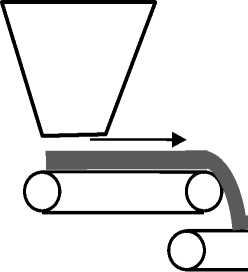
' 6 4 2 ; 8 5
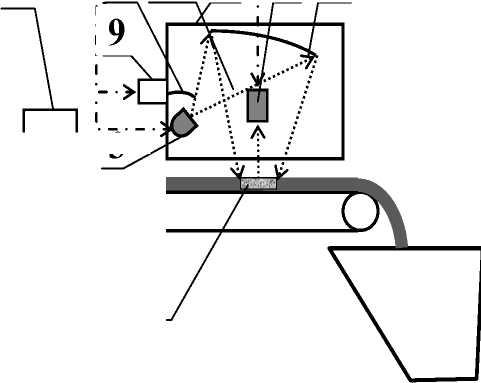
Рис.6. Установка телеметрического анализа крупности и качества руды. 1 – зона измерений; 2 – корпус, 3 – источник света, 4 – световой поток; 5 , 6 – основной и дополнительный отражатели; 7 – брызгала; 8 – видеокамера; 9 – привод отражателя; 10 – микропроцессор
Установка работает в двух чередующихся режимах. В первом режиме работы от отражателя 5 формируется рассеянное освещение, способствующее равномерному освещению пробы. Во втором режиме от отражателя 6 формируется плоскопараллельный световой поток. Это способствует максимальной «контрастности» изображения, что необходимо для измерения крупности руды.
Сканирование руды на конвейере осуществляется непрерывно. Получаемая от системы информация обрабатывается и усредняется. Далее по описанному выше алгоритму проводится распознавание сортности и крупности руды. Полученные результаты используются для автоматизированного управления процессами рудоподготовки и флотации.
Устройство для оптического анализа отобранной пробы руды
Недостатком анализа руды на конвейере остается невысокая точность измерений вследствие нечеткости фиксируемых изображений. Это обусловлено недостаточной однородностью плоского участка пробы и невозможностью фокусировки на всей поверхности руды.
В результате совместных исследований ученых НИТУ «МИСиС» и ГОКа «Эрдэнэт» был испытан новый способ диагностики руды на базе планшетного анализа минерального состава. Высокая точность визиометрического анализа достигается при использовании специальных устройств, инсталлируемых в схему отбора, и анализа проб руды отделом технического контроля. Для такого анализа была разработана специальная установка.
Установка включает столик для размещения пробы, выполненный из прозрачного стекла, источник светового потока, оптическую систему и оптический преобразователь.
Методика измерений включает измерений в виде плоского участка пробы, освещение и фиксацию изображений сформированного плоского участка пробы в видимой области спектра, освещение и фиксация изображения пробы осуществляются снизу вверх, в режиме двухмерного сканирования.
За счет «укладывания» зерен происходит существенное уменьшение неровности пробы. Формируется практически плоскопараллельная поверхность с равномерной освещенностью без затененных участков. Этим обеспечивается высокая четкость изображения и в последующем большая точность определения минералов.
Управление процессами обогащения на основе информации о сортности руды
Процесс управления качеством руды первоначально осуществляется на стадиях добычи и транспортирования руды. В нем предусматривается управление как усреднением руды в потоке, так и разделением первичного потока на потоки преимущественно сульфидных и преимущественно смешанных руд. Предлагаемая схема обогащения и средства автоматизированного контроля процесса обогащения представлены на рис. 8.
Первой стадией является отбор пробы и проведение минералогического анализа руды непосредственно на стадии горных работ. В качестве критериев качества руды используются показатели «окисленность руды» и «первичность руды». Критерий «окисленности руды» численно соответствует доле меди, находящейся в форме окисленных минералов (азурита, куприта, малахита, хризоколлы и др.). Критерий «первичности руды» рассчитывается как доля меди, находящейся в форме минерала халькопирита (первичного сульфидного минерала меди). В зависимости от значений указанных параметров формируют потоки окисленной руды, направляемой на выщелачивание, подготовку пробы руды, формирование зоны
первичной и смешанной руды, направляемых на обогащение.
Чтобы рассчитать оптимальные параметры измельчения и флотации различных сортов руды, проводились исследования на наиболее ярко выраженных пробах типовых руд и составлялись режимные карты процессов их измельчения и флотации. Учитывая невозможность получения проб, представляющих руду заданного сорта, проводились статистическая обработка результатов и моделирование режимов обогащения «типовых» руд: массивных первичных руд (МПР); смешанных вторично сульфидированных руд (СВСР); бедных пиритизованных руд (БПР); смешанных серитизированных руд (ССР) и смешанных окисленных руд (СОР).
Результаты моделирования в виде оптимальных параметров процессов измельчения и флотации каждого сорта руд (табл. 1) были рекомендованы для применения в системах автоматизированного управления на обогатительной фабрике ГОКа «Эрдэнэт».
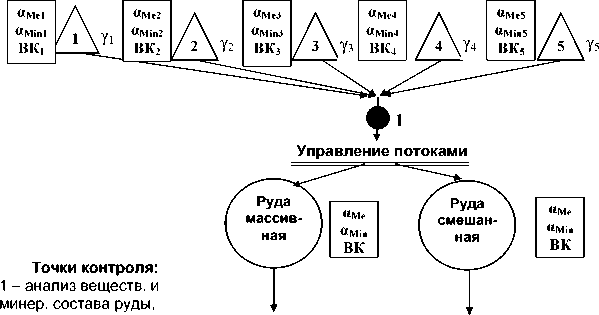
Дробление 1
расход руды;
2 – крупность измельч. руды и производ.
мельницы по гот. классу крупности;
3 вещ. состав к-та, хвостов

Дробление 1

Дробление 2-3
•1
Полусамоизмельчение
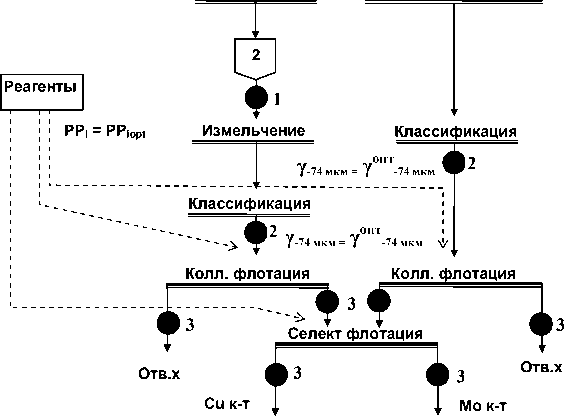
Рис. 8. Принципиальная схема формирования потока руды текущей переработки как смеси руд определенных технологических сортов и расположения точек опробования технологических продуктов, ВК – вкрапленность ценных компонентов
Оптимальные значения параметров процессов измельчения и флотации были использованы для расчета функций-задатчиков SF локальных автоматизированных систем автоматического регулирования с обратной связью [10]. После установки значений входных параметров, выбранных в соответствии с определенной сортностью руды, проводилось регулирование процесса.
Значение функции-задатчика SF для каждого параметра технологического процесса было рассчитано как взвешенное среднее оптимальных значений этих параметров для каждого стандартного сорта руды ( SFi ) с учетом вклада данного сорта в смеси руд по уравнению (4)
SF = Z'liSFi • (4)
где y i _ относительная массовая доля руды i -го типа в поступающей на переработку смеси руд.
В массив расчетных данных включены расходы реагентов, переработка руды, крупность измельчения и т.д.
При расчете расходов реагентов могут учитываться эффекты влияния при совместной переработке руд различных технологических типов. Взаимное влияние руд учитывается поправочными коэффициентами L i . Тогда уравнение (4) принимает вид;
SF^L i^ SF i . (5)
Предустановленные функции были использованы в качестве базового уровня в локальных системах автоматического регулирования процесса измельчения и флотации. Использование процедуры определения сортности руды повышает устойчивость автоматического управления. При использовании алгоритма оценки сортности руды на 5 % до 7 % увеличилась стабильность управления. Поддержание оптимальной степени измельчения и расхода реагентов при флотации руд текущей добычи обеспечивает увеличение извлечения меди и молибдена в концентраты на 0,3 и 1,1 %, соответственно, а также расходов реагентов на 2–3 %.
Таблица 1
Оптимальные параметры процессов измельчения и классификации – целевые функции в системах управления
Параметры технологического процесса |
МПР |
СВСР |
БПР |
СОР |
ССР |
Крупность измельчения, %, класс – 74 мкм |
67,50 |
64,50 |
67,00 |
66,00 |
66,00 |
Подача руды на мельницу, т/м3ч |
1,65 |
1,74 |
1,71 |
1,75 |
1,75 |
Плотность пульпы, % |
43,50 |
41,00 |
41,50 |
40,00 |
40,00 |
Расход собирателя АeroMX-5140 |
10,00 |
12,00 |
13,00 |
17,50 |
10.00 |
Расход вспенивателя МИБК |
13,00 |
16,00 |
16,00 |
19,00 |
13,00 |
Расход извести |
1100,00 |
1300,00 |
1300 |
1300,00 |
1100,00 |
Примечание. МПР – массивные первичные руды; СВСР – смешанные вторичные сульфидированные руды; БПР – бедные пиритизованные руды; ССР – смешанные серитизированные руды; СОР – смешанные окисленные руды.
ЗАКЛЮЧЕНИЕ
В результате совместных исследований ученых НИТУ «МИСиС» и ГОКа «Эрдэнэт» получил дальнейшее развитие принцип регулирования процесса флотации но основе опережающей оценки сортности перерабатываемой руды. Испытаны новые способы и устройства для автоматического измерения минерального состава руды на конвейере и в виде специально отобранной пробы. Алгоритм управления использует данные о сортности руды и накопленную информацию об оптимальных параметрах технологических режимов измельчения и флотации. Внедрение разработанной системы обеспечивает снижение потерь ценных компонентов и расходов реагентов на 3–5 %.
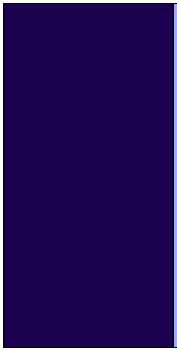
information-analytical bulletin. – 2011. – No. 12. – pp. 176-182.
Список литературы Совершенствование интеллектуальных методов управления процессами обогащения на основе визиометрического анализа сортности руды
- Daniel Sbárbaro, René del Villar Advanced Control and Supervision of Mineral Processing Plants. -Springer-Verlag London Limited, 2010. -332 p.
- Hyotyniemi H., Ylinen R. Modelling of visual flotation froth data//Automation in mining, mineral and metal processing 1998. In: Preprints of a 9th IFACSymposium, Cologn, Germany, 1-3 Sept. 1998. -Pergamon, 1998. -p. 309-314.
- Мойланен Я., Тимпери Ю., Кемппинен Х. Принципы компьютерного управления флотационным процессом на базе новой продукции Outotec -видеосистемы Frothmaster//Изв. вузов. Горный журнал. -2010. -№ 2. -С. 89-92.
- Hyotyniemi H., Koskinen K., Saloheimo K. Calibration of an X-ray fluorescence analyzer using clustered components//Future Trends in automation in mineral and metal processing. -Preprints of IFAC Workshop, Finland, 22-24 Augst 2000. -IFAC, Copy-set Oy, Helsinki, 2000. -p. 219-224.
- Olli Haavisto, Jani Kaartinen, and Heikki Hyötyniemi. 2006. Optical spectrum based estimation of grades in mineral flotation. In: Proceedings of the 2006 IEEE International Conference on Industrial Technology (ICIT 2006). Mumbai, India. -2006, Pp 2529-2534.
- Morozov V., Davaasambuu D., Ganbaatar Z., Delgerbat L., Topchaev V., Sokolov I., Stolyarov V. Modern systems of automatic control of processes of grinding and flotation of copper-molybdenum ore. In: 16th IFAC Symposium on Control, Optimization and Automation in Mining, Minerals and Metal Processing, Volume 15, Part1, IFAC (ed.), 2013. -Pp. 166-171.
- Agoston, Max K. Computer Graphics and Geometric Modeling: Implementation and Algorithms. London: Springer. -2005. Pp. 300-306. ISBN 1-85233-818-0.
- Морозов В.В., Ганбаатар З., Лодойравсал Ч. И др. Обогащение медно-молибденовых руд с применением комплексного радиометрического анализа сортности руды//Горный информационно-аналитический бюллетень. -2011. -№ 12. -С. 176-182.
- Улитенко К.Я., Морозов В.В., Бокани Л. Разработка и обоснование методов повышения эффективности процессов рудоподготовки на основе применения многоуровневых адаптивных систем регулирования//Плаксинские чтения/Материалы международной науч-практ. конф. -Казань, 2010 г. -С. 19-22.
- Ганбаатар З., Дэлгэрбат Л., Дуда А.М., Морозов В.В. Управление обогащением медно-молибденовых руд на основе комплексного радиометрического анализа руды//Плаксинские чтения/Материалы международной науч-практ. конф. -Екатеринбург, 2011. -С.118-121.