Совершенствование технологии проектирования сложных штампов на основе моделирования процесса их эксплуатации
Автор: Богомолов Родион Михайлович, Носов Николай Васильевич
Журнал: Известия Самарского научного центра Российской академии наук @izvestiya-ssc
Рубрика: Машиностроение и машиноведение
Статья в выпуске: 4-2 т.20, 2018 года.
Бесплатный доступ
В статье приводятся результаты проектирования сложных штампов при изготовлении заготовок буровых шарошечных долот с гарантированными прочностными параметрами на основе моделирования процесса их эксплуатации и применения теории приспособляемости без проведения длительных и дорогостоящих натурных экспериментов, а также методика конечно-элементного моделирования процесса штамповки, которые на стадии проектирования позволяют оптимизировать модели штампов с учетом изменяемых силовых и температурных режимов эксплуатации, геометрических параметров гравюры и выбора материала.
Лапа шарошки бурового долота, конечно-элементная модель, моделирование численное, оптимизация, режимы штамповки, сквозное проектирование, cad/cam/cae-технологии
Короткий адрес: https://sciup.org/148312466
IDR: 148312466
Текст научной статьи Совершенствование технологии проектирования сложных штампов на основе моделирования процесса их эксплуатации
соответсвующих возможно большей области приспособляемости. С этой целью на каждой итерации корректируются значения модулей упругости Ei в каждом из конечных элементов. Сокращение времени решения происходит за счет применения итерационного метода, состоящего в последовательном решении ряда линейных задач вместо пошагового решения на каждом цикле нагружения.
МОДЕЛИРОВАНИЕ ПРОЦЕССА
Для оценки границ приспособляемости использовалась статическая теорема Мелана. В соответствии с данной теоремой приспособляемость в идеальном упругопластическом теле наступает, когда можно найти такое, не зависящее от времени, поле фиктивных остаточных напряжений σ i ′ j , чтобы при любых изменениях нагрузки в заданных пределах сумма этого поля с полем упругих напряжений σ ij в идеально упругом теле была безопасна, т.е. суммарное напряжённое состояние σ ∗ ij находилось внутри полей текучести.
Внешние усилия, при которых рабочие напряжения σ ∗ ij и σ i ′ j достигают предела текучести, обозначаются соответственно через Q m ∗ и Q m ′ . Меньшее из этих усилий является оценкой границы приспособляемости на данной итерации: Q m = min( Q m ∗ , Q m ′ ) . Окончательная оценка – это величина Q = max( Q m ) . Она достигается на той итерации, где на m грузки Q m и Q m ′ оказываются наиболее близкими друг к другу.
Для практического решения задачи определения циклической несущей способности эле- ментов гравюры штампа заготовки лапы бурового долота применялась двухшаговая численная процедура конечно-элементного моделирования, согласно которой процесс штамповки сначала моделируется без учёта зависимости между тепловыми и механическими нагрузками.
При этом нижняя половинка штампа рассматривалась как абсолютно жёсткое тело, верхняя – как упругое тело, а заготовка имела термовязкоупругое поведение. Затем тепловые и другие поля напряжений в верхней половинке штампа рассчитывались с точностью, необходимой для решения задачи приспособляемости с применением пакета ANSYS. Геометрическая модель штампа строилась в CAD-системе Unigraphics, а затем передавалась непосредственно в ANSYS [4]. Анализ распределения напряжений и температур по поверхности гравюры и в сечениях штампа проводился на основе построения соответствующих изолиний.
При моделировании процесса взаимодействия контактных поверхностей между инструментом и заготовкой учитывались три аспекта: контактные напряжения, изменение коэффициента трения и коэффициент теплопередачи. Для описания процесса трения принимался закон трения Кулона. Эквивалентное касательное напряжение рассчитывалось в соответствии с условием текучести Треска
K I = Ц^ п при ЦО < m -^3 ;
τ
σσ m -^ при цо > m =
3 n 3
где µ – коэффициент трения скольжения, m – коэффициент касательных напряжений, σ o – предел текучести, σ n – нормальное напряжение на контактной поверхности.
Методика расчета предусматривала двухуровневое решение. Сначала гравюра верхней половины штампа (рис. 1) моделировалась с использованием относительно грубой конечноэлементной сетки. Затем на наиболее нагруженной часть штампа изменялась модель, в которой использовалась достаточно мелкая сетка.
Размер мелкой сетки подбирался таким образом, чтобы обеспечить достаточную точность аппроксимации градиента температур в приповерхностных слоях инструмента (рис. 2).
Решение задачи теплопроводности выполнялось для циклических условий нагружения, соответствующих реальным режимам процесса штамповки с использованием схематизированных диаграмм деформирования стали 5ХНМ.
Изменение температуры определялось в точке пересечения поперечного и продольного сечений, выбранной на наиболее нагруженной поверхности гравюры при последовательной штамповке нескольких заготовок (рис. 3).
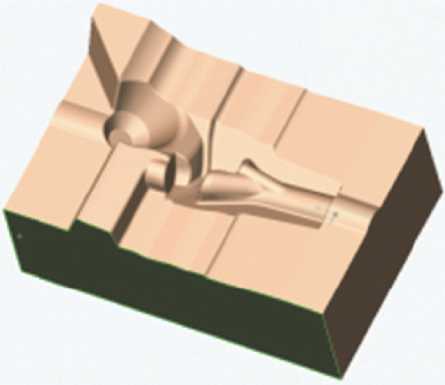
Рис. 1. 3-D модель верхней половины штампа
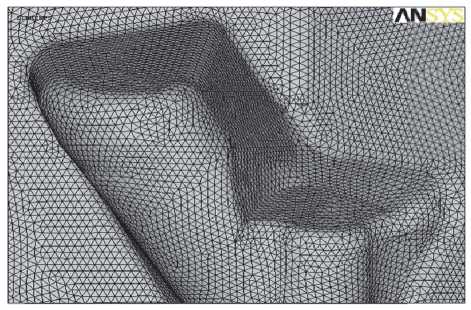
Рис. 2. Участок конечно-элементной сетки наиболее нагруженной части инструмента
Исследования показали, что разница температур при штамповке 3 и 4 заготовки составляет менее 5%, что позволяет считать температурный цикл установившимся.
Расчет полей упругих напряжений производился для двух моментов времени: при третьем и четвертом ударе (рис. 3). Затем они складывались из температурных напряжений и напряжений от усилий со стороны заготовки в наиболее нагретой точке в пределах базовой геометрии. Результаты анализа показали, что в наиболее нагруженных областях упругие напряжения, вызванные температурным градиентом, составляют до 90% от общих напряжений.
В соответствии с выбранными границами приспособляемости был выполнен прямой пошаговый расчёт напряжённо-деформированного состояния верхней половинки штампа при штамповке заготовки с температурой нагрева от 1100 °С до 1200 °С.
Оценка снизу границы приспособляемости проводилась по следующему условию
|^ч+ 5 ij\ T , (1) где σ i ′ j – поле остаточных напряжений после третьего удара при штамповке первой заготов-
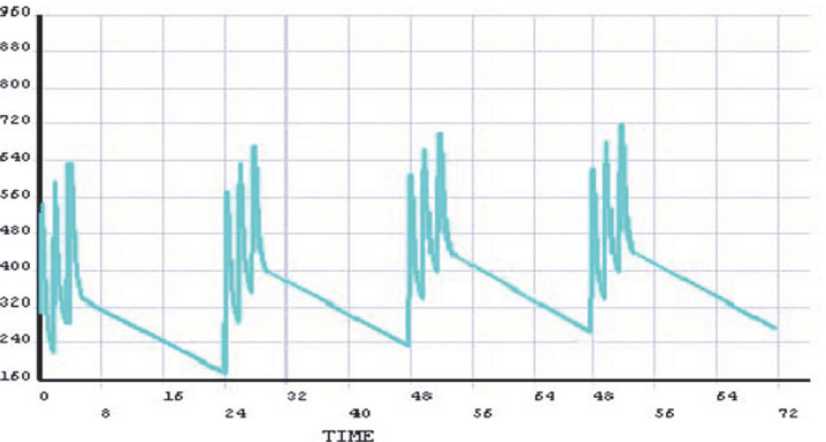
Время, с
Рис. 3. Влияние циклической нагрузки на температуру (градусы Цельсия) процесса
ки; σ ij – поле упругих напряжений во время третьего удара при штамповке третьей заготовки, когда достигается установившееся циклическое температурное состояние; s Т – предел текучести соответствует температуре в момент третьего удара.
Прямыми скобками показано вычисление интенсивности напряжений, которые соответствуют температуре в момент третьего удара при штамповке третьей заготовки.
Выполнение условия (1) означает, что приспособляемость имеет место. Проведённые расчёты для интервала температур заготовки от 1100 °С до 1200 °С показали, что для верхней границы интервала при повышении интенсивности напряжений в левой части (1) превышает предел текучести на 24%, а при температуре заготовки 1100 °С – ниже его на 5,7% (рис. 4).
Как видно из графика, снижение температуры заготовки на 100 °С приводит к значительному и практически равномерному снижению интенсивности упругих напряжений в приповерхностных слоях штампа (примерно на 5060%), что несомненно должно способствовать повышению стойкости штампов.
Из выполненного анализа следует, что варьированием температуры заготовки можно реально оптимизировать и повышать долговечность штампов.
Снижение интенсивности термоупругих напряжений на поверхности гравюры может быть также достигнуто за счёт изменения её геометрической формы и улучшения условий отвода тепла от поверхности.
Наибольшее влияние на условие отвода тепла из зоны деформации оказывают изменения гео-
X g 800
H 700
J 5 6oo
H s g я 500
§ I 400
я I 300
к 200
100 0
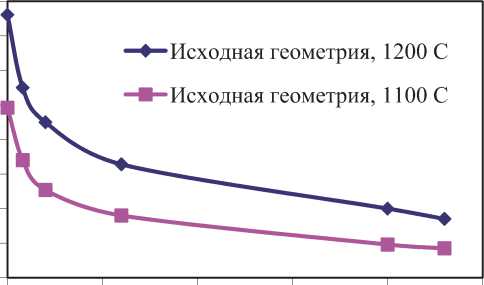
0 0,5 1 1,5 2 2,5
Глубина залегания, мм
Рис. 4. Интенсивность упругих напряжений и их глубина залегания в наиболее нагретой точке при штамповке третьей заготовки (третий удар) с учетом температуры заготовки метрической формы и в частности увеличение радиусов сопряжений поверхностей на 50-70%.
Произведен анализ напряженно-деформированного состояния гравюры штампов с измененной геометрией при температуре заготовки в 1200 оС по разработанной методике. Исследования показали, что превышение левой части уравнения (1) над правой составило примерно 3-8%.
Результаты исследования интенсивности упругих напряжений от глубины залегания при изменении геометрии штампа (увеличении радиусов скругления на 50-70 %) приведены на рис. 5.
Как видно из графика, при изменении радиусов скругления приводит к перераспределению напряжений за счет существенного их снижения на поверхности (с 761 МПа до 517 МПа) и незначительного роста в глубине штампа (с 170 МПа до 193 МПа). При этом, температура на поверхности в наиболее нагретой точке уменьшается на 940С, а на глубине практически остается неизменной (увеличение на 5 оС) (рис.6).
Таким образом, изложенный подход позволяет оптимизировать и количественно оценивать увеличение сопротивления смятию гравюры с измененной геометрией.
Разработанная методика позволяет не только спрогнозировать выбор марки штамповых сталей с целью повышения стойкости инструмента, но и учесть такие механические свойств, как пределов текучести, прочности, усталости, относительного удлинения при разрушении и др.
В работе исследованы нескольких марок стали: сталь 5ХНМ и сталь 5Х2НМФ. Физико-механические свойства этих сталей приведены в таблице, а теплофизические свойства этих сталей мало отличаются.
Расчеты показывают, что применение стали 5Х2НМФ практически не повлияло на распределение полей температур, а циклические напряжения оказались полностью в упругой области.
Для производства штамповой оснастки при изготовлении лап буровых долот наибо-
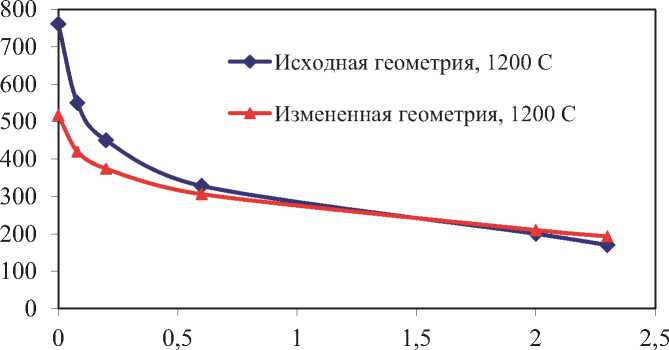
Глубина залегания, мм
Рис. 5. Интенсивность упругих напряжений и их глубина залегания в наиболее нагретой точке при штамповке третьей заготовки (третий удар) с учетом изменения геометрии
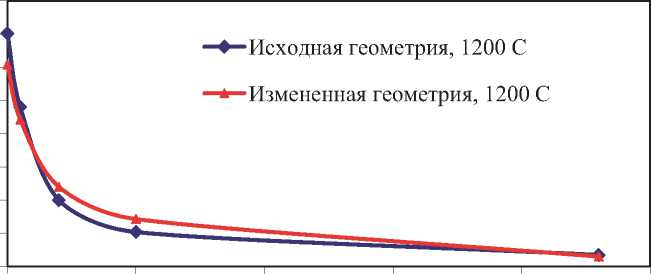
0 0,5 1 1,5 2 2,5
Глубина залегания, мм.
Рис. 6. Распределение температуры по глубине штампа в наиболее нагретой точке при штамповке третьей заготовки (третий удар)
Таблица. Физико-механические свойства сталей
Разработана схема процесса сквозного автоматизированного проектирования детали, поковки и штамповой оснастки для ее изготовления, проектирования технологии изготовления штампов, отслеживания и необходимой модификации хода выполнения проектных процедур на всех его стадиях, включая управление архивом проектных решений.
Из схемы видно, что концепция сквозного цикла использует 3-х -мерную модель как базовый элемент для объединения отдельных этапов подготовки и производства в единую информационную технологию. Предложено программное обеспечение для 2D- и 3D-моделирования, проектирования технологических процессов и инженерных расчетов, разработана методика и программный комплекс для построения 3D-моделей заготовки и штампа, созданы системы автоматизированного проектирования «САПР-Долото».
Концепция сквозного цикла еще на стадии проектирования обеспечивает возможность оптимизации геометрических параметров поковки и штампа на основе применения метода конечных элементов в процессе проектирования. После выбора оптимальной геометрии штампа выполняется разработка управляющих программ станков с ЧПУ для его изготовления. Возможности программного обеспечения CAD/ CAM являются ключевыми в обеспечении эффективной высокопроизводительной обработки штампов. Технология начинается с создания управляющей программы, которая в большой мере влияет на износ дорогостоящего станка, инструмента и качество обработки.
Таким образом, можно сделать следующие выводы:
-
1. Разработана более совершенствования технология проектирования и изготовления сложных штампов с гарантированными прочностными параметрами на основе моделирования процесса их эксплуатации и применения теории приспособляемости.
-
2. Предложена методика конечно-элемент-
Рис. 7. Схема процесса сквозного проектирования изделия (CAD/CAM/CAE – технологии)
-
3. Показано, что применение стали 5Х2НМФ существенно (на 90° и более) снижает температуру в наиболее напряженных зонах гравюры и до 60% интенсивность внутренних напряжений в поверхностных слоях.
-
4. Разработаны автоматизированная система сквозного проектирования лап буровых долот и их заготовок, которые на стадии проектирования позволяют оптимизировать модели штампов с учетом изменяемых силовых и температурных
ного моделирования процесса штамповки, установлены параметры нагрева заготовки, геометрическая форма гравюры в зависимости от механических свойств материала
режимов эксплуатации, геометрических параметров гравюры и выбора материала.
Список литературы Совершенствование технологии проектирования сложных штампов на основе моделирования процесса их эксплуатации
- Гавриленко М.В., Богомолов Р.М. Совершенствование технологии автоматизированного проектирования и изготовления штамповой оснастки для выпуска лап буровых долот // Заготовительные производства в машиностроении. 2004. № 6. 28-34 с.
- Исследование напряженно-деформированного состояния при запрессовке твердосплавных элементов вооружения шарошки бурового долота / В.И. Кремлёв, Н.В. Носов, Р.М. Богомолов, Л.В. Морозов ///Вестн. СамГТУ. Серия «Технич. науки». 2005, Вып. 39. С. 234-238.