Создание цифрового двойника процесса сборки рабочего колеса компрессора
Автор: Печенина Е.Ю.
Журнал: Известия Самарского научного центра Российской академии наук @izvestiya-ssc
Рубрика: Машиностроение и машиноведение
Статья в выпуске: 1 т.25, 2023 года.
Бесплатный доступ
Разработан цифровой двойник процесса сборки рабочего колеса компрессора, позволяющий прогнозировать угловые развороты лопаток, возникающие при сборке. Вычисляемые углы характеризуют натяги в соединениях торцевых полок лопаток. На входе в цифровой двойник поступают данные по отклонениям геометрии с контрольных операций деталей. При реализации цифрового использован метод случайного леса, обучение которого производилось на множестве численных экспериментов, выполненных в среде ANSYS с использованием конечно-элементной модели собранного рабочего колеса. Результаты экспериментов показали, что погрешность расчетов с использованием цифрового двойника не превышает 15 угловых минут.
Цифровой двойник, рабочее колесо, сборка, герметичность, конечно-элементная модель, метод случайного леса
Короткий адрес: https://sciup.org/148326097
IDR: 148326097 | DOI: 10.37313/1990-5378-2023-25-1-28-35
Текст научной статьи Создание цифрового двойника процесса сборки рабочего колеса компрессора
Заданная степень повышения давления, устойчивость и надежность работы компрессора зависит от обеспечения равномерности сборочных параметров между лопатками [1]. В рабочем колесе (РК) компрессора 8 ступени ключевым сборочным параметром является величина натягов между антивибрационными полками лопаток. Обеспечения равномерного натяга является при ремонте и использования двигателя в качестве наземной силовой установки первостепенной задачей, так как требуемый ресурс работы компрессора возрастает в 2-3 раза. На рисунке 1 приведена модель рассматриваемого рабочего колеса компрессора.
Из-за недостаточного или излишнего напряжения между лопатками, а также его неравномерности лопатка становится излишне вибронагруженной, начинает колебаться и разрушается, обломки лопаток в процессе работы двигателя разрушают остальные лопатки диска, а кроме того, и лопатки нескольких дисков за ним. На рисунке 2 приведена фотография РК со сломанными лопатками, не прошедшего испытания.
Равномерность натягов по антивибрационным полкам обеспечивается точностью изготовления лопаток и их сборкой. Сужение допусков на изготовление экономически не целесообразно [2]. Существенным резервом повышения эксплуатационных показателей является улучше-
ние технологии сборки лопаточных венцов. При ремонте рабочего колеса выполняют предварительные расстановки лопаток, стремясь достичь лучшего результата, что является ресурсоемким процессом с множеством испытаний. Учитывая, что число лопаток в рассматриваемой ступени 84, число комбинаций принимает огромное значение, равное факториалу от числа лопаток.
Высокотехнологичная промышленность нового поколения основана на использовании цифровых данных для повышения качества и снижения сроков выведения изделий на рынок. Основой для такой промышленности является разработка цифровых двойников (ЦД) изделий. Применительно к рассматриваемому рабочему колесу, цифровой двойник – цифровая копия физического колеса в собранном состоянии, помогающая обнаруживать проблемы со сборкой, предсказывать результаты сборки и получать более точные результаты по натягам между лопатками. Применение компьютерного моделирования [3] и прогнозирования результирующих сборочных параметров [4] рабочего колеса возможно за счет использования современных средств измерений, позволяющих достаточно точно воспроизводить объекты разных габаритов и сложности [5].
В настоящее время существуют все возможности учитывать данные, поступающие с контрольно-измерительных операций лопаток [6, 7], и на основании этих данных строить математические модели расчета сборочных параметров [8] и производить сборку быстро и с требуемым качеством [9]. Цифровое моделирование позволяет осуществлять метод индивидуального подбора деталей в сборках [10, 11].
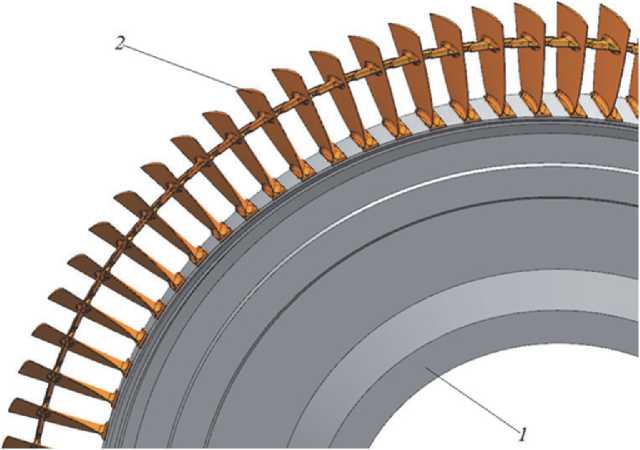
Рис. 1. Конструкторская модель рабочего колеса 8 ступени: 1 - диск; 2 - рабочая лопатка
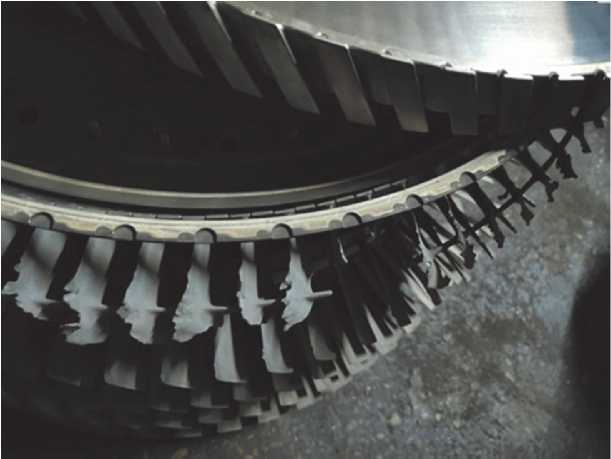
Рис. 2. Не прошедшее испытания рабочее колесо
Целью исследования является создание цифрового двойника процесса сборки рабочего колеса 8 ступени компрессора, позволяющего производить расчет углов закрутки лопаток, характеризующих натяги между антивибрационными полками рабочих лопаток. Для повышения скорости получения результатов расчетов сделано их обобщение с помощью использования подходов машинного обучения, в частности, метода случайного леса [12].
ЦИФРОВОЙ ДВОЙНИК ДЛЯ РАСЧЕТА УГЛОВ
Номинальные размеры и допуски на изготовление лопаток предполагают наличие натяга между антивибрационными полками, его величина определяется конструктором. Натяги определяются сочетанием геометрических от- клонений соседних лопаток, а также геометрическими отклонениями пазов диска, в которые они вставляются. Натяги в технологическом процессе контролируются в двух сечениях (рисунок 3) специальными приборами - угломерами: измеряется угол установки лопаток у:. в свободном и собранном состояниях; разница этих углов v. . характеризует величину натяга в соединении."
Согласно технологии изготовления, и на диске, и на лопатках проводится контроль геометрических параметров, характеризующих их качество.
На диске производится контроль пазов, ключевыми параметрами при их контроле являются: углы разворота пазов (между осью вращения диска и осями симметрии пазов) 3. ; величины углов деления пазов 5;,, . ' "
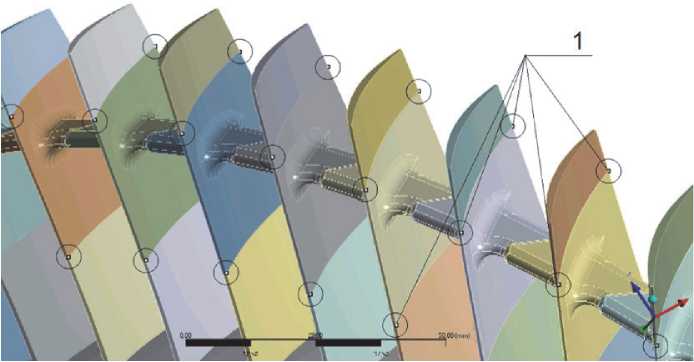
Рис. 3. Расположение контролируемых точек (1) на пере лопаток
При контроле лопаток в производстве измеряют: a) отклонение величин стыковых размеров по рабочим торцам антивибрационных полок лопаток ( ^sp ) со стороны спинки 51^ и корыта Sip ; б) фактические значения угла касательной к профилю в контрольных сечениях лопаток в свободном состоянии ( Уь) .
После измерений выполняется расчет отклонений измеренных параметров p от параметров , заданных по чертежу:
^as Pmeas Pt . (1)
Рассмотренные выше отклонения и план расположения лопаток в комплекте используются на входе в цифровой двойник для расчета значений возникающих натягов (характеризуемых Уь н). На рисунке 4 приведена архитектура цифрового двойника процесса сборки рассматриваемого РК и его место в технологическом процессе (ТП) сборки.
Основными этапами процесса сборки РК являются: 1) измерение геометрических параметров лопаток и дисков; 2) комплектование лопаток в РК; 3) сборка РК; 4) измерение сборочных параметров РК. На вход технологического процесса сборки РК поступают лопатки и диски. На выходе технологического процесса формируются РК. Повышение управляемости процессом сборки рабочих колёс возможно посредством выработки рациональных решений по комплектации и раскладке лопаток с использование ЦД. Между ЦД и технологическим процессом сборки предусмотрены прямая и обратная связи.
Прямая связь предусматривает передачу информации из ЦД в операцию комплектования ТП. Передаваемая информация содержит данные по рассчитанным отклонениям углов Yb m , характеризующих возникающие натяги в соединениях между лопатками. Использование численного
। ।
Рабочее колесо
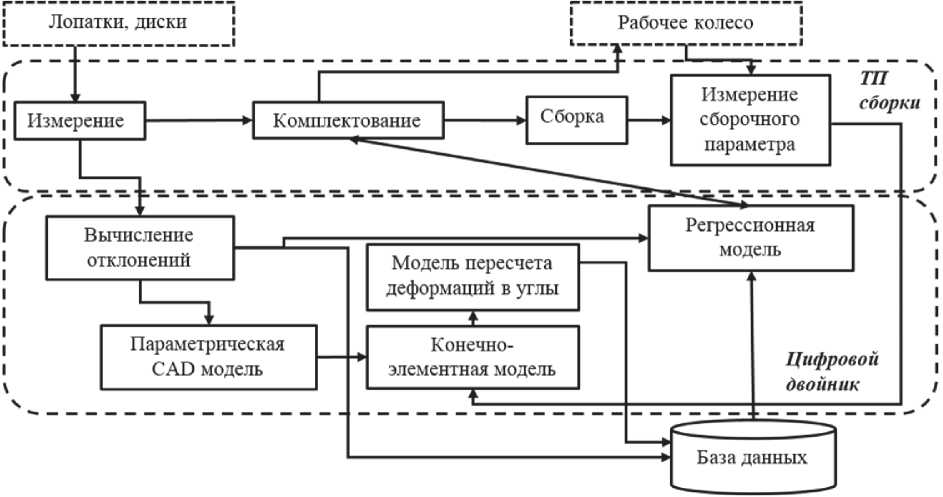
Модель пересчета деформаций в углы
Цифровой двойник
ТП х сборки
Конечноэлементная модель
1 п !
Лопатки, диски
Регрессионная модель
Измерение сборочного параметра
Параметрическая CAD модель
База данных
Вычисление отклонений
Комплектование
I Измерение
Сборка
Рис. 4. Архитектура цифрового двойника процесса сборки рабочих колёс
моделирования с использованием ЦД позволит принимать решение по улучшению комплектации (уменьшению неравномерности натягов) без многократных пересборок и измерений углов комплектов.
Обратная связь предусматривает передачу информации об измерениях геометрических параметров лопаток, дисков и рабочих колёс в ЦД для уточнения параметров моделирования при разработке модели.
ЦД включает в себя процедуру расчета отклонений параметров и комплекс моделей: параметрическая CAD-модель; конечно-элементная модель расчета деформаций; модель пересчета деформаций в углы установки; регрессионная модель, основанная на методе машинного обучения. Результаты рассчитанных углов и отклонений накапливаются в базе данных, информация из которой используется для обучения регрессионной модели. Рассмотрим разработанные модели, входящие в ЦД.
ПАРАМЕТРИЧЕСКАЯ CAD-МОДЕЛЬ
Параметрические модели лопаток созданы в программе NX. В модели упрощен хвостовик и пазы диска, осуществляется сдвиг и разворот торцевых контактных плоскостей антивибрационной полки. Кроме того, можно изменять угловое положение лопаток согласно погрешности деления пазов ^чч . На рисунке 5 приведен эскиз модели с обозначенными параметрами геометрических отклонений, которые можно вносить в модель.
КОНЕЧНО-ЭЛЕМЕНТНАЯ МОДЕЛЬ В ANSYS
Расчет изменения углов установки пера можно выполнить с использованием конечно-элементных моделей (КЭМ) в среде ANSYS. Создание конечно-элементной модели, как отмечалось выше, выполнялось в системе ANSYS Workbench, с использованием модуля Static Structural. Этапы формирования КЭМ: 1) задание механических свойств; 2) импортирование и связка параметризованных моделей лопаток и диска; 3) задание граничных условий; 4) задание выводимых параметров в препроцессоре.
Механические свойства материалов задавались исходя из материала лопаток рабочего колеса. Для выполнения КЭ моделирования сборки рабочего колеса задавались следующие механические свойства материала диска и лопаток: коэффициент Пуансо -на –0,36; модуль нормальной упругости 9,6 . 1010 Па; плотность материала 4620 кг/м3; предел прочности 1,07 . 109 Па; физический предел текучести 9,3 . 108 Па; условный предел текучести 9,3 . 108 Па; коэффициент теплового расширения 9,4 . 10–6 оС–1.
Для автоматизации задания параметров модели (геометрических отклонений, измеренных на деталях или сгенерированных) в пакете MATLAB был написан скрипт, управляющий процессом в ANSYS с помощью отправки APDL команд. Скрипт так же позволяет автоматически сохранять результаты расчетов. Исходные геометрические параметры лопаток загружаются из файла формата *.xlsx. После расчета величины деформаций вдоль координатных осей для контрольных точек экспортируются в формате *.txt.
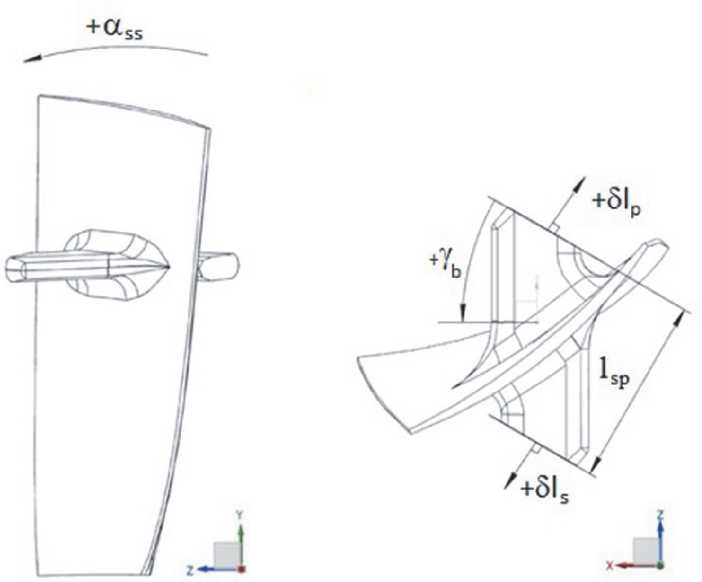
Рис. 5. Эскиз модели рабочей лопатки с параметрами отклонений
МОДЕЛЬ ПЕРЕСЧЕТА ДЕФОРМАЦИЙ В УСТАНОВКИ
Для расчета углов Yb из величин координат контрольных точек была разработана математическая модель, реализованная в среде MATLAB. Она позволяет преобразовать деформации, полученные из КЭМ, и координаты исходных точек геометрической модели в углы установки профилей. В результате для каждой лопатки рассчитываются величины изменений углов установки профилей.
На первом этапе координаты контрольных точек из конструкторской модели сохраняются в матрицу ^84X3. Значения деформаций точек на профиле лопаток вдоль трех осей последовательно загружаются и сохраняются в одну матрицу деформаций ^84X3 .
На втором этапе производится расчет координат точек на профиле лопаток после сборки, то есть когда лопатки контактируют друг с другом по антивибрационным полкам. Для этого необходимо просуммировать массив координат точек до сборки с массивом значений деформаций по правилу сложения матриц, получив матрицу :
@84x3 ~ ^84x3 + ^84x3 . (2)
Для выполнения расчета углов установки следует перейти в двумерную систему координат, что выполняется в два этапа. На третьем этапе преобразование Декартовой системы координат в полярную. За ось вращения примем ось двигателя X . Остальные две координаты точек в данном случае задаются с помощью угла •P и радиус-вектора p* от центра координат:
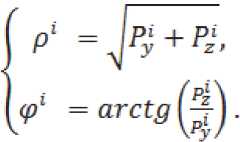
На четвертом этапе из двух полярных координат рассчитаем длину окружности для каждой точки, получив вторую ось X^ новой системы координат:
P'l = P£ ■ Ф1 № . (4)
На заключительном этапе в полученной плоской системе координат выполняется непосредственно расчет угла касательной к профилю лопаток Yb . Из координат точек вычисляются уравнения прямых, из уравнения прямых – углы наклона к оси X. Угол касательной до сборки на- ходится аналогично.
Далее вычисляется разность этих углов и, таким образом, получается угол между двумя прямыми – изменение угла
Yb , характеризу-
ющий разворот лопатки и возникающий натяг в соединении.
РАССМАТРИВАЕМЫЕ РЕГРЕССИОННЫЕ МОДЕЛИ
Расчет в КЭМ длится долго (для комплекта из 84 лопаток около двух часов на персональном компьютере с процессором AMD Ryzen 7 2700 Eight-Core с тактовой частотой 3,2 ГГц), требует долгой настройки и поэтому данный расчет проблематично использовать в производстве.
Моделирование посредством ANSYS случаев сборки используется для генерации выборки, достаточной для создания регрессионной модели, в которой на входе будут значения отклонений лопатки и двух ее соседей, на выходе величина угла разворота этой лопатки. Для построения регрессионной зависимости использовались методы машинного обучения: метод опорных векторов (SVM) [13], гребневая регрессия (KR) [14] и случайный лес (RF) [12]. Из трех методов выбирался лучший с точки зрения получаемой в прогнозе ошибки.
Оценка ошибок прогнозирования угла производится по трем критериям: доля спрогнозированных величин в пределах допустимой погрешности δ (количество случаев, не превышающих определенный порог), среднеквадратичная ошибка MSE и коэффициент детерминированности R 2. Допустимая величина ошибки была выбрана 10 угловых минут, или 0,167 °.
РЕЗУЛЬТАТЫ И ОБСУЖДЕНИЕ
Экспериментальные исследования включили в себя: апробацию разработанной конечноэлементной модели, используемой для создания обучающей выборки регрессионных моделей; проведение обучения трех моделей регрессии и выбор лучшей.
Используя результаты измерений лопаток для комплекта рабочих колес, было выполнено моделирование их сборки с использованием разработанной конечно-элементной модели. Углы были проанализированы и проведено их статистическое обобщение, а именно вычислено минимальное ^min , максимальное ^max значение, математическое ожидание /^ и среднеквадратическое отклонение .
Рабочее колесо было собрано, с использованием угломера были измерены углы Yb , и, соответственно, их разность Y ь m до и после сборки.
В таблице 1 приведены статистические характеристики углов Y ь m , полученных в эксперименте и рассчитанные с использованием КЭМ модели ЦД (математические ожидания, среднеквадратические отклонения, минимальные и максимальные значения).
Таблица 1. Статистические характеристики углов
Параметр |
Первое сечение |
Второе сечение |
||||
Эксперимент |
Модель |
Погрешность |
Эксперимент |
Модель |
Погрешность |
|
М , ° |
0,92 |
0,89 |
0,04 |
1,34 |
1,30 |
0,03 |
о , ° |
0,07 |
0,03 |
0,06 |
0,10 |
0,08 |
0,09 |
Д . ° mm, |
0,75 |
0,81 |
-0,11 |
1,15 |
1,10 |
-0,14 |
^ тах , |
1,07 |
0,94 |
0,17 |
1,66 |
1,45 |
0,25 |
Согласно обобщенным результатам в таблице 1, предельная погрешность модели не превышает 0,17° на первом сечении и 0,25° на втором сечении, или 15 угловых минут.
Основываясь на статистических данных по отклонениям лопаток, была выполнена искусственная их генерация для проведения моделирования достаточной обучающей выборки с использованием цифрового двойника. сего в ANSYS было проведено моделирование 15 комплектов по 84 лопатки в каждом с различными сочетаниями геометрических отклонений лопаток, для того чтобы максимально охватить возможные случаи сборки. Обучающая выборка для прогноза углов каждой лопатки составила 1008 случаев, тестовая 252 случая. Математическое ожидание обучающей выборки μ составило 1,632°, среднеквадратическое отклонение σ составило 0,249°.
В таблице 2 приведены значения минимального , максимального погрешностей прогноза , а так же и для тестовой и обучающей выборок при использовании рассматриваемых методов машинного обучения.
Меньшие погрешности дает модель RF, предельная величина погрешности для тестовой выборки фактически не превышает 0,05° для первого сечения и 0,11° для второго (6,6 угловых минут). При обучении предельные погрешности модели RF не превышают 0,163° (10 угловых минут). В таблице 3 приведены рассчитанные параметры точности прогнозирования с использованием рассмотренных методов машинного обучения для тестовой и обучающей выборки.
Согласно полученным результатам была выбрана модель регрессии с использованием метода случайного леса, имеющего наибольшей коэффициент R 2, наименьшую величину MSE и в котором ни один случай не выходит за допустимый предел погрешности в 10 угловых минут, что является хорошим результатом, так как в практике контроля сборочных параметров используют оптические угломеры, цена деления которых составляет 10 угловых минут.
ЗАКЛЮЧЕНИЕ
В результате исследований разработан цифровой двойник, позволяющий прогнозировать изменение углов установки, возникающие из-за контакта антивибрационных полок рабочих лопаток в сборке колеса компрессора, характеризующие натяги в соединении. В цифровом двойнике реализована конечно-элементная модель непосредственного расчета изменения углов, и кроме того обобщающая ее регрессионная модель, основанная на методе случайного леса. Погрешность расчета углов с помощью цифрового двойника не превышает 15 угловых минут, если использовать конечно-элементную
Таблица 2. Статистическая оценка погрешностей прогнозирования
Параметр |
Первое сечение |
Второе сечение |
||||||||||
SVM |
KR |
RF |
SVM |
KR |
RF |
|||||||
Обучение |
Тест |
Обучение |
Тест |
Обучение |
Тест |
Обучение |
Тест |
Обучение |
Тест |
Обучение |
Тест |
|
М, ° |
0,002 |
-0,001 |
-1-10-4 |
0,002 |
-0,002 |
-3-10-4 |
0,011 |
-0,002 |
-4-10-4 |
0,008 |
-0,005 |
-0,001 |
О,° |
0,049 |
0,028 |
0,004 |
0,049 |
0,029 |
0,011 |
0,056 |
0,072 |
0,011 |
0,061 |
0,065 |
0,029 |
^ mi» ° |
-0,100 |
-0,088 |
-0,021 |
-0,093 |
-0,082 |
-0,040 |
-0,244 |
-0,250 |
-0,059 |
-0,23 |
-0,163 |
-0,106 |
^ тах , ° |
0,100 |
0,062 |
0,016 |
0,100 |
0,052 |
0,046 |
0,152 |
0,173 |
0,042 |
0,132 |
0,146 |
0,093 |
Таблица 3. Параметры точности обучения и теста для разных моделей регрессии для прогноза
Список литературы Создание цифрового двойника процесса сборки рабочего колеса компрессора
- Иноземцев А.А., Нихамкин М.А., Сандрацкий В.Л. Основы конструирования авиационных двигателей и энергетических установок / А. А. Иноземцев, М.А. Нихамкин, В.Л. Сандрацкий. - Т.2. - М.: Машиностроение, 2008. - 365 с.
- Непомилуев, В.В. Повышение качества сборки путем обеспечения статистической управляемости технологических процессов изготовлекния деталей / В.В. Непомилуев, И.В. Дюпин // Сборка в машиностроении, приборостроении. - 2008. - № 2. - C. 3-7.
- Kannan S.M., Asha A., Jayabalan V. A new method in selective assembly to minimize clearance variation for a radial assembly using genetic algorithm // Quality engineering. 2005. Vol. 17. No. 4. P. 595-607. DOI: 10.1080/08982110500225398.
- Samper S., Adragna P-A., Favreliere H., Pillet M. Modeling of 2D and 3D assemblies taking into account form errors of plane surfaces // J Comput Inf Sci Eng. 2009. Vol. 9. No. 2. P. 1-12. DOI: 10.1115/1.3249575.
- Vezzetti E. Computer aided inspection: design of customer-oriented benchmark for noncontact 3D scanner evaluation // The International Journal of Advanced Manufacturing Technology. 2009. No. 41. P.1140-1151. DOI: 10.1007/s00170-008-1562-x.
- Chang H.-C., Li A.C. Automatic inspection of turbine blades using a 3-axis CMM together with a 2-axis dividing head // The International Journal of Advanced Manufacturing Technology. 2005. No.26. P.789-796. DOI: 10.1007/s00170-003-1877-6.
- Savio E., Chiffre L. De., Schmitt R. Metrology of freeform shaped parts // CIRP Annals - Manufacturing Technology. 2007. Vol. 56. No. 2. P. 810-835. DOI: 10.1016/j.cirp.2007.10.008.
- Groch D., Poniatowska M. simulation tests of the accuracy of fitting two freeform // International Journal of Precision Engineering and Manufacturing. 2019. Vol. 21. P. 23-30. DOI: 0.1007/s12541-019-00252-4.
- Zhang Z., Zhang Z., Jin X., Zhang Q. A novel modelling method of geometric errors for precision assembly // The International Journal of Advanced Manufacturing Technology. 2018. Vol. 94. P. 11391160. DOI: 10.1007/s00170-017-0936-3.
- Непомилуев В.В., Майорова Е.А. Оптимизация метода индивидуального подбора для многозвенных размерных цепей / В.В. Непомилуев, Е.А. Майорова // Известия МГТУ «МАМИ». - 2008. -№ 2(6). - C. 302-309.
- Осипович Д.А., Ярушин С.Г., Макеев А.Б. Исследование алгоритмов подбора лопаток при сборке сопловых аппаратов газотурбинного двигателя / Д.А. Осипович, С.Г. Ярушин, А.Б. Макеев // Сборка в машиностроении, приборостроении. - 2018. - № 7(216). - C. 313-319.
- Breiman L. Random Forests // Machine Learning. 2001. Vol. 45. No. 1. P. 5-32. DOI: 10.1023/A:1010933404324.
- Cristianini N., Shawe-Taylor J. An introduction to support vector machines and other kernel-based learning methods // Cambridge University Press, 2000. DOI: 10.1017/CBO9780511801389.
- Murphy K. P. Machine Learning: A Probabilistic Perspective // The MIT Press. 2012. ^apter 14.4.3, P. 492-493.