Способ переработки отходов производства стеклопластиков
Автор: Федарович Е.Г., Левданский А.Э., Ковалева А.А.
Журнал: Вестник Витебского государственного технологического университета @vestnik-vstu
Рубрика: Химическая технология
Статья в выпуске: 1 (51), 2025 года.
Бесплатный доступ
В настоящее время отмечается рост объема мирового рынка полимерных композиционных материалов, из которых наиболее широко распространенным является стеклопластик. Серьезной проблемой объемного производства и применения полимерных композиционных материалов является непременное образование отходов, оказывающих негативное влияние на окружающую среду. Для решения поставленной проблемы предлагается осуществлять переработку отходов стеклопластика механическим методом, путем их селективного измельчения в ударно-центробежной мельнице с последующей механической классификацией продуктов измельчения. Цель работы заключается в изучении фракционного состава продуктов переработки отходов стеклопластика в зависимости от режимов работы измельчителя. Для этого разработана экспериментальная установка исследования процесса механической переработки отходов стеклопластика. Механической переработке подвергались отходы производства стеклопластиковых изделий Депол С-180 ПТ образующиеся на предприятии ООО «Полоцк-Стекловолокно». В процессе исследований изменялась частота вращения ротора ударно-центробежной мельницы в диапазоне 1200–3000 об/мин. Полученные продукты переработки стеклопластика подвергали рассеву на фракции с последующим определением длины волокон в волокнистой фракции. Поверхность волокон и продуктов механической классификации исследовали при помощи микроскопа с 50–500 кратным увеличением. Установлено, что метод механической переработки с использованием ударно-центробежной мельницы позволяет выделить из стеклопластиковых отходов волокнистую фракцию, при этом ее количество в продуктах селективного измельчения напрямую зависит от частоты вращения ротора. Экспериментально определено, что переработку стеклопластиковых отходов целесообразно проводить при частоте вращения ротора в ударно-центробежной мельнице 2400 об/мин, что обеспечивает максимальный выход волокнистой фракции с наибольшим содержанием волокон длиной 12–18 мм. Выявлено, что механическая классификация не позволяет полностью разделить продукты переработки стеклопластиковых отходов на волокна и частицы полимерной матрицы. При механической классификации на ситах с размером ячейки 0,045–0,5 мм наблюдается образование «комков», препятствующих прохождению волокон и частиц через поверхность сита.
Стеклопластиковые отходы, механическая переработка, селективное измельчение, ударно-центробежная мельница, классификация, волокно, матрица
Короткий адрес: https://sciup.org/142244455
IDR: 142244455 | DOI: 10.24412/2079-7958-2025-1-77-89
Текст научной статьи Способ переработки отходов производства стеклопластиков
DOI:
В настоящее время, перспективным направлением развития технологии и техники во всем мире и в Республике Беларуси в частности является замена классических конструкционных металлических сплавов на полимерные композиционные материалы (ПКМ) (К.А. Токменинов, 2018). Наиболее широко распространенным среди ПКМ являются стеклопластики, представляющие собой композит на основе стеклянных армирующих волокон различного типа и полимерного связующего. В качестве связующего при этом используются в основном эпоксидные или полиамидные смолы с отвердителем.
По статистическим данным, объем мирового рынка композиционных материалов из стеклопластика в 2023 году оценивается в 47,61 млрд долларов США, а к концу 2030 года прогнозируется его рост до 79,09 млрд долларов США (М.С. Дориомедов, 2020).
В Республике Беларусь, исходные компоненты для производства изделий из стеклопластика, и собственно стеклопластики производятся на ряде предприятий, объединенных в инновационно-промышленный композитный кластер объединяющий порядка 11 организаций. Крупнейшим предприятием является ОАО «Полоцк-стекловолокно», мощность которого по производству стекловолокна и изделий на его основе составляет порядка 57 тыс. тонн в год.
Серьезной проблемой объемного производства и применения полимерных композиционных материалов, в частности наиболее распространенных стеклопластиков, является их утилизация (Е.Н. Каблов, 2008). В настоящее время решение проблемы утилизации ПКМ – приоритетная материаловедческая задача, поскольку создание и внедрение новых материалов непременно приводит к образованию отходов. С учетом специфических свойств ПКМ таких как стойкость к внешним воздействиям окружающей среды, проблема их утилизации носит, прежде всего, экологический характер (К.И. Донецкий, 2014; Ф.С. Власенко, 2013).
Кроме того, государственное законодательство многих стран формирует поведение общества стимулируя темпы переработки отходов и сводя к минимуму использование свалок (полигонов для захоронения твердых отходов). Директива Европейского Союза 2018/850 о захоронении отходов ограничивает количество твердых отходов, вывозимых на полигоны, до 10 % к 2035 г.
Основной путь решения проблемы утилизации ПКМ – это их вторичная переработка. Положительной стороной вторичной переработки является то, что получается дополнительное количество полезных продуктов для различных отраслей промышленности и не происходит загрязнения окружающей среды. По этим причинам вторичная переработка является не только экономически целесообразным, но и экологически предпочтительным решением проблемы утилизации композиционных материалов в условиях современного законодательства (А.В. Петров, 2015; Н.Р. Прокопчук, 2014).
Рассматривая состояние данного вопроса за рубежом, можно утверждать, наибольших успехов в данном вопросе достигли Германия, Великобритания, США, Бельгия, Франция, Дания, которые выполняют переработку ПКМ в промышленных масштабах (S. Katsuji, 2014; А. Kwame, 2017).
Переработка армированных композиционных материалов методом пиролиза находит наибольшее распространение для пластиков, армированных углеродным волокном. Например, с помощью данной технологии, компания CFK Valley Stade Recycling GmbH & Co KG (Герма- ния) ежегодно перерабатывает около 3500 тонн отходов, тем самым производится около 1000 тонн переработанных волокон. К числу компаний, использующих пиролиз для переработки армированных пластиков можно также отнести Materials Innovation Technologies MIT-RCF (США), Japan Carbon Fiber Manufacturers Association (Япония), Firebird Advanced Materials (США), Formoso Technologies Group (Испания) и т. д. (C.V. Amaech, 2020; S. Job, 2014; G. Oliveux, 2015).
Переработка стеклопластика в основном заключается в механическом измельчении композиционного материала в молотковых мельницах или аналогичных устройствах, с последующей классификацией на фракции. Данная технология используется на многих предприятиях, таких как Filon и Hambleside Danelaw (Британия), Mixt Composites Recyclables (Франция), Reprocover (Бельгия), Eco-Wolf (США), Extreme EcoSolutions (Нидерланды) и т.д (G. Oliveux, 2015; А. Jacob, 2011; S. J. Pickering, 2006).
Механический метод переработки стеклопластика имеет ряд преимуществ: сравнительная простота технологического оформления, применимость для практически любых полимерных композиционных материалов, одновременная переработка армирующих волокон и полимерного связующего, отсутствие вредных выбросов и испарений. Однако, данный метод не лишен недостатков, основным из которых является снижение качества волокон после переработки.
В связи с вышеизложенным цель работы заключается в изучении фракционного состава продуктов переработки отходов стеклопластика в зависимости от режимов работы измельчителя. В статье рассмотрен перспективный подход в области переработки отходов стеклопластика, позволяющий получать вторичный волокнистый материал.
Методы и средства исследований
Механической переработке подвергались отходы производства стеклопластиковых изделий образующиеся на предприятии ООО «Полоцк-Стекловолокно». Отходы представляли собой куски стеклопластика, состоящие в основном из армирующего компонента в виде хаотически расположенного волокна и связующего на основе полиэфирной смолы Депол С-180 ПТ (60–63 %). Размер исходных стеклопластиковых отходов составлял 240×90×(2–3) мм (рисунок 1).
Перед проведением экспериментальных исследований исходный материал подвергался первоначаль-
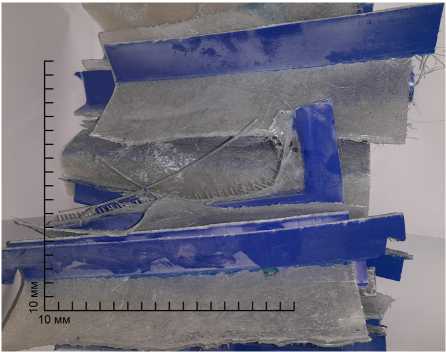
Рисунок 1 – Исходные стеклопластиковые отходы Figure 1 – Original fiberglass waste ной ручной резке до более мелких кусков с размерами 30×30×(2–3) мм, что определялось межлопаточным расстоянием в роторе ударно-центробежной мельницы.
Исследования осуществлялись на разработанной лабораторной экспериментальной установке исследования процесса механической переработки отходов стеклопластика, представленной на рисунке 2.
Экспериментальная установка состоит из питателя 1, ударно-центробежной мельницы 2 (Е.Г. Федаро-вич, 2023), частотного преобразователя 3. Посредствам трубопровода 4, к ударно-центробежной мельнице 2 подсоединен циклон 5 с емкостью сбора продуктов измельчения 6. Циклон 5, при помощи трубопровода 7, подсоединен к рукавному фильтру 8 с емкостью сбора пыли 9. Для проведения ситового анализа продуктов измельчения в установке имеется ситовой анализатор 10.
Исследования проводились следующим образом. Исходный материал, в виде кусков стеклопластика с размерами 30×30×(2–3) мм посредствам питателя 1 с постоянным массовым расходом (100 кг/ч) подавался в загрузочный патрубок ударно-центробежной мельницы 2. При помощи частотного преобразователя 3 в ударно-центробежной мельнице 2 задавалась частота вращения рабочего органа мельницы (ротора) n , об/мин: 1200, 1800, 2100, 2400, 2700 и 3000. Далее, полученные продукты измельчения совместно с воздушным потоком направлялись по трубопроводу 4 в циклон 5, где происходило их разделение. Извлеченные из воздушного по-
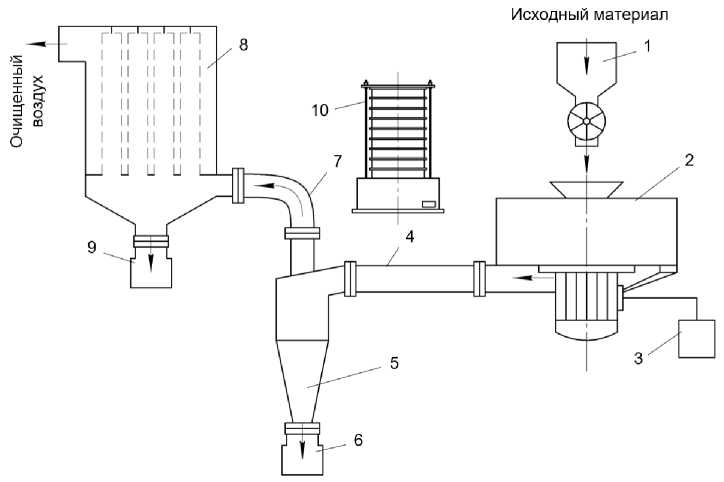
Рисунок 2 – Экспериментальная установка исследования процесса механической переработки отходов стеклопластика:
1 – питатель; 2 – ударно-центробежная мельница; 3 – частотный преобразователь; 4, 7 – трубопроводы; 5 – циклон; 6 – емкость сбора продуктов измельчения; 8 – рукавный фильтр;
9 – емкость сбора пыли; 10 – ситовой анализатор
Figure 2 – Experimental setup for studying the process of mechanical recycling of fiberglass waste:
1 – feeder; 2 – impact-centrifugal mill; 3 – frequency converter; 4, 7 – pipelines; 5 – cyclone;
6 – ground product collection tank; 8 – bag filter; 9 – dust collection tank; 10 – sieve shaker
тока продукты измельчения поступали в емкость 6. Воздушный поток, из циклона 5, по трубопроводу 7 поступал на дополнительную стадию фильтрования в рукавный фильтр 8, после чего выделенные мелкие частицы поступали в емкость 9. Полученные продукты измельчения отходов стеклопластика, из емкостей 6 и 9 с целью рассева на фракции, помещали в вибрационный ситовой анализатор 10 марки Retsch AS 200 с комплектом сит, мм: 4; 2; 1; 0,5; 0,25; 0,125; 0,063.
Микроструктуру исследуемого материала изучали с использованием микроскопа Микромед МЕТ с увеличением 50–500 крат., в комплекте с видеоокуляром ToupCam 5.1 MP.
Результаты исследований
В результате селективного измельчения стеклопластиковых отходов в экспериментальной установке, получен полидисперстный материал, представляющий собой систему, состоящую из кусков недоизмельченного стеклопластика, пучков стекловолокна, с размером волокон 7–26 мм, измельченной смолы и гелькоута (рисунок 3).
После проведения ситового анализа, полученные продукты условно можно разделить на три составляющие:
– недоизмельченные куски стеклопластика;
– волокнистая фракция;
– мелкодисперсный порошок.
Недоизмельченные куски стеклопластика, впоследствии нуждаются в повторном селективном измельчении. Стоит отметить форму кусков стеклопластика, которая представляет собой эллипс. Представленная форма недоизмельченных стеклопластиковых отходов говорит о том, что основным механизмом разрушения стеклопластика в ударно-центробежной мельнице заключается в постепенном разрушении наружных кромок хруп-
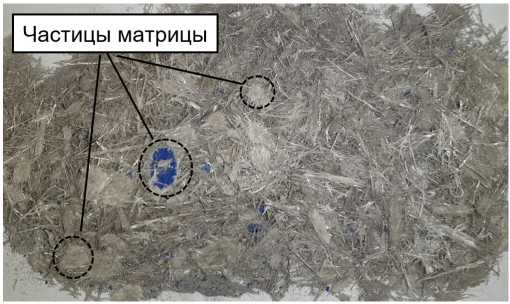
Рисунок 3 – Результат механической обработки отходов стеклопластика при частоте вращения ротора 2100 об/мин
Figure 3 – Result of mechanical recycling of fiberglass waste at a rotor rotational speed of 2100 rpm кой термореактивной смолы с каждым последующим ударом об отбойную поверхность с высвобождением волокон. При этом, разрушение материала происходит за счет одновременного действия различных механизмов. Во-первых, в момент удара внешних кромок куска стеклопластика об отбойную поверхность мельницы, в материале образуются поля динамических деформаций – растягивающих и сжимающих нагрузок, из-за чего происходит растрескивание материала вдоль волокон по границе раздела фаз, приводящее к их высвобождению. Ввиду того, что материал армирован хаотически расположенными короткими волокнами, растрескивание имеет локальный характер. Даже в случае разрушения волокна, повреждение останется локализованным, так как дальнейшему распространению растрескивания будут сопротивляться волокна, расположенные под различным углом (M.E. Hossain, 2014; М.В. Жихарев, 2019). Во-вторых, как известно, волокнистые композиционные материалы весьма чувствительны к усталостному разрушению. За счет воздействия в ударно-центробежной мельнице на стеклопластик многократных ударных нагрузок, в материале, начиная с наружных кромок происходит накопление повреждений, в менее прочном и более хрупком чем волокна связующем. Далее, повреждения, представленные в основном зародышевыми трещинами, сливаются и образуются магистральные трещины, приводящие к локальным расслоениям (А.Г. Иванов, 1991). При этом, необходимо учитывать, что исходный подаваемый в мельницу материал уже имеет ряд макроскопических дефектов в местах его предварительного резания до более мелких размеров.
Волокнистая фракция представляет собой остаток на сите 4 мм. Состоит преимущественно из волокон длиной от 5 до 25 мм.
Мелкодисперсный порошок представляет собой фракцию прошедшую через сито 4 мм, состоящую из измельченного стеколоволокна, частиц матрицы и гелькоута.
Исследуя влияние частоты вращения рабочего органа ударно-центробежной мельницы на эффективность измельчения стеклопластика, оцениваемую количеством недоимезльченного материала D , %, установлено, что увеличение частоты вращения ротора способствует более полному измельчению отходов стеклопластика. Так, при n = 1200 об/мин, количество недоизмельчен-ного материала составляет 40,0 %, при 2100 об/мин – 15,0 %, 3000 об/мин соответственно 1,5 %. Выполнена аппроксимация результатов экспериментов в виде уравнения логарифмической линии. Результаты этой аппроксимации представлены на рисунке 4. Отклонения результатов экспериментов от аппроксимационной зависимости не превышают 11 %.
Уменьшение количества недоизмельченного стеклопластика с увеличением частоты вращения ротора, очевидно связано с ростом кинетической энергии сообщаемой измельчаемому материалу на стадии его разгона.
40 г *
О о 35 -X
X
? 30 -
Л ^'ь q °ч
I Q 25 Г '• у =-42,751п(х) + 343,65
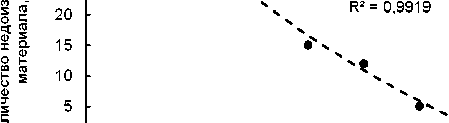
900 1200 1500 1800 2100 2400 2700 3000
Частота вращения ротора мельницы, п, об/мин
Рисунок 4 – Влияние частоты вращения ротора на количество недоизмельченного материала
Figure 4 – Effect of rotor rotational speed on undersized material content
Наличие у материала высокой кинетической энергии в момент удара приводит к большему образованию дефектных структур в виде растрескивания и микротрещин. Кроме того, увеличивается количество контактов измельчаемого материала с отбойной поверхностью мельницы.
На рисунке 5 представлена зависимость влияния частоты вращения ротора мельницы на количество волокнистой фракции, d , масс. %.
При n равном 1200–2100 об/мин, наблюдается наименьшее количество волокнистой фракции в продуктах селективного измельчения, что связано с большим количеством недоизмельченного материала, как это было показано на рисунке 6, и составило при 1200 об/мин – 2,26 масс. %, при 1800 – 15,7 масс. %, 2100 – 21,54 масс. % соответственно. Получаемая таким образом волокнистая фракция представляет собой преимущественно пучки разнонаправленных и однонаправленных волокон, скрепленных между собой недоизмельченной матрицей (рисунок 6 а, б).
Увеличение частоты вращения рабочего органа мельницы до 2400 об/мин позволяет существенно уве-
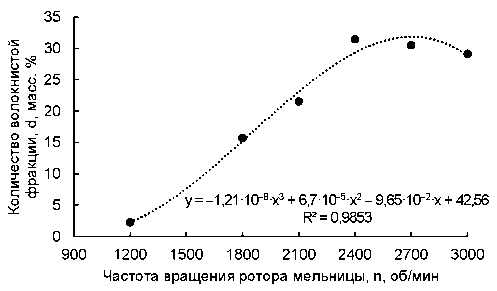
Рисунок 5 – Влияние частоты вращения ротора мельницы на количество волокнистой фракции Figure 5 – Effect of rotor rotational speed on fibrous fraction yield личить выход волокнистой фракции при селективном измельчении. Это обусловлено повышением энергии удара стеклопластика об отбойную поверхность в рабочей камере ударно-центробежной мельницы. Энергии удара достаточно для хрупкого разрушения матричного
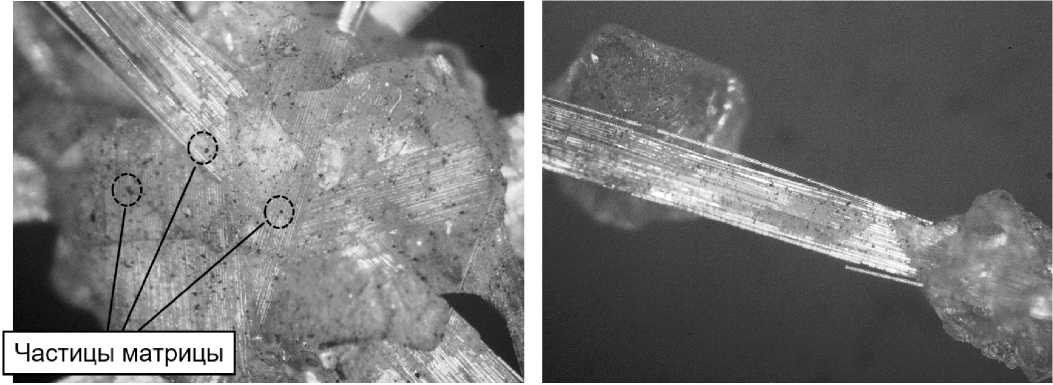
а б (b)
Рисунок 6 – Снимки (50 крат.) волокнистой фракции, полученной при n = 1200 об/мин: а – пучок разнонаправленных волокон, скрепленных матрицей;
б – пучок однонаправленных волокон, скрепленных матрицей
Figure 6 – Photos (50x) of fibrous fraction produced at n = 1200 rpm: a – a bundle of multidirectional fibers bonded with polymer matryx; b – a bundle of unidirectional fibers bonded with polymer matryx
полимера, но не достаточна для разрушения волокна. Следовательно, чем больше энергия удара в мельнице, тем больше выделяется волокон, при условии, что не происходит разрушение волокон
На рисунке 7 а, б представлены снимки волокнистой фракции полученной при частоте вращения ротора мельницы 2400 об/мин.
Как видно из представленных снимков, в сравнении с ранее полученным результатами, при n = 2400 об/мин в волокнистой фракции наблюдаются отдельные волокна (рисунок 7 а). Присутствующие в меньшем количестве пучки однонаправленных волокон (рисунок 7 б) имеют на поверхности значительно меньшее количество включений матрицы.
Помимо включений матрицы, которые скрепляют волокна в пучки, на самих волокнах также имеются микроскопические частицы матрицы, как это видно на рисунках 6 а и 7 а. Данные включения, при использовании вторичных волокон для производства новых материалов, могут существенно влиять на свойства готовых изделий. С одной стороны, они снижают качество поверхности волокон, что приводит к локальной концентрации напряжений и таким образом к снижению прочности получаемых на их основе изделий. С другой стороны, шероховатость поверхности волокон, за счет частиц эпоксидной смолы, может обеспечить дополнительное взаимодействие вторичных волокон с новой матрицей. Например, в работе (A. Rahimizadeh, 2019), направленной на использование вторичных волокон в качестве исходного сырья для получения нитей 3D-печати, наличие частиц эпоксидной смолы на поверхности вторичных волокон позволяет увеличить прочность межфазного взаимодействия между волокнами и матрицей на основе полимера молочной кислоты (ПМК). Изделия на основе вторичного волокна имели прочности на разрыв на 18–19 % выше, чем у образцов, полученных из первичных волокон. Улучшение прочностных свойств образцов объясняется в первую очередь улучшением механического и химического взаимодействия между матрицей и волокном, за счет шероховатости поверхности волокон, а также образованием водородных связей между частицами эпоксидной смолы и ПМК.
Определение длины получаемых волокон осуществляли по методике, описанной в ГОСТ 10213.4. Результаты проведенных исследований определения длины волокон представлены на рисунке 8 в виде гистограмм.
На представленных гистограммах видно, что волокнистый материал имеет широкий полидисперсный
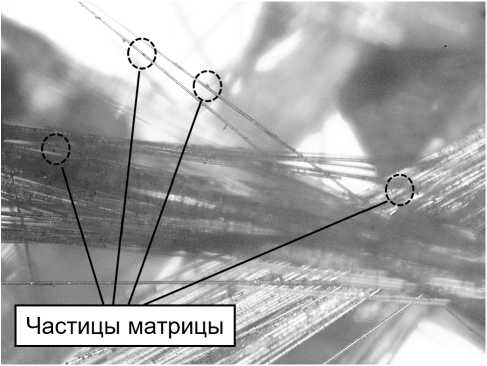
а
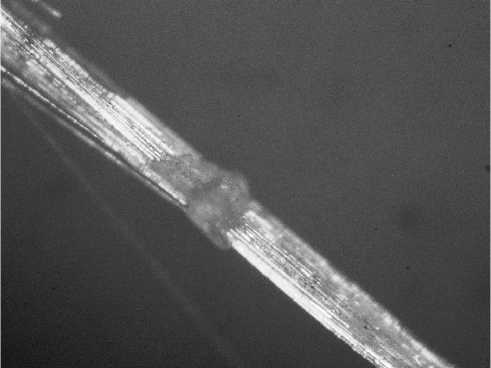
б (b)
Рисунок 7 – Снимки (50 крат.) волокнистой фракции, полученной при n = 2400 об/мин: а – волокнистая фракция; б – пучок однонаправленных волокон, скрепленных матрицей Figure 7 – Photos (50x) of fiberglass produced at n = 2400 rpm:
a – fiberglass fraction; b – bundle of unidirectional fibers bonded with polymer matrix
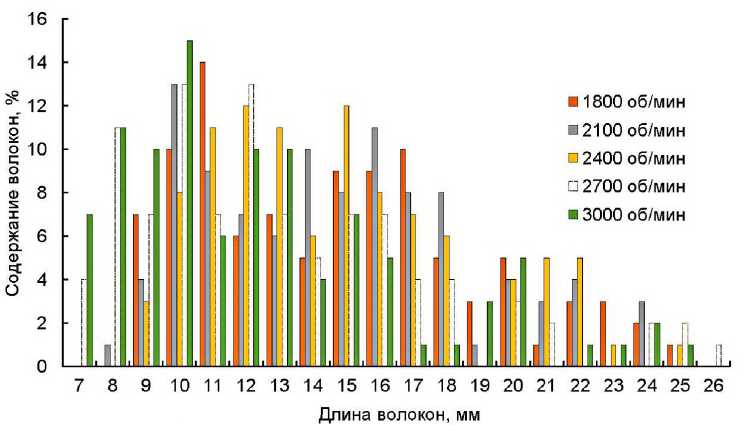
Рисунок 8 – Состав волокнистой фракции в зависимости от длины волокон Figure 8 – Size distribution of the fibrous fraction by fiber length
состав в зависимости от длины волокна, которая изменяется в диапазоне от 7 до 26 мм. При этом, наиболее часто встречаемыми в продуктах измельчения стеклопластика являются волокна с длиной 8–18 мм. На рисунке 9 представлена аппроксимация выше представленных гистограмм, в полиномиальные зависимости 5 порядка с величиной достоверности аппроксимации 0,65–0,8.
На преобразованных графических зависимостях отчетливо наблюдается увеличения количества более
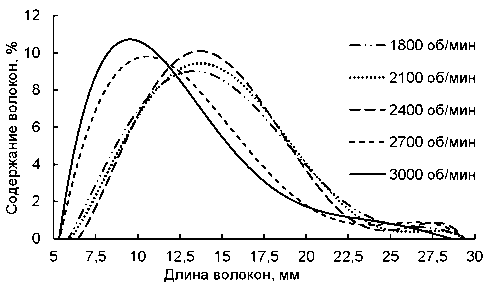
Рисунок 9 – Содержание в волокнистой фракции волокон различной длины
Figure 9 – Proportion of fibers by length category in the fibrous fraction мелких фракций (до 10 мм) при n = 2700–3000 об/мин, что связано с увеличением энергии удара материала об отбойную поверхность мельницы выше энергии разрушения волокна. При n равной 2400 об/мин наблюдается наибольшее количество более длинных волокон (12–18 мм).
Как известно, длина волокна существенно влияет на его армирующий эффект в композиционном материале. Чем меньше длина дискретного волокна, тем меньше доля эффективно работающего волокна. Поскольку короткое волокно не будет работать в полной мере, армирующий эффект от введения такого волокна будет снижаться. Таким образом, при армировании матрицы волокном армирующий эффект должен быть тем выше, чем больше длина волокон. Следовательно, при использовании волокнистой фракции в качестве армирующего компонента для производства композиционных материалов ее эффективность будет тем выше, чем больше в ней длинных волокон. Согласно некоторым экспериментальным исследованиям, оптимальной длиной стекловолокна, позволяющей обеспечить наилучший армирующий эффект составляет 15–20 мм (С.Н. Колдаева, 2005).
В результате, предпочтительной частотой вращения ротора ударно-центробежной мельницы, для получения волокнистой фракции с наибольшим количеством содержащихся в ней длинных волокон, является 2400 об/мин.
Необходимо отметить, что в процессе механической классификации волокнистого материала, на сите 4 мм, волокна скрепляются между собой и образуют на поверхности сита сплошной уплотненный «мат», в котором задерживаются частицы полимерной матрицы, тем самым снижая общее количество стекловолокна в волокнистой фракции. Также, как это было показано на рисунках 8 и 9, в полученной фракции присутствуют волокна различной длины от 5 до 30 мм.
В процессе классификации продуктов измельчения на ситах с отверстиями меньшего размера, происходит образование «пушистых комков» (рисунок 10), которые содержат в себе мелкие волокна и частицы измельченной полимерной смолы, которые в противном случае были бы классифицированы по последующим ситам с меньшим диаметром отверстий. По мере того, как они накапливаются на поверхности сит, они предотвращают дальнейшее прохождение волокон и частиц через поверхность сита. При увеличении частоты вращения ротора до 2700 и 3000 об/мин наблюдается увеличение их количества на ситах с размером ячейки 0,045–0,5 мм, что подтверждает ранее сделанные выводы об увеличении количества более мелкого измельченного волокна.
На рисунке 11 представлен снимок поверхности образующихся «комков» при механической классификации продуктов селективного измельчения при n = 2400 об/мин.
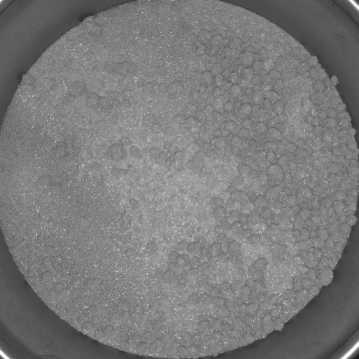
а
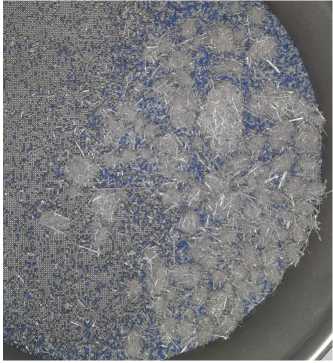
б (b)
Рисунок 10 – Образование «пушистых комков» при классификации продуктов измельчения стеклопластика: а – остаток на сите с размером ячейки 0,063 мм; б – остаток на сите с размером ячейки 0,5 мм
Figure 10 – Formation of “fluffy agglomerates” during mechanical classification of fiberglass ground products:
a – residue on a sieve with a mesh size of 0.063 mm; b – residue on a sieve with a mesh size of 0.5 mm
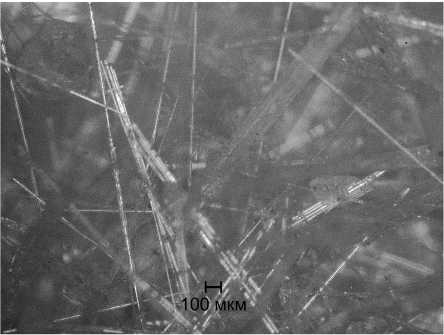
Рисунок 11 – Снимок (100 крат.) поверхности «комков» Figure 11 – Photo (100x) of the surface morphology of agglomerates
Как видно из представленного снимка, «комки» представляют собой преимущественно переплетенные между собой хаотичным образом волокна.
Полученные результаты механической классификации согласуются с исследованиями зарубежных авторов в области переработки волокнистых материалов. Так, авторами Jutte, R.B. и W.D. Graham (P. Joakim, 1994; R.B. Jutte, 1991) также отмечается, что форма и характер волокнистого материала не походит для классификации просеиванием через сито, так как волокна слипаются и образуют «пушистые комки», однако ввиду отсутствия более совершенного оборудования, классификацию вторичных материалов ПКМ до настоящего времени производят на ситах.
В результате, основными дальнейшими целями развития технологии переработки стеклопластиковых отходов будет являться совершенствование способов классификации продуктов селективного измельчения.
Выводы
В результате проведения экспериментальных исследований установлено, что метод механической переработки с использованием ударно-центробежной мельницы позволяет выделить из стеклопластиковых отходов волокнистую фракцию, которая в перспективе может быть использована в качестве вторичного материала в новых изделиях.
По результатам механической классификации продуктов переработки стеклопластиковых отходов установлено, что частота вращения рабочего органа мельницы является определяющим фактором, влияющим на выход волокнистой фракции и ее состав, в зависимости от длины волокна. Экспериментальным путем определена и обоснована предпочтительная частота вращения ротора – 2400 об/мин, позволяющая получать материал с наибольшим содержанием волокон длиной 12–18 мм и с наименьшим количеством включений матрицы.
Выявлено, что механическая классификация продуктов измельчения стеклопластика имеет ряд недостатков: отсутствие возможности получение волокнистой фракции содержащую волокна определенной длины, наличие в волокнистой фракции частиц матрицы, образование на поверхности сит «комков». Упомянутые недостатки свидетельствуют о необходимости проведения ряда дополнительных исследований в области определения более эффективного способа классификации волокнистых материалов.