Способы достижения надежности работы гидроцилиндров высокого давления буровых установок
Автор: Кудряшов Е.А., Яцун Е.И., Павлов Е.В., Алтухов А.Ю., Лунин Д.Ю.
Журнал: Известия Самарского научного центра Российской академии наук @izvestiya-ssc
Рубрика: Машиностроение
Статья в выпуске: 1-2 т.12, 2010 года.
Бесплатный доступ
В статье описывается обеспечение стабильного качества обработки поверхностей внутренних канавок втулок гидроцилиндров без изменения конструкции деталей гидроцилиндров.
Гидроцилиндры, буровые установки, надежность
Короткий адрес: https://sciup.org/148198951
IDR: 148198951
Текст научной статьи Способы достижения надежности работы гидроцилиндров высокого давления буровых установок
Алтухов Александр, аспирант
Лунин Дмитрий, аспирант
мер, включающих разработку новых технологических процессов изготовления втулок; применение композитных материалов в качестве материала заготовки; применение новых типов уплотнительных колец.
На ОАО «Геомаш» была поставлена задача
предложить мероприятия по устранению утечек, не изменяя конструкцию деталей гидроцилиндров. Поэтому в статье приводятся только предложения по обеспечению стабильного качества обработки поверхностей внутренних канавок втулок гидроцилиндров. Трение и износ уплотнительного узла в значительной степени зависит от шероховатости поверхностей деталей, по которым скользят уплотнительные элементы. Увеличение высоты микронеровностей уплотняемой поверхности сопровождается ростом сил
трения, причем с повышением давления эта зависимость проявляется более резко. Кроме того, силы трения зависят от формы и однородности микрорельефа. Увеличение радиусов закруглений вершин микронеровностей значительно уменьшает силы трения и износ уплотнений. Для соединений со знакопеременным давлением жидкости поверхности канавки и в особенности ее дно должны обрабатываться по требованиям,
предъявляемым к подвижным соединениям, т.е. с шероховатостью R a =1,25 мкм, что вызывает определенные трудности в обеспечении этого требования при обработке канавок лезвийным инструментом. Применение для окончательной доводки поверхностей канавок абразивной обработки, как показывает опыт, нежелательно, так как абразив внедряется в микропоры поверхностей и служит впоследствии причиной износа уплотнений.
Герметичность соединений определяет их способность удерживать утечку газа или жидкости [1]. Из закона Дарси для фильтрационного потока
утечка, характеризующая герметичность, может
быть определена по формуле:
Q
Σ =
πDΔpHk
µ′l
′′
Известия Самарского научного центра Российской академии наук, т. 12, №1(2), 2010
где μ′ – динамический коэффициент вязкости уплотняемой среды; l и D – размеры соединения, мм; ∆p – перепад давления, МПа; H – толщина пористого слоя под нагрузкой, мм; k″ – коэффи циент проницаемости.
Q = 0 0066 D R PU { 0,5 [ ( H maxi + H m„2 ) + ( ^ , . + W z 2 ) + 6 ( R a . + R a 2 ) ] - У ск. }
1 , ^l , (2)
где U – константа Кармана; y ck – контактное сближение деталей при скольжении; R a – среднее арифметическое отклонение профиля, мкм; W z – параметр волнистости, мкм; H max – максимальное макроотклонение, мкм.
Анализ полученной формулы показывает, что герметичность соединений наряду с геометрией уплотнения, физико-механическими свойствами его материала и факторами внешнего воздействия также зависит от состояния контактирующих поверхностей: параметров шероховатости Ra, волнистости Wz и макроотклонения Hmax [табл. 1, 2].
Таблица 1. Возможности методов обработки поверхностей вращения в обеспечении качества обработанной поверхности
Метод обработки |
Параметры состояния поверхностного слоя |
|||||
обработка наружных поверхностей вращения |
обработка внутренних поверхностей вращения |
|||||
R a , мкм |
W z , мкм |
H max , мкм |
R a , мкм |
W z , мкм |
H max , мкм |
|
точение |
0,8-2,5 |
1,6-4,0 |
40-100 |
0,8-2,0 |
2,5-6,25 |
20-80 |
шлифование |
0,2-1,25 |
0,5-4,0 |
10-40 |
0,32-1,60 |
1,25-6,25 |
10-40 |
раскатывание |
0,05-1,0 |
0,4-2,5 |
6-40 |
0,05-0,32 |
1,6-5,0 |
5-40 |
Графики зависимости герметичности соединения, характеризуемой утечкой Q Σ , от шероховатости R a при различных методах обработки внутренних поверхностей вращения представлены на рис. 1.
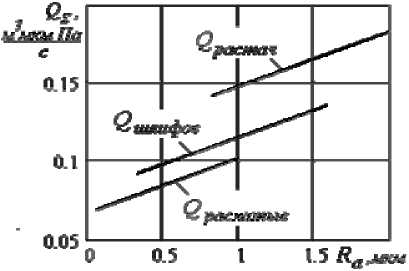
Рис. 1. Графики зависимости утечки Q Σ от шероховатости поверхности R a при различных методах обработки внутренних поверхностей
Количественная оценка повышения герметичности соединений при различных методах обработки может быть осуществлена на основании следующего коэффициента:
К = Q^ герм
Q 2 2
,
где Q Σ1 и Q Σ2 – значения утечки для двух сравниваемых методов обработки.
Графики зависимости коэффициента снижения утечки Кгерм от шероховатости Ra при различных методах обработки – шлифовании и раскатывании в сравнении с растачиванием представлены на рис. 2.
Таким образом, на основе сравнительного анализа возможностей различных методов обработки по обеспечению износостойкости и герметичности деталей типа тела вращения установлено, что износостойкость может быть повышена в 2-5 раз, а герметичность в 1,3-1,7 раза.
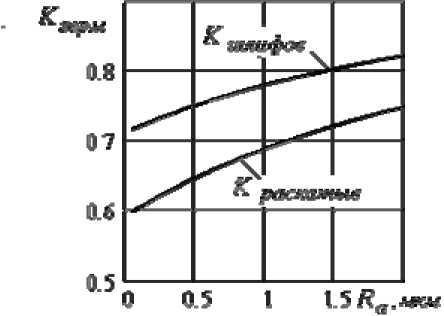
Рис. 2. Графики зависимости коэффициента снижения утечки К герм от шероховатости поверхности R a
Все факторы, обусловливающие шероховатость обработанной поверхности резанием, можно объединить в 3 основные группы: причины, связанные с геометрией процесса резания; пластической и упругой деформациями обрабатываемого материала; возникновением вибраций режущего инструмента [3]. Подбор резца с
СМП для обработки канавок проведен по каталогу представительства Mitsubishi в России [4]. Предложено производить расточку всех типов канавок специальным расточным канавочным резцом фирмы Mitsubishi, с обозначением: FCDG4132L4M, пластина DGM40CT шириной 4 мм, материал ВК8.
Чистовая расточка канавок во избежание образование ступенек (рис. 3, а) осуществляется по схеме (см. рис.3, б) с использованием продольной подачи для зачистки дна канавки. При этом в процессе резания участвуют главная и вспомогательные режущие кромки резца.
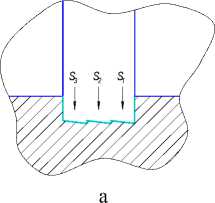
Рис. 3. Дно канавки: а – при обработке с поперечной подачей; б – при обработке с продольной подачей
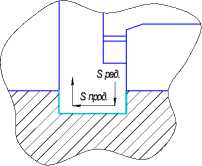
Результаты промышленных испытаний показали, что добиться стабильной шероховатости поверхности дна канавок под уплотнения обработкой резанием не удалось. Разброс шероховатости составил R а = 0,68-2,8 мкм из-за влияния нестабильности структуры обрабатываемого материала. Предложено провести обработку методами поверхностного пластического деформирования (ППД) – раскатывание. Произведен расчет на жёсткость демпфирующей части рас-катника (рис. 4).
По результатам работы проведены промышленные испытания обработки канавок раскатыванием с предложенными режимами обработки, в результате которых метод обработки канавок раскатыванием признан обеспечивающим стабильность качества поверхности по параметру шероховатости и был внедрен в производство.
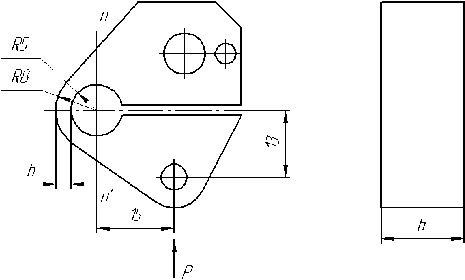
а)
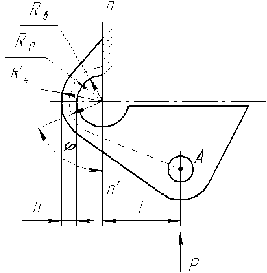
б)
Рис. 4. Демпфирующая головка раскатника (а) и схема нагружения (б)
Список литературы Способы достижения надежности работы гидроцилиндров высокого давления буровых установок
- Башта, Т.М. Машиностроительная гидравлика. Справочное пособие. -М.: Машиностроение, 1971. -672 с.
- Суслов, А.Г. Качество поверхностного слоя деталей машин. -М.: Машиностроение, 2000. -300 с.
- Маталин, А.А. Технология машиностроения. -Л.: Машиностроение, 1985. -496 с.
- Каталог Mitsibishi Carbide (Metal cutting carbide tools) 2002-2003.