Способы вибродиагностирования роторных механизмов
Автор: Грунтович Н.В., Петров И.В.
Журнал: Агротехника и энергообеспечение @agrotech-orel
Рубрика: Научно-техническое обеспечение процессов и производств в АПК и промышленности
Статья в выпуске: 4 (8), 2015 года.
Бесплатный доступ
В статье изложены достоинства и недостатки основных способов виброконтроля электрических двигателей и насосов. Указаны причины низкой достоверности диагностирования. Приведены формулы расчета информативных частот вибрации подшипников качения. Изложен принцип построения диагностической модели. Показано влияние принятых единиц измерения на достоверность и наглядность результатов измерений. Приведен пример влияния качества подшипников качения на вибрацию и долговечность электрических двигателей и насосов.
Вибродиагностирование, подшипник качения, электрический двигатель, насос, общий уровень вибрации, ударные импульсы, способ диагностирования по огибающей, прямой спектр, модель диагностическая, достоверность результатов
Короткий адрес: https://sciup.org/14770108
IDR: 14770108
Текст научной статьи Способы вибродиагностирования роторных механизмов
-
- низкие знания у специалистов физических основ работы объектов диагностирования;
-
- многие могут измерять, но не умеют анализировать и делать правильные заключения;
-
- незнание помех при диагностировании (систематические погрешности);
-
- метрологические характеристики используемых приборов и методы обработки не позволяют обеспечить высокую достоверность;
-
- нормативные документы по СТОиР разработаны без учета достижений науки и техники. (ТКП-181-2009).
Указанные факторы вызывают ошибки первого и второго рода. Ошибки первого рода - это пропуск дефекта. Они могут в отдельных случаях привести к остановке технологической линии, тогда потери могут составить до нескольких миллионов долларов. Эти потери обусловлены, во-первых, недоотпуском продукции, во-вторых, затратами ТЭР на разогрев и запуск технологической линии. Ошибки второго рода - это когда исправный механизм признается неисправным. В этом случае потери будут меньше и определяются затратами на необоснованный ремонт. С другой стороны известны случаи, когда при диагностировании исправный механизм выводился в ремонт. Если речь идет о замене подшипника качения, то нет никакой гарантии, что будет поставлен хороший подшипник. При применении подшипников качения белорусских, российских, украинских, китайских производителей велика вероятность того, что будет поставлен подшипник низкого качества. К заводским дефектам подшипников качения следует отнести: некруглость тел качения; овальность внутреннего кольца; трехвыпуклость внутреннего кольца; неравномерность зазоров между телами качения и кольцами (разные диаметры тел качения); повышенная волнистость колец; раковины на кольцах и телах качения.
Таблица 1 – Результаты контроля подшипников качения специалистами нефтеперерабатывающего предприятия
Качество |
Производитель Китай, % |
Производитель Россия |
||
VBF |
MPZ |
SPZ |
||
Годен |
11 |
21 |
4 |
51 |
Негоден |
44 |
24 |
16 |
11 |
Ограниченно годен |
45 |
55 |
80 |
38 |
По нашему мнению, здесь две основные причины: износ станочного оборудования на подшипниковых заводах, а в некоторых случаях, это низкое качество подшипниковой стали.
Поэтому следует уделять большое внимание как способу вибродиагностирования, так и методике обработки сигналов.
Постановка задачи. На предприятиях применяются следующие способы вибродиагностирования.
-
1. Определение степени износа по общему уровню вибрации в диапазоне 10-1000 Гц, единица измерения – мм/с.
-
2. Выявление наличия дефектов в подшипниках качения и редукторах на основе ударных импульсов, единица измерения – Дб.
-
3. Диагностирование подшипников качения и редукторов на основе анализа «огибающей», единицы измерения – мм/с; м/с2 (Дб).
-
4. Диагностирование подшипников качения, магнитной системы электрических машин, трансформаторов, насосов, редукторов по прямому спектру вибрации в диапазоне 5-10000 Гц, единицы измерения – мм/с, м/с2 (Дб).
Результаты исследований.
Для первых двух способов свойственна наибольшая погрешность по целому ряду причин.
Во-первых, не известны дискретные частоты вибрации конкретного дефекта, так как эти частоты вибрации вообще не вычисляются.
Во-вторых, при диагностировании по общему уровню в диапазоне 10-1000 Гц пропускаются дефекты, которые проявляются в диапазоне частот 1-10 Гц и более 1000 Гц. При диагностировании по общему уровню такие дефекты как износ сепаратора и внутреннего кольца, обрыв фазы статора могут остаться не выявленными. Разрушение сепаратора и внутреннего кольца приводит, как правило, к заклиниванию ротора и, как следствие, повреждение статорной обмотки и железа статора. Износ рабочих колес центробежного насоса вызывает вибрацию на первом этапе эксплуатации в диапазоне частот 2000-3000 Гц и нарушение балансировки ротора.
В-третьих, при диагностировании подшипников качения по ударным импульсам сигналы регистрируются в диапазоне 20-35 кГц. Это уже область акустической эмиссии. Ударные импульсы присутствуют всегда как у новых подшипников качения (китайских, украинских, белорусских), так и при начальной стадии износа – питтинг.
Большое значение для достоверности диагностирования имеет частотный диапазон вибрации исследуемого объекта и единица измерения. На рисунке 1 приведены спектры вибрации электродвигателя в одной и той же реперной точке. На рисунке 1, а представлены спектры вибрации двигателя до 4000 Гц, единицы измерения амплитуды- виброскорость (мм/с). На рисунке выделяются три амплитуды на дискретных частотах: 50Гц, 100 Гц и 1920 Гц. Амплитуда на 50 Гц – вибрация на частоте вращения ротора и помехи сети; 100 Гц – овальность внутреннего кольца; 1920 Гц – ослабление расклиновки обмотки статора. Из рисунков 1,б и 1, в видно, что виброускорение, как единица измерения, является более информативной. Состояние смазки вполне удовлетворительное (частота более 2000 Гц); уровень белого шума после 2000 Гц равномерный. В подшипнике качения кроме овальности внутреннего кольца другие дефекты не выявляются. Хочется обратить внимание, что при измерении вибрации в диапазоне до 1000 Гц всегда остаются без контроля такие дефекты как ослабление расклиновки обмотки
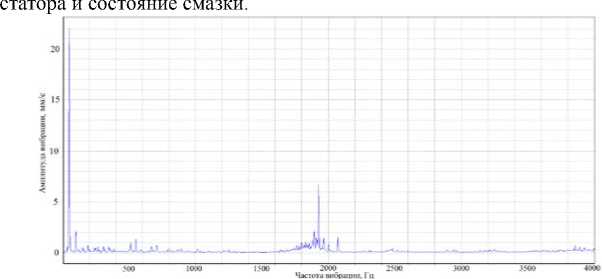
а - диапазон частот от 0 до 4000 Гц, по виброскорости, (мм/с)
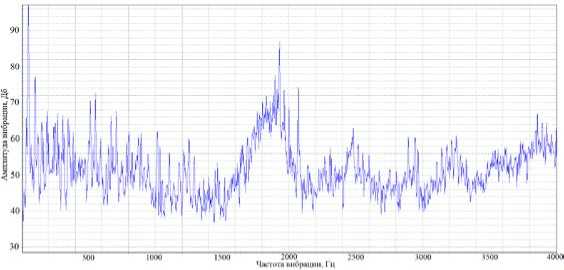
б- диапазон частот от 0 до 4000 Гц, по виброускорению, Дб
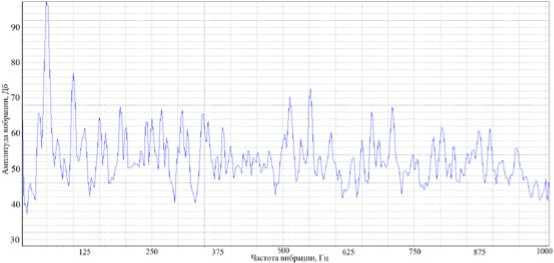
в- диапазон частот от 0 до 1000 Гц, по виброускорению, Дб
Рисунок 1 – Спектры вибрации двигателя насоса 250 кВт для различных частотных диапазонов и различных единиц измерения (точка измерения 1 – на лапе)
При диагностировании по общему уровню и на основе ударных импульсов используется принцип «черного ящика». По величине выходного сигнала принимается решение об опасности дефекта исследуемого объекта. А какие причины и дефекты вызвали эти отклонения – полнейшая неопределенность. Известно, что в зависимости от дефекта зависит ресурс подшипника качения: нарушение балансировки, повышенный зазор между кольцами и телами качения, дефекты колец, износ тел качения и сепаратора. Как показывает опыт, возникают эксплуатационные дефекты: заводские дефекты, которые приводят к интенсивному износу узлов подшипников качения; перекос внутреннего кольца; перекос наружного кольца; трещины на внутреннем кольце; износ сепаратора; неоднородный радиальный натяг; износ тел качения; загрязнение смазки; износ колец; вращение внутреннего кольца. Причем, в подшипниках качения могут быть два и более дефекта. В этом случае ресурс подшипника качения измеряется сотнями часов (рис. 2).
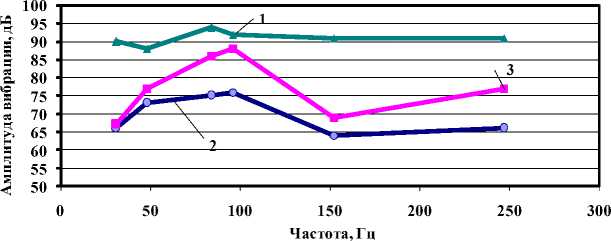
Рисунок 2 - Спектры вибрации нового подшипника качения №317 на информативных частотах с различными дефектами: 1 – эталонное предельное значение; 2 – эталонное минимальное значение;
3 – фактическое значение
В новом подшипнике № 317 выявлены следующие дефекты: дефекты тел качения (80 Гц), овальность внутреннего кольца (96 Гц), дефекты внутреннего кольца (250 Гц).
При диагностировании на основе огибающей или по прямому спектру предварительно вычисляются частоты на которых проявляются дефекты. Здесь выводятся две основные частоты вибрации. Частота вращения сепаратора вокруг центра вала:
fc =
f р • Rbh
(1),
2 • (Rbh + Гш )
где fр ̶̶̶ частота вращения вала, Гц;
R
вн
d + D
— г ш ; d, D - диаметры внутреннего и наружного
колец подшипников качения, мм;
rш - радиус тел качения, мм.
Частота вращения шара вокруг собственной оси:
f
ш
fр • Rbh
2 • г
ш
Все остальные частоты, характеризующие дефекты подшипников качения выводятся на основании первых двух.
Например, fч = f, • zw , где z„ количество тел качения,
характеризует повышенный зазор между кольцами и телами качения.
Вибрация при перекосе наружного кольца описывается зависимостью
f п = 2 • f с • Zш .
Частота вибрации при дефектах тел
качения определяется на основании двух частот: f ш и f ш · z ш . В таблице 2 представлены формулы для расчета информативных частот.
При диагностировании с применением способа огибающей возможны погрешности по следующим причинам:
-
1. Насколько выбранная полоса третьоктавного фильтра в спектре вибрации до 30 кГц характеризует физику работы исследуемого объекта.
-
2. Погрешностью при вычислении коэффициента модуляции и разностью между уровнем белого шума и максимальной амплитудой в полосе третьоктавного фильтра.
Как считает профессор Рябинин И.А. – разработчик основ теории надежности судовых электроэнергетических систем и теории безопасности структурно-сложных систем [] любая методика должна отвечать принципу повторяемости. Это значит, что все пользователи должны получать такой же результат, как и автор методики. Если этого не происходит, то методика несовершенна. Но, как показывает опыт общения с различными специалистами, многое зависит от квалификации и добросовестности пользователя.
Таблица 2 – Информативные частоты вибрации
№ п п |
Наименова ние дефекта |
Формула |
Подшипн ик №307 |
Подшипн ик №310 |
50 Гц |
50 Гц |
|||
1 |
Дефекты сепаратора |
f = f р • R вн с 2 ( R вн + Г ш ) |
18,78 |
19,04 |
2 |
Дефект наружного кольца |
f нк = f с • Z ш • k |
131,46·k |
152,3·k |
3 |
Дефект внутреннего кольца |
/ вк р o / вк вк ш |
31,2 |
30,96 |
218 |
247 |
|||
218·k |
||||
4 |
Дефект поверхности шара |
„ fp • RBH р вн f ш = ~ 2rш |
75,5 |
79,9 |
529 |
639 |
|||
5 |
Дефект внешнего кольца и поверхности шара |
f Ошв. = f ш - f р / 1 о.ш.в \1ш 1 р Т^ш |
25,6 |
29,9 |
178 |
239,9 |
|||
6 |
Радиальный зазор |
f -R .z р вн z ш °"" 2(R вн + Г ш ) |
131,46 |
152,3 |
7 |
Перекос внутреннего кольца |
f ,;,,. = 2 ( f р - f o ) z ш |
436 |
492 |
8 |
Перекос наружного кольца |
f п.н.к. = 2f с ·Z ш |
262,92 |
304,6 |
Дело в том, что при износе подшипников качения возникают не только дискретные частоты, характеризующие отдельные дефекты, но и увеличивается уровень белого шума. Не все объекты можно диагностировать с применением способа огибающей. Например, диагностировать магнитную вибрацию электрических машин, центробежные насосы и трансформаторы весьма сложно (рис.3). На рисунке 3 представлены спектры вибрации двух насосных агрегатов.
По оси абсцисс отложена частота вибрации в диапазоне от 0 до 5000Гц, по оси ординат – уровень вибрации (дБ – виброускорение). Из спектров вибрации насосов следует, что гидравлическая часть насоса мощностью 75 кВт изношено в большей степени, чем гидравлическая часть насоса мощностью 250 кВт.
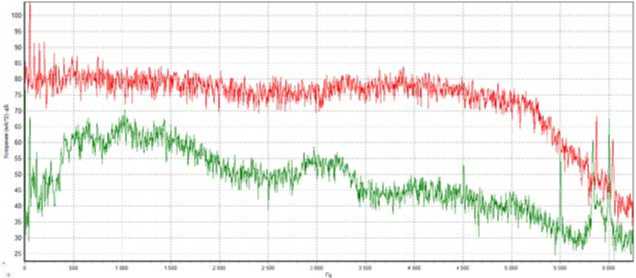
Рисунок 3 - Спектр вибрации подшипника гидравлического узла насоса (зеленым – насос №1 Рном= 250 кВт, красным – насос №2 Р ном =75 кВт. Датчики установлены на гидравлической части насоса.
Выявление дефектов при анализе прямого спектра является более достоверным, наглядным (при вибромониторинге) и универсальным. Этим способом можно проводить вибродиагностирование любого оборудования, которое вибрирует во время работы. Например, кроме роторного оборудования, можно диагностировать трансформаторы и трубопроводы, если имеется математическая модель вибрации. Самым главным элементом при техническом диагностировании является разработка и составление диагностической модели. Диагностическая модель строится на основе минимальной (условно-идеальной) машины и максимальной (условно-дефектной машины) вибрации на информативных частотах. Текущее значение вибрации по частоте и амплитуде сравнивается с диагностической моделью и выявляется дефект.
Порядок построения диагностической модели следующий.
При наличии выборки 6-10 разных электрических машин одного класса (новых, с износом, после ремонта) возможно построение диагностических моделей в виде таблицы (табличное отображение) или на спектре вибрации (графическое отображение).
Точным или приближенным методом вычисляются информативные частоты вибрации. На каждой информативной частоте определяется уровень вибрации исследуемых электрических машин. Далее выявляется максимальное (критическое) и минимальное
(начальное) значение амплитуды вибрации на каждой частоте. Тем самым определяется эталонная (минимальное значение из выборки) и критическая характеристика (максимальное значение из выборки) электрической машины. Измеренные значения сравниваются с эталонными и критическими, и определяется уровень износа элементов подшипников качения и магнитной системы электрической машины (таблица 3).
Для этого на каждой частоте интервал А кр -А нач разбивается на пять зон износа: начальный, малый, средний, предельный, аварийный. В таблице 3 текст «аварийный» печатается, если на любой информативной частоте значение вибрации А изм >А кр.
Таблица 3 – Диагностическая модель
№ |
f , Гц |
Акр, дБ |
Аизм, дБ |
А нач , дБ |
Степень износа |
1 |
14,3 |
116 |
50 |
49 |
Нач. |
2 |
28,7 |
114 |
45,6 |
39 |
Мал. |
3 |
5,9 |
132 |
45,5 |
43 |
Нач. |
4 |
177 |
106 |
110 |
46 |
Аварийное |
5 |
1518 |
107 |
90 |
70 |
Предельное |
6 |
32,9 |
112 |
44,3 |
39 |
Мал. |
7 |
988 |
109 |
83,9 |
69 |
Сред. |
8 |
18,6 |
114 |
60,2 |
37 |
Сред. |
9 |
558 |
107 |
73,2 |
47 |
Сред. |
10 |
8,4 |
134 |
41,3 |
37 |
Нач. |
11 |
253 |
109 |
89,2 |
52 |
Сред. |
12 |
688 |
106 |
81,4 |
62 |
Сред. |
13 |
545 |
109 |
75,5 |
53 |
Сред. |
14 |
1089 |
108 |
80 |
60 |
Предельное |
15 |
86 |
108 |
60 |
55 |
Нач. |
16 |
57,3 |
108 |
48,2 |
39 |
Мал. |
17 |
100 |
111 |
75,1 |
63 |
Мал. |
18 |
200 |
108 |
71,9 |
56 |
Мал. |
19 |
71,3 |
110 |
59,4 |
46 |
Мал. |
20 |
14,3 |
119 |
60 |
49 |
Нач. |
21 |
21,3 |
119 |
49 |
49 |
Среднее |
22 |
42,7 |
107 |
60 |
46 |
Нач. |
23 |
2300 |
108 |
100 |
80 |
Предельное |
24 |
3150 |
104 |
48 |
46 |
Нач. |
25 |
4500 |
109 |
55 |
53 |
Нач. |
26 |
50 |
110 |
88,1 |
55 |
Сред. |
Достоинство данной диагностической модели следующее:
-
- учитываются конструктивные особенности каждого типа машин;
-
- учитываются особенности эксплуатации каждой машины в отдельности;
-
- высокая наглядность и достоверность при выявлении дефектов и степени износа каждой машины в отдельности.
Выводы:
-
1 .Диагностирование роторных механизмов по общему уровню и на основе ударных импульсов приводит к большим погрешностям.
-
2 .Универсальным, наглядным и с высоким уровнем достоверности является способ диагностирования роторных механизмов по прямому спектру.
-
3 .Самым сложным и важным этапом при вибродиагностировании является разработка диагностической модели.
WAYS OF VIBRODIAGNOSTIC OF ROTARY MECHANISMS
Список литературы Способы вибродиагностирования роторных механизмов
- Грунтович, Н.В. Комплексное техническое диагностирование электротехнического оборудования -основа системы ремонтов «по состоянию»/Н.В. Грунтович, Н.И. Грачек.-Горный журнал, 2003, №7.
- Грунтович Н.В. Техническое диагностирование элементов АЭУ. Учебное пособие. Часть 1. Севастопольское ВВМИУ, 1984 г.-94 с.
- А.В.Барков Н.А.Баркова А.Ю.Азовцев "Мониторинг и диагностика роторных машин по вибрации", изд. СПб Государственного морского технического университета, г. СПб, 2000г, 169с.
- Рябинин И.А. Надежность и безопасность структурно-сложных систем.СПб,2000г. 248с.