Сравнение различных методов оценки качества внутренних антикоррозионных полимерных покрытий нефтепроводных труб
Автор: Юдин Павел Евгеньевич, Акулинин Александр Анатольевич
Журнал: Известия Самарского научного центра Российской академии наук @izvestiya-ssc
Рубрика: Научная жизнь
Статья в выпуске: 4-1 т.16, 2014 года.
Бесплатный доступ
В данной статье рассматриваются различные методы испытаний внутренних антикоррозионных полимерных покрытий трубопроводов. Показано, как влияют продолжительные выдержки в 3% растворе NaCl, сырой нефти при температуре +80°С, а также циклическое воздействие температуры -60°С…+60°С и тепловое воздействие при температуре +60 оС на стойкость к прямому удару и адгезионную прочность покрытий. Представлены основные закономерности изменения данных параметров. Предложена методика автоклавного теста, позволяющая моделировать разрушения, идентичные обнаруженным в условиях реальной эксплуатации трубопроводов с покрытиями. Показаны преимущества данной методики по сравнению с другими методами.
Выдержка в средах, метод термостарения, метод термоциклирования, автоклавный тест, нефтегазопроводные трубы, защита от коррозии
Короткий адрес: https://sciup.org/148203167
IDR: 148203167
Текст научной статьи Сравнение различных методов оценки качества внутренних антикоррозионных полимерных покрытий нефтепроводных труб
но-компрессорных труб. Данные по маркировкам исследованных образцов и соответствующим им основам покрытий представлены в табл. 1.
В ходе исследований определялись: адгезия (методом нормального отрыва грибка в соответствии с ИСО 4624) и стойкость к прямому удару (диаметр бойка 20 мм, груз массой 3 кг в соответствии с ИСО 6272) после выдержки в агрессивных средах и воздействия высоких температур. Поскольку любое антикоррозионное покрытие является проницаемым для агрессивных сред [3], то результате проникновения среды к границе металл-покрытие происходит его отслаивание и набухание. Данному процессу препятствуют адгезионные связи, чем выше величина адгезии при равных барьерных свойствах, тем медленнее происходит процесс отслаивания. С другой стороны, по изменению данного параметра можно судить о проницаемости агрессивных сред через покрытие и оценивать его стойкость и долговечность. Ударная прочность характеризует механические свойства полимера. В ходе взаимодействия со средой, вследствие старения, покрытие подвергается деструкции и происходит уменьшение показателя стойкости к прямому удару. Следовательно, совместное применение методов определения ударной и адгезионной прочности позволяет оценить свойства покрытия до и после лабораторных воздействий.
В соответствии с руководящим документом ВНИИСТ РД 05.00-45.21.30-КТН-005-1-05 [4] не допускается снижение адгезионной и ударной прочности более чем на 50%.
Гидротермальные воздействия моделируют воздействия агрессивных сред при высоких температурах, которые вызывают изменение эксп-
Таблица 1. Маркировка и соответствующий ей тип основы
Данные гидротермальные и термальные воздействия были выбраны в связи с их широким применением как в нормативной документации [4], так и в технических условиях заводов изготовителей [9-11].
На диаграммах рис. 1, 2 представлены результаты гидротермальных воздействий, а на рис. 3, 4
– термальных.
Из диаграммы рис. 1. видно, что выдержка в 3% растворе NaCl приводит к уменьшению адгезионной прочности большей части исследуемых образцов (Т7, Т10, Т14, Т16, Т17, У1, ЮК2, Ю6) (80%), у остальных (ТМ-1, Т8), наоборот, происходит возрастание данного параметра. Причинами уменьшения значений адгезии являются сорбция покрытием коррозионно-активных веществ
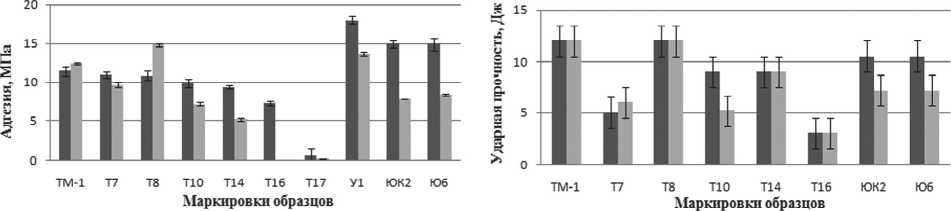
■ Адгезия в исходном состоянии, МПа ■ Ударная прочность в исходном состоянии, Дж
■ Адгезия после выдержки в 3% р-ре NaCl. МПа _ _
' Ударная прочность после выдержки в 3% р-ре NaCl. Дж
Р ис. 1. Изменение адгезии, МПа (слева) и ударной прочности, Дж (справа) после выдержки в 3% растворе NaCl
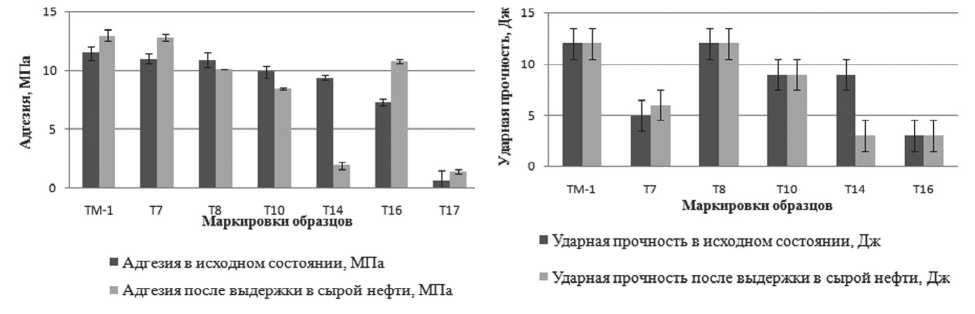
Рис. 2. Изменение адгезии, МПа (слева) и ударной прочности, Дж (справа) после выдержки в сырой нефти
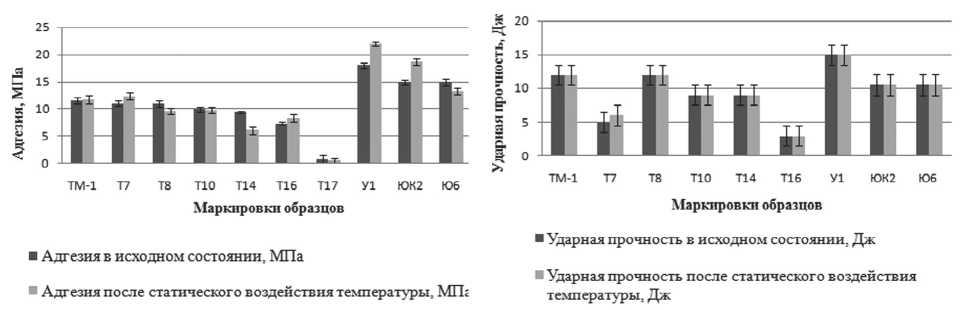
Рис. 3. Изменение адгезии, МПа (слева) и ударной прочности, Дж (справа) после циклического воздействия температуры
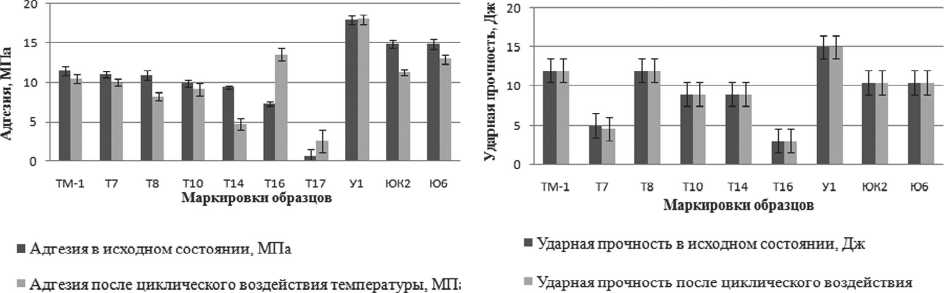
температуры, Дж
Рис. 4. Изменение адгезии, МПа (слева) и ударной прочности, Дж (справа)
после статического воздействия температуры из окружающей среды, которые затем диффундируют к металлу, и их последующее взаимодействие с материалом подложки [12]. В результате развивается коррозионная деструкция за счет хлорид-ионов, действие которых заключается в увеличении электропроводности среды, повышении степени растворимости продуктов коррозии и уменьшении экранирующих свойств защитной пленки. Выдержка в сырой нефти привела к противоположным результатам изменения адгезионной прочности (рис. 2). Для большей части (57%) исследуемых образцов (ТМ-1, Т7, Т16, Т17) она повысилась. При этом увеличение адгезии у образцов с маркировками ТМ-1, Т7 и Т17 обусловливается недостаточной степенью отверждения лакокрасочного покрытия, которая была выявлена в ходе проведения дифференциально-ска-нирующей калориметрии (у всех образцов тепловой эффект реакции полимеризации ~ 10 Дж/ г, в то время как для полностью полимеризованных покрытий он не превышает 5 Дж/г).
Как видно из представленных диаграмм (рис. 1, 2), гидротермальные выдержки в различных средах для образцов с маркировками Т7, Т8, Т16 и Т17 приводят к противоположным результатам по изменению адгезионной прочности, в одних случаях она возрастает, в других - уменьшается. Данное обстоятельство связано с различным взаимодействием основы покрытия со средой. Так, 3% раствор NaCl является полярной средой и, в отличие от сырой нефти (неполярная среда), реагирует с металлом трубы, в результате чего происходит коррозионное разрушение. В свою очередь, в среде сырой нефти коррозия происходит за счет старения полимерной основы покрытия вследствие адсорбции и набухания. Соответственно, данные виды воздействий для комплексной оценки необходимо проводить совместно в обеих средах.
Методы термальных воздействий (рис. 3, 4) не дополняют результатов гидротермальных воздействий (рис. 1,2). Отбраковка покрытий после данных видов воздействий не происходит, так как в большинстве случаев адгезионная прочность увеличивается (после термоциклирования для образцов Т16, Т17, У1, после теплового воздействия для образцов ТМ-1, Т7, Т16, У1, ЮК2), что связано с протеканием процессов полимеризации при увеличении температуры, а ударная прочность не изменяется. Следовательно, методы теплового воздействия и термоциклирования являются избыточными при использовании гидротермальных воздействий.
На основании полученных результатов можно сделать вывод, что гидротермальные воздействия дают объективные результаты для
Внешний вид покрытий после выдержки в Внешний вид по крытий после
лабораторном автоклаве эксплуатации
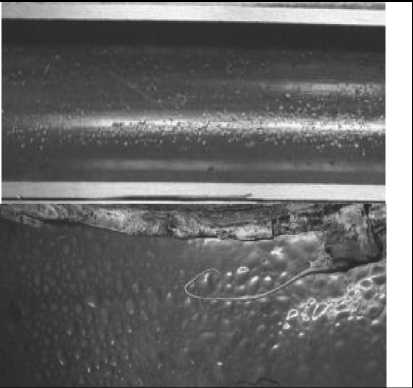
Рис. 5. Сравнение разрушения ВАКПП в лабораторном автоклаве и в результате эксплуатации в составе колонны насосно-компрессорных труб (верхние фотографии) и промыслового трубопровода (нижние фотографии)
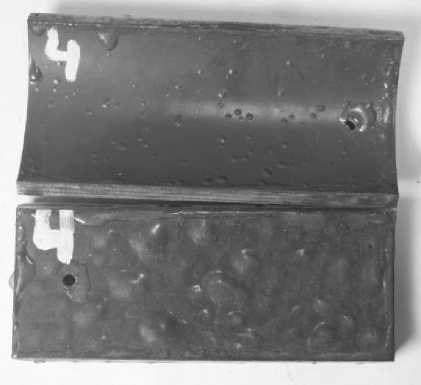
оценки барьерных свойств ВАКПП, однако, они являются длительными в исполнении, тогда как в нефтяной отрасли промышленности время является решающим фактором. Поэтому для решения задачи сокращения времени испытания на базе ООО «НПЦ «Самара» был разработан и применяется автоклав (патент № 130878 [13]), позволяющий моделировать механизмы разрушения труб с внутренними антикоррозионными покрытиями в реальных условиях. Автоклавным испытаниям посвящен ряд публикаций [14-15]. Общие основы испытаний внутренних антикоррозионных покрытий трубной продукции с помощью автоклавного теста обобщенно описаны в стандартах NACE TM0185 [16] API 5L7 [17]. Данный тест-метод, как и гидротермальные воздействия, позволяет определить барьерные свойства антикоррозионных покрытий, но, в отличие от них, требует минимальных временных затрат, а, вследствие использования многокомпонентных сред (газ+жидкость) и повышенного давления, позволяет моделировать реальные условия эксплуатации.
Автоклав оборудован устройствами автоматического поддержания заданного давления (1-160 атм) и температуры (25-120 °С) в диапазоне, достаточном для испытания покрытий, используемых в нефтегазовой промышленности. В качестве испытательной среды можно использовать практически любые коррозионно-активные газы (углекислый газ, кислород, сероводород и др., кроме сильных окислителей и кислотных агентов, как, например, хлор и хлороводород) и моделировать самые разнообразные условия эксплуатации антикоррозионных покрытий.
После проведения испытаний различных покрытий было установлено, что для оценки стойкости к взрывной декомпрессии оптимальное время выдержки составляет 24 часа при давлении 100 атм. с максимально допустимой температурой эксплуатации покрытий. Под стойкостью к взрывной декомпрессии понимается быстрое снижение давления ~18атм/с, которое зачастую приводит к растрескиванию и отслаиванию покрытия, что объясняется расширением газа на границе металл-покрытие, либо в дефектах структуры самого покрытия. Сброс давления по окончании выдержки в автоклаве производят в одном из двух режимов: быстром (5 сек) или медленном (5,5 часа). Растворимость различных газов для различных полимеров разная. Испытания проводились в СО2 или СО2 + H2S насыщенной среде. Как видно из рис. 6, в результате диффузии газа в покрытие и к границе металл-покрытие происходит либо адгезионное (рис. 6а), либо когезионное (рис. 6б) разрушение. Для покрытий, которые показали высокий срок службы в реальных условиях эксплуатации, такого эффекта не наблюдается (рис. 6в).
Для оценки степени старения полимерной основы оптимальное время выдержки в автоклаве составляет 10 суток при аналогичных условиях. За это время в случае низкого качества покрытий наблюдается появления вздутий, значительное уменьшение адгезии и ударной прочности покрытий. В табл. 3 представлены результаты автоклавного теста на старения для различных покрытий. Видно, что для покрытия №1, 2 наблюдается значительное уменьшение прочностных свойств, в то время как для покрытия №3 такого эффекта нет.
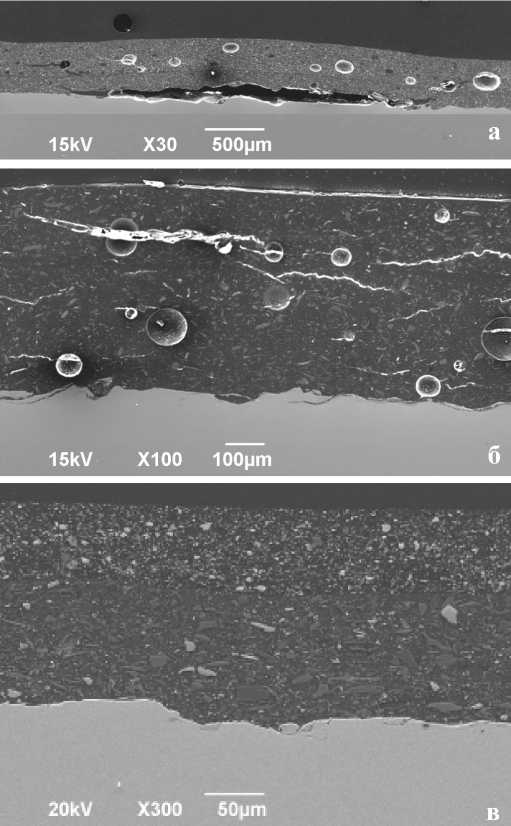
Рис. 6. Микроструктура образцов после испытаний в автоклаве на стойкость к взрывной декомпрессии: а – адгезионное разрушение, б – когезионное разрушение, в – разрушений нет
ВЫВОДЫ
Существующие лабораторные методы тепловых и гидротермальных исследований являются длительными в исполнении. Но время в нефтяной промышленности является очень важным фактором и, если результаты исследований появятся после установки нефтяных труб с внутренним антикоррозионным покрытием, то данная работа является бессмысленной при неудовлетворительном качестве нанесенного лакокрасочного покрытия. В связи с этим была разработана методика ускоренных испытаний на основе автоклавного теста. Данная методика позволяет оценивать качество покрытий в сжатые сроки (1-14 суток), в отличие от общепринятых методов, продолжительность которых составляет 1000 часов. Автоклавный тест позволяет не только в сжатые сроки произвести оценку стойкости ВАКПП к различным средам, но и оценить стойкость покрытия к взрывной декомпрессии.
Список литературы Сравнение различных методов оценки качества внутренних антикоррозионных полимерных покрытий нефтепроводных труб
- Фомин Г.С. Коррозия и защита от коррозии. Энциклопедия международных стандартов. М.: Протекор, 2013. 720 с.
- Ильдарханова Ф.И., Богословский К.Г. Выбор лакокрасочных покрытий для долговременной противокоррозионной защиты металлоконструкций нефтегазовой отрасли//Коррозия Территории Нефтегаз. 2013. №2. С. 22-27.
- Юдин П.Е., Александров Е.В. Разработка экспресс-метода оценки качества внутренних антикоррозионных покрытий нефтепроводных труб с использованием автоклавного теста//Коррозия Территория Нефтегаз. 2014. №1. С. 14-17.
- РД-05.00-45.21.30-КТН-005-1-05. ОАО «АК «ТРАНСНЕФТЬ». Руководящий документ. Правила антикоррозионной защиты резервуаров. М.: ОАО «АК «ТРАНСНЕФТЬ», 2005.
- Защита от коррозии, старения и биоповреждений машин, оборудования и сооружений: справочник [под ред. А.А. Герасименко]. М.: Машиностроение, 1987. 784 с.
- ГОСТ 9.403-80 ЕСЗКС Покрытия лакокрасочные Методы испытаний на стойкость к статическому воздействию жидкостей. М., 1980. 7с.
- ГОСТ Р53651-2009 (ИСО 3248:1998) Национальный стандарт Российской Федерации. Материалы лакокрасочные. Метод определения теплового воздействия. М., 2009. 8с.
- ГОСТ 27037-86 Материалы лакокрасочные. Метод определения устойчивости к воздействию переменных температур. М., 1986. 4с.
- ТУ 1390-003-52534308-2008 Трубы стальные диаметром 89-720 мм с наружным двухслойным полиэтиленовым покрытием и внутренним двухслойным эпоксидным покрытием (ЗАО «УПоРТ»).
- ТУ 1381-012-00154341-2002 Трубы стальные диаметром 102-530 мм с внутренним защитным покрытием на основе порошковых эпоксидных композиций (ООО «Предприятие Трубопласт»).
- ТУ 139000-012-01297858-2001 Трубы стальные диаметром 114-720 мм с внутренним изоляционным покрытием на основе эпоксидного материала с высоким сухим остатком (ООО «ЮКОРТ»).
- Чмутов К.В. Сорбция. М.: ГИТТЛ, 1957.
- Юдин П.Е., Желдак М.В., Петров С.С., Александров Е.В., Манахов А.М. Лабораторный автоклав//Патент России № 130878 опубл. 10.08.2013.
- Crolet J.-L., Bonis M.R. How to Pressurize Autoclaves for Corrosion Testing Under Carbon Dioxide and Hydrogen Sulfide Pressure//Corrosion. 2000. Vol. 56. № 2. P. 167-182.
- Hausler R.H. Methodology for Charging Autoclaves at High Pressures and Temperatures with Acid Gases/R.H. Hausler//Corrosion. 1998. Vol. 54. № 8. P. 641-650.
- NACE Standard TM0185-2006 Standard Test Method. 2006.
- API Recommende Practice RP5L7 (RP5L7) Second edition 1988.