Стадиальное выделение магнетит-гематитового концентрата при разработке технологии обогащения железистых карцитов
Автор: Опалев Александр Сергеевич, Хохуля Михаил Степанович, Бирюков Валерий Валентинович, Сытник Максим Владимирович, Конторина Татьяна Александровна, Буренина Ирина Викторовна
Журнал: Горные науки и технологии @gornye-nauki-tekhnologii
Статья в выпуске: 4, 2013 года.
Бесплатный доступ
Создана комбинированная магнитно-гравитационная технология получения железорудного концентрата из железистых кварцитов, перерабатываемых на ОАО,Олкон". Показано, что использование тонкого грохочения в сочетании с магнитно-гравитационной сепарацией обеспечивает его выделение уже на начальных стадияхобогащения и снижает энергозатраты на измельчение.
Железистые кварциты, магнитно-гравитационная сепарация, магнетит, гематит, кварц, концентрат, хвосты, содержание, извлечение
Короткий адрес: https://sciup.org/140215745
IDR: 140215745
Текст научной статьи Стадиальное выделение магнетит-гематитового концентрата при разработке технологии обогащения железистых карцитов
Наиболее распространенным промышленным типом железных руд являются железистые кварциты, однако при их переработке из-за отсутствия эффективных методов стадиального выделения в готовые концентраты как сильномагнитных, так и слабомагнитных минералов, происходит существенное переизмельчение полезных минералов по мере их раскрытия в рудоподготовительных операциях. В первую очередь это связано с тем, что магнетит и гематит имеют большую разницу в плотностных и прочностных свойствах по отношению к основному нерудному минералу - кварцу.
Технологические схемы магнитного обогащения железистых кварцитов российских ГОКов построены по принципу стадиального выделения отвальных хвостов. После каждой операции уменьшения крупности осуществляется магнитная сепарация с целью удаления хвостов. Готовый концентрат получается только в последней операции.
Циклы мокрой магнитной сепарации и гравитационного обогащения основаны на методах, которые не обеспечивают эффективного разделения тонких частиц как сильно, так и слабомагнитных минералов.
Одним из путей повышения эффективности схем обогащения является стадиальное выделение не только хвостов, но и концентрата, которое позволит снизить затраты на последующее измельчение, а также несколько повысить выход концентрата и извлечение железа в концентрат [1].
Железистые кварциты Заимандровской группы месторождений перерабатываются на дробильно-обогатительной фабрике ОАО «Олкон» по комбинированной магнитно-гравитационной схеме. Для выделения магнетитового концентрата используется магнитная сепарация, а гравитационное получение гематитового концентрата из промпродукта основной магнитной сепарации осуществляется на основе применения отсадки.
Действующая технология имеет типовое построение и базируется на стадиальном выводе из процесса хвостов с дальнейшим направлением рудной смеси в следующую стадию измельчения и классификации, работающей в замкнутом цикле с классификацией и магнитной сепарацией. Общим недостатком таких технологий из-за несовершенства работы классифицирующего оборудования является низкая степень раскрытия рудной фазы при совместном измельчении рудных зерен и их сростков с породообразующими минералами. Для выделения готового по крупности материала в циклах измельчения руд применяется, как правило, гидравлическая классификация, осуществляемая в механических классификаторах или гидроциклонах различных типов, но в целом эффективность их работы не превышает 35-50% по готовому классу.
Кроме того, высокие циркуляционные нагрузки замкнутого цикла измельчения приводят к переизмельчению магнетита и гематита, и соответственно, их потерям с тонкими классами при одновременном разубоживании концентрата сростковой фракцией.
Анализ вещественного состава измельченных продуктов данного предприятия показал, что уже после первой стадии шарового измельчения в них кроме большого количества раскрытых зерен пустой породы и различных по содержанию железа сростков находится значительная часть раскрытых зерен магнетита и богатых сростков, представляющих собой готовый концентрат[2-4], который необходимо своевременно выводить выводить из процесса.
Мировой опыт показал, что наиболее перспективным направлением работ по решению указанной выше задачи является применение операции тонкого грохочения в циклах измельчения. При этом задача энергосбережения может быть решена путем сокращения числа мельниц при неизменной производительности секции или увеличением объема переработки руды на секции при неизменном фронте измельчения.
Применение магнитно-гравитационного разделения в технологии получения магнетитовых концентратов в комбинации с тонким грохочением позволяет уже в начальных стадиях обогащения технологических схем выводить из процесса готовый концентрат требуемого качества [5, 6].Высокая эффективность разделения в магнитногравитационных аппаратах обеспечивается комплексностью воздействия физических сил на частицы разделяемого материала и высокой чувствительностью процесса к изменению соотношения магнитной и гидродинамической сил.
Существенное улучшение эффективности классификации достигается в настоящее время применением грохотов фирмы ,,Derrick Corporation”, обеспечивающих эффективную классификацию материала за счет максимального выхода расчетного класса в подрешетный продукт.
Положительный опыт от их применения в операции тонкого грохочения накоплен на ряде предприятий железорудной отрасли(ОАО «Карельский окатыш», ОАО «Соколово-Сорбайское ГПО, ОАО «Ковдорский ГОК» и др.)
С целью определения оптимального местоположения операций тонкого грохочения и магнитно-гравитационной сепарации в топологии технологической схемы обогатительной фабрики ОАО «Олкон» проведена серия экспериментальных исследований по доводке различных продуктов обогащения. Тонкому грохочению подвергалось питание гидроциклона ГЦ-650 и пески гидроциклона ГЦ-500 соответственно черновых концентратов I и II стадий обогащения 9-ой технологической секции фабрики.
Тестовые испытания по классификации указанных выше продуктов проводились с использованием грохота «StackSizerТМ» модели 2S648-1STK, при этом целью испытаний являлось установление технологических параметров разделения в зависимости от плотности питания, частоты вращения вибромотора, размера ячеек сита и производительности по твердому. Полученные результаты испытаний представлены в таблице 1, где производительность грохота варьировала в пределах 25-30 т/час, среднее содержание твердого в питании составляло 40%, частота колебаний деки находилась в пределах 40-50 Гц.
Дообогащение подрешетных продуктов грохота на лабораторном магнитном сепараторе не обеспечило получения концентратов кондиционного качества из стадиальных черновых концентратов, выделенных при различных режимах работы грохота, что предопределило использование для их доводки экспериментального образца магнитногравитационного сепаратора (рис. 1).
Исследованиями установлено, что напряженность магнитного поля в рабочем объеме магнитно-гравитационного сепаратора является определяющим параметром разделения, который позволяет изменять технологические показатели в широком диапазоне, а скорость восходящего водного потока является функцией крупности разделяемого материала и может варьировать в определенном диапазоне значений.
На рисунке 2 представлены графические зависимости изменения технологических показателей магнитно-гравитационной сепарации от напряженности магнитного поля Н . Полученные данные показывают, что ее применение магнитно-гравитационной сепарации в комбинации с тонким грохочением позволяет получить железорудные концентраты как кондиционного качества (65,7% Fe общ. ), так и содержащие более 70%.
Данное обстоятельство подтверждает целесообразность использования магнитно-гравитационной сепарации для стадиального вывода магнетитового концентрата по мере его образования, при этом функциональная зависимость содержания Feобщ. в концентрате от напряженности магнитного поля позволит решить проблему стабилизации качества производимой продукции современными средствами автоматизации в будущем.
Таблица 1.
Технологические показатели тонкого грохочения песков гидроциклона ГЦ-500 и питания гидроциклона ГЦ-650.
Размер ячейки сита, мкм (частота, Гц) |
Исходный продукт |
Надрешетный продукт |
Подрешетный продукт |
||||
Выход, % |
Содержание Fe общ , % |
Выход, % |
Содержание Fe общ , % |
Выход, % |
Содержание Fe общ , % |
||
Пески гидроциклона ГЦ 500 (черновой концентрат II стадии) |
|||||||
230 (50) |
100,0 |
51,8 |
29,4 |
40,6 |
70,6 |
53,4 |
|
Питание гидроциклона ГЦ 650 (черновой концентрат I стадии) |
|||||||
180 (50) |
100,0 |
45,2 |
58,0 |
36,8 |
42,0 |
56,8 |
|
180 (40) |
100,0 |
45,2 |
45,0 |
30,6 |
55,0 |
56,6 |
|
150 (43) |
100,0 |
44,0 |
77,0 |
38,3 |
23,0 |
59,7 |
|
150 (37) |
100,0 |
44,0 |
66,5 |
37,5 |
33,5 |
56,9 |
|
100 (43) |
100,0 |
44,3 |
86,0 |
37,0 |
14,0 |
59,9 |
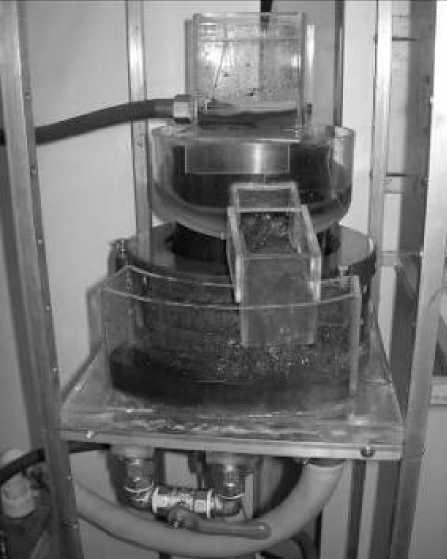
Рис. 1. Общий вид экспериментального образца магнитно-гравитационного сепаратора
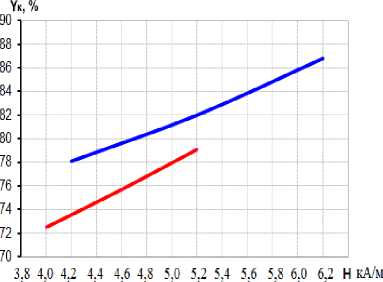
а)
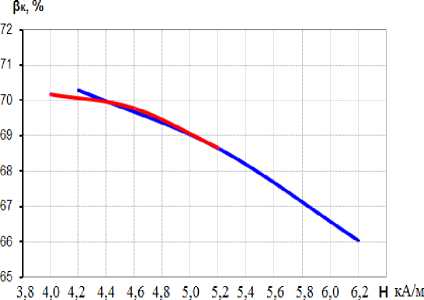
б)
РсЛ. %
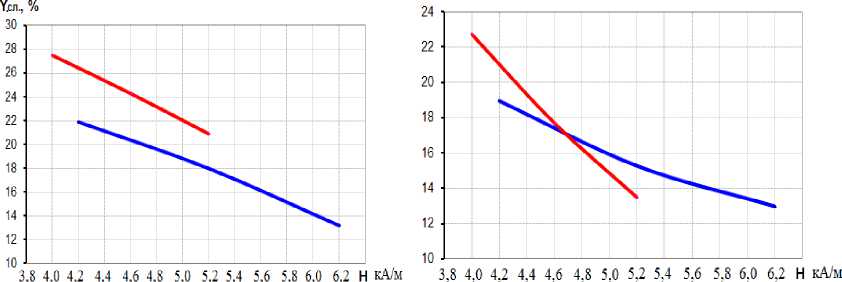
в)
г)
Рис. 2. Технологические показатели магнитно-гравитационной сепарации черновых концентратов ( -первой стадии; -второй стадии) от напряженности магнитного поля:
а) - выход концентрата; б) – содержание Fe общ. в концентрате; в) – выход слива; г) – содержание Fe общ. в сливе
Минералогическими исследованиями продуктов слива магнитногравитационной сепарации установлено, что в зависимости от напряженности магнитного поля происходит изменение их вещественного состава (рис 3).При значениях интенсивности магнитного поля около 6,0 кA/м сливы содержат бедные сростки магнетита с кварцем и породообразующими минералами (рис. 3а), а по мере снижения интенсивности магнитного поля растет содержание железа общего за счет появления в продуктах более богатых сростков (рис. 3б). При дальнейшем снижении интенсивности магнитного поля рост содержания Fe общ. связан с появлением тонких частиц раскрытого магнетита.
Проведенные технологические исследования показали принципиальную возможность применения комбинации тонкого грохочения и магнитно-гравитационной сепарации для получения магнетитовых концентратов с кондиционным содержанием массовой доли
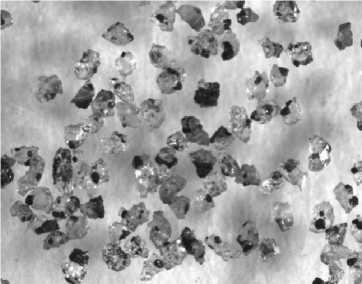
а)
Рис. 3. Микрофотографии продуктов слива магнитно-гравитационного сепаратора с различным содержанием массовой доли железа:
а) 13-15% Fe общ. б) 18-22% Fe общ .
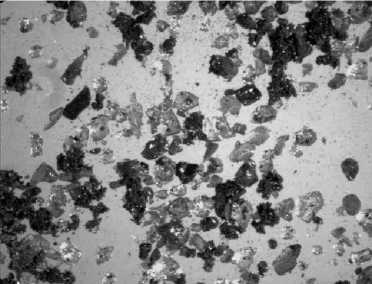
б)
железа и выше (до70%) уже на первой стадии магнитной сепарации после дообогащения подрешетного продукта грохота. Использование указанного выше технологического решения применительно к перерабатываемым на ОАО «Олкон» железистым кварцитам позволит не только уменьшить энергозатраты при производстве концентрата, но и решить вопросы стабилизации качества товарной продукции при внедрении соответствующих систем автоматизации технологических процессов.
Гравитационный цикл обогащения промпродукта основной магнитной сепарации, реализованный на ОАО ,,Олкон” и включающий использование диафрагмовых отсадочных машин, характеризуется недостаточной эффективностью извлечения мелких фракций гематита, что подтверждается низким, не более 40-45% извлечением гематитового железа в концентрат. Это связано с пространственными флуктуациями частиц в камере отсадочной машины, вызванными неоднородностью структуры элементарных объемов взвеси.
Учитывая особенности вещественного состава промпродуктов основной магнитной сепарации [7-9], выявлено преимущество их переработки в потоках малой толщины, предусматривающей использование двух стадий винтовой сепарации, что позволяет вывести в голове процесса отвальный продукт и обеспечить извлечение многообразных форм железа в концентрат.
Испытания проводились на материале, вещественный состав которого представлен в таблице 2. Основными факторами процесса разделения на винтовом сепараторе являлись их производительность и плотность разжижения исходного питания. Наиболее эффективный режим работы сепаратора зафиксирован при содержании твердого в питании на уровне 25% и исходной нагрузке 300 кг/час.
Таблица 2.
Минеральный состав промпродукта основной магнитной сепарации по классам крупности.
Классы, мм |
Выхо д класс а, % |
Содержание минералов, % |
Распреде -ление гематита, % |
|||||
Гемати т |
Квар ц |
Полев ые шпаты |
Амфибол ы, пироксены |
Слюд ы |
Гранат, эпидот |
|||
+1 |
1,4 |
3,2 |
34,6 |
49,8 |
6,8 |
4,1 |
1,5 |
0,3 |
-1+0,63 |
3,4 |
6,0 |
49,0 |
33,2 |
6,0 |
3,5 |
2,3 |
1,5 |
0,63+0,315 |
16.9 |
11,0 |
51,5 |
20,0 |
11,7 |
3,8 |
2,0 |
14,0 |
-0,315+0,2 |
27,8 |
15,8 |
48,6 |
16,0 |
14,0 |
3,6 |
2,0 |
33,0 |
-0,2+0,1 |
26,9 |
14,5 |
52,7 |
15,0 |
12,8 |
2,5 |
2,5 |
29,3 |
-0,1+0,071 |
11,3 |
12,0 |
48,8 |
16,0 |
17,0 |
3.5 |
2,7 |
10,2 |
-0,071 |
12,3 |
12,5 |
45,5 |
17,0 |
19,2 |
3,3 |
2,5 |
11,6 |
Итого: |
100,0 |
13,3 |
49,7 |
17,6 |
13,9 |
3,3 |
2,2 |
100,0 |
Для изучения распределения материала хвостов, гранулометрических классов, тяжелой железосодержащей и легкой фракций поток пульпы в конце винтового желоба делился на несколько продуктов разделения. К черновому концентрату основной винтовой сепарации были отнесены продукты первых трех отсеков с содержанием Fe общ. =33,4%, остальная часть материала относилась к хвостам, содержание железа в которых составило 4,45%.
На рис. 4 представлены в виде гистограмм графические зависимости разделения промпродукта основной магнитной сепарации по отдельным отсекам первой стадии винтовой сепарации.
Полученные результаты показывают, что существенное повышение массовой доли железа происходит в первых двух отсеках сепаратора, составившая соответственно 52,1 и 32,15% при извлечении более 52% Feобщ. При удалении потока пульпы от внутреннего борта желоба содержание общего железа начинает плавно снижаться с максимальным возрастанием выхода продукта до 28% в 5 отсеке сепаратора при содержании в нем более 4% Feобщ.
В последующем выход материала при его попадании в зону, расположенную ближе к внешнему профилю желоба начинает уменьшаться при некотором повышении содержания железа в последних двух отсеках. Это связано с сосредоточением тонких фракций гематита, которые не могут эффективно разделяться гравитационными методами из-за имеющихся ограничений по глубине обогащения мелких частиц, составляющей, как правило, не более 0,07 мм.
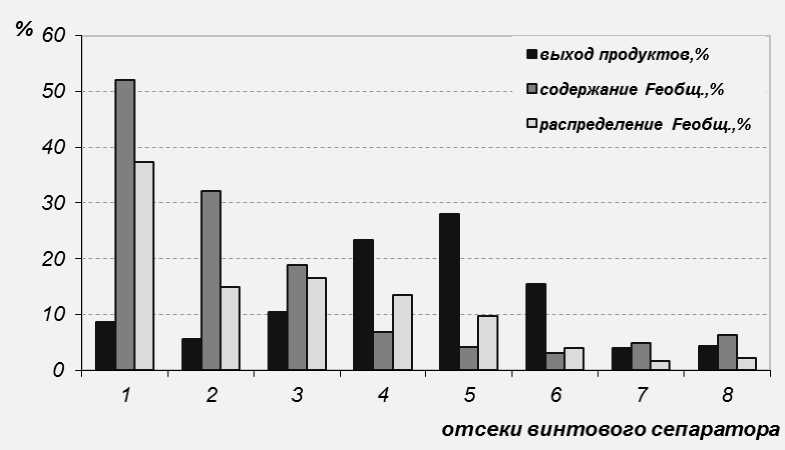
Рис. 4. Гистограммы распределения выхода продуктов, содержания и извлечения в них Feобщ. по отсекам основной винтовой сепарации
Результаты разделения свидетельствуют о том, что в тяжелую фракцию винтовой сепарации выделен черновой концентрат с содержанием более 33% Fe общ. при извлечении в него более 71% железа.
В таблице 3 приведены сводные показатели обогащения промпродукта основной магнитной сепарации.
Проведенная на этом же аппарате перечистка чернового концентрата первых трех отсеков обеспечила получение продукта с содержанием около 56% Feобщ. при его извлечении более 55% от исходной руды.
Дообогащение промпродукта 2 стадии винтовой сепарации на концентрационном столе повысило на 9,6% извлечение железа в гравитационный концентрат, содержащий 62,1% Feобщ.
Содержание железа в гравитационном гематитовом концентрате составило 62,1% при извлечении выше 64%. При этом его выход при замене отсадочных машин на рекомендуемую технологию увеличится примерно в 1,4-1,5 раза.
В дальнейшем гематитовый концентрат объединялся с магнетитовым концентратом магнитной сепарации, что обеспечило получение общего концентрата, выход которого составил 34% при содержании в нем 66,5% Fe общ. и извлечении 88,7%.
Разработанная технологическая схема, представленная на рис. 5, по сравнению с действующей, отличается снижением более чем в 2 раза циркуляционной нагрузки во II стадии измельчения, что приводит к сокращению фронта измельчения и, соответственно, к снижению более чем на 20% энергопотребления при получении магнетитового концентрата.
Таблица 3.
Показатели обогащения промпродукта основной магнитной сепарации гравитационными методами
Наименование продукта |
Выход, % |
Содержание Fe общ. , % |
Извлечение Fe общ. , % |
||
от операции |
от руды |
от операции |
от руды |
||
Основная винтовая сепарация |
|||||
Черновой к-т 1 |
24,7 |
24,7 |
33,4 |
71,1 |
71,1 |
Хвосты 1 |
75,3 |
75,3 |
4,45 |
28,9 |
28,9 |
Руда |
100,0 |
100,0 |
11,6 |
100,0 |
100,0 |
Перечистная винтовая сепарация |
|||||
Черновой к-т 2 |
46,8 |
11,6 |
55,8 |
78,2 |
55,7 |
Промпродукт |
22,2 |
5,5 |
25,8 |
17,2 |
12,2 |
Хвосты 2 |
31,0 |
7,6 |
4,9 |
4,6 |
3,2 |
Черновой к-т1 |
100,0 |
24,7 |
33,4 |
100,0 |
71,1 |
Доводка промпродукта концентрацией на столе |
|||||
Тяжелая фракция |
32,7 |
1,8 |
62,1 |
78,7 |
9,6 |
Легкая фракция |
67,3 |
3,7 |
8,15 |
21,3 |
2,6 |
Промпродукт |
100,0 |
5,5 |
25,8 |
100.0 |
12,2 |
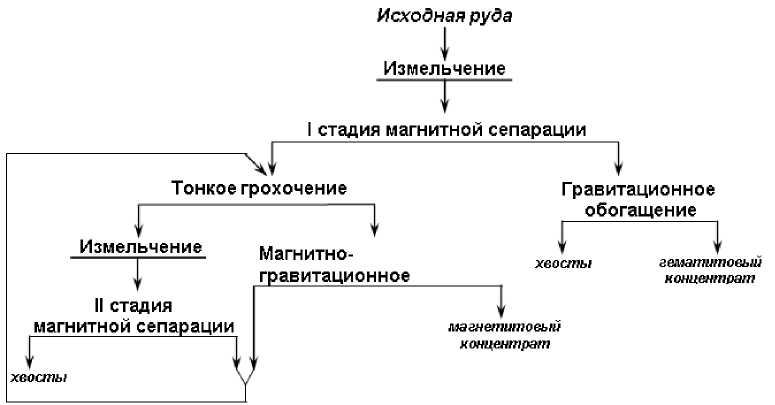
Рис. 5. Рекомендуемая схема получения коллективного гематитового концентрата из железистых кварцитов
железистые кварциты, магнитно-гравитационная сепарация, магнетит, гематит, кварц, концентрат, хвосты, содержание, извлечение ferrous quartzites, magnetic-gravity separation, magnetite, hematite, quartz, concentrate, tailings, content, recovery
Список литературы Стадиальное выделение магнетит-гематитового концентрата при разработке технологии обогащения железистых карцитов
- Пелевин А.Е. Стадиальное выделение железного концентрата//Обогащение руд, 2007. -№3. -С.10-15.
- Остапенко П.Е. Обогащение железных руд. -М.: Недра, 1985.
- Кармазин В.В., Кармазин В.И. Магнитные, электрические и специальные методы обогащения полезных ископаемых. Том I. -М.: МГГУ, 2005.
- Кармазин В. В., Кретов С. И., Синельникова Н. Г. Повышение качества концентратов на основе высокой селективности раскрытия и сепарации в процессах магнитного обогащения железных руд./Сб.«Форум горняков-2008». -Днепропетровск: Изд. НГУ, 2008.
- Усачев П.А., Опалев А.С. Магнитно-гравитационное обогащение руд. -Апатиты: Изд. КНЦ РАН, 1993. -92 с.
- Усачев П.А. Получение высококачественных железных концентратов на обогатительной фабрике ОАО «Лебединский ГОК»//Горный журнал, 2000. -№ 3. -С.41-44.
- Чантурия В.А., Гзогян Т.Н., Прокопьев С.А., Гельбинг Р.А. Перспективы применения гравитационных методов в схемах обогащения железных руд/Материалы международного совещания «Современные методы комплексной переработки руд и нетрадиционного минерального сырья», часть 1. -Апатиты, 2007. -С.182-185.
- Патковская Н.А., Тасина Т.И. Модернизация технологии обогащения железосодержащих руд Северо-Запада России//Обогащение руд, 2011.-№1.-С.6-10.
- Патковская, Н.А., Курова М.Д., Смирнова Л.В., Сладкович Л.М. Внедрение винтовых сепараторов на Оленегорском горно-обогатительном комбинате//Обогащение руд, 1975. -№5. -С.18-23.