Статистические инструменты обеспечения оперативного мониторинга качества продукции на этапах жизненного цикла
Автор: Благовещенский Д.И., Козловский В.Н., Панюков Д.И.
Журнал: Известия Самарского научного центра Российской академии наук @izvestiya-ssc
Рубрика: Машиностроение и машиноведение
Статья в выпуске: 2 т.24, 2022 года.
Бесплатный доступ
В статье представлены результаты разработки статистических инструментов для обеспечения эффективности контроля качества продукции на этапах жизненного цикла в автосборочном производстве.
Комплексные программы улучшения, контроль качества, автомобильная промышленность
Короткий адрес: https://sciup.org/148324476
IDR: 148324476 | DOI: 10.37313/1990-5378-2022-24-2-16-26
Текст научной статьи Статистические инструменты обеспечения оперативного мониторинга качества продукции на этапах жизненного цикла
и услуг. Надо полагать, что чем сложнее производство и создаваемая продукция, тем острее эта проблема и значительнее возможные негативные последствия [1, 2].
В представленной работе мы покажем несколько инструментов позволяющих оперативно реагировать на корпоративном уровне управления промышленного предприятия на кризисы качества продукции на этапах жизненного цикла продукции, на примере автосборочного производства.
При решении проблемы повышения оперативности измерений показателей качества продукции на различных этапах, на предприятии требуется проведение инвентаризации подходов и методов используемых в соответствующих процессах с прицелом на их модернизацию, либо на создание дополнительного комплексного инструментария, а также технического оснащения [1, 3].
Бесспорно, что все вопросы стандартизации и управления качеством, как ключевые элементы роста производительности труда и конкурентоспособности продукции должны являться первейшим предметом рассмотрения программы по цифровизации. При этом полагаем, что первоочередные задачи должны решаться как раз в области мониторинга и управления и такие проекты желательны к реализации в первую очередь рамках корпоративных программ цифровизации производства.
Для многих отечественных автопроизводителей получение оперативной информации о качестве продукции в эксплуатации до настоящего времени остается острой проблемой в силу доминирования индикаторов мониторинга, ориентированных на оценку качества продукции с привязкой к гарантийному парку, по месяцам эксплуатации. Такие индикаторы не обладают свойством необходимой чувствительности к инцидентам. Именно поэтому аппарат, реализующий измерение и расчет оперативных показателей, должен быть сосредоточен, в первую очередь, на измерение текущего (зафиксированного в корпоративной информационной системе) уровня качества автомобилей в динамике (например, по неделе выпуска продукции), индикатор должен измеряться в абсолютных единицах (например, количество дефектов) в отличие от используемых мировыми лидерами автопрома показателей, ориентированных под приведение абсолютного значения к объему выпуска продукции [1,4].
В качестве решения, предлагаем расчетностатистический инструментарий, позволяющий проводить оперативный мониторинг качества автомобилей, начиная с первой недели в эксплуатации (рисунок 1). Используя электронные базы данных по проданным автомобилям одной из ведущих в нашей стране марок с привязкой к дате производства, а также электронные базы
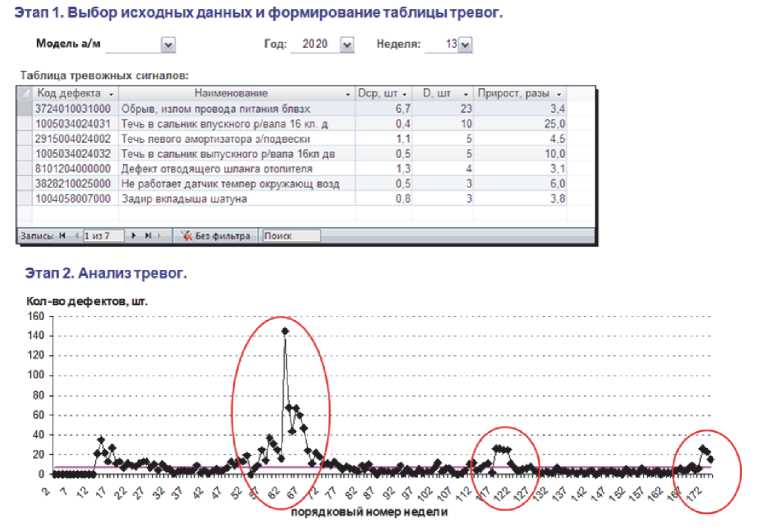
а
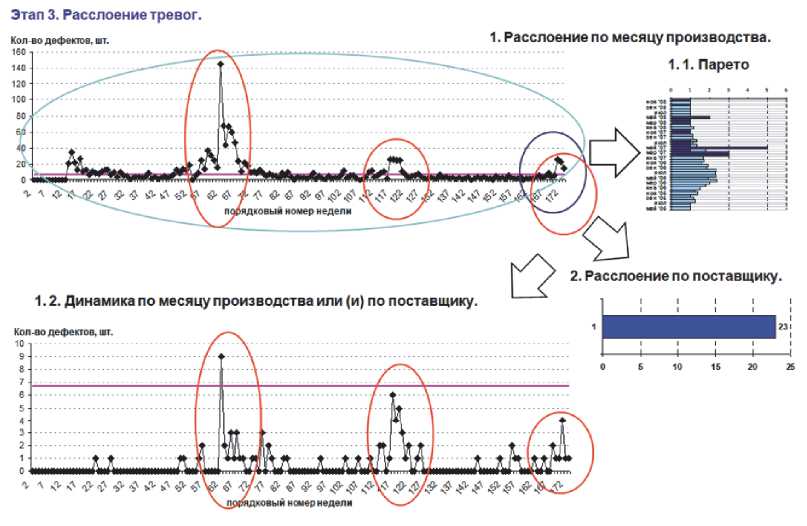
б
Рисунок 1 - Функционал аналитического инструмента мониторинга качества автомобилей в эксплуатации по области тревог данных по дефектам автомобилей в эксплуатации, возможный инструмент оперативного мониторинга качества автомобилей в эксплуатации можно представить в виде мониторинга показателя тревог. Здесь, отсчет недель (ось абсцисс) начинается с момента продажи автомобилей конечному потребителю, и соответственно прирост уровня дефектности, в абсолютных единицах, фиксируется сразу же с момента начала эксплуатации парка автомобилей с определенной датой производства.
Основная идея используемого индикатора тревог состоит в количественной оценке уровня дефектности автомобилей, имеющих определенные даты производства и периода эксплуатации (недели после продажи). В случае фиксации 2, 3-х разового и более превышения дефектности от некоторого устойчивого значения (рисунок 1 а) фиксируется тревога, и начинают работать аналитические инструменты по поиску причин кризиса качества продукции, с расслоением тревожного сигнала по кодам дефектов стандартизированного кодификатора и по поставщикам соответствующего комплектующего изделия (рисунок 1, б). После установ- ления причины тревоги запускается процесс, направленный на локализацию и решение проблемы качества продукции [1,5].
Почему предложенный инструмент более оперативен в сравнении с традиционными инструментами мониторинга? Ответ на данный вопрос вытекает из того, что как было показано, практически все традиционные инструменты мониторинга сегодня заточены на измерение показателей дефектности за отчетные периоды в качестве которых принимаются месяцы или кварталы. Предлагаемое решение сужает плечо мониторинга в разы до границы недель эксплуатации, что создает предпосылки для существенного повышения оперативности вскрытия проблем качества продукции.
На рисунке 2 показано рабочее окно предлагаемой корпоративной информационной системы мониторинга, реализующей предложенный инструментарий выявления тревожных сигналов в период эксплуатации продукции.
Следующим инструментарием предлагаемым в качестве повышающего оперативность реагирования предприятия на проблемы качества, является по сути целая группа статисти-
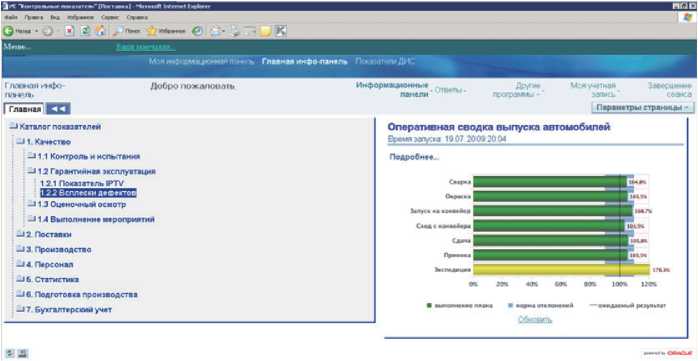
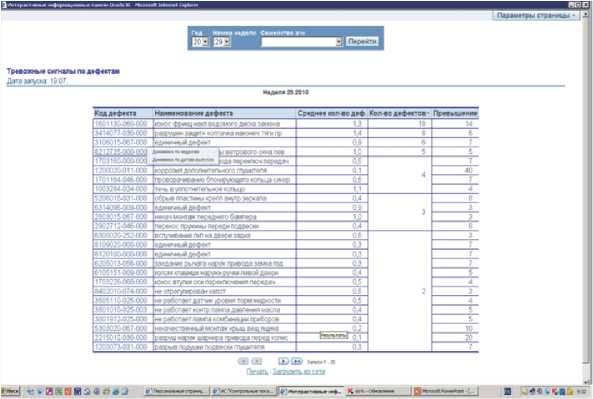
Рисунок 2 - Рабочее окно подпрограммы мониторинга тревог в области качества автомобилей в эксплуатации
ческих инструментов мониторинга состояния внутренних процессов предприятия направленных собственно на решение проблем качества продукции.
После сбора данных отражающих ТОП проблем качества продукции, на корпоративном уровне управления предприятием должно вырабатываться решение относительно того, какая часть из полученного ТОПового списка проблем должны быть охвачена мероприятиями по улучшению качества. Обычно на предприятиях работают со списками ТОП-10, 20, 50, 100 проблем качества.
После формирования аналитической справки, в которой зафиксированы ТОП проблемы предназначенные к решению, должен запускаться алгоритм действий автопроизводителя по проведению углубленного анализа возникшей проблемы и организации работы в рамках заказа на устранения несоответствия (ЗУН). Исходя из полученных ранее результатов исследования, можно утверждать, что момент времени t0, отражающий время идентификации проблемы и, по сути, начала работы в рамках мероприятий по устранению дефектов является критически важным параметром обеспечения эффективности соответствующей деятельности.
На рисунке 3 представлена графическая схема, ярко определяющая проблематичность работы в рамках действующих на предприятиях инструментов управления качеством. Схема дополнена численными значениями данных, отражающих действующие нормативы (время в днях) на решение задач в рамках отдельных этапов работы.
Нормативы, как правило есть, а вот инструментов мониторинга за четким исполнением этих временных границ как правило не существует в силу сложности и специфики работы различных функциональных служб на крупных производственных предприятиях. Одной из наиболее основных проблем здесь выступает как правило отсутствие единой информационной системы управления качеством продукции на этапах жизненного цикла. В каждом подразделении существует своя система или набор информационных систем, которые нуждаются в интеграции на уровне всего предприятия. Эта проблема глобальная, зависящая от административно-финансовых возможностей предприятия.
Но простое решение обозначенной проблемы мониторинга, по крайней мере на первых этапах, существует. Требуется кропотливое сведение данных о ходе реализации мероприятий по улучшению качества продукции из различных информационных систем предприятия в единые электронные таблицы по моделям выпускаемых автомобилей, например как это показано на рисунке 4.
Проследим оперативность реализации отдельных этапов с использованием статистических данных, полученных из различных корпоративных информационных систем автопроизводителя и совмещенных в одной электронной таблице. В качестве примера представим данные по двум популярным в нашей стране маркам автомобилей (рисунок 4).
Из анализа данных, представленных на рисунке 4 видно, что наиболее существенное вре-
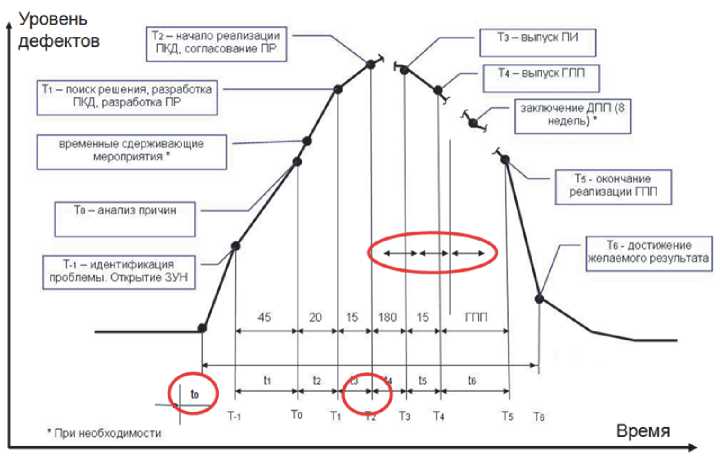
Рисунок 3 – Схема этапов решения проблем качества на автосборочном предприятии в рамках действующих инженерных инструментов управления: заказ на устранение несоответствия (ЗУН); план корректирующих действий (ПКД); предложение к изменению конструкции изделия (ПР); предварительное извещение об изменении конструкции изделия (ПИ);
график подготовки производства (ГПП)
Номер ЗУН |
I этап(дни) |
II этап (дни) |
III этап (дни) |
IV этап (дни) |
V этап (дни) |
VI этап (дни) |
• 002379 |
206 |
87 |
983 |
14 |
183 |
|
• 002500 |
1 |
314 |
449 |
234 |
||
• 002648 |
297 |
819 |
570 |
8 |
195 |
|
• 002686 |
113 |
52 |
828 |
1150 |
202 |
|
• 002712 |
15 |
712 |
547 |
889 |
148 |
195 |
• 002720 |
24 |
171 |
||||
• 002721 |
8 |
13 |
803 |
790 |
184 |
|
• 002729 |
867 |
167 |
234 |
|||
• 002731 |
15 |
972 |
||||
• 002732 |
15 |
720 |
632 |
182 |
8 |
244 |
• 002740 |
37 |
855 |
59 |
192 |
14 |
153 |
• 002750 |
164 |
66 |
731 |
240 |
||
• 002757 |
31 |
10 |
921 |
314 |
197 |
|
• 002775 |
15 |
90 |
631 |
423 |
||
• 002785 |
148 |
323 |
183 |
360 |
||
2018 год |
130 |
400 |
462 |
568 |
187 |
214 |
• 002788 |
748 |
653 |
||||
• 002823 |
195 |
3 |
412 |
|||
• 002825 |
277 |
514 |
202 |
|||
• 002833 |
48 |
48 |
22 |
29 |
169 |
|
• 002834 |
85 |
150 |
6 |
191 |
||
• 002840 |
29 |
|||||
• 002844 |
38 |
183 |
281 |
|||
2019 год |
112 |
237 |
136 |
281 |
13 |
257 |
• 002847 |
1 |
225 |
||||
• 002869 |
63 |
66 |
||||
• 002870 |
22 |
|||||
• 002871 |
22 |
|||||
• 002872 |
134 |
|||||
• 002873 |
29 |
|||||
• 002874 |
1 |
78 |
139 |
|||
• 002875 |
156 |
|||||
• 002876 |
156 |
|||||
• 002877 |
156 |
|||||
• 002878 |
14 |
|||||
• 002884 |
29 |
23 |
||||
• 002885 |
50 |
|||||
• 002891 |
22 |
183 |
||||
• 002903 |
17 |
60 |
||||
• 002904 |
15 |
22 |
||||
• 002907 |
1 |
|||||
2020 год |
47 |
91 |
100 |
183 |
||
Среднее |
91 |
313 |
367 |
544 |
143 |
222 |
a
НомерЗУН |
I этап(дни) |
II этап (дни) |
III этап (дни) |
IV этап (дни) |
V этап(дни) |
VI этап (дни) |
• 002632 |
45 |
489 |
66 |
1152 |
||
• 002662 |
49 |
76 |
5 |
185 |
||
• 002663 |
20 |
633 |
204 |
963 |
||
• 002664 |
270 |
112 |
1 |
798 |
||
• 002678 |
55 |
247 |
399 |
844 |
834 |
934 |
• 002692 |
79 |
374 |
83 |
897 |
820 |
185 |
• 002728 |
867 |
164 |
660 |
31 |
||
• 002733 |
15 |
701 |
7 |
268 |
||
• 002734 |
15 |
350 |
631 |
587 |
8 |
184 |
• 002737 |
471 |
853 |
641 |
15 |
15 |
|
• 002749 |
727 |
660 |
909 |
863 |
||
• 002751 |
21 |
601 |
65 |
132 |
||
• 002752 |
1 |
205 |
760 |
1172 |
||
• 002754 |
43 |
34 |
740 |
116 |
||
• 002755 |
1 |
435 |
1 |
888 |
36 |
|
• 002761 |
694 |
752 |
||||
• 002763 |
132 |
126 |
388 |
|||
• 002765 |
874 |
22 |
589 |
123 |
||
• 002778 |
141 |
|||||
• 002779 |
678 |
92 |
412 |
262 |
||
• 002783 |
1 |
770 |
764 |
805 |
192 |
|
• 002784 |
1 |
9 |
471 |
192 |
8 |
|
• 002789 |
84 |
297 |
189 |
|||
• 002821 |
386 |
604 |
113 |
70 |
||
• 002822 |
371 |
220 |
||||
2018 год |
223 |
412 |
357 |
607 |
254 |
310 |
• 002824 |
15 |
496 |
198 |
163 |
||
• 002827 |
346 |
312 |
||||
• 002828 |
122 |
660 |
20 |
|||
• 002829 |
22 |
252 |
270 |
8 |
184 |
|
• 002839 |
59 |
36 |
||||
2019 год |
113 |
274 |
234 |
660 |
8 |
122 |
• 002848 |
29 |
13 |
185 |
|||
• 002855 |
58 |
|||||
• 002856 |
30 |
13 |
84 |
|||
• 002865 |
15 |
|||||
• 002886 |
80 |
|||||
• 002887 |
31 |
35 |
||||
• 002889 |
1 |
42 |
61 |
|||
• 002895 |
49 |
|||||
• 002896 |
1 |
59 |
||||
• 002897 |
15 |
12 |
||||
• 002902 |
15 |
|||||
• 002909 |
14 |
|||||
2020 год |
28 |
29 |
61 |
84 |
185 |
|
Среднее |
151 |
326 |
329 |
580 |
234 |
267 |
б
Рисунок 4 - Статистические данные по времени реализации отдельных этапов ЗУН по двум моделям автомобилей популярной марки (а, б)
мя требуется на реализацию 2 - 4 этапов: начало реализации ПКД, согласование ПР; выпуск ПИ; выпуск ГПП.
Наличие фактических статистических данных представленных в электронном виде обеспечивает возможность для проведения более глубокого анализа причин связанных с превышением сроков отработки отдельных этапов работы по улучшениям в соответствии с функционалом подразделений непосредственно принимающих участие в работе. Для повышения информативности разрабатываемого инструментария мониторинга, предлагается использовать модифицированные диаграммы Парето, на которых можно выделить цветом процентные доли этапов улучшений отработанных подразделениями по плану и (или) с нарушениями установленных временных нормативов.
Полученные результаты статистического анализа проблемы нарушения сроков реализации этапа начала реализации планов корректирующих действий представлены на рисунке 5, где данные диаграммы показывают, что основной причиной отклонений процесса является срыв сроков согласования изменений в конструкторской документации. Причем можно зафиксировать явных лидеров, на долю которых приходится значительный процент нарушений, в число которых входят: дирекция по закупкам (ДПЗ); служба главного конструктора (СГК); сборочно-кузовное производство (СКП); плановобюджетное управление.
Статистический анализ проблемы нарушения сроков реализации этапа по выпуску предварительного извещения об изменении конструкции изделия (ПИ) представлен в виде диаграммы на рисунке 6, по данным которой выделяем нарушителей сроков согласования ПИ, вносящим наибольшую долю по сорванным срокам: ДПЗ; СГК; СКП; управление по планированию и поставкам запасных частей (УПОЗЧ). По сути, имеем те же подразделения нарушителей, что и в предыдущем анализе.
Полученные результаты, дают пищу для размышления. В который раз мы убеждаемся в том, что вид деятельности не охваченный контролем не обеспечивает прогрессирующего развития. По сути, основной причиной низкой оперативности решения проблем качества продукции внутри предприятия является недостаточная исполнительская дисциплина как производственных, так и инжиниринговых подразделений, службы закупок и даже планово-бюджетного управления. То есть нарушения наблюдаются
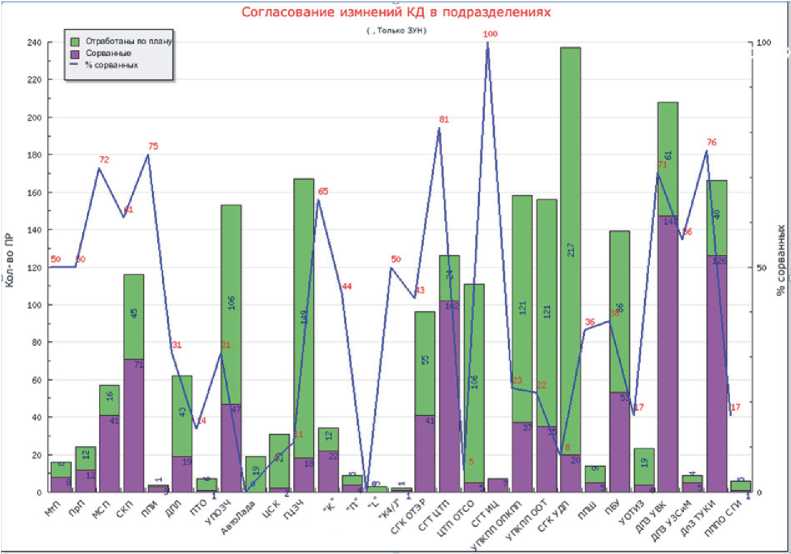
Рисунок 5 – Диаграмма статистического анализа прохождения этапа начала реализации ПКД
практически во всех подразделениях автопроизводителя, а это требует реализации мер, направленных на повышение ответственности подразделений, и более четкого определения стандартных сроков исполнения по отдельным этапам работ по устранению дефектов.
На рисунке 7, в виде диаграммы Парето, представлены обобщенные результаты статистического анализа по срокам согласования конструкторской документации (КД) на изменение изделий в рамках выполнения ЗУН за
11 месяцев 2019 г. Здесь выделены из массива данных по отдельным программам минимальные периоды времени и также выделены максимальные периоды времени согласования документации. При внимательном рассмотрении диаграммы представленной на рисунке 7, становится понятным масштаб проблемы. Вдумайтесь! В текущих, сегодняшних жестких условиях, на предприятии реально существуют подразделения, а главное работают реальные персонажи руководителей, где доля сорванных сроков при
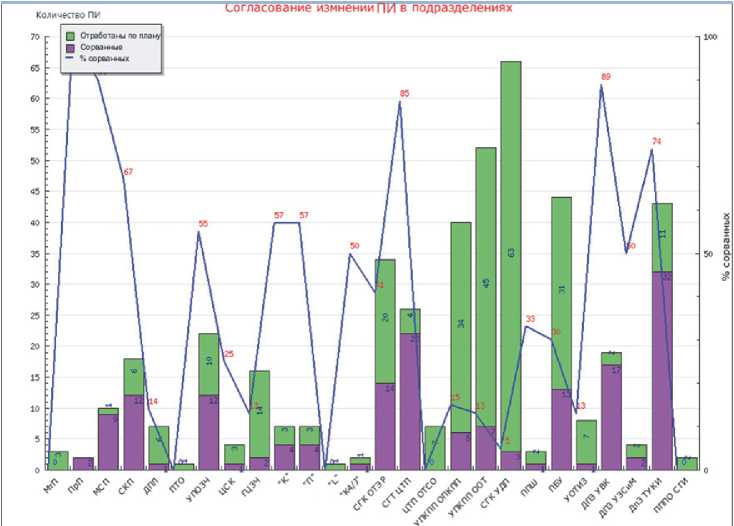
Рисунок 6 – Диаграмма статистического анализа прохождения этапа выпуска ПИ
реализации мероприятий направленных на улучшение качества продукции равна или приближается к 100%.
Совокупный статистический анализ проблемы срыва сроков реализации улучшений на начальном этапе, выпуска ПИ и графика подготовки производства (ГПП) представленый на рисунке 7 показывает что к выделенным ранее лидерам добавляются производственные подразделения: прессовое производство (ПрП); механосборочное производство (МСП); сборочнокузовное производство (СКП).
Резонный вопрос, вытекающий из анализа диаграммы представленной на рисунке 7: «А как же мы реально работали в области улучшения качества продукции с такими фактическими временными показателями?»
В результате проведенных исследований, становится понятно, что соответствующая деятельность направленная на решение проблем качества продукции в рамках улучшений нуждается в системном мониторинге, нормировании и установлении более жестких временных периодов отработки и согласования этапов улучшений, поскольку значения показателей времени на прохождение отдельных этапов мягко говоря не могут быть признаны адекватными. Например, для первой модели время прохождения 4 этапа в 2018 г. 568 дней, а для второй модели, соответствующий показатель составил 607 дней, что конечно сегодня может быть приемлемым.
Что предлагается сделать для определения обоснованных целевых показателей работы? Для ужесточения целевых значений времени прохождения этапов улучшений и согласований, в рамках проектов предлагается использовать функцию среднего статистического значения по всему массиву статистических данных рассматриваемых этапов, как это показано на рисунке 8 (например, оператор AVG в программном продукте Microsoft Excel).
На рисунке 8 мы видим три кривые, отражающие минимальное (зеленая), максимальное (красная) фактические и среднее статистическое (синяя) время прохождения этапов улучшений при проведении соответствующего мониторинга в течении практически полного года. Если в качестве целевого показателя выбрать среднее значение времени (108 дней), то сокращение времени реакции на запросы потребителей в рамках отдельных проектов по улучшению качества продукции может достигнуть 7 и более раз (по отношению к максимуму 838 дней).
Получаем целевые значения, которые после соответствующей формализации можно стандартизировать в актуализированной нормативной документации. Далее, добиваясь исполнения сроков согласования этапов улучшения качества продукции со стороны подразделений, необходимо пересматривать целевые показатели в сторону разумного уменьшения так, как это показано на рисунке 9.
Переходим к инструментам, определяющим деятельность по реагированию предприятия на проблемы качества в процессе производства продукции. Время локализации проблем качества продукции возникающей в процессе производства, наряду с вышеизложенными показателями, должно являться одним из важных индикаторов в оценке оперативности реакции
Доля сорванных сроков согласования ПР, ПИ, ГПП в %
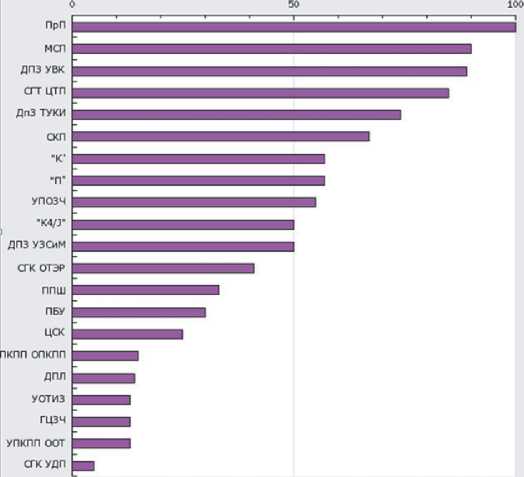
Рисунок 7 – Диаграмма Парето по обобщенным результатам статистического исследования по срывам сроков выполнения этапов 2 – 4 по реализации ЗУН
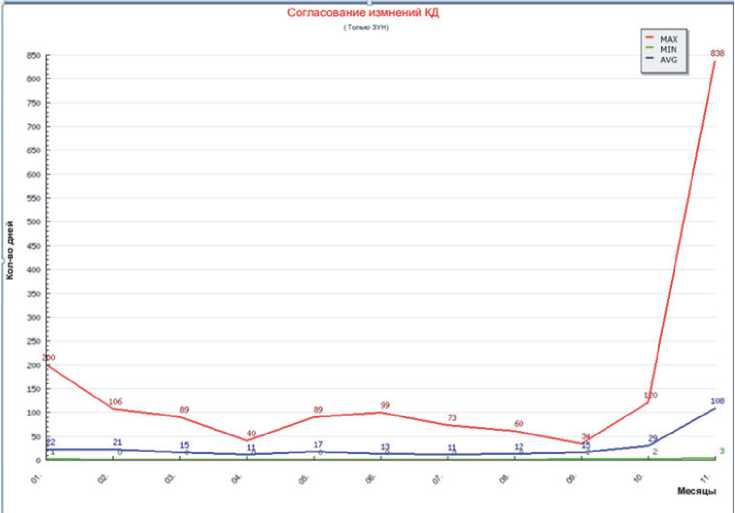
Рисунок 8 – Обобщенная диаграмма, отражающая затраты времени на согласование изменений КД в рамках решения проблем в области качества по программам ЗУН
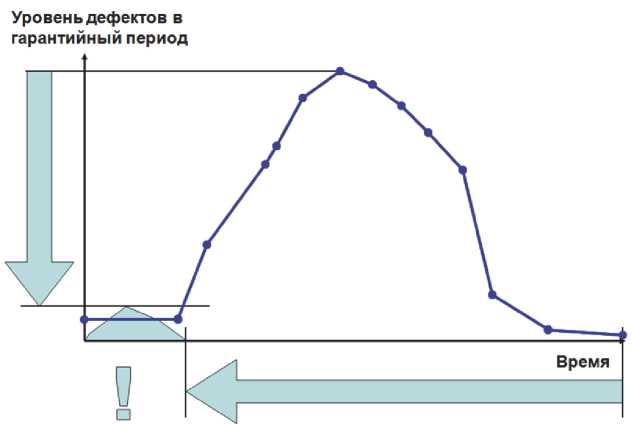
Рисунок 9 – Концепция повышения оперативности автопроизводителя при решении проблем в области качества продукции производителя на проблемы качества продук- В таблице 1 представлены данные отражаю-ции. И эта деятельность также нуждается в ин- щие существующие нормативы времени лока-струменте мониторинга и нормирования. лизации проблем без учета работы инструмента
Таблица 1 – Анализ времени на локализацию проблем качества продукции в производстве
Далее, нами проведена разработка и реализация инструмента мониторинга времени локализации проблем качества возникающих в реальном производстве автомобилей за 8 месяцев 2021 г. (рисунок 10). Было установлено, что в не охваченной системным мониторингом деятельности сложилась ситуация, при которой фактически установленные нормативы значительно превышают реальные сроки локализации проблем. И это тоже является недостатком, поскольку нормативы, которые в данном случае следует рассматривать как целевой показатель не обладает свойством напряженности, они не способствует улучшению процесса. Именно поэтому требуется актуализация целевого показателя времени локализации производственных проблем качества продукции. Но актуализация целевого показателя должна быть разумной, для ее проведения, в данном случае, совершенно точно требуется экспертная работа, результатом которой станет рациональный норматив времени локализации проблем качества продукции в производстве с учетом имеющихся возможностей. Но первичен в этой работе все же статистический анализ процесса, на основании которого можно выполнить требования по экспертной рационализации.
Именно поэтому соответствующий мониторинг нами проведен в 2021г. (рисунок 10). На ди- аграмме синяя кривая отражает максимальное, зеленая – минимальное, красная – статистически усредненное время локализации производственных проблем. Также как и в предыдущих случаях, использование разработанного статистического инструмента мониторинга времени локализации проблем качества обеспечивает возможность для разработки статистически адекватных целей для данной деятельности через усреднение показателя времени по всему массиву локализованных проблем. То есть в качестве целевого статистического можно рассматривать по кривой среднего значения времени локализации проблем количественный индекс примерно равный 4 часам (июльская точка). Этот аспект как раз освящен в таблице 1, в части определения цели на 2022 г. А в качестве дополнительного индикатора мониторинга, в данном случае может выступать такой показатель как количество локализованных дефектов в производстве с разбивкой по месяцам (рисунок 10). Ну а дальше – как сказано выше, экспертная работа и выработка нормативного целевого показателя.
Конечно, для стандартизации соответствующего вида деятельности, на предприятии должен быть разработан стандарт «Действие персонала при выявлении отклонений продукции в процессе изготовления» в части обеспечения защиты потребителя и определения четкого алгоритма взаимодействия между подразделениями и времени реагирования на проблемы.
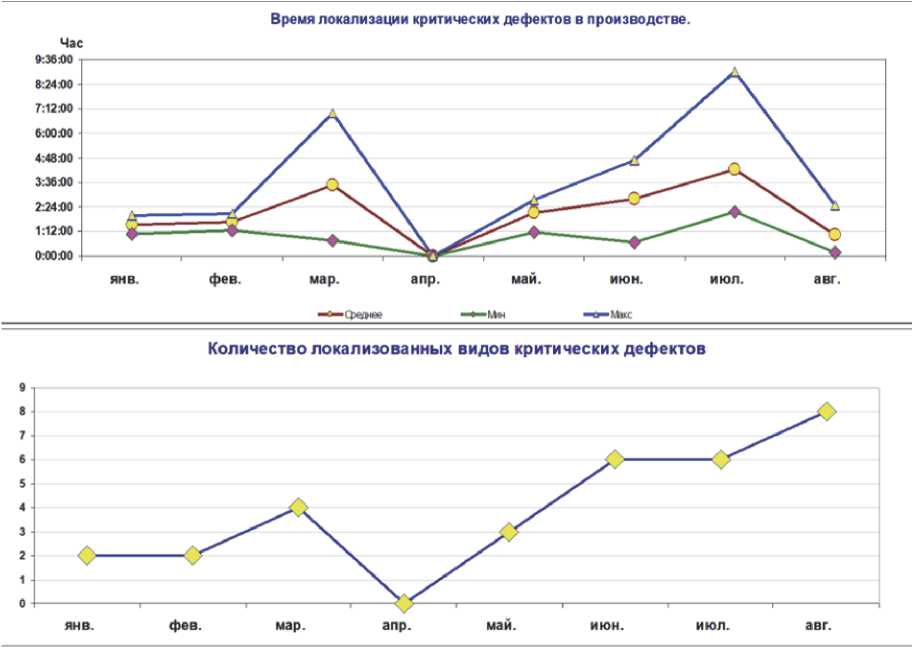
Рисунок 10 – Мониторинг времени и количества локализованных проблем качества в производстве
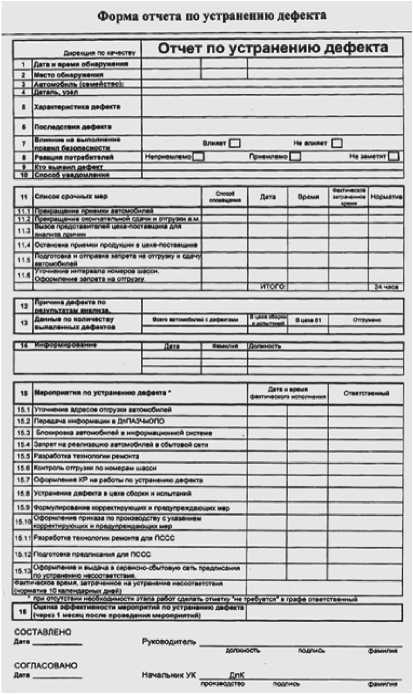
Спмаб r WMWnfNNU
CWCMCfOWtilWP
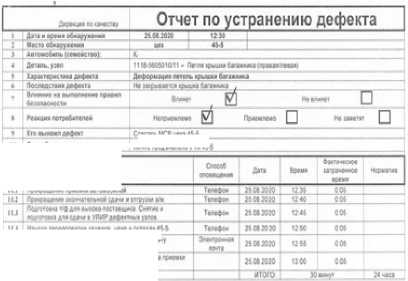
( 14 Ч>»^ УфареЛсне >4-^п11 •» Oh-дгИ]
№»Vt*u • отец aiwre «4 След» MCP mu Л^^прщ^нопксм COCTtiJlHO дмаякя СбКмйХадб Ли>а«аи б a Рисунок 11 – Стандартизированная форма (а) и пример отчета о локализации проблем качества в производстве (б) Элементы работы по соответствующему стандарту могут быть реализованы в виде формы отчета, пример которого представлен на рисунке 11. Используя предложенные статистические инструменты мониторинга качества на этапах жизненного цикла продукции, можно получать важную информацию о состоянии актуальных, нуждающихся в улучшении процессов производства, используя которую, в значительной степени повышается уровень оперативности реагирования предприятия на кризисы и изменение запросов потребителей в области качества продукции. Текущее положение дел в корпоративных подразделения занимающихся мониторингом и управлением качества на наших предприятиях требует первостепенного решения проблемы однозначного повышения значимости результатов объективного мониторинга качества продукции в процессе принятия решений верхнего уровня управления, а также повышения уровня информационно-технической компетентности кадров занимающихся анализом причин и последствий кризисов в области качества продукции и соответствующего технического оснащения рабочих мест.
Список литературы Статистические инструменты обеспечения оперативного мониторинга качества продукции на этапах жизненного цикла
- Благовещенский, Д.И. Разработка методологии и инструментария комплексной программы улучшений для повышения конкурентоспособности машиностроительных (автосборочных) предприятий: дис. ... д-ра техн. наук : 05.02.23 / Благовещенский Дмитрий Иванович; М-во науки и высш. образования Рос. Федерации, Самар. гос. техн. ун-т. - Самара, 2021.
- Козловский, В.Н. Обеспечение качества и надежности системы электрооборудования. Автореф. дис. ... д-ра техн. наук / Моск. гос. автомобил.-до-рож. ин-т (техн. ун-т). - Тольятти, 2010.
- Козловский, В.Н. Проблема стратегического планирования улучшения качества и надежности системы электрооборудования автомобилей / В.Н. Козловский, А.В. Заятров // Электроника и электрооборудование транспорта. - 2012. - № 1. - С. 44-47.
- Козловский, В.Н. Надежность системы электрооборудования легкового автомобиля / В.Н. Козловский, В.Е. Ютт // Электроника и электрооборудование транспорта. - 2008. - № 3. - С. 37-40.
- Kozlovskiy, V. Analytical models of mass as a method of quality management in the automotive industry / V. Kozlovskiy, D. Aydarov // Quality - Access to Success. - 2017. - Т. 18. - № 160.^ С. 83-87.