Структура напыленных покрытий типа Fe-C-Cr-Ti-Al после плазменного оплавления
Автор: Верхорубов Вадим Сергеевич, Коробов Юрий Станиславович, Филиппов Михаил Александрович, Щицын Юрий Дмитриевич, Невежин Станислав Владимирович, Неулыбин Сергей Дмитриевич
Журнал: Известия Самарского научного центра Российской академии наук @izvestiya-ssc
Рубрика: Механика и машиностроение
Статья в выпуске: 2-1 т.17, 2015 года.
Бесплатный доступ
В данной работе рассмотрено влияние плазменного оплавления на микроструктуру металлизационных покрытий из порошковых проволок системы легирования Fe-C-Cr-Ti-Al. Представлены результаты исследований структуры и микротвердости покрытий до и после плазменного оплавления.
Металлизационное покрытие, порошковая проволока, плазменное оплавление, структура, свойства, микротвердость
Короткий адрес: https://sciup.org/148203625
IDR: 148203625
Текст научной статьи Структура напыленных покрытий типа Fe-C-Cr-Ti-Al после плазменного оплавления
Газотермические покрытия находят широкое применение для защиты и восстановления деталей во многих отраслях промышленности. По технико-экономическим показателям среди методов газотермического напыления предпочтительной является дуговая металлизация (ДМ) [1, 2], а применение в качестве распыляемого материала порошковых проволок позволяет в значительных пределах варьировать систему легирования получаемых покрытий, путём добавления в шихту необходимых элементов, тем самым, придавая им необходимые характеристики [3].
Для повышения ресурса узлов оборудования, работающих в условиях абразивного изнашивания эффективно применяются напыленные покрытия из порошковых проволок ППМ-6 [4] и обладающие большей износостойкостью – ППМ-8 [5] системы легирования Fe-C-Cr-Ti-Al. Но условия формирования ДМ покрытий обуславливают ряд характерных дефектов, к числу которых
можно отнести: сравнительно низкую адгезию к основному металлу (20–35 МПа), пористость и неоднородность структуры. В условиях трения скольжения со смазкой пористость повышает износостойкость покрытий вследствие хорошей маслоудерживающей способности пор. Однако в условиях абразивного износа и трения скольжения без смазки наблюдается интенсивная потеря массы покрытия в результате микрорезания, при попадани абразивных частиц в поры покрытия, и когезионного отрыва отдельных частиц и кон-гломерированных участков покрытия, в зонах покрытия с ослабленной когезионной прочностью [6, 7]. Также пористость покрытий может привести к началу коррозионных процессов на границе основа-покрытие. Для улучшения сцепления напыленных покрытий и снижения пористости их подвергают последующему оплавлению концентрированными источниками нагрева [8–12]. По параметрам стоимости и мобильности оборудования наиболее перспективными являются плазменные источники нагрева [13].
Данная работа проводилась с целью определения влияния плазменного оплавления на структурные характеристики покрытий, полученных методом активированной дуговой металлизации из порошковых проволок системы легирования Fe-C-Cr-Ti-Al.
МЕТОДЫ ИССЛЕДОВАНИЙ
В качестве основы для нанесения покрытий были использованы пластины из стали 40 по ГОСТ 1050-88 размерами 240×70×10. Напыляемый материал – порошковая проволока марки ППМ-8 Ø 2 мм состава 80Х22Т2Ю2.
Перед нанесением покрытия производилась дробеструйная обработка поверхности покрытия. Параметры дробеструйной обработки представлены в табл. 1.
Таблица 1. Параметры предварительной дробеструйной обработки
Абразив |
Дистанция, мм |
Давление воздуха, МПа |
Угол атаки, град. |
Дробь чугунная колотая ДЧК 1-1,2 по ГОСТ 11964-81 |
150 |
0,6 |
70-90 |
Для нанесения покрытий толщиной 1,7–2 мм использовали аппарат активированной дуговой металлизации АДМ-10 [1]. Напыление производилось под прямым углом к поверхности изделия, на параметрах, представленных в табл. 2.
Плазменное оплавление металлизационного покрытия осуществлялось на оборудовании, разработанном на кафедре «СП и ТКМ» ПНИПУ [14]. В качестве защитного и плазмообразующего газа использовался аргон. Параметры режима плазменной обработки приведены в табл. 3.
Из пластины с нанесенным металлизаци-онным покрытием, до и после плазменного оплавления, с помощью электроэрозионного проволочно-вырезного станка AGIE CHARMILLES CUT 20 были вырезаны образцы размерами – 10×10×10 мм. Подготовка шлифов для проведения металлографических исследований напыленных и оплавленных покрытий выполнялась на станке Labopol с использованием пасты ГОИ № 2 и алмазной пасты НОМ 60/40. Травление образцов выполнялось царской водкой.
Микроструктурные исследования выполнены на металлографическом микроскопе Альтами, микротвердость с поверхности покрытий и по их сечению измеряли на микротвердомере Shimadzu HMV-G21DT при 0,5 Н (50 гс) и 3 Н (300 гс), рентгенофазовый структурный анализ определяли на дифрактометре Bruker D8 Advance в Cr-kα излучении.
РЕЗУЛЬТАТЫ И ИХ ОБСУЖДЕНИЕ
Металлизационное покрытие имеет характерную для всех видов напыления шероховатую поверхность (рис. 1, а). После плазменного оплавления покрытие напоминает наплавленный металл (рис. 1, б). На поверхности покрытия наблюдается появление шлаковых корок, и довольно крупных раковин, размерами 0,2–1,0 мм, образование которых, вероятно, связано с выходом на поверхность оксидов и газов, расположенных в порах покрытия, под действием конвективных потоков в сварочной ванне.
Покрытие имеет слоистую структуру (см. рис. 2), характерную для напыленных покрытий, и состоит из сильно деформированных зерен – ламелей, толщиной 5–10 мкм. Толщина покрытия составляет 1840 мкм. Видно, что покрытие характеризуется зна-
Таблица 2. Параметры режима активированной дуговой металлизации
Ток, А |
Напряжение, В |
Скорость перемещения пистолета, м/ч |
Дистанция напыления, мм |
Давление воздуха, МПа |
Давление пропана, МПа |
200 |
28 |
360 |
100 |
0,30 |
0,32 |
Таблица 3. Параметры режима плазменного оплавления
Ток, А |
Диаметр сопла, мм |
Скорость обработки, м/ч |
Дистанция обработки, мм |
Расход плазмообразующего газа, л/мин |
Расход защитного газа, л/мин |
160 |
4 |
6 |
5 |
2,5 |
4,5 |
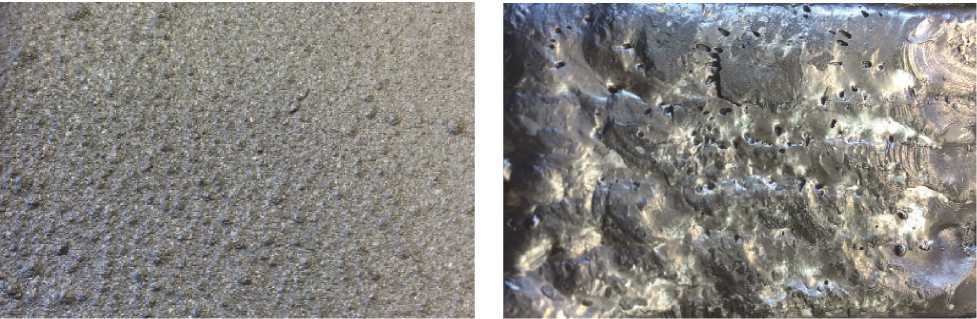
а) б)
Рис. 1. Поверхность металлизационного покрытия: а – до плазменного оплавления; б – после плазменного оплавления
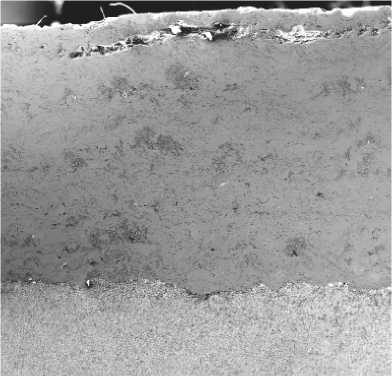
Рис. 2. Макрошлиф напыленного
АДМ покрытия (×50)
чительной неоднородностью структуры, наличием пор и несплошностей . Трещин в покрытии не обнаружено. Граница между покрытием и основанием имеет характерный зигзагообразный вид. В процессе напыления произошло хорошее соединение с основанием, о чем говорит отсутствие темной оксидной прослойки на границе покрытия с основой .
ных частицах покрытия наблюдается структура точечного характера, похожая на отпущенный мартенсит с включениями дисперсных карбидов.
Раковин, наблюдаемых на поверхности оплавленного покрытия, в поперечном сечении полученных образцов не обнаружено (рис. 4). Плазменная поверхностная обработка напыленного покрытия привела к его полному переплаву и устранению структурных неоднородностей. Толщина переплавленного покрытия составляет 2380 мкм. Следовательно, по изменению толщины покрытия, смешение с основой после плазменного оплавления составляет примерно 30 %.
Покрытие имеет однородную структуру, в которой, на первый взгляд, отсутствуют оксидные фазы, в большом количестве имевшиеся в исходном напыленном покрытии. Однако на снимке поперечного сечения, нетравленого образца, при увеличении в 1000 раз видны черные вкрапления круглой формы, размером до 2 мкм (см. рис. 5, а), предположительно оксидов. На снимке протравленного образца видно, что данные включения и карбиды, располагаются преимущественно по границам зерен (см. рис. 5, б).
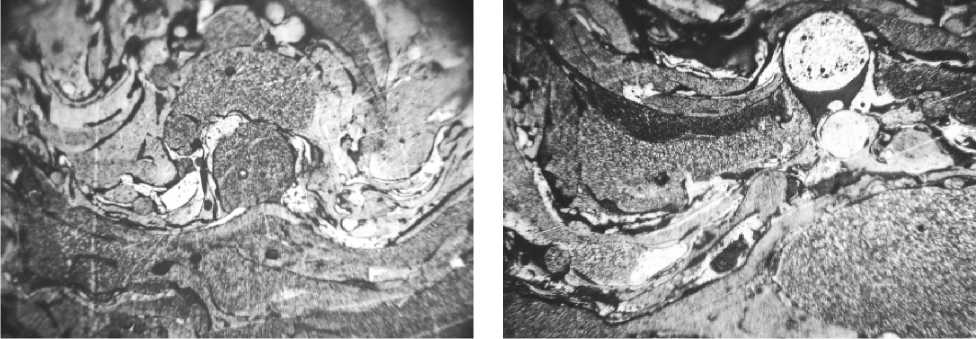
а) б)
Рис. 3. Микроструктура напыленного АДМ покрытия (×1000)
Травление выявляет несколько характерных цветов и оттенков структурных составляющих (см. рис. 3). Покрытие представляет собой тонкие чередующиеся волнообразные прослойки белого, серого и чёрного цвета, различной величины и конфигурации. Также наблюдается включения довольно крупных частиц более округлой и глобулярной формы (см. рис. 3, б). Кроме того, присутствуют поры глобулярной и дискообразной формы. Очевидно, что участки темно-серого и черного цвета являются оксидными прослойками. Слабое воздействие травителя на белые структурные составляющие, говорит о том, что это металлическая матрица с большим содержанием легирующих элементов. Эти металлические фрагменты представляют собой твёрдый раствор хрома в аустените и мартенсите. В наиболее круп-
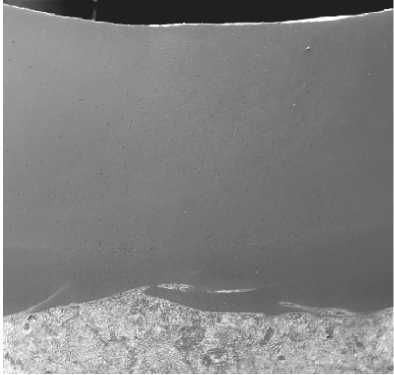
Рис. 4. Макрошлиф металлизационного покрытия после плазменного оплавления (×50)
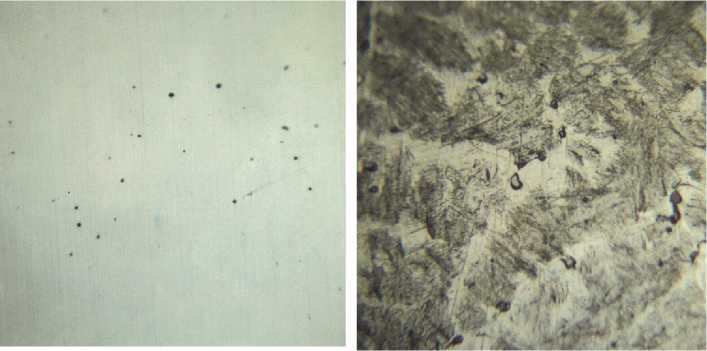
a
б
Рис. 5. Поперечный шлиф оплавленного покрытия (×1000): а – до травления, б – после травления
Металлографическое изучение поперечных шлифов показало, что зона сплавления и ЗТВ имеют типичный для наплавленных покрытий вид (см. рис. 6, а и б). В прилегающем к оплавленному покрытию слое основного металла наблюдается тонкая (50 мкм) зона обезуглероживания (см. рис. 6, б). При большом увеличении по всему сечению покрытия наблюдается игольчатая структура мартенсита (см. рис. 5, б). Структура переплавленного покрытия имеет дендритное строение и состоит из четырёх основных характерных зон в порядке их расположения от основного металла к поверхности оплавления (см. рис. 6, а):
-
1. К основной стали примыкает слой мелкозернистого переплавленного покрытия толщиной 50–150 мкм, состоящего из равноосных зёрен 8–9 баллов.
-
2. К 1-му слою примыкает тонкий слой до 50 мкм равноосных зерна несколько более крупнозернистого (6–7 балл) металла. 1 и 2 слои по структуре представляют собой пакетный мартенсит (см. рис. 6, б), характерный по морфологии для мало- и среднеуглеродистых сталей с содержанием углерода до 0,5–0,6 % [15], содержащий выделения дисперсных карбидов.
-
3. 1 и 2-й слои равноосных зёрен переходят в основной слой вытянутых столбчатых зёрен длиной до 500 мкм (см. рис. 6, в), ориентированных преимущественно перпендикулярно или под небольшим углам к поверхности раздела переплавленного и основного металла. Структура зёрен представляет собой пакетный мартенсит 1ой–2х ориентировок, окруженный тонкой оболочкой карбидной эвтектики.
-
4. Верхняя часть переплавленного покрытия (см. рис. 6, г) толщиной до 500 мкм состоит из равноосных зёрен размером 20–50 мкм, состоящих из мартенсита с выделением дисперсных карбидов.
Такая разница в структуре оплавленного покрытия обуславливается различием скоростей охлаждения. Примыкающий к основе нижний слой быстро кристаллизуется в результате отвода тепла в подложку, с высоким коэффициентом теплопроводности. Ближе к середине расплавленного покрытия скорости охлаждения ниже, охлаждение имеет направленный характер, в сторону подложки, вследствие чего образуется структура вытянутых, вертикально направленных дендритов. В результате равномерного прогрева оплавленного слоя направленное охлаждение металла уменьшается, что приводит к образованию равноосных зерен.
Рентгеноструктурный анализ полученных покрытий до и после оплавления подтверждает результаты металлографии. Структура металлической основы напыленного покрытия до оплавления представляет собой мартенсит (75 %) и остаточный аустенит (25 %), тогда как после плазменного оплавления практически отсутствует остаточный аустенит, который перешел в мартенсит (98 %).
Изучение структуры полученных покрытий дополнены замерами микротвердости по толщине покрытий, от поверхности до основы (рис. 7). В поле исследования попадали участки как чистого металла, так и оксидных прослоек в металлиза-ционном покрытии.
Исходное покрытие, полученное методом АДМ, характеризуется значительной неравномерностью микротвердости по толщине покрытия, что свидетельствует о наличии пор, несплош-ностей, структурных и фазовых неоднородностей. Значения микротвердости меняются в пределах от 200 до 650 HV. При этом микротвердость, измеренная при нагрузках 50 и 300 гс, имеет близкие значения.
Плазменная обработка покрытия привела к его переплавлению и существенному изменению структуры и микротвердости. Микротвердость покрытия значительно возросла: до 800 HV0,3 (рис. 7) При этом отмечается ее более равномер-
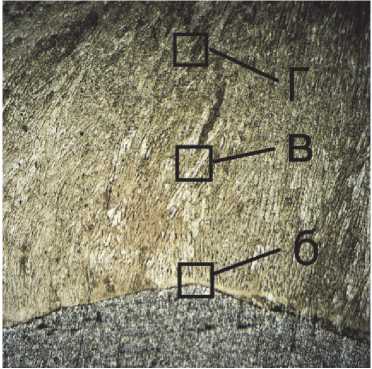
a
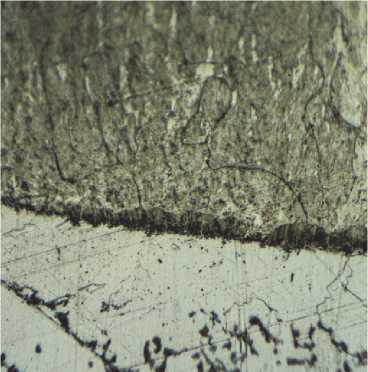
б
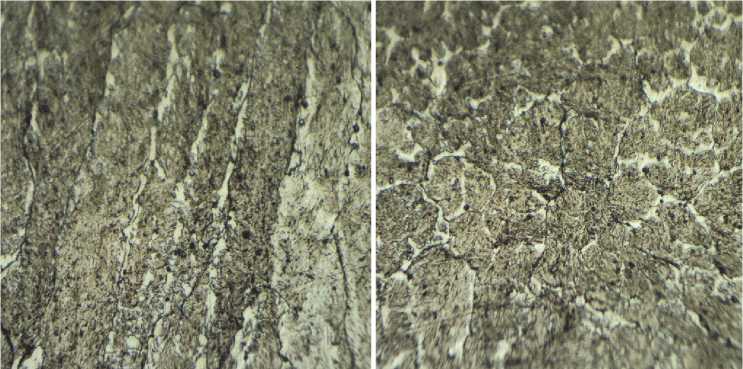
в
г
Рис. 6. Микроструктура оплавленного покрытия после травления: а – общий вид (×40), б – переходная зона (×400), в – столбчатый слой (×400), г – поверхностный слой (×400)
ное распределение по толщине покрытия, что обусловлено однородной структурой покрытия, отсутствием оксидных прослоек, пористости и несплошностей, а также равномерным распределением химических элементов в покрытии с образованием дисперсных упрочняющих фаз. Однако, при снижении нагрузки на индентор наблюдается повышение среднего значения микротвердости от 753 HV0.3 до 831 HV0.05 (рис. 8). Это объясняется наличием, рассмотренных ранее (см.
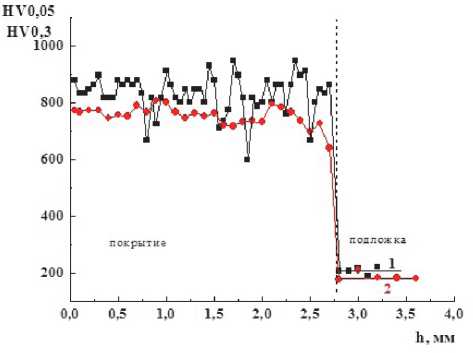
Рис. 8. Изменение микротвердости по толщине
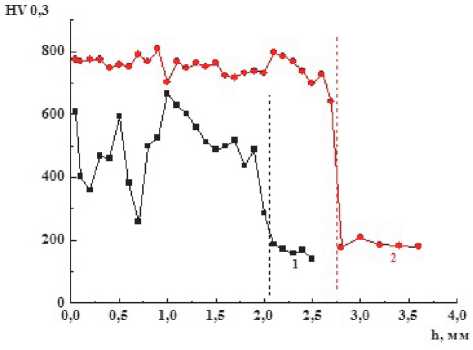
Рис. 7. Изменение микротвердости по толщине покрытия в исходном (1) и оплавленном (2) состоянии, при нагрузке на индентор 300 гс
покрытия с последующей плазменной обработкой, при нагрузке на индентор 50 гс (1) и 300 гс (2)
рис. 5, а), структурных микронеоднородностей в оплавленном покрытии. При повышении нагрузки на индентор, большее число неоднородностей попадает в исследуемую область, что приводит к снижению среднего уровня твердости. Следовательно, наблюдаемые микронеоднородности имеют твердость ниже, чем основной металл.
Такое значительное повышение твердости, очевидно, связано с образованием плотной мартенситной структуры покрытия. Также можно отметить, что исходя из представленных графиков, плазменная обработка не оказывает влияния на твердость основы.
ВЫВОДЫ
Покрытие в исходном состоянии характеризуется значительной неоднородностью структуры, наличием пор, несплошностей и оксидных прослоек, свойственных напыленному металлу, что объясняет сильный разброс значений микротвердости по толщине покрытия.
Плазменная обработка металлизационного покрытия приводит к его полному переплав-лению, существенному изменению структуры и равномерному распределению химических элементов. Образование кристаллов мартенсита внутри дендритных осей и уплотнение покрытия приводит к значительному повышению микротвердости. Однако в покрытии сохраняется некоторая неоднородность в виде микроскопических оксидных включений округлой формы.
Список литературы Структура напыленных покрытий типа Fe-C-Cr-Ti-Al после плазменного оплавления
- Коробов Ю.С. Эффективность применения активированной дуговой металлизации для нанесения защитных покрытий//Сварочное производство. 2005. № 2. С. 47-49.
- Структура и свойства покрытий из стали 40Х13, полученных с использованием различных методов газотермического напыления/П.А. Витязь, М.А. Белоцерковский, В.А. Кукареко и др.//Физическая мезомеханика. 2002. № 5. С. 29-36.
- Структура и трибо-технические характеристики покрытий, полученных электродуговой металлизацией с использованием порошковой проволоки/В.И. Похмурский, М.М. Студент, В.М. Довгунык и др.//Автоматическая сварка. 2003. № 8. С. 13-17.
- Структура и износостойкость напыленных покрытий системы Fe-Cr-C-Ti c метастабильным аустенитом/Ю. С. Коробов, В. И. Шумяков, М. А. Филиппов //Инновации в материаловедении и металлургии: материалы III Междунар. интерактив. науч.-практ. конф., Екатеринбург: Изд-во Урал. ун-та, 2013. С. 100-104.
- Экономнолегированная порошковая проволока для повышения ресурса эксплуатации плунжеров гидропрессов методом дуговой металлизации/Г.А. Ример, В.С. Верхорубов, С.В. Невежин, Ю.С. Коробов, М.А. Филиппов//Сборник докладов научно-технической конференции «Сварка и диагностика». Екатеринбург, 2014. с. 105-111.
- Lima C.R.C., Bette B.V., Camargo F., Fals H.C., Ferraresi V.A. Wear Performance of Thermally Sprayed and Welded Coatings Using Conventional and Nanostructured Materials. Proc. of ITSC 2013, ASM International: Busan, Korea, 2013. P. 424-428
- Утенков В.М., Зайцев А. Н. Исследование триботехнических характеристик перспективных износостойких плазменных покрытий при трении скольжения без смазки//Известия высших учебных заведений. Машиностроение, 2013. № 11. С.81-89.
- Исследование структуры и свойств никелевых порошковых покрытий после оплавления/В.А. Клеменов, В.Е. Панин, В.П. Безбородов и др.//Физика и химия обработки материалов. 1997. № 6. С. 68-75.
- Спиридонов Н.В., Кардаполова М.А., Девойно О.Г. Влияние лазерного нагрева на износостойкость композиционных покрытий//Трение и износ. 1988. т. 9. № 1. С. 60-65.
- Pokhmurs’ka H., Chervins’ka N., Student M., Zadorozhna Kh. Effect of the laser fusion of electrometallized coatings of the Fe-Cr-B-Al system on their corrosion resistance//Materials Science, Vol. 42, No. 6, 2006, P. 837-842.
- Pokhmurs’ka H.V., Dovhunyk V. M., Student M.M. Wear resistance of laser-modified arc-sprayed coatings made of FMI-2 powder wires//Materials Science, 2003. Vol. 39. No. 4. P. 533-538.
- Pukasiewicz A.G.M., Alcover Jr.P.R.C., Capra A.R., Paredes R.S.C. Influence of Plasma Remelting on the Microstructure and Cavitation Resistance of Arc-Sprayed Fe-Mn-Cr-Si Alloy//Journal of Thermal Spray Technology, 2014. Vol. 23 (1-2). P. 51-59.
- Щицын Ю.Д. Плазменные технологии в сварочном производстве. Ч.1. Пермь: Перм. гос. техн. ун-т., 2004. 73 с.
- Плазменная закалка тяжелонагруженных деталей из стали 40Х13/Д.С. Белинин, В.С. Верхорубов, П.С. Кучев, Н.Н. Струков, Ю.Д. Щицын//Вестник Пермского государственного технического университета, 2011. Т. 13. № 3. С. 12-18.
- Гуляев А.П., Гуляев А.А. Металловедение: учебник для вузов. 7-е изд., перераб. и доп. М.: АльянС, 2011. 643 с.