Структурно-фазовые состояния и напряжение течения при пластической деформации стали 12Х18Н10Т
Автор: Тусупжанов А.Е., Ерболатулы Д., Квеглис Л.И.
Журнал: Журнал Сибирского федерального университета. Серия: Техника и технологии @technologies-sfu
Статья в выпуске: 4 т.12, 2019 года.
Бесплатный доступ
В статье представлены результаты структурно-фазовых превращений и их корреляции с микротвердостью в стали 12Х18Н10Т после термомеханической обработки и высокотемпературной пластической деформации. Сделаны оценки истинных напряжений при одноосном растяжении.
Пластическая деформация, структурно-фазовое состояние, нержавеющая сталь, мартенсит
Короткий адрес: https://sciup.org/146281208
IDR: 146281208 | DOI: 10.17516/1999-494X-0150
Текст научной статьи Структурно-фазовые состояния и напряжение течения при пластической деформации стали 12Х18Н10Т
Как известно, сталь 12Х18Н10Т широко используется в промышленности как коррозионностойкий и износоустойчивый материал. Этот матераил применяется в ядерном реакторо-строении [1-3].
Пластичность, обусловленная мартенситным γ→α′-превращением, аустенитных сталей при низких температурах описана в работе [4]. Это превращение влияет на величину деформационного упрочнения и локализацию течения материала. Интенсивность образования мартенсита зависит от степени термической стабильности исходной γ-фазы (аустенита) и от термомеханической обработки. Старение и подбор оптимальной температуры приводит к более быстрому γ→α′-превращению [4]. Можно предположить, что большая доля мартенсита способна увеличить степень деформации при высокотемпературной деформации сталей. Ранее нами была изучена сверхпластичность превращения с Co-Ni-Nb сплава в работах [5, 6]. В работе [5] описана наша методика для определения истинных напряжений. Эта методика была апробирована на сплавах, где при высокотемпературной деформации происходит фазовое превращение.
В данной работе исследуются структурно-фазовое состояние и высокотемператураная деформация стали 12Х18Н10Т, обладающие уникальными физическими свойствами. Цель работы – исследовать структурно-фазовое состояние стали до и после пластической деформации при высоких температурах [7].
Материалы и методы исследования
Сталь 12Х18Н10Т применяется в качестве коррозионностойкого и жаропрочного материала и имеет следующий химический состав: основа Fe, 0,12%-С, 18%-Ni, 10%-Тi. Термическая обработка стали производилась в муфельной печи СОУЛ-4 с использованием кварцевой труб-– 439 – ки, где создавался вакуум не менее 10-3 МПа. Закалку проводили в воде комнатной температуры. Прокатку стали осуществляли на прокатном стане стандартного изготовления. Высокотемпературная пластическая деформация стали проводилась в испытательной машине 1246Р, где создавался вакуум не менее 10-5 МПа. Исследование микроструктуры проводили на оптическом микроскопе Неофот-21 и сканирующем электронном микроскопе JSM-6390LV производства компании JEOL Ltd. (Япония) с системой энергодисперсионного микроанализа INCA Energy Penta FET X3 компании OXFORD Instruments Analytical Limited. Фазовый состав образцов исследовали на рентгеновском дифрактометре ДРОН-3 с гониометрической приставкой ГП-13 с применением кобальтового и медного излучения, а также на мессбауеровском спектрометре МС1104ЕМ с 57Со-источником гамма-кванттов.
Результаты и их обсуждение
Для исследования эволюции структурно-фазовых превращений после термомеханической обработки и высокотемпературной пластической деформации нами была изучена структура стали после прокатки и отжига. В исходном состоянии структура стали имеет множество двойников, размер зерен составляет 〈 d 〉 = 19 мкм (рис. 1 а ). После прокатки на 80 % микроструктура стали плохо выявляется, наблюдается лишь деформационный рельеф в виде волокон текстуры вдоль одного направления (рис. 1 б ). При низкотемпературном отжиге прокатанной стали не отсутствуют рекристаллизационные процессы, структура является волокнистой с темными участками (рис. 1 в ). Дальнейшее увеличение температуры обработки приводит к образованию темных участков. Это области обратного мартенситно-аустенитного превращения, о чем свидетельствуют данные рентгеноструктурного анализа (рис. 3 в ). В отличие от низкотем-
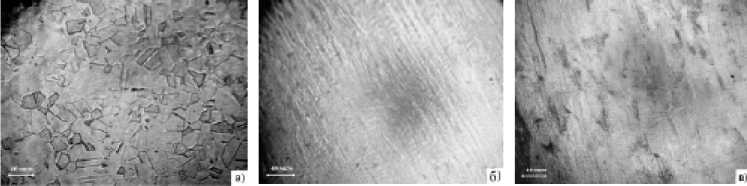
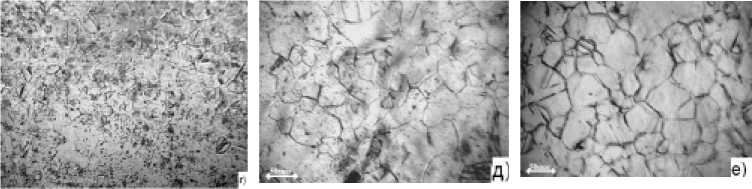
Рис. 1. Микроструктура стали 12Х18Н10Т: а) исходное состояние; б) прокатка на 80 %; в) прокатка на 80 % + отжиг при 600 °С (30 мин); г) прокатка на 80 % + отжиг при 920 °С (30 мин); д) прокатка на 80 % + отжиг при 1000 °С (30 мин); е) прокатка на 80 % + отжиг при 1200 °С (30 мин)
Fig. 1. The microstructure of steel 12Cr18Ni10Ti: a) initial condition; б) 80 % rolling; в) rolling for 80 % + annealing at 600 °С (30 min); г) rolling at 80 % + annealing at 920 °С (30 min); д) rolling at 80 % + annealing at 1000 °С (30 min); e) rolling at 80 % + annealing at 1200 °С (30 min)
пературного отжига при температурах выше 920 °С микроструктура стали выявлена в виде рекристаллизованных зерен (рис. 1 г, д, е ) и рентгенограммы (рис. 3 г, д, е ) соответственно. По фотографиям микроструктуры (рис. 1 д, е ) стали видно, что при высоких температурах отжига выше 1000 °С происходит рост зерен аустенита. Так, при 1000 °С средний размер зерен 〈 d 〉 = 37,3 мкм, 1100 °С – 〈 d 〉 = 35,3 мкм, 1200 °С – 〈 d 〉 = 45,8 мкм (рис. 1 д, е ).
Также нами проведены микроструктурные исследования на растровом электронном микроскопе с приставкой для энергодисперсионного анализа «INCA Energy». Как видно на рис. 2 а , особого различия между химическими составами не наблюдается, что косвенно подтверждает образование мартенсита деформации при прокатке стали, поскольку мартенсит образуется без-диффузионным методом [8]. После отжига при 920 °С также отсутствуют изменения в химическом составе (рис. 2 б ).
Рентгенодифракционные исследования образцов стали в исходном и отожженных состояниях приведены на рис. 3. Сначала сталь находится в γ -аустенитном состоянии (рис. 3 а ) с ГЦК-решеткой с параметром решетки а = 3,59 Å . А после прокатки на 80 % сталь полностью переходит в α′ -железо с параметром решетки α α = 2,875 Å (рис. 3 б ) [9]. Мартенситные превращения γ -Fe в α′ -фазу происходят в условиях пластической деформации, которые связаны с избыточными объемами в локальных наномасштабных областях [10, 11].
На дифрактограмме образцов после отжига при 600 °С наблюдается появление линий γ -Fe (аустенита), а также изменение соотношения интенсивностей линий α′ -фазы (рис. 3 в ), свиде-
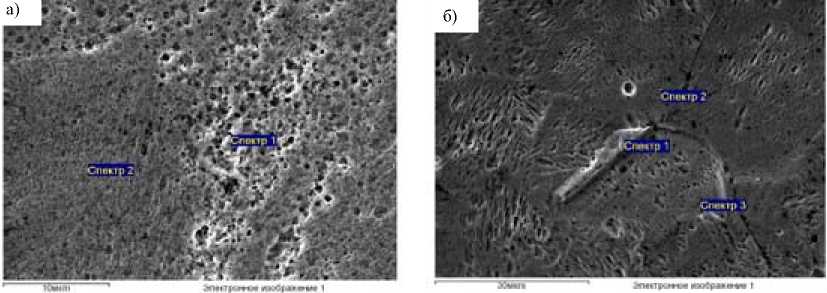
Спектр |
В стат. |
Si |
Cr |
Mn |
Fe |
Ni |
Итог |
Спектр 1 |
Да |
0.40 |
19.69 |
71.94 |
7.97 |
100.00 |
|
Спектр 2 |
Да |
0.53 |
18.94 |
1.34 |
71.45 |
7.74 |
100.00 |
Спектр 3 |
Да |
0.43 |
19.72 |
72.02 |
7.83 |
100.00 |
|
Макс. |
0.53 |
19.72 |
1.34 |
72.02 |
7.97 |
||
Мин. |
0.40 |
18.94 |
1.34 |
71.45 |
7.74 |
Спектр |
В стат. |
Si |
Cr |
Mn |
Fe |
Ni |
Итог |
Спектр 1 |
Да |
19.22 |
0.93 |
71.63 |
8.22 |
100.00 |
|
Спектр 2 |
Да |
0.46 |
18.85 |
1.26 |
71.61 |
7.82 |
100.00 |
Макс. |
0.46 |
19.22 |
1.26 |
71.63 |
8.22 |
||
Мин. |
0.46 |
18.85 |
0.93 |
71.61 |
7.82 |
Рис. 2. Микроструктура и микроанализ стали 12Х18Н10Т: а) прокатка на 80 % + отжиг при 600 °С; б) прокатка на 80 % + отжиг при 920 °С
Fig. 2. Microstructure and Microanalysis of steel 12Cr18Ni10Ti: a) rolling at 80 % + annealing at 600 °С; б) rolling at 80 % + annealing at 920 °С
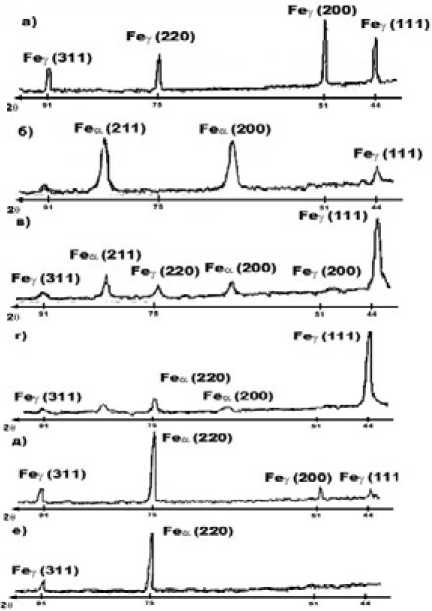
Рис. 3. Фрагменты дифрактограмм стали 12Х18Н10Т: а) исходное состояние; б) прокатка на 80 %; в) прокатка на 80 % + отжиг при 600 °С (30 мин); г) прокатка на 80 % + отжиг при 920 °С (30 мин); д) прокатка на 80 % + отжиг при 1000 °С (30 мин); е) прокатка на 80 % + отжиг при 1200 °С (30 мин)
Fig. 3. Fragments of diffractograms of steel 12Cr18Ni10Ti: a) initial condition; б) 80 % rolling; в) rolling for 80 % + annealing at 600 °С (30 min); г) rolling at 80 % + annealing at 920 °С (30 min); д) rolling at 80 % + annealing at 1000 °С (30 min); e) rolling at 80 % + annealing at 1200 °С (30 min)
тельствующие о снятии внутренних напряжений при отжиге. Отжиг при 700-800 °С не вызвал значительных фазовых изменений. Лишь линии γ -Fe (аустенита) стали более выраженными. Важным экспериментальным данным является то, что в данной работе установлен верхний температурный предел перехода α′ -фазы в γ -Fe для образцов, предварительно прокатанных на 80 %, – 920 °С (рис. 3 г ). Дальнейшее увеличение температуры отжига приводит лишь к росту интенсивности пиков от γ -Fe (рис. 3 д ). Также установлено, что повышение температуры отжига стали вызывает увеличение параметров решетки аустенита и мартенсита, так, после отжига при 700 °С параметры решеток а а = 2,878 А, a Y = 3,6 А .
Повышение температуры отжига приводит к резкому увеличению среднего размера зерна, что отрицательно влияет на эксплуатационные свойства стали. На рис. 4 представлены изменения микротвердости после различных обработок. В исходном состоянии микротвердость стали равна Н = 2507 МПа. После прокатки происходит увеличение микротвердости до Н = 5372 МПа из-за образования мартенсита деформации (рис. 3б). При обработке прокатки на 80 % и отжиге при 600 °С наблюдается уменьшение микротвердости до Н = 4566 МПа. Дальнейшее увеличение температуры отжига приводит к постепенному уменьшению микро-– 442 – твердости, так, при температуре отжига 920 °С микротвердость образца равна Н = 1883 МПа (рис. 4).
Исследования фазового состава на мессбауеровском спектрометре МС1104ЕМ с 57Со-источником гамма-квантов подтверждают результаты, полученные ранее. Как показано на рис. 5 а, в исходном состояниии сталь находится в аустенитном состоянии, как известно, ау-
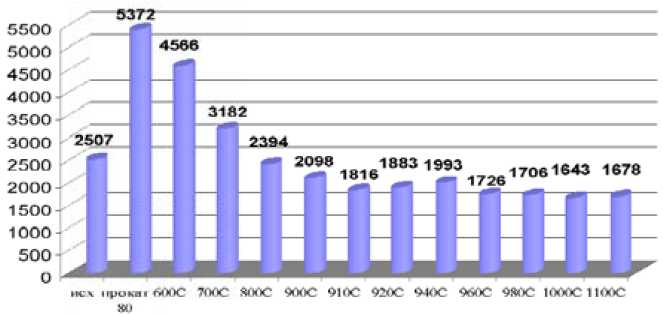
Рис. 4. Микротвердость стали 12Х18Н10Т после различных обработок
Fig. 4. Microhardness of steel 12Cr18Ni10Ti after various treatments
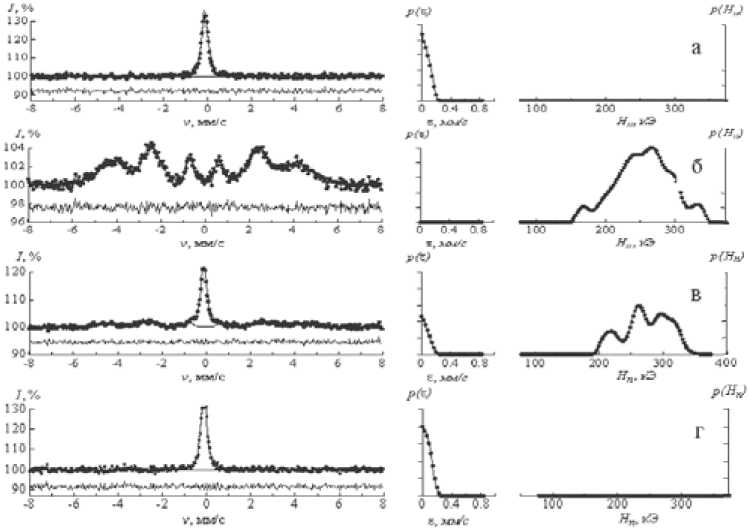
Рис. 5. Мессбауеровские спектры стали 12Х18Н10Т: а) исходное состояние; б) прокатка на 80 %; в) прокатка на 80 % + отжиг при 600 °С (30 мин); г) прокатка на 80 % + отжиг при 1000 °С (30 мин)
Fig. 5. Mössbauer spectra of steel 12Cr18Ni10Ti: a) initial condition; б) 80 % rolling; в) rolling for 80 % + annealing at 600 °С (30 min); г) rolling at 80 % + annealing at 1000 °С (30 min)
стенит является немагнитной фазой. У прокатанных на 80 % образцов стали мессбауеровские спектры отличаются от исходных (рис. 5 а, б ). В исходном состоянии наблюдается один пик, а в прокатанном – секстед. У оттоженных при 600 °С образцов стали наблюдаются пики как от аустенита, так и от мартенсита, также у образца сохраняются магнитные свойства. С повышением температуры отжига стали исчезают магнитные свойства и пики от мартенсита (рис. 5 д ). Данные, полученные методом гамма-резонансной спектроскопии, подтверждают данные, полученные методом рентгено-дифракционного фазового анализа.
Спектр обработан методом восстановления распределения сверхтонкого магнитного поля и методом модельной расшифровки. Видно, что максимум восстановленного распределения сверхтонкого магнитного поля достигается при Hn ~ 280 кЭ, после обработки прокатки на 80 % (рис. 5 б ). Это связано с перераспределением электронной плотности вокруг ядра железа. Такое перераспределение возникает благодаря формированию новой фазы – мартенсита деформации. После отжига при 600 °С максимум восстановленного распределения сверхтонкого магнитного поля смещается, Hn ~ 260 кЭ (рис. 5 в ). Это свидетельствует о неполном превращении ферромагнитного мартенсита в парамагнитный аустенит [12].
Поскольку в исследуемой стали не образовывается фаза диффузионным методом, то высокотемпературная пластичность происходит только за счет зернограничного проскальзывания. Поэтому структура стали после высокотемпературной деформации является высокопористой (рис. 6 а ). В стали также наблюдается вязкое разрушение (рис. 6 б ) [13]. Показатель пластичности δ = 130 %.
Рентгенофазовый анализ до и после высокотемпературной деформации стали 12Х18Н10Т подтверждает, что образования фаз не происходит (рис. 7), а также то, что при деформации случается обратное превращение мартенсита в аустенит (рис. 7 д ). Установлено, что высокотемпературная деформация инициирует переход α-железа в γ-железо и снижает температуру перехода с 920 до 780 °С.
На рис. 8 представлены изменения микротвердости стали до и после высокотемпературной деформации. На гистограммах видим, что после проведения прокатки и у стали про-
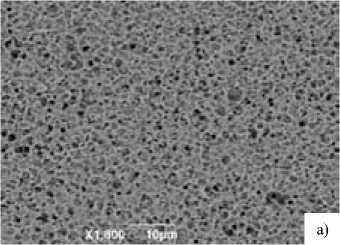
Рис. 6. Микроструктура стали 12Х18Н10Т: а) прокатка на 80 % + скоростной нагрев да 820 °С (3 мин) +
СПД (Т = 780 °С, е = 0,7240-2с-1); б) поверхность разрушения после СПД на 190 %
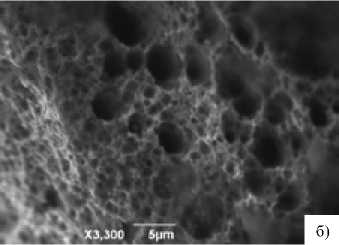
Fig. 6. The microstructure of steel 12Cr18Ni10Ti: a) rolling at 80 % + high-speed heating and 820 °С (3 min) +
SPD (Т = 780 °С, е = 0,7240-2с-1); б) surface damage after SPD by 190 %
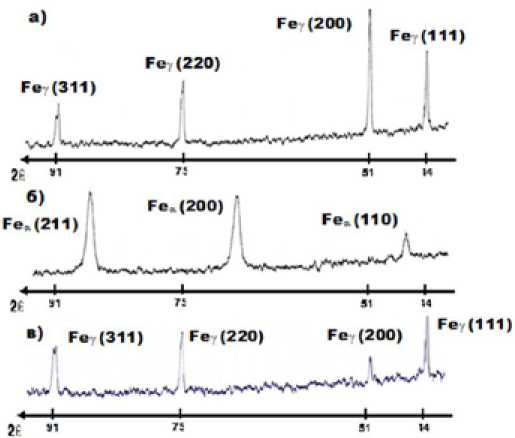
Рис. 7. Фрагменты дифрактограмм до и после высокотемпературной деформации стали 12Х18Н10Т: а) исходный; б) прокатка на 80 %; в) прокатка на 80 % + скоростной нагрев до 820 °С (3 мин) + СПД (Т = 780 °С, е = 0,72^10 - 2с - 1)
Fig. 7. Fragments of diffraction patterns before and after high-temperature deformation of steel 12Cr18Ni-10Ti: a) source; б) 80 % rolling; в) rolling at 80 % + high-speed heating to 820 °С (3 min) + SPD(Т = 780 °С, е = 0,7210 2с 1 )
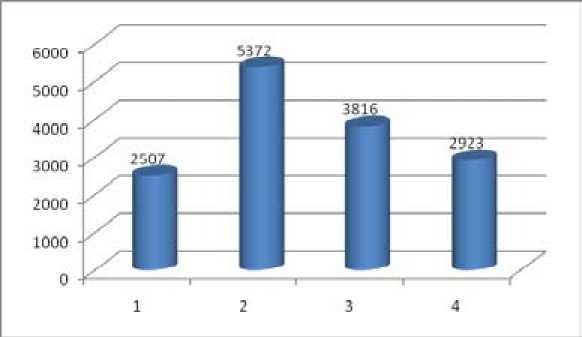
Рис. 8. Изменение микротвердости: 1 - исходный; 2 - прокатка на 80 %; 3 - прокатка на 80 % + скоростной нагрев 820 °С (3 мин); 4 – прокатка на 80 % + скоростной нагрев 820 °С (3 мин) + СПД (Т = 780 °С, е = 0,72Ю-3с-1)
Fig. 8. Microhardness change: 1 – source; 2 – rolling at 80 %; 3 – rolling at 80 % + high-speed heating 820 °С (3 min); 4 - rolling at 80 % + high-speed heating 820 °С (3 MIN) + SPD (Т = 780 °С, е = 0,72Ю-3с-1)
исходит увеличение микротвердости в два раза. При проведении деформации уменьшается микротвердость, но значение микротвердости не ниже исходного.
Согласно работам [7, 14], известны два основных типа сверхпластичности: микрозеренная и сверхпластичность превращения. Микрозеренная сверхпластичность свойственна металлам – 445 –
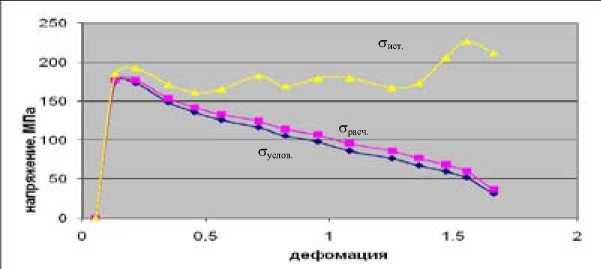
Рис. 9. График изменения напряжения течения в стали 12Х18Н10Т
Fig. 9. The graph of flow stress in steel 12Cr18Ni10Ti и сплавам с очень мелким равноосным зерном. Второй тип – сверхпластичность превращения, проявляется во время фазового превращения. В момент фазового превращения структура резко меняется, образующаяся фаза в начальный момент мелкозернистая, а в период трансформации однофазный сплав становится двухфазным.
На рис. 9 видно, что в начальный момент времени условное напряжение – σ усл. и расчетное теоретическое напряжение - о расч растет и, достигая предела прочности, равномерно уменьшается. А истинное напряжение σ ист , определенное фотометодом, изменяется скачкообразно. В работах [15-17] изложены некоторые особенности исследования истинных напряжений в сталях и сплавах. Истинное напряжение неплохо сходится с теоретическим и условным напряжениями до степени деформации - 0,5, в дальнейшем происходит рост истинного напряжения, максимум которого достигается в месте разрыва образца. В полученных данных имеется расхождение теоретических данных с экспериментальными, по-видимому, из-за того, что теоретическая формула не учитывает изменения скорости деформации и изменения площади поперечного сечения образца.
Выводы
Исследованиями структурных и магнитных характеристик установлено, что в результате прокатки происходит образование новой фазы – мартенсита деформации.
Неравновесные мартенситные фазы, возникающие при переходе γ-Fe в α′-фазу в условиях пластической деформации, связаны с имеющимися в материале избыточными объемами в локальных наномасштабных областях.
Пластическая деформация в стали 12Х18Н10Т - высокотемпературная пластическая деформация за счет перехода α′-фазы в γ-Fe по типу сверхпластичности превращения.
Список литературы Структурно-фазовые состояния и напряжение течения при пластической деформации стали 12Х18Н10Т
- Гуляев А.П. Сверхпластичность стали. М.: Металлургия, 1982. 56 с.
- Солонин М.И., Кондратьев В.П., Вотинов С.Н. Сплав ХНМ-1 как перспективный материал для элементов конструкции ядерных и термоядерных реакторов с водным теплоносителем. ВАНТ, Серия Материаловедение и новые материалы, 1995, 1(52), 13-20.
- Колотушкин В.И., Влияние структурного состояния на стабильность Cr-Ni сталей и сплавов при облучении нейтронами. ФММ, 2004, 97(2), 63-73.
- Новиков И.И. Теория термической обработки металлов. М.: Металлургия, 1978
- Тусупжанова А.Е., Ерболатулы Д., Квеглис Л.И., Немцев И.В. Исследование напряжения течения при сверхпластической деформации Co-Ni-Nb сплава. Журнал Сибирского федерального университета. Техника и технологии, 2015, 8(6), 802-810
- Тусупжанова А.Е., Ерболатулы Д., Квеглис Л.И., Филяровский А. Исследование структурно-фазовых состояний и особенностей пластической деформации аустенитного твердосплавного сплава Co-Ni-Nb. Металлы 2018, 8(1), 19;
- DOI: 10.3390/met8010019
- Новиков И.И., Золоторевский В.С., Портной В.К., Белов Н.А., Ливанов Д.В., Медведева С.В., Аксенов А.А., Евсеев Ю.В. Металловедение. Т. I. М.: Издательский Дом МИСиС, 2009. 496 с.
- Смирнов М.А., Счастливцев В.М., Журавлев Л.Г. Основы термической обработки сталей. Екатеринбург: Институт физики металлов УрО РАН, 1999. 496 с.
- Горелик С.С., Скаков Ю.А., Расторгуев Л.Н. Рентгенографический и электронно-оптический анализ. М.: МИСИС, 2002. 360 с.
- Панин В.Е., Панин А.В., Почивалов Ю.И., Елсукова Т.Ф., Шугуров А.Р. Масштабная инвариантность структурных трансформаций при пластической деформации наноструктурных твердых тел. Физ. мезомеханика, 2017, 20(1), 57-71
- Панин В.Е., Егорушкин В.Е., Елсукова Т.Ф. и др. Многомасштабное трансляционно-вращательное пластическое течение в поликристаллах. Справочник по механике материалов. Под ред. С.-Х. Hsuch et. и др. Сингапур: Springer Nature Singapore Pte Ltd., 2018.
- Кэмпбелл С.И., Качмарек В.А. Мессбауэровская спектроскопия применительно к материалам и магнетизму. Под ред. G.J. Лонг, Ф. Гранджин. Н.Ю., Пленум Пресс, 1996. Т. 2.
- Гоулдстейн Дж., Ньюбери Д., Джой Д., Фиори Ч., Лифшин Э. Растровая электронная микроскопия и рентгеновский микроанализ: В 2 кн. Книга 2. Пер. с англ. М.: Мир, 1984. 348 с.
- Као Ф.Р., Ли Ж.Л., Чжан Н.Х., Дин, Х., Йю F.X., Зуо Л., Сверхпластичность, течение и механизм разрушения в сплаве Al-12,7Si-0,7Mg. Материаловедение и инженерия. A 2013, 167-183
- Хорита З., Фурукава М., Немото М., Барнерс A.Дж, Лэнгдон Т.Г. Сверхпластическое формирование при высоких скоростях деформации после сильной пластической деформации. Acta. Mater. 2000, 48, 3633-3640.
- Смолей А., Клобзар Д., Сказа Б., Наголе A., Слацек E., Драгоевич В., Смолей С., Сверхпластичность прокатанного и обработанного трением сплава Al -4,5 Mg -0,35Sc -0,15Zr. Материаловедение и инженерия A 2014, 590, 239-245.
- Ли С., Уцуномия А, Акамацу Х., Неиши K., Фурукава М., Хорита З., Лэнгдон Т.Г. Влияние скандия и циркония на стабильность зерна и сверхпластичные пластичности в ультрамелкозернистых сплавах Al -Mg. Acta. Mater. 2002, 50, 553-564