Synthesis of Ca4GdO(BO3)3 single crystals using Czochralski method
Автор: Mckel Robert, Hengst Margitta, Reuther Christoph, Gtze Jens
Журнал: Журнал Сибирского федерального университета. Серия: Техника и технологии @technologies-sfu
Статья в выпуске: 4 т.2, 2009 года.
Бесплатный доступ
The oxoborate Ca4GdO(BO3)3 (GdCOB) is a potential material for advanced industrial applications because of its optical and electric properties. High quality single crystals of GdCOB have been grown from a melt using the Czochralski method. Single crystals of laboratory scale are of good optical quality showing no macroscopic defects like cracks, inclusions or discolouration. Crystals in [001] direction reveal regular growth, whereas crystals in [010] are of asymmetric shape but show less difficulties during the growth process.
Single crystal growth, czochralski, oxoborate, ca4gdo(bo3)3
Короткий адрес: https://sciup.org/146114515
IDR: 146114515
Текст научной статьи Synthesis of Ca4GdO(BO3)3 single crystals using Czochralski method
First investigations on the system REE2O3–CaO–B2O3 go back to the late 1960s, early 1970s, when Kindermann took care of the whole system [1]. Most of these early syntheses were realized by solid state reactions.
Later, Ca 4 REEO(BO 3 ) 3 (REECOB) was synthesized and described by Norrestam & Nygren [2], who produced the materials by simple solid state reactions of stoichiometric mixtures as well. They showed that most trivalent REE like La, Nd, Sm, Gd, Er, and Y fit into the crystal lattice crystallizing isostructurally. First analysis of the crystallographic structures revealed analogies to calcium fluoroborate (Ca 5 F(BO 3 ) 3 ) and also to well known structure of common fluorapatite (Ca 5 [F/(PO 4 ) 3 ]). They suggested a possible use of the new crystals as mini-laser material.
Later on Aka et al. [4,5] found that GdCOB is suitable for the Czochralski growth technique because of its congruent melting behaviour, and grew the first larger crystal of GdCOB. Therefore, the interest in the newly discovered material increased strongly, mainly due to its optical properties (e.g. [6]). During the last decade, GdCOB and isostructural compounds (some of them doped with
other rare earth elements) have been grown and their optical as well as laser-performing characteristics studied. The interest in piezoelectric applications of GdCOB is due to its non-centrosymmetric structure (space group Cm). First investigations on piezoelectric properties and applications in SAW components were done during the last few years [7,8]. These authors found excellent properties of these materials, which make it of special interest for the sensor developing industries.
2. History of Czochralski single crystal growth
The Czochralski method was invented by Jan Czochralski by coincidence in 1916. Abstractedly – as the legend has it – he dipped his writing feather in a crucible filled with fluid tin instead of the inkwell. While he pulled his feather out, tin crystallized on the cone end and a single crystal thread grew. Since he was a metallurgist, he found interest in this finding and developed an apparatus to repeat this chance discovery constantly and run different experiments. His interest was not focused on the single crystals itself, he also investigated the crystallization behaviour of several metals (initally tin, lead and zinc) by pulling at a distinctive velocity. A clockwork guaranteed constant pulling rate of single crystal metal wires. Seeding was performed by dipping into the melt a simple glass tube, which was linked to the clock mechanism by a silk thread [9].
Metz et al. [19] already developed a method to pull single crystals of materials of high vapour pressures by covering the exposed surface of the melt with an appropriate, inert liquid material: the idea of LEC (liquid encapsulation technique [65]) was born. Since that time, B 2 O 3 has proved mostly to be the encapsulating material of choice (especially for GaAs), due to its excellent properties. Nowadays it is still the method of choice for producing large scaled GaAs single crystals for semiconductor purpose.
The probably most innovative technical improvement of the method was the automatic controlled growth rate, weighing the growing crystal [21]. Thus, it is possible to control the diameter of crystals without the necessity of a skilled operator visually observing the growth process. The possibility of both weighing the crucible or the crystal via rod was given [21], but the most promising method was to weigh the crystal directly. Computer algorithms were quickly developed to refine the control system, e.g. [22].
Another purpose of Czochralski growth was to produce larger and larger crystals in order to decrease costs, which ended in 265 kg weighing and 300 mm in diameter measuring silicon single crystals nowadays [23]. The same applies for oxide crystals, although there are some more difficulties compared to growing metal alloys. Accordingly, the growth of specimens as large as silicon crystals is still not possible. A good review on the topic of pulling oxides from the melt is given by Brandle [24].
The Czochralski technique today appears in growing high perfection materials in short time for both optical and semiconductor application as well as sensor materials (mainly pyro- and piezoelectrical ones) and others. Currently, the demand for new materials with improved properties drives research to high levels.
3. Experimental procedure
Sintering
The Ca4GdO(BO3)3 compound was prepared by simple high temperature solid state reaction by mixing relevant basic raw materials, in this case CaCO 3 , B 2 O 3 and Gd 2 O 3 . Following the formular (1)
Gd 2 O 3 + 8 CaCO 3 + 3 B 2 O 3 → 2 Ca 4 GdO(BO 3 ) 3 + 8 CO 2 (1)
an appropriate stoichiometric mixture of the powders was made. Because of the loss of weight due to water adsorbed on B 2 O 3 , an excess of 2 wt.-% B 2 O 3 was added to the mixture. An example for weight calculation is given in Table 1.
Table 1. Calculation of material needed for 100 g end weight of Ca 4 GdO(BO 3 ) 3
Gd 2 O 3 |
CaCO 3 |
B 2 O 3 |
|
molecular mass [Da]* |
362.5 |
100.09 |
69.62 |
quantity |
1 |
8 |
3 |
100 g end weight Ca 4 GdO(BO 3 ) 3 [g] |
35.54 |
78.504 |
20.886 (incl. 2% excess) |
* 1 Da = 1.66×10-27kg
The mixture was homogenized in a melamine mortar and afterwards filled into an Al2O3-ceramic crucible. Sintering was carried out in two steps: heating up to 1000°C with several interstages and holding at this temperature for 10 hours. The material was grounded again after cooling down and heated once more up to 1200°C, holding for 10 hours. The theoretic loss of weight in a stoichiometric mixture due to degassing of CO2 is 25.66 wt.-%. The sintered material was rechecked by powder X-ray diffraction (XRD) using an URD 6 (Seifert/Freiberger Präzisionsmechanik) device operating with CoKα radiation (0,179 nm).
Czochralski growth
The pre-reacted material was melted in 2-3 steps in an iridium crucible and homogenized for at least one hour in the pulling device. The puller used is a Cyberstar Oxypuller 05-03 with maximum output power of 20 kW and a slightly modified coil, producing a 20-100 kHz alternating electrical field. All experiments were performed with an iridium crucible with dimension of 40 mm in diameter and height, and 1.5 mm wall thickness. A passive iridium afterheater was used to reduce the temperature – 402 –
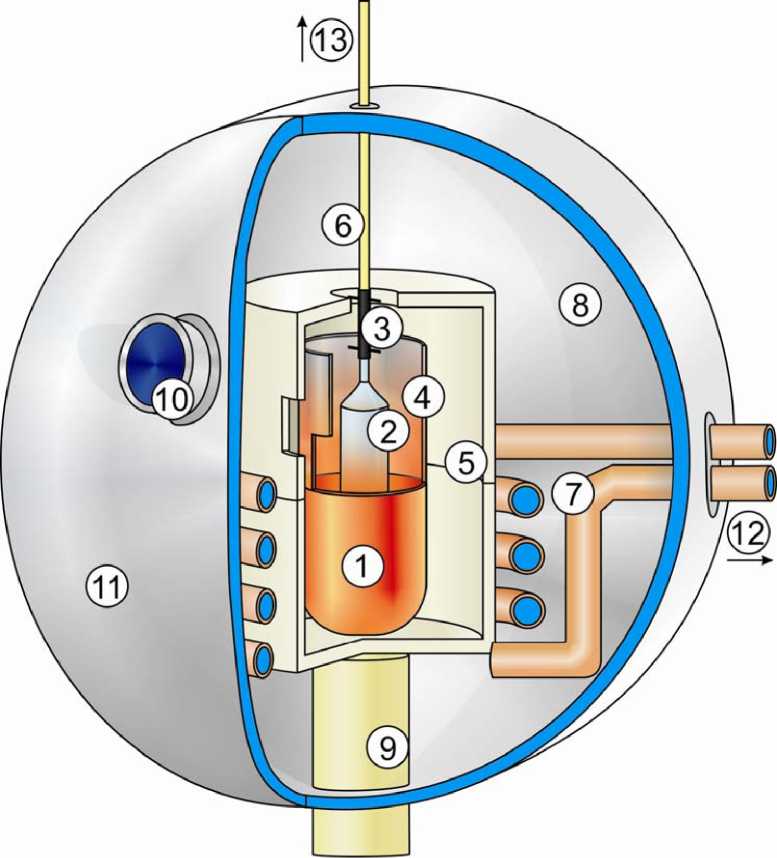
Fig. 1. Sketch of the used Czochralski system excluding periphals like weighing machine, water/power supply, control unit etc. (not to scale): 1. crucible including melt; 2. growing crystal; 3. seed mounting including seed; 4. afterheater (passive); 5. ceramic heat shield; 6. pulling rod; 7. radio freq. coil, water streamed; 8. water cooled chamber; 9. crucible support (adjustable); 10. observation window; 11. front door; 12. to power supply/cooling system; 13. to load cell/lifter gradient in the crystal. To prevent oxidization of iridium, nitrogen was used as inert gas atmosphere. A sketch of the used alignment is given in Fig.1.
During the time of homogenization, the seed was slowly lowered in order to ensure uniform heat propagation in the seed material. The seed was dipped manually into the melt and the power output was manually adjusted to generate equilibration conditions between melt and solid seed. Afterwards the automatic generating pulling sequence itself could be started. Seed and crystal were rotated with constant rate during the whole process, and the pulling rate was kept constant too. The growing crystal was observed via CCD camera which is attached in front of the observation window (see Fig 1) and weight of the crystal was controlled by the computer. The diameter is controlled via the weighing signal and modified by temperature/power output.
To grow a single crystal of a specific orientation one needs a preoriented seed, preferably of the same material (homogenous seed). While growing a crystal of a new system for the first time, one is forced to use another seeding material, if there is no homogenous seed. In the present case, we used a metal seed. In most cases, the growing on a heterogeneous seed will result in a polycrystalline crystal. The challenge is to produce a single crystal out of polycrystalline material large enough to be used as homogeneous single crystalline seed of a special orientation. This happens during several seeding procedures where the single crystalline areas are getting larger. Once there is a single crystal large enough to serve as seed, it has to be cut, oriented and mounted to the pulling rod. Afterwards an initial single crystal can be grown. The orientation has to be detected, possibly by morphological criteria or by single crystal X-ray diffraction. If the exact orientation of the initial crystal is known, other preferred orientations can be cut off. In most cases, there is at least one preferred growth direction, in the case of Ca 4 GdO(BO 3 ) 3 it is obviously [010] (b-axis).
To produce a single crystal, which is free of cracks and with a growing process not too timeconsuming, it is necessary to refine the growing parameters like pulling rate, optimal diameter, angle of shouldering and necking down as well as cooling rate. In literature there is partially imprecise information about these parameters so far. Thus, growing and pulling rates had to be optimized in several experiments, alternating from 1-3 mm/h and 10-45 rpm, respectively. These parameters depend on the specific mechanical assembly and are therefore not conferrable to different configurations.
At least one week is required for preparing the experiment (mixing, sintering twice, melting at least twice etc.). In addition, a typical growth process lasts 5-6 days, depending on size. Detailed parameters of the growth process are given in Table 2.
Table 2. Parameters of crystal growth
crucible |
Ir, 40mm height, 40 mm diameter |
atmosphere |
N 2 |
rotating rate pulling rate crystal dimension |
6 rpm 1 mm/h neck 20-50 mm length, 5mm in diameter shoulder 10-15 mm length cylinder up to 50 mm length, up to 18 mm in diameter |
typical run through time cooling down |
ca. 70-100 h depending on size 20 h |
4. Results
The sintering procedure was performed using the parameters listed in chapter 3. XRD measurements proved the resulting material to be pure Ca4GdO(BO3)3. The measured loss of weight during sintering was slightly higher (average of 26.2 wt.%) than the theoretic value of 25.66 wt.%, which can be related to the loss of water adsorbed on B2O3 – compensated by the excess. This fact was proved by DSC (differental scanning calorimetry) measurements. The sometimes proposed evaporation of B 2 O 3 (e.g. [25]) could not be confirmed.
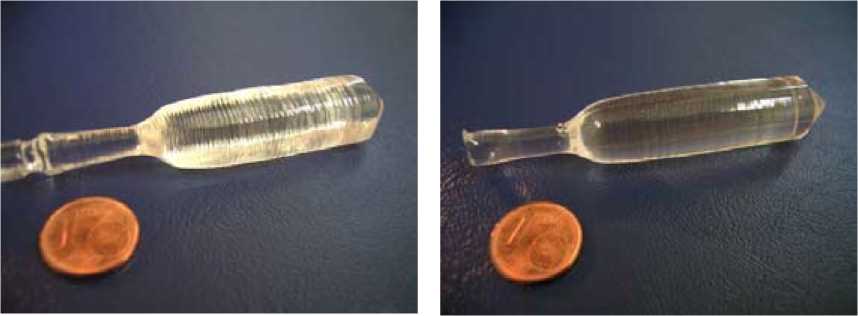
b
Fig. 2. Crystals grown in b-direction (a) and in c-direction (b)
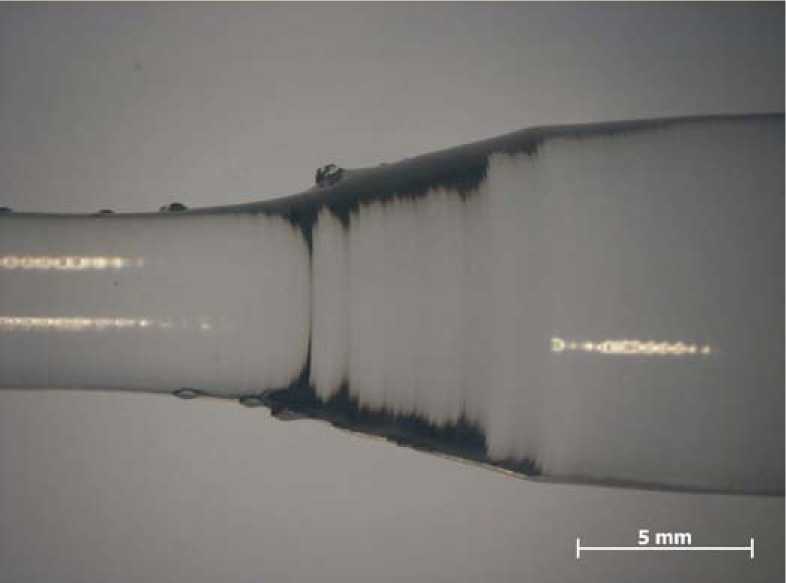
Fig. 3. Outgrowth features appearing on a [001]-grown crystal
Crystals with cylindric shape and sizes of up to 18 mm in diameter and 50 mm in length were grown in both directions ([010] and [001], Fig. 2 a and b, respectively). Most of the crystals were free of macroscopic defects like cracks, inclusions, etc. The crystals are colourless, transparent and non-hygroscopic. It appeared that the growth in c-direction is more difficult than in b-direction. In addition, cleavage appeared in two directions [20 1 ] and [010], which was reported earlier [4].
Single crystals grown in direction of the c-axis have a very smooth surface with nearly radial cross section (see Fig. 2b) and only few growth striation, whereas the b-direction shows a rather rhomboidal shape (see. Fig. 2a) with partially massive growth striation. The ( 2 01) and (101) faces can be clearly recognized, whereas the (100)-face is a fast-growing face and therefore disappears almost completely [26]. These rhombi also appear on the [001]-grown crystals perpendicular to the growth direction, most frequently and biggest in the shoulder parts. Especially in the shoulder they sometimes appear as outgrowth features, up to 1-2mm out of the surface (Fig. 3).
Crystal growth in the [010]-direction led to asymmetric growth, probably caused by a large difference in lattice constants and/or different growth velocities.
5. Conclusions
In the present study, single crystals of Ca4GdO(BO3)3 (GdCOB) were successfully grown from the melt using the Czochralski method. The syntheses have been performed in two different directions, during those the [001]-direction is more difficult to grow than the [010]-direction. However, the [001]-oriented GdCOB-crystals are regularly shaped with circular cross section. When successfully grown, the crystals show no macroscopic defects like cracks, inclusions, etc. The b-axis is obviously the preferred growth direction, which is proved by a higher number of successful experiments, and outgrowing features in b-direction during growth of [001]-oriented crystals. In a further step of experiments, crystals for economic purposes should be grown with higher growth velocity by increasing the pulling rate.