Технические средства и методики входного контроля качества PDC зубков алмазных буровых долот
Автор: Ненашев М.В., Ибатуллин И.Д., Журавлев А.Н., Косулин С.И.
Журнал: Известия Самарского научного центра Российской академии наук @izvestiya-ssc
Рубрика: Системные разработки трибологии машин и приборов
Статья в выпуске: 4-3 т.13, 2011 года.
Бесплатный доступ
В статье представлены результаты разработки методик и технических средств контроля качества зубков буровых долот со вставкой из синтетических поликристаллических алмазных покрытий (PDC). Представлены схемы исполнений.
Прочность, износостойкость, алмазное долото, pdc зубок, качество, опытный образец
Короткий адрес: https://sciup.org/148200218
IDR: 148200218
Текст научной статьи Технические средства и методики входного контроля качества PDC зубков алмазных буровых долот
разрушению при динамической нагрузке, стойкости к абразивному изнашиванию.
При оценке стойкости PDC зубков к хрупкому скалыванию режущей кромки при квазистатическом нагружении критерием качества является критическое напряжение скалывания – минимальное механическое напряжение, вызывающее скол рабочей кромки зубка. Это напряжение должно превышать давление на зубок, вызванное реакцией самой твердой фазы разрушаемой на забое породы. Критические напряжения лимитируют максимальный крутящий момент долота и твердость разрушаемой породы. Чем выше критические напряжения зубков, тем выше твердость породы, в которую может врезаться долото.
Другой немаловажный показатель – величина и характер скола, который можно классифицировать следующим образом: тип А - затрагивающий лишь локальный участок (кромку) материала покрытия; тип Б - когда осевая трещина проходит через покрытие и основу; тип В - когда происходит откалывание алмазного покрытия. Так, при одинаковых критических нагрузках более высокое качество зубков будет соответствовать меньшим повреждениям материала. Величину скола можно также оценивать как потерю веса разрушенных зубков, путем его взвешивания до и после эксперимента.
Методика контроля выполняется по следующим этапам
-
• Подготовка зубков (прогрев в печи до температуры 600 С - имитация теплового воздействия при пайке зубков).
-
• Установка двух зубков, с контактом по PDC покрытию, в оправку, позволяющую автоматически реализовать геометрическое нормирование площади взаимного перекрытия зубков (рис.1а). Оправка служит также для предохранения оператора от осколков при скалывании кромки зубка.
-
• Установка оправки в сжимающем устройстве, например, в машинных тисках или под прессом.
-
• Сжатие PCD зубков до скола кромки алмазного покрытия с одновременной регистрацией критической нагрузки сжатия.
-
• Снятие зубка из оправки и анализ величины и характера скола.
-
• Статистическая обработка результатов испытаний и занесение в базу данных.
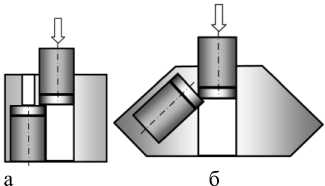
Рис.1. Схема испытаний на прочность со статическим приложением нормальной нагрузки: а – при нормальном контакте, б – при точечном контакте
При испытаниях необходимо нормировать номинальную площадь контакта покрытий испытываемых зубков, что целесообразно осуществлять методом геометрического нормирования за счет изготовления специальной оправки, задающей определенное взаимное расположение PDC зубков. При этом большей площади перекрытия будет соответствовать меньшее давление в контакте при одной и той же силе прижатия. Таким образом, выбор площади контакта определит уровень скалывающих нагрузок и технические средства для осуществления сжатия. Во избежание необходимости применения дорогостоящих прессов, желательно, чтобы скалывающие нагрузки не превышали 3-х тонн-сил (тс), которые можно реализовать в машинных тисках.
Для приближения испытаний к реальным условиям эксплуатации контакт зубков можно осуществлять не по нормали, а под углом ОС (рис.1б). В этом случае реализуется точечный контакт, при котором критические нагрузки будут существенно снижены.
При оценке стойкости PDC зубков к хрупкому скалыванию режущей кромки при динамическом нагружении в качестве критериев качества могут быть использованы следующие: энергоемкость (вязкость) процесса разрушения, например, потеря потенциальной энергии маятника при испытаниях материала на удар на маятниковом копре; количество циклов нагружения до разрушения материала (в последнем случае единичное воздействие должно представлять собой тарированный удар, имитирующих динамику работы долота на забое); дополнительным критерием качества, как и в предыдущем случае, является характер и величина скола.
Методика контроля выполняется по следующим этапам
-
• Подготовка зубков (прогрев в печи до температуры 600 С - имитация теплового воздействия при пайке зубков).
-
• Установка зубка в державке (рис. 2) прибора, позволяющего реализовать циклические ударные нагрузки стальным шариком по кромке PDC покрытия
зубка с возможностью оценки и регулировки величины динамической нагрузки. Управление силой и частотой ударов осуществляется путем регулирования частоты и величины импульсов напряжения, пропускаемых через катушки электромагнита.
-
• Испытания проводятся до появления скола на кромке PDC зубка.
-
• Статистическая обработка результатов испытаний и занесение в базу данных.
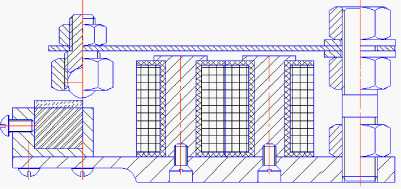
Рис. 2. Схема испытаний на стойкость к динамическим нагрузкам
При оценке стойкости PDC зубков к абразивному изнашиванию при трении в абразивной среде критерием качества является величина износа (весового или линейного) и интенсивность изнашивания, определяемая как отношение величины износа к обусловленному пути трения.
При испытаниях нормируется нормальное давление на поверхности трения, состав среды, размеры и форма абразивного инструмента.
Методика контроля выполняется по следующим этапам
-
• Подготовка зубков (прогрев в печи до температуры 600 С).
-
• Установка зубка в специальную оправку (рис. 3а), позволяющую задать необходимое взаимное расположение поверхности испытуемого зубка и контрповерхности (например, алмазного бора).
-
• Нагружение пары тарированной нагрузкой, создающей определенное давление в контакте и совершение в течение заданного времени относительного перемещения, например, вращения контрповерхности в контакте с неподвижным зубком.
-
• Снятие зубка из оправки и анализ величины износа путем взвешивания и (или) микрометрирова-ния.
-
• Расчет интенсивности абразивного изнашивания.
-
• Статистическая обработка результатов испытаний и занесение в базу данных.
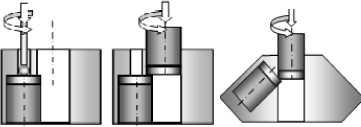
а б в
Рис.3. Схема испытания на абразивную износостойкость покрытия: а – с использованием алмазного шлифовального инструмента, б – с использованием одноименной пары трения при нормальном контакте, в – с использованием одноименной пары трения при точечном контакте Для ускорения и повышения достоверности экспериментов в качестве среды можно использовать алмазную пасту. Допустимо использовать также одноименную пару трения (рис. 2б), состоящую из зубков одной и той же марки – это позволит ускорить набор статистической информации о результатах эксперимента. Кроме того, можно дополнительно ввести гранулометрический анализ размеров частиц износа.
Для возможности ускоренного набора статистических данных об износостойкости алмазных покрытий при минимальной выборке зубков целесообразно локализовать область, подвергаемую абразивному изнашиванию (рис.2в). Оправка в этом случае служит в качестве кондуктора для алмазного инструмента или приспособления для стабилизации заданного межосевого расстояния между испытуемым зубком и алмазным инструментом.
Для апробации методик входного контроля качества поставляемых заводу PDC зубков были испытаны три образца различных фирм-изготовителей: 1) зубок фирмы Бил Шепард (Китай); 2) зубок производства США; 3) зубок фирмы New Asia (Китай). Для этого была спроектирована и собрана специальная установка для оценки стойкости PDC зубков к хрупкому скалыванию режущей кромки, включающая в себя (рис. 4): узел статического нагружения зубков с механическим приводом (станочные тиски - модель №7200-0221-02), обеспечивающий сжимающую нагрузку до 3 тс; тензометрический датчик силы с пределом измерений 3 тс и точностью ±5% от предела измерений; систему сбора данных с частотой выборок 1 кГц; компьютер для мониторинга и хранения результатов испытаний; специальные оправки для фиксации испытываемых зубков четырех типоразмеров: 19,05; 16; 13,3 и 9,5 мм. Оправки оснащены магнитным основанием и выполнены из стали 40Х (HRC 45).
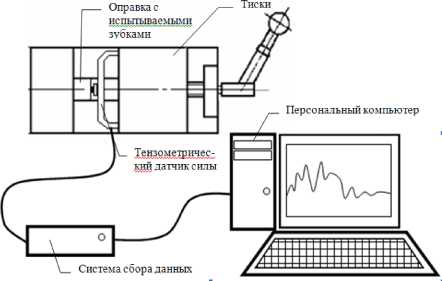
Рис. 4. Общий вид установки для испытаний алмазных зубков на статическое сжатие
Структурная электрическая схема прибора приведена на рис. 5.
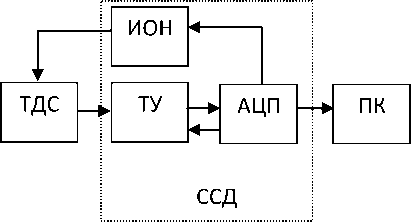
Рис. 5. Структурная электрическая схема испытательной установки: ДС – тензометрический датчик силы; ТУ – тензоусилитель; АЦП – аналого-цифровой преобразователь (ЛА2-USB); ПК – персональный компьютер; ИОН – источник опорного напряжения; ССД – система сбора данных
Подготовка к испытаниям включала следующие операции: выбор из исследуемой партии одной пары PDC зубков и проведение их термообработки; подбор соответствующей оправки; закрепление испытываемых зубков в оправке таким образом, чтобы алмазные покрытия были направлены встречно друг другу; установка датчика силы на одной губке тисков (для этого основание датчика силы оснащено постоянными магнитами); размещение оправки на противоположной губке тисков таким образом, чтобы выступающая из оправки часть зубка (около 2-х мм) располагалась напротив толкателя датчика силы (толкатель выполнен в виде усеченного шара для возможности его самоустановки при контакте с основанием зубка); включение компьютера и запуск программы PowerGraph; программную установку необходимых режимов отображения сигнала; прогрев электрической части в течение 15 минут. Испытания включали следующие операции: нагружение зубков медленным, плавным и равномерным поворотом рукоятки тисков по часовой стрелке до скола нагруженной кромки зубков (до щелчка); выключение режима записи сигнала; разгрузку зубков поворотом рукоятки тисков против часовой стрелки; снятие оправки, вынимание зубков из оправки и анализ величины и характера скола; повторная установка испытываемых зубков в оправке (поворотом вокруг оси на 30 ) так, чтобы в зону перекрытия зубков попала неповрежденная часть алмазного покрытии; повторная установка оправки с зубками на тисках и проведение испытаний (до 6 измерений на одной паре зубков); открытие файла с эпюрами нагружения зубков; усреднение результатов измерений и сохранение их в базе данных.
Характер получаемых сколов и результаты приведены в таблице 1. Вид образцев после испытания представлен на рис. 6
Оценка применяемого метода входного контроля показала экспрессность, экономичность, достоверность и воспроизводимость резкльтатов.
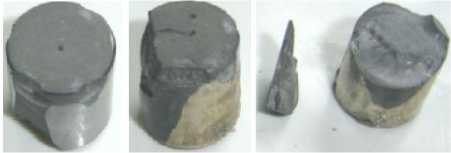
а
б
в
Рис.6. Образцы после испытаний: а – Билл Шепард, б – Raptor, в – New Asia
Заключение
Разработаны методики входного контроля PDC зубков алмазных буровых долот, включающие испытания на стойкость зубков к статическим и динамическим нагрузкам, а также к истиранию в абразивной среде.
Разработаны конструкции испытательных приборов для реализации вышеуказанных методик.
Проведена апробация контроля прочности рабочих кромок PDC зубков при статическом сжатии, показавшая высокую эффективность контроля.
Таблица 1. Результаты испытаний
Образец |
Билл Шепард |
Raptor |
New Asia |
Критическое усилие, кгс |
1300 |
2000 |
2000 |
Критическое напряжение, МПа |
3700 |
5710 |
5710 |
Характер разрушения |
Скол кромок покрытия и осевой скол твердосплавной основы |
Скол кромок покрытия |
Скол покрытия |
ENGINEERING TOOLS AND METHODS OF PDC BITS ENTRANCE QUALITY CONTROL