Технологические аспекты получения материалов для наружных деталей низа обуви
Автор: Радюк А.Н., Буркин А.Н.
Журнал: Вестник Витебского государственного технологического университета @vestnik-vstu
Рубрика: Технология материалов и изделий текстильной и легкой промышленности
Статья в выпуске: 3 (49), 2024 года.
Бесплатный доступ
В настоящее время перед обувной промышленностью Республики Беларусь стоит задача разработки оптимальных подходов к замене дорогостоящих и высококачественных импортных материалов на отечественные аналоги. Последние также должны выглядеть предпочтительнее импортных с экономической точки зрения. Поэтому очевидно, что эти аналоги должны воспроизводить основные характеристики обувных материалов мирового класса или приближаться к ним, но при этом иметь невысокую стоимость. Использование вторичного сырья для получения новых материалов с высокой добавленной стоимостью является одним из вариантов развития индустрии композитных материалов. Так введение различного рода дешевых наполнителей в виде побочных продуктов переработки древесины в композицию из вторичного пенополиуретана позволяет не только существенно снизить себестоимость, но и улучшить показатели свойств. Целью исследования является разработка технологии получения материалов для наружных деталей низа обуви, включающей необходимый перечень операций для ее реализации, а также рецептурный состав композиции для литья под давлением. Методы исследований - стандартные методики оценки физико - механических, упругопрочностных и эксплуатационных свойств для материалов (пластин обуви). В результате работы установлено, что значения свойств материалов (пластин обуви) выше при изготовлении модифицированного и наполненного гранулята как промежуточного продукта. Дальнейшее формование изделий (литье материалов и подошв) позволяет получить заданные (требуемые) значения показателей свойств.
Материалы, свойства, гранулят, анализ, наполнитель, композитные материалы, технологическая схема, направление реализации, состав
Короткий адрес: https://sciup.org/142243623
IDR: 142243623 | DOI: 10.24412/2079-7958-2024-3-61-74
Текст научной статьи Технологические аспекты получения материалов для наружных деталей низа обуви
DOI:
Полиуретаны (ПУ) являются одними из наиболее универсальных полимеров, поскольку их можно использовать во многих областях применения и в различных формах (Gama N. et al., 2018). В обувной промышленности ПУ используются с 60-х годов и на сегодняшний день стал очень популярным материалом для производителей обуви, так как способствует получению качественной, удобной и прочной обуви по невысокой цене. Подошвы обуви, изготовленные из ПУ, отличаются своей легкостью и устойчивостью к истиранию (Rajiс I. et al., 2020). Однако, в виду большого разнообразия областей применения, производство ПУ в последние десятилетия увеличилось, что привело к увеличению количества отходов ПУ (бывших в употреблении продуктов и отходов производства).
Отходы ПУ необходимо эффективно утилизировать и перерабатывать, что является не только требованием предотвращения загрязнения окружающей среды и ее защитой, но также является необходимостью снижения производственных затрат и улучшения использования материалов. На сегодняшний день выделяют три типа технологий (процедур) утилизации отходов ПУ: захоронение, сжигание и переработка (Yang W. et al., 2012). Однако, из-за низкой плотности и большого объема отходы пенополиуретана (ППУ) сложно вывозить на свалку для последующего захоронения, а при сжигании образуется ядовитый газ (Banik J. et al., 2023; Yang W. et al., 2012). Поэтому из-за их негативного воздействия на окружающую среду отходы ПУ должны эффективно перерабатываться, избегая их захоронения и сжигания.
Несмотря на то, что переработка этих потоков отходов в полезные товары является сложной задачей, существующие способы переработки отходов ПУ (механическая или (термо-) химическая переработка) показали некоторые многообещающие результаты (Jehanno C. et al., 2022; Kemona A. and Piotrowska M., 2020; Korley L. T. J. et al. 2021; Vollmer I. et al., 2020). При этом необходимо отметить, что полиуретановые материалы не могут подвергаться переработке бесконечно, поскольку их термомеханические свойства значительно ухудшаются с каждым циклом обработки, что приводит к необходимости захоронения или сжигания в конечном итоге по окончании срока службы (Kosloski-Oh S. C. et al., 2021; Schyns Z. O. G. and Shaver M. P., 2021).
Одним из вкладов в развитие композитных материалов, является возможность использования вторичного сырья для получения новых материалов с высокой добавленной стоимостью. Переработка представляет собой набор методов повторного использования и повторного введения отбракованных материалов в производственный цикл; она включает преобразование отходов в сырье для продуктов, аналогичных исходным. Таким образом, она вносит вклад в круговую экономику – циклическую, замкнутую систему для минимизации отходов (Salino R. E. and Catai R. E., 2023).
Растущая потребность в замене нефтехимического сырья возобновляемым, а также необходимость снижения производственных затрат подчеркнули необходимость разработки полимерных композитов с натуральными наполнителями. Согласно литературным данным, добавление наполнителя в матрицу ППУ приводит к заметным изменениям свойств конечного композитного материала (теплопроводности, плотности и морфологии пены) даже при использовании низкого содержания наполнителя. В этом отношении опилки, как наполнитель, являются чистым, дешевым и легкодоступным побочным продуктом обработки древесины, такой как фрезерование, сверление, шлифование и распиловка. Использование опилок в качестве наполнителя в полиуретановых пенах обеспечивает новое применение переработанных древесных волокон в разработке новых композитных материалов (Tiuc A.-E. et al., 2022).
В связи с растущим развитием деревообрабатывающей промышленности образование отходов является распространенной проблемой. Два побочных продукта переработки древесины — это пыль и древесные частицы. Литературные данные ясно указывают на то, что органические или неорганические наполнители могут значительно улучшить механические и термические свойства композитов ПУ (Mirski R. et al., 2021). Существуют также исследования, в которых наполнители использовались для снижения стоимости и повышения механических свойств, например, модуля упругости и прочности или плотности (Yuan J. and Shi S. Q., 2009).
Целью данного исследования является разработка технологии получения материалов для наружных деталей низа обуви, включающей необходимый перечень операций для ее реализации, а также рецептурный состав композиции для литья под давлением.
Данная работа является продолжением предыдущих исследований авторов, посвященных возможности использования побочных продуктов переработки древесины и отходов низа обуви для производства материалов с улучшенными свойствами.
Объект, методы и средства исследования
В соответствии с основными стадиями технологического процесса получения полимерных композиционных материалов (В. И. Костиков и Ж. В. Еремеева, 2021) была разработана технологическая схема процесса получения материалов (пластин обуви), представленная на рисунке 1.
Реализация схемы процесса получения материалов (пластин обуви), представленной на рисунке 1, осуществлялось в производственных условиях ЧПУП «Обувное ремесло» в рамках апробации получения материалов (пластин обуви) по 2 направлениям:
– получение гранулята отходов ППУ по технологии, приведенной в (А.Н. Радюк, 2024), а затем уже к нему добавление стабилизатора, пластификатора и наполнителя в соответствии с рецептурой (в таблицах 3–5 обозначено как Н. 1). По данному направлению отходы ППУ подвергаются рециклингу несколько раз, тем самым увеличивается кратность их переработки;
– с изготовлением гранулята как промежуточного продукта, включающего в себя отходы ППУ, стабилизатор, пластификатор и наполнитель (в таблицах 3–5 обозначено как Н. 2). Данное направление позволяет получить модифицированный и наполненный гранулят отходов ППУ для дальнейшего формования изделий из него.
Для получения материалов (пластин обуви) использовали компоненты, представленные на рисунке 2.
На основании данных, приведенных в патенте Республики Беларусь «Композиция для деталей низа обуви»1, полиуретановую матрицу модифицировали отходами стелечного картона, взятом в минимальном количестве 3 мас. %. Это позволило предположить использовать такое же количество наполнителя, так как
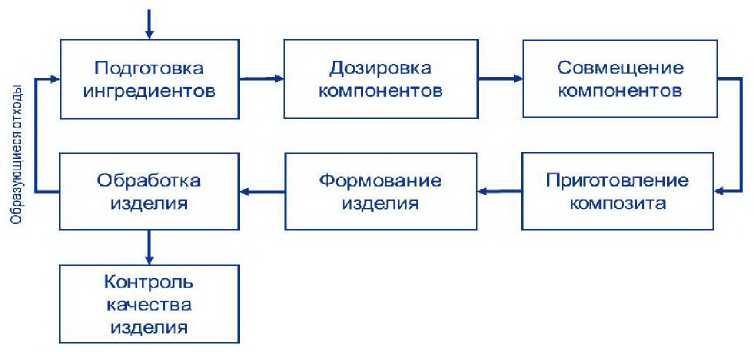
Рисунок 1 – Технологическая схема процесса получения материалов (пластин обуви) Figure 1 – Technological scheme of the process of obtaining materials (shoe plates)

Рисунок 2 – Основные компоненты для получения материалов (пластин обуви)
Figure 2 – Main components for obtaining materials (shoe plates)
точного состава материала типа кожволон нет.
Рецептурный состав композиции включал 2 варианта:
– гранулят на основе отходов ППУ / отходы ППУ + ДП (3 %) + стCa (0,5 %) + МИ (1 %);
– гранулят на основе отходов ППУ / отходы ППУ + ДВ (3 %) + стCa (0,5 %) + МИ (1 %).
Описание стадий технологического процесса представлено в таблице 1.
В результате производственной апробации и реализации технологической схемы были получены пластины обуви.
Полученные образцы пластин исследовали по показателям, представленным в таблице 2. Отбор проб для испытаний материалов и изделий проводился в соответствии с требованиями технических нормативных правовых актов (ТНПА).
Экспериментальные исследования и обсуждение результатов
В рамках работы проведен сравнительный анализ получения материалов (пластин обуви) по 2 направлениям технологии, описанным выше. С этой целью полученные материалы (пластины обуви) исследовали по показателям свойств, описанными в таблице 2. Результаты проведенных испытаний представлены в таблицах 3–5.
Результаты исследования показателей физико-механических свойств материалов представлены в таблице 3.
Результаты исследования показателей упругопрочностных свойств материалов представлены в таблице 4 (усредненные значения по 5 образцам).
Результаты исследования показателей эксплуатационных свойств материалов представлены в таблице 5.
Согласно требованиям (П.С. Карабанов, А.П. Жихарев, В.С. Белгородский, 2008; Л.П. Морозова и др., 1988) для материалов низа обуви, можно сделать следующие выводы:
– плотность монолитных материалов должна быть не более 1,3 г/см3, кожеподобных материалов – должна быть не более 1,1 г/см3. Как можно заметить из таблицы 2, плотность образцов соответствует требованиям для монолитных материалов и не выходит за рамки предельных значений, но не соответствует требованиям для кожеподобных материалов;
– твердость монолитных материалов должна быть в пределах 75–85 усл.ед., кожеподобных – 80–95 усл.ед. Твердость образцов, полученных по двум схемам материалов, находится в рамках нормируемых значений для кожеподобных материалов;
– условная прочность монолитных материалов должна быть не менее 4,5 МПа, кожеподобных – не менее 5,0 МПа. Условная прочность образцов с наполнителем ДВ, полученных по Н. 1, не соответствует требованиям для кожеподобных материалов; для остальных образцов – наблюдается соответствие требованиям и для монолитных, и для кожеподобных материалов;
– относительное удлинение при разрыве монолитных материалов должно быть не менее 160 %, кожеподобных – не менее 180 %. Относительное удлинение образцов с наполнителем ДВ, полученных по Н. 1, не соответствует требованиям для монолитных и кожеподобных материалов, образцов с наполнителем ДВ, полученных по Н. 2, не соответствует требованиям для кожеподобных материалов, для остальных материалов наблюдается соответствие требуемым значениям;
– остаточное удлинение монолитных и кожеподобных материалов должно быть не более 20 %. Остаточное
Таблица 1 – Стадии технологического процесса получения материалов (пластин обуви)
Table 1 – Stages of the technological process of obtaining materials (shoe plates)
Операция |
Стадии получения |
Характеристика стадии |
Подготовка ингредиентов* |
Измельчение отходов ППУ, отсев нужной фракции (5–7 мм) |
осуществляется с помощью дробилки Alpine A 40/63-5-3 и позволяет унифицировать размеры отходов ПУ до частиц 5–7 мм |
Сушка отходов ППУ |
осуществляется в термошкафу с принудительной конвекцией воздуха при температуре 80 °С в течение 3 часов до влажности 0,2–0,3 % |
|
Дозировка компонентов |
взвешивание компонентов в соответствии с рецептурным составов композиции |
|
Совмещение компонентов |
добавление к грануляту на основе отходов ППУ / отходам ППУ стабилизатора, пластификатора и наполнителя, смешивание компонентов в лопастных мешалках |
|
Приготовление композита |
Термомеханическая переработка |
осуществляется в экструдере ЭШПО-75Н4 при температурах от 150 °С до 180 °С, где композит пластифицируется, гомогенизируется и стабилизируется, а затем перемещается по винтовому каналу шнека, продавливается через формующую матрицу, перераспределяясь по сечению в виде пластины прямоугольного сечения |
Охлаждение и измельчение |
непосредственно перед литьем полуфабрикат охлаждали в ванне и измельчали до получения гранул длиной 2–4 мм |
|
Формование изделия |
Изготовление материалов литьем под давлением |
осуществлялось на машине SP 345-3 фирмы Main Group при температуре 150–190 °С, давлении впрыска 40–60 МПа; времени впрыска 15 с; выдержки 360 с |
Обработка изделия |
Обрезка выпрессовок и литников |
|
Контроль качества изделия |
Внешний осмотр изделия для выявления наружных дефектов |
Примечание: * для получения материалов (пластин обуви) из гранулята отходов ППУ на этом этапе предусмотрен контроль качества полученного гранулята и при необходимости сушка его до минимальной влажности.
Таблица 2 – Показатели свойств материалов (пластин обуви)
Table 2 – Indicators of material properties (shoe plates)
Наименование показателя, обозначение, ед. измерения |
ТНПА |
Применяемые средства измерения, оборудование |
Физический смысл показателя |
Объем выборки |
Плотность ( ρ ), г/см3 |
ГОСТ 267-73 |
Весы аналитические AS 220/C/2 «Radwag Wagi Elektroniczne», штангенциркуль |
отношение массы образца к объему вытесненной им жидкости |
Ê , n = 3 |
Твердость ( Í ), усл. ед. |
ГОСТ 263-75 |
Переносной твердомер 2033 ТИР |
сопротивление образцов погружению в них индентора |
Ê , m = 3 |
Относительное удлинение ( ε ), % |
ГОСТ 270-75 |
Разрывная машина РТ-250 |
– |
Ê , m = 5 |
Окончание таблицы 2 – Показатели свойств материалов (пластин обуви)
End of the table 2 – Indicators of material properties (shoe plates)
Условная прочность ( fð ), МПа Относительное остаточное удлинение после разрыва образцов ( θ ), % |
ГОСТ 270-75 |
Разрывная машина РТ-250 |
– |
Ê , m = 5 |
Сопротивление истиранию ( β ), Дж/мм3 (кгс·м/см3) |
ГОСТ 426-77 |
Прибор МИ-2, шлифовальная шкурка, контрольная наполненная резина |
истирание образцов, прижатых к абразивной поверхности вращающегося с постоянной скоростью диска, при постоянной нормальной силе и определении показателей сопротивления истиранию или истираемости |
Ê , n = 6 (3 пары) |
Устойчивость к многоцикловым и изгибающим воздействиям |
ГОСТ ISO 17707-2015 |
Установка, которая позволяет выполнять изгиб образца подошвы под углом 90±2°, копье для прокола, металлическая линейка |
оценка влияния материала подошвы и профиля поверхности на расширение разрыва |
пластина |
Примечание: Ê – среднее арифметическое, n – количество образцов, m – количество определений.
Таблица 3 – Показатели физико-механических свойств материалов
Table 3 – Indicators of physical and mechanical properties of materials
Показатель |
Н. 1 (из гранулята) |
Н. 2 |
||
ДП(гр) |
ДВ(гр) |
ДП |
ДВ |
|
1 |
3 |
4 |
5 |
6 |
Толщина материала (пластин обуви), мм |
6,6 |
6,8 |
6,7 |
6,9 |
Плотность, г/см3 |
1,24 |
1,22 |
1,22 |
1,19 |
Твердость, усл. ед. |
86 |
88 |
90 |
91 |
Таблица 4 – Показатели упругопрочностных свойств материалов
Table 4 – Indicators of elastic strength properties of materials
Показатель |
Н. 1 (из гранулята) |
Н. 2 |
||
ДП(гр) |
ДВ(гр) |
ДП |
ДВ |
|
1 |
3 |
4 |
5 |
6 |
Разрывная нагрузка, Н |
138 |
132 |
148 |
140 |
Условная прочность, МПа |
5,0 |
4,8 |
5,5 |
5,1 |
Относительное удлинение при разрыве, % |
140 |
180 |
160 |
240 |
Окончание таблицы 4 – Показатели упругопрочностных свойств материалов
End of the table 4 – Indicators of elastic strength properties of materials
Остаточное удлинение после разрыва, % |
18 |
17 |
15 |
10 |
Условное напряжение при заданном удлинении, МПа |
– |
4,2 |
5,3 |
3,6 |
Истинное напряжение при заданном удлинении, МПа |
– |
10,9 |
13,8 |
9,4 |
Истинная прочность, МПа |
12,0 |
13,4 |
14,3 |
17,3 |
Таблица 5 – Показатели эксплуатационных свойств материалов
Table 5 – Indicators of operational properties of materials
– сопротивление истиранию монолитных и кожеподобных материалов должно быть не менее 2,5 Дж/мм3. Сопротивление истиранию образцов соответствует вышеуказанным требованиям;
– сопротивление многократному изгибу монолитных материалов должно быть не менее 30 тыс. циклов, кожеподобных – не менее 20 тыс. циклов. Сопротивление многократному изгибу образцов соответствует требованиям и для монолитных, и для кожеподобных материалов. Данный показатель в настоящее время определяется в соответствии с ГОСТ ISO 17707-2015, в котором прописано минимальное пороговое его значение равное 30 000 циклов. До недавнего времени сущность метода испытаний на многократный изгиб по ГОСТ 422-75 заключалась в определении сопротивления разрастанию трещины в образце с проколом при его изгибе, чередующимся с принудительным выпрямлением, нормируемое число изгибов составляло 15 000 циклов, а трещина в точке прокола не должна была превышать 6 мм. При этом необходимо отметить, что несмотря на то, что в странах ЕС определение показателя предусмотрено по международному стандарту, для полиуретановых систем для низа обуви минимальное значение данного показателя начинается с 20 000 циклов.
Более наглядно данный анализ представлен на рисунках 3–9.
Значение показателя плотности соответствует монолитным резинам марки «В» (не более 1,3 г/см3).
Значение показателя твердости соответствует кожеподобным резинам марки «Кожволон» (75–90 усл. ед.).
Значение показателя условной прочности соответствует монолитным резинам марки «В» (не менее 4,5 МПа) и кожеподобным резинам марки «Кожволон» (не менее 5,0 МПа).
Значение показателя относительного удлинения при разрыве соответствует монолитным резинам марки «В» (не менее 170 %) для некоторых образцов, для других – кожеподобным резинам марки «Малыш» и «Кожволон» (не менее 180 %). Для образца «ДП из гр» данный показатель намного ниже требуемых значений.
Значение показателя остаточного удлинения после разрыва соответствует монолитным резинам марки «В» (не более 20 %) и кожеподобным резинам марки «Кожволон» (15–30 %) и «Малыш» (не более 30 %).
Значение показателя сопротивления истиранию соответствует монолитным резинам марки «В» (не менее 2,5–3,5 Дж/мм3), но не соответствует для некоторых образцов кожеподобным резинам марки «Малыш» (не менее 4,6 Дж/мм3) и для всех образцов кожеподобным резинам марки «Кожволон» (не менее 5,9 Дж/мм3).
Значение показателя сопротивления многократному изгибу соответствует монолитным резинам марки «В» (не < 15 тыс. циклов) и кожеподобным резинам марки «Кожволон» (не < 20 тыс. циклов).

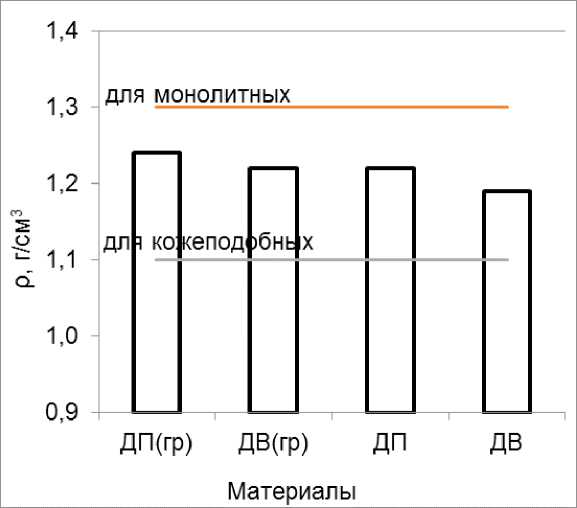
Рисунок 3 – Плотность полученных образцов Figure 3 – Density of the produced samples
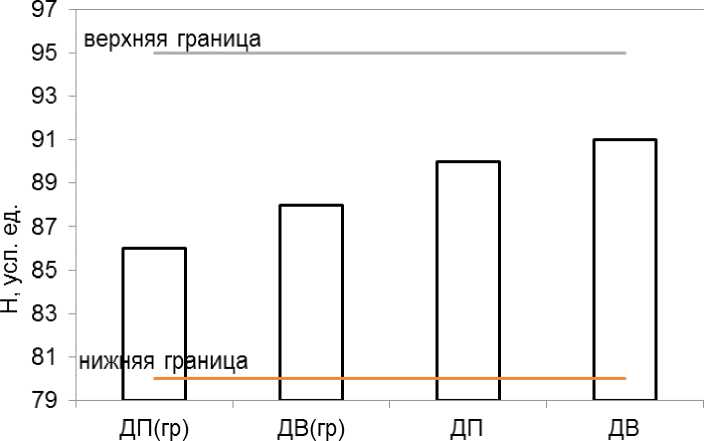
Материалы
Рисунок 4 – Твердость полученных образцов Figure 4 – Hardness of the produced samples
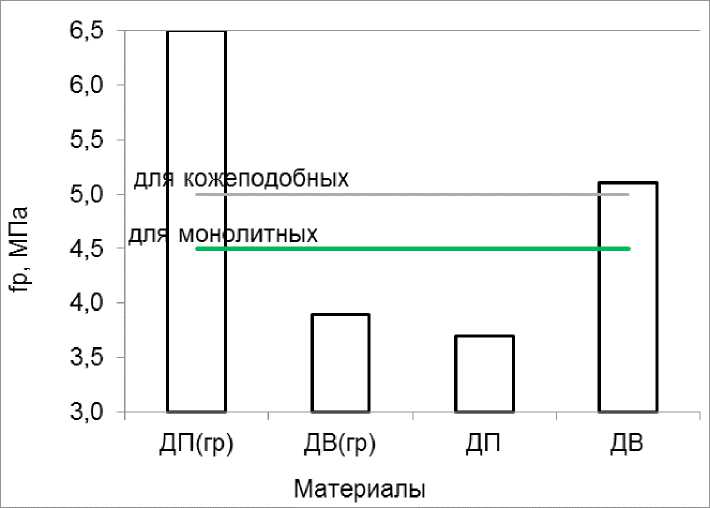
Рисунок 5 – Условная прочность полученных образцов Figure 5 – Conditional strength of the produced samples
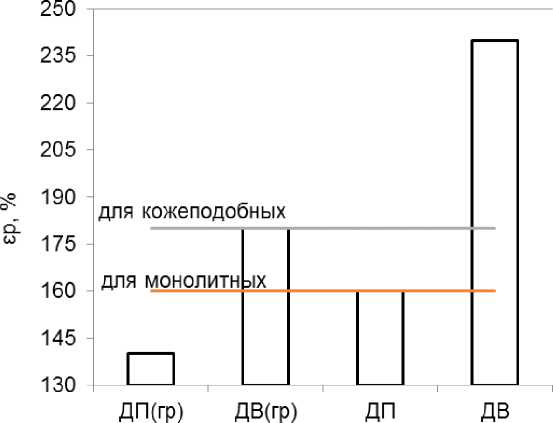
Материалы
Рисунок 6 – Относительное удлинение при разрыве полученных образцов Figure 6 – Relative elongation at break of the produced samples

Материалы
Рисунок 7 – Остаточное удлинение после разрыва полученных образцов Figure 7 – Residual elongation after rupture of the produced samples
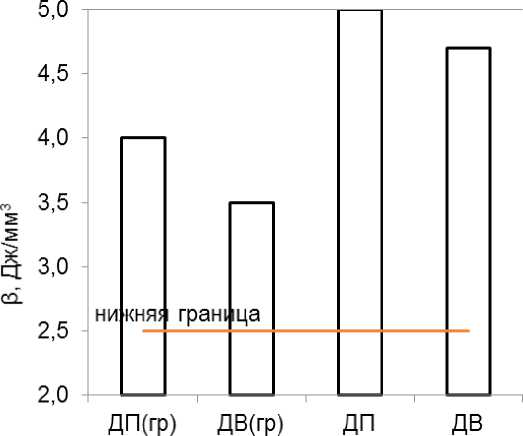
Материалы
Рисунок 8 – Сопротивление истиранию полученных образцов Figure 8 – Abrasion resistance of the produced samples
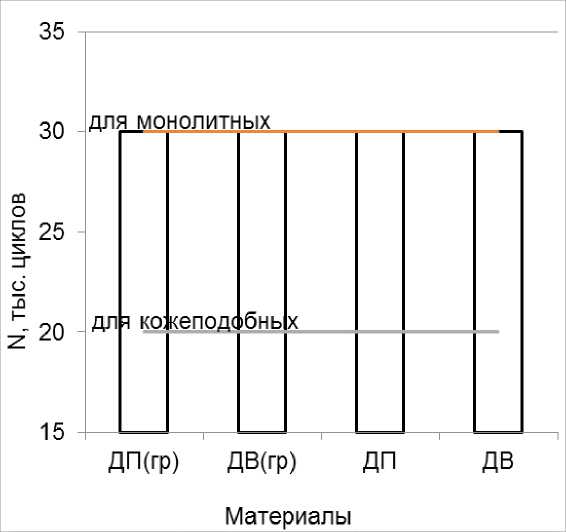
Рисунок 9 – Сопротивление многократному изгибу полученных образцов
Figure 9 – Resistance to repeated bending of the produced samples
Сравнивая полученные материалы с материалами типа кожволон можно заметить, что в некоторых источниках данные отличаются по предельным значениям их физико-механических свойств (Л.П. Морозова и др., 1988; П.С. Карабанов, А.П. Жихарев, В.С. Белгородский, 2008). Верхний предел плотности составляет 1,2 г/см3 (для кожеподобной резины релак – 1,3 г/см3), предел прочности должен быть не менее 5,0 МПа, нижний предел относительного удлинения при разрыве составляет 180 %, твердость по Шору А должна быть 80–95 усл. ед., сопротивление истиранию – не ниже 2,5 Дж/мм3 и сопротивление многократному изгибу не менее 20 тыс. циклов. Согласно этим данным, полученные материалы по Н. 2 соответствуют требованиям пороговых значений. Выводы
В результате проведенных исследований:
– разработана технологическая схема процесса получения материалов (пластин обуви), включающая 7 основных операций: подготовку ингредиентов, дозировку компонентов, совмещение компонентов, приготовление композита, формование изделия, обработку изделия и контроль качества изделия;
– предложено процентное соотношение ингредиентов в композиции на полимерной основе из ППУ и разработаны рецептурные составы композиций для получения изделий с требуемым уровнем свойств;
– проведен сравнительный анализ направлений реализации технологической схемы получения материалов (пластин обуви) в производственных условиях ЧПУП «Обувное ремесло»: из гранулята отходов ППУ с добавлением к нему модификаторов и наполнителя и с изготовлением модифицированного и наполненного гранулята как промежуточного продукта;
– установлено, что значения свойств материалов (пластин обуви) выше при реализации схемы процесса получения материалов (пластин обуви) по направлению Н. 2, так как получение гранулята, а на основании его в дальнейшем материалов связано с ухудшением свойств;
– рекомендуется получать гранулят как промежуточный продукт, включающий в себя отходы ППУ, стабилизатор, пластификатор и наполнитель (модифицированный и наполненный гранулят отходов ППУ); а на основании его далее проводить формование изделий (литье материалов и подошв).
Список литературы Технологические аспекты получения материалов для наружных деталей низа обуви
- Карабанов, П.е., Жихарев, А.П. и Белгородский, B.C. (2008). Полимерные материалы для деталей низа обуви. Москва: КолосС, Российская Федерация.
- Костиков, В.И. и Еремеева, Ж.В. (2021). Технология композиционных материалов. Вологда: Инфра-Инженерия, Российская Федерация.
- Морозова, Л.П., Полуэктова, В.Д., Михеева, Е.Я., Калита, А.Н., Швецова, 1П, Мореходов, Г.А., Фукин, В.А., Беляев, Л.С, Костылева, В.В., Кузнецова, Л.Н. и Комнова, А.В. (1988). Справочник обувщика (Проектирование обуви, материалы). Москва: Легпромбытиздат, Российская Федерация.
- Радюк, А.Н. (2024) Получение гранулята из отходов пенополиуретана ДЛЯ литья ПОДОШВ обуви, Технологии и качество, vol. 1(63), С. 32-39.
- Banik, J., Chakraborty, D., Rizwan, M., Shaik, A.H. and Chandan, M.R. (2023). Review on disposal, recycling and management Of waste polyurethane foams: a way ahead, Waste Management & Research, vol. 41(6), pp. 1063-1080.
- Gama, N., Ferreira, A. and Barros-Timmons, A. (2018). Polyurethane foams: past, present, and future, Materials, vol. 11 (10):1841.
- Jehanno, C„ Alty, J. W, Roosen, M„ De Meester, S„ Dove, A.P., Chen, E.Y.-X., Leibfarth, F.A. and Sardon, H. (2022). Critical advances and future opportunities in upcycling commodity polymers, Nature, vol. 603 (7903), pp. 803-814.
- Kemona, A. and Piotrowska, M. (2020). Polyurethane recycling and disposal: methods and prospects, Polymers, vol. 12 (8):1752.
- Korley, L.T.J., Epps, Т.Н., Helms, B.A. and Ryan, A.J. (2021). Toward polymer upcycling-adding value and tackling circularity, Science, vol. 373 (6550), pp. 66-69.
- Kosloski-Oh, S.C.,Wood, Z.A., Manjarrez, Y., de Los RiosJ.P. and Fieser, M.E. (2021). Catalytic methods for chemical recycling or upcycling Of commercial polymers, Materials Horizons, vol. 8 (4), pp. 1084-1129.
- Mirski, R., Dukarska, D., Walkiewicz, J. and Derkowski, A. (2021). Waste wood particles from primary wood processing as a filler Of insulation PUR foams,Materials, vol. 14 (17): 4781.
- Rajic, I., Govorcin Bajsic, E. and Holjevac Grguric, T. (2020). Application of polyurethane in the production of shoe soles, The Journal Leather & Footwear, vol. 69(1), pp. 7-9.
- Salino, R.E., Catai, R.E. (2023). A study of polyurethane waste composite (PUR) and recycled plasterboard sheet cores with polyurethane foam for acoustic absorption. Construction and Building Materials, vol. 387 (1):131201.
- Schyns, Z.O.G. and Shaver, M.P. (2021). Mechanical recycling of packaging plastics: a review, Macromolecular Rapid Communications, vol. 42 (3): 2000415.
- Tiuc, A.-E., Borlea (Muresan), S.I., Nemes, 0., Vermesan, H., Vasile, 0., Popa, F. and Pintoi, R. (2022). New composite materials made from rigid/flexible polyurethane foams with fir sawdust: acoustic and thermal behavior, Polymers, vol. 14 (17): 3643.
- Vollmer, I., Jenks, M.J.F., Roelands, M.C.P., White, R.J., van Harmelen, Т., de Wild, P., Meirer, F., Keurentjes, J.T.F. and Weckhuysen, B.M. (2020). Beyond mechanical recycling: giving new life to plastic waste,Angewandte Chemie, vol. 59 (36), pp. 15402-15423.
- Yang, W., Dong, Q., Liu, S., Xie, H., Liu, L. and Li, J. (2012). Recycling and disposal methods for polyurethane foam wastes, Procedia Environmental Sciences, vol. 16, pp. 167-175.
- Yuan, J., Shi, S.Q. (2009). Effect of the addition of wood flours on the properties of rigid polyurethane foam, Journal of Applied Polymer Science, vol. 113 (5), pp. 2902-2909.