Технологические аспекты создания керамических и стеклокристаллических декоративно- облицовочных материалов с применением вторичных продуктов промышленности
Автор: Тышлангян Юлия Сергеевна, Лазарева Елена Александровна
Журнал: Горные науки и технологии @gornye-nauki-tekhnologii
Статья в выпуске: 11, 2011 года.
Бесплатный доступ
В данной статье рассмотрен синтез декоративно-облицовочных материалов с использованием стеклобоя, природного и технического сырья. А также проведено исследование эксплуатационных свойств полученных стекол и стекломатериалов для выяснения возможности их использования в качестве декоративно-отделочного материала.
Декоративно-облицовочные, стекломатериалы, фазовый состав, свойства, рентгенофазовый анализ
Короткий адрес: https://sciup.org/140215257
IDR: 140215257
Текст научной статьи Технологические аспекты создания керамических и стеклокристаллических декоративно- облицовочных материалов с применением вторичных продуктов промышленности
В настоящее время стекло и стекломатериалы играют значительную роль в строительстве и архитектуре в качестве отделочных и художественно-выразительных материалов для интерьеров и экстерьеров зданий и сооружений [1].
На современном этапе научно-технического прогресса исключительно важными проблемами являются выпуск высококачественных декоративнохудожественных стекол и стекломатериалов, снижение материало- и энергоемкости их производства, решение проблем охраны окружающей среды, переход на безотходные технологии.
В связи с этим весьма актуальной проблемой является разработка научных основ и внедрение ресурсосберегающих технологий новых художественно-декоративных стекол и стекломатериалов с высокими показателями эстетических и эксплуатационно-технических свойств.
На основе вышеизложенного в данной статье рассмотрен синтез архитектурно-строительных стекол и стеклокристаллических материалов с применением природного, технического сырья и вторичных продуктов производства.
Комплексом физико-химических методов изучено влияние структуры и фазового состава декоративных стекол и стекломатериалов на их эксплуатационно-технические и эстетические свойства.
Учитывая все вышеизложенное, были выбраны следующие направления исследований:
-
- изучение технологических особенностей варки и выработки шлаковых стекол на основе техногенного сырья;
-
- получение шлаковых стекол и стеклокристаллических материалов по стекольной и керамической ресурсосберегающим технологиям для дизайна объектов строительства и архитектуры;
-
- изучение фазового состава, структуры и эксплуатационных свойств декоративной стеклоплитки и стекол на основе техногенного сырья.
Известно, что декоративно-отделочные стекловидные и стеклокристаллические материалы могут быть получены как по стекольной, так и по стеклокерамической технологиям.
По керамической технологии образцы готовили прессованием из порошков определенного гранулометрического состава, прошедших через сито №:0063 [2].
Уже готовые отобранные фракции смешивали в заданном рецептном соотношении, после чего навеску 6-8 г полученного порошка увлажняли на стекле 3-4 каплями дистиллированной воды, тщательно перемешивали и прессовали образцы размером 20х20х15 мм в специальной пресс-форме, на прессе под давлением 9,8 МПа.
Отформованные образцы сушили на воздухе, загружали в холодную печь и подвергали обжигу при определенной температуре для разных образцов. После этого проводили визуальную оценку эстетических характеристик материалов. К рассматриваемым характеристикам относятся форма, цвет, фактура, рисунок (природный - текстура).
Форма материалов, лицевая поверхность которых воспринимается визуально в процессе эксплуатации, непосредственно влияет на своеобразие фасада или интерьера здания. В современной архитектуре форма облицовочных материалов, как правило, лаконична - квадрат, прямоугольник [2].
Как известно цвет материалов - зрительное ощущение, возникающее в результате воздействия на сетчатку глаза человека электромагнитных колебаний, отраженных от лицевой поверхности в результате действия света. Все цвета материалов можно разделить на две группы -ахроматические (белые, черные и серые всех оттенков) и хроматические (красные, оранжевые, желтые, зеленые, голубые, синие, фиолетовые со всеми промежуточными оттенками). В работе на данном этапе цвет экспериментальных образцов определяли органолептическими методами -с помощью органов зрения, визуально.
Фактура - видимое строение лицевой поверхности материала, характеризуемое степенью рельефа и блеска. По степени рельефа выделяют гладкие, шероховатые (высота рельефа до 0,5 см) и рельефные (высота рельефа более 0,5 см) фактуры [2].
По степени блеска различают блестящие и матовые.
При спекании в различных соотношениях стеклобоя и хвостов углеобогащения с выдержкой 30 мин. видно, что образцы деформируются, вспучиваютсяи имеют грязно-серый цвет с значительным количеством вкраплений (рис. 1.).
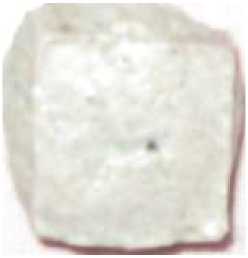
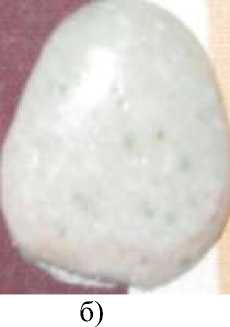
а)
Рис. 1. Внешний вид образцов материала после спекания при 9500С при соотношении стеклобой: «хвосты» углеобогащения:
а) 50:50; б) 85:15.
Поэтому для придания четких форм, прочности и приятного чвета было решено добавить природное(SiO 2 ) и техническое сырье( мел , сода, оксида магния и алюминия).
При спекании в различных соотношениях стеклобоя, «хвостов» углеобогащения и технического сырья было выявлено, что при содержании 50-90% «хвостов» сохраняются четкие грани и размеры, отсутствует вспучивание. Это можно объяснить, рассмотрев физикохимические процессы, протекающие в «хвостах» углеобогащения в интервале температур 20-9500С. Как показали исследования методом ДТА, наблюдаются эндоэффекты ( 1000С; 858,20С), которые связаны с дегидратацией, образованием твердых растворов, разложением карбонатов. Наличие экзоэффектов (137,00С;371, 0С; 436,50С; и обозначенный 783,40С) свидетельствуют о сгорании углерода и о возможности формирования кристаллической фазы CaO∙Fe 2 O 3 при использовании «хвостов» углеобогащения, например, в керамической технологии.
Характер термограммы в целом свидетельствует о выделении тепла при выгорании органической составляющей, это подтверждается результатами термографических исследований, потери при прокаливании до 9000С составляют 46,47 мас.%.
Следовательно можно сделать вывод о том, что повышенное количество «хвостов» углеобогащения способствует более эффективному спеканию образцов.
Таблица 1.
Параметры синтеза и характеристика образцов
№ |
Содержаниесырьевых компонентов,% по массе |
Температ ура спекания, 0С |
Предел прочнос ти на сжатии, МПа |
Водопог лощение ,% |
Эстетические характеристики образцов |
||
Стеклобой |
Хвосты углеобогащения |
Остальные компонен ты (сода, мел, песок, глинозем) |
|||||
1 |
2 |
3 |
4 |
5 |
6 |
7 |
8 |
1 |
50 |
10 |
40 |
850 |
9,6 |
12,6 |
четкие грани, шероховатая поверхность, светло-бежевый цвет |
2 |
50 |
30 |
20 |
850 |
9,2 |
13,9 |
четкие грани, шероховатая поверхность, бледно-розовый цвет |
3 |
30 |
50 |
20 |
850 |
7,9 |
14,3 |
четкие грани, шероховатая поверхность, бледно-розовый цвет |
4 |
20 |
70 |
10 |
850 |
6,4 |
14,8 |
четкие грани, шероховатая поверхность, кирпичный цвет |
5 |
5 |
90 |
5 |
850 |
3,5 |
15,2 |
четкие грани, шероховатая поверхность, терракотовый цвет |
6 |
50 |
10 |
40 |
900 |
9,6 |
11,7 |
четкие грани, шероховатая поверхность, бежевый цвет |
7 |
50 |
30 |
20 |
900 |
9,2 |
12,8 |
неровная вспученная поверхность, бледно-розовый цвет |
8 |
30 |
50 |
20 |
900 |
7,9 |
13,5 |
четкие грани, шероховатая поверхность, розовый цвет |
Продолжение табл. 1.
1 |
2 |
3 |
4 |
5 |
6 |
7 |
8 |
9 |
20 |
70 |
10 |
900 |
6,4 |
13,7 |
четкие грани, шероховатая поверхность, - розовый цвет |
10 |
5 |
90 |
5 |
900 |
3,5 |
14,9 |
четкие грани, шероховатая поверхность, кирпичный цвет |
11 |
50 |
10 |
40 |
950 |
9,3 |
10,5 |
четкие грани, шероховатая поверхность, матовый блеск, светло-бежевый цвет |
12 |
50 |
30 |
20 |
950 |
8,6 |
11,8 |
неровная вспученная поверхность, бледно-розовый цвет |
13 |
30 |
50 |
20 |
950 |
7,2 |
12,5 |
Неровная поверхность, бледно-розовый цвет |
14 |
20 |
70 |
10 |
950 |
5,7 |
13,2 |
четкие грани, шероховатая поверхность, терракотовый цве |
15 |
5 |
90 |
5 |
950 |
3,8 |
14,6 |
четкие грани, шероховатая поверхность, кирпичный цвет |
Синтез материалов на основе оптимального состава проводили по следующей технологической схеме (рис. 2.).
Проведенные исследования методом РФА позволили установить, что при введении 50% «хвостов» углеобогащения в структуре образуются такие кристаллические фазы как диопсид CaMgSi 2 O 6 (0,3349; 0, 2306; 0,2897 нм), фаялит Fe 2 SiO 4 (0,2847;0,2564; 0,2301нм), α-кварц(0,4258; 0,2459; 0,1544 нм), девитрит Na 2 Ca 3 Si 6 O 16 (3,844; 2,994; 2,564) [3]. При введении 70% хвостов углеобогащения в структуре помимо диопсида и α-кварца появляется феррит кальция CaFe 2 O 4 (0,3504; 0,2522; 0,1820 нм) [3]. Добавляя 90% «хвостов» основными кристаллическими фазами являются диопсид- CaMgSi 2 O 6 , α-кварца, девитрит- Na 2 Ca 3 Si 6 O 16 и феррит кальция-CaFe 2 O 4 ) [3].
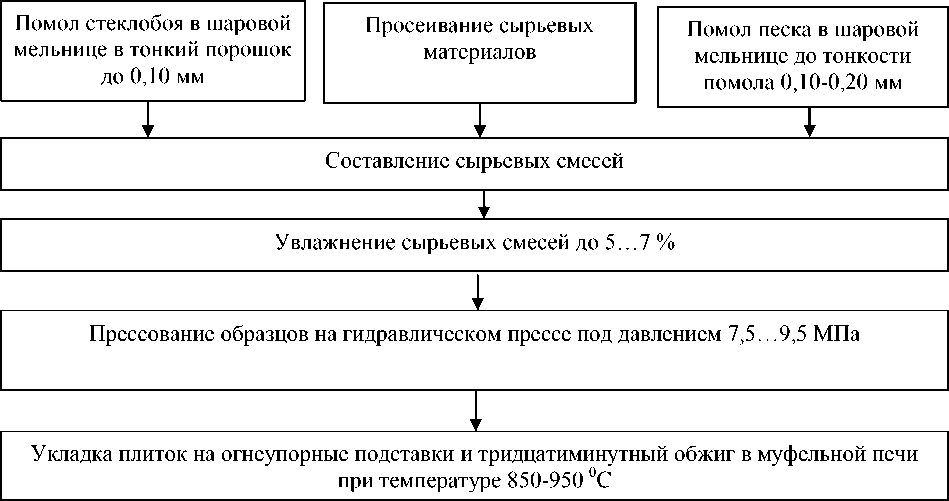
Рис. 2. Технологическая схема получения образцов на основе стеклобоя, «хвостов» углеобогащения, природного и технического сырья
Очевидно, что получение экспериментальных материалов базируется на сложном механизме формирования их структуры, включающей вышеперечисленные кристаллические фазы, способные предопределить требуемые показатели физико-механических и эстетических свойств стекол.
Для синтеза стекол был использован стекольный бой, прошедший следующие стадии подготовки:стекло измельчали на шаровой мельнице и просеивали. Применяли порошок стекла, прошедший через сито № 08 и задержанный на сите № 05, что соответствует размерам зерен стекла 0,5…0,85 мм. Кусочки, не прошедшие через сито № 08, растирали в ступке и снова просеивали.
Приготовленную шихту засыпали в алундовые тигли и ставили в электрическую печь, нагревая до Т=1350 0С, выдерживали в течение 2-2,5 часов до получения качественно проваренной стекломассы. Затем стекломассу выливали в углеродные тигли и охлаждали. Затем образцы экспериментальных стекол подвергали испытаниям в соответствии с известными методами и методиками [4].
С целью получения декоративных стёкол было использовано в качестве исходного листовое оконное стекло. Исходя из необходимости использования максимального количества стеклобоя проводили исследования различных шихтовых составов экспериментальных стекол. Варку исследуемых шихт в интервале температур 12300…1350 0С с изотермической выдержкой при максимальной температуре 2 часа.
Результаты проведенных исследований позволили установить следующее: полное завершение физико-химических процессов варки стекломассы в шихте происходит в интервале температур 1300 - 1350 0С.
Силикатообразование в шихте происходит в интервале температур 100-900 0С , завершается в интервале температур 950-11000С образованием пористого спека, состоящего из силикатов, алюмосиликатов кремнезема, оставшегося в количестве около 25% от его содержания в шихте после силикатообразования, и газов.
Наличие эндоэффекта при 101,8 свидетельствует о дегидратации и начале выгорания «хвостов» углеобогащения; при 361,0 0С с выгоранием «хвостов» углеобогащения, также происходит взаимодействие CaCO3 и Na 2 CO 3 . Эндоэффекты 570,40С , 6580С и 724,90С говорят о декарбонизации в интервале температур 600-8300С и взаимодействие Na 2 CO 3 c CaNa 2 (CO 3 ) 2 . В интервале температур 740-7800С эндоэффекты вероятно связаны с завершением процесса выгорания органической составляющей «хвостов» углеобогащения и происходит образование и плавление эвтектики Na 2 CO 3 - CaNa 2 (CO 3 ) 2 . Эндоэффект 810-835 0С свидетельствует о плавлении двойного карбоната CaNa 2 (CO 3 ) 2 и соды Na 2 CO 3 .
При повышении температуры до 1250 0С происходит плавление образовавшихся силикатов и алюмосиликатов и растворение в расплаве непрореагировавшего на стадии силикатообразования кварца (SiO 2 ). На стадии осветления и гомогенизации стекломассы при повышении температуры до 1350 0С происходит полное удаление газовых пузырей и свилей, что обеспечивает образование однородного расплава стекла. При вводе в состав стекольной шихты стеклобоя физико-химические процессы претерпевают существенные изменения, т.к. стеклобой является готовым стеклом.
При варке стекол с различным содержанием «хвостов» углеобогащения, стеклобоя и технического сырья в лабораторных условиях установлены следующие особенности в протекании различных стадий варки стекол: силикатообразования, стеклообразования, осветления, гомогенизации и студки.
Так, на стадии силикатообразования с увеличением количества стеклобоя уменьшается время, необходимое для образования силикатов и алюмосиликатов в связи с повышенным содержанием стеклобоя, в котором этот процесс завершен.
На стадии стеклообразования, сущность которой, как известно, заключается в расплавлении образовавшихся на стадии силикатообразования соединений и растворении в этом расплаве непрореагировавшей части SiO2, ввод стеклобоя с увеличением его количества сокращает время протекания этой стадии, т.к. при повышении количества стеклобоя соответственно уменьшается количество шихты и тем самым содержание кварца в ней. Это так же, как и на стадии силикатообразования, снижает энергозатраты на варку стекла. При повышении же количества «хвостов» углеобогащения увеличивается время на протекание стадии силикатообразования; при введении этого сырьевого компонента свыше 50% стекломасса при заданном режиме синтеза не проваривается.
На основании вышеизложенного для дальнейших исследований использованы образцы с содержанием «хвостов» углеобогащения 10% и 30%.
Для прогнозирования механизма кристаллизации стекол стекломатериалов проведен дифференциальный термический анализ стекла с содержанием 10% «хвостов» углеобогащения..
Характер кривой термограммы свидетельствует об образовании в экспериментальном стекле микронеоднородностей , вместе с этим ярко выраженные экзоэффекты отсутствуют.
В результате проделанной работы можно подвести итоги:
-
1. Разработаны составы и технологические параметры синтеза декоративно-облицовочных стекол с использованием боя листового стекла, «хвостов» углеобогащения, природного и технического сырья.Показано,что максимальная температура варки 1300-1350 0С, время выдержки 2,5-3часа.
-
2. Разработана ресурсосберегающая технология декоративнооблицовочных стекол на основе системы CaO-MgO-Al 2 O 3 -SiO 2 -FeO с использованием «хвостов» углеобогащения, природного и технического сырья, боя листового стекла. Получены стекла обладающие комплексом физико-химических свойств отвечающих требованиям дизайна объектов строительства и архитектуры.
-
3. По своим декоративным и функциональным свойствам экспериментальные стекла могут быть рекомендованы в производство марблита и стекломрамора.
-
4. Разработали составы и технологические параметры для стеклокристаллических материалов с использованием боя листового стекло, «хвостов» углеобогащения, природного и технического сырья. Спекание проводили в интервале температур 850-950 0С с выдержкой 30 минут.
-
5. Комплексом физико-химических методов исследований выявили особенности фазового состава, предопределяющих высокие значения физико-механических и эксплуатационных свойств материалов.
Список литературы Технологические аспекты создания керамических и стеклокристаллических декоративно- облицовочных материалов с применением вторичных продуктов промышленности
- Соловьев СП., Динеева Ю.М. Стекло в архитектуре. -М.: Стройиздат, 1981. -191 с.
- Лазарева Е.А. Технология изготовления художественных изделий из стекла: Учеб. пособие/Юж.-рос. гос. техн. ун-т. -Новочеркасск: ЮРГТУ, 2002. -160 с.
- Васильев Е.К., Нахнасон Н.С. Качественный рентгенофазовый анализ -Новосибирск: Наука, 1986. -59 с.
- Павлушкин Н.М., Сентюрин Г.Г. Практикум по технологии стекла и ситаллов. -М.: Стройиздат, 1970. -509 с.