Технология добычи блочного камня на сложноструктурных карбонатных месторождениях
Автор: Стромоногов А.В., Супрун В.И., Агафонов Ю.Г.
Журнал: Горные науки и технологии @gornye-nauki-tekhnologii
Рубрика: Разработка месторождений полезных ископаемых
Статья в выпуске: 2, 2016 года.
Бесплатный доступ
Установлено, что карбонатные месторождения Русской платформы представлены в основном слабосцементированными массивами со сложной пространственной сетью вертикальных эндогенных трещин и слоистостью, выражающейся в разделении толщи известняков на пласты и прослойки. В совокупности они определяют блочность массива. В геологической структуре месторождений доминируют (около 85 %) мелкоблочные разности от 0,2 до 0,9 м3 с выходом товарных блоков 1525 %. Всё это, вместе с возросшей потребностью в белом камне для строительно-реставрационных работ, предъявляет повышенные требования к качеству добываемых и поставляемых на камнеобработку блоков, которое невозможно обеспечить при использовании стандартных взрывных способов подготовки природных массивов к выемке. Предложена перспективная безвзрывная технология добычи блоков известняков и доломитов, обеспечивающая улучшение их качества. Технология, базирующаяся на использовании гидравлического экскаватора и баровой установки, позволяет максимально учитывать природные особенности сложноструктурных карбонатных месторождений. Установлено, что для большинства карбонатных месторождений Русской платформы разработка блочного известняка возможна как «попутная выемка» при комплексном использовании всей продуктивной толщи карбонатов. Для реализации данной технологии предлагается создание участка добычи блочного камня, интегрированного в рабочую зону крупного карьера, отрабатывающего карбонатный массив, с формированием нескольких грузопотоков разнотипного сырья. Рассмотрены технологические решения по экранированию участков выемки блоков от рабочей зоны основного карьера.
Блоки известняка, трещиноватость, слоистость, безвзрывная технология, гидравлический экскаватор, баровая установка
Короткий адрес: https://sciup.org/140215865
IDR: 140215865
Текст научной статьи Технология добычи блочного камня на сложноструктурных карбонатных месторождениях
Известняки и доломиты Русской платформы в секторе строительных материалов занимают прочное место. Это связано прежде всего с многовековой историей их использования в строительстве белокаменных сооружений, впервые появившихся во Владимиро-Суздальской Руси на рубеже XV-XVI вв. [1 - 5].
В наше время потребность в белом камне вновь выросла. Экологическая чистота, историческая адекватность, низкая стоимость дают известнякам и доломитам неоспоримые преимущества в сравнении с мраморами и гранитами отечественных и зарубежных месторождений. Использование недорогих местных строительных материалов становится все более привлекательным не только при реставрации культовых и исторических зданий, но и при новом строительстве [6 - 9].
Карбонатные месторождения Русской платформы представлены слабосцементированными массивами со сложной пространственной сетью вертикальных эндогенных трещин, образовавшихся в результате литификации осадков, и слоистостью, выражающейся в разделении толщи известняков на слои (прослойки, пласты). В совокупности они определяют размер геологических отдельностей, или блочность массива. В геологической структуре месторождений Русской платформы доминируют (около 85 %) мелкоблочные разности от 0,2 до 0,9 м3 с выходом товарных блоков 15 - 25 %.
Таким образом, несмотря на то что известняк в пределах Русской платформы является общераспространенным полезным ископаемым, проявления и зоны качественных блочных известняков являются редкими природными аномалиями. На балансе по категории «Природные облицовочные камни» находятся только два месторождения известняков - Коробчеевское в Московской области и Молоковское в Тверской [10-15].
Основными поставщиками белого камня сейчас являются карьеры, использующие стандартные взрывные способы подготовки природных массивов к выемке. В результате на камнеобрабатывающие предприятия поступают так называемые блоки-негабариты, имеющие «наведенную» взрывом микротрещиноватость и неправильную геометрическую форму. Использование такого сырья ведет к снижению выхода готовой продукции, ухудшению ее качественных характеристик и, как следствие, делает камнеобработку известняков малоэффективным процессом.
Вышеизложенное подтверждает то, что обоснование перспективных технологий добычи блочного камня, максимально учитывающих природные особенности карбонатных массивов, является весьма актуальной задачей.
Для оценки возможности создания специализированных участков (карьеров) по добыче блочного камня предлагается использовать в качестве критерия граничный коэффициент вскрыши [16]:
С -С
K гр= , ', (1)
Cв где C – себестоимость добычи полезного ископаемого подземным способом;
C – себестоимость добычи полезного ископаемого открытым способом;
C в – полные затраты на производство 1 м3 (1 т) вскрышных работ.
Схема для расчета K в условиях
вскрытых запасов продуктивного слоя и наличия остаточной карьерной выработки приведена на рис. 1.
Оговоримся сразу, что речь идет не о выделении пограничной зоны между открытым и подземным способом, а лишь о соотношении вскрышной толщи к мощности продуктивного пласта, при котором открытая разработка эффективна.
Рассматривая K как функцию выхода ( ) продукции из 1 м3 товарного блока и выхода блоков из массива ( b ), а также
ценности данного вида сырья
( M ), после несложных математических
преобразований получаем:
K гр
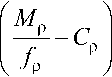
C m Cb м f г

Отсюда можно определить предельную мощность налегающей толщи карбонатных
вскрышных пород над продуктивным слоем:
H в пр
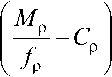
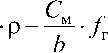
С в f г H c
где H c - мощность продуктивного слоя, м;
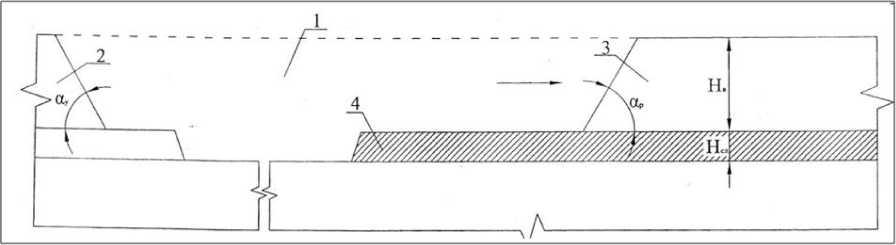
Рис. 1. Схема для расчета предельного коэффициента вскрыши в условиях вскрытых запасов продуктивного слоя и наличия остаточной карьерной выработки:
1 – выработанное пространство карьера; 2 – стационарный борт; 3 – вскрышной уступ; 4 – продуктивный слой
C m - стоимость доставки блока на камнеобрабатывающее предприятие, руб/м3;
Ср - себестоимость распиловки 1 м2 изделий из блока, руб/м2;
р - выход товарной продукции из «сырого» блока, м2/м3;
Мр - рыночная цена готовой продукции из природного камня, руб/м2;
b - выход товарных блоков из массива;
С в - полные затраты на разработку 1 м3 вскрышных пород, руб/м3;
f - коэффициент рентабельности карьера;
-
С , - себестоимость выемки 1 м3 блока, м
руб/м3;
f - коэффициент рентабельности камнеобрабатывающего предприятия.
Основными переменными, влияющими на значение H ”р, являются выход плиты (толщиной 20 мм) из 1 м3 ( р ), рыночная цена продукции ( M ) и выход блоков из продуктивного слоя ( b ).
Для известняков и доломитов Русской платформы вышеназванные показатели изменяются в следующих пределах: р = 7...23 м2/м3; М р =44...57 у.е./м2;
b = 0,1...0,5.
Для этих переменных расчетное значение HвЛр изменяется в интервалах от 3 до 7 м. При средней мощности продуктивного пласта 0,5…0,6 м это соответствует граничным коэффициентам вскрыши от 6 до 14 м3/м3.
В случае если реальная мощность налегающих над продуктивным слоем вскрышных пород выше рассчитанной по выражению (3), блочный камень может добываться только по принципу попутной выемки, при которой налегающая толща карбонатов не перемещается в отвал, а перерабатывается с получением различных видов товарной продукции (щебень, гашеная известь, бутовый камень, цементное сырье, карбонатный камень для стекольной промышленности, известковая мука и др.). Рентабельность переработки вмещающих пород может быть невысокой. Здесь важно понизить значение С„. в
Еще раз следует отметить, что полученные значения Hвпр , определяющие область и возможность создания самостоятельных участков (карьеров), справедливы для условий, когда имеются вскрытые геологические обнажения, сформированные карьерами, ранее разрабатывающими данное месторождение. Если речь идет о новых месторождениях, то дополнительным фактором, серьезно осложняющим создание самостоятельного карьера на данном месторождении, являются начальные капитальные затраты, связанные с их освоением.
Выполненный анализ горногеологических условий залегания продуктивных слоев известняка на месторождениях Русской платформы позволяет сделать вывод о том, что для абсолютного большинства карбонатных месторождений разработка блочного известняка возможна только по принципу «попутной выемки» при комплексном использовании всей продуктивной толщи карбонатов.
Это позволяет сформулировать следующие основные принципы выемки блочного камня на большинстве карбонатных месторождений Русской платформы:
-
- участок добычи блочного камня должен быть интегрирован в рабочую зону крупного карьера, отрабатывающего
карбонатный массив, с формированием нескольких грузопотоков разнотипного сырья;
-
- некондиционные блоки (до 90 %
извлекаемого объема) с участка выемки блочного камня должны быть экономически эффективно переработаны в другие виды продукции;
- породы, вмещающие продуктивные пласты известняков, на специализированном участке добычи блочного известняка должны разрабатываться безвзрывным способом, а сам участок должен быть экранирован от основной рабочей зоны карьера.
При формировании безвзрывной технологии выемки блочных известняков и доломитов необходимо максимально использовать природные особенности карбонатных месторождений Русской платформы (развитая система эндогенных трещин, слоистость, малая мощность продуктивных слоев).
Применение алмазно-канатного пиления [17-19] в силу этих особенностей, а также в связи с тем, что продуктивные горизонты расположены на средних и нижних гипсометрических уровнях разрабатываемого природного массива, затруднительно. Кроме того, на большинстве карьеров используются зависимые системы разработки с жесткой последовательностью выполнения вскрышных, добычных и горноподготовительных работ. При этом долговременные вскрышные запасы наилучшим образом соответствует технология разработки блочных известняков, базирующаяся на использовании гидравлического экскаватора и баровой установки [20-21].
Технологическая схема вскрытия представлена на рис. 2.
Отработка вскрышных рыхлых и полускальных пород ведется экскаваторами основного карьера.
В связи с тем что продуктивные пласты следует отрабатывать безвзрывным способом для сохранения их целостности, отработку этих слоев предлагается производить стреловыми фрезерными комбайнами. Применение именно стреловых фрезерных комбайнов, а не шнеко-фрезерных [22] или машин с роторными колесами, при отработке скальных пород на карбонатных месторождениях Русской платформы обусловлено тем, что при работе стрелового комбайна не требуется создания большого фронта работ, что является очень важным для машин класса CSM.
Баровой машиной производят вертикальные пропилы на глубину, равную мощности пласта. Работа бара должна осуществляться так, чтобы пропилы ограничены.
располагались перпендикулярно к
Геологической
структуре карбонатных
месторождений
Рыхлые породы
Русской
Механический / экскаватор
платформы
направлению трещин (рис. 3).
простирания
эндогенных
Рыхлые и полускальные (1) ■ породы
Механический экскаватор _____ Стреловой / фрезерный комбайн
Баровая установка
Скальные пород <
1 технология _ ,
_ _ _ _Ьлочныи_кам£нь
Скальные породы (Продуктивная толща) Стандартная технология (Механическая лопата + БВР)
Гидравлический экскаватор _____ Зона
/ экранирования
Механический экскаватор
Рис. 2. Технологическая схема участка по отработке известняков на блочный камень при комплексной отработке месторождения
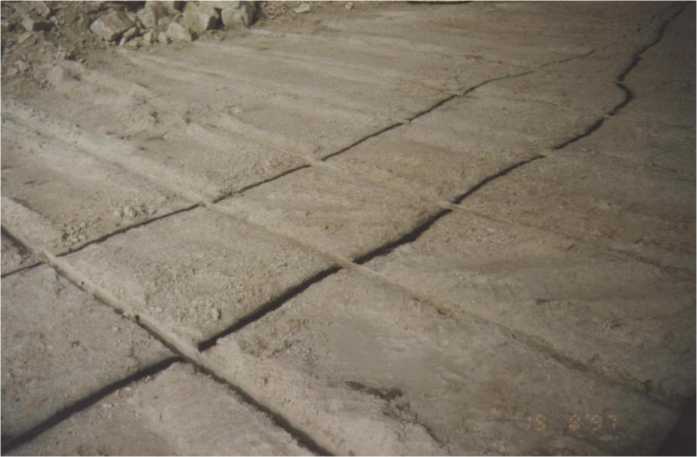
Рис. 3. Баровые пропилы в мячковском слое известняка (Афанасьевский карьер)
Это позволяет сформировать блоки прямоугольных очертаний и увеличить их выходы. Расстояние между баровыми пропилами должно обеспечивать такие размеры блоков, которые могут отгружаться в автотранспорт. При работе бара за счет резания и вибрации цепи происходит ослабление связей геологических отдельностей между собой и создание техногенных плоскостей ослабления, что в свою очередь приводит к снижению необходимого уровня усилия гидравлического экскаватора и тем самым к увеличению его производительности.
При использовании баровой установки для подготовки продуктивных слоев к выемке важно выполнить геометризацию массива, которая позволяет определить направление простирания основных эндогенных трещин, разбивающих продуктивный пласт на геологические отдельности [23, 24]. Баровая установка позволяет производить пропилы с учетом закономерностей изменения частоты и направления эндогенных трещин, повышая тем самым «фактическую» блочность. Трещины в карбонатных массивах Русской платформы составляют сложные пространственные сети (рис. 4). Они возникают из-за уменьшения объема горных пород при диагенезе осадков. Эти трещины носят название эндогенных, или первичных, трещин усыхания или трещин отдельности. Такие трещины располагаются перпендикулярно к слоистости и образуют несколько систем, предопределяющих в совокупности со слоистостью разделение массива на геологические отдельности определенных размеров (рис. 5).
Эндогенные трещины не выходят за границы пласта. Они ограничиваются плоскостями слоистости.
Следующим технологическим этапом является разборка продуктивного пласта на геологические отдельности по трем системам ослабляющих поверхностей, а именно, по контурам слоистости, вертикальным эндогенным трещинам и технологическим плоскостям ослабления. Приложение нагрузки к геологическим отдельностям должно осуществляться циклично снизу вверх (от контакта, лежащего на нижней плоскости слоистости к кровле продуктивного пласта). Реализации такой схемы выемочного процесса по кинематическим и силовым параметрам в наибольшей степени соответствует применение прямых гидравлических лопат с вырывным усилием 17…27 т Н [25, 26].
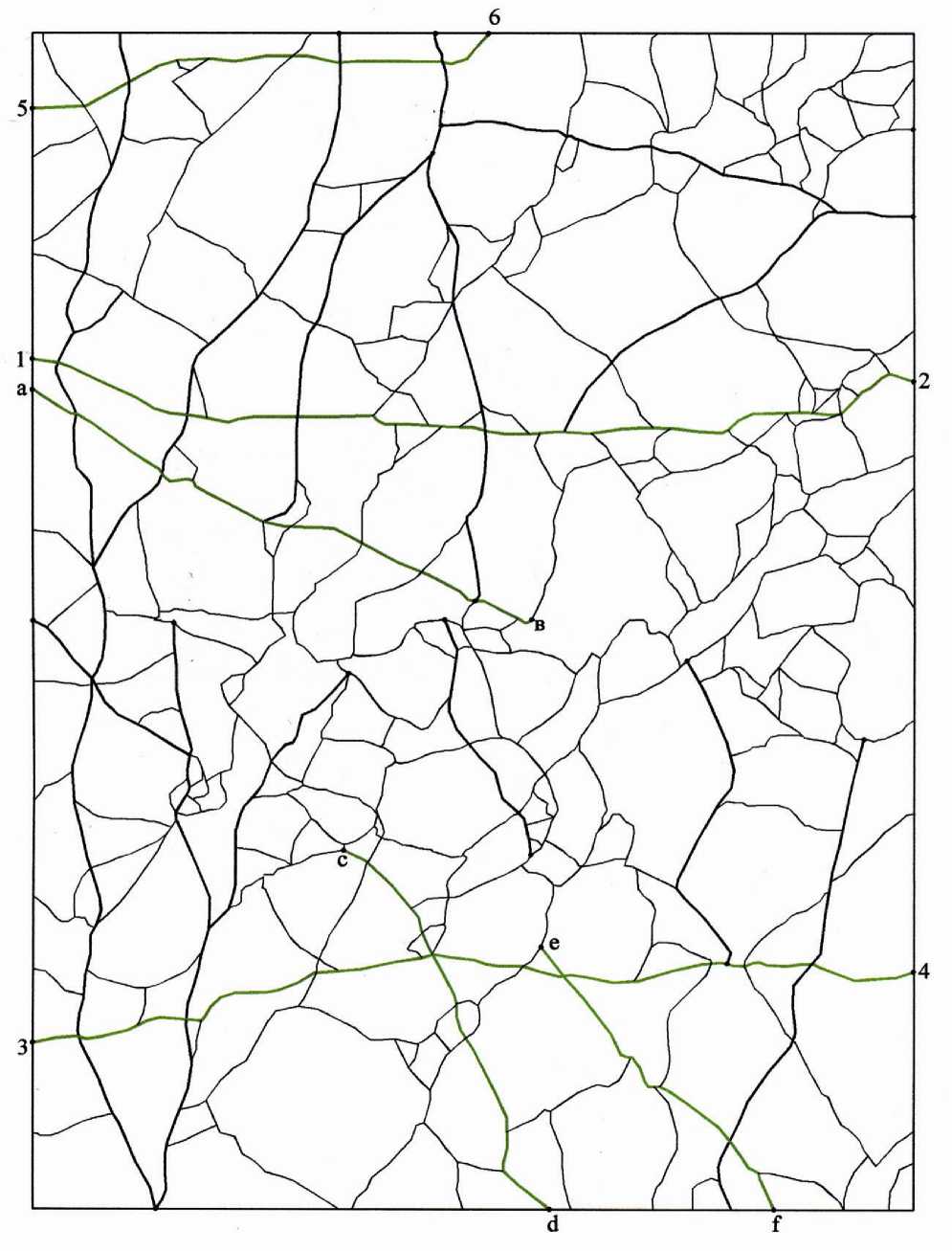
Рис. 4. Схема распространения вертикальных эндогенных трещин (срез по кровле слоя карбонатного массива): 1 - 2, 3 - 4, 5 - 6 - трещины первой системы;
a - b, c - d, e-f - трещины второй системы.
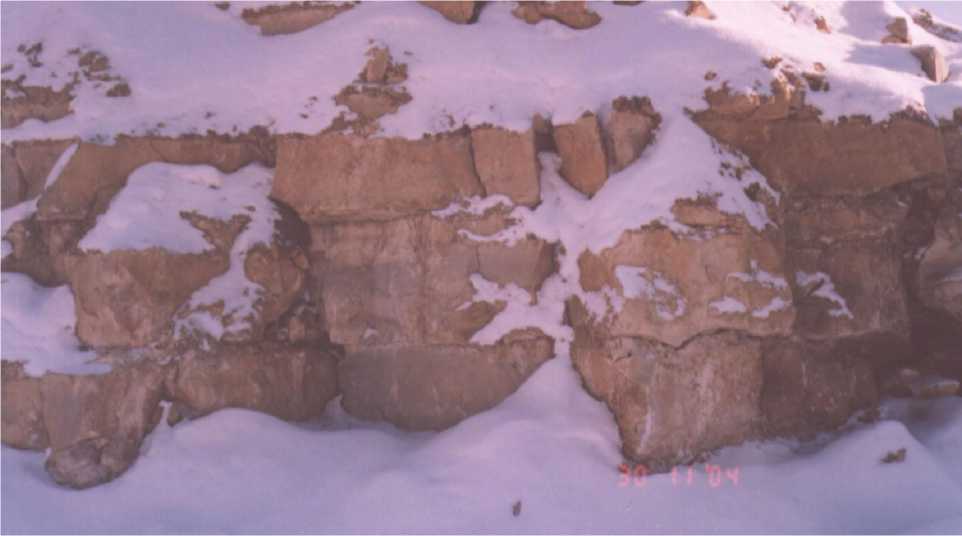
Рис. 5. Продуктивные пласты, разбитые вертикальными эндогенными трещинами на геологические отдельности
Разработка массива прямой гидравлической лопатой производится путем внедрения ковша в трещины между отдельностями (по плоскости поверхности) и взламывания блоков. Машинист экскаватора, видя забой, выбирает место ослабления и производит разборку массива. При работе экскаватора типа обратная лопата машинист не видит поверхность забоя и зоны контактов пород разностных слоев.
Опыт разборки карбонатных массивов на геологические отдельности показывает, что на эффективность разборки мало влияет механическая прочность самих отдельностей (она может достигать даже 110…150 МПа). Важнейшим фактором здесь являются силы сцепления вынимаемого блока с нижележащим слоем и распорные усилия, возникающие вдоль природных трещин, оконтуривающих геологическую отдельность (блок). Усилия копания для таких пород должны быть весьма высокими, так как производительность на погрузке имеет второстепенное значение.
Одной из важнейших составляющих предлагаемой технологии добычи блочного камня является экранирование участков выемки блоков от рабочей зоны карьера, где производство горных работ идет с использованием стандартных методов взрывной подготовки массива. Экранирование должно выполняться по трем профильным линиям (рис. 6). Две из них – AB и CD – отсекают участок выемки блочного камня ( F ) от рабочей зоны по высоте всей зоны скальных пород. Нижняя профильная линия экранирования АС отсекает участок F от группы нижних горизонтов карьера.
В качестве альтернативного может рассматриваться вариант, когда вместо экранирования по контуру ВАСD оставляется участок временной консервации горных работ (рис. 6). Однако данный вариант нельзя признать экономически благоприятным, так как он предполагает консервацию горных работ в полосе 40…50 м, что увеличивает капитальные и эксплуатационные издержки на создание специализированного участка по добыче блочного камня. Однако его использование возможно в случаях, когда карьер имеет резервы, позволяющие без ущерба для основного производства выделить на флангах или в центре рабочей зоны участок протяженностью 250…300 метров для безвзрывной добычи блочного камня.
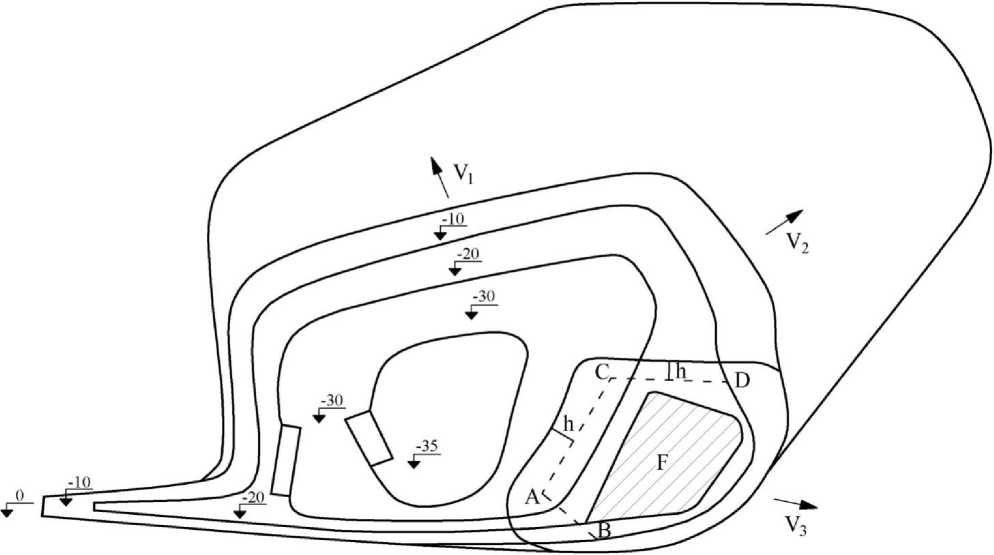
Рис. 6. Схема экранирования участка добычи блочного камня от рабочей зоны карьера
Наиболее эффективным методом экранирования участков выемки блоков в карбонатных массивах является метод предварительного щелеобразования. Его применение для экранирования требует обоснования основных параметров взрывных работ: диаметра скважин, расстояния между скважинами (шпурами), ориентацию линии контурных скважин, конструкции заряда в скважине.
Использование предлагаемых технологических решений при добыче блоков известняка на Афанасьевском месторождении в Московской области и Малеевском месторождении в Рязанской области показало их высокую эффективность.
Издательство «Горная книга», 2008. – 306 с.
Список литературы Технология добычи блочного камня на сложноструктурных карбонатных месторождениях
- Звягинцев Л.И. Русь белокаменная. -М.: Издательство «Горная книга», 2008. -306 с.
- Супрун В.И. Белый камень. -М.: Издательство «Горная книга», 2010. -153с.
- Стромоногов А.В., Супрун Е.В. Использование природного камня в храмостроительстве//Православный экономический вестник/Приход. -2003. -№4, 5.
- Воронин М.Н. Владимир, Боголюбово, Суздаль, Юрьев-Польский. -М.: Искусство, 1962.
- Сперанский А.Н. Очерки истории приказа каменных дел Московского государства. -М.: РАНИОН, 1930.
- Викторов А.М., Викторова Л.А. Природный камень в архитектуре. -М.: Стройиздат, 1983.
- Казарян Ж.А. Природный камень (добыча, обработка, применение): Справочник. -М.: Петракомплект, 1998.
- ГОСТ 30629-99. Материалы и изделия облицовочные из горных пород. Методы испытания.
- Беликов Б.П., Петров В.П. Облицовочный камень и его оценка. -М.: Наука, 1977.
- Звягинцев Л.И., Викторов А.М. Белый камень Подмосковья. -М.: Недра, 1989.
- ГОСТ 9480-89. Плиты облицовочные пиленые из природного камня. Технические условия.
- Ануфриев А.А. Белый камень Подмосковья/Природные условия строительства и сохранения Храмов православной Руси: Сб. тр. 1-го Междунар. науч.-практ. симпозиума//Московская Патриархия: Троице-Сергиева Лавра, 2000.
- Залесский Б.В., Степанов В.Я., Флоренский К.П. Опыт изучения физических свойств известняков мячковского горизонта (песковская группа месторождений). -АНСССР, Труды института геологических наук, вып. 123, Петрографическая серия (№37), 1950.
- Стромоногов А.В., Супрун Е.В. Требования к качеству белого камня для реставрационных работ//Камень и бизнес. -2003 (№2) -C. 12.
- Стромоногов А.В., Супрун Е.В. Реставрация и воссоздание каменных памятников древней Руси//Империя камня. -2005 (№6). -C. 64
- Ржевский В.В. Открытые горные работы. Ч. 1 и 2. -М.: Недра, 1985.
- Синельников О.Б. Природный облицовочный камень. -М.: Изд-во МГГУ, 2000.
- Косолапов А.И. Технология добычи облицовочного камня. -Красноярск: Изд-во Красноярского университета, 1990.
- C.Singewald., Naturwerkstein. Exploration und Gewinnung. -Steintechnisches Institut, Mayen-Köln: R.Muller, 1992.
- Штейнцайг В.М. Интенсификация открытых горных работ с применением мощных карьерных одноковшовых экскаваторов. -М.: Наука, 1990.
- Технология добычи блоков известняка/Л.И. Звягинцев, В.И. Супрун, Н.М. Кулин и др.//Камень и Бизнес. -2001. -№1 -С. 7.
- B.Schimm, J.Georg Wirtgen Surface Miner-The First Link of a Simple Extraction and Materials Handling Chain in «Medium Hard» Rock.Proceedings of the 12 Intertnational Symposium Continuous Surface Mining-Aachen 2014,Springer, s. 511-521.
- Руппенейт К.В. Деформируемость массивов трещиноватых горных пород. -М.: Недра, 1975.
- Анощенко Н.Н. Геометрический анализ трещиноватости и блочности месторождений облицовочного камня. -М.: МГИ, 1983.
- Штейнцайг Р.М. Методика определения параметров и показателей эффективности применения карьерных гидравлических экскаваторов. -М.: Ин-т горного дела им. А.А. Скочинского, 1980.
- Бульбашев А.П., Билюкин А.Б., Супрун В.И. и др. Безвзрывная селективная выемка сложноструктурных залежей//Горный журнал. -1996. -№11-12 -С. 70.