Технология и оборудование для получения новых видов топлив из отходов полимеров
Автор: Журавский Геннадий Иванович, Жданок Виталий Александрович, Матвейчук Александр Сергеевич, Мартинов Олег Георгиевич, Романовский Александр Васильевич
Журнал: Вестник Витебского государственного технологического университета @vestnik-vstu
Рубрика: Химическая технология и экология
Статья в выпуске: 1 (16), 2009 года.
Бесплатный доступ
Предложен способ высокоскоростного термолиза отходов полимеров, при котором подвод тепла к перерабатываемому материалу интенсифицируется введением перегретого водяного пара в зону реакции. Результаты выполненных расчетов подтверждают возможность реализации данной технологической схемы для получения новых видов топлив. Проанализированы основные пути использования конечных продуктов переработки.
Новые виды топлива, топливо из отходов, полимерные материалы, полимеры, технологии переработки, технологическое оборудование, отходы полимеров, переработка полимеров, продукты переработки, топлива, получение топлив, органические материалы, высокоскоростной термолиз, пиролиз, реакторы термолиза, вращающиеся реакторы, обогревающие рубашки, пароперегреватели, теплообмен, расчет теплообмена
Короткий адрес: https://sciup.org/142184544
IDR: 142184544
Текст научной статьи Технология и оборудование для получения новых видов топлив из отходов полимеров
В настоящее время высокоскоростной пиролиз (термолиз) органических материалов (в первую очередь отходов) рассматривается как метод для получения максимального количества жидких или газообразных продуктов топливного и сырьевого назначения.
Основная задача при реализации данного вида процесса – это подвод необходимой для термической деструкции энергии (теплоты) в течение интервалов времени, исчисляющихся секундами. Для решения этой задачи используется диспергированный органический материал и высокая разность температур между греющей поверхностью и частицами материала. При этом техническая реализация процесса осуществляется путем использования кипящего слоя, перемешивания и ряда других способов (инфракрасный нагрев, контактирование с нагретыми телами и др.) [1, 2].
Другой важной задачей при реализации технологии высокоскоростного термолиза является подавление вторичных реакций между продуктами разложения органического материала. Широко используемый в известных технологиях способ подавления вторичных реакций – это быстрая эвакуация продуктов разложения из реактора и быстрое их охлаждение путем организации высокоинтенсивного теплообмена в системе конденсации.
В настоящей работе предлагается способ решения вышеназванных задач, заключающийся во введении перегретого до температур свыше 1000 оС водяного пара в реактор термолиза со скользящим тонким слоем отходов. Это позволяет снизить концентрации газообразных продуктов разложения органических веществ и таким образом снизить (или полностью подавить) вероятность вторичного реагирования, а также интенсифицировать процесс подвода тепла к материалу.
Для реализации предложенного способа разработан специальный вращающийся реактор, а также система охлаждения и конденсации газообразных продуктов термического разложения органических составляющих отходов. Реактор представляет собой вращающуюся трубу с установленной внутри винтовой поверхностью, которая размещена в цилиндрической рубашке, содержащей пароперегреватель в виде змеевика. К рубашке реактора подключены горелки, в которых сжигается часть летучих продуктов разложения отходов. При вращении реактора органические отходы в виде тонкого слоя перемещаются по винтовой линии и контактируют с нагретой до температуры 600-800 оС внутренней поверхностью реактора. Таким образом, создается высокая разность температур между греющей поверхностью и частицами отходов, а необходимое для термолиза тепло передается как от нагреваемой продуктами сгорания стенки трубы, так и от перегретого водяного пара. Образующиеся в результате термолиза отходов летучие продукты разбавляются водяным паром и в виде парогазовой смеси выводятся в систему охлаждения и конденсации.
Рассмотрим два режима работы реактора I и II (см. табл. 1):
Таблица 1
I режим |
II режим |
|
T g – температура газового потока (вход и выход), оС |
1200 и 650 |
1100 и 550 |
T s – температура пара на входе в перегреватель, оС |
160 |
160 |
T s – температура потока перегретого пара (вход и выход), оС |
750 и 550 |
750 и 450 |
T t – температура парогазовой смеси (в реакторе), оС |
550 |
450 |
Обогревающая рубашка размещена вокруг реактора по винтовой линии с шагом 500 мм и имеет прямоугольное сечение 500 × 200 мм с учетом толщины стенок 10 мм. Таким образом, сечение для прохода продуктов сгорания равно 480 × 180 мм, а площадь сечения – 0,086 м2. Скорость течения газового потока в этом случае соответствует 12 м/с и 8 м/с. Расчет теплообмена при течении продуктов сгорания в обогревающей рубашке выполнен по известным соотношениям, которые приведены в табл. 2.
Таблица 2 – Расчет теплообмена в рубашке с пароперегревателем
I режим |
II режим |
(1200+650) / 2 = 925 оС – средняя температура продуктов сгорания, протекающих в обогревательной рубашке |
(1100 + 550)/ 2 = 825 оС; |
9, g = 12 м/с – скорость продуктов сгорания |
9 , g = 8 м/с |
A = 0.331 м – характерный размер |
A = 0.331м |
X g = 0.090 Вт/(м- о С) - теплопроводность газа при 925 оС |
X g = 0.080 Вт/м-оС -теплопроводность при 825 оС |
V g =130. 10-6 м2/с – кинематическая вязкость |
V g =110·10-6 м2/с |
Pr g = 0,60 |
Pr g = 0,61 |
Re g = ( 9 g A) / V g = (12.0,331) / 130-10 " 6 = 30554 |
Re g = (8·0,331) / 110·10-6= 27273 |
Nu g = 0.023 • ( 30554 ) 08 • 0.6043 = 71.5 |
Nug = 0.023 - ( 27273 ) 0.8 • 0.61 0'43 = 65,8 |
Nu •X 71.5 • 0.090 , 2 a =-----=----------= 19 Вт / м • g A 0.331 |
Nu •X 65.8 • 0.080 , 2 a =-----=---------- = 15.9 Вт/м • C g A 0.331 |
Характерный размер (диаметр) рассчитан следующим образом:
А = {4 (0,086 м2) / 3,14}0,5= 0,331 м.
В обогревающем канале размещен пароперегреватель (труба диаметром 150 мм). Таким образом площадь проходного сечения для продуктов сгорания в обогревающем канале равна S = 0,086 м2 - 0,017м2 = 0,069 м2.
Определим величину теплообмена излучением от продуктов сгорания к стенке обогревающего канала.
Удельный тепловой поток излучением и коэффициент теплоотдачи рассчитываются по формулам (1) и (2) соответственно:
q u = C o ' е
( 4 c
1100 J
( > 4
Tдг
( 100 )
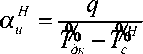
где Т дг - средняя температура продуктов сгорания, Т дг = 925 оС и 825 оС; Т -средняя температура стенки обогревающего канала; Т С = 650 оС и 550 оС; С о -излучательная способность абсолютно черного тела, С о = 5,67 Вт/(м2-К4); £ -степень черноты продуктов сгорания, £ = 0,18.
Расчет по соотношению (1) и (2) дает значения удельных тепловых потоков и коэффициентов теплообмена излучением в режиме I и II соответственно:
q U = 13615 Вт, а Н = 49.5 Вт/(м2 К);
q U = 10152 Вт, ат Т = 37 Вт/(м2-К) .
Суммарный коэффициент теплоотдачи при Тдг = 925 оС и Тдг = 825 оС соответственно:
£ а Н = а к + а Н = 68,5 Вт/(м2-К), (3)
£ а т = а к + а Т = 52,9 Вт/(м2-К). (4)
Учитывая, что коэффициент теплоотдачи от внутренней стороны стенок обогревающего канала а с = 78 Вт/(м2 оС), определим коэффициент теплопередачи по формуле:
к =
1 δ 1
+ +
α λ α с
где б - толщина стенки, б = 0,010 м; X - коэффициент теплопроводности материала стенки, X = 22 Вт/(м-К).
Подставив в (5) численные значения коэффициентов теплоотдачи, получим значение коэффициента теплопередачи при Т дг = 925 оС и Т дг = 825 оС соответственно: K Н = 36 Вт/(м2-К) и K Т = 28,5 Вт/(м2К).
Определяем количество тепла, передаваемое при Т дг = 925 оС и Т дг = 825 оС по соотношению (6):
Q Нер = К Н ■ F ■( Т дг - Т Н ) (6)
В результате получим Q Нер = 497376 Вт и Q Тер = 393756 Вт. При этом учтено, что площадь поверхности обогревающей рубашки F = 50,24м2.
Таким образом, тепловая мощность (передача тепла только от продуктов сгорания) равна 497,376 кВт (0,497МВт) и 393,756 кВт (0,393 МВт).
Тепло от цилиндрической стенки рубашки передается стенке трубы, в которой смонтирован шнек в основном излучением. В канале, образованном стенкой рубашки и стенкой трубы (расстояние между стенками σ) практически отсутствует движение газовой среды и поэтому конвективный теплообмен весьма мал. Можно также пренебречь и теплообменом путем теплопроводности через газовый зазор между стенками. Расчет теплообмена от цилиндрической стенки рубашки может быть выполнен по соотношению:
arad = Co •£„ • / (2 - £w ) { -1- 4 - ^ 4} / (Т - Т), (7) rad0w w 100 ) 1 100 )
Для значений T 1 = 923 К (средняя температура цилиндрической стенки рубашки), Т 2 = 823 К (средняя температура стенки трубы, в которой смонтирован шнек) и е w = 0,85 (коэффициент теплового излучения стальной стенки рубашки) расчет по вышеприведенному соотношению дает a rad = 112 Вт/(м2К), а для значений T 1 =
823 К и Т2 = 723 К расчет по вышеприведенному соотношению дает a rad = 78 Вт/(м2·K).
Процесс термолиза полимеров состоит из их нагрева до 350-500 оС и последующего разрушения. В теории это можно рассмотреть как изотермический процесс [2, 3]. Для производительности по отходам G t = 1000 кг/ч получим необходимую мощность (без учета тепловых потерь):
Q t = G < "[ c p«) • ( 500 — 20 ) + h t ] , (8)
где ht = 230 кДж/кг – средняя теплота термолиза полимеров; Cp(t) = 1,67 кДж/(кг K) – удельная теплоемкость отходов; 20 оС – начальная температура отходов; 500 оС – конечная температура отходов. Расчет по соотношению (8) дает значение Qt = 0,29 МВт.
Передача тепла от продуктов сгорания к водяному пару осуществляется через стенку трубы пароперегревателя. Расчет пароперегревателя для перегрева рабочего водяного пара с определением величины коэффициентов теплопередачи выполнены на основании соотношений, приведенных в табл. 3 и 4. Анализ данных таблиц показывает, что количество передаваемого от продуктов сгорания тепла к водяному пару лимитируется теплообменом от продуктов сгорания к внешней стенке пароперегревателя, а не теплообменом от внутренней стенки трубы пароперегревателя к водяному пару.
Таблица 3 – Расчет теплообмена при течении водяного пара в пароперегревателе
I |
II |
1 |
2 |
d c = 0,15 м – диаметр трубы пароперегревателя X s = 0,04 Вт/(м оС) - теплопроводность пара ц = 2,15•Ю-6 , 2 s кгс/м2 – динамическая вязкость P s = 1,0 кг/м3 - плотность пара g Ц Л 1 1 6 2 / V s = ^-- 2Ы0 м /с р - кинематическая вязкость п 51= Pr - S s Л “ 2 s 1 4 0.0177м2 – площадь сечения трубы |
d c = 0,05 м X s = 0,04 Вт/(м^оС) ц= 2,15 40 "6 , 2 s , кгс/м2 P s - 1.0 кг/м3 g ц 1 1 /\ 6 2 / Vs =^!-- 21 ^ 10 м / с р Рг 2^ Prs - 1 |
Продолжение таблицы 3
1 |
2 |
Скорость потока: ».= G s =------ 1000------ . 15.7 s 3600 -p s - Ss 3600 - 1,0 - 0,0177 м/с Re = 9А = 15.7 - 0, 1 5 5 0,112 - 10 6 s v 21 - 10 - 6 Nu = 0.023 - Re 08 • Pr 043 Nus = 0,023 - ( 0,112 - 10 6 ) 0,8 - 10,43 = 252 Nu -X 252 - 0,04 2 r a =----- =--------= 67.2 Вт/ м - C s d 0,15 |
9 = -----1000----- ^ 139
Re =-^ d c = 139 - 0, ° 5 = 0,33110 6 s v 21 - 10 - 6 Nu = 0.023 - Re 08 - Pr 043 Nu . = 0,023 - ( 0,331 - 10 6 ) °,8 - 1 °,43 = 599 Nu-X 599-0,04 - a =----=-----,— = 479 Вт / м 2 - C s d 0,05 |
Таблица 4 – Расчет теплообмена от продуктов сгорания к трубе пароперегревателя
I |
II |
1200 + 650 = 925 0 C |
1100 + 550 _ 0 |
2 – средняя температура |
2 |
9, g = 12 м/с – скорость нагревающего газа |
9 . g = 8 м/с |
d out = 0,16 м - внешний диаметр трубы |
d out = 0.06 м |
X g = 0,08 Вт/(м о С) - теплопроводность газа v = 180 - 10 - 6 м 2 /с s кинематическая вязкость Pr g " 0,74 Re 9 d out = 12 - 0,16 ~ 10667 |
X g = 0,075 Вт/(м оС) v s = 170 - 10 - 6 м 2 / с Pr g " 0,74
Re
= ^ |
g v 180 - 10 - 6 |
|
Nu = 0.177 - Re 0'64 - Pr 0'43 |
Nu = 0.177 - Re 064 - Pr 0-43 |
Nug = 0,177 - ( 10667 ) 0,6 4 - 0,740,43 = 58,8 |
Nug = 0,177 - ( 2824 ) 0,6 4 - 0,740,43 = 25.1 |
„ _ Nu -X_ 58,8 - 0,08 |
|
g d out 0,16 |
Nu -X 25.1 - 0,08 2 a =-----=---------= 33.5 Вт/м - C g d out 0,06 |
Вычисление общего коэффициента теплопередачи между продуктами сгорания и водяным паром, проходящими по пароперегревателю, представлены в табл. 5.
Таблица 5 – Расчет коэффициента теплопередачи
I |
II |
K R(g + .) = 11 = 1 1 = 20-4 ВТ /м2 - C + + a g a ra d 29.4 67.2 |
K R(g+s) = n-----r = 33 Вт/м 2 - C 1 35.5 479 |
Тепло, необходимое для перегрева пара до заданной температуры, рассчитано следующим образом (табл. 6):
Таблица 6 – Расчет необходимого тепла для перегрева водяного пара расходом 1000 кг/ч
I режим |
II режим |
Q s = G s • C p(s) • ( T ss - T s1 ) = =1000·0,5·(750 – 160) = 0,295 Гкал/ч = = 0,34 МВт |
Q s = G s • C p(s) • ( T ss - T s1 ) = = 1000·0,5·(750 – 160) = 0,295 Гкал/ч = = 0,34 МВт |
Определим поверхность трубы пароперегревателя и его длину (табл. 7):
Таблица 7 – Расчет величины поверхности и длины трубы пароперегревателя
I |
II |
Q s _ 0,34 • IO6 2 F =------=--------— 28,2 M K •A T 20.4 • 590 F 28,2 L = — =------— 56 м n d 3,14 • 0,16 |
F = -Qi- = 0,34 . 101 — 31.7 m 2 K •A T 33 • 325 F 317 L = — =------— 168м n d 3,14 • 0,06 |
Выполненные расчеты показывают, что технология высокоскоростного термолиза отходов полимеров для получения новых видов топлив может быть реализована с использованием вращающегося реактора. При этом из отходов полимеров, например, смеси полиэтилена, полипропилена, полистирола и резины путем высокоскоростного термолиза могут быть получены жидкие, газообразные и твердые продукты. Жидкие продукты по своим основным показателям являются аналогами жидких топлив, производимых из нефтяного сырья (мазут, печное топливо). Газообразные продукты могут использоваться как заменители природного газа, а твердые продукты могут найти применение в качестве фильтрующих материалов для очистки промышленных стоков.
Список литературы Технология и оборудование для получения новых видов топлив из отходов полимеров
- Железная, Т. А. Современные технологии получения жидкого топлива из биомассы быстрым пиролизом. Обзор. Часть 1/Т. А. Железная, Г. Г. Гелетуха//Промышленная теплотехника. ─ Том 27. ─ №4. ─ С. 91-100.
- Железная, Т. А. Современные технологии получения жидкого топлива из биомассы быстрым пиролизом. Обзор. Часть 2/Т. А. Железная, Г. Г. Гелетуха//Промышленная теплотехника. ─ Том 27. ─ №5. ─ С. 79-90.
- D.V. Aristarkhov, G.I. Zhuravskii. Modeling of the Vapor Thermolysis of Rubber Waste//Journal of Engineering Physics and Thermophysics. Vol. 74, №6, 2001.
- G.I. Zhuravskii, V.A. Sychevskii. Numerical Calculation of Vapor Thermolysis of Organic Wastes//Journal of Engineering Physics and Thermophysics. Vol. 674, № 6, 2003.