Технология оценки качества станков
Автор: Никитин А.В., Раменская Е.В., Бургардт Е.В., Филиппов Ю.А.
Журнал: Сибирский аэрокосмический журнал @vestnik-sibsau
Рубрика: Технологические процессы и материалы
Статья в выпуске: 3 (6), 2005 года.
Бесплатный доступ
Рассмотрены вопросы состояния станочного парка страны, проблемы управления вибрационными процессами на основе имитационного моделирования с целью создания новых конструкций станков повышенной точности и конкурентоспособности.
Короткий адрес: https://sciup.org/148175074
IDR: 148175074
Текст научной статьи Технология оценки качества станков
Производство товарной продукции в различных отраслях народного хозяйства до сих пор продолжается с использованием устаревшего и физически изношенного технологического оборудования, имеющего малую производительность и рентабельность. Отсутствие современной технологии ускоренной диагностики технического состояния эксплуатируемого технологического оборудования с целью вывода его из работы не позволяет принимать обоснованные технические решения без риска значительных потерь производственных мощностей предприятий ведущих отраслей России. Кроме этого, снижение темпов создания новых станков привело к пороговому уровню, свидетельствующему о невозможности воспроизводства даже освоенных ранее прогрессивных конструкций металлорежущих станков.
Ежегодный отчет по мировому производству и реализации металлообрабатывающего оборудования показывает, что на протяжении последних 5 лет лидерами являются Япония и Германия, имеющие по 12 ведущих станкостроительных фирм, созданных ранее по плану Маршалла и входящих в число 30 лидирующих фирм - изготовителей станочной продукции в мире. При этом 2 лидирующие фирмы ежегодно реализуют станки от 1,0 до 1,5 млрд долларов каждая. Российские предприятия станкостроения в этих отчетах не упоминаются, поэтому основной целью Постановления Правительства РФ № 226 от 16.03.2000 являлось определение перспектив развития станкостроительной и инструментальной промышленности для того, чтобы возвратить Россию в лидирующую группу мировых производителей станков.
Следует заметить, что индикатором начала развития и успешного функционирования экономики страны является превышение в 2...3 раза темпов роста выпуска технологического оборудования по сравнению с темпами выпуска потребительской товарной продукции. Но пока в Российской Федерации заметных изменений в этом плане не наблюдается. Основные причины такого положения известны. Главной из них является низкая культура технологии проектирования и изготовления оборудования, особенно по показателям назначения. Консерватизм в станкостроении особенно опасен при освоении и создании новых знаний, базирующихся на фундаментальных основах классической механики [2; 6].
В настоящее время небольшое, казалось бы, ответвление общего машиностроения - станкостроение - испытывает бурный рост, особенно в Китае, в то же время у нас вопросы реальной модернизации производства оборудования отошли на второй план. Так, например, в связи с запуском в производство новых моделей автомашин, характер задач управления и синхронизации мате риальных потоков качественно усложняется. Вопросы закупки нового оборудования конкретных типов и моделей и согласования их характеристик со старым, перестройки структуры и ритмов вспомогательных конвейеров, улучшения планировки размещения оборудования невозможно решить без наличия новой номенклатуры перспективного оборудования. Цействительно, начиная с 1990 г., в России значительно сократился выпуск металлорежущих станков (МРС) и кузнечно-прессового оборудования (КПО) (рис. 1).
Рис. 1. Выпуск станов в России, относительные единицы
Технология производства изделий, обеспечивающая качественные показатели товарной продукции, формирует функциональные требования к точности, жесткости и вибрации технологического оборудования (ТО). Убедительность и достоверность высказанному положению придают имеющиеся материалы по измерению вибрационных характеристик станков по различным компонентам, а также многочисленные публикации по вибрации металлорежущих станков.
На стадии разработки формирование качества нового ТО начинается с анализа динамики и процессов вибрации станков, обеспечивающего ускоренное продвижение их на рынки сбыта. Существующие основные показатели совершенства конструкций ТО: качество, надежность, производительность, безвредность, удобство работы и обслуживания - затрагивают вопросы вибрации. Значимость и важность проблемы снижения вибрации возрастает при создании станков нового поколения . Успешному решению этой проблемы препятствует недостаточность теоретических и практических разработок по формированию конструктивных параметров станков. Создание ТО с нормированными компонентами вибрации является главной задачей повышения их технического уровня.
Реализация идеи снижения и управления вибрацией станков повышает долю нового ТО, соответствующего мировому уровню на 35.. .45 %, а в отдельных случаях - до 100 %, по эффективности эквивалентной 15 % стоимости станков. Ввиду сложности кинематических и динамических процессов, происходящих в ТО, системный анализ и имитационное моделирование целесообразно проводить в сочетании различных элементов и параметров упругой системы станка. Первичная проработка конструкции станка начинается с анализа структурной схемы технологического процесса изготовления детали и изделия на основе типовых конфигураторов (рис. 2).
Модуль Модуль геометрической параметрической точности точности
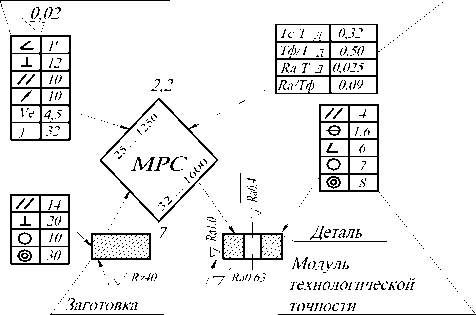
Рис. 2. Станочный конфигуратор для системного анализа технологического процесса
Базовыми показателями качества станка, включенных в станочный конфигуратор, являются численные значения геометрической, технологической, параметрической точ ности, а также компоненты вибрации: виброперемеше-ние, виброскорость и виброускорение, показатели назначения. Оценочные показатели металлорежущих станков различных классов точности представлены в параметрической матрице транзитивности (см. таблицу). Данные показатели учитываются при построении станочного конфигуратора [2; 5].
Необходимость и достаточность числа показателей для оценки качества станка, выбираемых по параметрической матрице транзитивности, принимается экспертным решением. При этом не исключается возможность принятия решения о внесении изменений в блочные показатели геометрической, технологической, параметрической точности.
При формировании модуля геометрической точности конфигуратора следует учитывать ужесточение сдаточных норм на заводе-изготовителе по действующим стандартам и техническим регламентам. Модуль технологической точности формируется на основе значений параметров действующих стандартов и технических условий на нормы точности для соответствующих групп станков.
Численный анализ размеров и допусков по рабочему чертежу детали по параметрам 2...4 позволяет выбрать необходимый класс точности станка, что способствует увеличению эффективности его использования. Начальное численное моделирование процессов в разрабатываемом или эксплуатируемом станке, подлежащем до-
Исходная параметрическая матрица транзитивности системного анализа технологического оборудования
Дескриптор оценочных показателей |
Класс точности металлорежущих станков |
||||
ISO 230-2 |
- |
Н |
Р |
SP |
UP |
ГОСТ 7599, ГОСТ 8 |
Н |
П |
В |
А |
С |
+ dt° С участка |
10 |
5 |
2 |
1 |
0,5 |
А = Т с / Т д |
0,36 |
0,32 |
0,25 |
0,2 |
0,16 |
R = R a / Т |
0,05 |
0,025 |
0,0125 |
0,0063 |
0,0032 |
Р Т. Т , 1,6 м |
-1 |
-2 |
-3 |
-4 |
-5 |
Квантиль т = 1,6 К |
0 |
-1 |
-2 |
-3 |
-4 |
Виброскорость В е , мм/с |
7,2 |
4,5 |
2,8 |
1,7 |
1.1 |
Точность ДОС: мкм угловые секунды |
10 3 |
5 3 |
2 1,5 |
1 1 |
0,5 0,3 |
Установка по уровню: мм/м угловые секунды |
0,1 20,7 |
0,04 8,3 |
0,02 4,14 |
0,02 4,14 |
0,01 2,07 |
Доля ТО: без точной механики в точной механике |
0,54 0,02 |
0,26 0,13 |
0,12 0,28 |
0,05 0,35 |
0,03 0,22 |
Модуль нагрузки |
1 |
0,8 |
0,63 |
0,5 |
0,4 |
Индекс жесткости |
1 |
1,25 |
1,56 |
1,95 |
2,15 |
Неравномерность вращения МГД % кн = 2( w max - w min )/( w max + w min ) механизм подачи |
0,14 0,03 |
0,1 0,02 |
0,07 0,015 |
0,06 0,012 |
0,05 0,01 |
Перепад скорости при ступенчатом регулировании, % |
4,1 |
2,6 |
1,2 |
1,2 |
1,2 |
Эксцентриситет центра инерции фундамента со станком и центра массы подошвы фундамента, в сторону уклона, % |
5 |
3 |
2 |
2 |
1 |
Класс надежности |
0 |
1 |
2 |
3 |
4 |
Вероятность безотказной работы |
0,85 |
0,9 |
0,99 |
0,999 |
0,9999 |
Радиальное биение, ряд РФ1, мкм |
16 |
10 |
6 |
4 |
2 |
Примечание. Применяемые обозначения: Т , - погрешность станка; Т ] - наименьший допуск на размер детали; R а - шероховатость; Т $ - допуск формы и расположения поверхностей; В е - эффективная виброскорость; ДОС - датчик обратной связи; w max , w min - вариация частоты вращения шпинделя, ходового винта.
работке и модернизации, выполняется с использованием регламентированных значений отдельных параметров станка.
Причиной вибрации являются множество факторов [1; 3; 5; 7]:
-
- конструкторские недоработки: выбор и назначение посадок, центрирование осей вращения роторов, жесткость, спектр частот вращения шпинделя;
-
- производственные факторы: отклонение размеров от чертежа, режимы термообработки, шероховатость, ошибки сборочных и регулировочных работ, базирование заготовок, качество режущего инструмента, приспособлений, масса заготовок и др.;
-
- эксплуатационные режимы: вязкость и чистота рабочих жидкостей, износ, техническое состояние ТО, внешние факторы.
Для нормирования вибрации в технических системах используют: виброперемещение, виброскорость, виброускорение с координатной привязкой к характерным точкам и поверхностям станка, а также добротность станка.
Компоненты вибрации являются интегральными показателями энергонасыщенности отдельных механизмов и станка в целом. Количественные характеристики значений геометрической точности станка непосредственно проявляются в измеряемых значениях компонентов вибрации. Вычисленные или измеренные значения этих компонентов при их сопоставлении с нормативными данными позволяют судить о качестве, жесткости, виброустойчивости и точности станка.
Изменение технического состояния станка проявляется в изменении значений измеряемой компоненты вибрации. Компоненты вибрации определяют на начальной стадии проектирования специальными динамическими расчетами, а достоверность результатов расчетов проверяют экспериментальными измерениями после изготовления первого образца станка в период приемосдаточных испытаний.
Полученные значения компонентов вибрации сравнивают с нормативными данными, включая санитарные нормы по ГОСТ 12.1.012-90. Руководствуясь информацией, полученной в процессе разработки станка, построенными математическими моделями компонентов вибрации, конструктор синтезирует характеристики, обеспечивающие достижение заданных показателей качества и виброактивности.
Характерные точки и области измерения вибрации анализируемых станков - это корпусные поверхности в зоне опор шпинделя, поверхности столов, место контакта станины с фундаментом или полом производственного помещения.
Виброперемещение представляет первую компоненту вибрации. Оно является составляющей перемещения, описывающей вибрацию, характеризующую движение точки или системы при поочередном возрастании и убывании во времени значений параметров [5; 7].
Функциональную зависимость виброперемещения можно записать в виде
5 5 o ■ sin( wt + ф), (1) где 5 o - текущее значение перемещения.
Второй компонентой вибрации является виброскорость, в общем случае представляющая первую произ водную виброперемещения по времени. В большинстве действующих стандартов, регламентирующих вибрацию двигателей и электрических машин металлорежущих станков и рабочих мест, виброскорость нормирована и представляет основную компоненту вибрационных процессов, отражающую особенности изменения энергии в упругой системе. Использование классической энергетической теории, соотношения потенциальной и кинетической энергии вибрационного процесса для свободных колебаний и принципа Релея позволили получить целевые функции вибрации, описывающие виброскорость У в общем случае:
yi = ds v /dt=j(w^). (2)
Главными аргументами целевой функции для каждого компонента являются многоуровневые частоты w . и характерное координатное перемещение х. ". За частотные уровни поперечных колебаний приняты пиковые wp , эффективные w, , минимальные w 1 значения, соответствующие идентифицированным процессам, протекающим в локальном объеме и экстремальных точках станка. Декадные всплески амплитудных значений виброскорости, в частности пиковых значений, характерны как для пусковых и переходных процессов, так и для квазистационарных режимов работы станков, в отличие от традиционных рекомендаций для экспертных оценок конструкций станков.
Из множества частот можно выделить частоты, формируемые и генерируемые непосредственно конструкцией шпинделя и станка.
Частота вибрации по ГОСТ 22061 определяется по функции
Щ р = п ■ d. ■ z / 60 ( d , - d. ), (3) где z - число тел качения в подшипнике; d , - диаметр беговой дорожки наружного кольца подшипника; d . - диаметр беговой дорожки внутреннего кольца подшипника.
Частота вибрации, рассчитываемая по функции (3), является наибольшей, так называемой пиковой интегральной частотой вибрации шпиндельной сборки и всей конструкции станка, которая функционально отражается на пиковом значении виброскорости.
Вторая, локальная средняя частота вибрации станка определяется по функции щм-п^П/30, (4)
где П - частота вращения шпинделя, мин 1.
Третья, локальная низшая частота станка ц рассчитывается по функции
Ю^П^Г/60, (5) где Г = d , / d . - коэффициент связи по условию демпфирования, здесь d - диаметр беговой дорожки наружного кольца подшипника, d . - диаметр беговой дорожки внутреннего кольца подшипника качения.
Рассмотренные частоты вибрации позволяют анализировать шпиндельные сборочные единицы (ШСЕ) и станок в характерном евклидовом пространстве, ограниченном контуром станка. Наиболее сложным при системном анализе целевой функции вибрации является количественная оценка и описание характерного координатного перемещения, даже при наличии проектного или ремонтного сборочного чертежа механизма главного движения станка. Проработку конструкции ШСЕ и станка начинают с составления общей матрицы согласия.
Функция перемещения представлена в виде
f ( P 6 ) |
если |
х е |
Д, |
|
f ( IT ) |
если |
х е |
д , |
|
f ( it ) |
если |
х е |
д • |
|
f ( x ) = ■ |
f ( e ) |
если |
х е |
д , (6) |
f ( У ) |
если |
х е |
д , |
|
не определена , |
если |
х е |
Д. |
Функция перемещения (6) состоит из основных пара метров станка, отвечающих допустимому решению и представляющих:
-
- радиальное биение шпинделя/( Р 6 );
-
- допуски, охватывающие элементы, форму и расположение отверстий характерной контактной пары/( IT);
-
- соответствующие допуски, охватывающие элементы, форму и расположение поверхностей характерных контактных пар вала/( it );
-
- конструктивный и технологический дисбаланс ШСЕ /( е ) по ГОСТ 22061;
-
- статический прогиб шпинделя на участках, обуславливающих формирование размера изделия/( у );
-
- внешние и внутренние факторы, не описанные соответствующими математическими моделями.
Функция радиального биения представлена в виде
Р 6, - 3 ■ [Б , !j °'5 + а (Б , !j °'5 + Б 2 / i °'5 ) / L ] / 2Ж, (7) где Р 61 - радиальное биение консоли шпинделя; Б , , Б 2 - радиальное биение подшипников передней, задней опоры;, / , i - число подшипников соответственно в передней и задней опорах; а - длина консоли левого или правого участка; L - расстояние между опорами шпинделя по Р 50-83-88; Ж - D / d - коэффициент связи по радиальному биению опор, здесь D , d -соответственно наружный и внутренний диаметры подшипника в передней или задней опорах шпинделя.
При использовании в компоновке подшипников разного диаметра коэффициент связи определяется по большему габариту и номеру подшипника, а при использовании подшипников разного класса точности по ГОСТ 520-89 выбирается подшипник с низким классом точности. Во всех случаях при анализе конструкций за правую или переднюю опору принята опора, расположенная у режущего инструмента.
Радиальное биение межопорного участка шпинделя Р 62 определяется по функции
R 62 -(3+ IT /2Ж, (8) где 3 - зазор или натяг посадки подшипника для ШСЕ; IT - допуск посадочного размера корпуса шпинделя.
При анализе виброактивности ШСЕ и станка значение радиального биения рассчитывается, как среднее арифметическое от функций (7) и (8).
Трудности выявления контактных пар преодолеваются, если начать анализ с двух парных точек посадочных диаметров внутреннего и наружного колец, принадлежащих подшипнику качения. Дисбаланс учитывается по эксцентриситету геометрической оси вращения шпинделя с осью, проходящей через центры тяжести вращающихся масс элементов конструкции ШСЕ.
Значение эксцентриситета определяется по зависи мости е - (е ■ w) / w, (9)
где ( е ■ w ) - скоростной параметр, выбираемый по ГОСТ 22061.
Для станка нормального класса точности класс точности балансировки принимается не более 4, а для станков повышенного класса точности - не более 3. Для станков прецизионного класса рекомендуемыми классами точности балансировки являются классы 1 и 2 по ГОСТ 22061. В практке системного анализа ШСЕ значение эксцентриситета берется как половина от значения, вычисленного по функции (9).
Значение прогиба консоли шпинделя вычисляется по функции у , - 103 В. ■а 3/3Е■I■Ц, (10)
где В . - т ■ g - приведенный параметр консоли шпинделя левой или правой части; а - длина соответствующей консоли шпинделя; Е - модуль упругости материала шпинделя; I - момент инерции сечения соответствующей консоли шпинделя; Ц - L / 2 d e - коэффициент связи по диаметру подшипника; здесь d - диаметр беговой дорожки наружного кольца подшипника.
Прогиб в пролете шпинделя определяется по формуле у 2 -10 3 В 2 -L 3 /48 E-I-Ц (11)
где В 2 - вес пролета шпинделя с вращающимися элементами; L - расстояние между опорами шпинделя по Р 50-83-88.
Кроме линейных размеров, вращающиеся массы существенно влияют и на формирование вибрационных процессов в ШСЕ и станке. В общем случае характерное координатное перемещение для новых, эксплуатируемых не более 18 месяцев станков следует определять как среднее арифметическое перемещений, вычисляемых по математическим моделям. А для станков, эксплуатируемых после среднего ремонта характерное координатное перемещение высчитывается, как сумма функциональных единичных параметров. Сложность определения координат функциональных точек заключается в раскрытии конструкции механизмов станков, не предусматривающих установки штатной диагностической аппаратуры. Определение пиковой, максимальной виброскорости в характерных точках станка выполняется по следующим функциям в экстремальной интегральной точке, принадлежащей механизму главного движения в области опор качения на поверхности корпуса ШСЕ:
' , (12)
где V p - виброскорость в энергонасыщенной интегральной точке механизма главного движения.
В локальной средней точке (ЛСТ), принадлежащей механизму базирования, направляющей линейке,
' ^ , (13)
где K mp - виброскорость в энергонасыщенной точке механизма базирования, направляющей линейки; k - w / w -коэффициент связи по координатному перемещению в ЛСТ.
В локальной низшей точке (ЛНТ), принадлежащей несущей системе станка, опорным поверхностям станка, зеркалу фундамента,
' ' , (14)
где V p - виброскорость в локальной низшей точке, принадлежащей как несущей системе, так и фундаменту; k с l = wllws- коэффициент связи по координатному перемещению в ЛНТ.
Виброскорость является базовым компонентом, характеризующим вибрацию и динамику станка. Третьим компонентом, оценивающей вибрацию станка, является виброускорение, представляющее производную виброскорости по времени. Из определения в общем случае следует a=d- svl dt2 =j(w^x.*)=dV I dt=-So ■ w2 ■ sin(w t+p). (15)
С учетом выполненных выкладок по виброскорости. исходные целевые функции вибрации по виброускорению имеют следующий вид
-
- виброускорение в экстремальной интегральной точке, принадлежащей механизму главного движения в области опор качения на поверхности корпуса ШСЕ,
% = w ■ У Ф ;
- виброускорение в локальной средней точке, принадлежащей поверхностям механизма базирования, направляющей линейки, механизма подачи,
Tv wT V mp ;
- виброускорение в локальной низшей точке, принадлежащей несущей системе станка, опорным поверхностям станка, зеркалу фундамента,
“ р = *Т У р . (18)
Наибольшее влияние на изменение виброускорения оказывает частота вращения шпинделя. По величине виброускорения можно судить о дополнительных динамических силах, действующих в конструкции ШСЕ и на опоры шпинделя, а также о соотношении статических и динамических нагрузок в подшипниках шпинделя. При значении виброускорения больше стандартного значения в опорах шпинделя возникают значительные динамические нагрузки, превышающие статические. В этом случае в конструкции ШСЕ и станка следует дополнительно проработать посадки, радиальные и аксиальные зазоры в подшипниках, установку динамических гасителей. Если значение виброускорения меньше стандартного значения, то в подшипниках ШСЕ динамическая нагрузка не превышает статическую нагрузку от веса сборки шпинделя с режущим инструментом и элементом привода.
В теории колебаний и вибрации показателем качества упругих механических систем является добротность. Добротность Qv раскрывает суть внутренних динамических процессов через относительные показатели изменения компонент вибрации, а также позволяет понять процессы стабилизации отдельных видов движений механизмов станка, подойти к сложному анализу динамики вращения шпинделя. Последнее относится к лаг-ранжевому движению нутации собственной оси шпинделя и пуансовому азимутальному движению оси шпинделя в зоне резания, проявляющихся в виде следа на замкнутой сфере с траекториями в форме синусоиды, острия и петли. Имитационное моделирование, анализ осциллограмм работы станка при начальных экспериментах позволили и получить зависимости для определения добротности на принципиально новой основе - по функции виброскорости в виде структуры функций:
Максимальные значения приняты в энергонасыщенной точке ШСЕ.
Вариация виброскорости в станке, как и другие компоненты вибрации, происходит вследствие ряда конструктивных причин, описываемых целевой функцией вибрации, а также реологическими свойствами упругой системы станка, содержащего, так называемые тела Гука и Ньютона, которые в конструкции станка с последовательным соединением выступают в форме тела Максвелла, с параллельным соединением - в форме тела Кельвина-Фойхгта, с комбинированным соединением - в форме тела Бюргерса-Френкеля.
Для качественной и количественной оценки конструкций новых станков имитационное моделирование динамики фрезерных станков проводилось в математическом пакете Mathcad 8 Pro с использованием специальных прикладных программ «Вибро» и «Аксель».
Произведя первичные преобразования общего уравнения вынужденных колебаний (20), записанного с коэффициентом сопротивления а [1; 2; 5]:
м • у + а • у + c • у = Q • sin ю • t , (20) получаем дифференциальное уравнение вынужденных колебаний (21) для моделирования виброактивности конструкций механизма главного движения и фрезерного станка:
У ,+ 2 • h • У , + p i • У ,- = H • sin ю • t , (21) где h = q I2m- коэффициент демпфирования станочной системы, с 1 ; q - коэффициент сопротивления, внутреннее трение в материале, Н ■ с I м; m . - приведенная масса системы, кг;р. = с I m - частота собственных колебаний системы, с -1 ; у. - характерное функциональное перемещение, мкм; Н- приведенная нагрузка, вызывающая вибрацию станочной системы, Н; ® - вынужденная частота процесса работы станка, с -1 ; t - функциональное время, с.
Численные значения угловых колебаний шпинделя на участке крепления режущего инструмента показаны на рис. 3.
X
-1 -10
- 5 - 1 0
5 - 10
4 - 10
3 - 10
2 - 10
1 - 10
-2 - 10
-3 - 10
-4 - 1 0
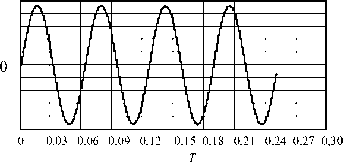
Рис. 3. Угловые колебания шпинделя, рад / м
Результат моделирования поперечных колебаний шпинделя по компоненте виброперемещения с физическим отображением параметра геометрической точности станка, в частности радиального биения шпинделя, представлен на рис. 4. Амплитуда поперечных колебаний, сопоставимая с радиальным биением шпинделя, позволяет оценить уровень точности и конкурентоспособности станка на стадии проектирования. Управляя формированием линейных размеров шпиндельной сборки механизма главного движения и роторов механизма подачи, можно создавать конструкции с новыми свойствами заданных движущих масс . Используя новую технологию проектирования на базе математического моделирования, можно значительно ускорить создание отечественных станков нового поколения.
X
1 . 10 5
8 . 10 6
6 . 10 6
4 . 10 6
2 . 10 6
1 . 10
iiiinimiijiiiiiiiiiiiiiiuiiiiniiiii пиши iiiiiiiiiiiiiihiiiinihiiuiiiNii hi пн ниш шип llllll|l|||||lilllVIIJilll|l||||||llllllllllllll ЮПШ 111111111111111II ШИ I Ill'll' 11 III' 11111111111
0 0.20.40.60.8 1 1.21.41.61
T
Рис. 4. Поперечные колебания станка
Переходны процесс разгона шпинделя (рис. 5) показывает динамику изменения амплитуды колебания и стабилизацию угловой скорости шпинделя.
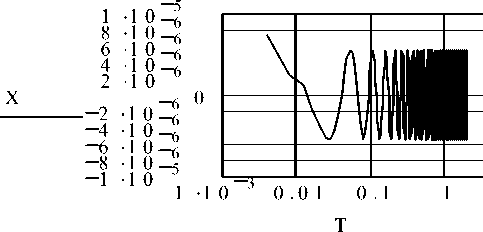
Рис. 5. Переходный процесс (разгон шпинделя)
Оценка принимаемых технических решений на стадии проектирования новых станков на основе использования технологии системного моделирования ускоряет запуск в производство конкурентоспособной станочной продукции. Первичные исследования подтверждают возможность управления компонентами вибрации при разработке нового технологического оборудования.
Современное состояние теории машин позволяет активно воздействовать на процесс проектирования и конструирования при создании конкурентоспособной продукции станкостроения.
Используя системный анализ и теорию малых колебаний, можно разрабатывать технические условия на основе синтеза основных параметров и характеристик как станка, так и детали, товарной продукции. Синтез обеспечивает оптимизацию линейно-массовых характеристик объекта разработки. Выходными параметрами, пригодными для системного анализа, являются компоненты вибрации: виброскорость, виброускорение и виброперемещение, которые анализируются по исходной конструкторской документации, состоящей из чертежей общего вида, проектных, рабочих, ремонтных сборочных чертежей.