Технология полульняных костюмных тканей в продольную полоску
Автор: Самутина Наталья Николаевна
Журнал: Вестник Витебского государственного технологического университета @vestnik-vstu
Рубрика: Технология и оборудование легкой промышленности и машиностроения
Статья в выпуске: 2 (19), 2010 года.
Бесплатный доступ
В статье рассматриваются вопросы оптимизации технологического процесса ткачества полульняных костюмных тканей. Для обеспечения нормального протекания процесса ткачества с оптимальной обрывностью основных нитей определены: заправочное натяжение 35 сН/нить и положение ламельного прибора на расстоянии 805 мм от опушки ткани, в отличие от данных РУПТП «Оршанский льнокомбинат» – 755 мм. В этом случае обрывность основных нитей составит 0,85 обрыва на метр (на предприятии обрывность 2,0 обрыва на метр), уработка основных нитей 8,34 %, уработка уточных нитей 7,4 %.
Костюмные ткани, полульняные костюмные ткани, оптимиация технологического процесса, ткачество, полульняные ткани, уработка нитей, основные нити, обрывность нитей, ткани в полоску, продольные полоски, уточные нити, заправочное натяжение
Короткий адрес: https://sciup.org/142184676
IDR: 142184676
Текст научной статьи Технология полульняных костюмных тканей в продольную полоску
На предприятиях текстильной промышленности первостепенное значение имеет повышение качества выпускаемой продукции и эффективности использования сырья и основных материалов, так как эти затраты в структуре себестоимости продукции составляют более 80%.
Целю данной работы является технология полульняных костюмных тканей, которая бы сопровождалась минимальной обрывностью основных нитей и позволяла получить ткань с небольшой уработкой основных и уточных нитей, что способствует снижению материалоёмкости ткани. Для достижения цели поставлена задача по нахождению оптимальных параметров изготовления данных тканей, что обусловлено применением в фоне тканей переплетений нового вида с эффектом продольной полосы различной ширины на базе уточноворсовых на станке СТБ-2-175 с жаккардовой машиной Z-344. В основе – хлопчатобумажная пряжа линейной плотности 25 текс х 2, в утке – чистольняная среднеоческовая пряжа линейной плотности 86 текс, плотность по основе 205 нит./10 см, по утку – 206 нит./10 см.
В производственных условиях РУПТП «Оршанский льнокомбинат» был проведён активный эксперимент по плану Бокса второго порядка [1, 3]. Входными параметрами приняты заправочное натяжение ( Х 1 ) и величина перемещения ламельного прибора по глубине заправки станка ( Х 2 ). При изготовления ткани заданного строения и для обеспечения нормального протекания технологического процесса ткачества нити основы должны иметь определённое заправочное натяжение при минимальной циклической деформации упругой системы заправки станка. Заправочное натяжение поддерживается постоянным в течение всего процесса ткачества, оно обеспечивает чёткое разделение нитей основы на две части при зевообразовании и создает определённое силовое воздействие нитей основы на уточную нить, необходимое для изгиба уточных нитей в ткани. Величина заправочного натяжения зависит от разрывной нагрузки нити (находится в пределах 3 – 7 %) и изменяется натяжением пружины фигурного рычага основного регулятора, с чем связан интервал варьирования параметра. Заправочное натяжение на нулевом уровне эксперимента выбрано 35 сН/нить, что составляет 5,69 % от разрывной нагрузки нити и соответствует 4 зарубке на рычаге основного регулятора. Невозможность использования центрального композиционного плана объясняется фиксированным положением фигурного рычага, что не позволяет произвести опыт в звездных точках (-1,414, +1,414), перемещение производилось на 1 зарубку. Данный параметр замерялся в зоне скало – основонаблюдатель в трёх точках по ширине заправки станка (в 15 см от правой и левой кромок и в середине станка) на группу из 48 нитей, что равно 4 раппортам по основе рисунка переплетения.
Известно, что от совместного воздействия изменяющихся по величине натяжения и трения основная пряжа в процессе зевообразования может разрушаться и наибольшее количество обрывов происходит на ткацком станке на участке разделительные прутки – опушка ткани. Правильная установка размеров зева может значительно снизить обрывность нитей при зевообразовании. Величина перемещения ламельного прибора по глубине станка связана с конструктивными особенностями ткацкого станка и изменяется перемещением мест крепления прибора к стойке. От геометрии зева, которая регулируется положением основонаблюдателя, зависит симметричность зева, а, следовательно, и условия формирования ткани. На нулевом уровне выбрано расстояние от грудницы до переднего валика прибора 805 мм, исходя из устройства станка СТБ.
В качестве критериев оптимизации приняты обрывность нитей основы ( Y 1 ), уработка основных нитей ( Y 2 ), уработка уточных нитей ( Y 3 ). Выбор критериев связан с тем, что от обрывности зависят производительность станка и качество вырабатываемой ткани. Нормализация процесса ткачества главной своей целью ставит снижение обрывности нитей. Уработка – характеризует изгиб нитей в ткани и является одним из основных факторов, влияющих на расход сырья. Она зависит от параметров заправки станка и деформации, которую испытывают нити в процессе тканеобразования. Поскольку выработать ткань на станке с прямолинейно расположенными нитями невозможно, уработка не может иметь нулевое значение, но так как она влияет на материалоёмкость ткани, её величина при заданных параметрах строения ткани должна быть минимальной. Как правило, уработка уточных нитей значительно ниже уработки основных, и в этих случаях нецелесообразно в качестве одного из критериев оптимизации принимать уработку уточных нитей. В спроектированных костюмных тканях уточные нити имеют достаточно большую уработку, близкую с основой. Поэтому в работе оптимизируется как уработка основы, так и утка. Уровни и варианты варьирования факторов представлены в таблице 1. Результаты корреляционного анализа – в таблице 2, где р – уровень значимости.
Таблица 1 – Уровни и варианты варьирования факторов
Факторы |
Уровни варьирования |
Интервалы варьирования |
||||
Х 1 – заправочное натяжение нитей основы, сН |
20 (-2) |
30 (-1) |
35 (0) |
40 (+1) |
50 (+2) |
5 |
Х 2 – положение основонаблюдателя по глубине (расстояние от опушки ткани до переднего валика прибора), мм |
694,3 (-1,414) |
765 (-1) |
805 (0) |
845 (+1) |
875,7 (+1,414) |
40 |
Таблица 2 – Результаты корреляционного анализа
Y 1 |
Y 2 |
Y 3 |
|
Х 1 |
0,5992 |
0,2331 |
0,2944 |
p = 0,030 |
p = 0,443 |
p = 0,329 |
|
Х 2 |
0,3478 |
0,7342 |
0,7032 |
p = 0,244 |
p = 0,004 |
p = 0,007 |
Исходя из корреляционного анализа, можно сделать вывод о том, что фактор Х 1 оказывает наиболее сильное влияние на выходной параметр Y 1 , Х 2 - на выходные параметры Y 2 и Y 3 . Уровень значимости для коэффициента корреляции не превышает 0,05. Это подтверждается значимостью парных коэффициентов корреляции.
Реализация опытов по плану ПФЭ подтверждает, что на процесс выработки полульняной костюмной ткани большое влияние оказывает заправочное натяжение основных нитей ( Х 1 ), чем величина перемещения ламельного прибора ( Х 2 ).
Небольшие изменения в заправочном натяжении основы вызывают резкое увеличение обрывности. При изменении величины перемещения ламельного прибора на всех уровнях варьирования заметного осложнения процесса ткачества не происходило. Этот вывод подтверждают полученные уравнения регрессии (формулы 1, 2, 3):
У, = 0,918 - 0,401 • X, + 0,003 • X2 + 0,004 • X2(1)
У2 = 8,472 - 0,206 • X1 - 0,702 • X2 + 0,002 • Х22 + 0,007 • Х22(2)
У = 7,649 -1,162 • Х2 + 0,0001 • X, • Х2 + 0,011 • Х2(3)
3 2 122
Математические модели являются адекватными, так как расчётные значения критерия Фишера не превышают табличных.
Компромиссное решение найдено графическим методом, путём наложения графиков обрывности нитей основы, уработки основных и уточных нитей. Областью оптимальных решений является область значений, выделенная на рисунке 1.
Таким образом, при заправочном натяжении, находящемся в пределах 31 – 41 сН/нить, и перемещении ламельного прибора по глубине зева на расстояние от опушки ткани до переднего валика ламельного прибора от 765,0 до 805 мм, обеспечивается нормальное протекание процесса ткачества, а также критерии оптимизации минимальны. Они близки к значениям, полученным на нулевом уровне эксперимента.
Величина перемещения ламельного прибора, мм
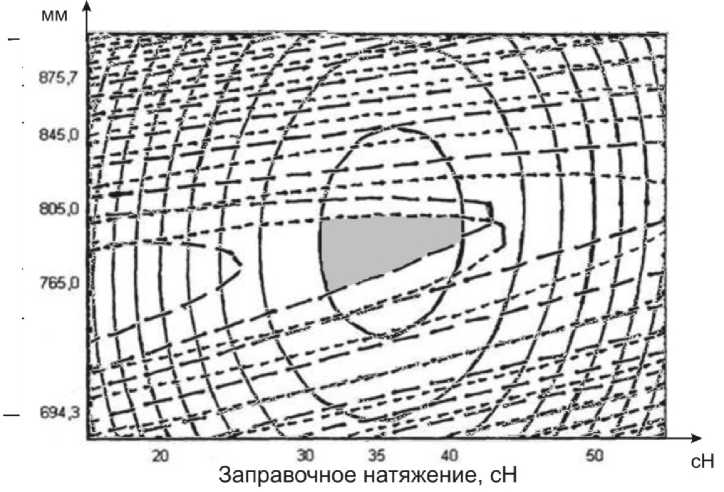
– для обрывности нитей основы
– для уработки основных нитей
– для уработки уточных нитей
Рисунок 1 – Двухмерное сечение поверхности отклика для области компромиссных решений
Данный вывод подтверждается следующим. Важнейшим технологическим показателем является деформация нитей основы при зевообразовании, которая зависит от свойств нитей, геометрических размеров зева, типа станка, скоростного режима. Данный показатель рассчитывают по упрощённой формуле (4), считая, что нить закреплена у опушки и в ламельном приборе и не учитывают релаксационные процессы [4]:
X =
Н2
• (
11 1
l 1 l 2
) [мм] ,
Н2 1 Н2 1
X1 = ”Ге ( T ) , X2 ^ v* ( Г ) [мм] (5, 6)
-
8 l1 8 l
где Н – полная высота зева, мм;
-
l 1 , l 2 – глубина и вынос зева, соответственно, мм;
λ 1, λ 2 – абсолютные деформации нитей основы при зевообразовании для передней и задней частей зева, соответственно.
В нашем случае перемещение ремизок вверх и вниз от среднего уровня одинаково, и полная высота зева равна 60 мм. Расчёт абсолютных деформаций согласно формул (5, 6) представлен в таблице 3.
Таблица 3 – Абсолютные деформации передней и задней частей зева
Наименование показателя |
До перемещения ламельного прибора |
После перемещения ламельного прибора |
λ |
4,86 |
4,63 |
λ 1 |
3,33 |
3,33 |
λ 2 |
1,53 |
1,30 |
Анализируя данные таблицы 3, можно сделать вывод о том, что перемещение ламельного прибора в сторону увеличения выноса зева способствует уменьшению суммарной абсолютной деформации и абсолютной деформации задней части зева.
Таким образом, для обеспечения нормального протекания процесса ткачества с оптимальной обрывностью основных нитей принимаем заправочное натяжение 35 сН/нить и положение ламельного прибора на расстоянии 805 мм от опушки ткани, в отличие от данных РУПТП «Оршанский льнокомбинат» – 755 мм. В этом случае обрывность основных нитей составит 0,85 обрыва на метр (на предприятии обрывность 2,0 обрыва на метр), уработка основных нитей – 8,34 %, уработка уточных нитей – 7,4 %. В результате снижения обрывности вследствие оптимизации технологических параметров изготовления ткани годовой ожидаемый экономический эффект от внедрения составит 5639486 рублей на один ткацкий станок.
Список литературы Технология полульняных костюмных тканей в продольную полоску
- Тихомиров, В. Б. Планирование и анализ эксперимента (при проведении исследований в лёгкой и текстильной промышленности)/В. Б. Тихомиров. -Москва: «Легкая индустрия», 1974. -264 с.
- Букаев, П. Т. Оптимизация процесса ткачества/П. Т. Букаев. -Москва: Легпромбытиздат, 1990. -120 с.
- Быкадыров, Р. В. Вероятностные методы расчета технологического процесса ткачества/Р. В. Быкадыров, С. Ю. Воронин. -Иваново: ИГТА, 2006. -150 с.
- Букаев, П. Т. Оптимизация процесса ткачества на бесчелночных станках/П. Т. Букаев. -Москва: Легпромбытиздат, 1990. -176 с.