Технология производства и методика металлографического исследования материала стали Х65 для деталей магистральных газонефтепроводов
Автор: Соколова Н.А., Борисова Л.Г.
Журнал: Научный форум. Сибирь @forumsibir
Рубрика: Природопользование
Статья в выпуске: 1 т.2, 2016 года.
Бесплатный доступ
Короткий адрес: https://sciup.org/140220245
IDR: 140220245
Текст статьи Технология производства и методика металлографического исследования материала стали Х65 для деталей магистральных газонефтепроводов
Единая газо-нефтетранспортная система России представляет собой сложный комплекс сооружений. Основным технологическим оборудованием, обеспечивающим, функционирование системы являются компрессорные станции с технологической трубопроводной обвязкой и магистральные газонефтепроводы. При магистральном транспорте природного газа и нефти возникает множество проблем, связанных с обеспечением надежности работы технологического оборудования.
Для долговечности магистральных трубопроводов необходимо обеспечить требуемый комплекс свойств. При разработке технологии производства листов, труб и соединительных деталей трубопроводов необходимо в первую очередь разработать концепцию легирования, которая в свою очередь будет конкурентоспособна, и обеспечивать комплекс свойств, в том числе экс-плуатационность.
Эксплуатация газонефтетранспортной системы сопровождается вариацией параметров перекачки и воздействием на оборудование различных нагрузок, в некоторых случаях с отклонением от расчетных значений. При наличии разнородной исходной информации, задачи повышения надежности оборудования становятся трудно формализуемыми. Обеспечение надежной работы транспортировки газа и нефти является приоритетной задачей.
Изготовление трубопроводов из стали Х60, начатое в период 1960-х годов, продолжается до настоящего времени. Нормализованный лист обычно производится из стали с 0,20 С %, 1,5% Mn, микролегирован-ной V, Ti и Nb или сочетанием микролегирующих элементов. Однако из-за высоких уровней содержания углерода, серы и азота эти нормализованные стали подвержены образованию холодных трещин [2]. Ме- ханические свойства и химический состав стали Х65 отвечают заданным требованиям для производства соединительных деталей трубопроводов.
Виды обработки стали класса прочности Х65 – это горячая штамповка и вальцовка труб. Во время проведения штамповки и вальцовки идут большие нагрузки, соответственно механические свойства снижаются. Наша задача состоит в том, чтобы подобрать такие режимы прокатки, после которой комплекс механических свойств после проведения горячей штамповки и вальцовки останется в требуемом диапазоне [3].
Х65 (10Г2ФБЮ) – сталь конструкционная низколегированная. В ходе решения поставленной задачи по разработке технологии производства листов с гарантией механических свойств стали категории прочности X65 были определены три варианта обеспечения требуемых свойств после термической обработки:
-
– выбор оптимальных режимов термической обработки на стандартном химическом составе;
-
– изменение концепции легирования стали;
-
– изменение типа образцов на растяжение.
Более важной и первоочередной считается задача улучшения качества толстолистового металла за счет правильного выбора температурного режима прокатки, термической и термомеханической обработки листа в технологическом потоке стана. Толстым называется лист толщиной от 4160 мм, шириной от 600 до 4900 мм и длиной от 2 до 12 м (иногда – до 18-20м) [3].
Рассмотрим термомеханическую (ТМО) и контролируемую прокатку толстого листа, которые ставят своей задачей разработку режимов одновременного воздействия на металл дозированной деформации и термообработки в процессе прокатки с целью получения требуемой структуры и свойств металла.
Существует несколько разновидностей ТМО низкоуглеродистых и низколегированных сталей. Наиболее распространена для толстого листа высокотемпературная термомеханическая обработка (ВТМО), при которой лист после горячей деформации закаливается и затем отпускается с получением ферритноперлитных или бейнитных структур.
Основная задача при охлаждении состоит в том, чтобы избежать коробления полосы из-за неравномерного ее охлаждения. Соответственно машина должна быть оборудована системами, обеспечивающими и контролирующими равномерность охлаждения полосы по всей площади. Обычно перед установкой лист должен пройти правку.[4]
Следует отметить, что титан растворяется в аустените при высоких температурах, поэтому применяется для сталей, нагреваемых до максимально возможных температур (1200–1250°С). Нитриды титана стабильны при высоких температурах и позволяют контролировать размер зерна аустенита. При последующем охлаждении в процессе прокатки карбиды титана выделяются при высоких температурах и упрочняют аустенит. Деформация упрочненного и мелкозернистого аустенита и последующий распад его обеспечивает получение упрочненных мелких зерен феррита.
Ванадий растворяется в аустените при более низких температурах (около 1150°С), следовательно, допускает более низкий нагрев под прокатку. Он практически не формирует выделений в аустените. Выделение карбонитридов ванадия происходит в основном в процессе и после фазового γ – α -превращения. Часть частиц выделяется непосредственно в феррит, способствуя его измельчению и упрочнению [5].
Как микролегирующий элемент для измельчения зерна наиболее эффективен ниобий, карбонитриды которого обеспечивают максимальное торможение рекристаллизации аустенита. При наличии ниобия в количестве 0,03% сталь вообще не рекристаллизуется при температурах ниже 950°С. При совместном легировании металла ванадием и ниобием расширяются возможности каждого из механизмов измельчения и упрочнения металла, расширяется диапазон температур, при которых выделяются упрочняющие частицы.
Таким образом, в зависимости от легирующих добавок для каждой марки стали выбирается как температура нагрева под прокатку, так и температурный и деформационный режим прокатки. Нагрев осуществляется в методической печи по второму уровню до среднемассовой температуры 1190-1200°С. Общее время нагрева – не менее 6,5 часов. Время нахождения каждого сляба в томильной зоне печи – не менее 40-60 мин. Темп посада соответствует темпу выдачи. На черновой стадии прокатки относительные обжатия не менее 10% [1].
На рис. 1 приведена обобщенная схема проведения высокотемпературной термомеханической обработки (ВТМО) и низкотемпературной термомеханической обработки (НТМО), при производстве толстого листа.
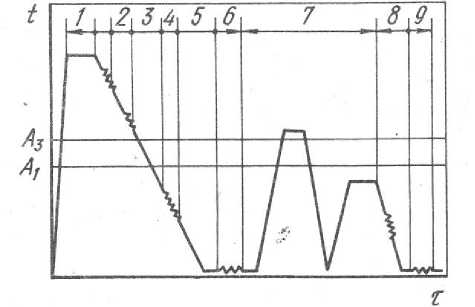
Рис. 1. Обобщенная схема термомеханических процессов при производстве толстого листа (1 – нагрев металла, 2 – горячая и низкотемпературная прокатка, 3 – охлаждение, 4 – горячая правка, 5 – охлаждение, 6 – холодная правка,7 – термообработка, 8 – охлаждение и горячая правка, 9 – холодная правка).
Как видно, в процесс формирования свойств металла вовлечены также операции горячей и холодной правки, на которых осуществляется также дозированная деформация металла за счет знакопеременного изгиба.
Таблица 1
Химический состав, %
С |
Mn |
Si |
P |
S |
Cr |
Ni |
Cu |
Al |
N |
Mo |
V |
Ti |
Nb |
Сэ |
0,10 |
1,62 |
0,26 |
0,01 |
0,001 |
0,01 |
0,03 |
0,06 |
0,04 |
0,005 |
0,003 |
0,068 |
0,016 |
0,047 |
0,4 |
0,10 |
1,65 |
0,38 |
0,01 |
0,001 |
0,03 |
0,03 |
0,08 |
0,03 |
0,007 |
0,004 |
0,078 |
0,017 |
0,040 |
0,4 |
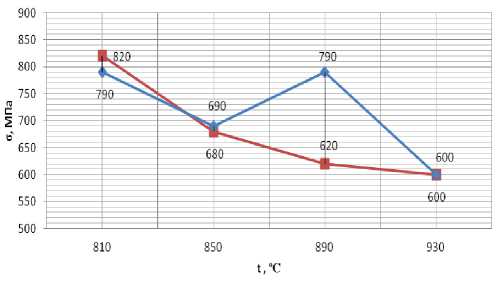
а)
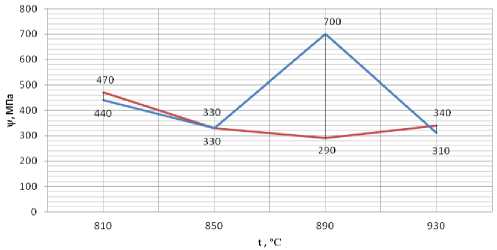
б)
Рис. 2. Влияние температуры и времени выдержки при нормализации на уровень прочностных свойств стали Х65: а) зависимость прочности от температуры выдержки; б) зависимость текучести от температуры выдержки.
В зависимости от толщины листа и марки стали состав и порядок операций меняется, а режимы конкретизируется [4].
Для определения оптимального режима термической обработки был выбран массив данных со стандартным химическим составом (табл. 1).
В соответствии поставленной задачи был поставлен эксперимент по определению влияния температуры и времени выдержки на уровень прочностных свойств стали Х65. Результаты представлены на рисунке 2.
Был произведен набор статистических данных по результатам испытаний образцов на растяжение в продольном и поперечном направлениях с наложением температуры нормализации 810, 830 и 850°С при температуре отпуска 590-610°С. Результаты в виде гистограмм представлены на рис. 3.
В ходе проведения работы было установлено, что с увеличением температуры и времени выдержки прочностные характеристики снижаются.
На основании результатов проведенного анализа были определены две температуры нормализации: 810°С и 850°С. Данные температуры выбраны по принципу 810°С – минимальное падение прочностных характеристик, 850°С – соответствует текущему режиму термической обработки проб по режиму производителя соединительных деталей.
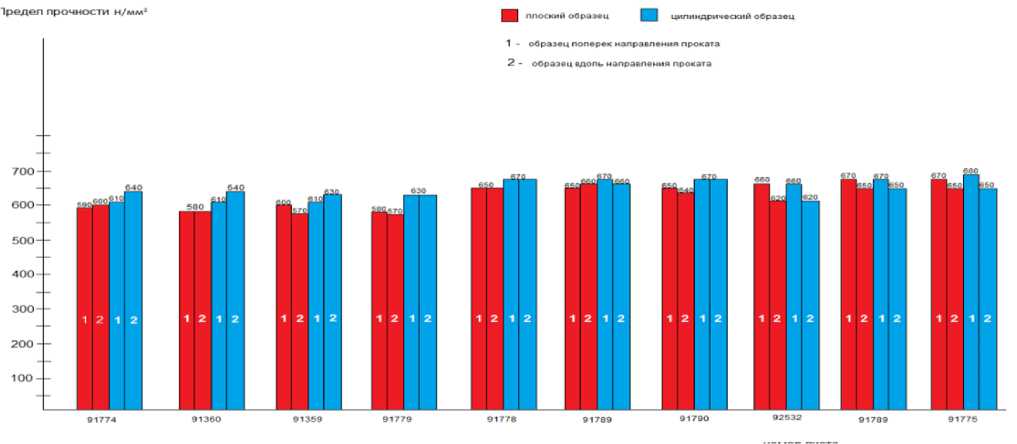
Рис. 3. Результат испытаний металла соединительных деталей.
Пробы подвергались нормализации на одну из температур и последующему отпуску на температуру 550-670°С с различным временем выдержки – 1 или 2 мин/мм. Уровень текучести в 100% случаев выше после нормализации 810°С, чем после 850°С.
Отсюда следует, что наибольшее влияние на предел текучести оказывает температура нормализации; при температуре нормализации 810°С получено минимальное снижение текучести; отпуск после нормализации снижает прочность и повышает текучесть стали.
Для проработки варианта было принято решение по изменению химического состава в части содержания никеля. В результате была запланирована выплавка двух плавок содержанием никеля с массовой долей 0,20-0,30%. Результаты производства дали положительный результат в части повышения предела текучести стали.
Легирование стали никелем позволило повысить выход годного на продукте до 100% при норме по текучести 392 МПа (категория Х65), однако распределение механических свойств имеет большой разброс, что может привести к единичным провалам.
Изменяя режимы нормализации, возможно, получать различную категорию прочности изделия – от Х52 до Х65 без применения закалочной ванны; изменение требований ТУ позволит повысить категорию прочности.
Результаты испытаний металла соединительных деталей показали удовлетворительный результат по пределу прочности и пределу текучести, что подтверждает правильность определенных режимов термической обработки, легирования никелем и применения цилиндрических образцов при механических испытаниях.
Список литературы Технология производства и методика металлографического исследования материала стали Х65 для деталей магистральных газонефтепроводов
- Гуляев А.П. Металловедение. Учебник для вузов. 7-е изд., пере-раб. и доп. -М.: Альянс. -2012. -644 с.
- Древаль А.Е. Краткий справочник металлиста/Е.А. Скороходов, А.В. Агеев -М.: Машиностроение. -2005. -960 с.
- Звягин В.Б., Цуканов В.В., Сивенков А.В. Оборудование и автоматизация процессов тепловой обработки материалов и изделий. Основное оборудование: Учеб. пособие. -СПб.: Изд-во НМСУ «Горный», 2012. -83 с.
- Зуев В.М. Термическая обработка металлов. -М.: Высшая школа. -1999. -288 с.
- Солнцев Ю.П., Пряхин Е.И. Материаловедение: учебник для ВУЗов. -СПб.: Химиздат, 2015. -783 с.