Термическая обработка отливок из белого износостойкого чугуна
Автор: Мирзаев Джалал Аминулович, Корягин Юрий Дмитриевич, Куликов Андрей Анатольевич, Созыкина Анна Сергеевна
Журнал: Вестник Южно-Уральского государственного университета. Серия: Металлургия @vestnik-susu-metallurgy
Статья в выпуске: 2 т.13, 2013 года.
Бесплатный доступ
Исследован высокохромистый чугун, применяемый для изготовления литых износостойких изделий. Установлены оптимальные температурно-временные параметры термической обработки отливок, обеспечивающие высокую износостойкость при сохранении достаточной вязкости.
Хромистый чугун, температура аустенитизации, твердость, закалка, изотермическая выдержка, ударная вязкость
Короткий адрес: https://sciup.org/147156819
IDR: 147156819
Текст научной статьи Термическая обработка отливок из белого износостойкого чугуна
На предприятии ООО «Технология-М» (г. Челябинск) начато внедрение в производство отливок из хромистого чугуна, предназначенных для футеровки помольного оборудования. Выплавка данного сплава была произведена в индукционной печи ИСТ-0,4. Плавка велась в штатном режиме на шпинельной футеровке, в качестве шихтовых материалов использовались: лом стали Ст3, феррохром ФХ-800, ферромолибден ФМо-60, ферромарганец ФМн-95 и ферросилиций ФС-65. Химический состав исследованного сплава приведен в табл. 1. Химический анализ был проведен с помощью атомно-эмиссионного спектрометра ДФС-500. Обращает на себя внимание высокая концентрация молибдена, который вводят с целью увеличения прокаливаемости и, возможно, вязкости [1].
Цель исследования заключалась в разработке экономичного режима термической обработки отливок, позволяющего получить для изделия высокую износостойкость при сохранении достаточной вязкости. Необходимо было также определить тип закалочной среды, в том числе и возможность воздушной закалки, после которой остаточные напряжения окажутся минимальными. Важным также является вопрос об отпуске закаленного чугуна, обеспечивающего достаточную пластичность.
Материал и методика исследования.
Стержни 0 20 мм были отлиты совместно с блоками футеровки мельниц из чугуна, химический состав которого показан в табл. 1. Одновременно с отливками футеровок, выполненным методом литья по газифицируемым моделям, были отлиты цилиндрические образцы диаметром 20 мм для исследования твердости, а также квадратные образцы сечением 20 x 20 мм и длиной 60 мм для оценки ударной вязкости. Измерения ударной вязкости (энергии разрушения) были проведены с помощью копра МК-30.
Цилиндрические отливки были разрезаны на образцы высотой 25 мм. Обе плоскости оснований были отшлифованы для сохранения параллельности. Измерения твердости были проведены на приборе ТР-5014 по методу Роквелла. Опыты по термической обработке проводили в нагревательных печах ПКЛ-1,2-12 и ПКЛ-1,2-36, снабженных термоконтроллерами.
Образцы укладывали на подставку – плиту из жаропрочной стали, а сверху покрывали графитовым тиглем для предотвращения обезуглероживания и окисления.
Полученные результаты позволили предложить несколько режимов термической обработки литья из данного сплава.
Результаты исследования и их обсуждение
Прежде всего отметим, что отливки используются для мельниц, с помощью которых происходит помол сырья, содержащего высокий процент SiO2, который имеет значительную истирающую способность.
Хорошо известно [1, 2], что твердость сплава в значительной мере определяет износостойкость деталей, во всяком случае, при работе без чрезмерно высокой ударной нагрузки. Поэтому было проведено исследование зависимости твердости от температуры закалки после аустенитизации исходных литых образцов в течение 15 и 60 мин. Отсчет длительности проводился через 15 мин после посадки образцов и закрывающего их сверху графитового тигля. Графики зависимости твердости от температуры и продолжительности нагрева показаны на рис. 1.
Кривые имеют максимумы твердости примерно при одной температуре – 950 °С. Рост твердости до максимума с повышением температуры аустенитизации обусловлен увеличением концентрации углерода в аустените, а после закалки – и в мартенсите.
Таблица 1
Химический состав изученного чугуна
Содержание элементов, мас. % |
||||||||
C |
Si |
Mn |
Cr |
Ni |
Cu |
Mo |
P |
S |
1,38 |
0,44 |
0,85 |
13,0 |
0,034 |
0,14 |
1,01 |
0,023 |
0,019 |
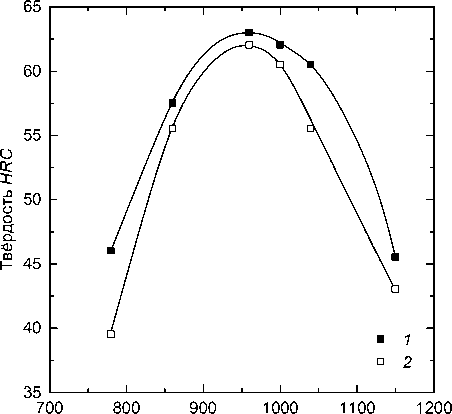
Температура аустенитизации, °C
Рис. 1. Влияние температуры закалки на твердость сплава: 1 – после аустенитизации 60 мин, 2 – после аустенитизации 15 мин
Последующее понижение твердости правее максимума связано с увеличением количества остаточного аустенита из-за чрезмерного обогащения его углеродом при повышенных температурах аустенитизации [2, 3]. Отметим, что штамповая сталь Х12М [3, 4] имеет состав почти такой же, как и исследуемый чугун, за исключением молибдена (0,5 % Мо в Х12М и почти 1 % в исследуемом сплаве). Однако для стали Х12М температура закалки на максимальную твердость составляет 1020 °С, тогда как в исследованном сплаве – 950 °С. Такое заметное различие в значительной степени вызвано повышенным содержанием мо- либдена, который, концентрируясь в основном в твердом растворе, снижает мартенситную точку, а поэтому появление остаточного аустенита в литых образцах будет происходить при более низких содержаниях в γ-фазе углерода и хрома.
Как следует из кинетических диаграмм распада аустенита сталей Х12 и Х12М [4, 5], минимальный инкубационный период распада переохлажденного аустенита соответствует температуре 680–700 °С. Поэтому для количественной оценки критической скорости охлаждения γ-фазы были проведены эксперименты, в которых образцы после нагрева до 900 °С и выдержки 1 ч, были последовательно перенесены на 680 °С и выдержаны различное время (до 64 мин). После выдержки каждого образца его охлаждали в воде. Зависимость твердости от длительности выдержки показана на рис. 2.
Снижение твердости обусловлено распадом аустенита на феррито-карбидную смесь. Грубо можно считать, что при выдержке до 30 мин распад аустенита был несущественен. Отсюда критическую скорость закалки можно оценить в 5 °С/мин. Оказалось, что при столь низкой критической скорости закалки твердость исходных литых образцов составляет всего 35,6 HRC несмотря на относительно малый диаметр образцов и высокое содержание молибдена. Это дает основание предполагать, что в литом состоянии сплав содержит большое количество аустенита, сохранившегося в отливках вследствие подавления реакции выделения карбидов из γ-фазы в ходе охлаждения. При нагреве под закалку этот аустенит может сохраниться почти в неизменном виде и структурно присоединиться к аустениту, возникающему выше 820 °С из кристаллов мартенсита и карбидов, образовавшихся в ходе охлаждения. В таком случае
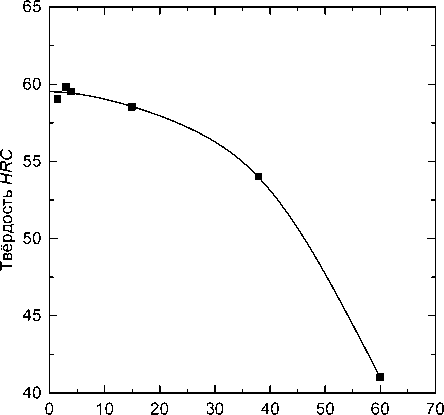
Длительность выдержки при 680 °C, мин
Рис. 2. Влияние длительности изотермической выдержки при 680 °С на твердость образцов после их переноса от 900 °С (выдержка 1 ч) на 680 °С и охлаждения в воде
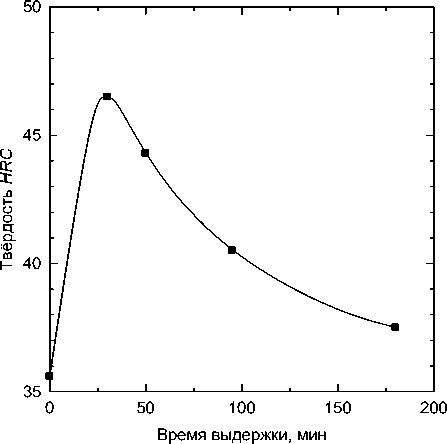
Рис. 3. Влияние длительности выдержки при 700 °С на твердость чугуна
при аустенитизации структурной перекристаллизации не будет, то есть зерно γ-фазы останется таким же, как и в литом состоянии, что может отрицательно повлиять на вязкость чугуна. Чтобы проверить это предположение, литые образцы были нагреты до 700 °С, выдержаны, а затем охлаждены в воде. Влияние длительности выдержки на твердость сплава показано на рис. 3.
Начальное увеличение твердости несомненно обусловлено вторичной закалкой. Дальнейшее снижение твердости обусловлено в том числе отпуском мартенсита при охлаждении литых заготовок. Следовательно, литые образцы действительно содержат большое количество остаточного аустенита.
Теперь становится понятным характер зависимости твердости от температуры закалки. Когда исходной литой структурой в основном является мартенсит, в ходе нагрева для аустенитизации происходит сначала отпуск мартенсита, а при достижении области γ+ К2 происходит α → γ-превра-щение и растворение карбидов в аустените до ус- тановления равновесия перед закалкой. В этом варианте максимум твердости по нашим расчетам действительно будет находиться в районе 1030 °С. В том же случае, когда из-за быстрого охлаждения расплава либо высокого содержания молибдена или марганца в литом состоянии сохраняется много остаточного аустенита, он при аустенитизации нагревается фактически без распада и только вблизи температуры закалки происходит не растворение, а наоборот, выделение карбидных частиц из аустенита. По мнению авторов, твердость сплава определяется двумя факторами: концентрацией углерода в аустените (мартенсите) и наличием дисперсных частиц карбидов. В этой ситуации максимум твердости будет смещен в область более низких температур (950 °С), где коагуляция карбидов происходит медленно.
Установление характера превращений в исследованном сплаве позволило предложить и опробовать несколько вариантов обработки, предоставленных на рис. 4.
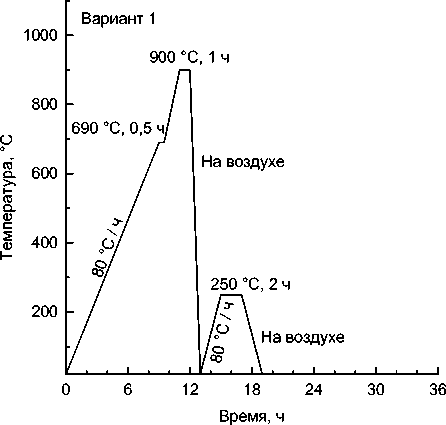
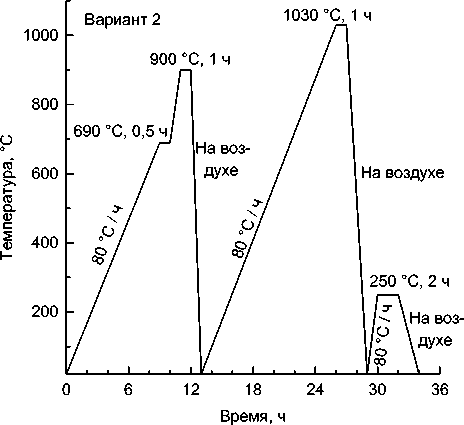
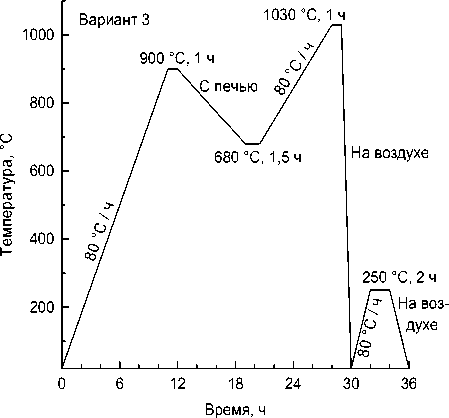
Рис. 4. Варианты термической обработки отливок из хромистого чугуна
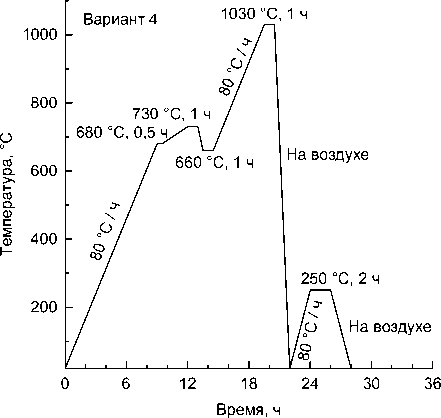
Сопоставление твердости и энергии разрушения образцов, термообработанных по вышеописанным режимам
Варианты термической обработки |
Твердость HRC |
Ударная вязкость, Дж/см2 |
Литое состояние |
39 |
3,6 |
Режим 1 |
53 |
0,9 |
Режим 2 |
57 |
5,1 |
Режим 3 |
56,6 |
4,9 |
Режим 4 |
56,5 |
5,3 |
В первом варианте предполагается закалка на максимальную твердость (см. рис. 1). Однако структурной перекристаллизации в этом режиме ожидать нельзя. Судя по данным [4], для стали Х12М низкотемпературный отпуск в интервале 150–400 °С приводит к непрерывному повышению ударной вязкости. Однако отпуск выше 250 °С создает чрезмерное (ниже 60 HRC) понижение твердости. Поэтому во всех предлагаемых вариантах окончательной операцией является отпуск при 250 °С.
Второй вариант отличается от первого тем, что после аустенитизации на 900 °С проводится закалка на воздухе, сопровождающаяся γ→α-превра-щением, и повторная аустенитизация, в ходе которой происходит перекристаллизация, и окончательная закалка на воздухе от 1030 °С.
В третьем варианте также проводится нагрев на 900 °С, но перекристаллизация проходит после охлаждения γ-фазы до 680 °С и выдержки 1,5 ч. При дальнейшем нагреве до 1030 °С происходит образование γ-фазы из α-фазы и карбидов, возникших при выдержке при 680 °С. Окончательная закалка проводится от 1030 °С на воздухе.
В четвертом варианте вместо изотермического отжига на 680 °С проводится колебательный отжиг: 680 °С → 730 °С → 660 °С, с последующей закалкой от 1030 °С и отпуском.
В табл. 2 представлены результаты измерения твердости и энергии разрушения образцов, обработанных по описанным выше режимам термической обработки.
К сожалению, как позднее выяснилось, фактическая температура в использованной для обработки по режиму 3 печи составляла не 680, а 645 °С, поэтому в ходе отжига твердость не изменилась, так как распад аустенита не происходил. Ударная вязкость оказалась почти такой же, как после режима 1. Повторное проведение термической обработки точно по режиму 3 привело к увеличению ударной вязкости до 4,9 Дж/см2. Вследствие прохождения перекристаллизации аустенита режимы 2, 3 и 4 дают приблизительно одинаковые ударную вязкость и твердость. Но по затратам времени, а значит, тепловой энергии, режимы 3 и 4 являются более экономичными, и именно их можно рекомендовать для термической обработки литых изделий.
Выводы
-
1. Литая структура из за высокого содержания молибдена в сплаве и быстрого охлаждения отливок и образцов оказалась преимущественно аустенитной. Ее нагрев в область стабильного аустенита (+ карбиды К 2 ) не сопровождается перекристаллизацией. Поэтому простая закалка от 900 °С или 1030 °С не является эффективной для повышения ударной вязкости операцией термообработки.
-
2. Проведение структурной перекристаллизации перед окончательной закалкой данного сплава позволяет значительно повысить его ударную вязкость.
-
3. Обеспечить перекристаллизацию аустенита можно двумя способами:
-
а) предварительной закалкой на мартенсит с последующей аустенитизацией;
-
б) распадом γ-фазы при выдержке в температурном интервале 680–720 °С, где расположен «нос» С-образной диаграммы превращения аустенита в карбидно-перлитную структуру.
Список литературы Термическая обработка отливок из белого износостойкого чугуна
- Цыпин, И.И. Белые износостойкие чугуны: Структура и свойства/И.И. Цыпин. -М.: Металлургия, 1983. -176 с.
- Металловедение, физика и механика применительно к процессу обработки графитированных материалов. Структура и износостойкость инструментов/А.Н. Емелюшин, Д.А. Мирзаев, Н.М. Мирзаева и др. -Магнитогорск: Изд-во МГТУ, 2002. -200 с.
- Геллер, Ю.А. Инструментальные стали/Ю.А. Геллер. -М.: Металлургия, 1968. -С. 287-292.
- Артингер, И. Инструментальные стали и их термическая обработка: справ./И. Артингер. -М.: Металлургия, 1982. -312 с.
- Tsypin I.I. Belye iznosostoykie chuguny: Struktura i svoystva [White Wear-Resistant Cast Irons: Structure and Properties]. Moscow, Metallurgiya, 1983. 176 p.
- Emelyushin A.N., Mirzaev D.A., Mirzaeva N.M., Petrochenko E.V., Koptseva N.V. Metallovedenie, fizika i mekhanika primenitel'no k protsessu obrabotki grafitirovannykh materialov. Struktura i iznosostoykost' instru-mentov [Metal Science, Physics and Mechanics Applied to the Process of Working of Graphitized Materials. Structure and Wear Resistance of Tools]. Magnitogorsk, MGTU Publ., 2002. 200 p.
- Geller Yu.A. Instrumental'nye stali [Tool Steels]. Moscow, Metallurgiya, 1968. 568 p.
- Artinger I. Szerszâmacélok és hokezelésü. Budapest, Müszaki Könyvkiado, 1978. 271 p. (Russ. ed.: Artin-ger I. Instrumental'nye stali i ikh termicheskaya obrabotka [Tool Steels and Their Heat Treatment]. Moscow, Metallurgiya, 1982. 312 p.)