Термометрический экспресс-контроль систем тракторов, самоходных машин в условиях эксплуатации и ремонта
Автор: Петрищев Н.А., Макаркин И.М.
Журнал: Агротехника и энергообеспечение @agrotech-orel
Рубрика: Технический сервис в агропромышленном комплексе
Статья в выпуске: 1 (1), 2014 года.
Бесплатный доступ
В статье рассмотрены примеры использования оборудования и средств, позволяющих проводить экспресс-контроль работы систем, узлов и агрегатов по тепловым характеристикам.
Термоиндикатор, термокарандаш, пирометр, тепловизор, термограмма
Короткий адрес: https://sciup.org/14769920
IDR: 14769920
Текст научной статьи Термометрический экспресс-контроль систем тракторов, самоходных машин в условиях эксплуатации и ремонта
Summary. The article discusses examples of the use of equipment and tools to conduct a rapid control work systems, components and assemblies for thermal performance.
Все процессы работы систем тракторов, самоходных машин сопровождаются выделением теплоты, учитываемой в энергетическом балансе. Несовершенство процессов передачи и преобразования энергии в кинематических, гидравлических системах машин характеризуется необратимой энтропией, преобразующей в теплоту часть передаваемой энергии. Известно, что при появлении отклонений значений, отличных от номинальных состояний, составляющие теплового баланса изменяются как для отдельных систем, так узлов и агрегатов, что позволяет уже на ранних стадиях оперативно выявлять неисправности по аномальным тепловым значениям температур поверхностей и не допускать наступления внезапных отказов. Повышение пороговых значений температуры в целом ряде случаев характеризует: снижение объёма рабочей жидкости, смазки в агрегатах двигателя, трансмиссии; загрязненность рабочих поверхностей теплообменников (радиаторов, каналов системы охлаждения); снижение КПД агрегатов гидропривода, топливной аппаратуры; усталостное повреждение элементов конструкций, снижающих в конечном итоге эксплуатационную надёжность, эффективную мощность, заложенные технико-экономические и экологические показатели.
Термометрический контроль может быть использован в процессе приемо-сдаточных испытаний новых, а также отремонтированных узлов и агрегатов, при предпродажной подготовке, инструментальном контроле технического состояния машин. Контроль и оценка максимальной температуры систем, и агрегатов позволяют сфокусировать внимание операторов машин и специалистов сервисных служб на ошибках и нарушениях при эксплуатации, проведении ЕТО, ТО, СТО, а для лизингодателя техники дает информацию о нарушении правил и рисков при эксплуатации техники; заводу-производителю о конструкционных недостатках изготавливаемой продукции. Это в итоге позволяет объективно находить и определять причинно-следственные связи появления неисправностей в работе машин.
Контроль температуры необходимо проводить для обеспечения соблюдения общих начальных условий процесса диагностирования систем и агрегатов, например, при замерах: дымности, компрессии, объемных расходов картерного газа в ДВС, рабочей жидкости в гидросистемах гидропривода и пр. При несоблюдении номинального температурного режима, измеренные значения могут отличаться от действительных в несколько раз, что неизбежно приводит к ошибочным выводам при определении технического состояния и принятии решения о проведении ремонта, сроках и объеме ремонтно-восстановительных работ. При превышении пороговых значений температуры агрегатов в процессе эксплуатации штатные системы контроля температуры лишь сигнализируют оператору о превышении номинальных значений, но не фиксируют сам факт превышения. Поэтому в дальнейшем факт перегрева узла можно констатировать только по изменению характеристик (геометрии, цвета, структуры) после разборки и дефектации.
В настоящее время для контроля температуры в технике могут применяться как контактные (датчики и показывающие устройства, штатно устанавливаемые в системы), так и бесконтактные (пирометры и тепловизоры, используемые диагностом) средства контроля температуры поверхностей и средства пассивного контроля – термопломбы, термоиндикаторы, термокраски (обратимые и необратимые), термокарандаши.
Наиболее бюджетным средством определения превышения температуры агрегатов в процессе эксплуатации являются термоиндикаторы. Данные средства позволяют фиксировать факт перегрева за счет использования эвтектических металлических сплавов с известной температурой плавления (сплавы: Роуза +100 °С, Вуда +68°С, Ньютона +94 °С, Лихтенберга +92 °С; припои: ПОИН52 +125°С, ПОСК 50-18 +142°С). Компания ООО «Мотортехнология» (г. Москва) использует термоиндикаторы (рисунок 1а) в качестве средства для обеспечения контроля правил эксплуатации отремонтированной ГБЦ потребителем в гарантийный период. Если в процессе эксплуатации происходил перегрев ДВС, ведущий к плавлению плавкой вставки термоиндикатора (рисунок 1б), то гарантийный ремонт ГБЦ не осуществляется.
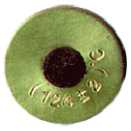
Общий вид
Рисунок 1а – термоиндикатора.
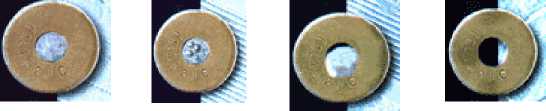
а) б) в) г)
а) +115ºС; б) +119°С; в) +124°С; г) +126 °С
Рисунок 1б – Динамика изменения внешнего вида термоиндикатора при изменении температуры.
Для бесконтактного термометрического контроля технического состояния узлов и агрегатов техники наибольшей информативностью обладают тепловизоры с пакетом прикладных программ, позволяющие оценивать температуры поверхностей и получать термограммы (распределение температур поверхности) для выявления температурных аномалий. Данные приборы нашли широкое применение при проведении энергетического аудита, при оценке утечек тепла в зданиях и сооружениях, энергосетях, ЖКХ, в ветеринарии, машиностроении.
Проведенные в ГОСНИТИ опыты по оперативному мониторингу систем при эксплуатации техники и в процессе послеремонтной обкатки с использованием тепловизора показали высокую эффективность поиска зон перегрева (таблица 1).
Таблица 1 – Опыты по использованию тепловизора Fluke Ti32
№ п/п
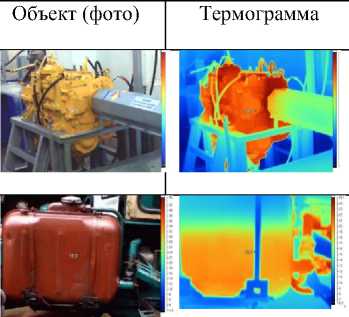
Примечание
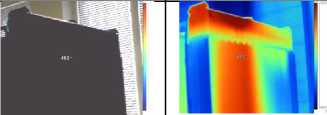
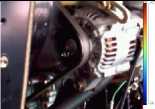
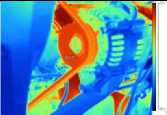
Утечки масла, повышенный нагрев подшипника первичного вала
Недостаточный объем заполнения гидробака рабочей жидкостью Исправность трубок радиатора системы охлаждения дизеля Сниженное натяжение приводного ремня генератора
Особенно ценным диагностическим признаком во многих случаях является не сама температура, а скорость ее изменения, особенно в первые минуты после начала работы агрегата. Эта величина определяет мощность потерь энергии, переходящих в тепло, а, следовательно, и КПД процесса или механизма. Поэтому желательно иметь средства контроля, позволяющие легко, быстро и многократно получать значения температур в контрольных точках или среднюю величину температуры поверхности агрегата. Также в ряде задач очень полезной информацией являются значения разности температур поверхностей в двух (или более) контрольных точках однотипных узлов одного агрегата (разность средних температур поверхностей корпусов подшипников одного вала, температур корпусов топливных форсунок одного двигателя, ступиц колес одной оси и других узлов a priori работающих в одинаковых условиях).
С учетом все возрастающей нагрузки на МТП, особенно в период весенне-осенних полевых работ, предлагается проведение следующих мероприятий:
-
- проведение системного тепловизионного входного контроля машины с применением тепловизоров для составления эталонных термограмм машин и агрегатов, с отслеживанием динамики изменения при обнаружении и устранения неисправностей;
-
- установка термоиндикаторов на все эксплуатируемые ДВС, в первую очередь на дизели, из-за сложности температурного контроля их работы в отсутствие нагрузки.
Рекомендовать ремонтным предприятиям проводить при проведении приемо-сдаточных испытаний машин, агрегатов тепловизионный контроль с применением пирометров, тепловизоров (с занесением значений в контрольных точках и (или) термограмм в протокол испытаний) и на основе эталонных оценок давать заключение о приемке работ; при проведении работ по ремонту ДВС устанавливать на ГБЦ термоиндикаторы.
Внедрение предложенных методов термометрического контроля при проведении диагностирования при эксплуатации и ремонте техники позволят:
-
- повысить достоверность диагностирования и оценки технического состояния узлов и агрегатов за счёт применения более совершенного метрологического оборудования;
-
- снизить затраты при диагностировании за счет проведения комплексного температурного контроля узлов и агрегатов в режиме реальной эксплуатации техники;
-
- выявлять ошибки при изготовлении, установке и ремонте агрегатов, что позволяет эксплуатационную повысить надежность сельскохозяйственной техники и инженерной инфраструктуры.
Список литературы Термометрический экспресс-контроль систем тракторов, самоходных машин в условиях эксплуатации и ремонта
- Петрищев Н.А., Макаркин И.М. Средства для контроля технического состояния узлов и агрегатов сельскохозяйственных машин по тепловым характеристикам//М.: Сельскохозяйственная техника: обслуживание и ремонт, №5, 2013. -с.38-43.