The experimental stand for an efficiency assessment of application of a multiple-pass heater as means of cooling of working liquid of a hydraulic actuator
Автор: Mohammad Almohammad A., Kulikova Nataly P., Sorokin Evgeny A.
Журнал: Журнал Сибирского федерального университета. Серия: Техника и технологии @technologies-sfu
Статья в выпуске: 7 т.6, 2013 года.
Бесплатный доступ
In this article the problem of increase in operability of a hydraulic actuator by use of a multiple-pass heater as means of cooling of working liquid is considered. For studying of thermal processes, check of mathematical model and an assessment of efficiency of application of a multiple-pass heater the developed experimental stand is given.
Hydraulic actuator, means of cooling of working liquid, multiple-pass heater, experimental stand
Короткий адрес: https://sciup.org/146114798
IDR: 146114798
Текст научной статьи The experimental stand for an efficiency assessment of application of a multiple-pass heater as means of cooling of working liquid of a hydraulic actuator
Modern hydroficated cars and the mechanisms applied practically in all industries, are operated in the most various conditions and quite often work in extreme conditions which are defined by production and natural factors.
The main factor defining efficiency of hydroficatedself-propelled cars is (air) ambient temperature on which temperature and viscosity of working liquid depend on. Other production and natural factors influence overall performance of a hydraulic actuator indirectly, through an operating mode of a hydraulic actuator and temperature of working liquid [1].
High temperatures have essential impact on productivity and durability of a hydraulic actuator as a whole. At increased temperatures there is an increase, both the volume of working liquid, and pressure in a hydraulic system. Viscosity decreases below admissible level, and volume losses sharply increase (internal movement and external leaks), increases direct contact of the interfaced surfaces of friction of details, local heating, there is an intensive wear and “gripping” of rubbing surfaces. It leads to partial or full loss of operability of the hydraulic equipment [13]. Therefore in hydraulic actuator system the increasing attention recently is paid to a problem of an exception of overheating of working liquid.
The vast experience of operation of hydraulic actuators shows that the specified problem can be solved successfully by reduction of losses of power and if necessary use of the corresponding heat exchangers.
The greatest distribution was gained by heat exchangers with air cooling (oil, heaters). They are carried out as automobile radiators or in the form of pipes, ribbed for increasing a surface of a heat transfer. For increase in efficiency of a heat transfer the surface of the heat exchanger is blown by air from the fan.
The multiple-pass heater [4] (Fig. 1) belongs to heaters of cooling systems, mainly hydraulic systems of transport, hoisting-and-transport and digging cars. The multiple-pass heater contains the heating element formed by a set of heat releasing tubes 1, connected among themselves tube plates 2, a collector 3 and 4, side shields 5, input 6 and output 7 branch pipes, the top reservoir with liquid 8 with a set of ports round each heat releasing tube 1, the pump 9, the bottom reservoir10. The moistened surface of heat releasing tubes provides stronger heat sink from a surface of tubes.
To increase overall performance of a hydraulic actuator by cooling system introduction – a multiple-pass heater, it is necessary to study the thermal processes happening in use of a hydraulic actuator. Complexity of these processes demands carrying out the pilot research, allowing to check results of mathematical models. The purpose of a pilot research is the assessment of efficiency of application of a multiple-pass heater for cooling of working liquid.
When performing experiment it is necessary to solve the following problems: to study the processes happening in a hydraulic actuator; to check and modify mathematical model of a multiple-pass heater; to estimate influence on working process of the device of cooling of working liquid.
The accompanying task puts detection of dependence of intensity of cooling from parameters of a multiple-pass heater and weight of working liquid, and also temperature of liquid sprayed a heater.
Pilot research has to be conducted in the conditions close to operational operating modes. The experimental stand which scheme is submitted in Fig. 2 was for this purpose developed. The stand represents a tank with working liquid, with a heating element established in it.
For determination of temperature of working liquid, in the period of a warming up, measuring probes of TP1, TP2, TP3 which are connected to the measuring ITM-4 block by means of cables are established.
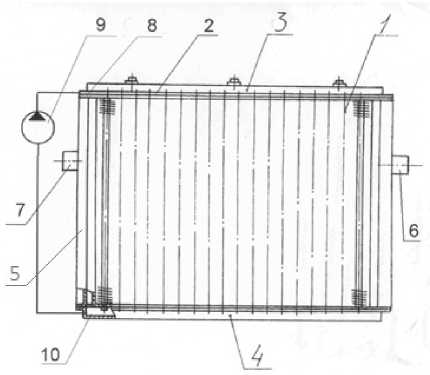
Fig. 1. Heater Device
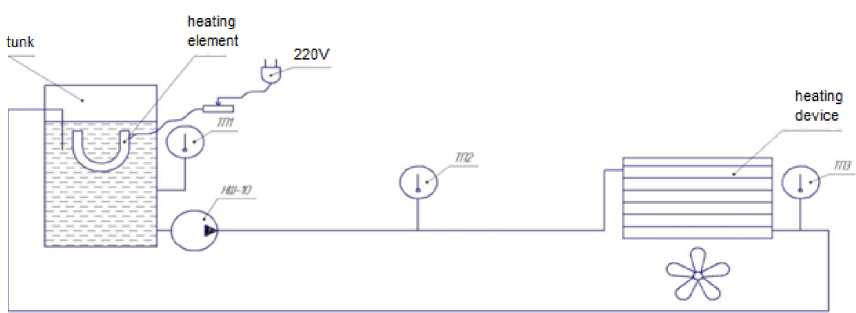
Fig. 2. Scheme of the experimental stand
Tight measuring probes of TP1, TP2, TP3 are executed from stainless steel. In probes thermal elements as which nickel thermal resistors are used settle down. The measuring ITM-4 block represents the four-channel measuring instrument of temperature. The range of measurement of temperature is from a minus of 40 (0/zero) °C to plus of 150 °C. Measurement error ± 0,5 °C.
When carrying out researches possibility of change of volume of working liquid in a hydraulic tank and a way of an irrigation of a heat-radiating surface of a heater is provided.
At research of the device of cooling of working liquid, the stand works as follows. Working liquid in a tank is warmed with the help of heating element, regulated by a rheostat, up to the demanded temperature. By means of the pump working liquid gets to a heater, with forced-air cooling through which heat is transferred to environment. For increase of efficiency of heat exchange processes on a heater surface we offer use of wetting of this surface by cooling liquid. Thus, after a heater we receive the cooled working liquid which arrives further on plums in a tank.
At production of a multiple-pass heater important that the heat carrier (working liquid) and a material of which the heater is made, possessed compatibility. When carrying out pilot studies the heat exchanger made of aluminum is used.
In the course of carrying out pilot studies the following parameters were supervised:
-
– temperature of working liquid in a hydraulic tank;
-
– air temperature;
-
– temperature on an entrance to a heater;
-
– temperature at the exit from a heater;
-
– period of operation of a heater.
-
– way of an irrigation of a heat-radiating surface of a heater.
Temperature of air was taken by means of the TL-2 thermometer. Temperature of working liquid was taken by means of submerged tight measuring probes executed of stainless steel. In probes thermal elements as which nickel thermoresistors are used are located.
Temperatures of working liquid taken value were fixed by the ITM-4 device.
Values of controlled parameters, when carrying out experiment, were entered in the register.
Researches were conducted at the volume of working liquid in a hydraulic tank of 25, 50 both 100 liters and various ways of an irrigation of a heat-radiating surface of a heater (dispersion, drop, jet).
On received, during experiment, to data dependences of temperature of working liquid on warming up time, for liquid volumes in a tank of 25, 50 and 100 liters are constructed at different ways of an irrigation of a heat-radiating surface of a heater (dispersion, drop, jet).
Thermal calculation of the stand
Capacity of a hydraulic tank gets out on the relation:
Vt = (1 - 1,5) Q Н , (1)
where: Q h – pump output.
We coordinate with all-Union State Standard 12448-80 and we choose hydraulictank capacity according to an exception of overheat of a hydraulic actuator.
We determine the area of heat transfer ofhydraulic tank by a formula:
F t = (6,0 - 6,9)3 Vt ,(2)
where: F t – area of heat transfer of a tank; V t – tank storage capacity.
Let’s determine the area of heat-radiating surfaces of a hydraulic actuator by a formula:
Fha = Ft ⋅αt,(3)
where: F t – the tank area; αb – coefficient
By a formula (4) we will determine quantity of heat allocated by a hydraulic actuator (at tl ):
Qha = (1 - Пи,)' NН ' kt' kp + QT,(4)
where: Q ha – quantity of heat allocated by a hydraulic actuator, kt – coefficient of time of operation under loading, kp – coefficient of efficiency of nominal pressure, QT – quantity of heat allocated with heating element, nt – output – input ratio in total.
Let’s determine established temperature in a hydraulic actuator:
t
es
Qha kha ' Fha
0max ,
where: tes – established temperature of working liquid, Khs – coefficient of heat transfer of surfaces of the hydraulic equipment, T omax – maximum temperature of air.
If the established temperature of working liquid exceeds admissible, in a hydraulic actuator it is necessary to apply the heat exchanger, which area is calculated according to the following equation:
F Т
_____Qh F ■ k ha , ( t es - t 0max ) ■ k T a° k T
where: F T – area of heat-radiating surfaces of a hydraulic actuator, m sq, k t – coefficient of a heat transfer of the heat exchanger.
Let’s determine the current temperature of working liquid in a hydraulic actuator by a formula:
tl =
Qha k Fha
1 -
V
i k ; Fh: a-vrx m ha ■ C ha exp
0max
where: t – time for which heat is allocated, with c, k – coefficient of a heat transfer of surfaces of t the hydraulic equipment in environment, Fha – average thermal capacity of materials of which the hydraulic actuator is made
_ Ci ■ mi + C he ■ m he
Cha mi + mhe where: Cl – heat conductivity of working liquid, ml – mass of working liquid, kg, mhe – mass of the hydraulic equipment, kg, Che– thermal capacityof the hydraulic equipment , J / kg °
Let’s determine the mass of liquid, believing that its volume in a hydraulic system exceeds liquid volume in a hydraulic tank by 1,5 times.
m l = P V t 1-5 , (9)
where: p – density at temperature of liquid, for used oil.
We count temperature of working liquid in time range with, with an interval 300 with (for convenience of calculation we will make the table and we will bring in it all parameters determined by calculation).
Temperature of over +700 Сis recognized as a zone of dangerous temperatures for hydraulic actuator operation as in this range intensive oxidation of working liquid, curing of rubber consolidations, increase of wear of details of the hydroequipment, reduction of volume efficiency of a hydraulic actuator, speed of movement of a working link of hydraulic engines and car productivities, external leakages of liquid which can lead to receiving strong burns of the operator begins. Therefore at achievement of temperature of working liquid, there will be an automatic turning on of the heat exchanger.
By results of calculation we build the schedule tl – τ. The schedule constructed by a settlement way allows to judge a thermal mode of a hydraulic actuator.
Thus, the stand allows to obtain data on influence of temperature of liquid sprayed a heater on intensity of cooling of working liquid, and as a result, to establish optimum design data of heatexchange devices.