УДК 539.38; 531.36 напряженно-деформированное состояние осесимметрических деталей и узлов в квазистатических условиях нагружения
Автор: Лепеш Г.В.
Журнал: Технико-технологические проблемы сервиса @ttps
Рубрика: Методические основы совершенствования проектирования и производства технических систем
Статья в выпуске: 3 (13), 2010 года.
Бесплатный доступ
Разработана математическая модель силового взаимодействия элементов газодинамических систем в процессе их функционирования. Решена задача расчета напряженно-деформированного состояния всех элементов, испытывающих упругие, малые упругопластические и конечные пластические деформации при продавливании осесимметрического изделия, состоящего: из корпуса, его наполнения и обтюрирующего деформируемого кольца, с трубой в процессе функционирования системы. Решение задачи разбито по иерархическим уровням, позволяющим на самых нижних уровнях применять метод конечных элементов. При решении задачи учитывается динамика процесса и техническое состояние трубы газодинамической системы.
Нагружение, радиальные деформации, контактные напряжения, силовое взаимодействие, труба, износ
Короткий адрес: https://sciup.org/148185869
IDR: 148185869
Текст научной статьи УДК 539.38; 531.36 напряженно-деформированное состояние осесимметрических деталей и узлов в квазистатических условиях нагружения
Квазистатические условия нагружения деталей многих машин и механизмов, например газодинамических импульсных устройств [1], характеризуются наличием значительных сил инерции, действующих в объемах деталей, величина которых пропорциональна [2] плотности рассматривае-
Л Л d'{u}/ мого элемента р и его ускорения / rTf2 .
В отношении деформационных ускорений речь идет об увеличении внутренних сил, характеризуемых напряжениями {^} , вели- чина которых возрастает пропорционально коэффициенту динамичности к > 1,0 , так что .
Рассмотрим общую схему нагружения элемента газодинамического импульсного устройства –корпуса радиальными ри осевыми р поверхностными силами, движущегося с ускорением под действием силы р (рис.1). Тогда внутри корпуса и его наполнения будут возникать силы инерции ^ИЕ, пропорциональные перечисленным физическим величинам, а присоединенные к данной системе элементы можно будет учесть поверхностными силами, пропорциональными массе и ускорению движения системы в целом, так что
^ИН,Еф тЕф " /^£2 ^ " Рд " 5 , (1)
где: ГОкр иm – массы присоединенного эле- мента (крышки) и всей системы соответственно; s – площадь наибольшего попереч-
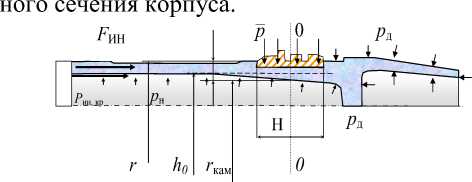
Рисунок 1 – Схема нагружения наполненного корпуса
Здесь: Ря – радиальное давление на полнения корпуса p c •О , МПа, где:
н1-Цcz ц c коэффициент Пуассона материала на- полнения (для абсолютно жесткого тела /Vc =0, а для жидкого цc=0.5);

масса наполнения, расположенного выше рассматриваемого поперечного сечения корпуса; ^мм радиус каморы корпуса (рис.1.).
Как правило, корпуса в процессе функционирования таких изделий нагружаются значительными внешними силами, приводящими к конечным пластическим деформациям при значительном формоизменении обтюрирующего кольца (ОК), под действием радиального давления Р и малым упругим или упруго-пластическим деформациям самого корпуса и его наполения.
Для корпуса цилиндрической формы, испытывающего упругие или упругопластические деформации известны зависимости для радиального прогиба W от действия радиальной силы p , полученные Ильюшиным А.А., которые в случае малых деформаций можем выразить суммой составляющих от действия каждой приложенной внешней силы:
W Wp Wp д ( WF ин Wp н) , (2)
где:
W 2 p A p и W p A p B (3)
в случае упругой и упругопластической деформации соответственно:
W 2 p д
p д e кор x
кор
r , a 0,
W p
н
2 k д
2 p н
cos cт x ;
кам
кам
r 2;
W 2 F ин p д
E
A dW 2 p
r2
22 кам
H
m в ; m
3 a
d p E 2 h 0
H 3 a a
A 00
E 2h 2h a0 k
E 1 k
k кор (1 2 ) E
4 E I ; кор 2
I r 2 4 r r кам r к 2 ам
36 ( r r )
кам
a 0 2 h 0 ;
фициент разупрочнения и модуль упругости материала корпуса соответственно ( 0,95 для корпусов, изготовленных из углеродистой стали с последующей термической обработкой «закалка + высокотемпературный отпуск»).
Зависимости (2 – 4) для корпусов имеющих значительные отличия по геометрии от гладкостенного цилиндра приводят к значительной погрешности результатов расчетов, однако необходимы для построения имитационной модели функционирования изделия более высокого уровня.
Более точное решение можем получить методом конечных элементов (МКЭ), которым возможно учесть геометрию изделия практически с любой наперед заданной точностью. Основной трудностью при этом является принятие той или иной физической модели деформируемых элементов (расчетной области).
Для получения решения МКЭ с использованием практически любых доступных программных средств (2 – 5) можем ограничиться упругопластической постановкой задачи. Тогда расчетная область (рис.2) будет представлена пространством, занимаемым корпусом и его наполнением.
1 k
1 h 0
2 a 0
г —г кам
r3
;
;
;
; (4)
h 0 радиусы наружной, срединной
поверхностей и толщина стенки корпуса изделия в зоне ОК соответственно; H ширина ОК; x координата положения ОК относительно донного среза корпуса; s предел текучести материала корпуса; k коэффициент, учитывающий непрямолиней-ность распространения пластической деформации в стенках корпуса ( k =0,9 среднее значение для тонкостенных корпусов, k *0,94 - для толстостенных); X, Е - коэф-
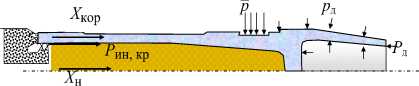
исунок 2 – Расчетная схема
Р
Здесь давление p в проточке корпуса, введено в расчетную схему как результат действия обтюрирующего кольца (ОК), испытывающего конечное формоизменение; , – объемные силы в материале кор пуса и его наполнения соответственно.
Схема дискретизации расчетной области для решения задачи МКЭ [3] представлена на рис.3. Сущность МКЭ заключена в исследовании системы линейных уравнений, записанной относительно узловых смещений сетки конечных элементов, в виде:
, (5)
где: мат рица жесткости системы, включающая осо-
бенности геометрии, граничные условия, и физические уравнения расчетного объема (постоянные в каждой подобласти, определенной материалом детали). В случае идеального упругого изотропного тела физиче- ские уравнения соответствуют закону Гука:
1x1 1x1 (1x3
{" . } = A ' B n
6x1 бхб 1^6x4
3x1 1x1 1хГ
U n }-{« T }-{£0} 4x1 6x1 6х1?
где A - матрица упругих констант в случае изотропного материала и осесимметриче- ского тела в цилиндрических координатах:
A h E (1-^
1 1 (1 + ц).(1-2-ц)
Ц /1-ц W / 1-ц
W |
ц/ |
0 |
Л-ц |
Л-Ц |
|
1 |
ц/ Л-Ц |
0 |
ц/ Л-Ц |
1 |
0 |
0 |
0 |
1-2-ц/ |
/2-(1"Ц) |
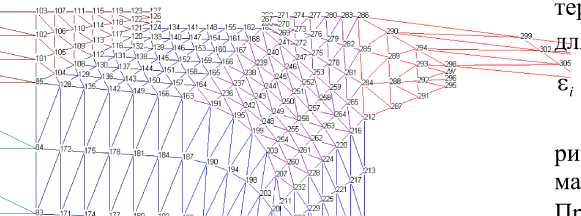
Рисунок 3 - Пример автоматического разбиения на конечные элементы ( фрагмент нумерации узлов в зоне возможных концентраций напряжений)
По физическому смыслу уравнение (5) представляет собой уравнение равновесия системы (в перемещениях). Для получения единственного решения система должна быть дополнена граничными условиями в перемещениях.
В большинстве задач динамического нагружения применение модели идеально упругого тела для расчета корпуса и некоторых других элементов системы невозможно, поскольку они могут испытывать пластические деформации. Это приведет к физической нелинейности уравнения (5).
Пусть условие перехода материала в пластическое состояние определяется на основании поверхности текучести Мизеса:
(стх -^v )2 +(Су -Ф )2 +(Сх"^ )2 +--+6Р2у+ ^ + ^ )-2" ^2-=0, где: <гт - предел текучести материала; сту, т. к - компоненты тензора напряжений [1]. Тогда в случае наличия малых упругопластических деформаций элементов системы, учет физической нелинейности произведем через зависимость между вектором напряжений {а} и вектором деформаций {е}. За пределом упругости в соответствии с деформационной теорией пластичности применима формула Ильюшина А.А., которую преобразуем к символьной форме:
р} = Ю + 23 • V {с} = Ро} + 2 • G ( и ) • {8} ’ (7)
где: G(и) - модуль сдвига несжимаемого за пределом упругости материала, значение которого зависит от самого деформированного состояния вследствие упрочнения ма- териала; si - интенсивность деформаций для осесимметрической задачи:
^ = А^2 + /3Р r- ее)2 + /3Р х + Р)2 .
В общем случае будем считать материал линейно упрочняющимся в области малых упруго-пластических деформаций. При этом истинная диаграмма oz = Ф(б,)
может быть аппроксимирована (рис.3) зависимостью о ,.=E.8;.(1-(0), (8)
где о - функция, учитывающая разупрочнение материала о = 0, при s i < Бт;
E-E' со =------ E

при s i < вт, где
E '
модуль разупрочнения, который, определяют на основании диаграммы ст, = Ф(б.) для идеального линейно упрочняющегося мате- риала по известным механическим характе- ристикам (см. таблицу 1) и формуле (рис.4)
тв
^ — / — ,
E (1 ) . Подставив это отношение в (7) получим
{ } { 0} 2 3 E { } 2 3 E { } ...
... { *} 2 G { } , (10)
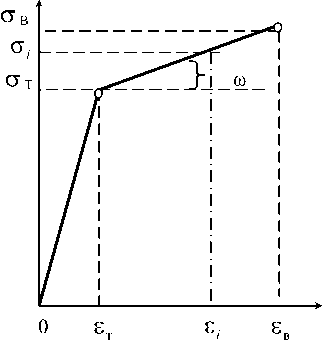
Рисунок 4 – Диаграмма линейно упрочняющегося материала где { *} вектор фиктивных упругих решений, которые возникли бы в идеальном упругом несжимаемом теле; G 1 3 E модуль сдвига, при условии несжимаемости ( =0,5).
В уравнение (6) вместо матрицы | A | c учетом физической нелинейности подставим | A |’ = | A | 2 G . При этом основное матричное уравнение (5) получим также в нелинейном виде
, (11)
где зависит от деформированного со стояния, являющегося однозначной функцией узловых перемещений .
Нелинейность приводит к тому, что решение системы (7) может быть получено лишь с помощью итерационных методов [2].
Для изделий, испытывающих динамические нагрузки, матричное уравнение МКЭ записывают в виде [4]: , (12)
где и общие матрица масс и век тор узловых ускорений для всей конструкции. При этом матрица формируется с помощью известных операций по значениям ее локальных коэффициентов m , связанных с отдельным КЭ, аналогично матрице
: m ( n )т ( n ) dV , а вектор
Vn определяется в большинстве случаев ускоренным поступательным движением изделия, так что |р„| •{«„ } = X |; |р|-{#} = X , где: плотность материала. Тогда компо ненты матрицы X определим пропорциональными ускорению изделия:
X ij p д s i ( n ) т ( jn ) dV . (13)
m
n
Таблица 1 – Механические характеристики материалов элементов
Индекс изделия, наполнения |
S л н 5 & |
S ■ гф С С ^ Й ( 8 i |
т , МПа. |
в , МПа. |
т |
в |
3ОФ59 (корпус) |
206 |
0,29 |
343 |
638 |
0,0017 |
0,032 |
3ОФ45 (корпус) |
206 |
0,29 |
540 |
1177 |
0,0026 |
0,121 |
3ОФ32 (корпус) |
206 |
0,29 |
334 |
834 |
0,0016 |
0,052 |
3ДС8 (корпус) |
206 |
0,29 |
314 |
834 |
0,0015 |
0,050 |
3ОФ25 (корпус) |
206 |
0,29 |
294 |
834 |
0,0014 |
0,049 |
3ОФ29 (корпус) |
206 |
0,29 |
559 |
981 |
0,0027 |
0,085 |
3Ц30 (корпус) |
206 |
0,29 |
1490 |
1962 |
0,0072 |
0,053 |
3БМ12 (сектор) |
206 |
0,29 |
1200 |
1800 |
0,0020 |
0,045 |
3БМ42 (сектор) |
6,98 |
0,27 |
589 |
700 |
0,0018 |
0,049 |
Наполнение (А-IX-2) |
0,98 |
0,26 |
14,7 |
118 |
0,0150 |
0,157 |
Применение МКЭ наиболее эффективно при наличии полностью автоматизированной программы [2], реализующей все этапы расчета конструкции (идеализация конструкции, формирование системы уравнений (12), решение этой системы, подсчет напряжений и других величин). Программа должна быть универсальной, пригодной для широкого круга практических задач. Весьма эффективны программы, имеющие блок автоматического разбиения области на элементы, сокращающие процесс составления и контроля обширной исходной информа- ции [3 - 6].
На рис. 5,6 приведены примеры графического изображения некоторых компонент НДС конструкции, представленной конечно-элементной схемой (рис. 2). Результаты получены при p =500 МПа и р д =300 МПа по программе [3], реализующей упругопластическую осесимметрическую задачу методом переменных жесткостей.
изделий, различающихся геометрией корпуса (цилиндрической формы - 3ОФ56; с перегородкой вблизи ВП и донной выемкой 3ОФ45, со стальным сердечником в качестве наполнения - 9СМ) и имеют различный характер. При этом наблюдается различное
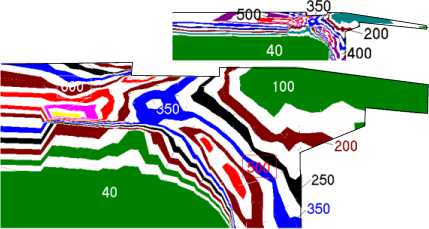
Рисунок 5 - Интенсивности напряжений, МПа (по Мизесу)
влияние сил инерции, вызываемых нагрузкой p . В одних случаях возрастание p приводит к увеличению прогиба корпуса, а в других, наоборот - к уменьшению.
В целом, вид графических зависимостей, полученных обоими способами подобен - они имеют практически линейный характер на упругом участке и криволинейный на упругопластическом (по Ильюшину - линейный), который также может быть приведен к приближенному линейному. При
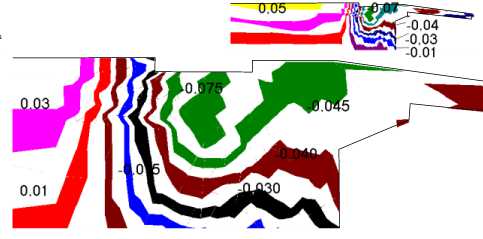
Рисунок 6 - Радиальные перемещения, мм
этом появляется возможность приведения зависимостей, полученных по МКЭ к зависимостям (2 - 4) путем введения некоторых фиктивных (“приведенных”) толщины корпуса в зоне ВП h 0 и радиуса срединной по
верхности а 0. Геометрические параметры "приведенной" оболочки с известным ра-
диусом наружной поверхности r можно оп-
ределить используя выражения для коэффи-
циентов A', A и B (3), определив их через
производные
A'=
а W2
и
p 0 cн
Полученные поля компонентов НДС полностью характеризуют это состояние. Их значения, в частности, можно использовать для получения зависимости радиального прогиба корпуса изделия в зоне приложения реакции p и наружного давления р д. Пусть с учетом всех внешних сил, включая инерционные, радиальный прогиб корпуса W2 выражается зависимостью
W2 = W2p + W2p д - ( W2F™ + W2p н ), (14)
где д - радиальное давление наполнения. Тогда в результате решения задачи в рассмотренных условиях нагружения с учетом различных значений внешних сил можем получить семейство, в общем виде нелинейных, зависимостей (рис.7), которые будут характеризовать подобно зависимостям (2 -4) радиальную жесткость корпуса для заранее известной геометрии изделия. Результаты аппроксимации (рис. 7) построены для
A
W
Р сн — 0
соответственно на упругом
и упругопластическом участках деформирования корпуса. Для приведенных значений толщины стенки оболочки и радиуса срединной поверхности на основании построенных по МКЭ зависимостей W2 ( р д, p ) по-
лучим формулы:
Г • V r h0 ;
1 + ^
где обозначено:
Х = 2
h a 0 = r у
(15) ,
H
-12/3
3L A-E *(1-0.9-Х)_
.
Здесь параметры A и B могут быть переменными, если присутствует криволинейный участок. В последнем случае для каждой i -той точки кривой получим
B =( A i -p i -w y
i
т
.
p , МПа 500
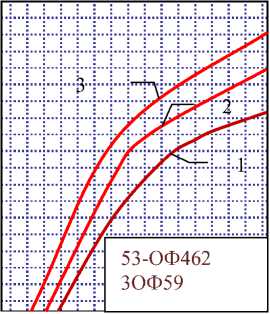
-0,1 0,0 0,1 0,2 0,3 W 2
p , МПа 500
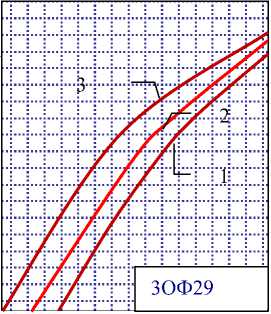

Рисунок 7 – Графики функции W ( p , p ), полученные МКЭ: 1 - рд =0 МПа; 2 - р д =150 МПа; 3 – p =300 МПа
-0,05 0,0 0,05 0,1 W2, мм p, МПа 500
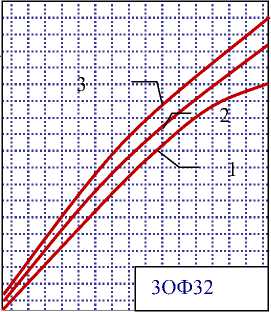

В табл. 2 приведены значения параметров h 0 и a 0 , рассчитанные по МКЭ и формулам (15) для корпусов, представленных в табл. 1. Из табл. 2. видно, что различие в расчетных значениях для традиционных схем изделия цилиндрических форм не велико (53-ОФ462, 53ОФ412, 3ОФ540,
3ОФ25, 3ОФ29, 3ОФ32), в то время как для нетрадиционных различается в несколько раз (3ОФ45, 3Ц30, 3Ц35).
Представленная система уравнений МКЭ имеет ряд условностей при применении ее для расчета НДС корпуса и других элементов изделия, испытывающих малые упругопластические деформации, обусловленные сложным нагружением в условиях функционирования. Характер нагружения элементов внешними силами (в частности корпуса) давлением и реакцией одного или двух ОК может приводить к существованию нескольких групп нагрузок, изме- няющихся независимым образом во времени и вызывающих сложное нагружение корпуса, а "эволюционный характер задачи", определяющийся развитием зон пластического нагружения, разгрузки и возможных вторичных выходов за пределы поверхности нагружения, приводит к необходимости учета "истории нагружения".
Таблица 2 – Приведенные параметры корпусов изделий (в мм)
Индекс изделия |
по Ильюшину А.А. |
по МКЭ |
||
53-ОФ462 (3ОФ59) |
20,71 |
50,37 |
21,5 |
50,2 |
53-ОФ540 (3ОФ25) |
29,27 |
61,22 |
29,1 |
61,6 |
3ДС8 |
75,85 |
37,93 |
83,9 |
34,3 |
3Ц30, 3Ц34 |
13,64 |
69,03 |
61,4 |
45,5 |
3ОФ29 |
21,70 |
38,65 |
27,8 |
36,1 |
3ДЦ10 |
75,85 |
37,93 |
83,9 |
34,3 |
53-ОФ462 (3ОФ59) |
28,07 |
61,47 |
17,1 |
67,7 |
3ОФ45 |
24,12 |
63,19 |
49,9 |
52,7 |
3Ц35 |
29,55 |
86,53 |
71,0 |
66,1 |
3ОФ43 |
37,57 |
81,72 |
63,2 |
76,8 |
3ОФ32 |
21,70 |
38,65 |
27,8 |
36,1 |
53-ОФ412 |
22,00 |
37,50 |
24,5 |
37,8 |
Решение упругопластической задачи с учетом истории нагружения и при наличии конечных пластических деформаций может быть получено с помощью метода последовательных приближений в совокупности с шаговой процедурой нагружения. Это значительно усложняет вычислительную процедуру МКЭ и приводит к дальнейшей дискретизации основного вариационного уравнения по i- тым шагам нагружения во времени ti . Для этого вектор внешних нагрузок, переменный во времени { P } i разбивается на ряд отдельных участков { P } i , что позволяет записать уравнение (11) для i -го шага нагружения в следующем виде
K ( u ) i 1 {A u } i { P } i 1 + { P } i , (17)
где { P} i приращение вектора внешней нагрузки на участке ti 1 ti ; K(u)i1 мат рица жесткости, построенная с учетом деформированного состояния, определяемого вектором {u}i 1 на i-1-м этапе. При этом {u}i {u}i 1 +{Au } i . С помощью этих зави симостей последовательно переходим от первого шага нагружения (i=1) ко второму
( i =2) и т.д., пока не будет получено значение вектора { u } при заданном уровне нагружения { P } . Процедура, аналогичная методу пошагового нагружения. Усложняющим отличием является наличие переменной матрицы K ( u ) .
Учитывая наличие невязки метода шагового нагружения будем производить итерационное уточнение на каждом шаге, например, методом последовательных приближений [2]. Основное матричное уравнение при этом для j -той итерации и i -го шага нагружения принимает следующий вид:
K ( uj 1 ) i 1 {A u } i , j { P } i . (18)
Используем данный подход для решения задачи о напряженно- деформированном состоянии обтюрирующего кольца, которое вдавливается в канал трубы и испытывает конечные деформации в ее входном конусе (рис.8).
Задачу будем решать относительно нормальных ОК и касательных TК контактных напряжений на поверхности контакта ОК и трубы, которые могут быть вычислены через характеристики НДС ОК, претерпевающего пластическое формоизменения через компоненты вектора напряжений {о} у поверхности ВП по формуле cosy + ax sin• у , (19)
где Y – угол входного конуса относительно образующей трубы, в цилиндрической системе координат rOx (рис. 8).
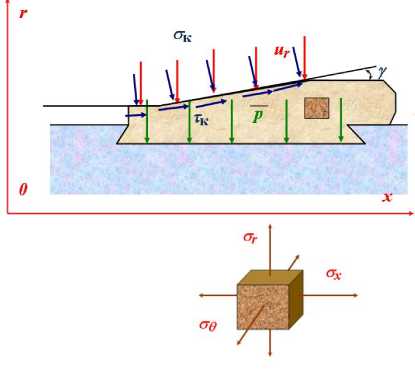
Рисунок 8 Схема деформирования ОК при вдавливании в канал трубы
В качестве граничных условий, ока- зывающих внешнее кинематическое воздействие на ОК, при решении задачи примем радиальные перемещения его поверхности ur в контактной зоне. Будем считать, что перемещение ur, определено из решения задачи более высокого иерархического уровня, учитывающей деформирование трубы Wx и корпуса W2, на котором закреплено ОК и с учетом профилей трубы R (/0 +1) и ОК r (x) вычисляется по формуле:
ur(x ) = R ( 1 0 + 1-x )- r 0 ( x )- W -W 2 , (20)
где: 1 , 10 - путь изделия в трубе и начальное положение системы координат r0x относительно системы ROL, связанной с трубой; r 0 ( x ) -координаты исходного профиля ОК.
Для использования вариационного уравнения (18) разобьем процесс вдавливания на ряд этапов, как этого требует теория пластического течения, и для каждого i -го этапа можем рассчитать:
A u ( x ) i = R ( 10 +1 - x ) - r ( x ) i , (21)
где r 0 ( x ) i- текущие значения координат профиля ОК, деформируемого в процессе врезания
Г о ( x ) i = Г о ( x )н - A U r ( x )w + W“ (22) .
Пусть на первом этапе значения радиальных прогибов W2 = W =0. Тогда определение граничных условий Uur ( x )1 ограничивается к решению только геометрической задачи.
Для приведения задачи к квазистати-ческим условиям нагружения, необходимым для ее решения методами механики деформируемого твердого тела, на поверхности взаимодействия ОК и корпуса изделия (по поверхности канавки под ОК) S кн введем дополнительные кинематические граничные условия - закрепления: u r = u x = 0, а также силовые граничные условия, соответствующие условиям трения при относительном скольжении поверхности ОК и трубы, которые пока неизвестны. Они могут быть приближенно определены по условия Зибеля по компонентам НДС, определенным из предыдущего этапа вдавливания ОК, тогда 1 i -1
тк = а • а. , где с. - интенсивность на- пряжений вблизи поверхности контакта, определяемая с учетом накопленной деформации в соответствии с функциональной зависимостью Gj = Ф(е; ) на основании эксперимента для i- 1-го этапа врезания; ос - опытный коэффициент пропорциональности, предельное значение которого в зоне пластических деформаций не превышает значений ос = 1/ \/3 , а при наличии смазки (краски и др.) уменьшается в два - три раза.
К силовым граничным условиям от- несем также давление на донную часть корпуса (до ОК) pд, действующее в виде распределенной нагрузки на части свободной поверхности ОК и корпуса. Теперь задача может быть решена МКЭ - методом поша- гового нагружения с итерационным уточнением методом последовательных приближений в полном соответствии с вариационным уравнением (18)
I K ( uHf\b u} - j ={ P}. (23)
Результаты решения задач в виде полей компонент векторов { } и { u } приведены на рисунках 9 - 10.
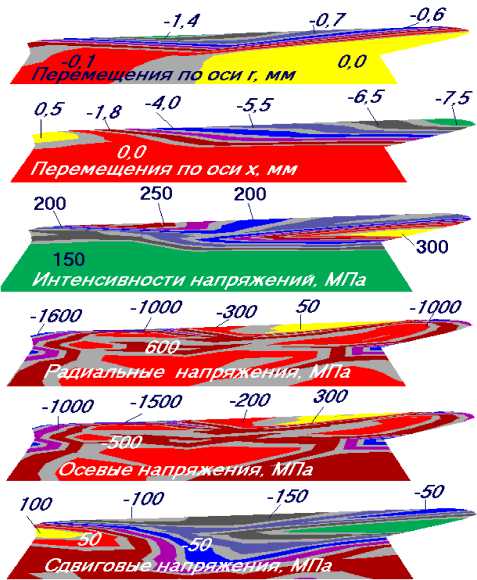
Рисунок 9 - Напряженно-деформированое состояние ОК при вдавливании в канал трубы
Более полное решение может быть получено с учетом наличия деформирования корпуса W . Тогда в расчетную схему необходимо включить непосредственно сам корпус и его наполнение, а в качестве алгоритма использовать заложенный ранее для решения уравнения (23). Результат решения такой задачи приведен на рис.11.
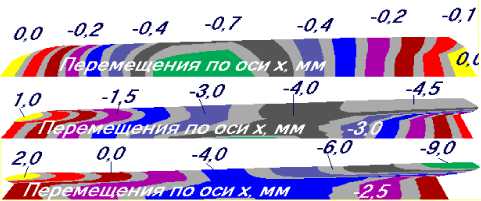
Рисунок 10 – Деформирование ОК сложного профиля при вдавливании в канал трубы
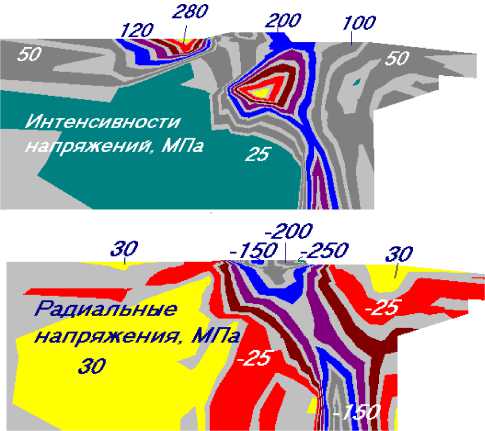
Рисунок 11 – Напряженно-деформированное состояние в зоне ОК.
Значимость этих параметров для СУ г может превышать точность учета граничных условий в области определения прогибов трубы W 1 и корпуса изделия W 2 . Значения напряжений СУ изменяются по поверхности ОК от сотен МПа до отрицательных, соответствующих "отслоению" ОК от поверхности контакта, что затрудняет расчет радиальной реакции ОК p осреднением СУ r по поверхности контакта
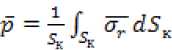
(24) с учетом формулы (19).
На рис.12 приведены распределения радиальных напряжений о в контакте ОК и трубы при вдавливании ОКП различных форм и размеров (диаметр трубы 152 мм), рассчитанные МКЭ в соответствии с изложенным алгоритмом. Из полученных графиков видно, что по мере вдавливания ОК значительно изменяется величина напряжений о и характер их распределения по контактной поверхности ОК. При этом значительную роль играет форма и размеры ОК, условия трения на поверхности контакта, угол входного конуса трубы у.
Вдавливание ОК в условиях функционирования изделия может сопровождаться рядом других процессов, оказывающих влияние на НДС ОК, которые можно учитывать через граничные условия и механические свойства его материала. В частности влияют: динамика процесса вдавливания, высокоскоростной характер трения, износ контактных поверхностей, нагревание ОК вследствие диссипации энергии трения и пластического деформирования и др.
Эти условия могут быть учтены путем поднятия иерархического класса математической модели за счет включения в нее перечисленных процессов, что усложняет саму задачу и ее параметрическую идентификацию.
Указанные недостатки присущи всем известным решениям НДС элементов изделий численными методами. Тем не менее, такое решение может быть использовано для расчетной оценки возможности применения различных материалов с учетом конструкций ОК по критериям, связанным с пластическими свойствами материалов, претерпевающих конечные пластические деформации, например по наибольшими допустимым деформациям [ г ], приводящим к разрушению ОК при вдавливании, т.е. по условию 8 [8], где 8 наибольшее значение компоненты вектора { г }. Решая последовательно ряд задач с изменением кинематических граничных условий u (0.
u ), возможно установление параметрической зависимости вида p = f ( ur ).
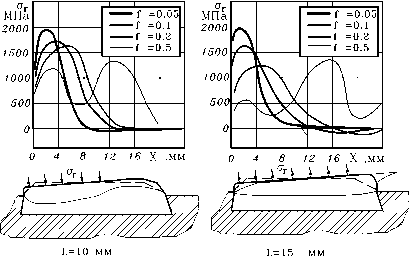
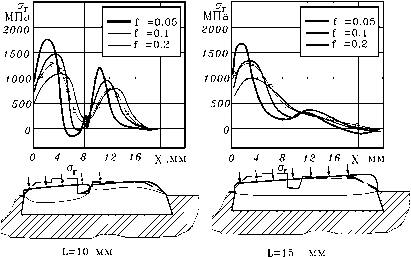
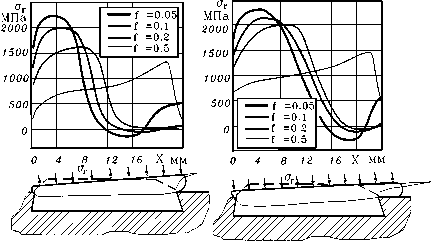
L=20 мм

Рисунок 12 - Распределение радиальных напряжений по поверхности ОК различных профилей
Такая зависимость позволит аппроксимировать задачу расчета НДС при вдавливании ОК для следующих иерархических уровней путем построения "кривых вдавливания", которые совместно с зависимостями (2 - 4, 14) позволит решить задачу вдавливания ОК на более высоком иерархическом уровне.
Алгоритм расчета радиальных и осевых взаимодействий изделия и трубы будем строить на основании функциональных связей между радиальными прогибами трубы Wx и корпуса изделия W2 с радиальной реакцией ОК p, полученными на основании численных решений задач МКЭ в виде табличных (графических) зависимостей для прогибов W2 (p, рд) (рис.7), считая, что давление pд известно. Причем учитывая общую постановку задачи о НДС численным методом (МКЭ) можем получить зависимость W2 (p, рд, x), где x - координата поверхности ОК. Предположим, что эта зависимость может быть выражена полиномом второго порядка по степеням x , тогда имеем:
W 2 ( p , p д , x ) = W 2 x =0 ( p , p д) + -
2 , (25)
... + c1( p, p д )' x + c 2( p, p д )" x где W2x=o(p, pд) “ зависимость W,(p, pд) построенная для точки поверхности ОК с координатой x =0 мм (расположенной у верхней кромки ОК) (рис. 13); c1(p, pд), c2(p, pд) - коэффициенты полинома, зави- сящие в общем случае от условий нагруже-
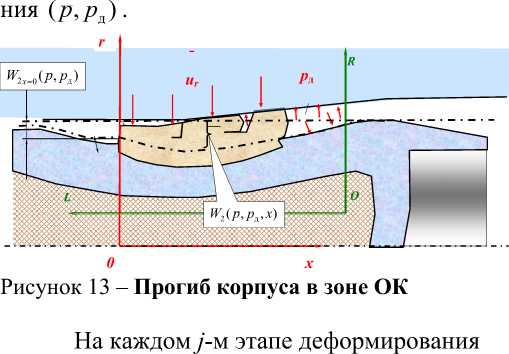
ОК в процессе вдавливания и после него, для каждой точки поверхности ОК с координатой x i граничные условия в перемещениях ur ( x ) определяются из решения трех следующих задач:
-
1. Деформирования трубы реакцией ОК p и давлением p д
W W p W p д ,
где
-
2. Деформирования корпуса изделия реакцией ОК p и давлением в канале p д;
-
3. Деформирования материала ОК в
W1p = k тр ■ p; W1pд = k т^р • Рд , где k т^р и kтр- коэффициенты жесткости трубы определяется из решения задачи радиального деформирования трубы (как правило упругой) кольцевыми нагрузками p д и p,соответственно, например с использованием МКЭ [3];
условиях заданного значения давления p д и известных граничных условиях (21).
Решение перечисленных, взаимосвязанных граничными условиями, задач может производится методом простых итераций. Причем решение первых двух задач представляется табличными зависимостями W2x=о(p,pд), ci(p,pд), c2(p,pд), построенными численно по МКЭ, а третья задача решается по МКЭ в уравнениях (23) с учетом (24), устанавливающих связь между внешними силовыми p и кинематическими u.(x) параметрами. Графическая интерпретация алгоритма приведена на рис. 14. При этом за начало итераций приняты условия, в которых прогибы трубы и корпуса изделия определены на предыдущем j-1 -м этапе деформирования u,0=(R-r)j-W.j-I-W,jV (26)
Условие (26) безразлично для организации итераций, но позволяет максималь- но сократить их число или вовсе их исклю- чить при достаточно малом этапе деформи-
W 2^ p j -1 , p д j _1 , x ) в
рования, принимая
начале этапа решения третьей задачи и вы- числяя W2
( pj , p д j’
x
в конце этапа.
Условием выхода из итераций, явля- ется следующее:
W,+w:,)i-W,+w„)„1 (Wj + W2,X орга-
низованное по i-тым итерациям, где s-любая наперед заданная приемлемая погрешность
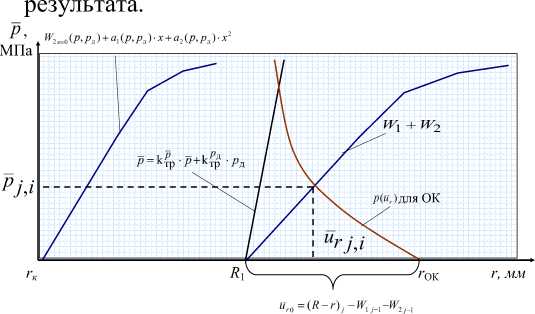
Рисунок 14 - Геометрическая интерпретация алгоритма расчета реакции ОК
На практике необходимо учитывать то, что, в общем случае, профиль канала трубы может быть сложным вследствие неравномерного по его длине радиального износа, возникающего в процессе работы системы, тогда профиль канала трубы выразим табличной функцией R ( L ), причем в процессе движения будет изнашиваться и поверхность самого ОК - А г изн . Еще одним фактором, требующим учета, является переменная во времени (в процессе движения изделия по трубе) величина давления в канале, тогда - p д (1 ) . Действие перечисленных факторов в процессе движения изделия по каналу трубы может приводить к разгрузке ОК. При этом реакция ОК p будет определяться условиями упругих взаимодействий системы "труба - ОК - корпус изделия". Причем возможно появление зазора между поверхностями ОК и трубы. Схема разгрузки ОК приведена на рис. 15. На участке разгрузки кривая p ( ur ) сохраняет наклон вследствие упругих свойств ОК (рис.15), которые можно учитывать зависимостью
Р(x) = Р(x) j-1 -E -utr (x) j-1 - ur (x) j ) h(x) , где p(x)max - наибольшее значение реакции ОК (радиальных напряжений) в точке контакта на предыдущем этапе. E - модуль уп- ругости материала ОК; h(x) - высота профиля ОК относительно координаты рассматриваемой точки поверхности.
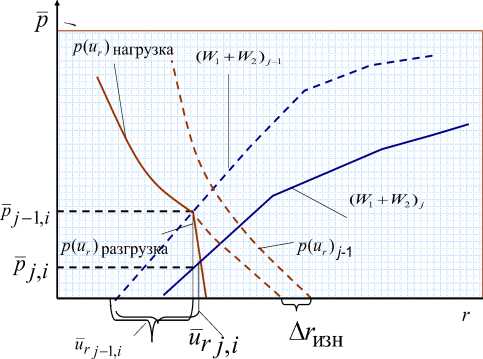
Рисунок 15 - Геометрическая интерпретация алгоритма расчета реакции ОК на этапе разгрузки
Условием появления зазора и его величиной в рассматриваемой точке поверхности ОК с координатой xi будет рассчитанное в результате итераций отрицательное значение ur(xi) = [R(L-xi)-r(xi)]j -...
... -W i (L-X i)- W 2 (x ^cO. (27)
Алгоритм расчета радиальных и осевых взаимодействий можно представить схемой, реализованной в ПК INNER [6], изображенной на рис. 16.
Установленная алгоритмом (рис. 16) зависимость между внешними силовыми p и кинематическими u ^x) параметрами, связанными с геометрией трубы и элементов изделия, с учетом их радиальных прогибов, позволяет в полной мере учитывать конструктивные особенности всех элементов рассматриваемой системы, а также нестабильности, связанные с технологией их изготовления и условиями процесса, в частности, с изнашиванием поверхности канала трубы и др.. В расчете характеристик силового взаимодействия можно учитывать множество других значимых факторов, изменяющихся в условиях функционирования изделия (pд, коэффициента трения f тр, скорости изделия v и др.) [6].
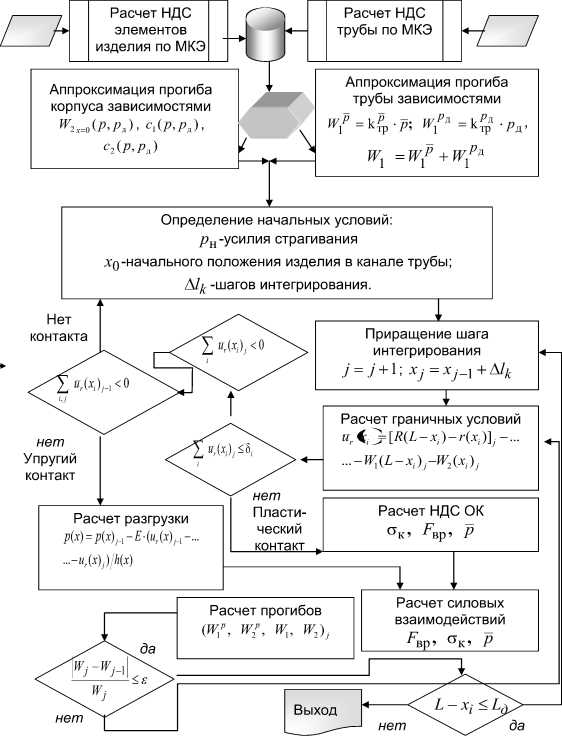
Рисунок 16 - Алгоритм расчета радиальных и осевых взаимодействий
При износе канала трубы в процессе работы системы происходят необратимые изменения геометрии канала, которые влекут за собой значительные изменения условий силового взаимодействия. В частности, с износом увеличивается время и путь процесса вдавливания, его динамичность и сложность условий силового взаимодействия, обусловленные неравномерным износом поверхности канала.
В табл. 3 и на рис. 17. приведены ре- зультаты сопоставительных расчетов, реализованные в ПК INNER характеристик силового взаимодействия для 152 мм изделия с обтюрирующим кольцом сложного гео- метрического профиля и труб, имеющих продольные нарезы и различный износ, в соответствии с числом реализаций процесса N = 0, 412, 900.
Из таблицы видно, что с числом реализаций процесса интенсивность радиальных реакций растет, а осевых составляющих силового взаимодействия снижается (рис. 17). Последнее обусловлено значительным снижением коэффициента трения f тр , изменение величины которого учитывалось по специальному алгоритму [7]. Пример графического изображения этих характеристик приведен на рисунке 17.
Таблица 3 – Наибольшие значения характеристик силового взаимодействия
Характеристика силового взаимодействия |
Число реализаций процесса N |
||
0 |
412 |
1000 |
|
Сила сопротивления движению Fвр ,max , КН |
587 |
271 |
257 |
Путь до Fвр ,max , мм |
107 |
1133 |
1216 |
Радиальная реакция p max , МПа |
146 |
203 |
214 |
Путь до p max , мм |
113 |
1133 |
1216 |
Контактное давление под полем о к 1 ,max , МПа |
443 |
466 |
488 |
Контактное давление под нарезом о к 2 ,max , МПа |
312 |
231 |
171 |
Радиальный прогиб тру бы W 1 ,max , мм |
0,178 |
0,218 |
0,209 |
Радиальный прогиб корпуса W 2 ,max , мм |
0,038 |
0,0195 |
0,0318 |

Рисунок 17 – Характеристики силового взаимодействия в новой и изношенной трубах