Упрочнение деталей машин покрытиями, синтезированными из газовой среды
Автор: Батищев А.Н., Ферябков А.В., Шевченко Г.В.
Журнал: Вестник аграрной науки @vestnikogau
Рубрика: Ремонт и органиация технического сервиса
Статья в выпуске: 1 (16), 2009 года.
Бесплатный доступ
Основным направлением повышения показателей надежности технических систем является повышение износостойкости быстроизнашивающихся деталей, которое может быть достигнуто путем применения современных технологических процессов их упрочнения. В данной статье рассмотрены основные способы получения упрочняющих покрытий из газовой фазы и проанализирована целесообразность их использования в ремонтном производстве АПК.
Короткий адрес: https://sciup.org/147123361
IDR: 147123361
Текст научной статьи Упрочнение деталей машин покрытиями, синтезированными из газовой среды
Российский государственный аграрный заочный университет
УПРОЧНЕНИЕ ДЕТАЛЕЙ МАШ ИН ПОКРЫ ТИЯМИ , СИНТЕЗИРОВАННЫ МИ ИЗ ГАЗОВОЙ ФАЗЫ
Основным направлением повышения показателей надежности технических систем является повышение износостойкости быстроизнашивающихся деталей , которое может быть достигнуто путем применения современных технологических процессов их упрочнения .
В данной статье рассмотрены основные способы получения упрочняющих покрытий из газовой фазы и проанализирована целесообразность их использования в ремонтном производстве АПК .
В ремонтном производстве широко применяются различные способы упрочнения , которые можно подразделить на 6 основных классов [1]:
-
1. упрочнение с образованием пленки на поверхности ;
-
2. с изменением химического состава поверхностного слоя ;
-
3. с изменением структуры поверхностного слоя ;
-
4. с изменением энергетического запаса поверхностного слоя ;
-
5. с изменением микрогеометрии поверхности и наклепом ;
-
6. с изменением структуры по всему объему материала .
В свою очередь , упрочнение с созданием пленки на поверхности , можно получить с помощью :
-
а ) химической реакции ;
-
б ) осаждением из газовой фазы ;
-
в ) электролитическим ( электрохимическим )
осаждением ( нанесением );
-
г ) напылением .
Характерной чертой получения упрочняющих покрытий из паровой или газовой фазы является прямое преобразование электрической или иной энергии в энергию технологического воздействия , основанную на структурно - фазовых превращениях в осажденном на поверхности конденсате или в самом поверхностном слое детали , помещенной в вакуумную камеру ( или в атмосфере ).
Основным достоинством данных методов является возможность создания весьма высокого уровня физико - механических свойств материалов в тонких поверхностных слоях , нанесение плотных покрытий из тугоплавких химических соединений , а также алмазоподобных , которые невозможно получить традиционными методами . Кроме того , эти методы позволяют обеспечить :
-
• высокую адгезию покрытия к основе ;
-
• равномерность покрытия по толщине на большой площади ;
-
• высокую чистоту поверхности покрытия ;
-
• экологическую чистоту производственного цикла .
Методы создания упрочняющих покрытий посредством осаждения в вакууме ( или в атмосфере рабочего газа ) бывают физическими (PVD) и химическими (CVD) ( рис . 1) [2]. Внутри этих двух групп существует достаточно большое число способов нанесения покрытий , в том числе комбинированных или способов с поддержкой или активацией процесса от других источников энергии .
Как следует из названия используемых процессов (PVD и CVD), они основаны на различных , по сути , явлениях . Конечный же результат и в том и в другом случае – осаждение из газовой фазы материала покрытия на основу . Сравнивая эти два метода , следует отметить , что основным преимуществом методов CVD является более простая технология : более простая загрузка деталей в камеру , нет необходимости в долговременной многоступенчатой очистке и соблюдении высокой чистоты поверхности , а так же нет необходимости во вращении детали при нанесении покрытия . Это делают метод CVD экономически выгодными при нанесении покрытий на большие партии деталей . В свою очередь , нанесение PVD- покрытий при помощи дугового или тлеющего разряда ( магнетрон a) обладает большей производительностью и не столь чувствительно к незначительным отклонениям технологических параметров .
При физическом осаждении (PVD) материал покрытия переходит из твердого состояния в газовую фазу в результате испарения под воздействием тепловой энергии или в результате распыления за счет кинетической энергии столкновения частиц материала . PVD- процессы проводят в вакууме или в атмосфере рабочего газа при достаточно низком давлении .
Метод химического осаждения (CVD) практически не имеет ограничений по химическому составу покрытий . Все присутствующие частицы могут быть осаждены на поверхность материала . Какие покрытия при этом образуются , зависит от комбинации материалов и параметров процесса . Если процесс протекает при заполнении пространства реакционно способным газом ( кислородом , азотом или углеводородами ), в результате химической реакции между атомами осаждаемых металлов и молекулами газа происходит нанесение оксидных , нитридных и карбидных покрытий . Состав покрытия зависит от парциального давления газа и скорости осаждения покрытия .
При использовании CVD- метода химические реакции происходят в непосредственной близости или на поверхности обрабатываемого материала . В отличие от процессов PVD, при которых твердые материалы покрытия переводятся в газообразную фазу испарением или распылением , при CVD- процессе в камеру для нанесения покрытия подается смесь газов . Для протекания необходимых химических реакций требуется температура до 1100 ° С , что ограничивает число материалов , на которые можно нанести CVD- покрытие ( рис . 1), т . к . прошедшие термическую обработку материалы теряют в результате отпуска свои свойства .
Процессы CVD происходят при давлениях 100…1000 Па . Покрытие наносится на всю поверхность изделия . Для получения одинаковых свойств всего покрытия в объеме рабочей камеры ( особенно большой ) необходимо обеспечить оптимальные потоки газа . С этой целью применяются специальные системы подачи газа , так называемый газовый душ . Установки CVD, как правило , имеют достаточно большие габариты . Для предотвращения опасных выбросов газов в атмосферу используется специальная система фильтров . Благодаря высокой температуре нанесения , обеспечивающей частичную диффузию наносимого материала в основу , покрытия CVD характеризуются лучшей адгезией , в сравнении с покрытиями PVD.
Для снижения вредного воздействия температуры на свойства твердых сплавов разработан способ нанесения покрытия CVD при температурах около 800° С , который получил название среднетемпературного метода (MT-CVD) ( рис . 1).
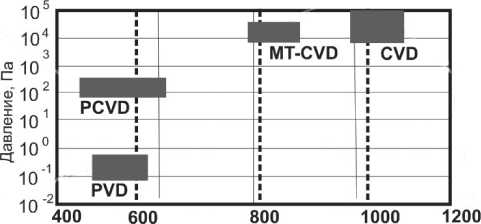
Температура нанесения покрытия, °C
Рисунок 1 – Параметры основных методов получения покрытий из газовой фазы в вакууме ( или в атмосфере рабочего газа )
PVD и CVD- методы также различаются по виду внутренних напряжений в слое наносимого покрытия . При методе PVD преобладают сжимающие напряжения , а при методе CVD – растягивающие .
Недавно была разработана еще одна разновидность метода CVD, позволившая снизить температуру нанесения покрытия практически до температур , используемых в PVD- методе [2], получившая название P-CVD ( рис . 2). Практически метод представляет собой комбинацию двух основных методов , поскольку нанесение покрытий CVD- методом происходит в среде плазмы ( как при PVD). Также в иностранной литературе применяют обозначения PA-CVD ( активированные плазмой CVD- процессы ) и PE-CVD ( усиленный плазмой CVD).
Для начала химических реакций при этом методе используется не высокая температура , а плазма в рабочей камере . Плазма оказывает каталитическое воздействие и концентрирует энергию . В результате процессы могут протекать при более низких температурах . С помощью P-CVD- метода , в зависимости от подводимого газа , можно наносить карбидные , нитридные и карбонитридные покрытия при температурах 400-500° С . По сравнению с полученными по методу PVD эти покрытия имеют лучшую адгезию и меньшие внутренние напряжения . Кроме того , отпадает необходимость в особом расположении изделий для получения равномерного покрытия . Однако метод P-CVD пока не получил широкого распространения .
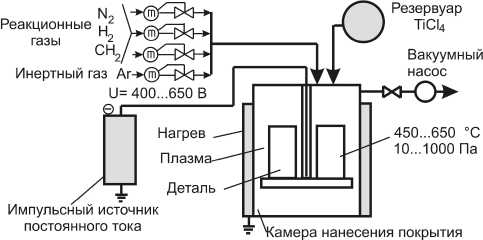
Рисунок 2 – Схема установки для нанесения покрытий методом P-CVD
Приведем примеры применения CVD для восстановления и упрочнения деталей . Так Козыревым В . В ., Козыревой Л . В ., Чупятовым Н . Н . и др . разработаны научные и технологические основы повышения надежности деталей композиционными материалами с применением CVD- метода элементоорганических соединений . Ими разработана и апробирована технология изготовления и восстановления подшипников поворотных опор навозоуборочных транспортеров ТСН -160 А ; созданы композиционные материалы с использованием ЭОС - модификаторов армирующих волокон , применение которых обеспечивает ресурс узлов трения , работающих в условиях несовершенной смазки под воздействием агрессивных сред органического происхождения [3]. Также разработаны технологические процессы восстановления и упрочнения подшипников скольжения шестеренных насосов НШ -50 У получением никелевого покрытия на алюминиевом сплаве способом CVD [4].
Процесс низкотемпературного газо - фазного синтеза плазмохимических покрытий ( ПХП ) – это один из немногих методов , разработанных в последнее время , способный многократно повысить долговечность изнашиваемых деталей с использованием малогабаритного легко переналаживаемого оборудования , работающего при атмосферном давлении , в отличие от способов PVD и CVD, осуществляемых в вакуумных камерах . Сущность процесса заключается в том , что легколетучие органические вещества , подаваемые в плазму , образуют различного рода химические соединения , которые конденсируются на обрабатываемой поверхности в виде тонких пленок , формирующих покрытие .
Цель ПХП – многократное увеличение усталостных свойств , коррозионной стойкости , жаростойкости , антисхватывания , фреттинг - стойкости , обеспечивающее повышение эксплуатационных свойств деталей .
Наиболее прогрессивным способом нанесения ПХП является финишное плазменное упрочнение ( ФПУ ). Само понятие ФПУ и технология впервые введены НПФ " Плазмацентр ", г . С .- Петербург .
Способом ФПУ наносят износостойкое покрытие, толщиной до 3…10 мкм в безвакуумном пространстве при атмосферном давлении [5]. При этом упрочнение деталей машин происходит при их температуре в процессе обработки порядка 100…200ºС . ФПУ можно проводить с нанесением износостойкого покрытия и с одновременной повторной закалкой подпленочного слоя или без нее. Отличительной особенностью ФПУ является возможность нанесения износостойкого покрытия без значительного термического воздействия на основной материал детали.
Основным принципом, взятым за основу технологии ФПУ, является разложение паров жидких химических реагентов, вводимых в дуговой плазмотрон, с последующим прохождением плазмохимических реакций и образованием на поверхности детали упрочняющего покрытия.
Процесс протекает в несколько стадий [6]:
-
• создание устойчивого потока плазмы дугового разряда с использованием в качестве плазмообразующего газа аргона и плазмотрона косвенного действия ;
-
• испарение жидких химических реагентов в объеме специального питателя и перенос их паров совместно с дополнительным потоком инертного газа в образованную ранее плазму дугового разряда ;
-
• получение в дуговом канале плазмотрона косвенного действия паро - плазменного потока содержащего возбужденные атомы , молекулы , радикалы , положительно и отрицательно заряженные ионы , электроны , кластеры ;
-
• прохождение плазмохимических реакций компонентов паровой фазы в плазме дугового разряда с образованием новых соединений и перенос продуктов реакций плазменной струей к поверхности детали ;
-
• конденсация продуктов реакций на поверхности детали с одновременным тепловым воздействием на нее факела плазменной струи ;
-
• прохождение взаимодействия между адсорбированными осажденными продуктами реакций на подложке , приводящего к зарождению и росту покрытия .
Протекание процесса ФПУ напоминает основные стадии физического осаждения покрытий из паровой фазы ( методы PVD). Но в отличие от известных процессов PVD данный метод упрочнения позволяет реализовывать все стадии образования покрытия при атмосферном давлении , без вакуумных камер . Кроме того , покрытия , нанесенные методом PVD, при их осаждении на низкотемпературную основу с температурой менее 250º С обычно имеют низкую адгезию [6].
В качестве источника тепловой энергии для нанесения покрытия при ФПУ используется плазменная струя , истекающая при атмосферном давлении из малогабаритного дугового плазмотрона ( рис .3). Эффективность ФПУ основана на повышении ресурса деталей минимум в два раза [5, 6], что достигается за счет образования диэлектрического , химически инертного защитного покрытия с одновременным изменением физико - механических свойств поверхностного слоя детали : увеличением ее микротвердости ( как правило , в 1,5…2 раза ), значительного уменьшения коэффициента трения , выравнивания микродефектов .

ПГ
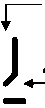
ТГ+П
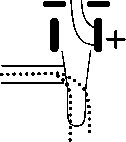
Рисунок 3 – Схема плазмотрона для ФПУ . Газы : ПГ – плазмообразующий , ТГ – транспортирующий , ДГ – дополнительный , П – реагенты упрочнения
Выводы
-
1. Оборудование С VD и PVD дорогостоящее , технически сложное , стационарное и имеющее большие габаритные размеры . В ряде случаев на данном оборудовании нецелесообразно упрочнение мелких партий изделий .
-
2. Технологии CVD и PVD достаточно сложны и подразумевают качественную многоступенчатую очистку и подготовку поверхности , использование дорогостоящих высокочистых химических реактивов (TiCl4, NH3 и т . д .) и прецизионных дозаторов химических реагентов , точный контроль продуктов химических реакций в рабочей камере и т . п .
-
3. Оборудование для ФПУ включает в себя переносной блок аппаратуры с дозатором - испарителем реагентов и малогабаритным плазматроном , водяную систему охлаждения и баллон с плазмообразующим газом - аргоном , вытяжку . В качестве источника питания может использоваться серийный сварочный выпрямитель .
-
4. Технологический процесс ФПУ включает в себя операции очистки ( обезжиривания ) поверхности детали и непосредственной ее обработки открытой плазмой , в отличие от CVD и PVD не в вакууме , а на открытом воздухе . Продолжительность обработки деталей не превышает нескольких минут . Температура нагрева деталей при этом не более 200 оС , геометрия поверхности и параметры шероховатости не изменяются . Требования безопасности при ФПУ не накладывают ограничений для его широкого использования и определяются применением вытяжек и сварочных источников питания .
-
5. Технологии CVD и PVD используются в основном в крупносерийном и массовом производстве режущего инструмента и деталей машин для их упрочнения . В ремонтном производстве АПК , на наш взгляд , данные технологии , в большинстве случаев , использовать нецелесообразно .
-
6. Для ремонтного производства АПК наиболее приемлемым из возможных способов получения упрочняющих покрытий осаждением из газовой фазы является финишное плазменное упрочнение или аналогичный способ получения плазмохимических покрытий .
Список литературы Упрочнение деталей машин покрытиями, синтезированными из газовой среды
- Тушинский, Л.Н. Теория и технология упрочнения металлических сплавов [Текст]/Л.Н. Тушинский. -Новосибирск: Наука, 1990.
- Локтев, Д. Методы и оборудование для нанесения износостойких покрытий [Текст]/Д. Локтев, Е. Ямашкин//Наноиндустрия. Научно-технический журнал. -2007. -№4. -С.18-26.
- Козырева, Л.В. Повышение надежности поворотных опор навозоуборочных транспортеров ТСН-160А композиционными материалами с применением CVD-метода элементоорганических соединений [Текст]: автореф. дисс. канд. техн. наук./Л.В. Козырева. -М., 2007. -16с.
- Чупятов, Н.Н. Технология восстановления и упрочнения деталей шестеренных насосов НШ-50У CVD-методом металлоорганических соединений [Текст]: автореф. дисс. канд. техн. наук/Н.Н. Чупятов. -М., 2008. -16с.
- Тополянский, П.А. Финишное плазменное упрочнение инструмента и оснастки -итоги исследований и внедрений [Текст]/П.А. Тополянский, Н.А. Соснин, С.А. Ермаков//Технологии ремонта, восстановления, упрочнения и обновления машин, механизмов, оборудования и металлоконструкций. Материалы 6-й Международной практической конференции-выставки 13-16 апреля 2004 г. -Санкт-Петербург: Изд. СПбГПУ. -2004. -С.232-257.
- Тополянский, П.А. Исследование адгезионных свойств и механизма образования покрытия, наносимого методом финишного плазменного упрочнения [Текст]/П.А. Тополянский//Технологии ремонта, восстановления и упрочнения деталей машин, механизмов, оборудования, инструмента и технологической оснастки. Материалы 7-й Международной практической конференции-выставки 12-15 апреля 2005 г. -Санкт-Петербург: Изд. СПбГПУ. -2005. -С.316-333.