Влияние дисперсности карбидов вольфрама на свойства и износостойкость многослойных газотермических покрытий с подслоем никеля
Автор: Паркин Анатолий Алексеевич, Жаткин Сергей Сергеевич, Смин Александр Борисович
Журнал: Известия Самарского научного центра Российской академии наук @izvestiya-ssc
Рубрика: Машиностроение и машиноведение
Статья в выпуске: 4-2 т.18, 2016 года.
Бесплатный доступ
Работа посвящена исследованию структуры, механических свойств и износостойкости многослойного покрытия, сформированного ацетиленокислородной наплавкой из карбидосодержащх гибкого шнура, порошкового материала с подслоем и без подслоя никеля. Установлены зависимости изменения величины износа от структуры наплавленного материала и условий наплавки.
Наплавка, порошковый материал, никель, микроанализ, образец, структура
Короткий адрес: https://sciup.org/148205729
IDR: 148205729
Текст научной статьи Влияние дисперсности карбидов вольфрама на свойства и износостойкость многослойных газотермических покрытий с подслоем никеля
порошкового никеля (образцы №№ 3, 4); 4 – аналогично схеме 2, но с подслоем из порошкового никеля (образцы №№ 5, 6) .
В работе проведены исследования микроструктуры; измерения микротвердости; рентгеноспектральный микроанализ наплавленных материалов; проведены локальные испытания на абразивный износ. Исследование микроструктуры позволили установить форму и размеры карбидов для различных условий наплавки.
Из рис. 1 видно, что после наплавки гибкого прутка (шнура) без подслоя никеля формируется карбидосодержащий наплавленный слой с карбидами различной формы у дна зоны расплава с глубиной проплавления заготовки не больше 0,05мм.
Использование подслоя из никеля толщиной до 1 мм (рис. 2) увеличило глубину проплавления материала заготовки до 0,1-0,2 мм, исключило оседание карбидов вольфрама непосредственно до поверхности материала заготовки.
При наплавке трехслойного покрытия, рис. 3: подслой никеля + слой 60WС40Ni (гибкий пруток + слой наплавленного порошка 80 WС 20 Ni ) в поверхностном слое наплавленного материала формируется композиционное мелкозернистое покрытие с равномерным распределением карбидов вольфрама.
При трехслойной наплавке глубина проплавления материала заготовки уменьшается.
РЕЗУЛЬТАТЫ ПРОВЕДЕНИЯ ЭЛЕМЕНТНОГО МИКРОАНАЛИЗА
На рис. 4 – 5 показаны различные области образца №7 (наплавка без подслоя, шнуром (60WC40Ni+порошок 80WC20Ni), в которых проводился элементный микроанализ. В таблице 1 представлены результаты элементного микроанализа в различных зонах наплавки.
Результаты исследования микроанализа представлены в табл. 1.
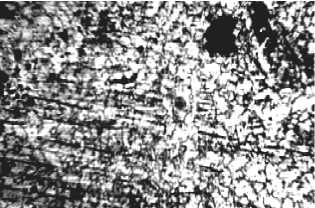
а
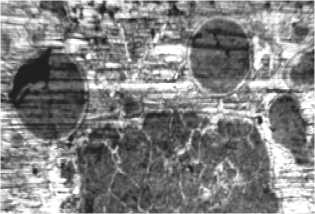
б
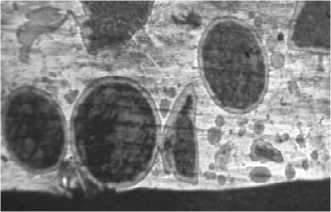
в
Рис. 1. Микроструктура образца №2 (без подслоя никеля – шнур 60WС40Ni : а – верх зоны наплавки; б – середина зоны наплавки; в – низ зоны наплавки (зона сплавления)

а б в
Рис. 2. Микроструктура образца №4 (подслой никеля+шнур 60WС40Ni ): а – верх зоны наплавки; б – середина зоны наплавки; в – низ зоны наплавки (зона сплавления)
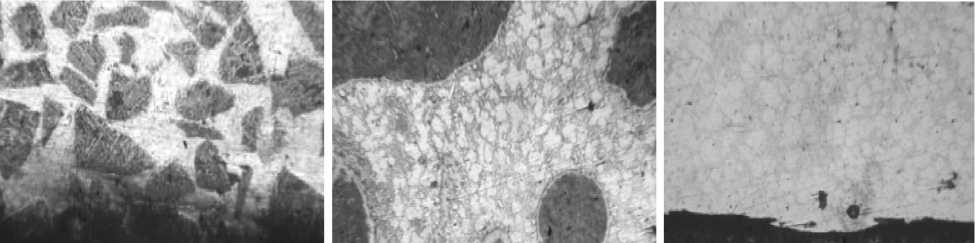
а б в
Рис. 3. Микроструктура образца №5 (подслой никеля +шнур 60WС40Ni + порошок 8 0WС20Ni ): а – верх зоны наплавки; б – середина зоны наплавки; в – низ зоны наплавки (зона сплавления)
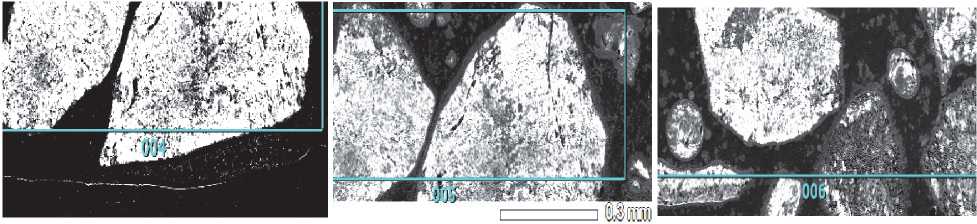
Рис. 4. Структура и элементный микроанализ зон наплавки образца №7 без подслоя никеля: 004 – зона дна наплавленной ванны из гибкого шнура; 005 – зона наплавленного шнура;
006 – зона наплавленного порошка

Рис 5. Структура и зона элементного анализа подслоя никеля
Микроанализ показал, что в наплавленный материал происходит восходящая диффузия железа из материала матрицы с уменьшением массового процентного содержания к поверхностному слою.
При наплавке с подслоем никеля (рис. 5) процентное содержание железа уменьшается практически до исходного значения, то есть подслой препятствует проникновению железа в наплавляемый карбидосодержащий материал.
Таблица 1. Элементный микроанализ материала заготовки, наплавленного шнура и порошка
№ зоны |
C |
O |
Si |
Cr |
Fe |
Ni |
W |
Total |
003 (заготовка) |
1.82 |
0.44 |
0.03 |
2.42 |
92.83 |
1.62 |
0.85 |
100.00 |
004 |
3.41 |
1.03 |
8.41 |
0.93 |
6.15 |
7.42 |
72.64 |
100.00 |
005 |
2.43 |
0.59 |
8.08 |
1.66 |
5.64 |
11.27 |
70.33 |
100.00 |
006 |
2.50 |
0.97 |
7.33 |
2.87 |
5.15 |
24.42 |
56.49 |
100.00 |
Таблица 2. Элементный микроанализ материала подслоя наплавленного никеля
№ зоны |
C |
O |
Si |
Mn |
Cr |
Fe |
Ni |
W |
Total |
007 |
0.41 |
0.00 |
2.12 |
0.56 |
9.44 |
2.27 |
85.21 |
0.00 |
100.00 |
Таблица 3. Результаты измерения микротвердости наплавленных материалов в зависимости от вида наплавки
№ обр. |
Вид наплавляемого материала |
Микротвердость, кг/мм2 |
Размер карбидов вольфрама в зоне наплавки, мкм |
1 |
Без подслоя никеля, шнур 60WC40Ni |
1500 ± 1000 |
40-100; 110-500; 700900 |
2 |
Без подслоя никеля, шнур 60WC40Ni |
900 ± 500 |
40-100; 150-450; 700900 |
3 |
Подслой никеля+шнур 60WC40Ni |
1000 ± 500 |
50-150; 170-500; 700900 |
4 |
Подслой никеля+шнур 60WC40Ni |
800 ± 400 |
60-100; 120-500 |
5 |
Подслой никеля+шнур 60WC40Ni+порошок 80WC20Ni |
1200 ± 450 |
До 350 максимальные |
6 |
Подслой никеля, шнур 60WC40Ni+порошок 80WC20Ni |
900 ± 150 |
До 300 максимальные |
7 |
Без подслоя никеля, шнур 60WC40Ni+порошок 80WC40Ni |
1500 ± 400 |
До 250 |
9 |
Без подслоя никеля, шнур 60WC40Ni |
1600 ± 500 |
До 700, сферические карбиды |
Таблица 4. Сравниетельные результаты испытаний на износ наплавленных шнура (60Wc40Ni) и порошка (80Wc20Ni) при АКН и CARPENTERMicro-MeltNT-60 при плазменной наплавке
№№ образца |
8 |
9 |
Состав наплавленного материала |
Без подслоя никеля WC 60%+ Ni 40%(шнур) + WC 80%+ Ni 20%(порошок) |
Без подслоя никеля, WC 60%+ Ni 40%(шнур) |
Структурный Фактор |
Карбиды вольфрама средних размеров (100-250 мкм) с равномерном распределением |
Глобулярные карбиды вольфрама, размерами до 400 - 1100 мкм С® ‘ |
Средняя величина износа, мкм , (за 600 секунд трения при размере алмазного порошка 2-3 мкм и силе нагрузке F н = 10 кгс). |
22 ÷23 |
15÷17 |
Средняя величина износа при плазменной наплавке CARPENTERMicro-MeltNT-60 по трем зонам трения, мкм: |
Ток дуги 70А - 31 Ток дуги 85 А - 37 Ток дуги 100 А - 39 |
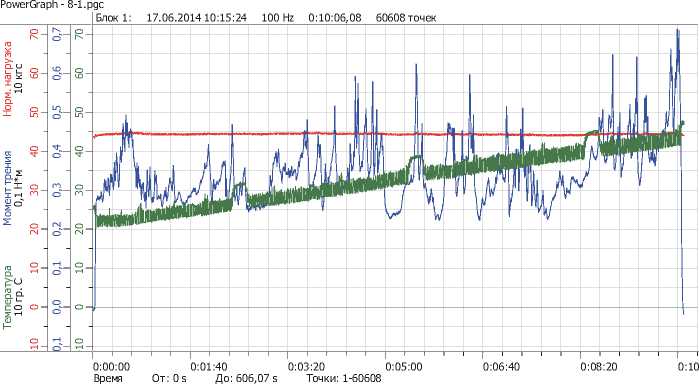
Рис. 6. Диаграмма износа образца №8 – наплавка без подслоя шнуром (60WC 40Ni) + порошок (80WC 20Ni)
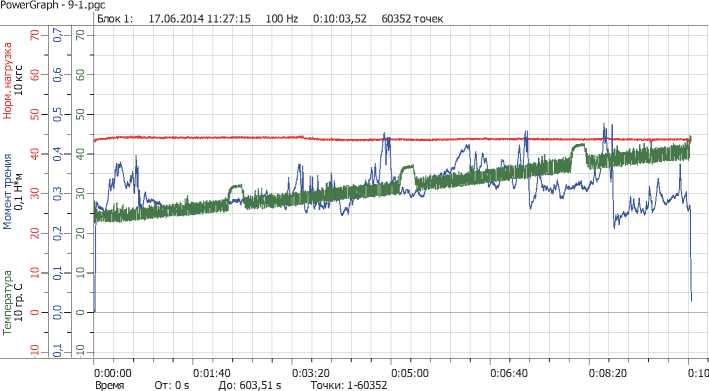
Рис. 7. Диаграмма испытаний на износа образца №9 - наплавка без подслоя шнуром (60WC 40Ni)
Из таблицы 2, видно, что в наплавленный подслой входят также хром и кремний. Микроанализ непосредственно карбидов показал, что они имеют практически исходный состав, то есть при температурах ацетиленокислордной наплавки, растворение связующего никеля и других элементов в них не происходит и, следовательно, на свойства карбидов не влияют. В то же время при плазменной наплавке в карбидах вольфрама наблюдается растворение железа и никеля. Результаты измерения микротвердости и ее разброса наплавленных материалов в зависимости от технологии наплавки представлены в табл. 3.
Наименьший разброс значений микротвердости наблюдается при наплавке с порошком карбида вольфрама. Наплавленный карбид вольфрама в виде шнура имеет наибольший разброс значений микротвердости относительно среднего значения. Невысокие значения разброса микротвердости относительно ее средней величины установлены также в зоне наплавки шнура при формировании сферической морфологии карбидов вольфрама.
Сравнительные результаты испытаний на износ при АКН и плазменной наплавке представлены в табл. 4.
Величина износа существенным образом зависит от формы направленных карбидов вольфрама. Округлая форма уменьшает величину износа, что может быть обусловлено проскальзыванием частиц абразива (порошок алмаза 2 -3 мкм) по поверхности карбидных частиц наплавленных материалов. Сравнительный анализ показывает, что при АКН наплавке износ наплавленного материала, содержащего одинаковое процентное карбидов вольфрама, ниже, чем при плазменной наплавке.
Диаграмма испытаний на износ образца №8 - наплавка без подслоя никеля шнуром (60WC 40Ni) + порошок (80WC 20Ni) показана на рис. 6.
Диаграмма испытаний на износ образца №9 - наплавка без подслоя никеля шнуром (60WC 40Ni) представлена на рис. 7.
АНАЛИЗ ОБРАЗОВАНИЯ ДЕФЕКТОВ
На образцах с наплавленным шнуром 60WC 40Ni без подслоя никеля (образцы №1; №2; №3; №9; №10), наблюдается тенденция к образованию крупных (до 4мм) дефектов в виде пор. Дефекты образуются в основном в области наплавки шнура и в подслое никеля (рис. 8 - 10).
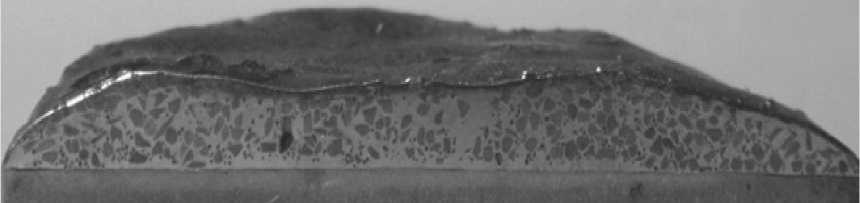
Рис. 8. Образец №1 - наплавка шнуром - 60WC 40Ni без подслоя
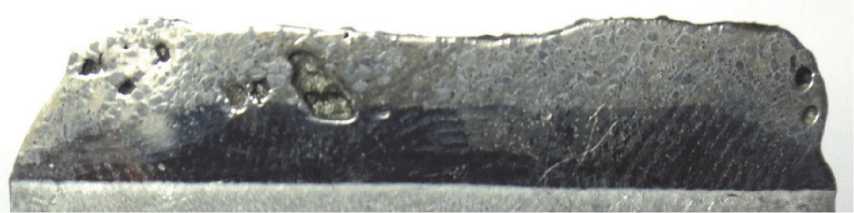
Рис. 9. Образец №3 - наплавка шнуром (60WC 40Ni) с подслоем никеля
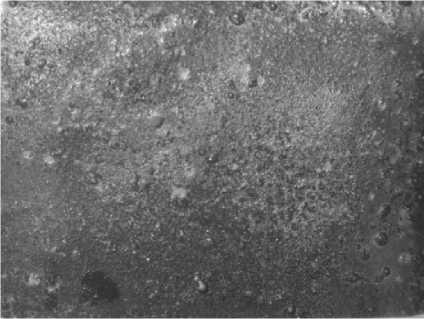
а
Рис. 10. Поверхность наплавленных образцов:
а – наплавка на поверхности образца № 6 порошкового материала 80WC 20Ni;
б – дефектная структура поверхности образца №9 наплавленного шнуром - 60WC 40Ni
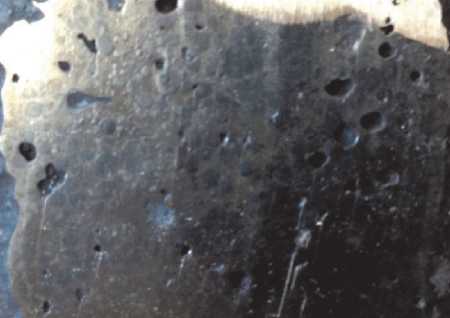
б
ВЫВОДЫ
-
1. При наплавке шнуром, наблюдается образование дефектов в виде пор.
-
2. При наплавке с применением порошка, дефекты не наблюдаются, поверхность формируется более равномерной и однородной.
-
3. Образование зоны сплавления и ее глубины в значительной степени зависит от наличия подслоя и процесса реализации технологии наплавки.
-
4. Технология ацетиленокислородной наплавки дает возможность получить химически чистые карбиды с высокими эксплуатационными свойствами.
-
5. Структура с крупными глобулярными карбидами обладает большей износостойкостью с минимальным разбросом значений микротвердости, однако наблюдается склонность к образованию дефектов.
-
6. Величина износа во многом зависит от размеров карбидов и плотности их расположения.
-
7. Ацетиленокислородная наплавка имеет экономическое преимущество перед плазменной наплавки из-за низкой стоимости оборудования и самой технологии наплавки.
Список литературы Влияние дисперсности карбидов вольфрама на свойства и износостойкость многослойных газотермических покрытий с подслоем никеля
- Паркин А.А., Жаткин С.С., Минаков Е.А. Влияние структуры и свойств на износ покрытия Micro Melt NT-60 после плазменной порошковой наплавки//Известия Самарского научного центра Российской академии наук. 2011. Т. 13. №4(3). С. 847-852.
- Исследование локального износа покрытий Micro Melt NT-60 и Stellite 190W, полученных плазменной порошковой наплавкой/Е.А. Минаков, С.С. Жаткин, А.А. Паркин, О.С. Фураев, В.Г. Климов//XII международная научно-практическая конференция «Фундаментальные и прикладные исследования, разработка и применение высоких технологий в промышленности и экономике». 8-10 декабря 2011 г. Санкт-Петербург, Россия. C. 254-259.
- Паркин А.А., Жаткин С.С., Минаков Е.А. Оптимизация технологии плазменной наплавки порошковых материалов//Металлургия машиностроения. 2011. № 1. С. 44-49.