Влияние химического состава основного металла на вязкие свойства зоны термического влияния электросварных труб большого диаметра
Автор: Худяков Артем Олегович
Журнал: Вестник Южно-Уральского государственного университета. Серия: Металлургия @vestnik-susu-metallurgy
Статья в выпуске: 3 т.14, 2014 года.
Бесплатный доступ
Раскрыта проблема снижения вязких свойств в зоне термического влияния сварных соединений толстостенных труб. Наибольший провал вязких свойств наблюдается в области крупного зерна зоны термического влияния, непосредственно прилегающей к линии сплавления. Это связано со значительными структурными изменениями в данной области сварного соединения.Показано, что с увеличением толщины стенки свариваемых труб неизбежно происходит рост погонной энергии сварки, соответственно, происходит падение скорости охлаждения после сварки. Так, при сварке труб с толщиной стенки свыше 23 мм скорость охлаждения падает ниже 10 °С/с, что привоит к сильному охрупчиванию зоны термического влияния заводских сварных соединений. Таким образом, для обеспечения эксплуатационной надежности толстостенных труб большого диаметра необходимо внести кардинальные изменения в технологию сварки, позволяющие существенно снизить погонную энергию, или разработать химический состав основного металла, менее чувствительного к термическому циклу сварки.Проанализировано влияние отдельных химических элементов на прочностные свойства основного металла высокопрочных трубных сталей и на вязкие свойства в зоне термического влияния (ЗТВ). Показано негативное влияние кремния и молибдена на вязкие свойства в ЗТВ. Дополнительное легирование стали ванадием также приводит к значительному охрупчиванию области крупного зерна ЗТВ.Для достижения высоких вязких свойств сварных соединений труб большого диаметра необходимо: исключить ванадий из химического состава стали; снизить содержание кремния до уровня 0,1 %; легирование молибденом должно осуществляться на минимальном уровне для достижения требуемых прочностных свойств.
Вязкость, зона термического влияния, скорость охлаждения, погонная энергия сварки
Короткий адрес: https://sciup.org/147156886
IDR: 147156886
Текст научной статьи Влияние химического состава основного металла на вязкие свойства зоны термического влияния электросварных труб большого диаметра
Современный уровень развития металлург и ческой промышленности позволяет производить металлопродукцию с уникальным комплексом механических и эксплуатационных свойств. С о временный металл для производства труб нефтег а зового сортамента имеет высокие показатели прочности (до 700 Н/мм2 и более), пластичности (δ>20 %), ударной вязкости (300 Дж/см 2 и более) и хладостойкости до –60 °С [1].
Известно, что основной проблемой изготовления сварной конструкции с точки зрения экс- плуатационной надежности сварных соединений является поведение металла в зоне термического влияния (ЗТВ). Как показывает практика эксплуатации конструкций и результаты испытаний сварных соединений, металл ЗТВ подвержен разрушению больше, чем основной металл трубы.
Сварное соединение обладает ярко выраженной структурной, а следовательно, и механической неоднородностью (рис. 1). При очень высоких значениях вязких свойств основного металла (CTOD ≥ 1 мм) и литого металла сварного шва
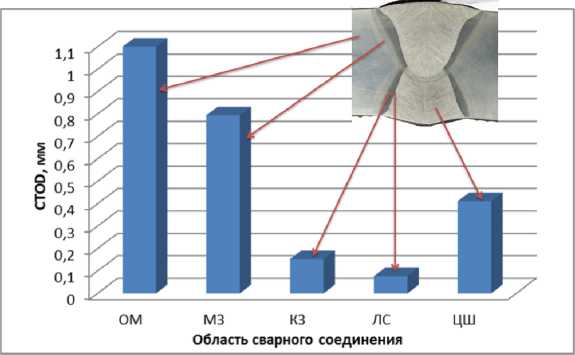
Рис. 1. Механическая неоднородность сварных соединений труб большого диаметра
(CTOD > 0,4 мм) уровень вязких свойств области ЗТВ, непосредственно прилегающей к сварному шву, т. е. области крупного зерна ЗТВ очень мал (CTOD < 0,1 мм). Это связано с наибольшими структурными изменениями, происходящим и в зоне, нагреваемой выше температуры начала и нтенсивного роста аустенита.
Трубы большого диаметра производятся из толстолистового проката, выполнение продольных сварн ых швов выполняется с помощью многод у говой сварки под слоем флюса с использованием до 5 электродов.
Особенность производства заключается в том, что сварку выполняют по Х- образной разделке по предварительно сваренному электродуговой сва ркой в среде защитного газа «технологическому шву». При этом нормативно- техническая докуме нтация обязывает производителя при выполнении наружного шва обеспечить переплавление техн о логического шва. Обязательными условиями я в ляются также ограничения по ширине и усил ению сварного шва. Таким образом, при выполн е нии продольного шва все производители выпо л няют задачу с одинаковыми граничными усл о-виями[2]:
– заполнение разделки;
– обеспечение требуемой глубины проплавл е ния с целью полного переплавления технологич еского шва;
– обеспечение требуемой геометрии сварного соединения.
Погонная энергия сварки или тепловложение является интегральной характеристикой режима сварки и определяется из выражения:
Е = q, Дж/мм , v где v – скорость сварки; q – эффективная тепловая мощность сварочного процесса.
Эффективная тепловая мощность сварочного процесса определяется по формуле q=nX( Iсвид),Дж, где Iсв – сварочный ток; Uд – напряжение на дуге; η – эффективный КПД.
Для автоматической сварки под слоем флюса принимают η = 0,95.
С увеличением толщины стенки свариваемых труб необходимо обеспечить более глубокое проплавление и заполнение большего пространства разделки кромок, что неизбежно ведет к повышению погонной энергии сварки. Зависимость применяемой погонной энергии сварки от толщины стенки приведена на рис. 2.
Оценка влияния термического воздействия сварки на структуру и механические свойства металла ЗТВ основана на моделировании термических циклов сварки. Исследования проводятся с нагрева образцов до температур, характерных для максимальных температур нагрева ЗТВ при сварке (1300–1350 °С), при изменении скоростей охлаждения в диапазоне соответствующих различным режимам сварки (0,1–300 °С/с). Для оценки охрупчивания стали после сварки проводят испытания образцов на ударный изгиб, нагретых до температур 1300–1350 °С, с последующим охлаждением с различными скоростями. В результате испытаний строится зависимость ударной вязкости от скорости охлаждения (рис. 3).
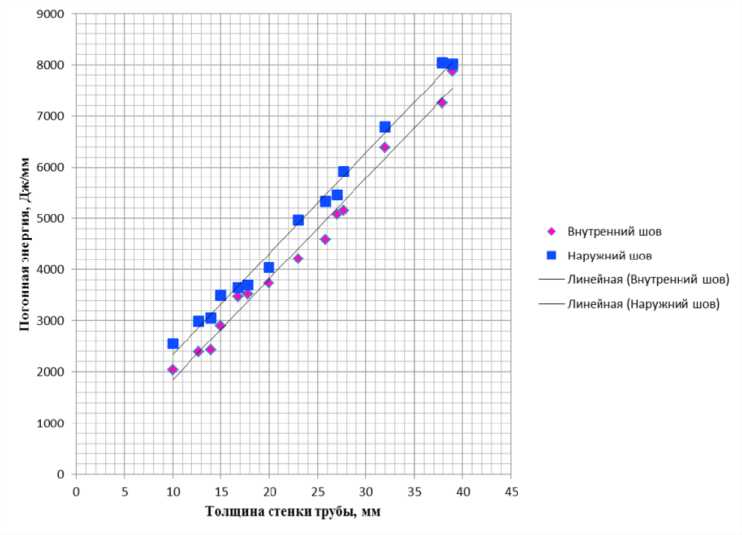
Рис. 2. Зависимость погонной энергии сварки от толщины стенки свариваемых труб
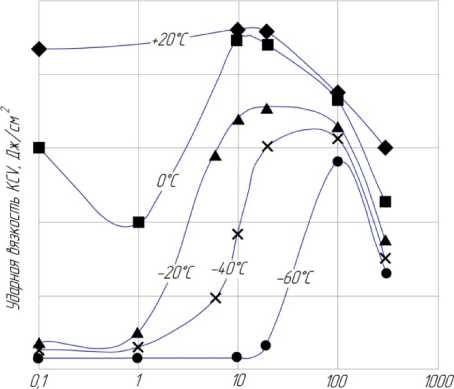
Скорость охлаждения (800/500‘С), вС/сек
Рис. 3. Зависимость ударной вязкости от скорости охлаждения ЗТВ
Многочисленные испытания образцов с им и тированными циклами сварки показывают, что при снижении скорости охлаждения ниже 10 °С происходит резкое снижение вязких свойств ЗТВ сварн ых соединений труб большого диаметра.
Скорость охлаждения ЗТВ сварных соедин е ний в реальных условиях напрямую зависит от погонной энергии сварки. Таким образом, с увел и чением толщины стенки труб в результате увел и чения погонной энергии сварки происходит сни жение скорости охлаждения ЗТВ (рис . 4)
Из приведенных данных видно, что при ув е личении толщины стенки труб свыше 23 мм ск о рость охлаждения опускается ниже 10 °С, следова тельно, происходит резкое снижение вязких свойств в ЗТВ.
Исходя из вышесказанного, следует, что для обеспечения эксплуатационной надежности толстостенных труб большого диаметра необходимо вносить кардинальные изменения в технологию сварки, позволяющие существенно снизить погонную энергию, или разработать химический состав основного металла, менее чувствительного к термическому циклу сварки.
С целью разработки химического состава стали, обладающей высокими вязкими свойствами, в ЗТВ после сварки был выполнен эксперимент по оценке влияния различных легирующих элементов на вязкие свойства в ЗТВ сварных соединений труб большого диаметра. В ходе выполнения эксперимента было выплавлено четырнадцать сталей с различным химическим составом. Химический состав сталей представлен в таблице. Химический состав выбирался таким образом, чтобы оценить влияние отдельных химических элементов. Содержание микролегирующих элементов во всех сталях одинаково: Nb – 0,04 % и Ti – 0,01 % [3].
Из выплавленных сталей были прокатаны полосы толщиной 30 мм по режимам контролируемой прокатки. Затем была произведена сварка этих пластин с погонной энергией 6,5–7,0 кДж/мм, после чего произведена оценка механических свойств основного металла и сварного соединения. Результаты испытаний на растяжение цилиндрических образцов, вырезанных поперек направления прокатки, представлены на рис. 5.
Значительного различия предела текучести у обыкновенной стали А и стали Б со сниженным содержанием кремния не наблюдается, хотя снижение содержания кремния привело к снижению временного сопротивления. Снижение содержания углерода с 0,09 до 0,06 % привело к падению временного сопротивления ниже минимального тре-
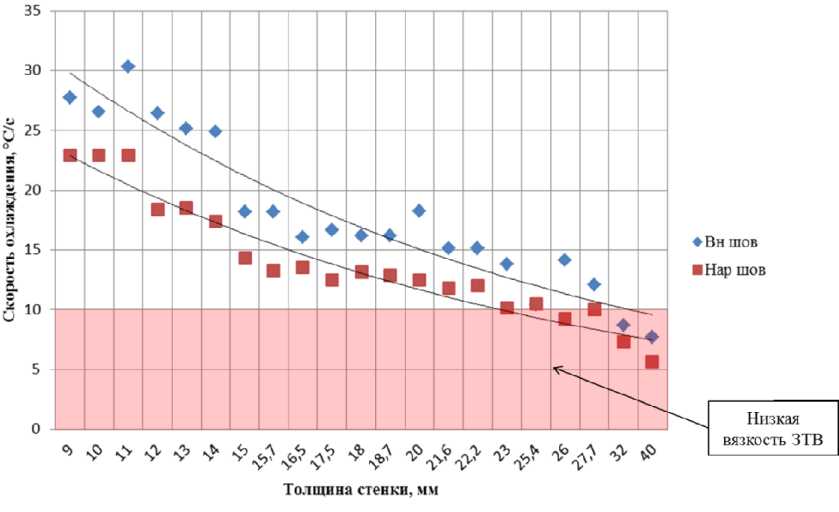
Рис. 4. Зависимость скорости охлаждения ЗТВ от толщины стенки свариваемых труб
Химический состав сталей, выплавленных в ходе эксперимента
Сталь |
Содержание х имических элементов , % |
||||||||
C |
Si |
Mn |
Cu |
Cr |
Ni |
Mo |
CE(IIW) |
Pcm |
|
А |
0,09 |
0,3 |
1,6 |
– |
– |
– |
– |
0,38 |
0,19 |
Б |
0,09 |
0,1 |
1,6 |
– |
– |
– |
– |
0,37 |
0,17 |
В |
0,06 |
0,1 |
1,6 |
– |
– |
– |
– |
0,34 |
0,15 |
Г |
0,06 |
0,1 |
1,6 |
0,20 |
– |
0,25 |
– |
0,37 |
0,16 |
Д |
0,06 |
0,1 |
1,6 |
0,40 |
– |
0,50 |
– |
0,41 |
0,18 |
Е |
0,06 |
0,1 |
1,6 |
– |
0,20 |
– |
– |
0,37 |
0,15 |
Ж |
0,06 |
0,1 |
1,6 |
– |
0,30 |
– |
– |
0,39 |
0,16 |
З |
0,06 |
0,1 |
1,6 |
0,20 |
0,30 |
0,25 |
– |
0,42 |
0,17 |
И |
0,06 |
0,1 |
1,8 |
– |
– |
– |
– |
0,38 |
0,16 |
К |
0,06 |
0,1 |
1,8 |
0,12 |
– |
0,17 |
– |
0,40 |
0,17 |
Л |
0,06 |
0,3 |
1,8 |
0,21 |
– |
0,24 |
– |
0,42 |
0,18 |
М |
0,06 |
0,1 |
1,8 |
0,12 |
– |
0,17 |
0,15 |
0,40 |
0,17 |
Н |
0,06 |
0,1 |
1,8 |
– |
0,20 |
– |
0,11 |
0,42 |
0,17 |
П |
0,04 |
0,1 |
1,7 |
0,21 |
– |
0,26 |
– |
0,38 |
0,15 |
Р |
0,04 |
0,1 |
2 |
0,12 |
– |
0,18 |
0,16 |
0,45 |
0,17 |
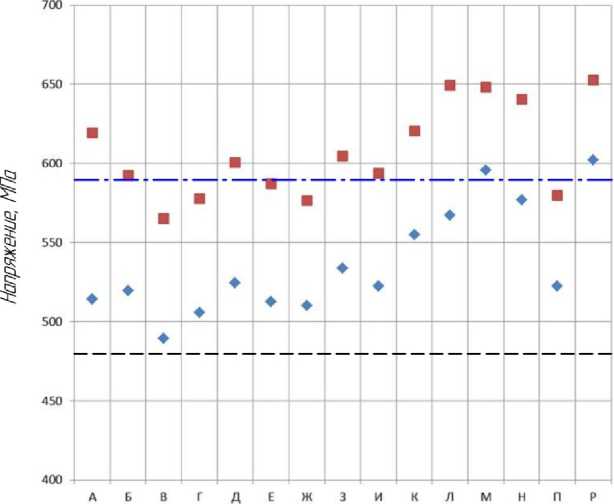
Временное сопротивление
♦ Предел текучести
----Минимальный предел текучести для стали К60
---Минимальное Временное сопротивление для стали К60
Рис. 5. Предел текучести и временное сопротивление листов из сталей, выплавленных в ходе эксперимента буемого значения для стали К60. Потерю прочности можно компенсировать за счет добавок меди и никеля в химический состав стали, что показано результатами испытаний сталей Г и Д. Также повышение прочностных свойств может быть достигнуто за счет добавления хрома (стали Е и Ж). Достижение требуемых прочностных свойств для стали класса прочности К60 может быть достигнуто совместным легированием никелем, медью и хромом (сталь З). Также значительно увеличить прочностные свойства стали можно за счет увеличения содержания марганца до 1,8 % (стали И и К). Незначительное содержание молибдена в химическом составе стали (порядка 0,15 %) приводит к существенному повышению как предела текучести, так и временного сопротивления (стали М и Н).
Рассмотрен вариант снижения содержания углерода до уровня 0,04 % (стали П и Р). В случае стали П, не содержащей молибдена, произошло существенное снижение прочностных свойств.
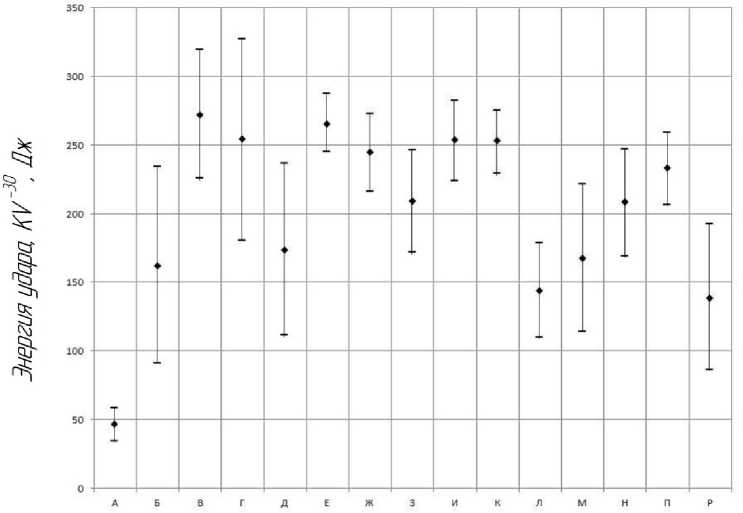
Рис. 6. Ударная вязкость образцов с надрезом 50/50 по линии сплавления сварных соединений экспериментальных сталей
В стали Р с повышенным до 2,0 % содержанием марганца и легированной медью, никелем и молибденом достигнуты прочностные свойства уровня стали М.
Средние значения ударной вязкости ЗТВ сварных соединений экспериментальных сталей при температуре испытаний –30 °С представлены на рис. 6.
Наименьшей ударной вязкостью ЗТВ обладает сталь А, не оптимизированная для конструкций, эксплуатируемых при низких температурах, с содержанием углерода 0,09 % и кремния 0,03 %. Снижение содержания кремния приводит к существенному повышению вязких свойств ЗТВ (сталь А). Еще большее повышение ударной вязкости наблюдается при снижении содержания углерода до 0,06 % (сталь В). Результаты испытаний стали Г показывают, что небольшие добавки меди и никеля не приводят к существенному снижению среднего значения ударной вязкости в ЗТВ сварных соединений. Большие добавки меди и никеля могут привести к снижению ударной вязкости (сталь Д). Стали И и К показывают, что увеличение содержания марганца до уровня 1,8 % не оказывает негативного влияния на вязкие свойства ЗТВ сварных соединений. Дополнительное легирование сталей молибденом (стали М и Р) приводит к сильному снижению вязких свойств ЗТВ сварных соединений.
Оценка влияния ванадия на вязкие свойства ЗТВ сварных соединений труб большого диаметра приведена в [2]. Авторы проводили эксперименты на двух сталях класса прочности К60, микролеги-рованных ниобием и ниобием и ванадием.
Введение в ниобийсодержащую сталь ванадия приводит к снижению устойчивости аустенита в результате смещения всей термокинетической диаграммы в сторону больших скоростей охлаждения. При наличии температурно-временных условий микролегирующие элементы Nb и V могут вывести из твердого раствора и связать в стойкие карбиды около 0,01–0,02 % углерода. Причем коэффициент активности ванадия почти в два раза выше коэфициента активности ниобия (kNb = 0,59; kv = 1,1). Таким образом, введение в ниобийсодержащую сталь ванадия приводит к выделению карбидной фазы и обеднению твердого раствора по углероду, что в свою очередь вызывает снижение устойчивости аустенита.
Для оценки вязких свойств ЗТВ исследуемых сталей использовали образцы с имитированными термическими циклами сварки. Наблюдаются существенные отличия вязких свойств исследуемых сталей. Уровень вязких свойств в ЗТВ у стали, легированной Nb +V, значительно ниже, чем у стали, легированной Nb, при этом область оптимальных скоростей охлаждения смещена в сторону более высоких скоростей охлаждения, что неблагоприятно для сварки толстостенных труб.
Заключение
Сварные соединения труб большого диаметра обладают значительной неоднородностью вязких свойств. Наибольший провал вязких свойств наблюдается в области крупного зерна ЗТВ, что связано со значительными структурными изменениями в данной области сварного соединения.
Вязкость области крупного зерна ЗТВ зависит от скорости охлаждения после сварки. Наблюдается резкое снижение вязких свойств в этой области с понижением скорости охлаждения ниже 10 °С. При сварке труб с толщиной стенки свыше 23 мм скорость охлаждения ЗТВ опускается ниже критической, что приводит к существенному охрупчиванию ЗТВ, и, следовательно, к снижению эксплуатационной надежности труб большого диаметра.
Проведенные исследования показали, что вязкие свойства ЗТВ сварных соединений труб большого диаметра зависят от химического состава основного металла труб. С целью разработки химического состава стали, менее чувствительной к термическому циклу сварки, обладающей довольно высокими вязкими свойствами в ЗТВ, были проведены исследования по оценке влияния отдельных химических элементов на ударную вязкость сварных соединений. Показано негативное влияние кремния и молибдена на вязкие свойства в ЗТВ. Дополнительное легирование стали ванадием также приводит к значительному охрупчиванию области крупного зерна ЗТВ.
Для достижения высоких вязких свойств сварных соединений труб большого диаметра необходимо:
– исключить ванадий из химического состава стали;
– снизить содержание кремния до уровня 0,1 %;
– легирование молибденом должно осуществляться на минимальном уровне для достижения требуемых прочностных свойств.
Список литературы Влияние химического состава основного металла на вязкие свойства зоны термического влияния электросварных труб большого диаметра
- Особенности многоэлектродной сварки под слоем флюса при производстве высокопрочных толстостенных труб/А.Н. Борцов, И.П. Шабалов, А.А. Величко и др.//Металлург. -2013. -№ 4. -С. 69-76.
- Сравнение свариваемости высокопрочных трубных сталей, микролегированных ниобием, ниобием и ванадием/А.В. Назаров, Е.В. Якушев, И.П. Шабалов и др.//Металлург. -2013. -№ 10. -С. 56-61.
- Effect of base metal composition on the toughness in the heat affected zone of DSAW-welded largediameter linepipes/C. Stallybrass, O. Dmitrieva, J. Schroder, A. Liessem//Ostend, 6th International Pipeline Technology Conference. -2013. -Paper no. S26-02.