Влияние количества и дисперсности золы на формирование структуры и свойства цементного камня
Автор: Махмудов Азамджон Махмудович, Трофимов Борис Яковлевич, Гафоров Фазлиддин Абдухалимович
Рубрика: Строительные материалы и изделия
Статья в выпуске: 4 т.21, 2021 года.
Бесплатный доступ
Экологические вопросы требуют большого внимания со стороны общественности и экологических организаций. Зола - мелкая, состоящая преимущественно из шарообразных стекловидных частиц, образующаяся при сжигании мелко молотого угля и обладающая пуццолановыми свойствами и/или гидравлической активностью. Использование золы в производстве бетона представляет экономичный и экологический способ ее утилизации по сравнению с доменным граншлаком, также распространенной пуццолановой добавкой, золу не нужно гранулировать и размалывать. В этой статье рассмотрена замена части портландцемента отвальной и дополнительно измельченной золой. Уменьшение размера частиц золы приводит к увеличению площади поверхности, в то время как добавление в качестве частичной замены цемента улучшает прочность, долговечность и микроструктурные характеристики цементного камня. Представлены результаты определения физико-химических характеристик цементного камня с различным зольным замещением.
Зола, цементный камень, пуццолан, прочность, структура гидратных фаз
Короткий адрес: https://sciup.org/147236596
IDR: 147236596 | DOI: 10.14529/build210405
Текст научной статьи Влияние количества и дисперсности золы на формирование структуры и свойства цементного камня
Бетон – это основной строительный материал, который будет пользоваться спросом и в будущем, производится с применением в основном цементов типа ЦЕМ I и ЦЕМ II. Каждая тонна произведенного портландцемента приводит к выбросу в атмосферу в среднем одинакового количества CO2 – около 6 % всех антропогенных выбросов углерода, что вредно для окружающей среды [1–4].
Следовательно, бетон должен быть изготовлен с минимальным количеством цемента, насколько это возможно и практично. Это может быть достигнуто путем замены части цемента пуццолановыми материалами (промышленными побочными продуктами) тепловых электростанций и металлургической промышленности, особенно золой уноса и доменным шлаком.
Несмотря на растущее значение возобновляемых источников энергии (геотермальной, ветровой и солнечной энергии), доля угля в мировом энергетическом балансе продолжает расти. Поэтому мировое производство угольной золы увеличивается и существует настоятельная необходимость ее переработки и утилизации [5, 6].
В процессах слоевого или факельного сжигания углей на ТЭС образуются газообразные продукты и твердые золошлаковые отходы – золы (размер частиц менее 0,315 мм) и шлаки. Это продукты высокотемпературной (1200–1700 °С) переработки минеральной части топлива [7–9].
Зола состоит в основном из SiO 2 , но может также содержать значительные количества Al 2 O 3 . Количество CaO ограничено, но сильно варьируется в зависимости от происхождения летучей золы [10].
Когда зола используется в сочетании с портландцементом, гидроксид кальция, выделяющийся при гидролизе силикатов кальция портландцемента, вступает в реакцию с алюмосиликатным стеклом, присутствующим в золе, с образованием цементных соединений, обладающих когезионными и адгезионными свойствами. Продукты этих реакций, гидросиликаты кальция, зависят от времени, но в основном имеют тот же тип и характеристики, что и продукты гидратации цемента. Однако пуц-цолановые реакции протекают намного медленнее, чем реакции гидратации цемента [11–14].
Пуццоланы снижают количество гидроксида кальция в цементном камне за счет образования вторичного геля гидрата силиката кальция (CSH) с более низким отношением Ca/Si [15, 16].
Зола может сильно различаться по своим физическим и химическим характеристикам, поэтому контроль качества особенно важен. Необходимо проверять содержание углерода и степень кристалличности [17].
Некоторые из преимуществ бетона на ЦЕМ I с добавкой золы включают улучшенную обрабатываемость, пониженную проницаемость, повышенную предельную прочность, лучшую поверхность и пониженную теплоту гидратации.
Зола в целом очень неоднородна, состоит из смеси стекловидных частиц с различными идентифицируемыми кристаллическими фазами, такими как кварц, муллит и различные оксиды железа. Однако медленное развитие прочности на начальном этапе ограничивает ее дальнейшее применение в области гражданского строительства в качестве хорошего экологически чистого материала.
В своих исследованиях Мехта [18] п роверил 11 видов летучей золы из разных источников и обнаружил, что содержание кальция и грануло метрический состав являются решающими параметрами, определяющими скорость развития прочности.
Увеличение степени измельчения золы также увеличивает ее пуццолановую активность и плотность цементного камня. Это положительно сказывается на прочности и долговечности бетонов, содержащих золу [19].
Замена цемента исходной золой уменьшает размеры пор цементной пасты, а включение измельченной золы приводит к дальнейшему уменьшению размеров пор цементного камня [20]. Исследования показывают, что чем меньше размер частиц золы, тем выше ее активность и скорость гидратации.
Материалы и методы исследования
На кафедре «Строительные материалы и изделия» ЮУрГУ проведены исследования с целью изучения влияния количества золы на формирование структуры и свойств цементного камня.
В этом исследовании использовались:
-
– портландцемент 52,5Н производства «Дюк-керхофф Коркино цемент» с истинной плотностью 3,1 г/см3, НГ = 28,2 %;
-
– отвальная зола Троицкой ГРЭС. Химический состав материалов показан в табл. 1;
– вода, соответствующая ГОСТ 23732–2011.
Портландцемент имеет следующий минералогический состав: С3S – 64,2 %; С2S – 10,0 %; С3А – 6,3 %; С 4 АF – 14,1 %.
Тонкость помола, нормальную густоту и сроки схватывания цемента и золы определяли согласно ГОСТ 310. 2,3-81.
Для замены части портландцемента использовали 10, 20, 30 и 40 % исходной и дополнительно измельченной золы от массы вяжущего. Нормальная густота (НГ) цементного теста составляет 28,2 %, при увеличении количества исходной золы до 30 % НГ уменьшается до 27,4 %. Цементные пасты с измельченной золой имеют нормальную густоту от 29,5 % до 31,0 %, увеличивающуюся с повышением дисперсности измельченной золы в смеси.
Шаровая мельница использовалась для уменьшения размера частиц золы за счет ударов и истирания с использованием стальных шаров.
Из смеси ЦЕМ I и золы готовили тесто нормальной густоты и формовали образцы – кубики с ребром 20 мм. Образцы выдерживали в нормальных условиях твердения при температуре 20 ± 2 °С и влажности более 95 %. Испытания на прочность при сжатии проводили по ГОСТ 10180-2012 в возрасте 28, 42, 56 и 90 суток.
При подготовке проб к термоанализу для остановки процесса гидратации и карбонизации цементного камня образцы предварительно обрабатывали этиловым спиртом, дополнительно высушивали при 60 °C в течение 24 часов и измельчали в ступке для прохождения через сито 80 мкм [21].
Содержание Ca(OH)2 в гидратированных цементных пастах определяли термогравиметрическим анализом (ТГА).
В этом исследовании рентгенофазовый анализ был использован для изучения минералогического состава образцов цементного камня с добавками в возрасте 90 суток.
Результаты
Как правило, зола снижает прочность в раннем возрасте, однако значение Rсж увеличивается в более позднем возрасте.
Согласно полученным данным (табл. 2), прочность цементного камня в основном зависит от сроков твердения, количества и дисперсности золы. Результаты исследования показывают, что через 28 и 42 суток нормального твердения прочность цементного камня с золой ниже, чем беззольного. После 56 суток прочность цементного камня с заменой 10 и 20 % золой выше, чем без неё, и при 30–40%-ной замене приближается к прочности контрольных образцов. Прочность цементного камня без золы в возрасте 90 суток нормального твердения составила 97,6 ± 2,7 МПа, а максимальное значение до 100 ± 3 МПа выявлено при 20 %. При 30%-ной замене получено 98,5 ± 2,3 МПа, что ниже максимального и выше беззольного. Однако при 40%-ной замене получено минимальное значение прочности 84,3 ± 3,7 МПа.
Прочность цементного камня с измельченной золой превышает прочность беззольного цемент-
Таблица 1
Химический состав портландцемента и золы
Материалы |
Содержание оксидов, % масс. |
|||||||
SiO 2 |
Al 2 O 3 |
Fe 2 O |
CaO |
MgO |
Na2O |
SO 3 |
ппп |
|
ЦЕМ I |
19,9 |
5,1 |
4,5 |
63,2 |
1,6 |
0,5 |
3,0 |
0,9 |
Зола |
62,53 |
28,75 |
4,1 |
7,64 |
2,61 |
2,35 |
0,2 |
0,61 |
Строительные материалы и изделия ного камня в возрасте 42 суток при 20%-ной замене, а в 56 суток – при 30%-ной. В 90 суток при замене цемента на 40 % измельченной золой значение прочности уравнивается с прочностью контрольного.
Значительное повышение прочности на сжатие цементного камня с золой объясняется высокой пуц-цолановой активностью золы и ее способностью выполнять функции микронаполнителя (см.табл. 2).
Коэффициент вариации прочности образцов составляет менее 5 %.
Развитие прочностных характеристик образцов кубиков портландцемента с различной дозировкой золы показано на рис. 1.
Результаты показывают, что замена части цемента золой снижает прочность цементного камня в раннем возрасте по сравнению с контрольными образцами. Однако в более позднем возрасте образцы либо набрали высокую прочность, либо очень приблизились к прочности контрольных образцов цементного камня. Образцы с 20 и 30 % золы показали более высокий прирост прочности, чем с 40 % золы. Прочность цементного камня с измельченной золой нарастала быстрее, чем у контрольного.
Непрерывная гидратация цемента приводит к постоянному увеличению содержания Ca(OH) 2 , но пуццолановая реакция золы поглощает некоторое количество Ca(OH)2. Согласно полученным результатам по данным дифференциального термического анализа (ДТА) (рис. 2, 3), замена части цемента золой в возрасте 90 суток нормального твердения снижает количество портландита. При замене 30 % исходной золой содержание Ca(OH) 2 в цементном камне снижается до 7,03 % по сравнению с контрольным составом без золы – до 9,95 %. При замене 40 % цемента измельченной золой снижается количество портландита до 4,07 %. Это указывает на то, что пуццолановая активность измельченной золы выше, чем у исходной золы, и что измельченная зола оказывает более значительное влияние на гидратацию цемента. Также на дериватограммах при температуре 830–860 °C наблюдается экзотермический эффект, свидетельствующий об образовании слабо-закристаллизованной фазы C-S-H (I). Эндотермический пик примерно при 920–950 °C на кривых ДТА вызван разложением небольшого количества CaCO 3 .
Таблица 2
Прочностные характеристики цементного камня
Состав образцов |
НГ |
Прочность цементного камня, МПа |
|||||
Цемент, % |
Зола, % |
Зола молотая, % |
28 сут |
42 сут |
56 сут |
90 сут |
|
100 |
– |
– |
28,2 |
92,15 |
94,18 |
94,88 |
97,63 |
90 |
10 |
– |
28,2 |
89,27 |
92,65 |
95,78 |
98,72 |
80 |
20 |
– |
28,0 |
80,97 |
90,88 |
94,42 |
100 |
70 |
30 |
– |
27,5 |
77,64 |
89,0 |
91,8 |
98,42 |
60 |
40 |
– |
28,5 |
70,22 |
73,95 |
76,0 |
84,35 |
90 |
– |
10 |
29,5 |
91,81 |
94,53 |
99,13 |
100,33 |
80 |
– |
20 |
30,0 |
91,5 |
94,45 |
100,77 |
101,2 |
70 |
– |
30 |
30,5 |
90,77 |
91,78 |
98,82 |
102,42 |
60 |
– |
40 |
31,0 |
83,77 |
85,0 |
86,28 |
96,83 |
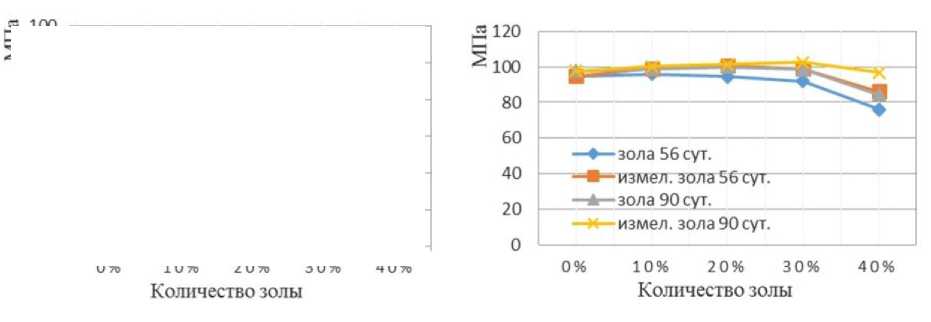
а)
б)
Рис. 1. Развитие прочности при сжатии цементного камня без и с заменой части портландцемента золой: а – в возрасте 28 и 42 сут с отвальной и дополнительно измельченной золой; б – в возрасте 56 и 90 сут с отвальной и дополнительно измельченной золой
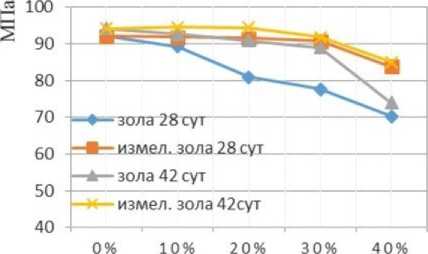
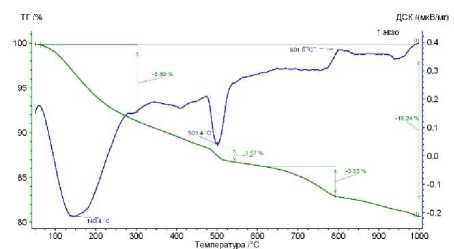
а)
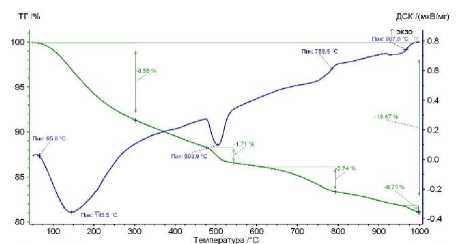
в)
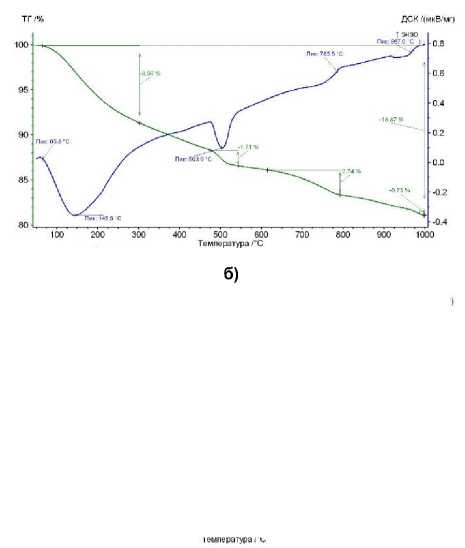
г)
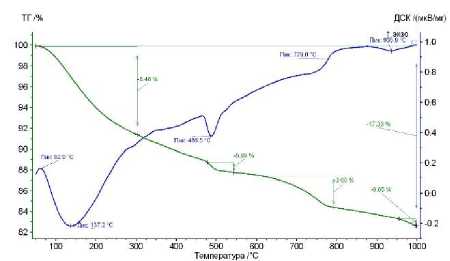
Рис. 2. Дериватография цементного камня без золы (а), 30 % зола (б), 30 % измельченная зола (в) и 40 % измельченная зола (г)
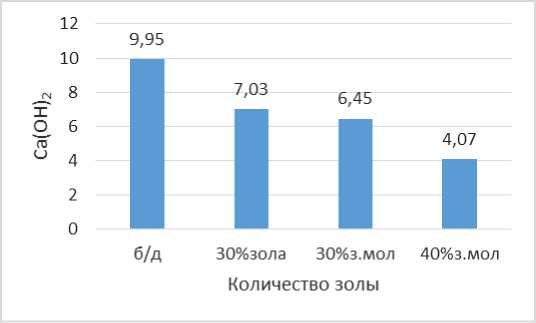
Рис. 3. Влияние количества и дисперсности золы на содержание портландита в цементном камне
Гель C-S-H не только является наиболее распространенным продуктом гидратации, но также отвечает за многие важные свойства цементного камня и, следовательно, за бетон в целом. Это наиболее плотная фаза, которая склеивает продукты гидратации и зерна заполнителя, придавая материалу плотность и прочность. Другие продукты гидратации, например, Ca(OH) 2 , образуют прочные отдельные твердые кристаллы, которые не вносят большого вклада в прочность материалов.
Рентгенофазовый анализ подтверждает, что структура цементного камня без и с золой представлена слабозакристаллизованными гидросиликатами C–S–H(I) 12,5; 3,032; 2,09; 1,52 нм, C–S–H(II) 9,8; 4,92; 3,032; 2,883; 2,09; 1,728 нм,
Ca(OH) 2 4,92; 3,115; 2,63; 1,926; 1,796; 1,688; 1,485 нм, С 5 S 6 H 5 2,747; 2,544; 2,186; 1,926; 1,76; 1,523; 1,36 нм.
Рентгенограмма образцов цементного камня и с добавлением золы в возрасте 90 суток представлена на рис. 4–6.
Пики интенсивности Ca(OH) 2 появляются при 18,07; 28,75; 34,13; 47,12 и 50,85 градуса. Замена цемента измельченной золой более эффективно снижает интенсивность Ca(OH) 2 , чем исходная зола. Хорошо известно, что снижение Ca(OH) 2 зависит от степени пуццолановой реакции. Факторами, влияющими на пуццолановую реакционную способность, являются дисперсность и содержание стеклообразной фазы в золе. Более мелкая зола
Строительные материалы и изделия
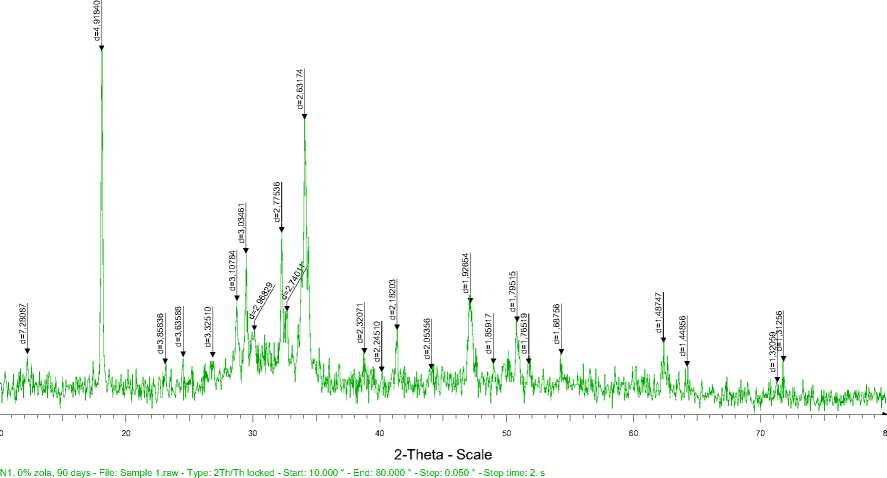
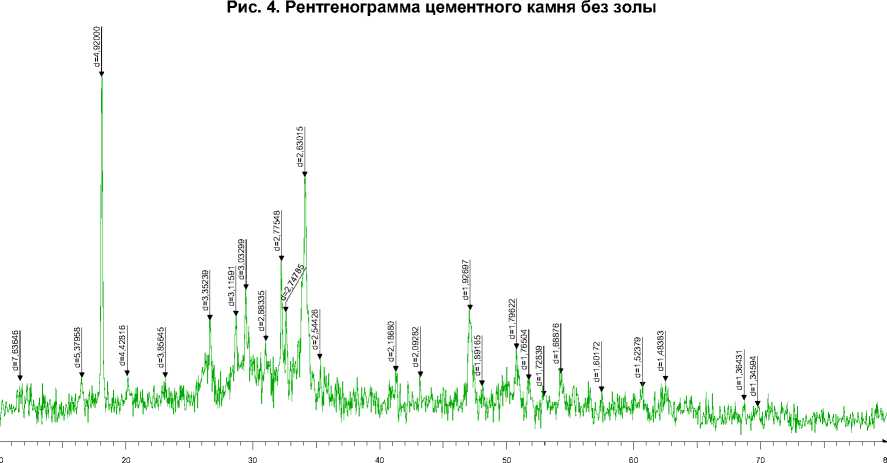
2-Theta - Scale
N2, 30% zola, 90 days - File: Sample 2.raw - Type: 2Th/Th locked - Start: 10.000 ° - End: 80.000 ° - Step: 0.050 ° - Step time: 3. s
Рис. 5. Рентгенограмма цементного камня с заменой 30 % цемента золой
имела большую площадь поверхности и повышенную пуццолановую реакционную способность, чем исходная зола.
Выводы
На основе полученных экспериментальных результатов можно сделать следующие выводы.
Замена части портландцемента золой снижает водопотребность цемента и прочность при сжатии цементного камня в раннем возрасте. При 30%-ной замене цемента золой в возрасте 90 суток нормального твердения прочность цементного камня превышает прочность контрольных образ- цов (без замены цемента золой), а при 30%-ной замене цемента измельченной золой прочность выше чем у беззольного образца начиная с 56-суточного возраста.
Замена части цемента золой снижает количество Ca(OH)2 из-за пуццолановой реакции и повышает содержание цементного геля - низкоосновного гидросиликата кальция (C-S-H), что увеличивает прочность, плотность, водонепроницаемость и в целом долговечность цементного камня и бетона.
Благодаря оптимизационной роли измельченной золы процесс гидратации цемента ускоряется,
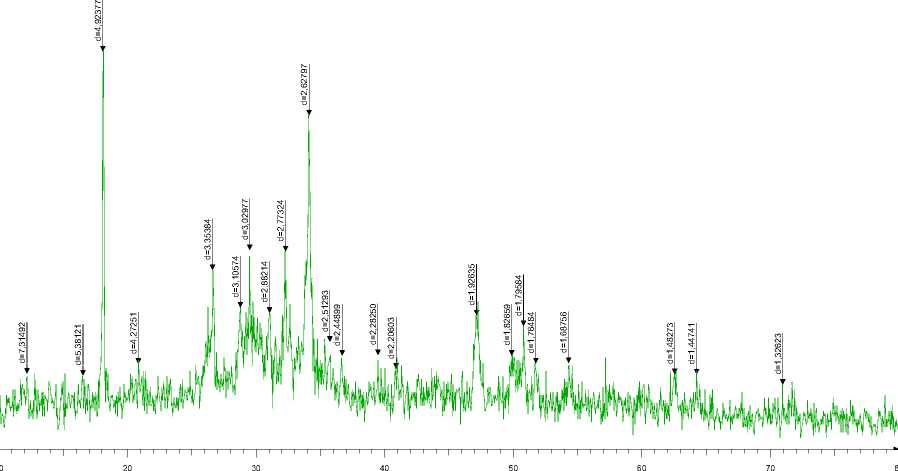
2-Theta - Scale
30% zola molotaya, 90 days - File: Sample 3.raw - Type: 2Th/Th locked - Start: 10.000 ° - End: 80.000 ° - Step: 0.050 ° - Step time: 3. s
Рис. 6. Рентгенограмма цементного камня с заменой 30 % цемента измельченной золой
а количество, однородность и плотность продуктов гидратации повышаются.
Исходя из полученных результатов, дисперсность и количество золы, замещающей ЦЕМ I, оказывают значительное влияние на структуру и свойства цементного камня.
Список литературы Влияние количества и дисперсности золы на формирование структуры и свойства цементного камня
- Benhelal, E. Green cement production: potentials and achievements / E. Benhelal, A. Rafiei, E. Shamsaei // International journal chemical engineering. - 2012. - Vol. 3. - P. 407-409.
- IEA, Technology Roadmap - cement. - 2018 https://www.iea. org/reports/technology-roadmap-low-carbon-transition-in-the-cement-industry.
- Shihwen Hsu. Effect of fineness and replacement ratio of ground fly ash on properties of blended cement mortar / Shihwen Hsu, Maochieh Chi, Ran Huang // Construction and Building Materials. -2018. - Vol. 10. - P. 250-258.
- Технология получения бикарбоната аммония при утилизации выбросов углекислого газа цементной промышленности России и Украины / Г.Р. Мингалеева, И.В. Дмитриенко, А.И. Здоров и др. // Современные проблемы науки и образования. - 2013. - № 5.
- Franus, W. Coal fly ash as a resource for rare earth elements / W. Franus, M.M. Wiatros-Motyka, M. Wdowin, // Environmental Science and Pollution Research. - 2015. - Vol. 22. - P. 9464-9474. DOI: 10.1007/s11356-015-4111-9
- Худякова, Л.И. Использование золошлако-вых отходов тепловых электростанций. XXI век / Л.И. Худякова, А.В. Залуцкий, П.Л. Палеев // Техно-сферная безопасность. - 2019. - № 4. - С. 290306.
- Панибратов, Ю.П. К вопросу применения зол ТЭС в бетонах /Ю.П. Панибратов, В.Д. Староверов // Технологии бетонов. - 2011. - № 1-2. -С. 43-47.
- Адеева, Л.Н. Зола ТЭЦ перспективное сырье для промышленности / Л.Н. Адеева, В. Ф. Бор-бат // Вестник Омского университета. -2009. -№ 2. - С. 141-145.
- Фоменко, Н.А. Применение окисленных бурых углей для повышения экологической безопасности утилизации золошлаковых отходов: дис. ... канд. техн. наук / Н.А. Фоменко. - М., 2019.
- Navdeep, S. Reviewing the role of coal bottom ash as an alternative of cement / S. Navdeep, Shehnazdeep, B. Anjani // Construction and Building Materials. - 2020. - Vol. 233. - P. 117276.
- Joshi, R.C. Fly Ash - Production, Variability and Possible Complete Utilization / R.C. Joshi // Indian Geotechnical Conference. - 2010. - P. 16-18.
- Коровкин, М.О. Высокопрочные бетоны с высоким содержанием золы Канско-Ачинского буроугольного бассейна /М.О. Коровкин, А.В. Петухов // Инженерный вестник Дона. - 2017. -№ 1. - С. 106-112.
- Siddique, R. Supplementary Cementing Materials, Engineering Materials / R. Siddique, M.I. Khan. - Springer-Verlag, Berlin Heidelberg, 2011. - 297p. DOI: 10.1007/978-3-642-17866-5 1.
- Волженский, А.В. Минеральные вяжущие вещества: (технология и свойства) / А.В. Волженский, Ю.С. Буров, В.С. Колокольников. - М.: Строй-издат. 1979. - 476 с.
- Lothenbach, B. Supplementary cementitious materials / B. Lothenbach, K. Scrivener, R.D. Hooton // Cement and Concrete Research. - 2011. - Vol. 41. -P. 1244-1256.
- Парфенова, Л.М. Применение зол тепловых электростанций в бетонах / Л.М. Парфенова // Вестник Полоцкого государственного университета. Серия F. - 2013. - № 16. - С. 68-72.
- Mohammad, Sh.A. Effects of systematic increase of pozzolanic materials on the mechanical, durability, and microstructural characteristics of concrete: A thesis submitted for the degree of doctor of philosophy / Sh.A. Mohammad. - Canberra, 2007.
- Mehta, P.K. Influence of fly ash characteristics on the strength of portland-fly ash mixtures /P.K. Mehta // Cement and Concrete Research. - 1985. -Vol. 15 (4). -P. 669-674.
- Semsi, Y. Effects of fly ash fineness on the mechanical properties of concrete / Y. Semsi, S.A. Hasan // Sadhana - Indian Academy of Sciences. - 2012. - Vol. 37. Part 3. - P. 389-403.
- Properties of cements and concretes containing fly ash / R.E. Davis, R. Carlson, J.W. Kelly, H. Davis // Journal of the American Concrete Institute. - 2008. - Vol. 33 (5). - P. 577-611.
- Горшков В.С. Методы физико-химического анализа вяжущих веществ / В.С. Горшков, В.В. Тимашев, В.Г. Савельев. - М.: Высшая школа. 1981. - 335 с.