Влияние механоактивации на стабилизацию свойств золы уноса красноярских ТЭЦ
Автор: Енджиевская И.Г., Василовская Н.Г., Дубровская О.Г., Баранова Г.П., Чудаева А.А.
Журнал: Журнал Сибирского федерального университета. Серия: Техника и технологии @technologies-sfu
Статья в выпуске: 7 т.11, 2018 года.
Бесплатный доступ
В данной статье анализировался генезис техногенного продукта, определяющий его состав, структуру, состояние, свойства. Рассматривалась возможность использования техногенных отходов Красноярских ТЭЦ в производстве строительных материалов. Показано, что значительные колебания в химическом составе и строении золы ТЭЦ-2 обусловливают необходимость дополнительного воздействия на нее в целях стабилизации состава и свойств, а также для предотвращения негативного влияния СаОсвоб., вызванного поздними сроками гидратирования из-за стекловидной поверхностной оболочки. Для снятия опасности деструктивных процессов в продуктах твердения строительных материалов на основе золы путем нейтрализации свободного оксида кальция, как первопричины дефектов структуры камня, стабилизации состава золы и возможности использования ее в качестве наполнителя в цементных композициях (бетонах, растворах) целесообразно активировать ее в гидродинамическом диспергаторе. Изучение фазового состава продуктов твердения бесцементных составов на основе золы показало, что после активации он более однородный, с малым количеством отражений, что свидетельствует о большей гомогенности и стабильности структуры. Повышение прочностных характеристик связано в том числе с равномерностью изменения объема активированной золы.
Золы красноярских тэц, химический состав, минералогический состав, фазовый состав, физико-механические свойства, кавитация, гидродинамический диспергатор, прочность при изгибе, прочность при сжатии
Короткий адрес: https://sciup.org/146279552
IDR: 146279552 | DOI: 10.17516/1999-494X-0099
Текст научной статьи Влияние механоактивации на стабилизацию свойств золы уноса красноярских ТЭЦ
В последние годы экологические проблемы приобретают все большую актуальность и являются предметом многих современных научных исследований. К ним относятся: изменение климата под воздействием выбросов парниковых газов в результате сжигания органического топлива, истощение озонового слоя, кислотные дожди, накопление отходов и загрязнение окружающей среды тяжелыми металлами, органическими соединениями [1]. Топливно-энергетический комплекс создает многие экологические проблемы современности. В России около 70 % выбросов углекислого газа в атмосферу осуществляют предприятия энергетической отрасли [2]. Основным видом промышленных отходов, занимающих одно из первых мест по объему выхода и представляющих серьезную экологическую опасность, являются золы уноса [5].
Ведущим направлением обеспечения экологической безопасности является поэтапное сокращение уровня негативного воздействия на окружающую среду отходов топливноэнергетического комплекса. Значительная площадь земель, отведенная под золошлаковые отходы, безвозвратно изымается из полезного использования, консервация их требует значительных затрат. Токсичные вещества, содержащиеся в золах уноса, такие как SO3, при взаимодействии с влагой воздуха могут образовывать сильные кислоты, которые приводят к коррозии эксплуатируемых строительных конструкций, загрязнению почв, грунтовых и поверхностных – 843 – вод, воздушного бассейна, представляя угрозу для окружающей среды. Агрессивные вещества, попадая в организм человека по трофическим цепям, вызывают широкий спектр тяжелейших заболеваний.
Использование золошлаковых отходов позволяет сократить их накопление и снизить нагрузку на окружающую среду. Поскольку промышленность строительных материалов является наиболее материалоемкой, то глобальное использование отходов связано именно с этой отраслью [5]. Все большее применение находит сухая зола уноса с электрофильтров ТЭЦ, получившая всеобщее признание как материал, имеющий важное значение в качестве добавки к различным бетонам, строительным растворам, керамике, тепло- и гидроизоляционным материалам [6-13].
Рассматривая данную проблему на примере г. Красноярска, где главным источником энергии служат топливосодержащие ископаемые – бурые угли, наибольшая доля произведенной тепловой энергии и, следовательно, количество отходов приходятся на ТЭЦ-1, ТЭЦ-2 и ТЭЦ-3, расположенные в черте города. Количество топлива (угля), израсходованного на получение тепловой и электрической энергии в 2007 г., представлено в табл. 1 [3, 4].
Таким образом, в год сжигается около 5 млн т угля и при этом образуется около 500 тыс. т золы и шлака.
В настоящее время в России имеется значительное количество научных разработок в части использования попутных продуктов производства для повышения качества строительных материалов. В направлении расширения сырьевой базы для производства бетонов, растворов, сухих строительных смесей работают Ю.М. Баженов, М.Н. Мороз, В.И. Калашников, И.В. Ерофеева, Ш.Н. Иохан [15-20].
Пригодность золы для изготовления вяжущих и бетонов устанавливают путем опытной проверки химического состава и содержания вредных примесей, к которым относятся несгоревшие топливо, сера, оксид кальция и магния [21-25].
Систематизацией исследований по таким видам материалов занимаются ведущие институты страны, такие как МГСУ, НИИЖБ, ЦНИИС, ВНИИСтром. Активно работают в этом направлении как российские, так и зарубежные ученые [23-27], в том числе над проблемами стабилизации структуры золы уноса [26-28].
Как показывает практика технической и технологической эксплуатации зданий и сооружений, увеличение срока службы напрямую связано с восстановлением функциональных качеств отдельных конструктивных элементов, особенно первой степени ответственности,
Таблица 1. Расход угля крупнейшими ТЭЦ г. Красноярска в 2007 г.
Table 1. Сoal сonsumption by the largest CHP systems in Krasnoyarsk in 2007
В строительном материаловедении получили развитие теории конструирования структур композитов с использованием техногенных отходов с разработкой принципов и методологии экспериментального моделирования материалов с управляемыми свойствами и оптимизированной структурой [22-29].
Однако применение золы имеет ряд технологических проблем, из-за чего производство строительных материалов с использованием зол уноса, особенно при сгорании бурых углей, ограничено. Это связано с нестабильностью химического и минералогического состава зол, получаемых при обжиге разных пластов месторождения угля, повышенным содержанием в них оксида кальция и магния, количество которых достигает 23 %, а также с режимами сжигания топлива, которые оказывают влияние на неоднородность строения: в одном случае больше оплавленной стекловидной фазы, в другом – повышенная пористость и др.
В связи с этим задача формирования концепции управления структурой строительных материалов с применением различных видов техногенных отходов остается чрезвычайно важной [14].
Постановка задачи
В развитии указанной концепции проведенные исследования представляли следующий алгоритм с рядом этапов:
-
1. Анализировался генезис техногенного продукта, определяющий его состав, структуру, состояние, свойства. Оценивалась многотоннажность отходов, анализировался химический, дисперсный состав.
-
2. Рассматривались методы воздействия на отходы, повышающие стабильность его состава и свойств. Отрабатывались оптимальные технологические параметры, и определялась мера стабильности характеристик и свойств изучаемого отхода для получения материала с комплексом заданных свойств.
-
3. Составлялись и отрабатывались экспериментальные смеси и изучались процессы струк-турообразования материалов. Осуществлялись лабораторные исследования продуктов современными методами.
Целью настоящей работы являлось исследование влияния механоактивации золы уноса ТЭЦ на физико-механические свойства бесцементных растворов для стабилизации ее состава и локализации вредного влияния свободных СaO и MgO.
Методология
Для достижения поставленной цели анализировался элементный состав зол гидроудаления Красноярских ТЭЦ, отобранных из устройств золоудаления в течение года, на рентгенофлуоресцентном спектрометре.
Методами наблюдения и сравнения выявлена высокая неоднородность состава и строения во времени, исследованы свойства зольных суспензий при различных режимах обработки в гидродинамическом диспергаторе и продуктов твердения бесцементных составов на их основе.
Решение поставленных задач
Химический, минералогический и фазовый составы зол зависят от вида сжигаемого угля, условий его сжигания, способа улавливания и отбора зол из шлаков.
Химический анализ отобранных в 2016 г. зол Красноярских ТЭЦ приведен в табл. 2.
В зависимости от химического состава золы делятся по модулю основности на два класса: 1-й – Мо = 0,6 – 1,5, 2-й – Мо < 0,6. По этому показателю золы ТЭЦ-2 (Мо=0,73) относятся к 1-му классу, а золы ТЭЦ-1 и ТЭЦ-3 (Мо=0,25 и 0,47 соответственно) относятся ко 2-му классу.
Основным оксидом, характеризующим золы как основные или кислые, является СаО [19, 20]. В каменных углях с преобладанием SiO2 золы получаются кислыми, с суммарным содержанием кислых оксидов около 80 % и более, с низким модулем основности, характеризуются пуццолановой активностью. Их используют как пуццолановую добавку либо как инертный материал.
При сжигании бурых углей Канско-Ачинского энергетического бассейна образуется высокое количество оксида кальция, в том числе свободного. Такие золы отличаются гидравлической активностью, имеют высокий модуль основности и делятся по химическому составу на:
-
– среднекальциевые – содержание СаО общ. 20-30 % и СаО своб. < 3 %;
-
– высококальциевые – содержание СаОобщ. 30-45 % и СаОсвоб. до 9 %;
-
– ультра высококальциевые – содержание СаО общ. > 45 % и СаО своб. > 10 %.
По содержанию оксида кальция золы Красноярских ТЭЦ-1 и ТЭЦ-3 относят к среднекаль-циевым. Зола ТЭЦ-2 является высококальциевой с высоким содержанием общего и свободного оксида кальция, характеризуется гидравлической активностью, однако из-за нестабильности режимов сжигания и образующейся стекловидной оболочки аморфной фазы может произойти разрушение затвердевшей структуры во времени вследствие поздних сроков гидратации.
Дисперсность, гидравлические и физико-механические свойства зол Красноярских ТЭЦ приведены в табл. 3.
Таблица 2. Химический состав зол Красноярских ТЭЦ
Table 2. Chemical composition of ashes of Krasnoyarsk TPPs
Наименование показателя |
Содержание, % по массе |
||
Зола Красноярской ТЭЦ-1 |
Зола Красноярской ТЭЦ-2 |
Зола Красноярской ТЭЦ-3 |
|
SiO 2 |
68,8 |
35,6 |
48,8 |
CaO |
15,2 |
28,73 |
23,0 |
CaO своб. |
3 |
4,71-12,06 |
5,2 |
MgO |
3,82 |
3,44 |
4,1 |
Fe 2 O 3 |
3,57 |
8,8 |
9,3 |
Al 2 O 3 |
6,22 |
8,21 |
8,2 |
SO 3 |
0,93 |
3,9 |
0,7 |
K 2 O |
0,45 |
0,4 |
0,6 |
Na 2 O |
0,18 |
0,6 |
0,3 |
ппп |
< 0,1 |
1,12 |
0,7 |
Хлориды |
< 0,01 |
10,2 |
5,2 |
Таблица 3. Свойства зол Красноярских ТЭЦ
Table 3. Ashes properties of Krasnoyarsk TPPs
Место отбора золы |
W о 2 ™ 3 £ Л о ^2 ^ С О |
CQ СХО У ° О о д |
н |
Сроки схватывания, ч-мин |
Предел прочности после тепловой обработки, МПа |
||||
начало |
конец |
при изгибе |
при сжатии |
||||||
1 сут |
28 сут |
1 сут |
28 сут |
||||||
Красноярская ТЭЦ-1 |
1835 |
18,8 |
25,75 |
2–25 |
3–30 |
- |
0,75 |
- |
2,4 |
Красноярская ТЭЦ-2 |
3434 |
12,1 |
26,75 |
0–30 |
1–20 |
1,1 |
2,4 |
6,5 |
7,95 |
Красноярская ТЭЦ-3 |
2625 |
15,8 |
32,5 |
1–10 |
2–45 |
0,7 |
1,02 |
2,04 |
3,32 |
Таблица 4. Химический состав золы уноса ТЭЦ-2
Table 4. Chemical composition of CHP-2 fly ash
№ пробы |
Содержание оксидов, % масс |
Стекло фаза |
||||||||
SiO 2 |
Al 2 O 3 |
Fe 2 O 3 |
MgO |
CаO общ. |
R 2 0 |
SO 3 |
ппп |
СаО своб. |
||
1 |
31,31 |
4,9 |
13,79 |
5,51 |
38,27 |
0,61 |
3,25 |
2,38 |
6,89 |
43,3 |
2 |
31,31 |
3,62 |
13,7 |
5,54 |
38,31 |
0,64 |
3,27 |
3,2 |
6,44 |
44,2 |
3 |
31,52 |
6,65 |
13,4 |
5,29 |
35,92 |
0,64 |
2,99 |
2,98 |
8,39 |
38,9 |
4 |
37,42 |
6,72 |
10,09 |
6,29 |
30,41 |
1,01 |
2,49 |
5,5 |
7,65 |
46,2 |
5 |
39,01 |
6,2 |
9,65 |
6,0 |
36,14 |
0,61 |
2,1 |
3,48 |
11,89 |
40,0 |
6 |
31,31 |
6,9 |
13,79 |
5,58 |
38,27 |
0,52 |
3,2 |
2,38 |
7,04 |
39,6 |
7 |
43,4 |
7,02 |
10,44 |
4,5 |
30,80 |
0,7 |
2,37 |
0,97 |
7,29 |
45,0 |
8 |
31,38 |
5,46 |
11,34 |
7,06 |
37,99 |
0,67 |
3,15 |
2,34 |
8,4 |
41,0 |
9 |
34,62 |
6,64 |
10,59 |
8,18 |
35,27 |
0,72 |
1,14 |
2,33 |
10,69 |
40,0 |
10 |
34,39 |
11,55 |
9,91 |
8,35 |
31,53 |
0,81 |
2,77 |
1,39 |
8,1 |
44,6 |
11 |
30,71 |
9,56 |
9,34 |
8,18 |
37,0 |
0,58 |
1,13 |
3,26 |
4,71 |
46,01 |
12 |
29,45 |
11,95 |
10,34 |
8,39 |
36,2 |
0,79 |
1,04 |
1,75 |
6,8 |
49,2 |
13 |
38,64 |
9,19 |
10,37 |
6,86 |
33,3 |
0,48 |
1,41 |
2,23 |
6,54 |
44,8 |
14 |
27,6 |
6,18 |
11,68 |
5,78 |
38,91 |
0,62 |
1,32 |
0,86 |
12,06 |
46,4 |
15 |
32,06 |
5,66 |
11,4 |
5,69 |
38,0 |
0,67 |
3,15 |
2,4 |
8,39 |
40,5 |
16 |
37,42 |
6,72 |
10,09 |
6,29 |
30,41 |
1,01 |
2,49 |
5,5 |
7,65 |
48,4 |
17 |
36,7 |
6,03 |
10,42 |
5,22 |
36,36 |
0,62 |
2,27 |
2,38 |
6,89 |
38,0 |
Из данных табл. 2, 3 видно, что наибольшей гидравлической активностью обладают золы Красноярской ТЭЦ-2 с учетом значительного содержания CaOобщ. и CaOсвоб., а также высокой удельной поверхности, сопоставимой с дисперсностью цемента.
Существенной проблемой, из-за которой ее применение не нашло широкого распространения, является большой разброс состава и свойств. Некристаллическая фаза, или стекло, служит основным компонентом золы уноса, поэтому высокая реакционная способность высоко-кальциевой золы уноса может быть отнесена к химическому составу стекла.
Результаты исследования состава и количества стеклофазы в пробах золы уноса ТЭЦ-2, отобранных в большом временном интервале (в течение года), приведены в табл. 4.
Столь значительные колебания в химическом составе и строении золы ТЭЦ-2 обусловливают необходимость дополнительного воздействия на нее с помощью специальных технологических приемов в целях стабилизации состава и свойств, а также локализации вредного влияния свободного СаО и MgO как первопричины дефектов структуры камня. Для этого применяют такие методы, как предварительный помол, автоклавирование, обработка в быстроходном смесителе, гидрохимический и др., позволяющие снизить содержание СаОсво6 . , механически разрушить стекловидную оболочку за счет диспергирования.
Для механической обработки золы в работе использовали гидродинамический диспергатор. Принцип его действия основан на кавитационной обрабработке, в результате которой образуется однородная мелкодисперсная суспензия с микронным размером частиц. Кавитационные пузырьки, образованные локальным понижением давления жидкости, при его повышении захлопываются со сверхзвуковой скоростью, порождая ударную волну. Возникающее при этом давление, локально достигающее десятков и даже сотен тысяч атмосфер, настолько резко возрастает, что частицы золы подвергаются диспергированию с ожидаемым разрушением стекловидной оболочки частиц СаОсво б .
Для определения оптимального режима активации золы в диспергаторе исследуемыми параметрами являлись скорость и длительность обработки. При активации зольно-водной смеси получали дисперсные и однородные суспензии, вязкость которых с увеличением длительности и скорости изменялась.
Продолжительность механоактивации золы уноса в гидродинамическом диспергаторе изменяли в пределах от 1 до 5 мин при постоянной скорости 3000 об/мин.
При наименьшей продолжительности активации суспензия золы была тягучей и вязкой, поскольку процесс активации связан в первую очередь с раздроблением макроскопических частиц золы, однако с увеличением времени обработки до 3 мин становилась более подвижной, возможно, из-за высокой энергии перемешивания суспензии, а свыше 3 мин нарастала, смесь становилась жесткой, видимо, из-за значительного увеличения дисперсности частиц золы, вызывая нехватку воды затворения, и внутреннего трения, возникающего вследствие значительной диспергации частиц и взаимодействия молекул.
Для оценки влияния скорости обработки в диспергаторе золы уноса на ее физикомеханические свойства выбирали три режима - 3000, 5000 и 10000 об/мин при общей продолжительности активации 1 мин.
По мере нарастания скорости обработки наблюдалось уменьшение вязкости суспензии, что в данном случае связано с значительным увеличением дисперсности частиц золы и отделе -нием воды. Однако при активации на скорости 10000 об/мин наблюдалось разжижение суспензии, а дальнейшие испытания продуктов твердения показали практически полное отсутствие гидратации, т. е. инертность обработанной золы уноса. Возможно, такая скорость активации привела к разрушению реакционноспособных минералов.
Для изучения влияния активации на физико-механические свойства продуктов твердения изготавливались бесцементные составы, в которых в качестве вяжущего применяли золу ТЭЦ-2. Зольно-водная смесь обрабатывалась в гидродинамическом диспергаторе с различной продолжительностью - 1, 3, 5 мин - и скоростью - 3000, 5000, 10000 об/мин. После обработки изготавливались образцы с добавлением к зольно-водной смеси мелкого песка (остаток – 848 –
Таблица 5. Физико-механические показатели продуктов твердения бесцементных составов на основе активированной золы в зависимости от продолжительности активации
Table 5. Physical and mechanical properties of hardening products of cement-free compositions based on activated ash depending on the activation duration
Зависимость прочностных показателей продуктов твердения от продолжительности обработки с постоянной скоростью 3000 об/мин представлена в табл. 5, а зависимость от скорости обработки с постоянным временем 1 мин – в табл. 6.
Анализ результатов табл. 5 показывает, что оптимальное время активации в гидродинамическом диспергаторе составляет 1 мин. Прочностные показатели продуктов твердения бес-цементных составов на основе золы активированной в течение этого времени (состав № 2-в) повышаются на 24 % по отношению к контрольному составу, что, очевидно, связано с разрушением стекловидной оболочки на поверхности зерен СаО, повышением гидравлической активности золы и с равномерностью изменения объема активированной золы.
Однако дальнейшее увеличение времени активации нецелесообразно, поскольку повлекло за собой резкое снижение прочности, возможно, за счет понижения гидравлической активности золы, и увеличивало энергетические затраты.
Визуальный осмотр образцов продуктов твердения неактивированных составов (контрольный № 1-в) показал наличие волосяных и мелких трещин глубиной до 4-5 мм, возможно, из-за деструктивных процессов и неравномерного изменения объема.
Наблюдения образцов состава № 2-в, полученных с использованием золы уноса, обработанной в гидродинамическом диспергаторе в течение 1 мин со скоростью 3000 об/мин, показали отсутствие дефектов.
Более длительная обработка в диспергаторе – в течение 3 мин и более – приводит к дополнительному повышению дисперсности частиц золы до коллоидной степени, в связи с чем зольноводная смесь имеет большую вязкость при том же расходе воды затворения. Поэтому у затвердевших образцов (состав № 3-в и № 4-в) наблюдались дефекты поверхности, такие как тонкие трещины и сколы углов, возможно, вызванные усадочными явлениями в результате неполной гидратации за счет недостаточного расхода воды затворения при высокой дисперсности.
Как видно из данных табл. 6 наибольшую прочность имеют продукты твердения бесце-ментных составов на основе золы, активированной со скоростью 3000 об/мин. При увеличении скорости обработки у затвердевших образцов наблюдались дефекты поверхности.
Таблица 6. Физико-механические показатели продуктов твердения бесцементных составов на основе активированной золы в зависимости от скорости обработки
Table 6. Physical and mechanical properties of hardening products of cement-free compositions based on activated ash depending on the processing speed
№ п/п состава |
Скорость обработки, об/мин |
Состав |
Средняя прочность при изгибе, МПа |
Средняя прочность при сжатии, МПа |
||
Зола, масс. части |
Песок, масс. части |
Водо/ вяжущее |
||||
1-с (контрольный) |
- |
1 |
2 |
0,44 |
1,11 |
2,93 |
2-с |
3000 |
1,65 |
3,86 |
|||
3-с |
5000 |
0,74 |
1,67 |
|||
4-с |
10000 |
0,82 |
1,99 |
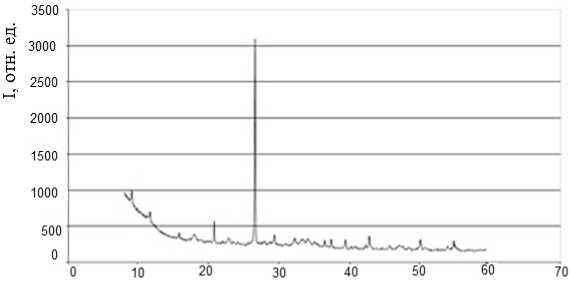
Рис. 1. Дифрактограмма продуктов твердения бесцементных составов на основе неактивированной золы (состава № 1-в (контрольный))
Fig. 1. Diffractogram of hardening products of cement-free compositions based on activated fly ash. Composition № 1-в – control
Для определения зависимости фазового состава продуктов твердения от режима обработки зольных суспензий выполнялся рентгенофазовый анализ, представленный на рис. 1–4.
Рентгеноструктурный анализ продуктов гидратации показал, что в процессе активации зол не только происходит диспергация материала, но и поэтапно изменяется его фазовый состав. В результате деструкции появляется активная полиморфная модификация γ-Al 2 O 3 , которая в результате взаимодействия с СаОсвоб. в присутствии SO3 (до 3 %) в процессе активации в гидродинамическом диспергаторе способствует образованию в продуктах твердения соединений типа гидросульфоалюминатов кальция, регистрируемых рентгенофазовым анализом (d= 0,96 нм).
При этом могут образовываться хорошо оформленные кристаллы эттрингита, что ведет к возрастанию прочности, либо рыхлые бесформенные пучки, из которых позднее формируются иглы.
На рис. 1 наблюдается значительное количество дифракционных максимумов, определяющих большое количество различных фаз и нестабильность показателей качества золы. Диф-рактограммы продуктов твердения бесцементных составов на основе активированной золы – 850 –
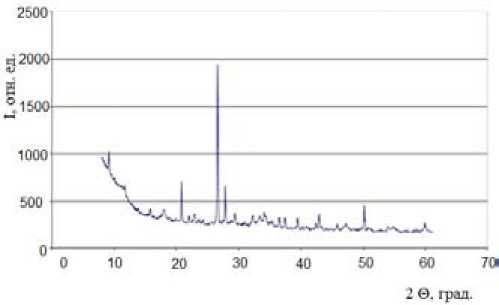
Рис. 2. Дифрактограмма продуктов твердения бесцементных составов на основе активированной золы, обработанной в гидродинамическом диспергаторе с продолжительностью 1 мин и со скоростью 3000 об/мин (состав № 2-в)
Fig. 2. Diffractogram of hardening products of cement-free compositions based on activated fly ash treated in a hydrodynamic disperser. Duration – 1 min, speed – 3000 rpm; composition № 2-в
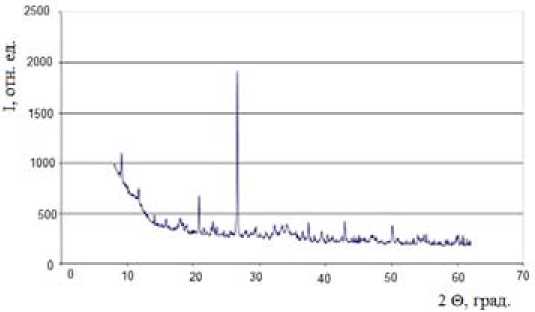
Рис. 3. Дифрактограмма продуктов твердения бесцементных составов на основе активированной золы, обработанной в гидродинамическом диспергаторе с продолжительностью 3 мин и со скоростью 3000 об/мин (состав № 3-в)
Fig. 3. Diffractogram of hardening products of cement-free compositions based on activated fly ash treated in a hydrodynamic disperser. Duration – 3 min, speed – 3000 rpm; composition № 3-в
(рис. 2-4) более однородны, с малым количеством отражений, что свидетельствует о большей гомогенности и стабильности структуры и строения.
Выводы
В результате проведенных исследований можно сделать следующие выводы.
-
1. Наибольшей гидравлической активностью обладают золы Красноярской ТЭЦ-2 со значительным содержанием CaOобщ. и CaOсвоб., а также высокой удельной поверхностью, сопоставимой с дисперсностью цемента. Исследования состава и количества стеклофазы в пробах, отобранных в большом временном интервале (в течение года), показали, что ее количество колеблется в пределах от 40 до 50 %.
-
2. Механоактивация зольно-водной суспензии в гидродинамическом диспергаторе приводит к стабилизации состава, локализует вредное влияние СaOсвоб. и MgO. Увеличение времени и скорости обработки влечет за собой значительное повышение дисперсности частиц золы, что вызывает нехватку воды затворения и возрастание вязкости суспензии.
-
3. Установлена зависимость прочностных показателей продуктов твердения бесцемент-ных составов на основе активированной золы, фазового состава и физического состояния зольно-водных суспензий от технологических параметров гидродинамической обработки золы и возможность влияния на уровни их структуры, определяемая размерами частиц, которые участвуют в ее формировании.
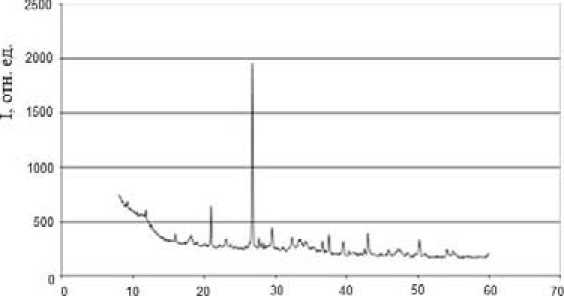
2 0, град.
Рис. 4. Дифрактограмма продуктов твердения бесцементных составов на основе активированной золы, обработанной в гидродинамическом диспергаторе с продолжительностью 5 мин и скоростью 3000 об/ мин ( состав № 4-в)
Fig.4. Diffractogram of hardening products of cement-free compositions based on activated fly ash treated in a hydrodynamic disperser. Duration – 5 minutes, speed – 3000 rpm; composition № 4-в
Наибольшими показателями прочности при изгибе и сжатии обладали продукты твердения на основе золы, активированной в гидродинамическом диспергаторе в течение 1 мин со скоростью 3000 об/мин.
Таким образом, применение механоактивации золы уноса в гидродинамическом диспергаторе с нейтрализацией колебаний в химическом составе и структуре золы дает возможность использования ее в приготовлении бетонов или растворов с улучшением их физико-технических характеристик.
Благодарность
Исследование выполнено при финансовой поддержке РФФИ и Правительства Красноярского края в рамках научного проекта № 18-41-242008.
Список литературы Влияние механоактивации на стабилизацию свойств золы уноса красноярских ТЭЦ
- Sinyak Yu.V. The concept of global economic development and energy. Forecasting problems, MAIK, "Science", Moscow, 1998, 3, 56-73
- Review of the state and environmental pollution in the Russian Federation for 2007. Roshydromet, 2008, 164 p
- OJSC "Yenisei TGC (TGC 13) Access: http://elib.sfu-kras.ru/handle/2311/34415
- Ecological efficiency of coal gasification technology on the example of Krasnoyarsk agglomeration [Electronic resource-Access:http://modernproblems.org.ru/ecology/24-hlebopros8.html
- Kuzmich N.P. Expanding the resource base of the construction complex based on the use of local raw materials and energy-efficient technologies. Eurasian International Scientific Analytical Journal. 2012, 2 (42), 325-328.
- Yezhov A.I. Evaluation of technogenic raw materials in the Russian Federation (Solid minerals). Mountain science and technology. 2016, 4, 62-72.
- Adeeva L.N., Borbat V.F. Zola CHPP is a promising raw material for industry. Vestn. Ohm Un-that. 2009, 2, 141-151.
- Cherepanov A.A., Kardash V.T. Integrated processing of ash and slag waste of CHP (results of laboratory and pilot tests). Geology and minerals of the oceans. 2009, 2, 98-115.
- Kalashnikov V.I., Belyakova E.A., Moskvin R.N., Moroz M.N., Ibragimov R.A. Priority directions in technology of concrete. Composite building materials. Theory and Practice: Coll. international scientific tech. conf. 2013, 39-42.
- Tselykovsky Yu.K. Some problems of using ash and slag waste from thermal power plants in Russia. Energetic. 1998, 7, 29-34.
- Babak N.A. Geoecological reserve of technologies, materials and structures in construction using industrial mineral waste. News PGUPS. 2011, 1. 113-119.
- Tselykovsky Yu.K. Experience of industrial use of ash and slag waste from thermal power plants Yu.K. Tselykovsky New in the Russian power industry. Energy Publishing. 2000, 2, 22-31.
- Berry E.E., Malhotra V.M. Fly Ash for use in concrete -a critical review. Acij. 1982, 2(3), 59-73.
- Vatin, NI, Petrosov, DV, Kalachev, AI, Lakhtinen, P., Application of Ashes and Ashes and Slag Waste in Construction. Engineering and Construction Journal. 2011, 4, 16-21.
- Bazhenov Yu.M. New Century New Concrete [Building materials, equipment, technologies of the XXI century, 2000, 2, 10-11.
- Bazhenov Yu.M., Demyanova B.C., Kalashnikov V.I. Modified high-strength concrete, Moscow, DIA, 2007, 368 p.
- Kalashnikov V.I., Borisov A.A., Polyakov L.G. et al. Modern ideas about the use of commodities and materials and VNV in concrete, Construction materials, 2000, 7, 12-13.
- Kalashnikov VI, Moroz M.N. High-hydrophobic multicomponent low-slag fine-grained concrete Scientific Herald of the Voronezh State University of Architecture and Civil Engineering. Construction and architecture, 2010, 1, 106-111.
- Moroz M.N., Kalashnikov V.I., Erofeeva I.V. Effective concretes of a new generation with low specific consumption of cement per unit of strength. Young Scientist, 2015, 6, 189-191.
- Moroz M.N. Vysokovitaminnye mineralology composite materials, dis.... kand. tech. sciences’. Penza, 2007, 210 р.
- Pugin K.G., Yushkov V.S. Construction of roads with the use of man-made materials. Volga Scientific Herald, 2012, 4 (8), 25-30
- Entin Z.B. Ashes TES-raw materials for cement and concrete. Cement and its application, 2012, 2, 40-46
- Entin ZB, Strzhalovskaya N. Once again about the fly ash of thermal power plants. Cement and its application, 2009, 106-111
- Nguyen Dinh Chin, Nguyen Thé Vinh, Bazhenov Yu.M. High-strength concretes with complex use of rice husk ash, fly ash and superplasticizers. Vestnik MGSU, 2011, 1. 76-81
- Kapustin F.L. Technological and environmental aspects of the use of fly ash from the Reftinskaya GRES in the production of building materials. Concrete technology, 2011, 7(8), 64-65
- Rakhimova N.R. Effect of ash additives on the properties of slag alkaline and concrete. Building materials, equipment, technologies of the XXI century, 2007, 3, 36-37
- Thomas M.D.A., Bamforth P.B. Modeling Chloride Diffusion in Concrete: Effect of Fly Ash and Slag. Cement and Concrete Research, Vol. 29, 1999, 487 -495.
- Safarov K.B., Stepanova V.F. Regulation of the reactivity of aggregates and increase of the sulfate resistance of concrete by the joint use of low-calcium fly ash and highly active metakaolin. Construction Materials, 2016, 5, 70-73
- Makarenko S.V., Konovalov N.P. Investigation of the physicochemical properties of the ashes of CHP-9 and the New Irkutsk CHP for use in ash-alkali binders. Construction Materials, 2011, 6, 60-62
- Complex system of CSM utilization. -Access: http://ksfenix.org
- GOST 25818-2017 "Fly ash of thermal power plants for concrete. Technical conditions. "Instead, GOST 25818-91; Enter 03.01.2017, Moscow: Standardinform, 2017.