Влияние наночастиц на структуру и механические свойства алюминиевых сплавов
Автор: Суходаев П.О., Редькин В.Е., Богданова Т.А., Кузнецов В.А.
Журнал: Журнал Сибирского федерального университета. Серия: Техника и технологии @technologies-sfu
Статья в выпуске: 3 т.10, 2017 года.
Бесплатный доступ
В статье рассмотрено влияние добавок нанопорошков на структуру и механические свойства сплавов алюминия АК12 и А7. По результатам внутриформенного модифицирования выбраны порошки для упрочнения отливок. Получены образцы с уменьшенным размером зерен, обладающие повышенной твердостью и прочностью.
Литье, композиционные материалы, наночастицы, нанопорошки, модифицирование, макроструктура, микроструктура, твердость, упрочнение
Короткий адрес: https://sciup.org/146115203
IDR: 146115203 | DOI: 10.17516/1999-494X2017-10-3-317-326
Текст научной статьи Влияние наночастиц на структуру и механические свойства алюминиевых сплавов
шинстве работ по данной тематике используется небольшой набор нанопорошков, чаще всего представленный оксидом кремния, который характеризуется наименьшим углом смачивания жидким металлом. В результате ограниченным оказывается применение других перспективных наноматериалов – нанотрубок, наноалмазов, электровзрывных керамических порошков и др., содержащих частицы значительной прочности и высокой дисперсности.
В данной работе авторами использована технология внутриформенного модифицирования, позволяющая улучшить усвоение широкого спектра НЧ жидким алюминиевым расплавом и быстро оценить их влияние на структуру отлитого металла [5]. В первой части экспериментов по этой технологии изготавливали образцы литьем в песчаную форму с использованием восьми видов порошков. Во второй части с использованием отобранных порошков отливали образцы в кокиль для испытаний на твердость.
-
1. Экспериментальная часть
-
1.1. Внутриформенное модифицирование при литье в песчаную форму
-
Технология внутриформенного модифицирования позволяет вносить частицы в расплав непосредственно при заливке. Схема литейной 6-позиционной формы приведена на рис. 1.
Металл при такой схеме заполняет форму, насыщаясь модификатором, что обеспечивает возможность быстрого заполнения из одного ковша нескольких форм. Фильтры предотвращают расплав от загрязнения.
Модификатор в виде таблетки изготавливали путем перемешивания медного порошка марки ПМС-1 с используемыми нанопорошками в шаровой мельнице в течение 5 мин в соотношении 5 к 1 по массе. Массу таблетки выбирали так, чтобы содержание порошков в матрице составляло 0,1 масс. %, при котором возможно достижение упрочнения без потери пластичности [7].
С помощью данного способа было получено 10 групп образцов, содержащих различные нанопорошки; состав модификаторов приведен ниже:
-
1) Медь, ПМС-1 (без углеродных добавок); 2) медь + технический углерод (ГОСТ 7885-86); 3) медь + технический углерод термообработанный; 4) медь + многослойные углеродные на-
- Рис. 1. Пресс-форма для изготовления литейных форм: 1 – керамические фильтры; 2 – модификатор в алюминиевой фольге; 3 – образец на растяжение; 4 – образец для микроструктурных и дюраметрических исследований и для проведения химического анализа
нотрубки (УНТ) производства института катализа г. Новосибирск; 5) медь + однослойные УНТ производства компании «OcSiAl»; 6) медь + ультрадисперсный алмазографитовый порошок детонационного синтеза, полученный по красноярской технологии (УДП-АГ – ТУ 40-206791001-91); 7) медь + ультрадисперсный алмазный порошок (УДП-А – по ТУ 3974-001-10172699-94); 8) медь + карбид бора наноразмерный (СибГИУ г. Новокузнецк); 9) медь + механоактивирован-ный графит (ИЦМИМ СФУ); 10) контрольный образец без модификатора.
Медь была выбрана как пластичный и непирофорный материал, способный эффективно образовывать покрытия на керамике при помоле в шаровой мельнице, что улучшает смачивание порошков. В качестве матричного металла был использован сплав алюминия с кремнием марки АК12. Температура сплава при разливке составляла 720 °С. После заливки и охлаждения заготовок из них вырезали образцы для исследования структуры и механических свойств [8].
Во всех образцах, содержащих НЧ, наблюдалось уменьшение размера зерна (определенное по ГОСТ 21073.0-75), величина которого и коэффициент модифицирования К представлены на рис. 2 и 3.
K = D/d. (1)
где D - величина зерна образца без модификатора (№10), мкм; d - величина зерна модифицированного образца, мкм.
Видим, что наибольшего измельчения удалось достичь при использовании углеродных наноматериалов и карбида бора. Это можно объяснить тем, что данные материалы обладают наибольшей дисперсностью и при попадании в расплав создают большое количество центров кристаллизации.
При исследовании макроструктуры у некоторых образцов было выявлено наличие дефектов газоусадочного характера и неравномерность структуры в осевом направлении. Это связа-
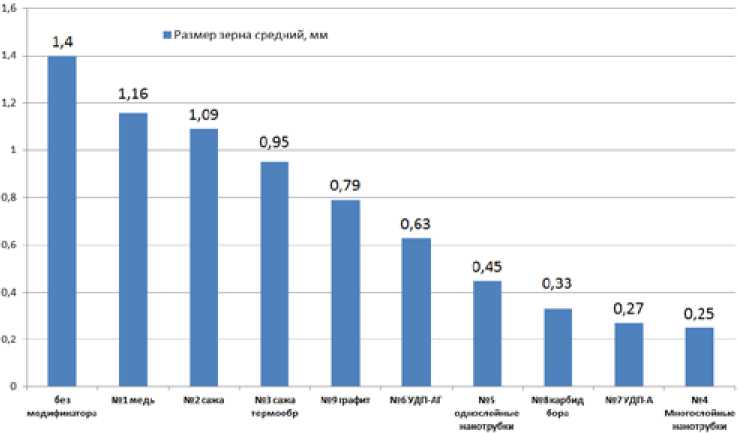
Рис. 2. Величина зерна в структуре образцов
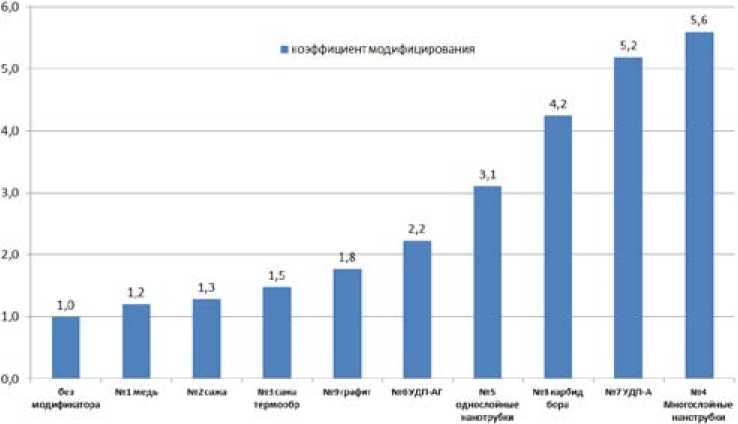
Рис. 3. Коэффициент K
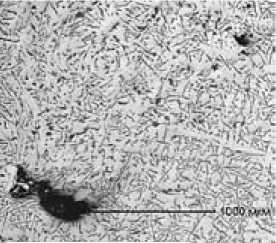
Рис. 4. Микроструктура базового (слева) и модифицированного наноалмазами (справа) сплава АК12
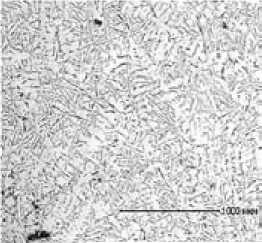
но с отсутствием перемешивания, усадкой при литье в песчаную форму, наличием адсорбированных газов на поверхности НЧ, которые не успевают выйти до затвердевания.
Микроструктура всех образцов представляет структуру силумина эвтектического состава, которая состоит из доли α-твердого раствора алюминия и немодифицированной эвтектики (рис. 4).
Вырезка образцов для испытаний механических свойств после разрыва проводилась из «донной» части исследуемых образцов по 4 штуки от каждого. Результаты испытаний представлены на рис. 5. Исследование изломов разрывных образцов показало присутствие в структуре дефектов в виде пор, разрушения имеют идентичный хрупкий характер (рис. 6). Уровень относительного удлинения всех представленных образцов не превышает 2 %.
Из-за повышенного содержания адсорбированных газов в порошках с наивысшей удельной поверхностью – нанотрубках, карбиде бора и наноалмазах прочность образцов с этими модификаторами оказалась самой низкой из всех, несмотря на минимальный размер зерен, зафиксированный в этих образцах.
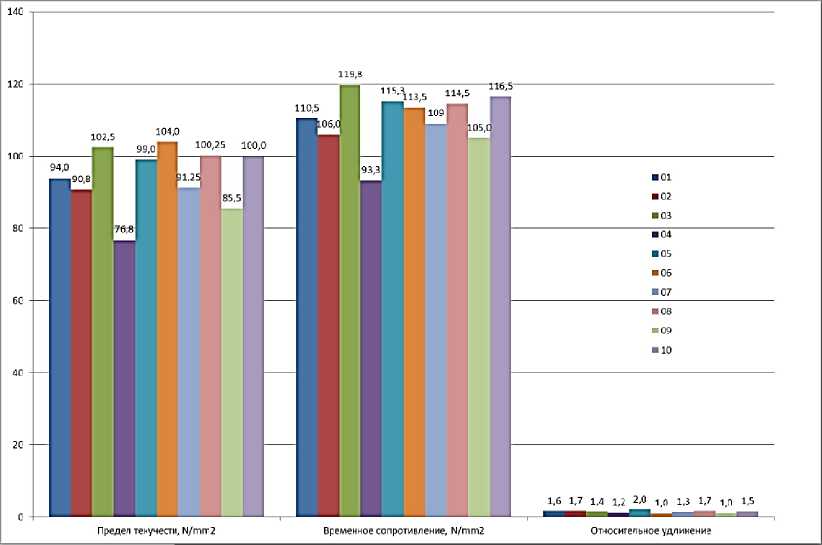
Рис. 5. Уровень механических свойств образцов
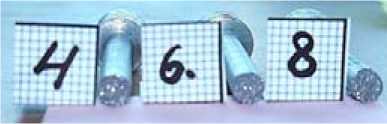
Рис. 6. Изломы образцов после испытаний на разрыв
-
1.2. Литье в кокиль
Во второй части экспериментов проводилось литье в кокиль. Из используемых порошков были отобраны УДП-А и УДП-АГ, при применении которых были получены хорошие результаты уменьшения зерна. Кроме того, эти материалы обладают относительно низкой стоимостью и могут производиться в больших масштабах по сравнению с нанотрубками. Также использовался оксид алюминия электровзрывного синтеза (производства Института сильноточной электроники, г. Томск).
Изучение гранулометрического состава наноалмаза и оксида алюминия проводилось путем осаждения в дисковой центрифуге CPS 24000. Метод основан на седиментации частиц в жидкости и отличается от других методов высоким разрешением, точностью и широким диапазоном измерения. Главный элемент центрифуги – диск, в котором происходит осаждение суспензии исследуемого вещества от центра до края в центробежном поле сил, создаваемым вращением со скоростью до 24000 об/мин. На рис. 7 представлено распределение порошка УДП-А по размерам.
На распределении виден пик 12 нм и небольшой пик ближе к началу координат, который плохо различим на данном рисунке. Если ограничить ось абсцисс областью в начале координат и растянуть, то вид распределения преобразуется в изображенный на рис. 8.
Здесь малый пик 4 нм хорошо различим. Он, вероятно, являет собой первичные неагреги-рованные частицы [9].
На рис. 9 представлено распределение порошка оксида алюминия.
Наибольшее количество частиц здесь имеет двойной пик – 15 и 20 нм.
Для литья использовался первичный алюминий марки А7, который нагревали в титановом тигле до температуры 790 °С, после чего в расплав помещали таблетку-модификатор, изготов-
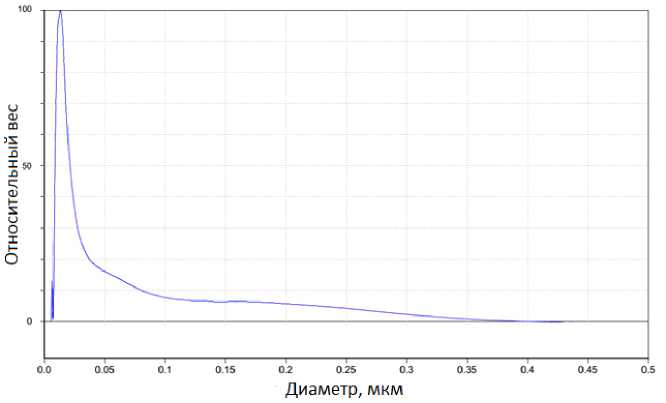
Рис. 7. Гранулометрический состав порошка УДП-А
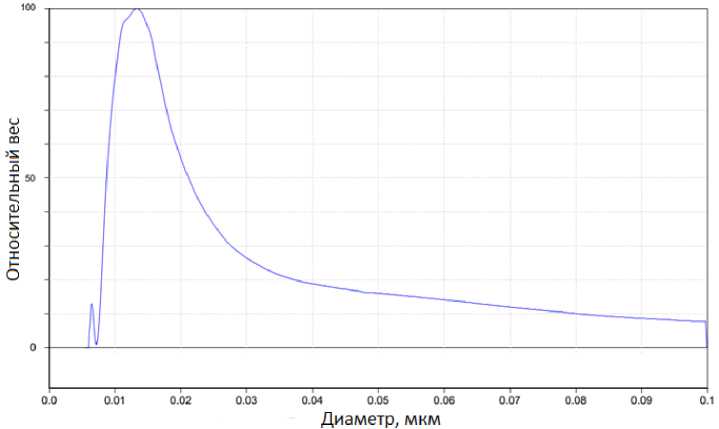
Рис. 8. Гранулометрический состав порошка УДП-А (часть графика до 0,1 мкм)
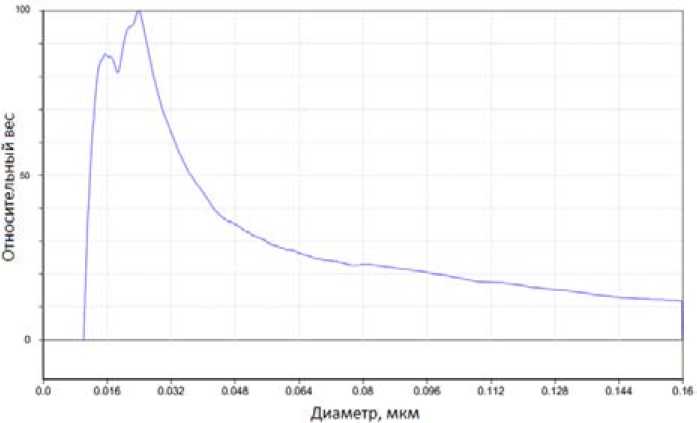
Рис. 9. Гранулометрический состав порошка AI 2 O 3 электровзрывного синтеза
ленную так же, как и при первом эксперименте. Расплав выдерживали 15 мин и затем разливали в кокиль. Во время выдержки модификатор растворялся, и газам было достаточно времени для выхода из расплава. Образцы отливались с двумя массовыми содержаниями каждого порошка – 0,05 и 0,1 %.
Макроструктура и размер зерен отлитых образцов приведен на рис. 10 и 11.
В образце, содержащем НЧ Al2O3 удалось достичь 10-кратного уменьшения зерен.
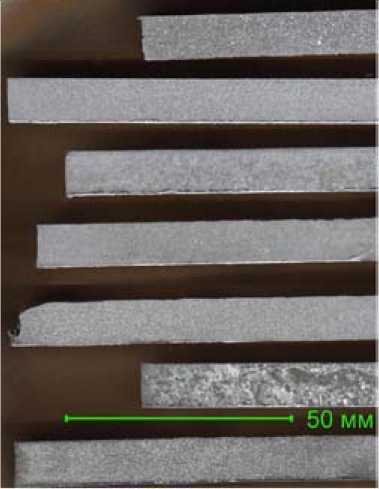
УДП-А, 0,05 %
УДП-АГ, 0,1 %
УДП-АГ, 0,05 %
Контрольный
Al 2 O 3 , 0,05 %
Al 2 O 3 , 0,1 %
УДП-А, 0,1 %
Рис. 10. Макроструктура отлитых в кокиль образцов
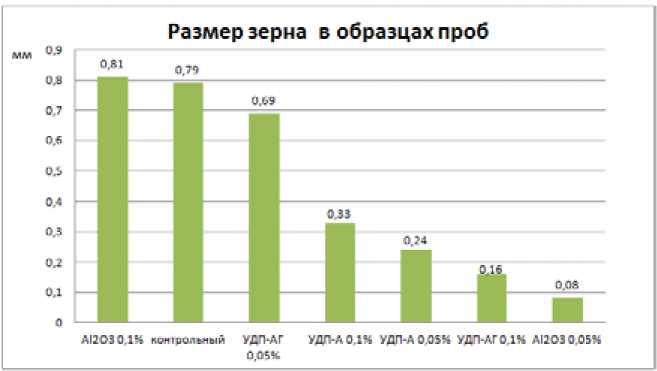
Рис. 11. Размер зерна образцов
Таблица. Твердость образцов, отлитых в кокиль
Модификатор |
Контрольный образец |
УДП-А, 0,05 % |
УДП-А, 0,1 % |
УДП-АГ, 0,05 % |
УДП-АГ, 0,1 % |
Al 2 O 3 , 0,05 % |
Al 2 O 3 , 0,1 % |
Твердость, HB |
24,1 |
27,9 |
28,5 |
25,0 |
30,1 |
24,2 |
30,1 |
Предел прочности σ в, МПа (расчет) |
87,2 |
101,0 |
103,2 |
90,5 |
109,0 |
87,6 |
109,0 |
Твёрдость образцов, измеренная по методу Бринелля, приведена в таблице. В третьей колонке даны значения временного сопротивления, рассчитанные по соотношению [10]
ав = 3,62НВ(МРа). (2)
Можно видеть, что все модифицированные образцы обладают повышенной твёрдостью. Таким образом, используемые наноматериалы являются эффективными добавками для увеличения твердости (следовательно, и износостойкости) и механической прочности алюминия.
Заключение
Исследовано модифициравание алюминиевых сплавов с помощью метода внутриформен-ного введения нанопорошков. Наиболее перспективные модификаторы были выбраны для получения упрочненных образцов.
При литье в кокиль с помощью добавок нанопорошков удалось достичь уменьшения размера зерна в полученных сплавах до 10 раз. Значения твердости, полученные в модифицированных образцах, на 20-25 % выше, чем у базового сплава.
Дальнейшие исследования могут быть направлены в сторону подбора оптимального гранулометрического состава нанопорошков, что может улучшить их инокулирующую способность [11] и в большей степени измельчить структуру.
Список литературы Влияние наночастиц на структуру и механические свойства алюминиевых сплавов
- Goetzel C.G. Dispersion strengthened alloys: "The possibilities of light metals." Journal of metals, 1959, 11(3), 189-194
- Крушенко Г.Г., Балашов Б.А., Василенко З.А., Фильков М.Н., Миллер Т.Н. Повышение механических свойств алюминиевых литейных сплавов с помощью ультрадисперсных порошков. Литейное производство, 1991, 4, 17-18
- Zhang Z., Chen D.L. Contribution of Orowan strengthening effect in particulate-reinforced metal matrix nanocomposites. Materials Science and Engineering: A, 2008, 483, 148-152
- Mirza F.A., Chen D.L. A unified model for the prediction of yield strength in particulate-reinforced metal matrix nanocomposites. Materials, 2015, 8(8), 5138-5153
- Кузнецов В.А. Влияние ультрадисперсных порошков тугоплавих материалов на свойства литых изделий из черных и цветных металлов и сплавов, автореф. дис. … канд. техн. наук. Красноярск, 2013, 26 с
- Li X., Yang Y., Weiss D. Ultrasonic cavitation based dispersion of nanoparticles in aluminum melts for solidification processing of bulk aluminum matrix nanocomposite: Theoretical study, fabrication and characterization. AFS Transactions, 2007, 115(07-133), 249-260
- Сабуров В.П., Черепанов А.Н., Жуков М.Ф., Галевский Г.В. и др. Плазмохимический синтез ультрадисперсных порошков и их применение для модифицирования металлов и сплавов (Низкотемпературная плазма. Т. 12). Новосибирск: Наука, 1995. 344 с
- Суходаев П.О., Богданова Т.А., Кузнецов В.А., Редькин В.Е. Литые композиционные материалы на основе алюминия, упрочненные наночастицами. Евразийский союз ученых, 2014, 4(4), 117-120
- Ставер A.M., Губарева Н.В., Лямкин А.И., Петров Е.А. Ультрадисперсные алмазные порошки, полученные с использованием энергии взрыва. Физика горения и взрыва, 1984, 20(5), 100-104
- Фридман Я. Б. Механические свойства металлов. Часть 2. Механические испытания. Конструкционная прочность. М.: Машиностроение, 1974. 368 с
- Greer A.L. Grain refinement of alloys by inoculation of melts. Philosophical transactions of the Royal Society of London A: mathematical, physical and engineering sciences, 2003, 361(1804), 479-495