Влияние режима коксования и углеродсодержащей пыли на коэффициент анизометрии пекового кокса
Автор: Дыскина Б.Ш., Малютина Е.М.
Журнал: Вестник Южно-Уральского государственного университета. Серия: Металлургия @vestnik-susu-metallurgy
Статья в выпуске: 21 (93), 2007 года.
Бесплатный доступ
Короткий адрес: https://sciup.org/147156579
IDR: 147156579
Текст статьи Влияние режима коксования и углеродсодержащей пыли на коэффициент анизометрии пекового кокса
С развитием цивилизации проблема охраны окружающей среды все более приобретает планетарный характер. Особенность электродного производства - интенсивное образование углеродсодержащей пыли. Соответственно, на всех технологических переделах действует система пылеулавливания. В зависимости от точки сбора различают пыль сырого и прокаленного коксов, антрацитов и термоантрацитов, пересыпочных материалов печей обжига и графитации, а также пыль механической обработки графитированных и обожженных изделий. Многие годы фильтровая пыль систематически вывозилась и поныне вывозится на свалку. Согласно данным авторов работы [1], в 1982 году количество углеродсодержащих отходов, вывезенных на свалку, по советской электродной подотрасли составило 26,8 тыс. тонн, из них фильтровой пыли -17,1 тыс. тонн, в том числе по одному из электродных заводов - 4,5 тыс. тонн. Хотя в 80-е годы была разработана комплексная программа по снижению потерь и рациональному использованию отходов, этот же электродный завод в 2005 году вывез на свалку еще большее количество фильтровой пыли - порядка 7 тыс. тонн.
В настоящих условиях дефицитной сырьевой базы электродной подотрасли России, обусловленной отсутствием производства малосернистых нефтяных и пековых коксов для графитированных электродов, ограниченным производством пекового электродного кокса [2-4], проблема рекуперации электрофильтровой пыли, содержащей углерод в пределах 95-98 %, остается актуальной. Одновременно вовлечение пыли в технологию могло бы привести к снижению твердых выбросов и сокращению площади свалок.
Электрофильтровые углеродсодержащие пыли неоднородны по гранулометрическому составу, удельной поверхности и зольности [5], что является препятствием для прямого использования их в качестве сырьевого материала. В литературе известны способы применения углеродсодержащих пылей:
- в качестве компонента угольной шихты [6]; - в качестве окускованного твердого топлива [7]; - путем изготовления нудель-графита и после дующим его использованием как технологического сырья для производства угольной продукции [5].
Однако эти способы не получили широкого промышленного внедрения.
Для данного исследования выбраны угольная (УП) и графитированная (ГП) пыли Челябинского электродного завода, отобранные с электрофильтров цеха механической обработки угольной и графитированной продукции, соответственно (табл. 1). В технологии производства угольной продукции основные сырьевые материалы термоантрацит и каменноугольный пек перерабатывают по схеме: прессование -> обжиг (900-1000 °C); графитированной - прокаленные нефтяной или пековый коксы и пек - по схеме: прессование -> обжиг (9001000 °C) -> охлаждение до температуры окружающей среды -> графитация (-2500 °C). Из этого следует, что угольная пыль состоит, в основном, из частиц термоантрацита и кокса связующего, полученного при температурах порядка 1000 °C; графитированная - прокаленного нефтяного или пекового кокса плюс кокса связующего, прошедшие двухстадийную термообработку 1000 и 2500 °C с промежуточным охлаждением. На наш взгляд, исходя из основного состава этих пылей, они могли бы быть вполне пригодны в качестве наполнителя при производстве пекового кокса.
С использованием проб этих пылей нами изготовлены лабораторные образцы пекового кокса из среднетемпературного каменноугольного пека Челябинского КХП (ГОСТ 10200-83). Качество пека представлено в табл. 2.
Количество наполнителя, введенного в пек -10, 20, 30 и 40 % и контрольная проба - без добавок. Коксование проводили в режиме полукоксования с конечной температурой 500 °C и коксования -900 °C, а также в режиме, моделирующим коксование полукокса (500 + 900 °C). Режимы термообработки представлены на рис 1.
В режиме полукоксования (500 °C) с наполнителем в количестве 10 и 20% получен кусковой пековый кокс серо-черного цвета, при большем содержании - получена коксовая мелочь с содержанием частиц более 4 мм до 80 %. В режиме коксования (900 °C) получен кусковой пековый кокс во всех пробах.
Характеристика проб углеродсодержащей электрофильтровой пыли
Таблица 1
Пробы ЭФ пыли |
Зольность, % |
Ди, г/см3 |
Сера, % |
Массовая доля частиц менее 0,05 мм, % |
графитированной |
0,56-1,12 |
2,18 |
0,33 |
67,44 |
угольной |
2,18 |
1,71 |
0,78 |
44,48 |
Таблица 2
Показатели качества каменноугольного пека
Наименование показателя |
Значение |
Норма ГОСТ 10200-83 |
||
марка А |
марка Б |
марка В |
||
Температура размягчения, °C |
66,5 |
65-70 |
67-73 |
85-90 |
Массовая доля веществ, нерастворимых в толуоле ( ос -фракция), % |
32,26 |
24-28 |
25-31 |
не менее 31 |
Выход летучих веществ, % |
62,5 |
59-63 |
58-62 |
53-57 |
Зольность, % |
0,23 |
не более 0,3 |

Время, мин
Рис. 1. Графики коксования: П-900 °C и полукоксования о - 500 °C.
Макроструктура образцов кокса с графитированной пылью менее плотная, чем с угольной, пористость равномерная по всей поверхности. У коксов с угольной пылью - пористость менее равномерная. На всех образцах полученного кокса проведено определение коэффициента анизометрии частиц размером 1-2 мм. Результаты представлены в табл. 3.
Из табл. 3 видно, что при однократной термообработке введение наполнителя обусловило повышение анизометрии частиц на 12,6-6,3 % в режиме полукоксования, и на 6,5-3,3 % - коксования. Двукратная термообработка (полукоксование -> охлаждение -> коксование) заметно способствовала увеличению анизометрии частиц контрольного пекового кокса на 15,4-11,8%. В этом режиме наполнение пека пылевыми частицами способствовало получению пекового кокса более изотропной структуры: коэффициент анизометрию частиц снизился при добавке 10 % пыли на 4,9-6,3 %; 20 % - на 2,8-0,7 % и 30 % - на 3,5-2,1 %.
Влияние материала пыли особенно заметно при полукоксовании пека. Характер зависимости анизометрии частиц пекового кокса от количества наполнителя одинаковый (рис. 2а), но графитированная пыль в большей мере способствует повышению анизометрии зерен кокса. Это может быть связано с ориентирующим влиянием структуры графита на мезофазные превращения, а возможно и меньшей зольностью графитированной пыли. В работе [8] методом реплик на электронном просвечивающем микроскопе выявлено, что скол кокса из пека без наполнителей имеет мелкоглобулярное строение с размером глобул 0,1-0,2 мкм. Введение в пек термоантрацита привело к увеличению размеров глобулярных образований до 0,4-0,6 мкм, а графита - до 0,35-1,30 мкм, наблюдались и очень крупные единичные глобулы до 2 мкм. В работе [9] показано, что снижение зольности с 1,70 до 0,28 % приводит к увеличению коэффициента анизотропии удельного электросопротивления пекового кокса с 1,12 до 1, 33; линейного термического расширения - с 1,05 до 1,33
Разность влияния графитированной и угольной пылей возрастает пропорционально увеличению количества (А = 0,19х). При наполнении 30 % разность составила 5,2 %. В образцах режима коксования (900 °C) влияние материала пыли значительно меньше. При наполнении 10-20 % разница составила 2,3 %, более анизометричны образцы с угольной пылью. С увеличением количества пыли разность снизилась до 1,6% с превалирующим влиянием на анизометрию графитированной пыли (рис. 26). Полукокс, полученный в режиме 500 °C, подвергли коксованию при 900 °C. Повторная термообработка обусловила выравнивание коэффициента анизометрии частиц пекового кокса с наполнением, независимо от вида и количества пыли. При этом у всех образцов пекового кокса двухстадийной обработки уровень анизометрии выше, чем
Таблица 3
Влияние режима коксования и количества наполнителя на коэффициент анизометрии пекового кокса
Режим коксования |
Количество пыли |
Пек без пыли |
|||||||
10% |
20 % |
30% |
40% |
||||||
УП |
ГП |
УП |
ГП |
УП |
ГП |
УП |
ГП |
||
500 °C |
1,41 |
1,43 |
1,30 |
1,35 |
1,35 |
1,42 |
— |
— |
1,27 |
900 °C |
1,30 |
1,27 |
1,31 |
1,28 |
— |
1,27 |
1,29 |
1,23 |
|
500 + 900 °C |
1,35 |
1,33 |
1,38 |
1,41 |
1,39 |
1,37 |
— |
- |
1,42 |
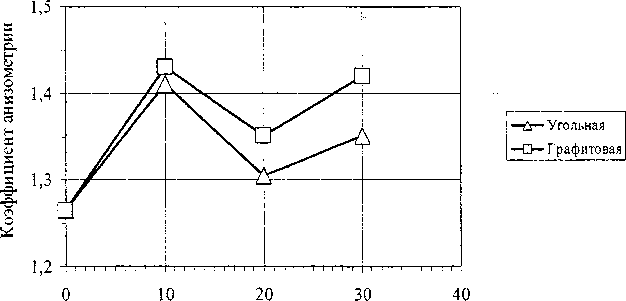
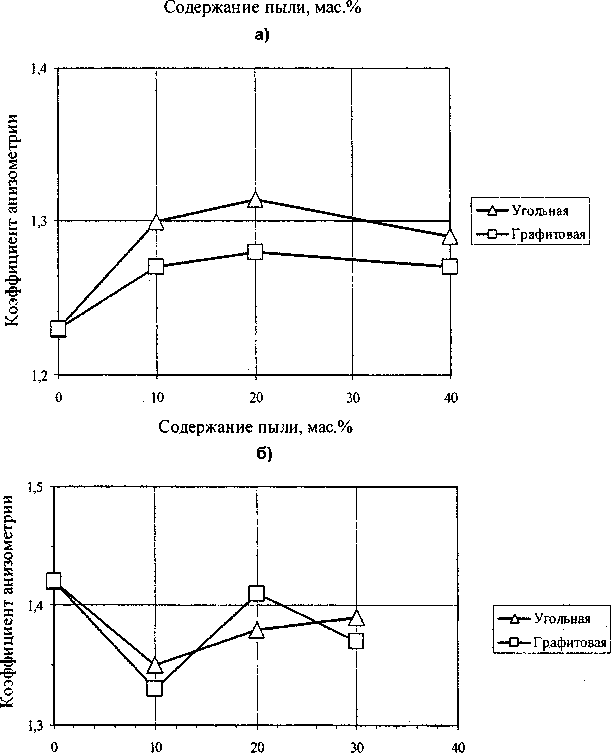
Содержание пыли, мас.% в)
Рис. 2. Зависимость коэффициента анизометрии от количества наполнения и режима коксования: а - 500 °C; б - 900 °C; в - 500 + 900 °C полученных однократным нагревом при 900 °C (рис. 2в). По всей видимости, структура кокса, сформировавшаяся в режиме полукоксования (500 °C) или охлаждения замораживается, а затем при повторном нагреве (прокалке) стабилизируется, и в значительной мере, сохраняется. При однократном нагреве до 900 °C (без выдержки при 500 °C) скорость нагрева, очевидно, превышает скорость образования устойчивых структурных составляющих, формирующих анизотропные свойства зерновых фракций кокса.
В промышленности пековый кокс получают коксованием в камерных печах. Максимальная температура в осевой плоскости коксового пирога составляет 900—1100 °C, в периферии близ стенок камеры может достигать 1200-1300 °C. Пробы промышленного пекового кокса из объема коксового пирога и пристеночные отличаются макроструктурой. Кокс из объема крупнопористый, серочерного цвета, характеризуется волокнистой структурой, коэффициент анизометрии составил 1,52. Пристеночные образцы кокса - более плотные мелкопористые, матовые с коэффициентом анизометрии, равным 1,36. Таким образом, чем выше температура и скорость коксования сырья, тем меньше анизометрия полученного кокса. Поскольку объем лабораторного коксования был невелик, анизометрия зерен лабораторных коксов близка к анизометрии промышленного пристеночного кокса. Из табл. 3 видно, что режим коксования, моделирующий промышленный, способствует формированию более изотропного кокса.
В электродных технологиях используют прокаленные коксы. Температура прокаливания 1200-1300 °C. Прокаливанию подвергают, так называемые «сырые» нефтяные коксы замедленного коксования, полученные при температурах 450-500 °C, прокаливают и пековые коксы камерного коксования. Этим в большей мере реализуется способ сохранения анизометричных структур в нефтяных коксах и изометричных - в пековых. Наполнение пека графитированной и угольной пылью в исследованных количествах позволяет поддерживать уровень анизометрии пекового кокса не ниже, чем у пекового полукокса. С повышением анизометрии частиц кокса, соответственно, возрастает и анизотропия таких свойств, как удельное электросопротивление, линейное термическое расширение изделий на его основе.
Таким образом, применение фильтровой углеродсодержащей пыли в технологии производства пекового кокса целесообразно с точки зрения регулирования качества пекового кокса и утилизации пыли.
Выводы
-
1. Экспериментально выявлено, что наполнение среднетемпературного пека фильтровой графитированной или угольной пылью приводит к формированию кускового пекового кокса при введении пылей до 20 % в режиме полукоксования; до 40 % - в режиме коксования.
-
2. Показано, что повышению анизометрии прокаленного пекового кокса способствует прокалка предварительно полученного полукокса без добавок или с 20-30 %-ным наполнением углеродсодержащей пылью. Режим коксования с одно
кратным нагревом до 900 °C, моделирующий промышленный, способствует формированию наиболее изотропного кокса без введения добавок.
Список литературы Влияние режима коксования и углеродсодержащей пыли на коэффициент анизометрии пекового кокса
- Классификация, учет и использование вторичных материальных ресурсов в электродном производстве/В.Г. Зеленкин, Л. А. Шкатова, Н.П. Шохина и др.//Тезисы докладов и сообщений V всесоюзной научно-технической конференции электродного производства «Повышение качества и эксплуатационной стойкости углеродной продукции», 1983. -С. 71-73 2.
- Проблема кокса для производства графитированных электродов/П.Б. Рабин, Н.И. Воробьев, Н.Р Сайфуллин и др.//Сб. науч. тр. "Современные проблемы производства и эксплуатации углеродной продукции».-Челябинск, 2000. -С. 26-27
- Селезнев, А.Н. Проблема сырьевой базы электродной промышленности // А.Н. Селезнев, В. И. Костиков, Н.Н. Шипков // Химия твердого топлива. - 1999 -№ 4.- С. 64-68.
- Селезнев, А.Н. Углеродистое сырье для электродной промышленности/А.Н. Селезнев. -М: Профиздат, 2000. -85 с. 5.
- Туйчина, О.Г. Использование отходов электродного производства в технологии изготовления футеровочных блоков/О.Г. Туйчина, Н.Г. Пуль,Н.Ф. Кондрашенкова//Тезисы докладов и сообщений V всесоюзной научно-технической конференции электродного производства «Повышение качества и эксплуатационной стойкости углеродной продукции». -Челябинск, 1983. -С. 337-340. 6.
- Коксовая пыль как компонент угольной шихты/С.Д. Тихов, А.В. Березин, П.Д. Нагибин и др.//Кокс и химия. -2004. -№ 2.-С 10-13. 7
- Ухов, О.А. Получение брикетированного связующего и регулирование физико-химических свойств формованного топлива-восстановителя: автореферат дис. канд. техн. наук/О.А. Ухов. -Уфа, 1983. -23 с. 8.
- Структурные особенности кокса из пека при добавлении различных наполнителей/О.Б. Громова, С.Н. Михайлец, В.Е. Громов, Ю.К. Сухов//Тезисы докладов и сообщений VI всесоюзной научно-технической конференции электродной промышленности. -Челябинск, 1988. -С. 17 9
- Фиалков, А.С. Углерод, межслоевые соединения и композиты на его основе/А.С. Фиалков -М. Аспект Пресс, 1997.-718 с.