Влияние структурных и фазовых изменений при термической обработке трубных сталей на скорость общей коррозии
Автор: Маковецкий Александр Николаевич, Мирзаев Джалал Аминулович, Васильев Евгений Николаевич
Журнал: Вестник Южно-Уральского государственного университета. Серия: Металлургия @vestnik-susu-metallurgy
Рубрика: Металловедение и термическая обработка
Статья в выпуске: 4 т.16, 2016 года.
Бесплатный доступ
Коррозия является одним из основных факторов, ограничивающих срок эксплуатации нефте- и газопроводных труб. Для повышения коррозионной стойкости стали легируют элементами, которые позволяют получить плёнку окислов, защищающую металл от растворения. В то же время можно ожидать, что и для обычных углеродистых и низколегированных сталей скоростью коррозии можно до некоторой степени управлять, изменяя их структуру путём термической обработки. Данное исследование посвящено изучению этого фактора на примере трубных сталей 20А и 20ФА. С этой целью стали были подвергнуты 18 различным режимам термической обработки, которые включали нормализацию при различных температурах, полную закалку с высоким отпуском и закалку из межкритического интервала с высоким отпуском. После термической обработки были исследованы механические свойства и скорость равномерной (общей) коррозии сталей в модельной среде, содержащей сероводород, с целью выявить возможное влияние структурных изменений на стойкость против коррозии. Наихудшую коррозионную стойкость обеспечивали режимы с закалкой из межкритического интервала Ac1…Ac3, по-видимому, потому, что перераспределение углерода и легирующих элементов между α- и γ-фазами во время выдержки в межкритическом интервале усиливает коррозию. Но в целом коррозионная стойкость сталей колебалась нерегулярно, без заметной корреляции с размером зерна, характером структуры, температурой отпуска и уровнем ударной вязкости. Таким образом, наглядно продемонстрировано, что сопротивление трубных сталей коррозии в сероводородной среде в основном определяется не режимом термической обработки и особенностями структуры, а химией процесса растворения металла (например, образованием защитных плёнок), а также, возможно, неметаллическими включениями.
Трубные стали, общая коррозия, коррозионная стойкость, сероводородсодержащая среда, ударная вязкость, термическая обработка
Короткий адрес: https://sciup.org/147157054
IDR: 147157054 | DOI: 10.14529/met160414
Текст научной статьи Влияние структурных и фазовых изменений при термической обработке трубных сталей на скорость общей коррозии
Коррозия и коррозионное растрескивание являются основными причинами ограниченного срока эксплуатации нефте- и газопроводных труб. Скорость коррозии углеродистых и низколегированных сталей в основном определяется интенсивностью поступления кислорода из атмосферы через водный раствор к окисляемой поверхности и образовании оксидной плёнки Fe(OH)2. Когда она возникает, то атомы кислорода должны продиф-фундировать через плёнку к металлу, что приводит к утолщению плёнки с одной стороны и растворению в водном растворе с другой [1]. Основной принцип борьбы с коррозией заключается в легировании стали такими элементами (Cr, Si, Ni и др.), которые позволяют получить плёнку окислов, мало проницаемую для кислорода [2]. Однако и для рядовых сталей, изменяя фазовый состав и структуру, вероятно, можно оказать некоторое влияние на скорость общей коррозии, хотя этот вопрос изучен всё ещё поверхностно [3]. Настоящее исследование посвящено накоплению и обобщению экспериментальных данных о скорости коррозии трубных сталей 20А и 20ФА.
Материал и методика исследования
В работе использовались трубные стали 20А и 20ФА, химический состав которых согласно ТУ 14-158-115-99 и 14-158-114-99 приведён в табл. 1.
Термической обработке подвергали патрубки из стали 20А и темплеты из стали 20ФА. Затем из термообработанных образцов вырезали образцы для испытаний на растяжение [4], образцы Шарпи с V-образным надрезом для испытаний на ударную вязкость при –50 °С [5] и образцы для проведения коррозионных испытаний. Для проведения механических испытаний использовалась разрывная машина
Таблица 1
Химический состав сталей, мас. %
Сталь |
C |
Mn |
Si |
Al |
V |
20А |
0,17–0,24 |
0,35–0,65 |
0,17–0,37 |
0,02–0,05 |
– |
20ФА |
0,17–0,22 |
0,50–0,65 |
0,17–0,37 |
0,03–0,05 |
0,02–0,05 |
Сталь |
Cr 1 |
Cu 1 |
Ni 1 |
S 1 |
P |
не более |
|||||
20А |
0,40 |
0,25 |
0,30 |
0,013 |
0,018 |
20ФА |
0,40 |
0,25 |
0,25 |
0,020 |
0,015 |
ЕИ-40 и маятниковый копёр 2010КМ-30 с максимальной энергией удара 300 Дж.
Исследование стойкости к общей коррозии проводилось по методике, разработанной ОАО «ВНИИТнефть» на основе ГОСТ 9.908–85 [6] для оценки стойкости низколегированных и углеродистых сталей к равномерной (общей) коррозии в модельной среде, содержащей сероводород. В основу методики положено определение потери массы с единицы поверхности образцов за время их пребывания в агрессивных средах.
Для испытаний изготавливают плоские образцы размером 40×10×2 мм. Шероховатость поверхности образцов ( Ra ) должна быть не более 6,3 мкм. Выдержка образцов осуществляется в химически инертной по отношению в водному раствору сероводорода ёмкости, которая соединяется с источником Н2S. Испытательная среда представляет собой водный раствор, содержащий 5 % хлорида натрия и 0,5 % уксусной кислоты, насыщенный сероводородом (среда по стандарту NACE ТМ-0177). Приготовленный раствор до насыщения его сероводородом имеет pH 2,7–3,0. Температура испытаний составляет 20 ± 3 °С, время выдержки 96 ч.
Показателем стойкости к равномерной (общей) коррозии является скорость коррозии v [г/(м2 ч)], которую вычисляют по формуле m -m v= 1 2,
Sτ где m1 – масса образца до испытаний, г; m2 – масса образца после испытаний, г; S – площадь поверхности образца, м2; τ – время выдержки, ч.
Результаты исследования и их обсуждение
Результаты испытаний на стойкость к общей коррозии образцов сталей 20ФА, а также механические свойства и данные о микроструктуре приведены в табл. 2. Отметим, что ферритные участки, которые присутствуют в микроструктуре после полной закалки, появляются вследствие малой устойчивости переохлаждённого аустенита низкоуглеродистой мелкозернистой стали. В ходе быстрого охлаждения феррит выделяется при температурах существенно выше мартенситной точки.
По данным табл. 2, наблюдается тенденция к увеличению скорости коррозии с уменьшением размера зерна (ср. режимы 8, 1, 3, 11–14). При высоком отпуске карбиды выделяются, как правило, по границам зерна. Именно там возникает наибольшая химическая неоднородность и действуют гальванические пары, поэтому можно было бы ожидать, что с увеличением протяженности границ скорость коррозии увеличивается. Однако возможно, что при увеличении площади границ уменьшается плотность выделения карбидов, и эффект ослабляется. Возможно, поэтому отмеченная зависимость, представленная также на рис. 1, выражена очень слабо, так что можно говорить лишь о тенденции, а не о закономерности.
Была сделана попытка выяснить, не существует ли закономерной связи между скоростью коррозии и ударной вязкостью образцов. С этой целью на график (рис. 2) были нанесены значения соответствующих характеристик для всех исследованных плавок данной стали. Видно, что зависимость скорости общей коррозии от ударной вязкости отсутствует, эти величины не связаны.
Зависимость скорости общей коррозии от температуры отпуска (после закалки от 880 °C) приведена на рис. 3. На основе анализа этих данных также нельзя говорить о какой-либо взаимосвязи температуры отпуска и скорости коррозии. Этот результат означает, по-видимому, что дисперсность карбидных частиц почти не влияет на скорость коррозии. Но необходимо отметить, что в ходе охлаждения при закалке почти во всех случаях наблюдается выделение феррита. Возможно, что именно неоднородность структуры феррит + отпущенный мартенсит и увеличивает скорость коррозии.
В табл. 2 представлены данные о скорости коррозии образцов стали 20ФА для всех опробованных режимов термической обработки. Разброс результатов очень большой, но можно проанализировать, при каких режимах термообработки наблюдается наименьшая скорость коррозии. Скорость 0,705 мм/год наблюдается после закалки от 880 °C и отпуска при 650 °C (режим 7). Однако после обработки образцов по сходному режиму 12 с отпуском при 670 °C скорость коррозии составила 1,07 мм/год, что близко к максимальному значению среди всех режимов. Трудно себе представить, что изменение температуры отпуска на 20 °C может привести к столь значительному изменению скорости коррозии. При этом микроструктура образцов после отпуска при 650 и 670 °C оказывается очень близкой.
Таблица 2
Результаты испытаний на стойкость к общей коррозии образцов из стали 20ФА
№ режима |
Режим термической обработки |
KCV–50, Дж/мм2 |
Балл зерна |
Микроструктура |
Общая коррозия, мм/год |
1 |
Н 880 °С, 2 ч + З 780 °С, 1,5 ч + О 710 °С, 1 ч, воздух |
2,13 |
10 |
70 % Ф + 30 % С отп (С отп в виде прослоек) |
0,74 |
2 |
З 780 °С, 1, ч + О 710 °С, 1 ч, воздух |
1,66 |
10 |
50 % Ф + 50 % С отп |
0,78 |
3 |
З 880 °С, 1 ч + З 780 °С, 1,5 ч + О 710 °C, 1 ч, воздух |
1,95 |
12 |
Ф + К сф по границам зёрен |
1,05 |
4 |
З 880 °C, 1,5 ч + О 710 °C ,1 ч, воздух |
1,89 |
11 |
Ф + К сф |
0,95 |
5 |
З 1050 °C, 1 ч + О 710 °C, воздух |
1,87 |
6 |
Ф + К сф (свободный Ф отсутствует). Ряд К на месте мартенситных игл |
0,86 |
6 |
Н 880 °C, 1 ч |
1,32 |
9 |
Ф + П (сорбитообразный) |
1,00 |
7 |
З 880 °C, 1 ч + О 650 °C, 1 ч, воздух |
2,15 |
11 |
Ф + К сф (равномерно распределённые) |
0,71 |
8 |
Н 1000 °C, 1 ч + Н 880 °C, 1 ч |
1,73 |
8 |
Ф+П (сорбитообразный) |
0,74 |
9 |
Н 1050 °C, 1 ч |
0,62 |
6 |
Ф + П (пластинчатый) + Ф видм |
0,96 |
10 |
З 880 °C, 1 ч, + О 550 °C, 1 ч, воздух |
2,16 |
11 |
Ф + П (сорбитообразный) + бейнит |
0,91 |
11 |
З 880 °C 1 ч + З 780 °C, 1 ч + О 650 °C 1 ч, воздух |
2,10 |
11 |
Ф + К сф по границам зёрен |
1,12 |
12 |
З 880 °C, 1 ч + О 670 °C, 1 ч, воздух |
2,03 |
12 |
Ф + П (сорбитообразный) + К сф по границам зёрен |
1,07 |
13 |
З 880 °C, 1 ч + О 710 °C, 1 ч, вода |
1,27 |
11 |
Ф + К сф по границам зёрен |
1,08 |
14 |
З 880 °C, 1 ч + О 710 °C, 1 ч, воздух |
2,22 |
11 |
Ф + К сф по границам и по телу зёрен |
1,05 |
Примечание. З – закалка; О – отпуск; Н – нормализация; Ф – феррит; Ф видм – видманштеттов феррит; П – перлит; С отп – сорбит отпуска; К – карбиды; К сф – сфероидизированные карбиды.
1,2
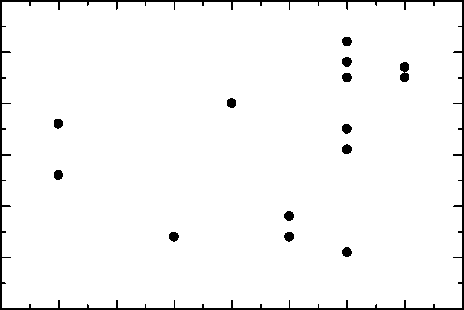
s 1,0 co s 0,9
о 0,8 Q.
2 0,7 о
0,6
5 6 7 8 9 10 11 12 13
Балл зерна
Рис. 1. Распределение скорости общей коррозии в зависимости от балла зерна для образцов из стали 20ФА
о
1,2
1,1
1,0
0,9
0,8
0,7
0,6
0,5
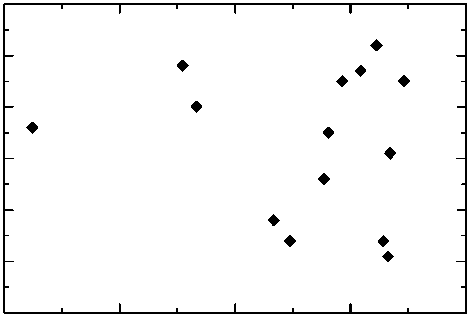
1,0 1,5 2,0
KCV –50, Дж/мм2
2,5
Рис. 2. Распределение скорости общей коррозии в зависимости от ударной вязкости для образцов из стали 20ФА
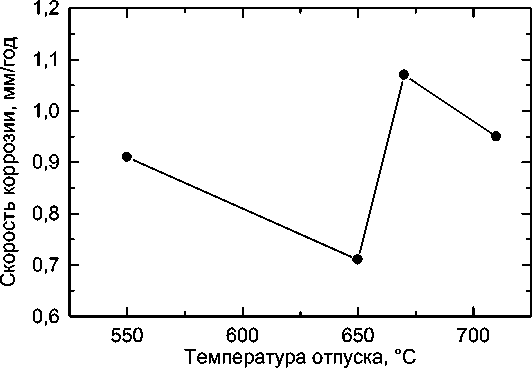
Рис. 3. Скорость общей коррозии образцов стали 20А после различных режимов термической обработки
Если повысить температуру отпуска до 710 °C, то структура существенно изменяется: карбиды сосредотачиваются по границам ферритных зёрен, а сами зёрна разрастаются, вероятно, вследствие рекристаллизации мартенситных кристаллов. В этом случае можно было бы ожидать наибольшую концентрационную неоднородность и наибольшую скорость коррозии, но последняя оказывается такой же, как и после отпуска при 670 °C. По-видимому, существует скрытый фактор, имеющий отношение не к структуре, а к химии процесса растворения (например, образование защитных плёнок), случайные и слабые изменения которого под влиянием структурных преобразований определяют разброс результатов. Роль случайного фактора могут играть и неметаллические включения, по- скольку образцы не всегда принадлежали к одной плавке.
Закалка от 880 °C с последующей межкритической закалкой от 780 °C и отпуском при 650 °C (режим 11) дала в отношении скорости коррозии наихудший результат, подчёркивающий, что глобальное перераспределение углерода и легирующих элементов между α - и γ -фазами в условиях выдержки в межкритическом интервале усиливает коррозию.
Результаты испытаний на стойкость против общей коррозии термообработанных по различным режимам образцов из стали 20А приведены в табл. 3 и на рис. 4. Из них видно, что для образцов из стали 20А также отсутствует взаимосвязь структуры и скорости коррозии. Наибольшая скорость наблюдается после закалки от 880 °C и отпуска при 670 °C,
Таблица 3
Результаты испытаний образцов из стали 20А
№ режима |
Режим термической обработки |
KCV–50, Дж/мм2 |
Балл зерна |
Микроструктура |
Общая коррозия, мм/год |
15 |
З 880 °C, 1 ч + О 730 °C, 1 ч, воздух |
2,47 |
11 |
Ф + К сф по границам зёрен |
0,83 |
16 |
З 780 °C + О 690 °C, воздух |
2,08 |
8 |
Ф + К сф по границам и по телу зёрен + пластинчатые К |
0,84 |
17 |
Н 880 °C,1 ч |
1,45 |
6 |
Ф + П |
0,94 |
18 |
З 880 °C, 1 ч + О 670 °C, 1 ч, воздух |
2,33 |
11 |
Ф + Кс ф по границам и по телу зёрен |
1,09 |
Примечание. З – закалка; О – отпуск; Н – нормализация; Ф – феррит; П – перлит; К – карбиды; К сф – сфероидизированные карбиды.
1,1
СЕ i 1,0
s' s co s 0,9
a. 0,8 о
0,7
-
• 14
•6
О 17
о 15 ° 16
•2
Закалка Закалка Нормализация от 880 °C от 780 °C от 880 °C
Рис. 4. Сравнение стойкости к общей коррозии образцов из сталей 20ФА (сплошные кружки) и 20А (пустые кружки) после термической обработки по различным режимам. Номера режимов указаны у точек в соответствии с табл. 2 и 3
наименьшая – после закалки от 880 °C и отпуска при 730 °C.
Вывод
Полученные результаты не дают чёткой картины влияния микролегирования ванадием, а также различных режимов термической обработки, приводящей к существенному изменению структуры и механических свойств низколегированных трубных сталей 20А и 20ФА, на скорость общей коррозии. Влияние этих факторов невелико, а определяющим является, по-видимому, химический фактор условий образования оксидной плёнки на поверхности образцов.
Список литературы Влияние структурных и фазовых изменений при термической обработке трубных сталей на скорость общей коррозии
- Ефимов, А.П. Химическое сопротивление материалов/А.П. Ефимов. -М.: Нефть и газ, 2004. -254 с.
- Семенова, И.В. Коррозия и защита от коррозии/И.В. Семенова. -М.: Физматлит, 2002. -335 с.
- Сухотин, А.М. Способы защиты оборудования от коррозии/А.М. Сухотин, Е.И. Чекулаев. -М.: Химия, 1987. -280 с.
- ГОСТ 1497-84. Металлы. Методы испытания на растяжение. -М.: Изд-во стандартов, 1997. -36 с.
- ГОСТ 9454-78. Металлы. Метод испытания на ударный изгиб при пониженных, комнатной и повышенных температурах. -М.: Изд-во стандартов, 1990. -14 с.
- ГОСТ 9.908-85. Единая система защиты от коррозии и старения. Металлы и сплавы. Методы определения показателей коррозии и коррозионной стойкости. -Введ. 1987-01-01. -М.: Изд-во стандартов, 1999. -17 с.