Влияние структуры и свойств на износ покрытия Micro Melt NT-60 после плазменной порошковой наплавки
Автор: Паркин А.А., Жаткин С.С., Минаков Е.А.
Журнал: Известия Самарского научного центра Российской академии наук @izvestiya-ssc
Рубрика: Системные разработки трибологии машин и приборов
Статья в выпуске: 4-3 т.13, 2011 года.
Бесплатный доступ
В работе представлены результаты исследований на абразивный износ покрытия Micro Melt NT-60, сформированного плазмен-ной порошковой наплавкой при токах дуги 70А, 85А и 100А. Определены некоторые закономерности износа в зависимости от формируемой структуры и свойств наплавленного материала, а также тока плазменной дуги. Установлены изменения элемент-ного состава в наплавленном слое и показана его связь с износом материала.
Плазменная наплавка, износостойкость, микроструктура, микротвердость, рентгеноспектральный микроанализ
Короткий адрес: https://sciup.org/148205538
IDR: 148205538
Текст научной статьи Влияние структуры и свойств на износ покрытия Micro Melt NT-60 после плазменной порошковой наплавки
ке. Для наплавки применялся порошок с размером частиц 40 - 150 мкм.
Структура наплавленного материала исследовалась на оптическом микроскопе МИМ-8. Изучение микроструктуры и микроанализ зон наплавки проводились на аналитическом растровом электронном микроскопе JSM-6390A фирмы JEOL , измерение микротвердости осуществлялось по стандартной методике с использованием микротвердомера ПМТ-3. Испытания на линейный износ были проведены на установке Универсал-1А, собранной на базе сверлильного станка СС-13/350 [7,8]. Испытания проводились локально в четырех участках зоны наплавки (рис.1). Это связано с тем, что при плазменной наплавке величина тепловложения возрастала от начала к концу наплавки, что приводило к разогреву образца и к некоторому изменению условий формирования структуры и свойств наплавленного материала. Точка 1 (рис. 1) соответствует началу наплавки, а точка 4 – концу наплавки. Высота наплавленного слоя после шлифовки в зоне трения составила 0,4 мм. Контртело было изготовлено из стали 40Х (закалка до HRC 46-48) в виде трубки внешним диаметром 6 мм.
Испытания проводились при нормальной нагрузке в 26 кгс, в течение 10 минут, с частотой вращения шпинделя 600 об/мин. При испытаниях использовалась алмазная паста марки АСМ-3/2-НОМГ.
Pезультаты испытаний на износ. В табл. 1 представлены результаты испытаний наплавленного материала в различных зонах (рис.1) при токах плазменной дуги 70А, 85А и 100А. Площадь трения составляла 1,57*10-5м2. Схема расположения зон трения показана на рис. 1.
Наибольший износ наплавленного материала, сформированного при токе плазменной дуги 70А, происходит в начале наплавки (зона трения №1), к концу наплавки происходило уменьшение величины износа (зона трения №4). Величина износа существенно отличается по ширине наплавленной дорожки - она значительно больше на ее внутреннем крае, чем на внешнем. С ростом тока дуги происходит увеличение величины износа, при этом снижается разброс его значений по внутреннему и внешнему краю наплавленной дорожки. Наблюдается корреляция между изменением величин износа и коэффициента трения для различных зон трения, но в рамках одного образца. На рис. 2 представлена структура зон трения. В наплавленном материале Micro Melt NT-60 при токе дуги 70А (рис.2, а) в зонах трения происходит увеличение плотности карбидов, что приводит к снижению величины износа (табл. 1). При токе дуги 85А (рис.2, б) произошло уменьшение плотности карбидов, что привело к увеличению величины износа.
Плотность карбидов и её изменение в зонах трения наплавленного Micro Melt NT-60 при токе дуги 100А незначительно. Изменение размеров и плотности карбидов зависит от тока плазменной дуги и высоты зоны наплавки, что связано с их седиментацией.
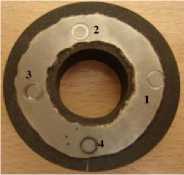
Рис. 1. Расположение зон трения:
1 – начало наплавки; 4 – конец наплавки
На рис. 3 показано изменение микротвердости по высоте зоны наплавки. Микротвердость изменяется скачкообразно по высоте наплавки, что указывает на неоднородность структуры, связанную с неравномерным распределением карбидной фазы. Наиболее равномерная структура формируется во внутренней зоне наплавки. Среднее значение микротвердости составляет <Нμ = 350-400кг/мм2>.
Поверхность трения (пунктирная линия) наплавленного Micro Melt NT-60 при токе дуги 70А (рис.3, а ) находится в области наибольшей плотности карбидной фазы, где микротвердость достигает 700 кгс/мм2. В соотвествии с этим износ данной поверхности трения минимален (табл.1). При токах дуги 85А и 100А микротвердость поверхности трения в основном определяется твердостью никелевой связки, которая значительно ниже микротвердости зон с большим содержанием карбидной фазы. Соответственно износ данных повер-хностей существенно выше. То есть величина износа зависит также от плот-ности карбидов и твердости никелевой основы. На рис.4 и в табл.2 представлены результаты исследований изменения микроструктуры наплавленного Micro Melt NT-60 и микроэлементного состава по ширине, высоте наплавленного материала и непосредственно в зоне трения на высоте наплавленного материала, равным 0,4 мм.С увеличением тока плазменной дуги до 85А происходит измельчение карбид-ной фазы и увеличение ее плотности по объему. В тоже время при токе плазменной дуги 100А происходит рост карбидов и уменьшение их плотности. Это однозначно наблюдается на внешнем крае, но менее заметно на внутреннем крае наплавленной дорожки.
Таблица 1. Зависимость величины износа в различных зонах трения
№ зоны трения |
И 1 , мкм |
И 2 , мкм |
<И>, мкм |
μ |
ΔT0С |
I Д =70А |
|||||
1 |
58 |
29 |
43,5 |
0,11 |
10 |
2 |
29 |
27 |
28 |
0,09 |
11 |
3 |
15 |
33 |
24 |
0,09 |
7 |
4 |
8 |
5 |
6,5 |
0,071 |
8 |
<25,5> |
|||||
І Д = 85А |
|||||
1 |
51 |
20 |
35,5 |
0,1 |
10 |
2 |
50 |
22 |
36 |
0,1 |
11 |
3 |
55 |
23 |
39 |
0,11 |
7 |
4 |
58 |
25 |
41,5 |
0,1 |
8 |
<38> |
|||||
І Д = 100А |
|||||
1 |
62 |
21 |
41,5 |
0,077 |
8 |
2 |
65 |
15 |
40 |
0,069 |
6 |
3 |
59 |
13 |
36 |
0,054 |
5 |
4 |
56 |
12 |
34 |
0,046 |
8 |
<38> |
Примечание: И 1 – величина износа внутреннего края наплавленной дорожки, И 2 – величина износа внешнего края наплавленной дорожки.
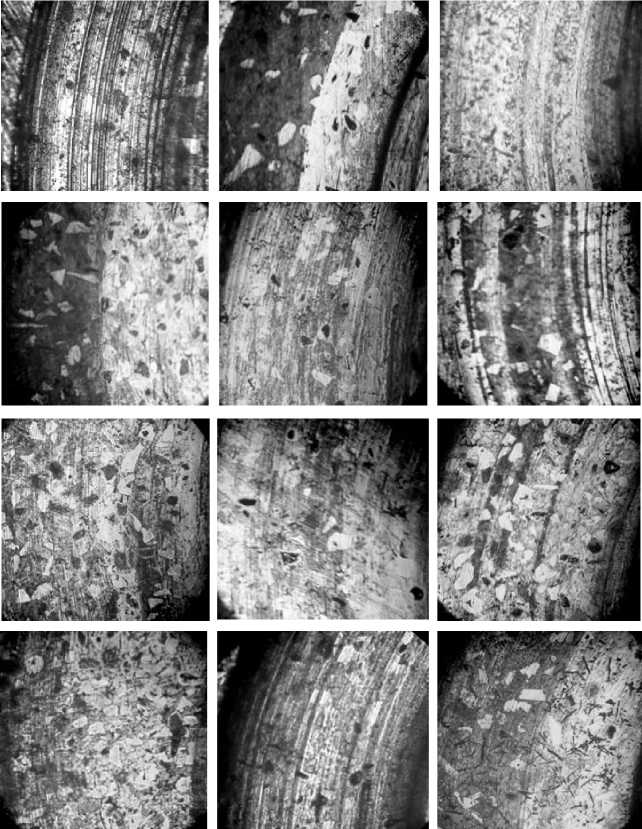
Зона трения №1
Зона трения №2
Зона трения №3
Зона трения №4
а
б
в
Рис. 2. Структура зон трения: а – Iд =70А; б – Iд =85А; в – Iд =100А; х105.
H μ , кгс/мм2
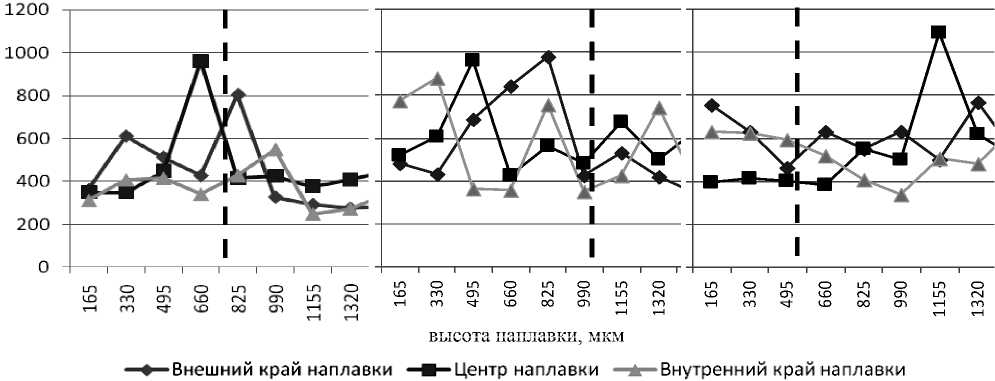
высота наплавки мкм
б
в
Рис. 3. Микротвердость наплавленного Micro Melt NT-60 по высоте наплавки: а – Iд =70А; б – Iд =85А; в – Iд =100А; пунктирная линия – зона трения.
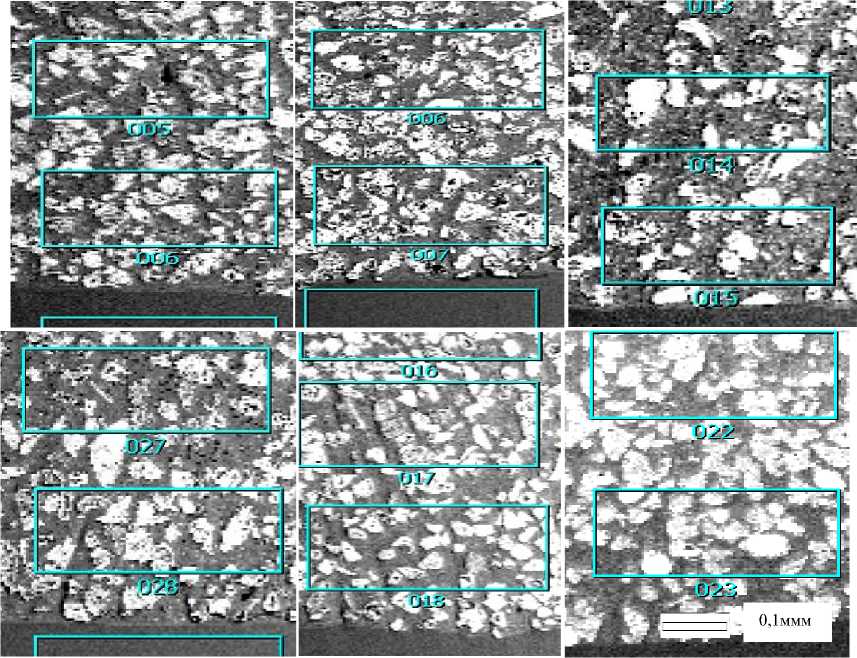
внешний край внутренний край
а
б
в
Рис. 4. Структура зоны наплавки по высоте: а – Iд =70А; б – Iд =85А; в – Iд =100А.
Таблица 2. Элементный спектральный анализ по зонам
№ зоны Микроанализа |
C |
Cr |
Fe |
Co |
Ni |
W |
Total(Mass%), зона наплавки |
I Д =70А |
|||||||
5 |
2,99 |
0,36 |
13,85 |
0,06 |
41,55 |
41,18 |
100 (внешний край) |
17 |
4,15 |
0,37 |
13,33 |
0,2 |
37,67 |
44,28 |
100 (внутренний край) |
I Д =85А |
|||||||
2 |
3,19 |
0,38 |
20,94 |
0,06 |
33,6 |
41,83 |
100 (внешний край) |
27 |
3,07 |
0,45 |
23,02 |
0,11 |
37,15 |
36,2 |
100 (нутренний край) |
I Д =100А |
|||||||
13 |
3,41 |
0,53 |
36,22 |
0,3 |
38,4 |
21,14 |
100 (внешний край) |
22 |
2,55 |
0,47 |
30,36 |
0,27 |
31,47 |
34,88 |
100 (нутренний край) |
Непосредственно на поверхности зоны трения плотность мелких карбидов более высокая при токах дуги 70А и 85А.
Наблюдается также седиментация карбидов, особенно при токе плазменной дуги 100А, что приводит к резкому уменьшению карбидов в зоне трения (рис.4, верхняя граница) и соответственно повышение их плотности от поверхности наплавленного материала ко дну ванны расплава. Данный экспериментальный факт может указывать на неравно-мерность величины износа наплавленного Micro Melt NT-60 по высоте наплавки.
Повышение тока плазменной дуги вызывает возрастание неравномерности распределения элементного состава по ширине и глубине наплавленного Micrо Melt NT-60 - концентрации железа с ростом высоты зоны и тока дуги плазменной наплавки и уменьшение концентрации карбидов вольфрама. В целом это приводит к неравномерности износа наплавленного материала по ширине и высоте зоны наплавки, что подтверждается экспериментально в данной работе.
На рис. 5 представлено изменение микроструктуры наплавленного Micro Melt NT-60 в зоне трения в зависимости от токов плазменной дуги. При плазменной наплавке с ростом тока дуги происходит измельчение карбидов вольфрама в результате их распада и растворения в жидком связующем никеле. Данный процесс резко интенсифицируется при токах плазменной дуги выше 85А и более активно протекает на внутреннем крае наплавляемой дорожки.
Рентгеноспектральный микроанализ показывает, что наряду с карбидами вольфрама в зоне наплавки образуются карбиды железа (темные пластинчатые структуры), сложные карбиды или диффузионные области железа в карбиде вольфрама (темные области в карбидах вольфрама), растворы железо-никель, железо-никель – вольфрам (светлые вкрапления на темном фоне). Вольфрам в никеле растворяется в жидкой фазе в результате распада карбидов вольфрама.
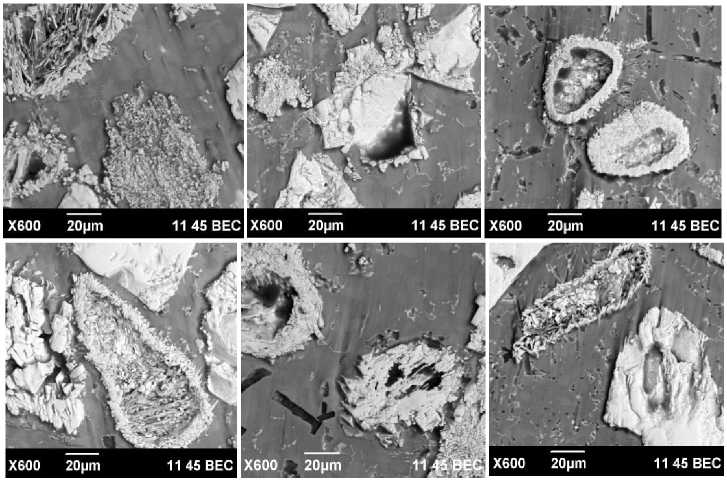
Внутренний край зоны наплавки
Внешний край зоны наплавки
б
а
в
Рис. 5. Структура зоны наплавки по высоте: а – Iд =70А; б – Iд =85А; в – Iд =100А.
То есть при плазменной наплавке в наплавленном Micro Melt NT-60 происходит упрочнение никелевой связки за счет растворения в ней железа, вольфрама и мелких частиц карбида вольфрама, что соответственно приводит к увеличению ее твердости и уменьшению величины износа плазменно-наплавленного Micro Melt NT-60.
Выводы. На основе проведенных испытаний по локальному износу и комплексных экспериментальных исследований структуры, микротвердости, рентгеноспект-рального анализа можно сделать следующие выводы:
-
1. Величина износа существенным образом зависит от времени и тока дуги плазменной наплавки. С ростом тока плазменной дуги величина износа возрастает.
-
2. На величину износа сильное влияние оказывает структура наплавленного слоя. С ростом плотности карбидов в зоне трения величина износа уменьшается.
-
3. Степень износа наплавленного Micro Melt NT-60 зависит от твердости связующего материала, свойства которого изменяются в результате легирования вольфрамом, карбидами вольфрама, растворения в ней железа и образованием более сложных карбидов, таких как (Fe, W)С.
Список литературы Влияние структуры и свойств на износ покрытия Micro Melt NT-60 после плазменной порошковой наплавки
- Паркин А.А., С. С. Жаткин, Минаков Е. А. Оптимизация технологии плазменной наплавки порошковых материалов. Металлургия машиностроения. -2011. -№ 1. -С.44-49.
- Жаткин С. С., Паркин А.А., Минаков Е. А., Семин А.Б., Сибикин А.В., Скворцов А.А. Влияние расхода порошка и толщины подложки на процесс плазменной порошковой наплавки Stellite 190W на стали.//Материалы 9 Международной практической конференции-выставки "Технология ремонта, восстановления и упрочнения деталей машин, механизмов…." Санкт-Петербург. 2010. -С.220-225.
- Паркин А.А., Жаткин С. С., Макейкин И.В, Харымов А.А., Писарев Д.А. Определение оптимальных режимов плазменной наплавки Stellite 12.//Материалы международной научно-технической конференции "Актуальные проблемы трибологии". Самара. СамГТУ. 6 -8 июня 2007 г. С. 121-124.
- Ana Sofia C.M. D' Oliveira, Paulo Sergio C.P. da Silva, Rui M.C. Vilar. Microstructural features of consecutive layers of Stellite 6 deposited by laser cladding.//Surface and Coatings Technology 153 (2002) 203-209.
- ZHU Yuan-zhi, YIN Zhi-min, TENG Hao. Plasma cladding of Stellite 6 powder on Ni76Crl9AlTi exhausting valve.//Trans. Nonferrous Met. Soc. China 17 (2007) 35-40.
- Hazoor Singh Sidhu, Buta Singh Sidhu, S. Parkashc. Characteristic Parameters of HVOF sprayed NiCr and Stellite-6 coatings on the boiler steels using LPG as fuel gas.//International Journal of Engineering and Information Technology Copyright© 2010 waves publishers IJEIT 2010, 2(2), 133-139
- Ибатуллин И.Д. Кинетика усталостной повреждаемости и разрушения поверхностных слоев//Монография/И.Д. Ибатуллин -Самара: Самар. гос. техн. ун-т, 2008. -387 с.: ил. ISBN -978-5-7964-1211-4.
- Ибатуллин И.Д. Новые методы и приборы для экспрессной оценки энергетических параметров усталостной повреждаемости и разрушения поверхностных слоев.//Диссертация на соискание ученой степени д. т. н. Специальность: 01.04.01. Год: 2010.