Влияние технологических параметров на элементный состав микродугового оксидирования покрытий на алюминиевых и титановых сплавах
Автор: Михеев А.Е., Гирн А.В., Орлова Д.В., Вахтеев Е.В., Трушкина Т.В.
Журнал: Сибирский аэрокосмический журнал @vestnik-sibsau
Рубрика: Технологические процессы и материалы
Статья в выпуске: 4 (44), 2012 года.
Бесплатный доступ
Проведены исследования по определению элементного состава микродугового оксидирования покрытий из алюминиевых и титановых сплавов. Установлена зависимость химического состава покрытия от технологических режимов и различных составов электролитов.
Микродуговое оксидирование, титановые сплавы, алюминиевые сплавы, элементный анализ
Короткий адрес: https://sciup.org/148176896
IDR: 148176896
Текст научной статьи Влияние технологических параметров на элементный состав микродугового оксидирования покрытий на алюминиевых и титановых сплавах
Алюминиевые и титановые сплавы широко применятся в аэрокосмической и других областях промышленности, что связано с их высокими удельными характеристиками. Однако существуют области, где применение этих сплавов ограничено их невысокой твердостью и износостойкостью. В связи с этим актуальной является задача поверхностного упрочнения алюминиевых и титановых сплавов. Перспективным методом поверхностного упрочнения является микро-дуговое оксидирование (МДО) [1–5]. Упрочнение металлов при МДО происходит за счет образования на поверхности металла покрытия, которое состоит из оксида металла подложки и оксидов химических элементов, входящих в состав электролита [3].
Важной задачей, особенно при получении покрытий различной цветовой гаммы и покрытий с высокой излучающей способностью, является качественное и количественное определение их химического состава.
В процессе формирования МДО-покрытия большую роль играют плазмохимические и термические процессы, в результате которых на поверхности образуются сложные химические соединения.
Так в растворе силиката натрия при микродуговом оксидировании алюминиевых сплавов химическая реакция протекает по следующей схеме [2]:
2Al + 3H2O ^ Al2O3 + 3H2
Установлено что полученные покрытия состоят в большинстве случаев из аморфного Al 2 O 3 , хотя при определенных условиях наблюдается образование γ-Al 2 O 3 .
Термическое воздействие может оказывать влияние и на другие компоненты электролита, вызывая их гидролиз (например, солей, образованных слабой кислотой и сильным основанием). Степень такого воздействия увеличивается с ростом температуры и концентрации электролита, которая сильно повышается в приэлектродном слое из-за выкипания воды:
Na2SiO3 ^ NaHSiO3 ^ H2SiO3
Далее, претерпевая термическую дегидратацию, кремниевая кислота H 2 SiO 3 дает диоксид кремния SiO 2 в виде α-кристаболлита и/или α-кварца, что и наблюдается при микродуговом оксидировании в растворах, содержащих силикаты. При МДО на алюминиевом электроде возможно образование силлиманита:
Al2O3 + SiO2 ^ Al2SiO 5
Введение в состав электролитов солей переходных металлов, например, для окрашивания, повышения твердости и других физико-механических свойств, приводит к повышенному содержанию этих металлов в МДО-покрытии и образованию большого количества оксидов различных металлов. Так, по данным работы [6], при обработке алюминия в электролите, содержащем гексафторалюминат натрия, тартрат калия, фторид натрия и гидроксид калия, входящий в состав гексафторалюминат-ион гидролизуется, в результате чего образуется гидроксид алюминия, термолиз которого в условиях микроплазменных разрядов приводит к образованию в составе покрытий на алюминии оксида Al 2 O 3 , который в ходе микродугового оксидирования модифицируется фтором:
AlF63 " + 3H2O ^ Al(OH)3 + 3H + + 6F "
2Al(OH)3 t , °C > Al2O3 + 3H2O
Согласно данным элементного анализа, в покрытии образуется оксид алюминия, модифицированный фтором, формула которого может быть представлена в виде Al 2 O 3– x F x , характерном для стеклофазы [6].
При обработке алюминиевых и титановых сплавов [7] в электролите, содержащем дигидрофосфат натрия, ферроцианид калия, вольфрамат натрия или молибден натрия, методом рентгенофазового анализа установлено наличие в покрытии шпинелей FeAl2O4, Al2O3 ■ Fe3O 4 ■ WO3 или
Al2O3 ■ Fe3O 4 ■ MoO3, Al2O3и A1PO 4 на алюминии и его сплавах и Al2O3 ■ TiO2 — на титане и его сплавах. Кроме того, на сплавах алюминия и титана установлено наличие соединения K 3 FeO 4 . Шпинель состава FeAl 2 O 4 , синтез которой осуществляется на алюминиевом аноде, обеспечивает покрытию черный цвет.
При анодной поляризации ферроцианидов происходит анодное окисление последних:
[Fe(CN 6 )] 4 -^ [Fe(CN) 6 ]3 -
Далее, при наличии кислорода идет распад комплексного аниона:
^ Fe ( CN ) 6 J 3 " + 12H 2 O O2 > 4Fe(OH)3 + 12HCN + 12CN "
В результате плазмохимической реакции на аноде имеем
4Al3 + + 3O2 t , °C > 2Al2O3
2Fe(OH)3 t , °C > Fe2O3 + 3H2O
Al2O3 + Fe2O3 сплавление > FeAl 2 O 4
(черного цвета)
Al2O3 + Fe(OH)3 — сплавление м FeAl 2 O 4
Кроме того, черный цвет покрытиям придает соединение K 3 FeO 4 , который получается на аноде сплавлением K 2 O с Fe 2 O 3 в атмосфере кислорода. Аналогичные реакции проходят на титане и его сплавах [7].
При получении на поверхности изделий, выполненных из алюминиевых и титановых сплавов, черных покрытий в электролите, в состав которого входят гексаметафосфат натрия и метаванадат натрия или аммония, результаты рентгенофазового анализа показали, что в них содержатся оксиды ванадия V 4 O 9 и V 2 O 4 . На основании количественных анализов следует, что внешний слой покрытия преимущественно состоит из V 4 O 9 и V 2 O 4 с включением оксидов фосфора и незначительным включением оксидов алюминия. Слой покрытия, прилегающий к металлу, состоит из собственного оксида обрабатываемого металла.
Механизм образования черных пленок со слоистой структурой схематически можно представить следующим образом. Первоначально в доискровой области обработки идет окисление металла с образованием собственного оксида. При достижении определенной толщины пленки появляются искровые разряды. Далее, при достижении определенного напряжения на аноде, механизм образования покрытия претерпевает изменение. Внешне это проявляется в изменении характера искрения на аноде и появлении на серо-белой первичной пленке черных точек зародышей фаз оксидов ванадия. При дальнейшем ведении процесса оксидирования черные участки разрастаются, покрывая всю поверхность пленки. При этом напряжение на аноде остается примерно постоянным. В этот период возникают условия для преимущественного роста пленки за счет оксидов ванадия, что можно объяснить возникновением трудностей в диффузии ионов металла подложки во внешнюю часть растущей пленки за счет формирования объемных зарядов в пленке и образованием микроплазменных разрядов в пространстве между областью объемных зарядов и электролитом, т. е. в поверхностной части растущей пленки, что приводит к ее дальнейшему росту за счет элементов электролита, причем преимущественно за счет оксидов ванадия [8].
При обработке титана [9] в электролите, содержащем алюминат, сульфат, тетраборат натрия и борат алюминия, образуется эмалевидная пленка, плотная, белого цвета, состоящая из рутила TiO 2 , шпинелли Al 2 TiO 5 и корунда α-Al 2 O 3 .
При нанесении покрытия на титановые сплавы [10] в электролите, содержащем фосфат натрия и иодат калия, локальное повышение температуры (до 2800–3000 °С) в момент искрения, приводит к переплавке продуктов оксидирования. Адсорбированные в начальный период анодирования (до 100 В) ионы под воздействием высокого напряжения (400–500 В) и температуры образуют соединения с двуокисью титана типа фосфидов или P2O5, о чем свидетельствует наличие на всех рентгенограммах обширной аморфной фазы, которую на основании данных ОЖЕ-спектроскопии необходимо отнести к соединениям типа фосфидов или P2O5. Фосфорный ангидрид образует с двуокисью титана дифосфат титана по реакции
TiO2 + P2O 5 > TiP2O 7
Кроме того, при сплавлении TiO 2 с фосфатом натрия происходит образование комплексного соединения триортофосфатодититаната натрия:
TiO2 + NaPO3 (распл.) > Na[Ti2 (PO 4 )3 ]
Эти соединения улучшают электрофизические свойства оксидных пленок [3].
В работе [3] авторы, исследуя фазовый состав покрытий, формируемых на титане в фосфатном электролите, пришли к выводу, что появление рутильной фазы связано с возникновением интенсивных микродуг на поверхности анода при высоких потенциалах формирования. Это подтверждает тот факт, что температурный фактор является одним из основных при формировании соответствующих структур при МДО-процессе; при более низких потенциалах формирования в составе покрытий обнаружены TiO 2 (анатаз), TiP 2 O 7 , NaTi 2 (PO 4 ) 3 и аморфная фаза. Образование TiP 2 O 7 на аноднополяризованном электроде из титана возможно в результате взаимодействия оксида титана с ортофосфорной кислотой или с фосфорным ангидридом при воздействии высоких температур:
TiO2 + 2H 3 PO 4 —T-> TiP2O 7 + 3H2O
TiO2 + P2O 5 —> TiP2O 7
На аноде температурный режим для протекания указанных реакций реализуется в зонах пробоя. Синтез триортофосфатодититаната натрия NaTi 2 (PO 4 ) 3 характерен для гидротермальных процессов с системе TiO 2 –NaHPO 4 –H 2 O. Обнаруженные рентгеноаморфные фазы в покрытии, по предположениям авторов, состоят из стеклофаз, формируемых в системе Na 2 O– P2O5–TiO2.
Таким образом, несмотря на большое количество исследований элементного состава МДО-покрытий, количественное соотношение соединений, входящих в покрытие, исследовано недостаточно. Поэтому в работе проведены экспериментальные исследования по определению количественного соотношения химических соединений, входящих в МДО-покрытия, при различных технологических режимах обработки на алюминиевых и титановых сплавах.
Обработке подвергались образцы алюминиевого сплава АМг6. Формирование покрытий проводили в двух электролитах:
– 4 г/л KOH, 10 г/л Na 2 SiO 3 (№ 1);
– 2 г/л KOH, 14 г/л алюминат натрия NaAlO 2 (№ 2).
Обрабатывали образцы в следующих режимах: плотность тока I = 5…40 А/дм 2 ; продолжительность оксидирования – 60 мин; соотношение анодной и катодной составляющей силы тока I к / I a , = 0, –1, 2, температура электролита – 15…40 °С.
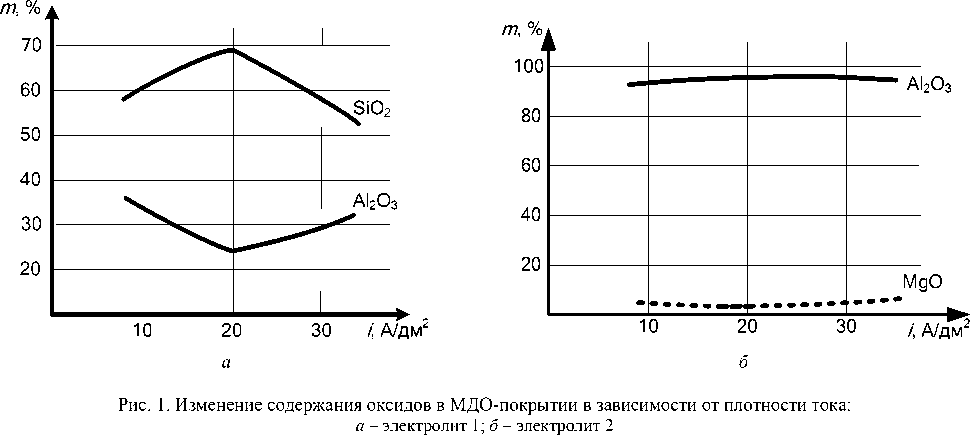
Таблица 1
Составы электролитов и оптимальные параметры технологических режимов
№ образца |
Состав электролита |
Режимы обработки |
1 |
Na 2 HPO 4 – 60 г/л |
t = 20 мин, I = 16 А/дм 2 , U = 360–380 В |
2 |
Na 6 P 6 O 12 – 30 г/л NaVO 3 ·2H 2 O – 20 г/л |
t = 10 мин, I = 32 А/дм2, U = 300–380 В |
3 |
NaH 2 PO 4 – 20 г/л K 4 [Fe(CN) 6 ]·4H 2 O – 25 г/л Na 2 MoO 4 ·2H 2 O – 5 г/л |
t = 30 мин, I = 16 А/дм2, U = 210–300 В |
4 |
Na 2 SiO 3 – 50 г/л KOH –30 г/л |
t = 10 мин, I = 32 А/дм2, U = 250–300 В |
Таблица 2
Результаты химического анализа покрытий
№ образца |
Содержание оксидов в покрытии, % |
||||||
TiO 2 |
P 2 O 5 |
Al 2 O 3 |
SiO 2 |
V 2 O 5 |
Fe 2 O 3 |
Na 2 O |
|
1 |
70,96 |
24,76 |
2,78 |
– |
– |
0,0749 |
– |
2 |
47,19 |
33,08 |
– |
– |
17,37 |
0,184 |
– |
3 |
38,77 |
27,85 |
– |
– |
– |
22,78 |
2,01 |
4 |
39,95 |
– |
1,61 |
57,00 |
– |
0,0652 |
– |
При помощи рентгенофлуоресцентного спектрометра ARL Quant’x исследовался химический состав полученных покрытий (рис. 1). По результатам элементного анализа на образцах алюминиевых сплавов, оксидируемых в электролите 1 было выявлено значительное содержание таких оксидных элементных форм, как SiO 2 и Al 2 О 3 (рис. 1, а ). При обработке в электролите 2 в покрытии выявлен оксид Al 2 О 3 и незначительное количество MgO, образующегося за счет магния, входящего в состав сплава (рис. 1, б ).
В результате исследований выявлено, что наибольшее содержание твердой фазы Al 2 О 3 увеличивается при увеличении катодной составляющей по току (рис. 2).
Также исследовался элементный состав покрытий на титановых образцах, выполненных из сплава ВТ14.
Составы электролитов и параметры технологических режимов приведены в табл. 1.
Результаты исследования элементного состава полученных покрытий приведены в табл. 2.
Поскольку наиболее твердым из соединений в покрытии является TiO 2 , то для получения износостойких покрытий на титановых сплавах обработку необходимо проводить в электролите 1. Дальше исследовалось влияние технологических режимов обработки на содержание TiO 2 в покрытии. Покрытия формировали при соотношениях анодной и катодной составляющих Iк/Iа от 0,6 до 1,2, плотностях тока в диапазоне от 10 до 40 А/дм 2 , в течении 5–30 мин. Полученные результаты представлены на рис. 3.
Химический анализ показывает, что больше всего оксида титана в покрытии, полученном при соотно- шении анодной и катодной составляющих тока Iк = 1, плотности тока i = 40 А/дм2 и времени обработки t =10 мин.
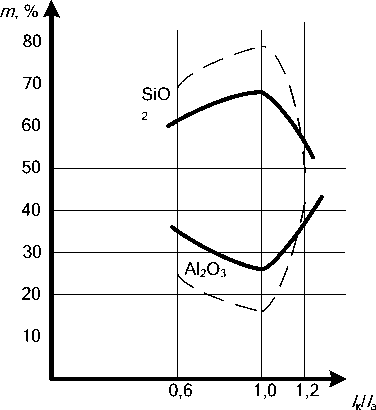
Рис. 2. Изменение химического состава МДО-покрытия в зависимости от I к/ I a в электролите 1:
– i = 10 A/дм 2 ; --- – i = 20 A/дм 2 )
Таким образом, в работе установлена связь между технологическими параметрами МДО обработки и количественным и качественным содержанием химических соединений в покрытии. Выявлены пути повышения содержания химических соединений, обеспечивающих покрытию повышенную износостойкость.