Влияние технологических режимов микродугового оксидирования на пористость и коррозионную стойкость сплава системы Al-Mg-Sc
Автор: Трушкина Т.В., Михеев А.Е., Сиденко Н.А., Раводина Д.В., Гирн А.В.
Журнал: Сибирский аэрокосмический журнал @vestnik-sibsau
Рубрика: Технологические процессы и материалы
Статья в выпуске: 4 т.17, 2016 года.
Бесплатный доступ
Алюминиевый сплав 01570, имеющий в своем химическом составе легирующий элемент скандий, обладает высокими удельными физико-механическими характеристиками, но в агрессивных средах имеет низкую коррозионную стойкость. Для повышения коррозионной стойкости рабочих поверхностей элементов конструкций летательных аппаратов, изготовленных из сплава 01570, предложен метод формирования покрытий микродуговым оксидированием (МДО), в процессе которого на поверхности обрабатываемых материалов образуются плотные оксидные слои. Проведены исследования морфологии, расчет пористости и коррозионной стойкости МДО-покрытий. Алюминиевым сплавам свойственна питтинговая коррозия, переходящая со временем в межкристаллитную. Во избежание проникновения активной коррозионной среды по сквозным порам МДО-покрытия до поверхности алюминиевого сплава, необходимо получать покрытия с минимальной пористостью. Установлено, что с увеличением соотношения катодной и анодной составляющей тока от 0,8 до 1,2 наблюдается уменьшение общей пористости. Для определения коррозионной стойкости сформированных покрытий проводились ускоренные лабораторные испытания согласно ГОСТ 9.308-85 (метод 9). Процесс коррозионного разрушения искусственно ускоряется за счет чередования погружения образцов в коррозийную среду, с последующей сушкой при комнатной температуре. Количественный анализ с применением гравиметрического метода определения скорости коррозии в условиях, имитирующих морскую среду, показал, что убыль веса незначительна, и по расчетам глубинного показателя коррозии покрытия, полученные микродуговым оксидированием на сплаве 01570, относятся к группе совершенно стойких.
Алюминий и его сплавы, пористость, коррозионная стойкость, функциональные покрытия, морфология, микродуговое оксидирование
Короткий адрес: https://sciup.org/148177638
IDR: 148177638
Текст научной статьи Влияние технологических режимов микродугового оксидирования на пористость и коррозионную стойкость сплава системы Al-Mg-Sc
Введение. Алюминиевые сплавы обладают высокой коррозионной стойкостью, так как способны легко пассивироваться, образуя на своей поверхности оксидную пленку толщиной до 20 мкм [1–7]. Однако эксплуатация изделий ракетно-космической техники (РКТ) проходит в экстремальных условиях в присутствии агрессивных сред, поэтому с целью повышения коррозионной стойкости алюминиевых изделий их поверхность модифицируют защитными покрытиями, которые обеспечивают требуемые эксплуатационные характеристики. В ракетно-космической технике все более широко применяется алюминиевый сплав 01570, содержащий в своем химическом составе легирующий элемент скандий, который в растворах или парах солей имеет низкую коррозионную стойкость. На данном этапе развития предприятий данной отрасли актуальным направлением является применение современных методов нанесения защитных покрытий, к которым можно отнести микродуговое оксидирование (МДО). Это процесс модификации поверхности металла в высоковольтном режиме, находящегося в электролите, позволяющий получать многофункциональные покрытия с уникальными физико-механическими свойствами, толщиной более 100 мкм [3–9]. Проведенные ранее металлографические исследования выявили, что покрытия для металлов вентильной группы, полученные при различных режимах МДО-обработки, состоят из следующих слоев: тонкого переходного, прилегающего к металлу и основного рабочего с максимальной твердостью и минимальной пористостью. Тонкий слой обеспечивает высокую адгезионную прочность покрытия с основой, рабочий слой в основном состоит из смеси α-А1 2 О 3 , γ-А1 2 0 3 и наружного технологического, обогащенного алюмосиликатами [7]. Были определены количественные характеристики химического состава покрытия, сформированного на поверхностях образцов из сплава 01570, а также выявлено влияние технологических режимов процесса МДО на толщину оксидного слоя [10–12].
Экспериментальная часть. В данной работе формирование МДО-покрытия проводилось на образцах из алюминиевого сплава 01570 в силикатнощелочном электролите, при фиксированном значении времени оксидирования и плотности тока на установке ИАТ-Т. Регулируемым технологическим параметром процесса являлось значение соотношения катодной и анодной составляющих тока, которое варьировалось в диапазоне от 0,8 до 1,2.
В связи с тем, что коррозионная стойкость и физикомеханические характеристики покрытий являются основополагающими при использовании их в про- мышленности, определяющим исследованием является определение структуры поверхностных слоев покрытия, его пористости и коррозионной стойкости.
Проведенные ранее исследования МДО-покрытий алюминиевых сплавов показывают, что им присуще изменение структуры, с увеличением соотношения катодной и анодной составляющих тока с 0,8 до 1,2. Прослеживается изменение размера и количества пор: их становиться меньше, но их площадь увеличивается. Наличие катодной составляющей тока приводит к разогреву внутренней части покрытия и образованию в этой области высокотемпературных фаз оксидов и оплавлению поверхности слоя, что обеспечивает низкую пористость, повышение физико-механических характеристик и коррозионной стойкости формируемых оксидных структур [13–15].
Алюминиевым сплавам свойственна питтинговая коррозия, переходящая со временем в межкристаллитную. Во избежание проникновения активной коррозионной среды по сквозным порам МДО-покрытия до поверхности самого алюминиевого сплава необходимо получать покрытия с минимальной пористостью. Следовательно, чем меньшее число сквозных пор присутствует в покрытии, тем выше коррозионная стойкость изделия в целом. Для решения данной задачи требуется отработка технологических режимов процесса нанесения покрытий. Исследование пористости покрытий проводили с полученных микрофотографий морфологии при помощи программного обеспечения Siams 700, для чего с кадров микрофотографий морфологии полученных образцов производили визуальный подсчет пор «кратеров» методом выделения каждой области темного цвета на фоне общей светлой площади образца. В табл. 1–3 представлены результаты по динамике изменения пористости и зависимость от технологических режимов процесса МДО.
Для определения коррозионной стойкости сформированных покрытий проводились ускоренные лабораторные испытания согласно ГОСТ 9.308–85 (метод 9). Суть данного метода заключается в том, что процесс коррозионного разрушения искусственно ускоряется за счет чередования погружения образцов в условия, имитирующие морскую среду, с последующей сушкой при комнатной температуре. Испытания проводились в течение 336 часов. Образцы до и после коррозионных испытаний показаны на рис. 1, 2.
При визуальном осмотре образцов на поверхностях обнаружено отложение солей в виде кристаллов (рис. 2). Повреждений, связанных с воздействием коррозионной среды, не наблюдается. Покрытие сохранило свою целостность, что свидетельствует о его высокой коррозионной стойкости в условиях, имитирующих морскую среду.
В работе использовался количественный анализ с применением гравиметрического метода определения скорости коррозии, сущность которого заключается в измерении веса образца до проведения испытаний и после удаления продуктов коррозии. По полученным значениям масс образцов проводили расчет глубинного показателя коррозии. Из расчетов скорости коррозии определено, что с увеличением соотношения составляющих тока от 0,8 до 1,2 скорость коррозии снижается, защитные свойства повышаются. Зависимость изменения скорости коррозии от соотношения катодной и анодной составляющих тока представлена на рис. 3.
Таблица 1
Пористость МДО-покрытий на сплаве 01570 Ik/Iа = 0,8
Число пор |
Минимальное значение, мкм2 |
Максимальное значение, мкм2 |
Среднее значение, мкм2 |
|
Площадь |
1509 |
0,26 |
487,61 |
20,99 |
Периметр |
1509 |
1,43 |
308,22 |
21,57 |
Таблица 2
Пористость МДО-покрытий на сплаве 01570 Ik / Iа = 1
Число пор |
Минимальное значение, мкм2 |
Максимальное значение, мкм2 |
Среднее значение, мкм2 |
|
Площадь |
1484 |
0,30 |
344 |
13,09 |
Периметр |
1484 |
1,55 |
209,5 |
14,90 |
Таблица 3
Пористость МДО-покрытий на сплаве 01570 Ik / Iа = 1,2
Число пор |
Минимальное значение, мкм2 |
Максимальное значение, мкм2 |
Среднее значение, мкм2 |
|
Площадь |
1357 |
0,28 |
700,59 |
14,49 |
Периметр |
1357 |
1,51 |
432,4 |
16,10 |
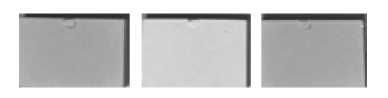
Рис. 1. Образцы сплава 01570 с МДО-покрытием до проведения коррозионных испытаний
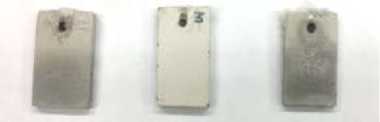
Рис. 2. Образцы сплава 01570 с МДО-покрытием после коррозионных испытаний
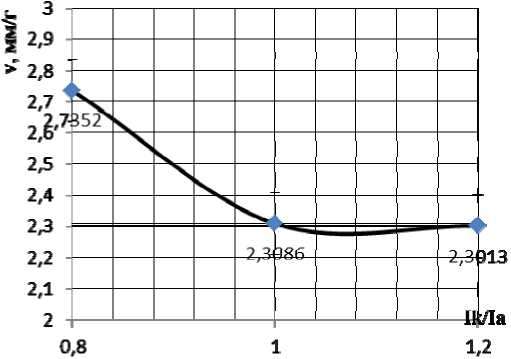
Рис. 3. Зависимость скорости коррозии МДО-покрытий на сплаве 01570 от соотношения катодной и анодной составляющих тока
Покрытия, полученные на алюминиевом сплаве 01570, относятся к группе совершенно стойких в условиях, имитирующих морскую среду. Оценка покрытий по отношению к группам коррозионной стойкости осуществлялась по результатам расчета глубинного показателя коррозии согласно ГОСТ 5275–68 [16].
Заключение. В ходе проведения экспериментальных исследований установлено:
– для достижения минимальной пористости и высокой коррозионной стойкости покрытия вести процесс МДО целесообразнее при соотношении катодной и анодной составляющих тока Ik/Iа от 1 до 1,2;
– МДО-покрытия, формируемые на сплаве 01570, обладают высокими защитными характеристиками от воздействия агрессивных сред.
Применение технологии микродугового оксидирования для получения покрытий на сплаве 01570 с высокими антикоррозионными свойствами актуально для предприятий оборонно-промышленного комплекса, изготавливающих изделия, эксплуатируемые в экстремальных условиях.
Список литературы Влияние технологических режимов микродугового оксидирования на пористость и коррозионную стойкость сплава системы Al-Mg-Sc
- Модель перехода анодирования в микродуговой режим/В. И. Белеванцев //Изв. СО АН СССР. Сер. хим. наук. 1989. Вып. 6. С. 73-81.
- Область применения и свойства покрытий, получаемых микродуговым оксидированием/Э. С. Атрощенко //Физика и химия обработки материалов. 1996. № 3. С. 8-11.
- Вячеславов П. М., Шмелева Н. M. Методы испытаний электролитических покрытий. Л.: Машиностроение, 1977.
- Федоров В. А. Модифицирование микродуговым оксидированием поверхностного слоя деталей/В. А. Федоров. М.: Энергия, 1992. 190 с.
- Булычев С. И., Федоров В. А., Данилевский В. П. Кинетика формирования покрытия в процессе микродугового оксидирования//Физика и химия обработки материалов. 1993. № 6. С. 53-59.
- Марков Г. А., Слонова А. И., Терлеева О. П. Химический состав, структура и морфология микроплазменных покрытий//Защита металлов. 1997. Т. 33, № 3. С. 289-294.
- Технологические возможности микродугового оксидирования алюминиевых сплавов/А. Е. Михеев //Вестник машиностроения. 2003. № 2. С. 56-63.
- Тихоненко В. В., Шкилько А. М. Диагностика наружного слоя покрытия, полученного микродуговым оксидированием на сплавах алюминия//Вестник НТУ «ХПИ»: сб. науч. тр. 2010. № 47. С. 119-125.
- Белецкий В. М., Кривов Г. А. Алюминиевые сплавы (состав, свойства, технология, применение). Киев: КОМИНТЕХ, 2005. 365 с.
- Микродуговое оксидирование: теория, технология, оборудование/И. В. Суминов //М.: Экспо. 2005. 368 с.
- Земскова Е. П. Технологическое обеспечение коррозионной стойкости деталей из алюминиевых сплавов формированием тонких МДО-покрытий: автореф. дис. … канд. техн. наук. М., 2009. 20 с.
- Химические процессы при микродуговом оксидировании/А. Е. Михеев //Вестник СибГАУ. 2013. Вып. 2 (48). С. 212-216.
- Морфология и пористость поверхности оксидных покрытий/Т. В. Трушкина //Вестник СибГАУ. 2014. Вып. 2 (54). С. 144-148.
- Трушкина Т. В. Технология формирования высокопрочных коррозионно-стойких покрытий на алюминиевых сплавах микродуговым оксидированием: автореф. дис. … канд. техн. наук. Красноярск, 2015. 123 с.
- Разработка функциональной схемы влияния основных факторов процесса микродугового оксидирования на свойства покрытий/Т. В. Трушкина //Вестник СибГАУ. 2015. Т. 16, № 2. С. 464-469.
- ГОСТ 5272-68. Защита от коррозии. Ч. 4. Методы натурных испытаний. М.: Изд-во стандартов, 1999. 10 с.