Влияние термической и термоциклической обработки на структуру и свойства мартенситно-стареющей стали
Автор: Биронт Виталий С., Крушенко Генрих Г.
Журнал: Журнал Сибирского федерального университета. Серия: Техника и технологии @technologies-sfu
Статья в выпуске: 3 т.1, 2008 года.
Бесплатный доступ
В статье рассмотрено изменение фазового состава мартенситно-стареющей стали (МСС) 03Х11Н10М2Т-ВД в зависимости от режимов термической (ТО) и термоциклической обработки (ТЦО) в температурной области α-γ превращения. Предварительная ТО и ТЦО повышает размерную точность изделий при последующей закалке и увеличивает стойкость к коррозионному разрушению под напряжением. Использование предварительной термической обработки позволяет регулировать эксплуатационные свойства путем изменения фазового состава, температуры старения мартенситно-стареющей стали.
Мартенситно-стареющая сталь, термическая обработка, термоциклическая обработка, фазовый состав, свойства
Короткий адрес: https://sciup.org/146114467
IDR: 146114467
Текст научной статьи Влияние термической и термоциклической обработки на структуру и свойства мартенситно-стареющей стали
Мартенситно-стареющие стали (МСС) являются одними из наиболее перспективных материалов для создания современных высокопрочных, коррозионностойких изделий, работающих в условиях повышенных и сверхнизких температур, при высоких давлениях, благодаря специфическому механизму упрочнения, высокой прочности и технологичности таких материалов.
За последнее время накоплена обширная информация по МСС [1-4] как в основном классическом варианте (легирование высоконикелевых сталей молибденом и кобальтом), так и экономнолегированных сталей с минимальным содержанием дорогих и дефицитных элементов. Широкое применение в различных конструкциях, работающих в агрессивных средах, находят коррозионно-стойкие аустенитно-ферритные стали [5]. Получение МСС в двухфазном состоянии с высокой прочностью и стойкостью к коррозионному разрушению под напряжением (КРН) в агрессивных средах позволяет расширить области их применения и повысить размерную точность деталей и неразъемных конструкций. Однако отсутствие достаточных экспериментальных данных о влиянии предварительной ТО на фазовый состав и свойства окончательно термически обработанных МСС ограничивает их применение.
В настоящей статье излагаются результаты работ по влиянию различных режимов предварительной ТО и ТЦО на изменение фазового состава, механических свойств, размеров и стойкости к коррозии под напряжением экономнолегированной стали 03Х11Н10М2Т-ВД.
Методики исследований
Основным методом анализа, позволяющим определять соотношение между мартенситом и аустенитом в стали, признан рентгенофазовый анализ [6]. Содержание аустенита определяли с использованием дифрактометра ДРОН-2.0 на Fe-Kα излучении, безэталонным методом по отношению интегральных интенсивностей линий (111)γ- и (110)α-фаз при нагреве в интервале α-γ превращения в высокотемпературной приставке ГПВТ-1500 с одной установки образца и замерами при разных температурах.
Дилатометрический анализ изменения коэффициента линейного термического расширения (КЛР) и размеров образцов осуществляли на дилатометре системы «Шевенар» с записью дифференциальных кривых с эталонным образцом. Дополнительно изменение длины образцов 70х70х10 мм определяли микрометром до и после различных режимов ТО.
Сравнительную оценку стойкости к коррозии под напряжением (КРН) проводили ускоренным методом с использованием знакопеременной поляризации по методике, изложенной в работе [7].
Изучение влияния изменения геометрии деталей в зависимости от режимов ТО и ТЦО проводилось на образцах 70х10х10 мм, вырезанных из горячекатаных листов толщиной 10 мм, закаленных при 950 – 1000 °С, 1 ч.
Результаты экспериментов
Результаты изменения фазового состава и размеров в процессе нагрева в температурной области α-γ превращения и изменения фазового состава в зависимости от температуры нагрева и последующего охлаждения приведены на рис. 1.
При нагреве образцов, предварительно закаленных при 1000 °С, 1 ч, из листов толщиной 10 мм до различных температур в области α-γ-превращения и последующего охлаждения происходит изменение фазового состава стали с образованием остаточного аустенита.
Так, с увеличением температуры нагрева от 535 до ~625 °С происходит увеличение количества остаточного аустенита до 45 %. Образовавшийся при этом аустенит при нагреве в результате α-γ-превращения стабилен и не претерпевает обратного γ-α-превращения в процессе охлаждения. Увеличение температуры нагрева приводит к дальнейшему образованию аустенита при нагреве. Однако в этом случае образующийся при нагреве аустенит оказывается нестабильным и при дальнейшем охлаждении претерпевает обратное мартенситное превращение. В результате цикла нагрева до 750 °С с выдержкой 1 ч и последующего охлаждения достигается уменьшение количества остаточного аустенита от 45 до 3 %. Таким образом, установлено, что в процессе нагрева стали 03Х11Н10М2Т-ВД в температурной области 535…800 °С происходит полное полиморфное α-γ превращение с одновременным относительным уменьшением размеров образцов на 0,36 %.
Температурный интервал, в котором происходят процессы α-γ превращения, оказывающие влияние на структуру образующегося аустенита, можно разделить на две температурные – 248 –
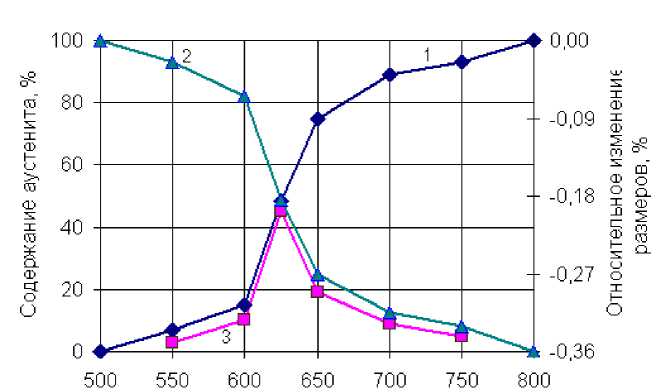
Температура нагрева, "С
Рис. 1. Относительное изменение при нагреве МСС 03Х11Н10М2Т-ВД: 1 - фазового состава, 2– размеров, 3 - количества остаточного аустенита после охлаждения
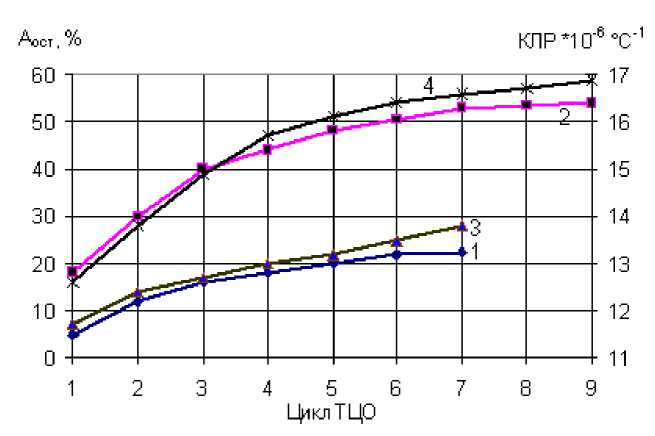
Рис. 2. Изменение суммарного количества остаточного аустенита в МСС 03Х11Н10М2Т-ВД при ТЦО: 1 - ТЦО с 750 °С; 2 - ТЦО с 650 °С. Изменение КЛР при ТЦО: 3 - с 750 °С, 1 ч; 4 - с 650 °С, 1 ч области: первая – низкотемпературная область до ~625 °С α-γ-превращения, где протекают процессы, стабилизирующие структуру аустенита, который не претерпевает обратного γ-α-превращения при последующем охлаждении; вторая – высокотемпературная область ~625… 800 °С, где развиваются процессы образования аустенита с неустойчивой структурой, который претерпевает обратное превращение при охлаждении.
Одновременно происходит дестабилизация ранее образовавшегося аустенита в низкотемпературной области. Процесс дестабилизации аустенита развивается более полно с увеличением температуры нагрева, и при 800 °С он заканчивается полностью.
Обнаруженный температурный интервал развития обратимого и необратимого фазового превращения позволяет предложить новые технологические режимы термоциклической обработки (ТЦО), выполняемой с использованием этого интервала. Использование ТЦО может стать дополнительным способом регулирования фазового состояния стали после окончательной термической обработки, определяющего конечные свойства стали.
Изменение исходного фазового состава стали достигалось путем использования термоциклической обработки с температур нагрева в высокотемпературной области α-γ-превращения по режиму: нагрев до заданной температуры, выдержка 1 ч и последующее охлаждение на воздухе. Такие циклы повторялись требуемое число раз (от одного до девяти). Полученные результаты изменения фазового состава при комнатной температуре при ТЦО с нагревом до температур 650 °С, 1ч и 750 °С, 1ч приведены на рис. 2.
В результате проведения ТЦО с температурой нагрева в циклах 750 °С происходит увеличение суммарного количества остаточного аустенита от 4 до 21 % для пятого цикла, а после шестого цикла и далее заметного изменения не наблюдается. Снижение температуры нагрева до 650 °С при аналогичной ТЦО приводит к увеличению количества остаточного аустенита от 20 до 55 %. Изменение фазового состава МСС вызывает изменение коэффициента линейного термического расширения пропорционально содержанию остаточного аустенита (см. рис. 2).
Электронно-микроскопический анализ, выполненный на угольных репликах, показал, что при ТЦО с использованием температуры нагрева в циклах 650 °С после первого цикла структура характеризуется выделяющимися мелкодисперсными α- и γ-фазами с пластинчатым субзеренным строением одного направления в пределах зерна. Пятикратная ТЦО увеличивает контраст неравномерной травимости пластинчатых субзерен и увеличивает размеры мелкодисперсных фаз. При ТЦО с использованием температуры нагрева в циклах 750 °С, по сравнению с 650 °С, увеличивается толщина «пластин» субзерен α- и γ-фаз и при этом уменьшается контрастность травимости их границ.
Таким образом, выявленные закономерности при формировании фазового состава в процессе ТО и ТЦО с температурной областью α-γ-превращения дают возможность управлять изменением фазового состава и свойствами стали и прогнозировать эти изменения.
На рис. 3 приведены результаты измерения длины образцов в зависимости от схемы и режимов предварительной ТО и ТЦО с применением различных температур в температурной области 550…800 °С, а также изменение размеров при последующей закалке с 1000 °С, 1 ч.
Анализ представленных результатов показывает, что увеличение температурного интервала термоциклирования вызывает существенное уменьшение длины образцов, что непосредственно отражает увеличение содержания остаточного аустенита, имеющего меньший объем – 250 –
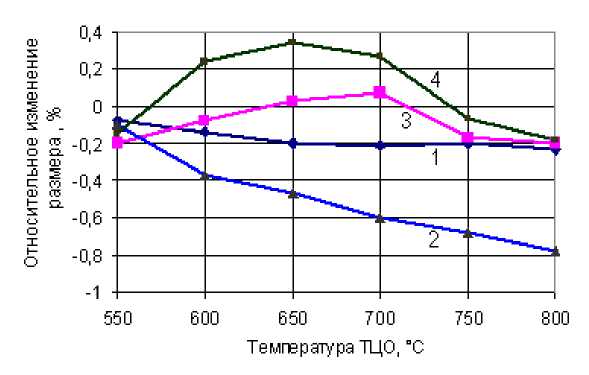
Рис. 3. Изменение размеров образцов 70x10x10 мм МСС 03Х11Н10М2Т-ВД при в зависимости от температуры ТО и ТЦО в области 550^800 °С: 1 - при ТО; 2 - при пятикратной ТЦО. Изменение размеров образцов при последующей закалке с 1000 °С, 1 ч: 3 - предварительно ТО; 4 - предварительно прошедших пятикратную ТЦО по сравнению с мартенситом. Наиболее сильное уменьшение длины образцов происходит при использовании температуры нагрева в циклах 800 °С (- 0,8 %). В то же время последующая закалка возвращает размеры образцов к исходным значениям.
Применение другого значения температуры нагрева в циклах (600 - 750 °С) снижает эффект уменьшения размеров образцов непосредственно после ТЦО, однако дает возможность увеличивать конечные размеры образцов после окончательной термической обработки. Причем значение прироста размеров после окончательной термической обработки оказывается возможным регулировать, изменяя температурные условия предварительного термоциклирования. Использование однократной предварительной термической обработки в том же интервале температур качественно влияет аналогичным образом, однако эффективность однократной термической обработки значительно ниже по сравнению с термоциклированием.
Практический интерес представляет изменение размеров образцов при закалке, прошедших предварительно термическую или термоциклическую обработку. Анализ изменения размеров после закалки при 1000 °С, 1 ч и старения при температуре 538 °С, 3,5 ч, по 26 образцам из листов толщиной 10 мм стали 03Х11Н10М2Т-ВД, предварительно закаленных при 950 °С, 1 ч и ТО при температуре 650 °С, 1 ч, приведен в табл. 1.
При нормальном распределении результатов измерений изменение размеров образцов после закалки и старения, предварительно термически обработанных с использованием температуры нагрева 650 °С и выдержки 1 ч, почти на порядок меньше, чем закаленных при 950 °С, 1 ч. Анализ изменения длины и сечения (толщины), полученного расчетом изменения объема, определенного методом гидростатического взвешивания, показал, что после ТО и ТЦО с использованием низкотемпературной области a—Y—превращения наблюдается одинаковое их изменение. С повышением температуры до 800 °С, 1 ч наблюдается уменьшение длины и увеличение сечения (толщины) образцов.
Изменение размеров по длине и сечению (толщине) образцов после закалки при 1000 °С, 1 ч, предварительно ТО и ТЦО в температурной области 600…800 °С, 1 ч приведены в табл. 2.
Таблица 1. Изменение длины образцов 70×10×10 мм после закалки с 1000 °С, 1 ч и старения при 538 °С, 3,5 ч, в зависимости от вида предварительной термической обработки
Режим термообработки |
Изменение размеров в зависимости от режимов термической обработки |
|||
Среднее арифметическое |
Дисперсия |
Стандартное отклонение |
Доверительный интервал (0,95) |
|
Предварительная закалка с 950 °С, 1 ч |
||||
Закалка при 1000°С, 1 ч |
- 0,177 |
0,0008 |
0,0287 |
0,0110 |
Старение 538 °С, 3,5 ч |
- 0,078 |
0,00014 |
0,0119 |
0,0045 |
Закалка при 1000°С, 1 ч+ Старение 538 °С, 3,5 ч |
- 0,257 |
0,0010 |
0,0315 |
0,0121 |
Предварительная термообработка с 650 °С, 1 ч |
||||
Закалка при 1000°С, 1 ч. |
0,042 |
0,00037 |
0,0194 |
0,0074 |
Старение 538 °С, 3,5 ч |
- 0,077 |
0,00017 |
0,0130 |
0,0500 |
Закалка при 1000°С, 1 ч+ Старение 538 °С, 3,5 ч |
- 0,035 |
0,00035 |
0,0188 |
0,0072 |
Таблица 2. Изменение размеров образцов 70х10х10 мм стали 03Х11Н10М2Т-ВД при закалке с 1000 °С, 1 ч в зависимости от температуры предварительной ТО и ТЦО
Температура предварительной ТО и ТЦО, °С |
Изменение размеров образцов после ТО, % |
Изменение размеров образцов после пятого цикла ТЦО, % |
||
Длина |
Сечение (толщина) |
Длина |
Сечение (толщина) |
|
600 |
-0,080 |
0,224 |
0,250 |
0,429 |
650 |
-0,040 |
0,259 |
0,320 |
0,463 |
750 |
-0,150 |
0,145 |
-0,080 |
0,334 |
800 |
-0,200 |
0,100 |
-0,180 |
0,140 |
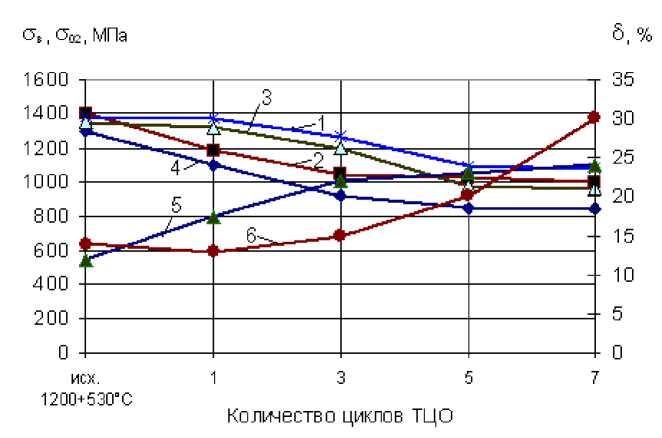
Рис. 4. Изменение временного сопротивления разрыву, а В МСС 03Х11Н10М2Т-ВД: 1 - при ТЦО с 750 ° С, 1 ч; 2 - при ТЦО с 650 ° С, 1 ч. Изменение предела текучести, а 0 2 : 3 - при ТЦО с 750 ° С, 1 ч; 4 - при ТЦО с 650 ° С, 1 ч. Изменение относительного удлинения, 5 : 5 - с 750 ° С, 1 ч; 6 - с 650 ° С, 1 ч
Таблица 3. Изменение стойкости к КРН стали МСС 03Х11Н10М2Т-ВД в зависимости от температуры старения
Температура старения °С, в течение 3…5 ч |
Время до разрушения, ч Количество разрушившихся образцов |
||||
От 0,5 до 1,5 |
От 1,5 до 2,5 |
от 2,5 до 10 |
от 10 до 24 |
24 и более |
|
320 |
0,0 |
0,0 |
0,0 |
0,0 |
100 |
350 |
0,0 |
0,0 |
0,0 |
0,0 |
100 |
360 |
0,0 |
0,0 |
0,0 |
0,0 |
100 |
370 |
0,0 |
0,0 |
0,0 |
50 |
50 |
380…385 |
0,0 |
16 |
16 |
40 |
28 |
390…395 |
43 |
35 |
15 |
7 |
0,0 |
400…435 |
50 |
27 |
21 |
2 |
0,0 |
450…480 |
72 |
23 |
5 |
0,0 |
0,0 |
500 |
54 |
40 |
6 |
0,0 |
0,0 |
520 |
26 |
26 |
35 |
13 |
0,0 |
535 |
0,0 |
14 |
38 |
28 |
20 |
540 |
0,0 |
0,0 |
20 |
20 |
60 |
550 |
0,0 |
0,0 |
0,0 |
12 |
88 |
560 |
0,0 |
0,0 |
0,0 |
0,0 |
100 |
580 |
0,0 |
0,0 |
0,0 |
0,0 |
100 |
Полученные изменения размеров образцов стали 03Х11Н10М2Т-ВД дают возможность прогнозировать их изменение в процессе закалки путем изменения режимов предварительной ТО и ТЦО в температурной области α-γ-превращения в широких пределах от - 0,200 до 0,320 % по длине и от 0,100 до 0,463 % по поперечному сечению.
Анализ изменения механических свойств (рис. 4) и фазового состава (рис. 2) при ТЦО показал, что изменение фазового состава при ТЦО с образованием до 50 % аустенита приводит к уменьшению прочностных характеристик с одновременным повышением пластичности стали 03Х11Н10М2Т-ВД.
Образцы, прошедшие ТО и ТЦО с использованием температур 650 и 750 °С, 1 ч, обладают высокой стойкостью к КРН. Механические свойства образцов с содержанием до 50 % аустенита имеют высокие прочностные и пластические характеристики и находятся на высоком уровне в сравнении с современными [5] аустенитными, ферритными и аустенито-ферритными коррозионно-стойкими сталями.
Полученные результаты по изменению механических свойств (рис. 6) и стойкости к КРН (табл. 3) в зависимости от температур старения стали 03Х11Н10М2Т-ВД показывают, что старение на максимальную прочность в температурной области 400…500 °С, 1 ч, вызывает снижение стойкости к КРН. Использование температуры старения 540 °С, обеспечивающей достижение предела прочности 1300-1350 МПа, и при более высоких температурах (560…650 °С) позволяет значительно повысить стойкость к КРН.
Существенное влияние на стойкость к КРН оказывает присутствие в структуре остаточного аустенита. Образцы с содержанием более 5 % остаточного аустенита при проведении соответствующей ТО в процессе ускоренного испытания не разрушались при выдержке более 24 ч, что указывает на высокую стойкость к КРН.
аБ, ^ог. МПа
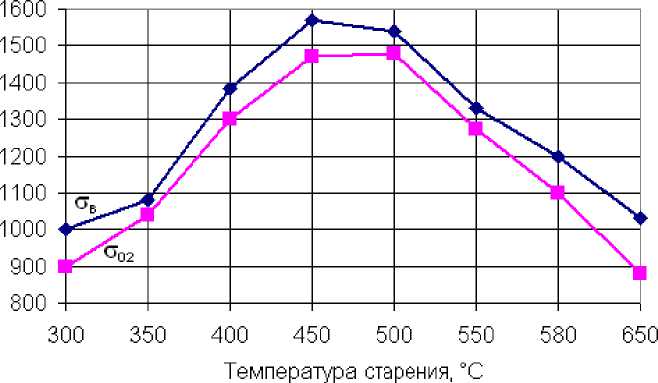
Рис. 5. Изменение механических свойств МСС 03Х11Н10М2Т-ВД листа толщиной 3 мм в зависимости от температуры старения в течение 3,5 ч
Выводы
-
1. На основании выполненного исследования изменения фазового состава мартенситностареющей стали (МСС) 03Х11Н10М2Т-ВД в зависимости от режимов термической (ТО) и термоциклической обработки (ТЦО) в температурной области α-γ-превращения установлена различная устойчивость аустенита, образующегося как при первичном нагреве, так и при по -вторных нагревах до температур 650 – 800 °С.
-
2. Показано, что применение предварительной ТО и ТЦО позволяет повысить размерную точность изделий при последующей закалке и увеличивает стойкость стали к коррозионному разрушению под напряжением.
-
3. Использование предварительной термической обработки позволяет регулировать эксплуатационные свойства МСС путем изменения ее фазового состава и температуры старения.