Влияние толщины упрочнённого слоя на сопротивление усталости при опережающем поверхностном пластическом деформировании
Автор: Кирпичв Виктор Алексеевич, Сазанов Вячеслав Петрович, Семнова Ольга Юрьевна, Михалкина Светлана Алексеевна
Журнал: Известия Самарского научного центра Российской академии наук @izvestiya-ssc
Рубрика: Машиностроение и машиноведение
Статья в выпуске: 1-2 т.18, 2016 года.
Бесплатный доступ
Исследовалось влияние толщины упрочнённого поверхностного слоя при опережающем поверхностном пластическом деформировании на предел выносливости полых цилиндрических образцов из стали 20 диаметром 25 мм с отверстием диаметром 15 мм с круговыми надрезами полукруглого профиля трёх радиусов: R = 0,3 мм, R = 0,5 мм, R = 1,0 мм. Различная толщина упрочнённого поверхностного слоя создавалась пневмодробеструйной обработкой и обкаткой роликом на двух режимах. Установлено, что с увеличением радиуса надреза сжимающие остаточные напряжения в опасном сечении образцов уменьшаются, в результате чего уменьшается предел выносливости. Для сохранения эффекта упрочнения в случае опережающего поверхностного пластического деформирования при увеличении глубины надреза следует увеличивать толщину упрочнённого поверхностного слоя детали.
Опережающее поверхностное пластическое деформирование, остаточные напряжения, толщина, упрочнённый слой, предел выносливости
Короткий адрес: https://sciup.org/148204370
IDR: 148204370
Текст научной статьи Влияние толщины упрочнённого слоя на сопротивление усталости при опережающем поверхностном пластическом деформировании
В исследовании изучалось влияние толщины упрочнённого поверхностного слоя при опережающем поверхностном пластическом деформировании (ОППД) образцов из стали 20 диаметром 25 мм с отверстием диаметром 15 мм на предел выносливости при изгибе. Гладкие образцы подвергались пневмодробес-труйной обработке (ПДО) дробью диаметром 1,5–2,5 мм при давлении воздуха 0,28 МПа в течение 10 минут, а также обкатке роликом (ОР) диаметром 60 мм и профильным радиусом 1,6 мм при усилии Р =0,5 кН и Р =1,0 кН с подачей 0,11 мм/об и скоростью вращения образца 400 об/мин. Затем на все упрочнённые и неупроч-нённые гладкие образцы наносились круговые надрезы полукруглого профиля трёх радиусов: R =0,3 мм, R =0,5 мм и R =1,0 мм.
Остаточные напряжения в гладких образцах определялись экспериментально методом колец и полосок [1]. Распределение осевых σ z остаточных напряжений по толщине поверхностного слоя а гладких образцов приведено на рис. 1. Из данных рис. 1 следует, что после нанесения на упрочнённые ПДО образцы надрезов с радиусами R =0,3 мм и R =0,5 мм материал на дне концентраторов находился в ненаклё-панном состоянии. Такое же состояние наблюдалось после нанесения на упрочнённые ОР образцы при Р =0,5 кН надрезов с радиусом R =0,5 мм. Для образцов с надрезами R =1,0 мм во всех случаях упрочнения материал на дне концентраторов находился в ненаклёпан-ном состоянии.
В остальных случаях обкатки роликом материал на дне надрезов находился в наклёпанном состоянии ( Р =0,5 кН – R =0,3 мм; Р =1,0 кН – R =0,3 мм и R =0,5 мм). Остаточные напряжения в упрочнённых образцах с надрезами определялись аналитическим методом –
Михалкина Светлана Алексеевна, старший преподаватель кафедры высшей математики суммированием дополнительных остаточных напряжений и остаточных напряжений гладких образцов [2], а также численным методом с использованием программного комплекса NASTRAN/PATRAN [3].
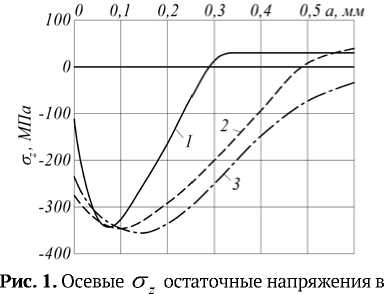
упрочнённых гладких образцах после:
1 – ПДО; 2 – ОР, Р =0,5 кН; 3 – ОР, Р =1,0 кН
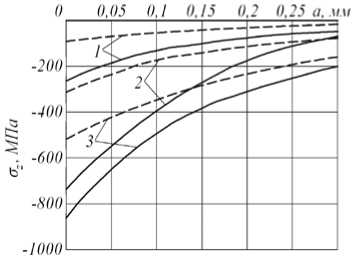
Рис. 2. Осевые σ z остаточные напряжения в упрочнённых образцах с надрезами ( ––––– – R =0,3мм; – – – – R =0,5 мм ) после:
1 – ПДО; 2 – ОР, Р =0,5 кН; 3 – ОР, Р =1,0 кН
Распределение осевых σz остаточных напряжений по толщине поверхностного слоя а наименьшего сечения образцов приведено на рис. 2 и рис. 3. Анализируя данные рис. 1–3, можно видеть, что при практически одинаковых максимальных остаточных напряжениях гладких образцов в образцах с надрезом одной глубины остаточные напряжения тем выше, чем больше толщина упрочнённого поверхностного слоя гладких образцов со сжимающими остаточными напряжениями. Эта закономерность объясняется концентрацией остаточных напряжений в области дна надреза. Испытания на усталость при изгибе в случае симметричного цикла образцов с надрезами проводились на машине УММ-01 [4], база испытаний – 3·106 циклов нагружения.
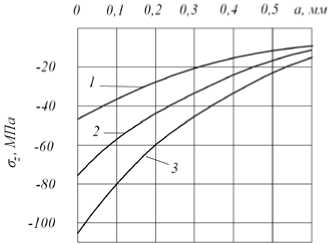
Рис. 3. Осевые G z остаточные напряжения в упрочнённых образцах с надрезами R =1,0 мм после: 1 –
ПДО; 2 – ОР, Р =0,5 кН; 3 – ОР, Р =1,0 кН
Результаты испытаний на усталость по определению предела выносливости G - 1 представлены в табл. 1.
Распределение осевых G z остаточных напряжений по толщине поверхностного слоя а наименьшего сечения образцов приведено на рис. 2 и рис. 3. Анализируя данные рис. 1–3, можно видеть, что при практически одинаковых максимальных остаточных напряжениях гладких образцов в образцах с надрезом одной глубины остаточные напряжения тем выше, чем больше толщина упрочнённого поверхностного слоя гладких образцов со сжимающими остаточными напряжениями. Эта закономерность объясняется концентрацией остаточных напряжений в области дна надреза. Испытания на усталость при изгибе в случае симметричного цикла образцов с надрезами проводились на машине УММ-01 [4], база испытаний – 3·106 циклов нагружения. Результаты испытаний на усталость по определению предела выносливости G - 1 представлены в табл. 1.
Таблица 1. Результаты испытаний на усталость и определения остаточных напряжений
Надрез R , мм |
Неупрочн. образцы G - 1 , МПа |
Упрочнённые образцы |
||||||
упрочн. обр-ка |
G - 1 , МПа |
пов G z , МПа |
W g |
t кр , мм |
G ост , МПа |
W g |
||
0,3 |
95 |
ПДО |
127,5 |
-307 |
0,106 |
0,452 |
-88 |
0,368 |
ОР1 |
155 |
-732 |
0,082 |
0,445 |
-181 |
0,331 |
||
ОР2 |
177,5 |
-861 |
0,096 |
0,442 |
-248 |
0,333 |
||
0,5 |
110 |
ПДО |
127,5 |
-124 |
0,121 |
0,438 |
-47 |
0,372 |
ОР1 |
152,5 |
-311 |
0,137 |
0,442 |
-128 |
0,332 |
||
ОР2 |
182,5 |
-517 |
0,140 |
0,446 |
-218 |
0,333 |
||
1,0 |
90 |
ПДО |
95 |
-29 |
0,175 |
0,410 |
-14 |
0,357 |
ОР1 |
105 |
-77 |
0,195 |
0,420 |
-39 |
0,384 |
||
ОР2 |
110 |
-105 |
0,191 |
0,420 |
-53 |
0,377 |
Выстоявшие базу испытаний упрочнённые образцы при напряжении, равном пределу выносливости, доводились до разрушения при бόльшем напряжении. Во всех упрочнённых образцах были обнаружены нераспространяющиеся трещины усталости, средняя глубина tкр которых для каждой партии образцов представлена в табл. 1. На рис. 4 приведена фотография излома упрочнённого ОР при Р = 1,0 кН образца с надрезом радиуса R=0,5 мм, на которой видна серповидная нераспространяющаяся трещина 2. Следует отметить, что значения tкр , измеренные в настоящем исследовании, хорошо согласуются с установленной ранее [5, 6] зависимостью tp = 0,0216 ■ D
1 - 0 , 04 ■1 - 1 - 0 , 54 ■1 - 1 V D ) V D J
где D – диаметр опасного сечения упрочнённого образца (детали) с концентратором напряжений, d – диаметр отверстия.
Из данных табл. 1 видно, что с увеличением глубины надреза приращение предела выносливости упрочнённых образцов снижается, так как уменьшаются сжимающие остаточные напряжения в их опасном сечении. Поэтому для сохранения эффекта упрочнения при ОППД с увеличением глубины надреза необходимо увеличивать толщину слоя гладкой детали со сжимающими остаточными напряжениями.
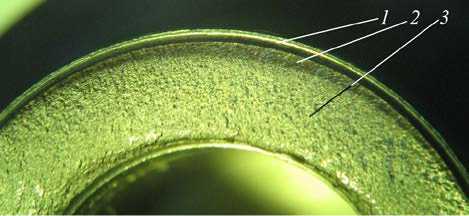
Рис. 4. Фотография излома упрочнённого роликом при Р= 1,0 кН образца с надрезом R =0,5 мм: 1 – надрез, 2 – нераспространяющаяся трещина, 3 – зона долома
Для оценки приращения предела выносливости Ag i за счёт поверхностного упрочнения использовались два критерия влияния остаточных напряжений на предел выносливости при изгибе в случае симметричного цикла. Первым критерием [7-11] являются осевые остаточные напряжения σzпов на поверхности концентратора. Зависимость для определения приращения предела выносливости А ст 1 упрочнённых образцов (деталей) в этом случае имеет вид
Аст-1 = • |ст"°в|, (2)
где ψσ – коэффициент влияния остаточных напряже- пов ний по критерию σz на предел выносливости по разрушению.
Для определения второго критерия в работе [12] использовалось решение задачи [2] о дополнительных остаточных напряжениях в наименьшем сечении образца (детали) после нанесения надреза полуэллипти-ческого профиля на упрочнённую поверхность. Выделив основную часть решения [2], был получен второй критерий σост влияния остаточных напряжений на предел выносливости образца (детали) в виде
σ ост
2 . f ст . ( ^ )
п 0^-^
d ξ ,
где CTz (^) - осевые остаточные напряжения в опасном сечении образца (детали), ξ= a tкр – расстояние от дна концентратора до текущего слоя, выраженное в долях tкр , tкр – критическая глубина нераспростра-няющейся трещины усталости, возникающей при работе образца (детали) на пределе выносливости.
Критерий σост , который называется критерием среднеинтегральных остаточных напряжений, имеет чётко выраженный физический смысл – это остаточное напряжение на дне нераспространяющейся трещины усталости с точностью до постоянного коэффициента, зависящего от радиуса у дна трещины и её глубины. Приращение предела выносливости А ст-1 при изгибе в случае симметричного цикла при исполь- зовании критерия σост определяется по следующей формуле:
∆σ - 1 = ψ σ ⋅ σ ост , (4)
где ψσ – коэффициент влияния остаточных напряже- ний по критерию σост на предел выносливости по разрушению.
Значения остаточных напряжений на поверхности надрезов σ z пов и среднеинтегральных остаточных напряжений σ ост приведены в табл. 1. По результатам испытаний на усталость неупрочнённых и упрочнённых образцов вычислялись коэффициенты ψσ и ψσ , значения которых представлены в табл. 1. Из данных табл. 1 можно видеть, что оценка влияния поверхностного упрочнения на предел выносливости образцов по первому критерию – остаточным напряжениям на поверхности концентратора σ z пов – приводит к значительному рассеянию коэффициента ψσ . Этот коэффициент в настоящем исследовании изменяется в широких пределах – от 0,082 до 0,195, то есть почти в 2,5 раза, что неприемлемо для прогнозирования предела выносливости поверхностно упрочнённых деталей.
Оценка влияния поверхностного упрочнения по второму критерию – среднеинтегральным остаточным напряжениям σ ост – приводит к существенно мéнь-шему рассеянию соответствующего коэффициента ψσ . Это объясняется тем, что критерий среднеинтегральных остаточных напряжений учитывает влияние на сопротивление усталости не только величины сжимающих остаточных напряжений, но и характера их распределения по толщине поверхностного слоя опасного сечения детали (образца). Коэффициент ψσ в проведенном исследовании изменяется от 0,331 до 0,384, составляя в среднем 0,354, и практически совпадает со значением ψσ =0,36, установленным в [6] для упрочнённых образцов и деталей с аналогичной концентрацией напряжений.
Необходимо отметить, что на значения коэффициентов ψσ и ψσ не оказывает влияние состояние материала на дне концентраторов. Из данных табл. 1 видно, что не наблюдается определённой зависимости между величинами коэффициентов ψσ , ψσ и наклёпанным или ненаклёпанным состоянием материала образцов.
Выводы: проведенное исследование показало, что с уменьшением толщины упрочнённого слоя при ОППД сжимающие остаточные напряжения в опасном сечении детали уменьшаются, в результате чего приращение предела выносливости за счёт упрочнения снижается. Для сохранения эффекта упрочнения с увеличением глубины надреза необходимо увеличивать толщину упрочнённого поверхностного слоя со сжимающими остаточными напряжениями при ОППД.
Список литературы Влияние толщины упрочнённого слоя на сопротивление усталости при опережающем поверхностном пластическом деформировании
- Иванов, С.И. К определению остаточных напряжений в цилиндре методом колец и полосок. Остаточные напряжения. -Куйбышев: КуАИ, 1971. Вып. 53. С. 32-42.
- Иванов, С.И. Влияние остаточных напряжений на выносливость образцов с надрезом/С.И. Иванов, М.П. Шатунов, В.Ф. Павлов//Вопросы прочности элементов авиационных конструкций. -Куйбышев: КуАИ. 1974. Вып. 1. С. 88-95.
- Сазанов, В.П. Моделирование перераспределения остаточных напряжений в упрочнённых цилиндрических образцах при опережающем поверхностном пластическом деформировании/В.П. Сазанов, А.В. Чирков, В.А. Самойлов, Ю.С. Ларионова//Вестник СГАУ. 2011. №3(27). Ч. 3. С. 171-174.
- Филатов, Э.Я. Универсальный комплекс машин для испытания материалов и конструкций на усталость/Э.Я. Филатов, В.Э. Павловский. -Киев: Наукова Думка, 1985. 92 с.
- Павлов, В.Ф. Влияние на предел выносливости величины и распределения остаточных напряжений в поверхностном слое детали с концентратором. Сообщение II. Полые детали//Известия вузов. Машиностроение. 1988. №12. С. 37-40.
- Павлов, В.Ф. Прогнозирование сопротивления усталости поверхностно упрочнённых деталей по остаточным напряжениям/В.Ф. Павлов, В.А. Кирпичёв, В.С. Вакулюк. -Самара: Издательство СНЦ РАН, 2012. 125 с.
- Кравченко, Б.А. Обработка и выносливость высокопрочных материалов/Б.А. Кравченко, К.Ф. Митряев. -Куйбышев: Куйбышевское книжное издательство, 1968. 131 с.
- Серенсен, С.В. К вопросу об оценке сопротивления усталости поверхностно упрочнённых образцов с учётом кинетики остаточной напряжённости/С.В. Серенсен, С.П. Борисов, Н.А. Бородин//Проблемы прочности. 1969. №2. С. 3-7.
- Туровский, М.Л. Концентрация напряжений в поверхностном слое цементированной стали/М.Л. Туровский, Н.М. Шифрин//Вестник машиностроения. 1970. №11. С. 37-40.
- Иванов, С.И. Влияние остаточных напряжений и наклёпа на усталостную прочность/С.И. Иванов, В.Ф. Павлов//Проблемы прочности. 1976. №5. С. 25-27.
- Иванов, С.И. Влияние остаточных напряжений на сопротивление усталости при кручении в условиях концентрации напряжений/С.И. Иванов, В.Ф. Павлов, А.А. Прохоров//Проблемы прочности. 1988. №5. С. 31-33.
- Павлов, В.Ф. О связи остаточных напряжений и предела выносливости при изгибе в условиях концентрации напряжений//Известия вузов. Машиностроение. 1986. №8. С. 29-32.