Восстановление деталей сельскохозяйственных машин гальваническими покрытиями на основе цинка
Автор: Юдин В.М., Вихарев М.Н.
Журнал: Вестник аграрной науки @vestnikogau
Рубрика: Ремонт и органиация технического сервиса
Статья в выпуске: 1 (16), 2009 года.
Бесплатный доступ
В статье представлены технологический процесс восстановления деталей гальваническим цинкованием с применением активатора и результаты экспериментов в виде графиков зависимости скорости нанесения покрытия от плотности тока и скорости движения активатора.
Короткий адрес: https://sciup.org/147123362
IDR: 147123362
Текст научной статьи Восстановление деталей сельскохозяйственных машин гальваническими покрытиями на основе цинка
Российский государственный аграрный заочный университет
ВОССТАНОВЛЕНИЕ ДЕТАЛЕЙ СЕЛЬСКОХОЗЯЙСТВЕННЫ Х МАШ ИН ГАЛЬВАНИЧЕСКИМИ ПОКРЫ ТИЯМИ НА ОСНОВЕ ЦИНКА
В статье представлены технологический процесс восстановления деталей гальваническим цинкованием с применением активатора и результаты экспериментов в виде графиков зависимости скорости нанесения покрытия от плотности тока и скорости движения активатора .
Материалы и методика исследований
Цинк – металл серебристо-белого цвета. Плотность цинка 7,1 г/см3, температура плавления 420 о С. Цинковые покрытия обычно бывают мягкими (500…600МПа), пластичными и хорошо выдерживают изгибы, развальцовку, но плохо – запрессовку. Поэтому цинкование чаще всего применяют для защиты от коррозии. В ремонтном производстве цинковые покрытия применяют для защиты от коррозии крепежных деталей и восстановления посадочных поверхностей малонагруженных деталей.
Восстановление деталей гальваническими покрытиями имеют следующие преимущества перед другими способами восстановления :
-
- отсутствие термического воздействия на детали, вызывающего в них нежелательные изменения структуры и механических свойств;
-
- получение с большой точностью заданной толщины покрытий, что позволяет снизить до минимума припуск на последующую механическую обработку и ее трудоемкость или вовсе исключить ее;
-
- осаждение покрытий с заданными непостоянными по толщине физико-механическими свойствами;
-
- одновременное восстановление большого числа деталей (в ванну загружают десятки деталей), что снижает трудоемкость и себестоимость единицы изделия;
-
- возможность автоматизации процесса.
Основным недостатком цинкования является малая скорость нанесения покрытия, порядка 6÷15мкм/ч.
В Российском государственном аграрном заочном университете (РГАЗУ) проведены предварительные исследования по устранению этого недостатка.
Решающее влияние на скорость нанесения покрытий оказывает катодная плотность тока:
C⋅D ⋅η
-
V = k k , 1000 ⋅ γ
где V – скорость осаждения покрытий , мм / ч ;
С – электрохимический эквивалент , г / А∙ч ;
Dk – катодная плотность тока , А / дм 2;
-
η k – катодный выход метала по току , %;
-
γ – плотность осаждаемого металла , г / см 3.
Поскольку С и γ – величины постоянные, и η, при использовании кислого электролита для цинкования, близок к 100%, то основной путь повышения скорости осаждения покрытий – увеличение катодной плотности тока.
Известно, что существенное увеличение катодной плотности тока возможно при перемешивании электролита. Однако при увеличении катодной плотности тока ухудшается качество наносимого покрытия:
-
- происходит образование дендритов;
-
- пористая поверхность нанесенного покрытия (питтинг).
Для устранения этих недостатков мы используем экспериментальную установку с активирующим устройством.
Активирующее устройство (активатор)
перемешивает электролит и активирует восстанавливаемую поверхность , тем самым предотвращает обеднение прикатодного слоя электролита и уменьшает химическую поляризацию катода, которая является основной причиной ограничения катодной плотности тока при цинковании из сернокислых электролитов. Возникает реальная возможность увеличения катодной плотности тока, а следовательно, и скорости нанесения покрытия.
Щ етки активатора, активируя поверхность , предотвращают образование дендритов и явления питтинга на поверхности наносимого покрытия.
На рисунке 1 представлены результаты экспериментов в виде зависимости скорости нанесения покрытия от скорости движения активатора относительно восстанавливаемой поверхности. Нанесение покрытия проходило при технологическом процессе с постоянными параметрами, кроме скорости движения активатора.
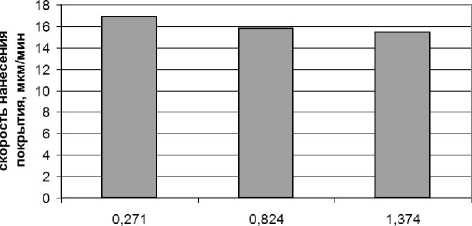
скорость движения активатора относительно восстанавливаемой поверхности, м/с
Рисунок 1 – Зависимость скорости нанесения покрытия от скорости движения активатора
Технологический процесс:
-
• механическая обработка;
-
• обезжиривание;
-
• травление при плотности тока на аноде 50А/дм2, продолжительность 30с;
-
• предварительная обработка катода на ассиметричном токе. плотность тока на катоде 23—25 А/дм2, на аноде - 20 А/дм2, продолжительность 60с;
-
• нанесение покрытия, при плотности тока на катоде 100 А/дм2, продолжительность 12мин;
-
• температура электролита 15 – 40 о С (в результате исследований было выявлено, что при изменении температуры электролита от 15 о С до 40 о С, скорость нанесения покрытия практически не изменяется);
-
• плотность электролита 1,27г/см3;
-
• pH=4.
Состав электролита: 500г/л – сернокислого цинка, 20 – 30 г/л – сернокислого алюминия.
Результаты и их обсуждения
В результате были получены образцы с качественным покрытием, но, как видно из графика, большая скорость нанесения цинкового покрытия при скорости движения активатора 0,271м/с, поэтому последующие исследования проводились с этой скоростью.
Приняв скорость движения активатора 0,271м/с, нами проведены исследования о влиянии усилия прижатия щеток активатора к поверхности на скорость нанесения покрытия. В результате было выявлено, что при меньшем усилии прижатия щеток скорость нанесения покрытия увеличивается, но ухудшается качество наносимого покрытия. Поэтому для дальнейших исследований нами было выбрано наиболее рациональное значение усилия – 20Н/см.
При использовании в качестве щеток активатора влагостойкой шкурки, на качество и на скорость нанесения покрытия влияет размер зерен абразива. При меньшей зернистости шкурки качество и скорость нанесения покрытия выше.
В дальнейшем было исследовано влияние катодной плотности тока на скорость нанесения покрытий и их качество. Эксперименты проводили с 4-мя активаторами, при усилии прижатия активатора 20Н/см и его скорости 0,271м/с. Технологический процесс тот же, что и в предыдущих экспериментах. Результаты представлены в виде зависимости скорости нанесения покрытия от плотности тока на рисунке 2.
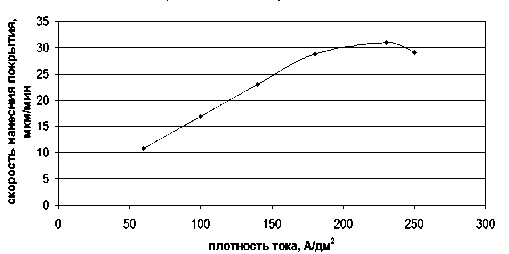
Рисунок 2 – Зависимость скорости нанесения покрытия от катодной плотности тока
Из графика видно, что с увеличением плотности тока с 60А/дм2 до 230А/дм2 увеличивается и скорость нанесения покрытия с 10,750мкм/мин до 30,917мкм/мин, при этом качество нанесенного покрытия остается на хорошем уровне. При увеличении плотности тока выше 230 А/дм2, уменьшается скорость нанесения и ухудшается качество покрытия.
Выводы
-
1. Таким образом, применение активатора при цинковании позволяет в десятки раз увеличить скорость нанесения покрытий и расширяет диапазон применения цинковых покрытий при восстановлении деталей.
-
2. В результате экспериментов была выявлена зависимость между усилием прижатия, скоростью движения активатора и скоростью нанесения цинкового покрытия, а также его качеством. В последующих экспериментах планируется определение наиболее рациональных условий нанесения цинковых покрытий с учетом выше изложенного.
Список литературы Восстановление деталей сельскохозяйственных машин гальваническими покрытиями на основе цинка
- Батищев, А.Н. Пособие гальваника-ремонтника [Текст]/А.Н. Батищев. -2-е изд., перераб. -М.: Агропромиздат, 1986.-192с.
- Петров, Ю.Н. Ремонт автотракторных деталей гальваническими покрытиями [Текст]/Ю.Н. Петров, В.П. Косов, М.П. Стратулат. -Кишинев: Картя молдовеняскэ, 1976.
- Ревякин, В.П. Ремонт автотракторных деталей гальваническим способом [Текст]/В.П. Ревякин. -Иркутск: Иркутское областное издательство, 1952.-139с.