Выбор силовых элементов электропривода стана холодной прокатки труб ХПТ-450 ПАО "ЧТПЗ"
Автор: Холодилин Иван Юрьевич, Коржов Антон Вениаминович, Григорьев Максим Анатольевич, Дудкин Максим Михайлович, Хохлов Юрий Иванович, Кушнарев Виктор Александрович
Журнал: Вестник Южно-Уральского государственного университета. Серия: Энергетика @vestnik-susu-power
Рубрика: Электромеханические системы
Статья в выпуске: 4 т.21, 2021 года.
Бесплатный доступ
С ростом требований к позиционным системам электропривода для применения в металлургии стандартная замена оборудования не позволит обеспечить необходимую точность и быстродействие. Модернизацию системы электропривода необходимо производить комплексно, с последовательной частной оптимизацией силовых элементов. В работе описаны критерии и методы выбора силовых элементов. Оптимизация на каждом участке переходного процесса производилась по критерию минимума расчетного времени. Выбор элементов осуществлялся исходя из полученных опытным путем данных о технологической установке, а именно стана ХПТ-450 на ПАО «ЧТПЗ». Выявлено, что изменение передаточного числа редуктора позволяет повысить качество настройки системы подчиненного регулирования с учетом податливости механической части системы. Увеличение отношения длины активной части ротора к его диаметру позволяет увеличить быстродействие системы, а, следовательно, и его точность. Результаты выбора оборудования были опробованы на опытном образце в НТЦ «Приводная техника», в результате удалось сократить время технологического процесса практически в 2 раза.
Станы холодной прокатки труб, последовательная частная оптимизация, быстродействие
Короткий адрес: https://sciup.org/147235765
IDR: 147235765 | DOI: 10.14529/power210412
Текст научной статьи Выбор силовых элементов электропривода стана холодной прокатки труб ХПТ-450 ПАО "ЧТПЗ"
Производство тонкостенных труб с переменным сечением наиболее эффективно при холодной прокатке металла. На станах холодной прокатки труб (ХПТ) получают высокопрочные трубы высокого качество со сверхтонкой стенкой. Такие трубы наиболее востребованы в атомной промышленности, авиа- и машиностроении. В России находится более 200 станов холодного проката труб в промышленной эксплуатации, производящие трубы различного назначения. В пятом цехе ПАО «Челябинский трубопрокатный завод» эксплуатируется два стана ХПТ-450, которые позволяют выпускать трубы широкого сортамента с постоянным или переменным сечением готового изделия диаметром от 150 до 450 мм. В последнее время по понятным причинам к качеству проката стали предъявляться повышенные требования со стороны атомной промышленности и военнопромышленного комплекса, в связи с чем необходима модернизация главного приводного оборудования.
Замена отдельных элементов системы электропривода не позволит добиться требуемых показателей. Например, задача повышения быстродействия системы обычной заменой электродвигателя на более мощный не может быть осуществлена, поскольку в этом случае допустимое ускорение М Н/ J иногда даже снижается. Задача улучшения показателей технологического процесса механизма подачи трубы может быть решена только путем комплексного подхода к выбору приводного оборудования стана, а именно, системы электропривода и редуктора.
Методика выбора силового оборудования
Достичь улучшения точности отработки задания следящей системы электропривода механизма подачи стана холодного проката возможно путем повышения быстродействия проектируемой системы. От быстродействия системы напрямую зависит точность следящего электропривода, что описано в [1, 2]. Работу по выбору силового оборудования необходимо производить исходя из данных о переходном процессе и нагрузочных диаграмм. Для механизма подачи трубы опытным путем получены исходные данные технологического процесса, которые представлены на рис. 1, кривые 1, 2, 3 – в виде графиков. Из рис. 1 видно, что время позиционирования рабочего органа занимает более 0,3 с, при этом точность линейного перемещения – 0,1 мм. Настоящий комплекс электропривода выполнен на базе синхронного частотно-регулируемого электропривода.
Исходя из полученных данных о технологическом процессе и допустимой точности, для решения задачи обеспечения максимального быстродействия обратимся к методу последовательной оптимизации системы.
На первом этапе выбора силового оборудования необходимо провести анализ диаграмм цикла механизма подачи трубы и разбить цикл работы механизма на несколько участков временных интервалов, которые характеризуют различные переходные процессы в электроприводе.
Первый интервал времени t 0– t 1 является переходным процессом в контуре регулирования тока якоря. На втором интервале t 1 – t 2 электропривод находится на участке линейного ускорения.
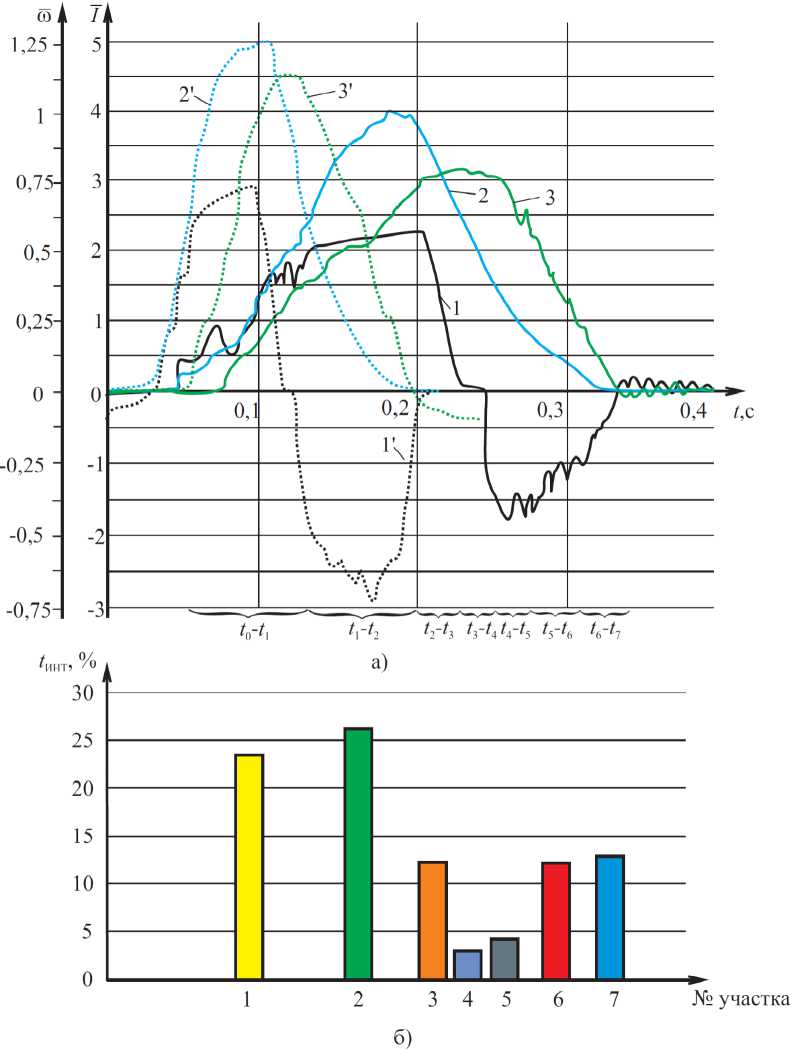
Рис. 1. Кривые переходных процессов станов холодной прокатки труб (а): 1 – ток якоря; 2 – задание на скорость; 3 – текущая скорость и гистограммы нагрузок электропривода на разных участках (б)
Интервал t 2– t 3 характеризует работу электропривода с постоянной установившейся скоростью. На временном интервале t 3– t 4 электропривод выходит на участок торможения в генераторном режиме. На последнем интервале электропривод осуществляет точный останов рабочего органа.
Дальнейший выбор силового оборудования и параметров системы управления необходимо производить с учетом переходных процессов на каждом из участков по критерию минимума расчетного времени [3].
В промежутке t 0– t 1 происходит разгон электропривода, здесь разница между сигналом задания по положению и реальным положением вала двигателя достигает максимального значения, что выводит работу регуляторов положения и скорости в предельные значения. Возмущающий сигнал на вход канала управления по положению выполнен в виде ступенчатой функции, как видно из графика переходного процесса, позиционирование вала двигателя происходит с запаздыванием, что обусловлено маховыми массами.
Предположим, что контуры регулирования момента и тока имеют одинаковое быстродействие. Упрощенная структурная схема регулятора крутящего момента представлена на рис. 2. Замена нелинейной системы путем применения метода приближенной аппроксимации рассмотрена в [4]. Новая структура регулятора включает в себя последовательно соединенные звено чистого запаздывания с постоянной времени, равной частоте дискретизации, и апериодическое звено первого порядка.
На рис. 3 (кривая 1) представлен автоколебательный режим работы, к которому приводит увеличение коэффициента усиления последовательного корректирующего устройства.
Проблемы, связанные с автоколебаниями последовательного регулятора, могут быть решены внедрением регулятора переменного типа (см. рис. 2б). В регуляторах такого типа коэффициент усиления имеет переменное значение. В зависимости от комбинации сигнала ошибки и ее производной изменяется значение коэффициента усиления регулятора [5]. В случае, когда произве- дение сигнала ошибки и ее производной имеет положительный знак, коэффициент усиления принимает значение α. При отрицательном результате произведения сигнала ошибки и ее производной коэффициент усиления принимает значение β. При завершении переходного процесса переключатель переходит в третье положение и коэффициент усиления принимает значение γ.
На диаграмме переходного процесса (рис. 3, кривая 2) представлена зависимость скорости от времени электропривода при воздействии внешнего возмущения (статического момента сопротивления) в установившемся режиме работы. В момент воздействия внешнего возмущения в промежутке времени от 0 до 1,8 с, коэффициент контура регулятора скорости принимает значение α, поскольку произведение ошибки по скорости и ее производной имело положительный знак. После того как регулятор отработал ошибку на временном промежутке от 1,8 до 3 с, знак произведения ошибки и ее производной изменился с положительного на отрицательный и передаточная функция приняла значение β; на заключительном
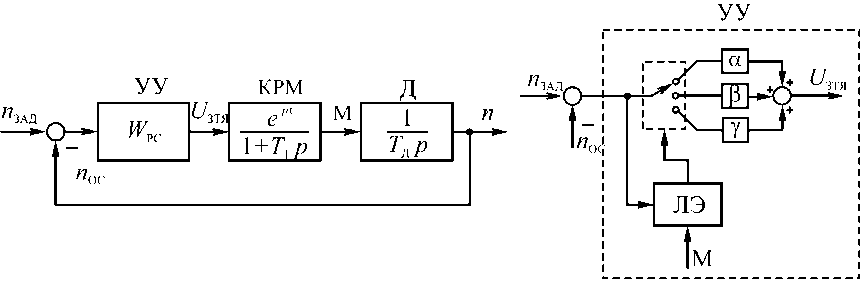
а)
б)
Рис. 2. Последовательный упрощенный регулятор (а) и регулятор скорости с переменной структурой (б):
УУ – устройство управления; КРМ – контур регулирования крутящего момента; Д – звено, учитывающее механическую инерцию двигателя; ЛЭ – логический элемент; n зад – задание на скорость; n ОС – сигнал обратной связи по скорости; U ЗТЯ – задание тока якоря; W РС – передаточная функция регулятора скорости; Т Д – механическая постоянная двигателя;
Т 1 – эквивалентная постоянная контура регулирования момента; e – pt – звено чистого запаздывания
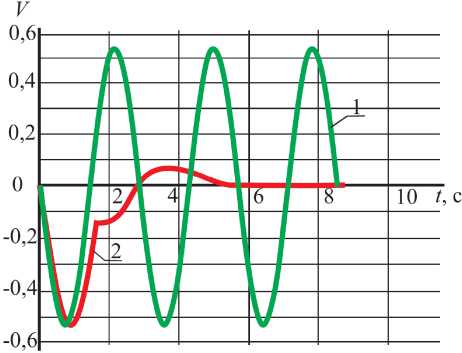
Рис. 3. Кривые переходных процессов в контуре регулирования тока до введения коррекции (1) и с регулятором переменной структуры (2)
интервале переходного процесса, на временном отрезке 3 с, регулятор скорости принял положение γ и система снова перешла в установившийся режим работы. Таким образом, система регулирования сохранила устойчивость в условиях колебательного характера переходного процесса. Из графика переходного процесса видно, что переменная структура регулятора не обеспечивает полную компенсацию негативного влияния звена чистого запаздывания, однако позволяет расширить диапазон равномерного пропускания частот. Несмотря на это, регуляторы со структурой переменного типа способны повысить быстродействие системы в 2 раза [6].
В промежутке t 1– t 2 (см. рис. 1а) колебания тока якоря прекращаются, что означает завершение переходного процесса в контуре регулирования тока. В свою очередь, электропривод выходит на участок линейного ускорения. Улучшить быстродействие электропривода в режиме ускорения возможно лишь путем уменьшения момента инерции.
Предельное значение ускорения электромеханического преобразователя определяется его механической постоянной времени Т Д . Данная постоянная времени определяет необходимое количество времени электрической машины для разгона от нуля до скорости идеального холостого хода при номинальной статической нагрузке на валу.
Величина постоянной времени напрямую связана с коэффициентом добротности М Н/ J , который зависит от массогабаритного показателя электрической машины. Так, улучшить массогабаритный показатель электрической машины, т. е. уменьшить момент инерции, возможно изменением ее геометрии. Увеличение длины магнитопровода в его активной части и сокращение ротора в диаметре позволит повысить динамику электрической машины.
Изменение соотношения длины активной части магнитопровода к его диаметру в машинах общепромышленного назначения приводит к прогибу вала и ухудшению вентиляции внутри самой машины. Данные конструкционные проблемы возможно избежать в реактивных электродвигателях с цельным безобмоточным ротором, который имеет жесткую конструкцию в радиальном направлении.
Синхронные реактивные машины независимого возбуждения (СРМНВ) благодаря конструкции ротора не имеют потерь на нагрев, польску ротор не отстает от поля статора, а конструкция ротора не подразумевает наличие обмоток. Несмотря на это, ротор СРМНВ в условиях реальной эксплуатации нагревается за счет коммутационных потерь в статоре, однако данные потери можно снизить путем оптимизации геометрии скоса паза и оптимизации конструкции ротора.
Ниже приведены зависимости допустимого по нагреву ускорения электропривода (МН/J) от пере- менных номинального момента двигателя и длины ротора на примере асинхронного двигателя и синхронной реактивной машины независимого возбуждения (рис. 4а, б). Увеличение длины активной части магнитопровода каждого типа двигателя положительно влияло на допустимое максимальное ускорение. Однако в асинхронном двигателе относительный прогиб вала (не более 10 % от воздушного зазора) ограничивает предельные значения длины вала, а следовательно, и его ускорение.
На отрезке времени t 2– t 3 выходы регуляторов скорости и положения достигают предельных значений. Оптимальное предельное значение регулятора скорости также необходимо учитывать при проектировании систем следящих электроприводов, это позволит добиться как высокой точности позиционирования, так и повысить быстродействие системы. Существует несколько критериев выбора оптимального значения максимальной скорости. Рассмотрим два критерия. Одним из таких является критерий минимальной кинетической энергия электромеханической системы (двигателя и рабочего органа) [7]. Данный критерий был предложен еще в начале прошлого века, его рационально использовать в случае, когда в частота среза первого контура наибольшая, частота среза в третьем контура наименьшая, т. е. текущее значение передаточного числа редуктора меньше предельного значения. Предельное значение передаточного числа редуктора определится выражением
j ; -^
7 ро • 1
к РМ^РС к ДС ' уз
Второй критерий предложен профессором Ю.С. Усыниным [4]. Критерий поиска оптимального значения передаточного числа редуктора по условию минимума резонансного максимума в двухмассовой системе за счет усиления или ослабления электромеханической связи в зависимости от соотношения обобщенных параметров электротехнического комплекса, которые оценивают частотами среза ω 1 , ω 2 , ω 3 , описывается следующей системой уравнений:
^ — 7 ро
РМ ^ РМ' ^ РС к дС- j
^ — / РО — 1 •
2 ;
^ КРС —
к рм ^к рс ^к дс
( ®2
I —, если ю7
I ют
® з — „з
ω
I —, если © 2
<
' РС .
1 •
> — ' РС
Юз — , 1 ,
'РМ где m1 - частота среза контура регулирования скорости двигателя; ш2 — контур, учитывающий наличие упругого звена с крутильной жесткостью C1; контур 3 учитывает наличие электромеханического влияния упругих колебаний на работу контура
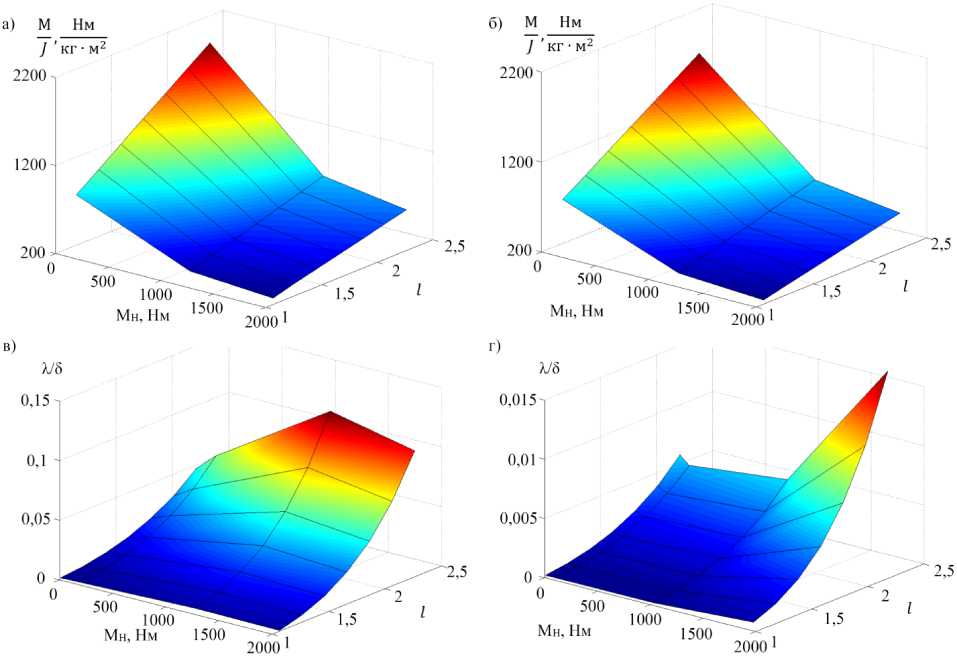
Рис. 4. Оптимизация второго участка движения: а - отношение М Н/ J в асинхронном двигателе; б - отношение М Н/ J в многофазном синхронном реактивном электроприводе; в - прогиб вала в асинхронном двигателе;
г – прогиб вала в многофазной синхронной реактивной машине
Критерии
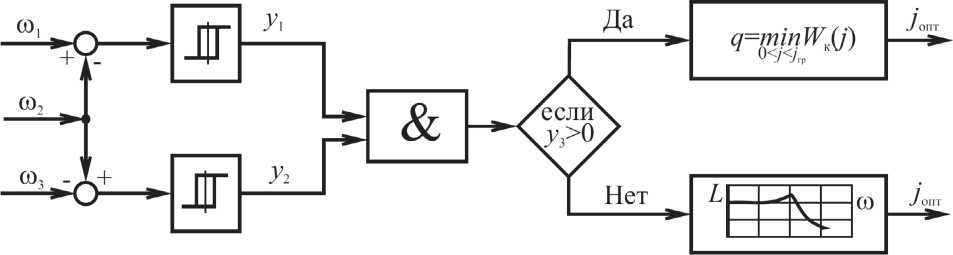
Рис. 5. Выбор максимальной скорости по различным критериям
регулирования скорости; к РМ - передаточный коэффициент контура регулирования момента; j - передаточное число редуктора; /РО , /дв - моменты инерции рабочего органа и двигателя; к РС - коэффициент передачи регулятора скорости.
В случае, если условие применения первого критерия не выполняется, рационально использовать второй критерий [8]. На рис. 5 представлен алгоритм выбора предельной скорости по различным критериям.
На промежутке t4–t5 (см. рис. 1) движения электропривода регуляторы работают в линейном режиме. На данном участке обеспечение устойчи- вости путем выбора структуры и оптимальной настройки регуляторов контура положения является нетривиальной задачей. Это обуславливается неустойчивыми режимами работы при большой разнице заданного и фактического значений сигналов в случае обеспечения устойчивости при малом рассогласовании.
Электроприводы с многофазными синхронными реактивными машинами позволяют обеспечить высокую перегрузочную способность по крутящему моменту, что позволяет не только увеличить уставку по предельной скорости, но и расширить диапазон регулирования электропривода. При этом необходимо учитывать, что продолжительная перегрузка по моменту, а следовательно, и по току, ведет к перегреву электрической машины. Время работы в таком режиме будет зависеть от способа охлаждения [9]. В случае если по результатам расчета по нагреву электропривод не обеспечивает требуемую нагрузку, возможно прибегнуть к применению жидкостного охлаждения, поскольку увеличение мощности машины повлечет увеличение момента инерции, что вернет к проблеме обеспечения динамики электропривода.
Результаты практического применения
Проектирование, выбор силового оборудования и расчет параметров системы управления для опытного образца системы электропривода в ООО НТЦ «Приводная техника» выполнялось согласно представленной методике [10]. При помощи измерительного оборудования были получены диаграммы переходного процесса, которые на рис. 1 представлены диаграммами 1', 2', 3'.
Тиристорные источники питания были заменены на транзисторные, что позволило сократить потери и увеличить быстродействие в контуре регулирования момента. Помимо этого, в контур регулирования момента был внедрен последовательный регулятор с переменной структурой. В результате это позволило сократить время переходного процесса на первом отрезке времени.
Для сокращения времени переходного процесса на втором отрезке времени при линейном ускорении электромеханического преобразователя был спроектирован двигатель с удлиненным ротором, что позволило снизить момент инерции машины примерно в 2 раза. Результатом данного внедрения стало сокращение времени линейного ускорения на 25–30 %, что объясняется высокой долей инерции рабочего органа относительно электродвигателя в составе электромеханической системы. Также двигателю необходимо было обеспечить большую скорость в сравнении с действующей системой за счет увеличения её предельного значения.
Транзисторный источник питания позволил повысить ограничение скорости на третьем временном отрезке в 1,5 раза, что обусловлено повышением допустимой несущей частоты преобразователя. Так, в действующем тиристорном источнике питания по условиям теоремы Найквиста допустимая несущая частота была 25 Гц. Преобразователь частоты, построенный на базе транзисторных полностью управляемых силовых ключей, способен работать на несущей частоте в диапазоне от 2 до 16 кГц, что позволяет с применением широтно-импульсной модуляции обеспечить устойчивую выходную частоту, в 4 раза превышающую исходный источник питания. Требуемое переда- точное число редуктора рассчитывалось по критерию минимума кинетической энергии, в результате изменение передаточного числа редуктора j незначительное. Оптимизация системы приблизила график скорости к треугольной форме, в результате чего участок работы на установившейся скорости исчез.
Активный выпрямитель на входе позволяет обеспечить интенсивное динамическое торможение, что позволило сократить время технологического процесса при торможении. С учетом увеличения в 1,5 раза быстродействия контура регулирования скорости время разгона и торможения сократилось на 30 %.
Применение регулятора нелинейного типа и увеличение предельного значения в блоке ограничения в контуре регулирования положения позволило увеличить быстродействие на последнем временном отрезке технологического процесса на 60 % с учетом предельных значений по крутящему моменту (до 4 М Н).
Работы, проводимые в рамках модернизации стана ХПТ-450, позволили сократить примерно в 2 раза время технологического процесса, затрачиваемое на позиционирование рабочего органа. Необходимо обратить внимание, что на графике рис. 1, а нет однозначной связи между кривыми электромагнитного момента и скорости, как это описывает основное уравнение движения электропривода. Это возникает из-за требуемого в начальный момент времени большого значения момента сопротивления при срыве трубы с оправки, что влечет неравномерный график нагрузки в реальных условиях.
Выводы
Критерии выбора силовых элементов при разработке современных систем позиционного электропривода с широким диапазоном регулирования по крутящему моменту должны удовлетворять современным требованиям, предъявляемым к электроприводу.
Для обеспечения высокой точности работы и увеличения быстродействия системы к вопросам оптимизации параметров электромеханической системы необходимо подходить комплексно. Выбор оптимального передаточного числа редуктора по одному из перечисленных в работе критериев позволит обеспечить снижение влияния колебаний в первоначальный момент разгона и при завершении останова, в то же время это позволит повысить качество настройки регуляторов по подчиненной схеме управления электроприводом.
Выбор силовых элементов и параметров системы управления методами, описанными в работе, актуален и для традиционных систем электроприводов, которые работают в повторно-кратковременном режиме.
Список литературы Выбор силовых элементов электропривода стана холодной прокатки труб ХПТ-450 ПАО "ЧТПЗ"
- Law, J.D. Design and performance of field regulated reluctance machine / J.D. Law // IEEE Transactions on Industry Applications. - 1994. - Vol. 30, no. 5. - P. 1185-1192. DOI: 10.1109/28.315228
- Law, J.D. Design and performance of the field regulated reluctance machine / J.D. Law, A. Chertok, T.A. Lipo // IAS Annual Meeting (IEEE Industry Applications Society). - 1992. - P. 234-241. DOI: 10.1109/IAS.1992.244289
- Platonov, V.V. Mechatronics system control by criterion of minimum losses / V.V. Platonov, A.A. Imanova, A.A. Gryzlov // 2017 International Conference "Quality Management, Transport and Information Security, Information Technologies". - 2017. - P. 339-342. DOI: 10.1109/ITMQIS.2017.8085828
- Усынин, Ю.С. Системы управления электроприводов: учеб. пособие для вузов / Ю.С. Усынин. - Челябинск: Изд-во ЮУрГУ, 2004. - 328 с.
- Васильев, Б.Ю. Релейно-импульсные системы управления асинхронными электроприводами: прямого и фаззи-логического управления / Б.Ю. Васильев, А.Е. Козярук // Электротехнические системы и комплексы. - 2014. - № 1 (22). -С. 31-35.
- Sychev, D.A. Dynamic and technological traction drive parameters optimization / D.A. Sychev, N.I. Naumovich, E.S. Khayatov // Procedia Engineering. - 2015. - No. 129. - P. 987-991. DOI: 10.1016/j.proeng.2015.12.158
- Ключев, В.И. Теория электропривода: учеб. для вузов / В.И. Ключев. - М.: Энергоатомиздат, 2001. - 704 с.
- Kruglov, G.A. Calculation methods of electric drives and generators based on the field regulated reluctance machine / G.A. Kruglov, A.N. Gorozhankin, V.Y. Bespalov // 2017 International Conference on Industrial Engineering, Applications and Manufacturing (ICIEAM). - 2017. - P. 1-4, DOI: 10.1109/ICIEAM.2017.8076349
- Dadenkov, D.A. On the synthesis of passive-adaptive systems for electric drive control / D.A. Dadenkov, V.P. Kazantsev // Russian Electrical Engineering. - 2015. - Vol. 86, no. 11. - P. 661-666. DOI: 10.3103/s1068371215110024
- Innovative solutions from Privodnaya Tekhnika / S.A. Chupin, D.V. Sokolov, E.S. Chupin, N.I. Naumovich // Russian Electrical Engineering. - 2014. - Vol. 85, no. 10. - P. 628-629. DOI: 10.3103/s1068371214100046