Выбор сплава системы Mg-Zn-Zr и оптимизация изготовления заготовок для штамповки
Автор: Богданова Татьяна Александровна, Меркулова Галина Александровна, Горохов Юрий Васильевич, Скороходова Надежда Юрьевна, Чернов Сергей Васильевич
Журнал: Сибирский аэрокосмический журнал @vestnik-sibsau
Рубрика: Технологические процессы и материалы
Статья в выпуске: 2 (42), 2012 года.
Бесплатный доступ
Изучены структура и механические свойства сплавов ZK60A и МА14 системы Mg-Zn-Zr после литья, гомогенизации и деформации. Предложено заменить сплав МА14 на ZK60A для изготовления крупногабаритных штамповок. Показана возможность исключения операции редуцирования.
Магниевый сплав, структура, механические свойства, литье, гомогенизационный отжиг, деформация
Короткий адрес: https://sciup.org/148176787
IDR: 148176787
Текст научной статьи Выбор сплава системы Mg-Zn-Zr и оптимизация изготовления заготовок для штамповки
Деформируемые магниевые сплавы применяют в различных отраслях промышленности, в частности в самолетостроении, а также в конструкции автомобилей. Это связано с постоянными требованиями снижения веса, которые ведут к снижению расхода топлива и загрязнения окружающей среды. Однако магниевые сплавы обладают пониженными пластичностью и деформируемостью, и получение деформируемых изделий из них является проблемой. Данная работа является продолжением исследования литой структуры сплава системы Mg-Zn-Zr, в которой оптимизирована литая структура сплава ZK60А перед горячей деформацией [1].
Цель данной работы – обоснование возможности замены отечественного сплава МА14 на зарубежный ZK60A (система Mg-Zn-Zr) и поиск оптимальной технологии получения заготовок (галет) для изготовления крупногабаритных штамповок.
В связи с этим перед настоящей работой были поставлены следующие задачи:
– получить заготовки (галеты) из двух сплавов по различным технологиям, учитывающим исходное состояние и степени деформации;
– выполнить искусственное старение в одной садке;
– изучить механические свойства;
– исследовать микроструктуру.
Работа выполнена на образцах магниевых сплавов МА14 и ZK60A в лабораториях кафедры «Металловедение и термическая обработка металлов» Института цветных металлов и материаловедения СФУ. Испыта- ние механических свойств и опробование режимов деформации проведено в производственных условиях.
Деформируемые сплавы МА14 (отечественный) и ZK60A (зарубежный) относятся к системе Mg-Zn-Zr. Сплав МА14 в Российской Федерации начали применять в середине ХХ в. Его изготавливают по ГОСТ 14957–76.
Первая публикация по сплаву ZK60A (Mg – 6 % Zn – 0,7 % Zr) появилась в 1946 г. [2]. В работах S. Bhan, Г. И. Морозовой, Е. Ф. Волковой и других приведены некоторые результаты исследований сплавов системы Mg-Zn-Zr [3–5].
В данной работе изучены полуфабрикаты сплава МА14 (табл. 1) и круглые слитки сплава ZK60A (табл. 2).
Слитки режут на заготовки и после гомогенизации подвергают горячей объемной штамповке и искусственному старению. После определения механических свойств и структуры штамповки отправляют заказчику.
Технология изготовления штамповки в открытом штампе предусматривает операцию изготовления заготовок (галет). В данной работе исследованы 15 осаженных в «торец» заготовок с разной степенью деформации. Исходные заготовки были разбиты на 5 групп (табл. 3).
Редуцирование – процесс вытяжки круглой заготовки, заключающийся в уменьшении поперечного сечения путем всестороннего бокового обжатия.
Давление в рабочем цилиндре пресса составляет 200, 100, 50 атмосфер соответственно, или 20, 10, 5 МПа.
Таблица 1
Химический состав сплава МА14, % (масс.) по ГОСТ 14957–76
Основные компоненты |
Примеси, не более |
|||||||||
Мg |
Zn |
Zr |
Аl |
Cu |
Ni |
Si |
Be |
Fe |
Мn |
Прочие примеси |
Основа |
5,0–6,0 |
0,3–0,9 |
0,05 |
0,05 |
0,005 |
0,05 |
0,002 |
0,03 |
0,1 |
0,3 |
Таблица 2
Химический состав сплава ZK60A, % (масс.) по ASTM В296
Основные компоненты |
Примеси, не более |
||||||||
Mg |
Zn |
Zr |
Al |
Cu |
Ni |
Si |
Fe |
Mn |
Прочие примеси |
Основа |
5,18 |
0,58 |
– |
0,0019 |
0,000 56 |
0,001 1 |
0,002 1 |
0,013 |
– |
В каждой группе взяли по 3 заготовки, отличающиеся степенью деформации (табл. 4):
-
1) ∅ 290–310 мм;
-
2) ∅ 360–400 мм;
-
3) ∅ 505–590 мм.
Так как при деформации происходило увеличение диаметра, то рассчитывали коэффициент осадки λ по формуле
λ = F 2 / F 1 , (1)
где F 1 – площадь образца до деформации; F 2 – площадь образца после деформации.
Механические свойства галет приведены на рис. 1–4.
Испытания проводили на трех образцах в радиальном (долевом) и хордовом (поперечном по ширине) направлениях. Сравнительный анализ механических свойств образцов, отобранных в долевом (из центральной зоны заготовки) и широтном (из периферийных зон) направлениях показал, что наиболее стабильные свойства имеют образцы в широтном направлении. Это предполагает наследственную структуру исходной заготовки и значительную анизотропию свойств в центральной зоне заготовок с различной степенью деформации. Поэтому показателями качества заготовок являлись характеристики временного сопротивления (σв), условного предела текучести (σ0,2) и относительного удлинения (δ), полученные для образцов в хордовом направлении, что можно объяснить более высокой степенью проработки периферийных зон галет и подтвердить сравнительным анализом микроструктуры центра и периферии.
Технология получения галет
Таблица 3
Группа |
Марка сплава |
Получение галет |
Усилие пресса, атмосфер (МПа) |
Маркировка на галетах |
1 |
МА14 |
прессованный пруток ∅ 240 мм |
100 (10) |
7, 8, 9 |
2 |
ZK60A |
литая заготовка ∅ 260 мм без дополнительной гомогенизации перед деформацией |
200 (20) |
1–2, 2–2, 3–2 |
3 |
литая заготовка ∅ 260 мм после дополнительной гомогенизации перед деформацией |
100 (10) |
4, 5, 6 |
|
4 |
литая заготовка после редуцирования ∅ 220 мм с температурой деформации 330 °С (маркировка на галетах Р1, Р2, Р3) |
50 (5) |
Р1, Р2, Р3 |
|
5 |
литая заготовка после редуцирования ∅ 220 мм с температурой деформации 270 °С |
50 (5) |
Р4, Р5, Р6 |
Значение коэффициента осадки
Таблица 4
Маркировка на галетах |
4 |
5 |
6 |
7 |
8 |
9 |
1-1 |
1-2 |
3-2 |
Р1 |
Р2 |
Р3 |
Р4 |
Р5 |
Р6 |
Конечный диаметр, мм |
310 |
370 |
590 |
290 |
360 |
520 |
310 |
400 |
560 |
290 |
350 |
505 |
310 |
350 |
505 |
Начальный диаметр, мм |
260 |
240 |
260 |
220 |
|||||||||||
Коэффициент осадки, λ (при увеличении диаметра) |
1,42 |
2,03 |
5,15 |
1,5 |
2,25 |
4,69 |
1,42 |
2,37 |
4,64 |
1,2 |
1,8 |
3,77 |
1,42 |
1,8 |
3,77 |
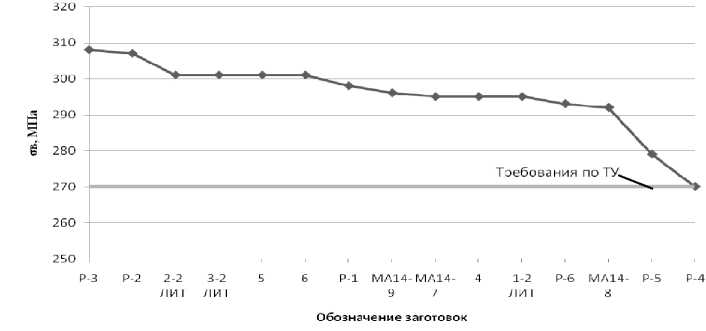
Рис. 1. Изменение временного сопротивления разрыву «долевых образцов» в зависимости от технологии изготовления заготовки
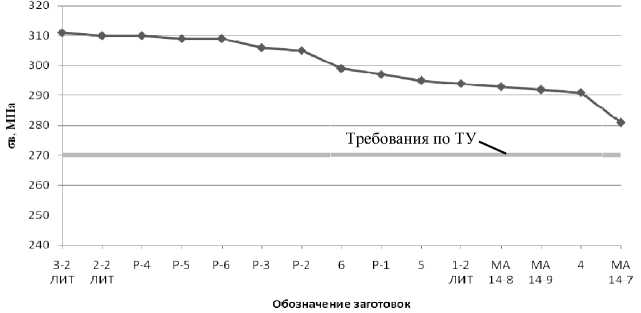
Рис. 2. Изменение временного сопротивления разрыву «широтных образцов» в зависимости от технологии изготовления заготовки
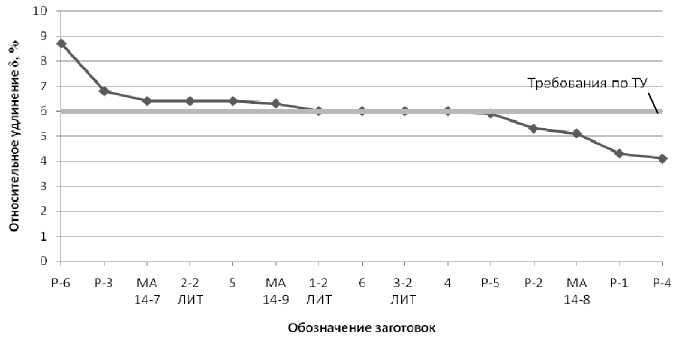
Рис. 3. Изменение относительного удлинения «долевых образцов» в зависимости от технологии изготовления заготовки
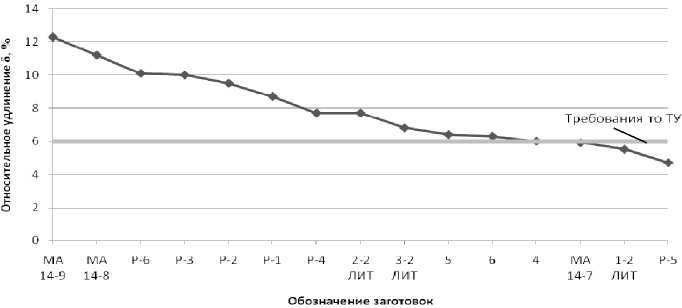
Рис. 4. Изменение относительного удлинения «широтных образцов» в зависимости от технологии изготовления заготовки
Анализ результатов испытаний механических свойств позволил выявить наиболее низкие значения прочностных свойств и высокий уровень относительного удлинения у галет из сплава МА14 с высокой и средней степенью деформации.
Близкие по значениям свойства получены у заготовок после редуцирования, но только с высокой степенью проработки. Самую низкую пластичность имеют галеты всех групп с малой степенью проработки.
Сопоставив механические свойства двух сплавов, можно сделать вывод о целесообразности применения сплава ZK60A.
Для оценки стабильности свойств относительно выбора исходной заготовки показательным является анализ образцов в радиальном направлении. У образцов, отобранных из центральной зоны галет и прошедших операцию редуцирования, получены самые нестабильные результаты механических свойств относительно периферии.
Для уточнения режимов изготовления штамповок из литых заготовок сплава ZK60A с применением операции редуцирования было дополнительно проведено пробное изготовление 3 штамповок.
Результаты испытания механических свойств опытных штамповок приведены в табл. 5. Всего для испытания было отобрано 48 образцов: 12 – в долевом направлении, 24 – по ширине и 12 – по толщине.
На основании полученных положительных результатов пробного изготовления штамповок было проведено редуцирование ряда заготовок различных плавок. Результат редуцирования оказался отрицательным – все заготовки не выдержали деформации и разрушились (рис. 5).
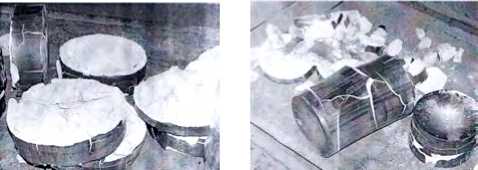
Рис. 5. Разрушение заготовок после редуцирования
Температуру в печи с находящимися на нагреве заготовками снизили на 20 ºС, через 4 часа после выравнивания температуры воздуха в печи провели редуцирование. Результат получен положительный, разрушения не произошло.
Очередную партию заготовок различных плавок редуцировали при установленной температуре, вновь получен отрицательный результат, заготовки разрушились.
Проанализировав ранее полученные результаты и сопоставив полноту гомогенизации заготовок, очередную партию заготовок подвергли циклическому нагреву, после чего проведено редуцирование. Результат получен положительный. Необходимо отметить, что использование операции редуцирования приводит к снижению выхода годного материала и повышению общезаводских затрат. Поэтому предложено исключить операцию редуцирования из технологии получения штамповок.
Вид осаженных заготовок № 4, 5, 6 представлен на рис. 6.
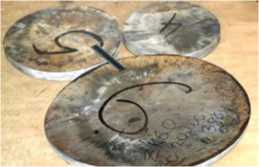
Рис. 6. Вид осаженных заготовок из сплава ZK60A на ∅ 310 мм (№ 4), ∅ 370 мм (№ 5), ∅ 590 мм (№ 6)
Исследование микроструктуры выполнено на образцах, отобранных из центральной и периферийной зон галет (рис. 7).
Таблица 5
Уровень механических свойств пробных штамповок
Направления вырезки образцов |
Статическая функция |
Характеристика |
||
σ в , МПа |
σ 0,2 , МПа |
δ, % |
||
Долевое |
Среднее значение |
314 |
254 |
12,1 |
Интервал (min–max) |
306–324 |
237–270 |
7,2–20 |
|
По ширине |
Среднее значение |
304 |
230 |
13,3 |
Интервал (min–max) |
293–311 |
192–257 |
8,8–20,8 |
|
По толщине |
Среднее значение |
293 |
153 |
15,7 |
Интервал (min–max) |
288–301 |
138–185 |
8–21,2 |
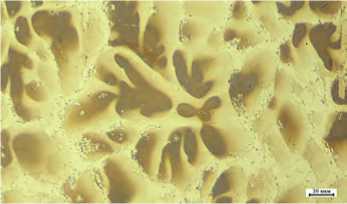
а
Рис. 7. Микроструктура образцов сплава ZK60A, вырезанных из центра ( а ) и периферии ( б ) заготовки № 4 Ø 310 мм (без редуцирования)
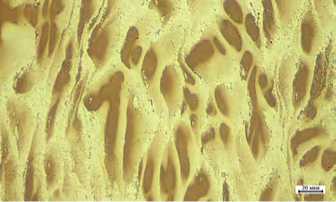
б
В магниевых сплавах низкие скорости диффузионных процессов приводят в условиях неравновесной кристаллизации к сильному развитию дендритной ликвации (даже при малых скоростях охлаждения при затвердевании).
Дендритная ликвация способствует снижению механических свойств и технологической пластичности слитков. Поэтому перед деформацией слитки необходимо подвергать гомогенизирующему отжигу [2], после которого все еще видны дендриты (рис. 7).
Таким образом, проведенное опытно-промышленное изготовление штамповок из сплава ZK60A с применением редуцирования показало невозможность получения стабильных качественных штамповок из-за сложности оптимизации технологии гомогенизации исходного металла.
Анализируя приведенные результаты, можно сделать вывод о возможности использования сплава ZK60A для изготавления крупногабаритных штамповок вместо МА14, так как галеты из сплава ZK60A имеют более высокие значения прочностных свойств, и целесообразности исключения операции редуцирования.