Взаимосвязь стойкости к коррозионно-термической усталости котельных труб с теплопроводностью дефектных структур
Автор: Помазова А.В., Панова Т.В., Заворин А.С., Артамонцев А.И.
Журнал: Журнал Сибирского федерального университета. Серия: Техника и технологии @technologies-sfu
Статья в выпуске: 4 т.10, 2017 года.
Бесплатный доступ
В статье представлены результаты исследования влияния многократной нормализации на коэффициент теплопроводности углеродистой стали 20, применяемой в теплоэнергетике для изготовления труб поверхностей нагрева. Установлено влияние термообработки на характер формирующихся коррозионных отложений. Обнаружено, что помимо фазового состояния стали 20 на величину теплопроводности оказывают влияние и структурные изменения, происходящие в стали при термообработке. По мере увеличения межпластинчатого расстояния и толщины пластинок цементита теплопроводность увеличивается. Проведенные исследования выявили, что коэффициент теплопроводности образцов труб в состоянии поставки при температуре, близкой к температуре эксплуатации (300 °С), имеет значительный разброс данных (от 10 до 20 %). Анализ разрушенных образцов показал, что скорость развития коррозионно-термической усталости различается в 1,4 раза и зависит от уровня теплофизических свойств и вида окалины.
Коэффициент теплопроводности, нормализация, структурно-фазовое состояние, сталь 20, коррозия
Короткий адрес: https://sciup.org/146115899
IDR: 146115899 | DOI: 10.17516/1999-494X-2017-10-4-557-571
Текст научной статьи Взаимосвязь стойкости к коррозионно-термической усталости котельных труб с теплопроводностью дефектных структур
пульсирующий характер, при этом часто и резко изменяется скорость движения эмульсии, ее паросодержание [1]. Кроме того, в процессе эксплуатации возможны такие ситуации, когда на горячую поверхность попадает среда с более низкой температурой, что способствует ускорению процесса коррозионно-термической усталости [2]. Очагами развития КТУ, как правило, служат язвы, каверны и другие поверхностные дефекты.
Влияние коррозионной среды на сопротивление усталостному разрушению исследовалось различными авторами [3, 4]. Роль структуры поверхности и строение поверхностной оксидной пленки были рассмотрены в работе [5]. При этом экспериментальные исследования влияния структуры на сопротивление знакопеременным нагрузкам практически отсутствуют [2]. В работе [6] было показано, что скорость коррозии зависит от степени однородности микроструктуры, и установлен наиболее эффективный режим термической обработки углеродистой стали 20, применяемой в теплоэнергетике для изготовления труб поверхностей нагрева. Термическая обработка по-разному влияет на коррозионные свойства, на изменения свойств образующихся защитных окисных пленок на поверхности металла, а также на теплофизические характеристики углеродистой стали.
Одной из основных характеристик работы элементов котла является величина тепловой нагрузки поверхности нагрева, по которой можно судить, насколько эффективно используется поверхность нагрева, проводить сравнение для всего агрегата или отдельных его частей [7]. Через материал поверхности нагрева, а также через слои внешних и внутренних отложений теплота передается за счет их теплопроводности. При этом от толщины и теплопроводности отложений очень зависит температура металла поверхности нагрева [8, 9]. В процессе термоциклирования наличие температурных градиентов приводит к термическим напряжениям. Анализ теплопроводности для прогнозирования термомеханической усталости, теплового сопротивления, оценки срока службы трубных элементов, работающих в условиях тепловой усталости, был представлен в модельной оценке в работах [10-12]. Авторы работы [13] показали, что теплопроводность структурных составляющих в процессе термообработки ограничивает размеры фаз, что затрудняет получение желаемой микроструктуры. При этом тепловая неравномерность является следствием неравномерности тепловосприятия, конструктивной нетождественности и гидравлической разверки. Неравномерность тепловосприятия связана с неоднородными распределениями температуры, скорости продуктов сгорания, циркулирующего теплоносителя и теплопроводности металла стенки трубы [14]. Корреляция между микроструктурой и теплопроводностью, связанная с дефектами структуры [15], приводит к увеличению теплопроводности в бинарных сплавах при уменьшении числа дефектов кристаллической решетки и мелкодисперсных частиц в процессе термообработки [16-18].
Экранные трубы из стали 20, подвергнутые термообработке согласно техническим условиям «Трубы стальные бесшовные для паровых котлов и трубопроводов» [19], не исследовались на характер влияния микроструктуры на теплопроводность. В связи с этим в настоящей работе проведено исследование влияния теплофизических характеристик труб из углеродистой стали 20 на стойкость к КТУ. Представляется актуальным изучение влияния многократной нормализации на теплопроводность такой стали, на характер формирующихся коррозионных отложений, а также выявление взаимосвязи между теплопроводностью дефектных структур котельных труб и стойкостью к коррозионно-термической усталости.
Материалы и методы
Образцы первой партии стали 20 (состав, мас. %: углерод 0,185±0,016, кремний 0,28±0,03, марганец 0,49±0,03, хром 0,085±0,008, никель 0,035±0,008, медь 0,041±0,008, сера 0,004±0,002, фосфор 0,007±0,002, остальное железо), вырезанные из листового проката, подвергались многократной нормализации в электропечи камерной СНОЛ-1,4.2,5.1,2/12,5-И1 при температурах 900, 910, 920, 930, 940, 950 ºС. Количество циклов при каждой температуре варьировалось от одного до пяти. Во второй партии были взяты образцы, поврежденные в результате развития коррозионно-термической усталости: две трубы потолочного пароперегревателя из стали 20 одинакового типоразмера 0 42x5 мм после 122 (образец № 1) и 175 (образец № 2) тыс. эксплуатации при температуре 368 ºС и давлении 15,2 МПа. Для исследования теплопроводности были взяты образцы с менее нагруженной тыльной стороны. Морфологический анализ структурных составляющих стали проводился на металлографическом анализаторе фрагментов микроструктуры твердых тел «Ресурс С7», включающем в себя инвертированный микроскоп Olympus GF41 с программным обеспечением SIAMS Photolab (относительная погрешность измерений от ± 0,25 (при увеличении до *500 включительно) до ± 0,65 % (при увеличении свыше *500)).
Существующие модели расчета теплопроводности в зависимости от состава и температуры не показывают высокой точности [15], поэтому исследование коэффициента теплопроводности в настоящей работе проведено экспериментально стационарным методом неограниченной пластины [9]. Структурно-фазовое состоянии исследовалось на рентгеновском дифрактометре ДРОН-3М ( X Cu=1,54 А). Механические испытания и оценка коррозионных отложений проводились, соответственно, на разрывной машине Р-5 и на микроскопе Neophot-2 (погрешность измерения составила 5 %).
Результаты и их обсуждение
В теплоэнергетике используются введённые с 2004 г. технические условия, согласно которым котельные трубы из углеродистой стали 20 поставляют в термообработанном состоянии, после однократного режима нормализации в температурном интервале 920÷950 ºС [19]. Экспериментальные зависимости изменения теплопроводности образцов от температуры испытания, полученные после однократной нормализации в диапазоне температур 900÷950 °С, приведены на рис. 1. Они построены по методу наименьших квадратов и обобщают (аппроксимируют) экспериментальные данные, представленные в табл. 2.
Видно, что температура нормализации оказывает значительное влияние на коэффициент теплопроводности, который закономерно уменьшается при росте температуры испытания для всех режимов термообработки. При этом интенсивность снижения коэффициента теплопроводности возрастает с увеличением температуры нормализации. Начиная с температуры 920 ºС угол наклона прямых практически одинаков, однако его величина отличается для каждого режима испытания. Коэффициент теплопроводности образцов, прошедших рекомендованную по техническим условиям термообработку в температурном интервале 920-950 °С, при температуре, близкой к температуре эксплуатации ~300 ºС, имеет значительный разброс данных (~10 %). Разброс значений при этой температуре во всем исследованном температурном диапазоне нормализации (900÷950 ºС) также составляет ~10 %.
На рис. 2 показано повреждение образцов № 1 и № 2, взятых с прямых участков плавниковых труб п цов произошло с огневой стороны на наружной поверхности образ лкими фрагментами на половин с. 3 а ). Оксидная пленка на наруж ия в виде редких отслоений мелк 3 б ). Нарушение целостности окс ности резко возрастает теплова ературы на этой части поверхнос
После удале ескивание на наружной и внутре ь трещин составляет до 60 мм (ри

Рис. 1. Зави си мость теплопр овод ности об^разцо в от те м п ера^ тур ы по сле о днокр атной нормал изации, проведенной при различных темп ературах
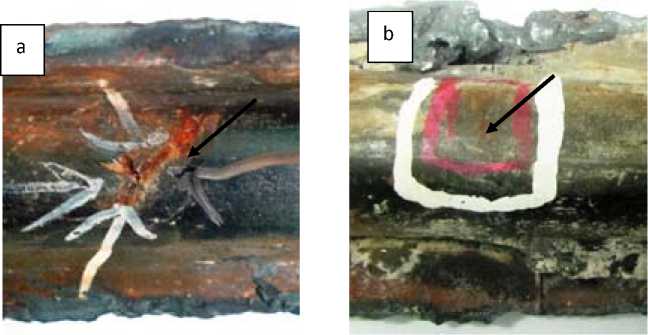
Рис. 2. Внешний вид по вреждения о браз цов № 1 (а) и № 2 (b)
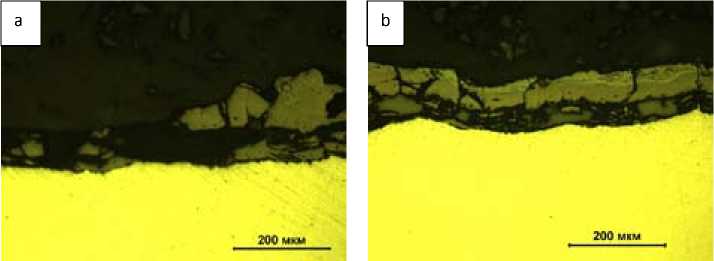
Рис. 3. Состояние ок алины на н аружной п ове рхности об ^ разцов № 1 (а) и № 2 (b) ( ^ нет р авле н ый ш лиф ^ )
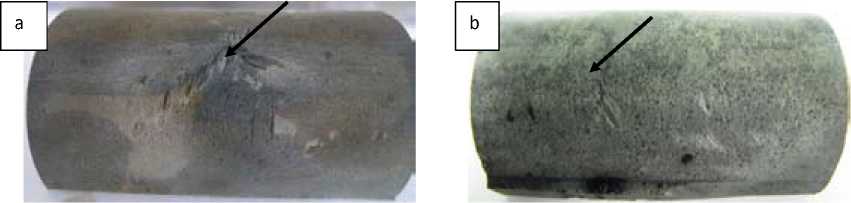
Рис. 4. Наружная п ов ерхность п о врежденны х о бразц ов № 1 (а) и № 2 (b) по сл е у^дал ен ия к^орро зионны х отложений
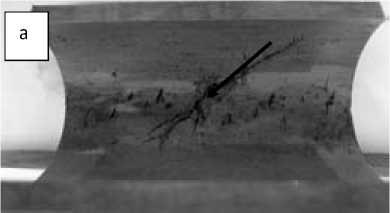
Рис. 5. Внутрення я п оверхность по врежденн ых об ^ разцов № 1 (а) и № 2 (b) посл е уд ал ени я кор ^ ро зио нных отложений
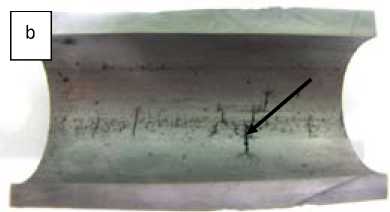
Резул ьтаты механи ческих испытани й, значени я коэффици ента тепло проводн ости, скоро -сти развития КТУ, фактора разнозернистости основного металла приведены в табл. 1. Анализом механиче ск их характер истик устано влено, что раз ница этих св о йст в ме ж ду о бразц ами незначительна и находится в пределах погрешности и змерений. О^ днако при этом теплопроводность обра зцов отличаетс^я сущест венно.
Для у^ становления причи н трещи нообразов ания вблиз и мест по врежден ия бы ли сд ела ны продольные срезы, которые показали траектории развития трещин КТУ (рис. 6). У образца № 1 траектория трещины более развита, из вершины трещина развивается по трем направлениям.
Таблица 1. Предел прочности ( σв ), предел текучести ( σ т), относ итель н ое удлинение ( δ ), относительное сужение ( ψ ), коэффициент теплопроводности ( λ ), фактор разнозернистости (FZ), скорость развития КТУ (V КТУ ) разрушенны х образцов
Образец |
а . , МПа |
а т, МПа |
δ , % |
ψ , % |
λ , В т/ (м·град) |
F z |
V KTy , мм/за 105 ч |
Основной металл трубы № 1 |
4,59±0,18 |
3,44±0,14 |
6 8 ,3±2 ,7 |
36,4±1 ,5 |
40,3 |
0,25 |
3,1 |
Основной металл трубы № 2 |
4, 72±0,19 |
3,7 7±0,15 |
65, 3±2,6 |
37 ,2±1,5 |
48,2 |
0,26 |
2,2 |
Требован ия ТУ 14-3Р-55 -2001 [19] |
4,20-5,60 |
≥2,20 |
≥45,0 |
≥24,0 |
- |
- |
- |
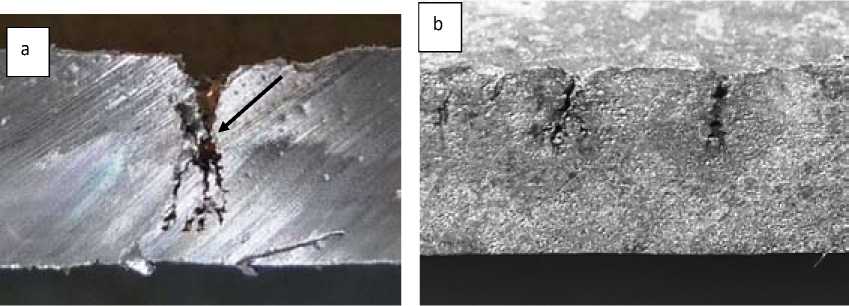
Рис. 6. Развитие т ^ рещины ко ^ ррозионно- термической усталости по тол щине стенк и тр ^ убы образ ца № 1 (а) и № 2 (b)
Это отличие может быт ь связано как с разны м с труктурн ым состоянием, так и с наличием градиента твердости то толщине стенки трубы, приводящего к сложнопрогнозируемому механизму раз вития т^рещ ин ы [10].
При металлографическом исследовании „„e™. что трещины ра^ааю™ „реиму щественно от коррозионных язв и имеют транскристаллитный характер с пережимами в сечении, раздваивающ имися по м е ре рос та и за полненны ми продуктами корр озии (рис . 7). В первом образце трае к тори я тр ещин более развит а. Макси мальная ширина меж кри стал литных трещи н в микроструктуре трубы № 1 составляет 190 мкм, в микроструктуре трубы № 2 - 115 мкм. Ширина межкристаллитных трещин двух образцов отличается в 1,6 раз. Микроструктура металла феррито-перлитная, со всех сторон трубы без значительных структурных изменений.
Анализ морфологии раз рушенных зон показал, что, несмотря на разное вр ем я эксплуатации, разру шение осу ществляется по одному и т ому же меха ^ низму и о пределяю щим фактор ом является коррозионно-термическая усталость, скорость которой различается в 1,4 раза и зависит от теплофизических свойств и вида окалины. Остальные контролируемые характеристики двух труб отличаются друг от друга незначительно. Значения коэффициентов теплопроводности отличаются на 20 % и составляют 40,3 и 48,2 Вт/(м^град) для труб № 1 и № 2 соответственно. Это различие больше в два раза, чем было показано по аппроксимирующей зависимости – 563 –
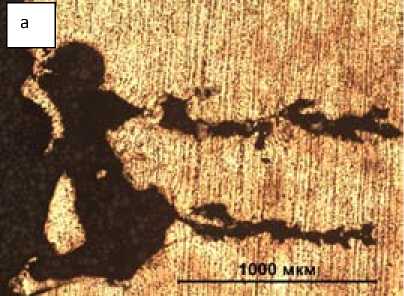
Рис. 7. Профил ь п оперечног о сечения трещ ин корр озионно-т ермической усталости, разви вающихся о т коррозионных язв н а в нутренней повер хно сти образцов № 1 (а) и № 2 (b) (^травленый шл иф^)
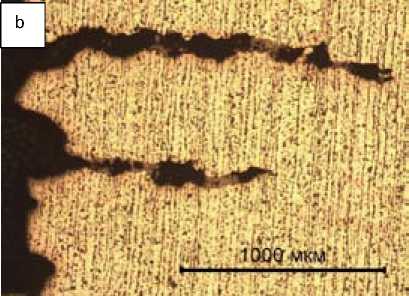
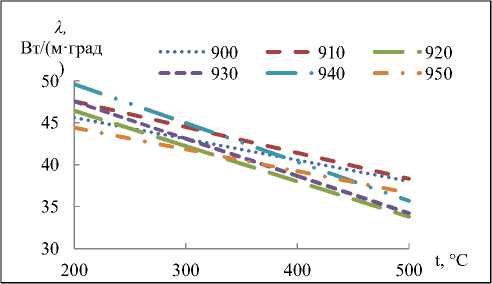
Рис. 8. Зависи мо сть теплопров одности образцов о т температ ур ы после двукр атной нормализации , проведенной при различных т емпературах
при проведении лаб свой ствах труб оно, по-видимому, связа зменение тепло проводности при изг от
Поскольку ран приводит к значительному изменени х характеристик и улучшению одноро ования теплопроводности образцов по лом 10 °С в температурном диапазон сти образцов стали 20 от темпе ра^туры после д вукратной нормали зац ии (рис. 8) по казывает, что в образцах, подвергнутых двукратной норм ал изац ии, разброс значений коэ ффицие нта тепл опроводности при температуре экс плуа^тации ~30 0 °С уменьшае тся. При этом р азб^рос зн ачени й коэффициента теплопроводности при температуре 300 °С во всем исследованном температурном диапазоне нормализа ции составляет ~7 %, пр и 4 00 °С – ~12 %, при 2 00 °С – ~14 %, при 5 00 °С – ~24 %. Х арактер ум еньшения коэ ффициента теп лопр овод н ости практически аналогичен варианту однократной нормализации.
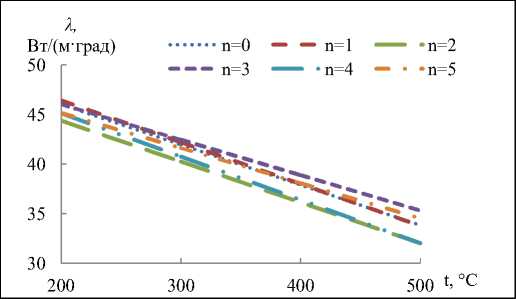
Рис. 9. Зависим!ость теплопроводности от температуры! образцов после нормализации при 920 °С при различных количествах ц икло в (n ^ =1÷5 )
Количество циклов нормализации при 920 °C влияет на значение коэффициента теп лопрово нта теплопроводности при температуре 300 °С наблюдается у образцов, прошедших пятикратный цикл нормализации, - 42,4 Вт/(мтрад), минимальная - у образцов после четырехкратного цикла нормализации - 39,5 Вт/(м-град).
Известно, что фазовые превращения, происходящие в стали и ри термообработке, оказывают существенное влияние на теплопроводность, которая изменяется в зависимости от объемной концентрац ии составл яющих фаз [21 ]:
N ц ( λ ф - λ ц ) Nц N ф t
-
N ( λц ) Nф 30
ц 2λ^ф где Хспл - коэффициент теплопроводности искомого сплава; хф - коэффициент теплопроводности ф еррита при 0 °С (λ = 76,8 Вт/(м·г рад)); λц – коэф фициент т еплопровод ности цем ентита (λ =7,1 Вт/(м· град)^); Nц – доля цементита в сплаве; Nф – доля феррита в с плаве (^Nф + Nц=1); t – темпе рат ура сплава.
Формула применима для всех углеродистых сталей при температуре до 727 °С и дает по-грешно сть в этих у^слов иях н е более 10 % [2 1]. Рент гено фазовый анал из пока зал , ч то в исходном сост оя нии и после вс ех видов т ерм и ческо й обработки струк^тура ста ли 20 яв ляет ся феррито-п ерлитной [2 0]. От носи тельна^я объемная доля ферр итной фаз ы сос тав ляет 68,6 ÷85,4 %, перлитной – 14, 6÷31,4 % для ис следуемого диапа зона темпер атур н ормализации . Анализ полученных результатов расчета с использованием правила аддитивности и сравнение с экспериментальными данными по измерению теплопроводности показали отклонение от правила (табл. 2), с превышением допустимой погрешности после отдельных циклов нормализации. Очевидно, что при увеличении циклов нормализации стали 20 помимо фазового состояния на теплопроводность могут оказывать влияние и структурные изменения, такие как изменения межпластинчатого расстояния и толщины пластинок цементита, образование видманштетта и другие изменения степени однородности системы. Так, было установлено, что при образо- – 565 –
Таблица 2. Расчетные и экспериментальные определения коэффициента теплопроводности при 300 °С
Зависимость коэффициента теплопроводности образцов стали 20 от размерных параметров перлита при t=300 °С (рис. 10) демонстрирует, что по мере увеличения межпластинчатого расстояния и толщины пластинок цементита теплопроводность увеличивается, что указывает – 566 – на значительное влияние морфологии перлита на теплофизические свойства образцов из стали 20. Минимальное значение коэффициента теплопроводности соответствует межпластинчато -му расстоянию ~0,2 мкм после четырех циклов нормализации при 920 °С. При этом корреляционная связь между коэффициентом теплопроводности и степенью деформации кристаллической решетки о тсутствуе т.
Сравнением изменения теплопроводности при 300 °С образцов стали 20 после всех циклов тер мообработки и пр и р азли чных темпе ратурах нормал изации (табл. 2 и рис. 11 ) у стано вле но, что во всем исследуемом температурном интервале максимальное значение коэффициента теплопроводности наблюдается после пятикратного цикла нормализации при 950 °С, минимальное – в режиме 920 °С и двух циклах. При n=1 и 2 независимо от температуры термообработки коэффициент теплопроводности практически не меняется. При анализе режимов, рекомендованных техническими условиями, видно, что они приводят к формированию разного уровня тепл офизическ их свойств (разниц а ~ 4 Вт/(м·град )).
Вт/(мтрад)
45,0
• • • • • межпластинчатое расстояние
^ * толщина цементитных пластинок
44,0
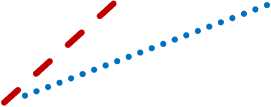
0 0,2 0,4 0,6 0,8 Г’МКМ
43,0
42,0
41,0
Рис. 10. Зависимость теплопроводности образцов стали 20 от размерных параметров перлита при t=300 °С
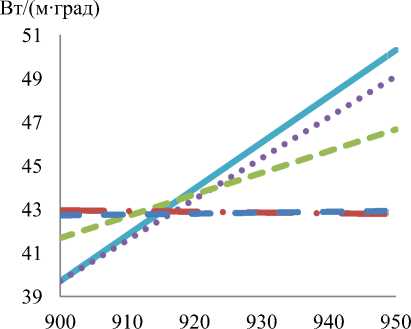
Рис. 11. Зав исимость тепл опроводности образц ов при 30 0 °С пос ле нормал изации при разл ичн ых температурах и количествах циклов
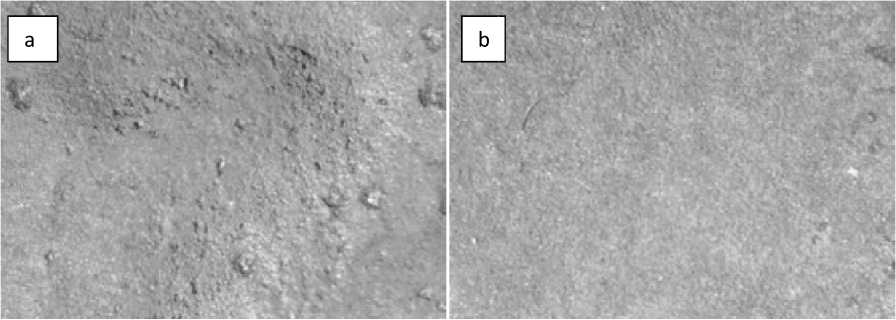
Рис. 12. Пове рхно сть образца из с тали 20 по сле пятикр атно й норма лизации при 95 0 °С (а) и двукратн ой – при 920 °С (b) (×70)
Режим, увеличивающий теплопроводность труб из стали 20, благоприятен по условиям экономичн ости. О днако одно временно с э тим после таких ре жимов термоо бработки на п оверх-ности труб ы формируетс я рыхлый неод нородн ый с лой продуктов корро зии (рис. 12 а ^), приводящий к снижению тепловой напряженности поверхности нагрева, что нивелирует эффект нормализации. На поверхности образцов стали 20, прошедших двукратную нормализацию при 920 °С, создается относительно ровный и плотный слой продуктов коррозии, имеющий достаточно хорошую адгезионную связь с поверхностью металла и защищающий ее от взаимодействия с рабочей средой (рис. 12 б ). Различие в значениях теплопроводности между этими образцами и образцами с максимальной теплопроводностью составляет 23 %. При этом разница в скоростях наружной коррозии – 62 % [20].
Коэффициент теплопроводности отложений на два порядка ниже коэффициента теплопроводности стали. Поэтому даже очень тонкий слой коррозионных отложений представляет собой тепловую изоляцию. Существующие технологии уменьшения толщины коррозионных отложений направлены либо на их механическое удаление, либо на совершенствование процессов горения и качества топлива [22]. Вместе с тем полученные результаты показали, что уменьшение толщины отложений может быть достигнуто также за счет увеличения коррозионной стойкости материала трубы путем дополнительной термообработки [23] и за счет пассивации трубы в режиме паровоздушной обработки [24].
Заключение
Проведенные исследования показали, что коэффициент теплопроводности образцов труб в состоянии заводской поставки имеет при температуре, близкой к температуре эксплуатации (300 °С), значительный разброс значений (от 10 до 20 %), что приводит к разной скорости развития КТУ в процессе эксплуатации. Обнаружено, что отдельные режимы термической обработки вызывают увеличение теплопроводности труб из стали 20. Однако одновременно с этим после таких режимов термообработки на поверхности трубы формируется рыхлый неоднородный слой продуктов коррозии, приводящий к снижению тепловой напряженности поверхности нагрева, что нивелирует эффект нормализации. Режим двукратной нормализации при 920 °С, – 568 – значительно улучшая антикоррозионные характеристики, много снижает теплопроводность, что, по-видимому, связано с формированием сорбитообразной структуры перлита.
Список литературы Взаимосвязь стойкости к коррозионно-термической усталости котельных труб с теплопроводностью дефектных структур
- Акользин П.А. Коррозия металла паровых котлов. М.: Энергия, 1957. 224 с
- Улиг Г.Г., Реви Р.У. Коррозия и борьба с ней. Введение в коррозионную науку и технику. Л.: Химия, 1989, 456 с
- Пачурин Г.В. Механизмы коррозионно-усталостного разрушения металлических материалов. Химия, биология, биотехнологии в современном мире: теория и практика: материалы международных научных конференции и симпозиума, 2013, 95-108
- Похмурский В.И. Коррозионная усталость металлов. М.: Металлургия, 1985. 207 с
- Пачурин Г.В. Роль структуры поверхности в коррозионной усталости деформированных металлических материалов. Современные проблемы науки и образования, 2014, 1, 209-225
- Помазова А.В., Панова Т.В., Геринг Г.И. Влияние разнозернистости структуры на коррозионную стойкость наружной поверхности труб из углеродистой стали 20, применяемых в теплоэнергетике. Вестник Южно-Уральского государственного университета. Серия «Металлургия», 2014, 14(4), 37-44
- Резников М.И., Липов Ю.М. Паровые котлы тепловых электростанций. М.: Энергоиздат, 1981. 240 с
- Рудыка А.В., Шейкин С.И., Шлыгин В.В. Температурный режим труб топочных экранов котла П-67. Теплоэнергетика, 1991, 3, 32-36
- Заворин А.С., Кузьмин А.В., Раков Ю.Я. Методы определения теплопроводности конденсированных сред. Томск: Изд-во Томского политехнического университета, 2009. 184 с
- Torabian N., Favier V., Ziaei-Rad S., Dirrenberger J., Adamski F., Ranc N. Thermal response of DP600 dual-phase steel under ultrasonic fatigue loading, Materials Science and Engineering: A, 2016, 677, 97-105
- Li D., Barrett R.A., O’Donoghue P.E., Hyde C.J., O’Dowd N.P., Leen S.B. Micromechanical finite element modelling of thermo-mechanical fatigue for P91 steels, International Journal of Fatigue, 2016, 87, 192-202
- Nilsson K., Dolci F., Seldis T., Ripplinger S., Grah A., Simonovski I. Assessment of thermal fatigue life for 316L and P91 pipe components at elevated temperatures, Engineering Fracture Mechanics, 2016, 168(A), 73-91
- Peet M.J., Hasan H.S., Bhadeshia H.K.D.H. Prediction of thermal conductivity of steel, International Journal of Heat and Mass Transfer, 2011, 54 (11-12), 2602-2608
- Богачев В.А. Повышение надежности поверхностей нагрева котлов ТЭС на основе исследования термогравитационных и магнитных явлений: дис.... д-р. тех. наук: 01.04.14, 05.11.13. М., 2002, 295 с
- Misra D.K., Sumithra S., Chauhan N.S., Nolting W.M., Poudeu P.F.P., Stokes K. L. Correlation between microstructure and drastically reduced lattice thermal conductivity in bismuth telluride/bismuth nanocomposites for high thermoelectric figure of merit, Materials Science in Semiconductor Processing, 2015, 40, 453-462
- Zhong L., Peng J., Sun S., Wang Y., Lu Y., Pan F. Microstructure and Thermal Conductivity of As-Cast and As-Solutionized Mg-Rare Earth Binary Alloys, Journal of Materials Science & Technology, 2016, 101, 160-165
- Su C., Li D., Ying T., Zhou L., Li L., Zeng X. Effect of Nd content and heat treatment on the thermal conductivity of MgNd alloys, Journal of Alloys and Compounds, 2016, 685, 114-121
- Kanaan А., Mazloum A., Sevostianov I. On the connections between plasticity parameters and electrical conductivities for austenitic, ferritic, and semi-austenitic stainless steel, International Journal of Engineering Science, 2016, 105, 28-37
- ТУ 14-3Р-55-2001. Трубы стальные бесшовные для паровых котлов и трубопроводов. М.: РНИИТП, 2001. 84 с
- Помазова А.В., Панова Т.В., Геринг Г.И. Роль структурных факторов в повышении коррозионной стойкости трубной стали при циклической термообработке. Известия Томского политехнического университета. 2015, 326(5), 15-21
- Давыдов С.В., Гуляев Ю.В., Симочкин В.В. Влияние теплофизических свойств углеродистых сталей на эвтектоидное превращение аустенита. Вестник Брянского государственного технического университета. 2008, 1, 4-9
- Отс А.А. Коррозия и износ поверхностей нагрева котлов. М.: Энергоатомиздат, 1987. 272 с
- Помазова А.В., Панова Т.В., Геринг Г.И. Способ повышения коррозионной стойскости труб из малоуглеродистых сталей. Патент РФ № 2580256. Бюллетень № 10, 2016
- Любимова Л.Л., Заворин А.С., Лебедев Б.В. и др. Способ определения оптимальной температуры пассивации трубных элементов теплоэнергетического оборудования и устройство для коррозионных испытаний. Патент РФ № 2544313. Бюллетень № 8, 2015