Закалка с последующим обогащением углеродом непревращенного аустенита (Q&P обработка) мартенситной коррозионностойкой стали AISI 414
Автор: Рущиц Сергей Вадимович, Ахмедьянов Александр Маратович, Маковецкий Александр Николаевич, Красноталов Александр Олегович
Журнал: Вестник Южно-Уральского государственного университета. Серия: Металлургия @vestnik-susu-metallurgy
Рубрика: Металловедение и термическая обработка
Статья в выпуске: 4 т.18, 2018 года.
Бесплатный доступ
Термическая обработка, заключающаяся в закалке стали до температуры внутри интервала мартенситного превращения с последующим перераспределением углерода между образовавшимся мартенситом и непревращенным аустенитом (Q&P обработка) применена к коррозионностойкой стали мартенситного класса AISI 414 (15Х13Н2). Моделирование режимов Q&P обработки выполнено на симуляторе термомеханических процессов Gleeble 3800. Фазовые превращения в процессе обработки изучались с помощью контактного дилатометра, измеряющего изменение диаметра образца в месте приварки термопары. После аустенитизации при 1150 °С в течение 3 мин температура начала мартенситного превращения исследуемой стали составила 270 °С. Для реализации Q&P обработки образцы закаливали до температур 250, 200, 150 и 100 °С. Перераспределение углерода между образовавшимся мартенситом и непревращенным аустенитом осуществлялось в процессе 3-минутной выдержки при 450 °С. Закалка до температур 200-250 °С с последующим отжигом при 450 °С не обеспечивает обогащение непревращенного аустенита углеродом, достаточное для подавления мартенситного превращения при последующем охлаждении до комнатной температуры. Понижение температуры закалки до 150 °С с последующим отжигом при 450 °С приводит к полной термической стабилизации непревращенного аустенита вплоть до температур -60 °С, что обеспечивает за счет TRIP эффекта высокую низкотемпературную вязкость исследуемой стали (KCV-60 = 59 Дж/см2), превосходящую значения, заложенные в требования к высокопрочным трубным сталям. Сделан вывод о перспективности Q&P обработки исследуемой стали для получения высокопрочного состояния с высоким уровнем низкотемпературной вязкости.
Мартенситные коррозионностойкие стали, q&p обработка, стабилизация остаточного аустенита, trip эффект
Короткий адрес: https://sciup.org/147232521
IDR: 147232521 | DOI: 10.14529/met180410
Текст научной статьи Закалка с последующим обогащением углеродом непревращенного аустенита (Q&P обработка) мартенситной коррозионностойкой стали AISI 414
В последние годы Q&P обработка была успешно использована для повышения комплекса свойств некоторых промышленных коррозионностойких сталей мартенситного класса [10–12]. Так, закалка стали AISI 410 (Fe–0,1 %C– 12%Cr) до температуры 240 °С и последующая выдержка при 450 °С в течение 6 мин обеспечила ~ 15 % обогащенного углеродом остаточного аустенита [10]. За счет TRIP эффекта достигнуто общее удлинение 22 % при пределе прочности 1200 МПа. Указывается, что добавки кремния в данном случае не являются обязательными, так как выделение карбидов в процессе стабилизирующей выдержки при 450 °С в значительной степени подавляется высоким содержанием хрома [10]. Тем не менее, легирование стали AISI 1 % кремния дополнительно увеличило долю остаточного аустенита и, как следствие, пластичность стали [11]. Применение Q&P обработки к стали AISI 420 (Fe–0,3 %C– 13 %Cr) показало, что присутствие в структуре «свежего» мартенсита, образованного в процессе охлаждения от температуры стабилизирующей выдержки, приводит к резкому падению пластичности и хрупкому разрушению и потому не допустимо [12]. В оптимальном режиме Q&P обработки (закалка до 80 °С с отжигом при 450 °С в течение 3 мин) обеспечивается наилучшее соотношение прочности и пластичности (предел прочности 1570 МПа, общее удлинение 16 %).
Материал и методика исследований
Химический состав исследуемой коррозионностойкой стали 15Х13Н2 (AISI 414) мартенситного класса приведен в табл. 1. Образцы для исследования вырезались из горячекатаной трубы, прошедшей термическую обработку, включающую закалку из межкритического интервала и последующий двукратный отпуск.
Цилиндрические образцы нагревали в вакууме до температуры аустенитизации 1150 °С со скоростью 10 °С/с и выдерживали 180 с. Высокая температура нагрева обеспечивала полное растворение карбидов, присутствующих в исходной структуре [12]. После аустенитизации один из образцов был охлажден со скоростью 20 °С/с до комнатной температуры. Остальные образцы охлаждались с той же скоростью до заданной температуры Т з в интервале мартенситного превращения (100 °С– 250 °С). После 60-секундной паузы при температуре закалки образцы нагревали, как и в работах [11, 12], до 450 °С и выдерживали 180 с для осуществления перераспределения углерода между мартенситом и аустенитом. Далее следовало охлаждение образцов до комнатной температуры со скоростью 20 °С/с (рис. 1).
Избранные режимы Q&P обработки были повторены на образцах квадратного сечения размерами 10 x 10 мм и длиной 55 мм с целью проведения последующих испытаний на ударную вязкость KCV при температурах 0 °С и –60 °С.
Таблица 1
Химический состав исследуемой стали
C |
Mn |
Si |
P |
S |
Cr |
Ni |
Cu |
Mo |
0,14 |
0,52 |
0,28 |
0,012 |
0,002 |
12,45 |
2,26 |
0,15 |
0,10 |
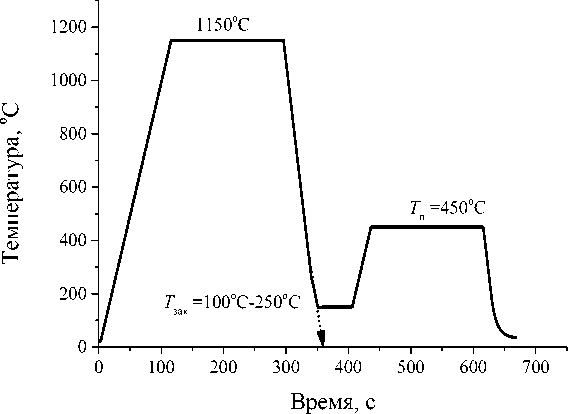
Результаты и их обсуждение
Перегибы, наблюдаемые на дилатограммах, указывают на то, что образование аустенита при нагреве исследуемой стали происходит в две стадии (рис. 2). Первая стадия превращения начинается при температуре Ас1 = 640 °С и заканчивается при температуре 730 °С. Вторая стадия, сопровождаемая более сильным дилатометрическим эффектом, происходит в интервале температур 775–840 °С (Ас3). Подобное двухстадийное образование аустенита ранее обнаружено в супермартенситной коррозионностойкой стали Fe–0,02%C– 12,3%Cr–5,6%Ni–2%Mo [13]. Авторы [13] полагают, что обнаруженное явление обусловлено локальной неоднородностью распределе- ния никеля, сформировавшейся при нагреве в межкритический интервал. Вероятно, и в нашем случае на первой стадии превращения аустенит образуется из участков α-фазы, обогащенных никелем, тогда как на второй стадии происходит образование аустенита из участков, обедненных этим элементом.
На рис. 3 толстыми линиями (кривая 1) представлены участки дилатограммы образца, охлажденного после аустенитизации до комнатной температуры. Единственный перегиб на кривых охлаждения при 270 °С отвечает температуре М н начала мартенситного превращения. На рис. 3 (тонкие линии) приведены участки дилатограмм образцов, закаленных до разных температур Т з в интервале
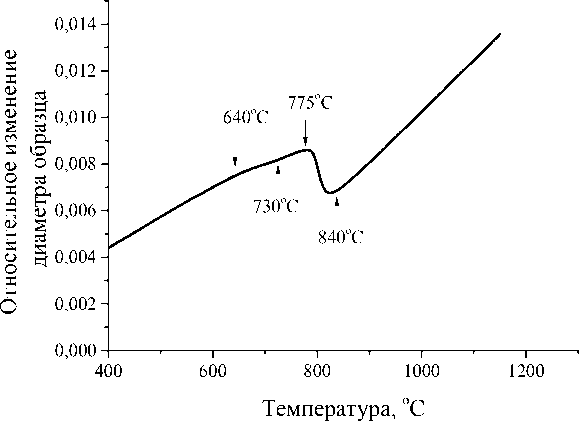
Рис. 2. Фрагмент дилатограммы, отвечающий стадии нагрева до температуры аустенитизации
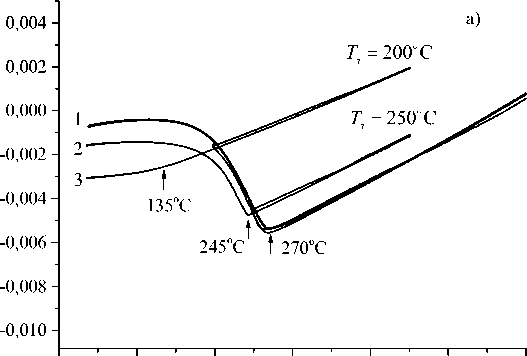
0 100 200 300 400 500 600
Температура, оС
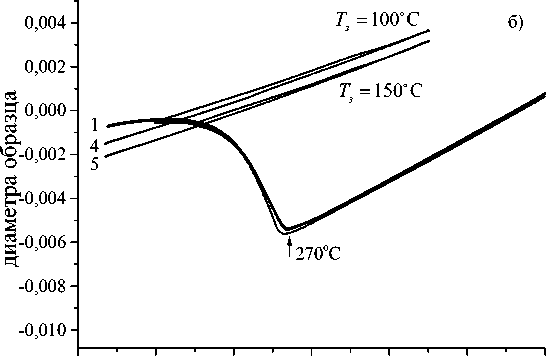
0 100 200 300 400 500 600
Температура, оС
Рис. 3. Фрагменты дилатограмм, отвечающие стадии закалки, последующему отжигу при 450 °С и охлаждению до комнатной температуры
При закалке до температуры 250 °С (кривая 2 на рис. 3а) лишь небольшая часть аустенита превращается в мартенсит. Соответственно невелико и обогащение углеродом не-превращенного аустенита в процессе выдержки при 450 °С. При последующем охлаждении сохранившийся аустенит вновь испытывает мартенситное превращение, хотя температура его начала падает с 270 до 245 °С.
С понижением температуры закалки до 200 °С (кривая 3 на рис. 3а) полнота мартенситного превращения возрастает. Степень обогащения углеродом непревращенного аус- тенита в процессе отжига при 450 °С также увеличивается. Однако и в этом режиме обработки полной стабилизации оставшегося аустенита до комнатной температуры не происходит: ниже 135 °С образуется небольшое количество «свежего» мартенсита.
При понижении температуры закалки до температур 150 и 100 °С количество образовавшегося мартенсита еще более возрастает (кривые 4 и 5 на рис. 3б). Во время выдержки при 450 °С углерод настолько сильно обогащает прослойки сохранившегося аустенита, что он оказывается стабильным при последующем охлаждении до комнатной температуры, о чем свидетельствует отсутствие перегибов на соответствующих участках дилато-грамм.
На рис. 4 представлены зависимости относительного изменения диаметра образцов от времени на этапе обработки, следующем за закалкой образцов до разных температур Т з в интервале мартенситного превращения. Изотермическая выдержка в течение 60 с после окончания закалки при температурах 150 °С и выше (область I) сопровождается слабым уменьшением объема, вероятно, обусловленным выделением малой порции е -карбида или карбидов М 3 С. В процессе 180-секундного стабилизирующего отжига при 450 °С (область II) значимых объемных изменений, и, соответственно, дополнительного карбидооб-разования, не наблюдается.
В отсутствие значительного выделения карбидов можно полагать, что в процессе перераспределения весь углерод из мартенсита переходит в аустенит [2]. В этом случае концентрация углерода в аустените после перераспределения углерода ( С ') равна отношению концентрации углерода в стали ( С )к доле непревращенного аустенита ( f , ):
С
C ‘ = у . (1) f у
Долю аустенита, не превращенного при закалке до температуры T з , оценим по уравнению Койстинена – Марбургера [14]:
f г= exp [ - k ( M н - Т 3 ) ] , (2) где в качестве параметра k примем значение 0,0151 К–1, полученное в [12] для стали мартенситного класса AISI 420 с 13 % хрома.
Для оценки термической стабильности аустенита требуется знать зависимость температуры М н от концентрации углерода. В работе [10] для сталей с 12,5 % хрома получено следующее выражение
M н( ° С) = 379 - 510 ■ C (вес. %).
Дополнительное присутствие в исследуемой стали 2 % никеля понижает температуру М н , но не изменяет зависимость температуры начала мартенситного превращения от содержания углерода. Поэтому модифицируем приведенное выражение так, чтобы при исходной концентрации углерода C = 0,14% температура М н оказалась равной наблюдаемой экспериментально величине 270 °С:
M н( ° С) = 341 - 510 ■ C . (3)
Используя выражения (1)–(3), получим оценки доли f Y непревращенного аустенита после закалки до температуры Т з , концентрации C ' в нем углерода после перераспределения и температуры M н начала последующего мартенситного превращения (табл. 2).
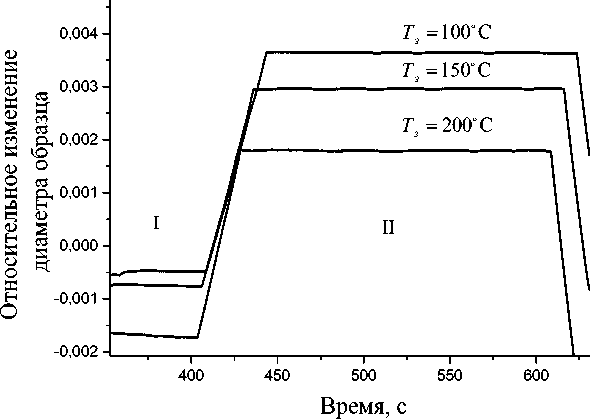
Рис. 4. Относительное изменение диаметра образов на этапе обработки, следующем за закалкой образцов до разных температур Т з
Таблица 2
Оценка доли непревращенного аустенита и его термической стабильности
Т з , ° C |
f Y |
C ', % |
M н , ° С |
( M ‘ ) , ° C н эксп |
250 |
0,74 |
0,19 |
245 |
245 |
200 |
0,35 |
0,40 |
136 |
135 |
150 |
0,16 |
0,86 |
–95 |
– |
100 |
0,08 |
1,82 |
– |
– |
Таблица 3
T ауст , °С |
T зак , °С |
T расп , °С |
KCV 0 , Дж/см2 |
KCV –60 , Дж/см2 |
1150 |
100 |
450 |
104 |
21 |
1150 |
150 |
450 |
120 |
58 |
1050 |
150 |
150 |
119 |
59 |
Рассчитанные температуры M н обогащенного углеродом аустенита после закалки до температур 250 и 200 °С совпали с их экспериментальными значениями, приведенными в последнем столбце табл. 2. Согласно выполненным оценкам, после закалки до 150 °С с последующим перераспределением углерода при 450 °С непревращенный аустенит оказывается термически стабильным до температуры –95 °С, а после закалки до 100 °С область термической стабильности распространяется вплоть до температуры 0 К.
Ударная вязкость KCV –60 образцов, закаленных до температуры 100 °С (21 Дж/см2) оказалась ниже требуемого значения (50 Дж/см2), что, вероятно, обусловлено малым количеством остаточного аустенита (около 8 %) и его высокой механической стабильностью, тогда как после закалки до более высокой температуры 150 °С, сохраняющей по нашим оценкам ~ 16 % остаточного аустенита, значения ударной вязкости (58 Дж/см2) превосходят значения, заложенные в требования к высокопрочным трубным сталям.
Понижение температуры аустенитизации с 1150 до 1050 °С в последнем режиме Q&P обработки ( Т з = 150 °С) не оказало отрицательного влияния на ударную вязкость, измеренную при температурах 0 °С и –60 °С (см. табл. 3).
Выводы
-
1. Моделирование режимов Q&P обработки коррозионностойкой стали AISI 414 (15Х13Н2) показало, что закалка до температур 200–250 °С с последующим отжигом при 450 °С не обеспечивает обогащение аустенита углеродом, достаточное для подавления мартенситного превращения при последующем охлаждении до комнатной температуры.
-
2. Понижение температуры закалки до 150 °С с последующим отжигом при 450 °С приводит к полной термической стабилизации
-
3. Режим Q&P обработки стали AISI 414, включающий закалку до 150 °С с последующим 3-минутным отжигом при температуре 450 °С перспективен для получения высокопрочного состояния с высоким уровнем низкотемпературной вязкости.
непревращенного аустенита вплоть до температур –60 °С, что обеспечивает за счет TRIP эффекта высокую низкотемпературную вязкость исследуемой стали (KCV –60 =59 Дж/см2), превосходящую значения, заложенные в требования к высокопрочным трубным сталям.
Список литературы Закалка с последующим обогащением углеродом непревращенного аустенита (Q&P обработка) мартенситной коррозионностойкой стали AISI 414
- Speer J.G., Matlock D.K., De Cooman B.C., Schroth J.G. Carbon Partitioning into Austenite after Martensite Transformation // Acta Materialia, 2003, vol. 51, pp. 2611-2622. DOI: 10.1016/S1359-6454(03)00059-4
- Speer J.G., Edmonds D.V., Rizzo F.C., Matlock D.K. Partitioning of Carbon from Supersaturated Plates of Ferrite, with Application to Steel Processing and Fundamentals of the Bainite Transformation // Current Opinion in Solid State Materials Science, 2004, vol. 8, pp. 219-237. DOI: 10.1016/j.cossms.2004.09.003
- Edmonds D.V., He K., Rizzo F.C., De Cooman B.C., Matlock D.K., Speer J.G. Quenching and Partitioning Martensite - A Novel Steel Heat Treatment // Materials Science and Engineering, A, 2006, vols. 438-440, pp. 25-34. DOI: 10.1016/j.msea.2006.02.133
- Clarke A.J., Speer J.G., Matlock D.K., Rizzo F.C., Edmonds D.V., Santofimia V.J. Influence of Carbon Partitioning Kinetics on Final Austenite Fraction during Quenching and Partitioning // Scripta Materialia, 2009, vol. 61, pp. 149-152. DOI: 10.1016/j.scriptamat.2009.03.02
- Speer J.G., De Moor E., Clarke A.J. Critical Assessment 7: Quenching and Partition // Materials Science and Technology, 2015, vol. 31, no. 1, pp. 3-9. DOI: 10.1179/1743284714Y.0000000628
- Wang L., Speer J.D. Quenching and Partitioning Steel Heat Treatment // Metallography, Microstructure, and Analysis, 2013, vol. 2, no. 4, pp. 268-281.
- DOI: 10.1007/s13632-013-0082-8
- Somani M.C., Porten D.A., Karjalainen L.P., Misra D.K. Evalution of DQ&P Processing Rout for the Development of Ultra-High Strength Tough Ductile Steels // International Journal of Metallurgical Engineering, 2013, vol. 2 (2), pp. 154-160.
- DOI: 10.5923/j.ijmee.20130202.07
- Jin X. Quenching and Partitioning Heat Treatment: High-Strength Low-Alloys // Encyclopedia of Iron, Steel, and Their Alloys, 2015, pp. 2761-2775.
- DOI: 10.1081/E-EISA-120051355
- Hong S.C., Ahn J.C., Nam S.Y., Kim S.J., Yang H.C., Speer J.D, Matlock D.K. Mechanical Properties of High-Si Plate Steel Produced by the Quenching and Partitioning Process // Metals and Materials Internatinal, 2007, vol. 13, no. 6, pp. 439-445.
- DOI: 10.3365/MMI.2007.12.439
- Tsuchiyama T., Tobata J., Tao T., Nakada N., Takaki S. Quenching and Partitioning Treatment of a Low-Carbon Martensitic Stainless Steel. Materials Science and Engineering, A, 2012, vol. 532, pp. 585-592.
- DOI: 10.1016/j.msea.2011.10.125
- Tobata J., Ngo-Huynh K.-L., Nakada N., Tsuchiyama T., Takaki S. Role of Silicon in Quenching and Partitioning Treatment of Low-Carbon Martensitic Stainless Steel // ISIJ International, 2012, vol. 52, no. 7, pp. 1377-1382. 10.2355 /isijinternational.52.1377
- DOI: 10.2355/isijinternational.52.1377
- Mola J., De Cooman B.C. Quenching and Partitioning (Q&P) Processing of Martensitic Stainless Steels // Metallurgical and Materials Transactions A, 2013, vol. 44A, pp. 946-967.
- DOI: 10.1007/s11661-012-1420-1
- Bojack A., Zhao L., Morris P.F., Sietsma J. Austenite Formation from Martensite in a 13Cr6Ni2Mo Supermartensitic Stainless Steel // Metallurgical and Materials Transactions A, 2016, vol. 47, no. 5, pp. 1996-2009.
- DOI: 10.1007/s11661-016-3404-z
- Koistinen D., Marburger R. A General Equation Prescribing the Extent of the Austenite-Martensite Transformation in Pure Iron-Carbon Alloys and Plain Carbon Steels // Acta Metallurgica, 1959, vol. 7, pp. 59-60.
- DOI: 10.1016/0001-6160(59)90170-1