Защита поверхности анода алюминиевого электролизёра от окисления
Автор: Гильдебрандт Э.М., Вершинина Е.П., Фризоргер В.К.
Журнал: Журнал Сибирского федерального университета. Серия: Техника и технологии @technologies-sfu
Статья в выпуске: 3 т.3, 2010 года.
Бесплатный доступ
Разработан материал и способ защиты поверхности анода от окисления углекислым газом. Выполнены термодинамические расчёты реакций взаимодействия предполагаемых материалов покрытий с СО2, HF и AlF3, проведён дифференциально-термический и рентгенофазовый анализ композиций. Сделан сравнительный микроскопический анализ поверхности угольных материалов.
Анод, расход углерода, реакция газификации, защитное покрытие
Короткий адрес: https://sciup.org/146114539
IDR: 146114539
Текст научной статьи Защита поверхности анода алюминиевого электролизёра от окисления
Угольный анод алюминиевого электролизера сформирован из анодной массы, состоящей из нефтяного кокса (70 – 72 %) и кокса, получающегося в результате коксования каменноугольного пека (30 – 28 %), играющего роль связующего материала.
Избыточный расход анода алюминиевого электролизёра получается в результате реакции углерода анода с кислородом воздуха и углекислым газом, являющимся одним из продуктов электролиза. Реакция газификации углерода активно протекает при температуре более 700 °С. Воздействию углекислого газа подвергается как часть поверхности анода между уровнем электролита и нижним краем анодного кожуха, так и поверхность, находящаяся в электролите.
Изучение «динамического» состава пылегазовой смеси [1] свидетельствует о том, что доминирующими в анодных газах являются монооксид углерода СО (в среднем 52 об.%) и диоксид углерода СО 2 (в среднем 39 об.%).
При селективном окислении матрицы связующего, обладающей большей реакционной способностью, частицы кокса-наполнителя отрываются от поверхности анода и попадают в электролит. Осыпавшиеся частицы углерода – составная часть «пены», удаление которой приводит к увеличению трудозатрат при электролизе. Связанная с протеканием этих процессов
величина избыточного расхода углерода составляет 150-200 кг С/т Аl при общем расходе около 520 кг С/т Аl.
Реакционная способность угольных материалов определяется несколькими основными факторами:
-
– наличием катализаторов или ингибиторов окисления в составе материала;
-
– доступом газа к реакционной поверхности анода.
Анализ публикаций с 1997 по 2006 гг. показал, что число исследований, в которых разрабатываются и предлагаются к использованию добавки к электродным массам, невелико. Несколько из них посвящено непосредственно анодам [2-4] и две работы [5, 6] – углеродной массе для подовых и бортовых блоков электролизёров.
Многочисленные работы по защитным покрытиям относятся, прежде всего, к катодным блокам [7-27]. Только в четырёх публикациях [4, 28-30] изложены способы защиты поверхности анода от окисления с использованием различных борсодержащих химических соединений. Предложен способ пропитки обожжённого анода раствором борной кислоты в вакууме для защиты от окисления под воздействием воздуха. Испытания этого метода проведены на трёх промышленных электролизёрах. Отмечено снижение окисления и более равномерный расход анодов.
Основная проблема, возникающая при внедрении борсодержащего защитного покрытия, состоит в переходе бора в электролит, а затем и в металл. Поэтому целью лабораторных исследований является изучение защитных свойств борсодержащих покрытий с добавками глинозема.
Экспериментальная часть
В качестве базового материала защитного покрытия поверхности анода выбраны оксид бора В2О3 и ортоборная кислота Н3ВО3 с добавками глинозёма.
Диаграмма состояния системы B 2 O 3 – Al 2 O 3 приведена на рис. 1. При температурах 470 – 1035 °С возможно образование химического соединения B2O3 · 2Al2O3.
Две реакции взаимодействия диоксида углерода с коксом анода и оксида бора с фторидом водорода приведены ниже:
C ( т ) + CO2 ( г ) = 2CO ( г ) .
B2O3 ( ж ) + 6HF ( г ) = 2BF3 ( г ) + 3H2O ( г ) .
Для термодинамических расчётов изменения энергии Гиббса ( ∆ G0 T ) этих реакций использованы известные термодинамические свойства веществ [31-34]. Выбранный температурный диапазон 700 – 950 °С соответствует температуре поверхности анода между электролитом и анодным кожухом. Расчёты показали, что при увеличении температуры в названом диапазоне энергия Гиббса первой реакции уменьшается до -50 кДж, а второй – увеличивается от -38 кДж до -13 кДж.
Можно отметить, что при рабочих температурах поверхности анода возможно протекание этих реакций. Одна из них может привести к образованию нового для электролиза токсичного реагента BF 3 , предельно допустимая концентрация которого составляет 1 мг/м3 [35]. Расчёты
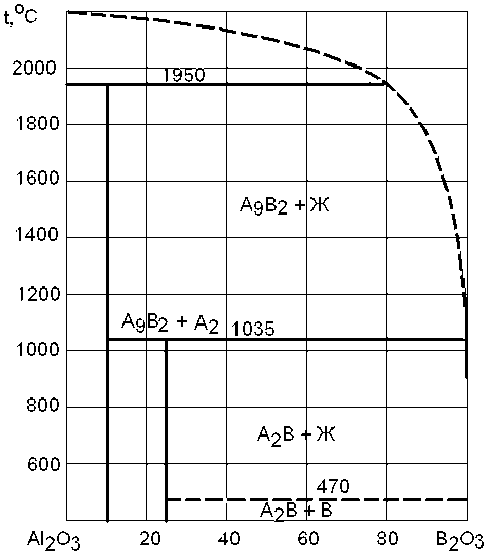
Рис. 1. Диаграмма состояния системы Al2O3(A) – B2O3(B)
отражают «нормализованную» ситуацию, когда исходное давление газообразных реагентов принято равным атмосферному.
Проведены исследования свойств композиции, в которой содержание глинозёма составило примерно 10 мас. %, а остальное – борная кислота. Дифференциально-термический (ДТА) и термогравиметрический анализ (ТГ) проведены на дериватографе Q-1500 D в режиме нагрева до 1000 °С образцов со скоростью 10 °С/мин.
Результаты исследований свойств борной кислоты показывают, что в соответствии с известными представлениями:
-
– убыль массы при переходе от борной кислоты к оксиду бора составляет 40 %;
-
– этот переход происходит в интервале температур 107 – 275 °С и описывается следующей схемой:
H 3 BO 3 107 °С > HBO 2 275 °С > B 2 O 3.
Далее происходит размягчение с образованием жидкой фазы.
На кривой ДТА системы на основе борной кислоты с добавкой 10 % (масс.) Al2O3 выявляется несколько эндотермических и экзотермических эффектов. Экзотермический эффект при температуре 763 °С может быть связан с температурой ликвидуса системы В2О3 – Аl2O3. Два эндотермических эффекта – 641 и 615 °С, возможно, связаны с процессом синтеза химического соединения 2Аl2O3 ⋅ В2О3.
Для проверки этого предположения проведён рентгенофазовый анализ на дифрактометре Shimadzu XRD-6000. Проба того же состава предварительно нагревалась до температуры 950 °С, расплав выдерживали в течение трёх часов, а затем охлаждали. Рентгенограмма об- – 274 –
1 000
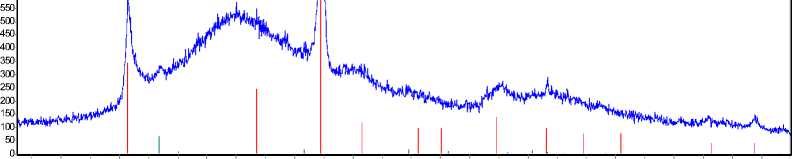
8 10 12 14 16 18 20 22 24 26 28 30 32 34 36 38 40 42 44 46 48 50 52 54 56 58
Рис. 2. Рентгенограмма образца
разца приведена на рис. 2. В образце с исходным содержанием оксида алюминия 10 мас.% находится 94 % В 2 О 3 , из которых половина представлена кристаллической формой, а половина – аморфной. Содержание химического соединения 2Аl2O3 ⋅ В2О3 равно 6 %.
Полученные результаты показывают, что использование смеси борной кислоты и глинозёма приводит к образованию покрытия, в котором в качестве связующего выступает жидкий раствор на основе оксида бора, а в качестве твёрдого наполнителя – частицы химического соединения 2Аl2O3 ⋅ В2О3.
Для проведения лабораторных испытаний защитных свойств борсодержащих химических соединений на угольных материалах был выбран шликерный метод. Он заключается в нанесении покрытия на поверхность образца в виде шликера – концентрированной суспензии или пасты. В состав исходной твёрдой фазы входили порошки борной кислоты (или оксида бора) и оксида алюминия с размером частиц от 1 до 200 мкм. В качестве жидкой составляющей шликера использовали воду. Особенность такого покрытия – жидкое состояние при нанесении покрытия при комнатных температурах, твёрдое состояние после сушки и снова образование жидкого слоя при температурах выше 300 °С.
Для исследований поведения защитных материалов в токе углекислого газа и в среде, содержащей фториды, создана лабораторная установка, схема которой приведена на рис. 3. Образец углеродного материала с покрытием (1) помещали на кварцевую подставку (2), которая одновременно служила для сбора осыпающихся в ходе окисления твёрдых частиц. Подставку с образцом устанавливали в кварцевой реторте (3) в силитовую печь сопротивления (4). Реторту герметизировали пробками (5), которые имели вводы для термопары (6), подачи и вывода газообразного реагента (7). Углекислый газ подавали от баллона через расходомер (8).
В опытах, моделирующих фторидную газовую среду, под образцом устанавливали тигель с фторидом алюминия (9). При температурах эксперимента AlF 3 переходил в газовую фазу, и масса его в тигле заметно уменьшалась. Взаимодействие фторида алюминия с водяным паром, содержащимся в углекислом газе, обеспечивало образование фторида водорода.
Образцы имели форму цилиндра высотой 22 мм и диаметром 55 мм, площадью (85 ± 5) см2. Масса образцов составляла 80-90 г. Перед опытом каждый образец взвешивали, после взвешивания наносили покрытие из защитной пасты толщиной 2-3 мм и направляли на сушку. После сушки образцы снова взвешивали и на подставке устанавливали в реторту печи.
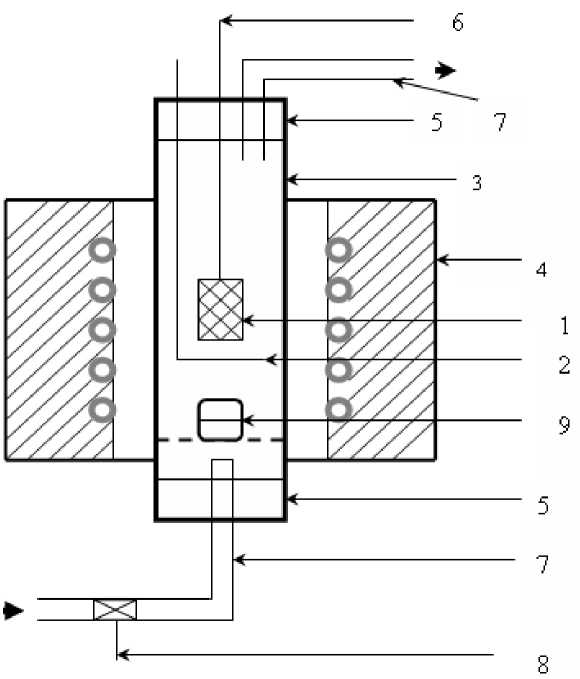
Рис. 3. Схема лабораторной установки: 1 – образец материала; 2 – кварцевая подставка; 3 – кварцевая реторта; 4 - печь сопротивления; 5 - пробка; 6 - ввод для термопары; 7 - подача и вывод СО2; 8 -расходомер; 9 – тигель
После герметизации реторту продували аргоном, включали печь и температуру поднимали до рабочего значения 950 °С. После достижения заданной температуры подавали углекислый газ, продувку вели в течение трёх часов с расходом газа 50 дм3/мин. Затем печь отключали, а реторту заполняли аргоном. После охлаждения доставали подставку с образцом, собирали и взвешивали осыпавшиеся твёрдые частицы, а затем определяли массу образца после опыта. Толщина слоя защитного покрытия после обжига составляла 0,1-0,4 мм.
Разрушаемость (Р) и осыпаемость (Ос) рассчитывали по известной методике:
P = ^m; Oc = -m, t ж S t ж S где Р - разрушаемость образца, мг/см2 ч; Am - убыль массы образца; t - время подачи газообразного реагента; S – площадь поверхности образца; m – масса осыпавшихся частиц материала.
Из этих экспериментальных величин можно рассчитать величину окисляемости (Ок):
Ок = Р - Ос , определяющую расход углерода по реакции газификации.
Результаты исследований и их обсуждение
Для приготовления защитного покрытия на основе оксида бора борную кислоту переплавляли, расплав В2О3 выливали в изложницу, охлаждали и после кристаллизации дробили. Полученный порошок использовали для создания пасты и защитных покрытий на образцах графита.
После обработки в газовой среде по описанной выше методике покрытие растворяли в воде. Графитовый образец сушили в сушильном шкафу, измеряя убыль массы. По достижении постоянного значения образец взвешивали. Разность масс до опыта и после него использовали для расчёта разрушаемости.
Результаты исследования поведения материала с различным содержанием глинозёма в токе СО2 и в смеси СО2 + AlF3 приведены в табл. 1.
Полученные результаты показали, что использование композиции оксид бора – глинозём обеспечивает создание защитного покрытия, однако при увеличении содержания Al2O3 более чем на 50% эффективность защиты снижается.
Защитное покрытие на графитовом образце, изготовленное из смеси оксида бора и глинозёма, после обработки в печи при температуре 950 °С в среде углекислого газа в смеси с фторидами соскабливали и проводили рентгенофазовый анализ этой пробы. Сравнение с рентгенограммой образца покрытия до взаимодействия с газовой фазой (рис. 4) говорит о том, что сохраняются основные фазы, представленные продуктами взаимодействия между исходными веществами покрытия – сложным оксидом 2Аl 2 O 3 ⋅ В 2 О 3 и оксидом бора.
Результаты определения разрушаемости и осыпаемости угольных образцов, отобранных непосредственно из анода, без покрытия и с покрытием в различных газовых средах представлены в табл. 2. Для образцов, имеющих защитное покрытие, отсутствует осыпаемость, поэтому для них приведена только разрушаемость.
Результаты, приведённые в табл. 2, для наглядности представлены в виде гистограммы на рис. 4. Сравнение результатов этих трёх серий опытов показывает, что Н 3 ВО 3 обладает хорошими защитными свойствами. Её использование позволило полностью исключить осыпаемость и резко снизить окисляемость угольного материала. Борная кислота, переходя в В 2 О 3 при низких температурах, обеспечивает образование жидкого покрытия, хорошо смачивающего поверхность образца. Получается тонкая плёнка, обладающая хорошими адгезионными свойствами.
Таблица 1. Разрушаемость (Р) образцов с покрытием из смеси В 2 О 3 и Al 2 O 3
Газовая среда СО 2 |
|||||||
№ образца |
11 |
12 |
13 |
14 |
|||
Покрытие |
Без покрытия |
50%В 2 О 3 +50% Al 2 O 3 |
25%В 2 О 3 +75% Al 2 O 3 |
9%В 2 О 3 +91% Al 2 O 3 |
|||
Свойство |
Р |
Р |
Р |
Р |
|||
Значение, мг/см2ч |
2,63 |
0,63 |
1,48 |
2,16 |
|||
Газовая среда СО 2 + AlF 3 |
|||||||
№ образца |
15 |
16 |
17 |
18 |
19 |
||
Покрытие |
Без покрытия |
14% Al 2 O 3 |
25% Al 2 O 3 |
35% Al 2 O 3 |
50% Al 2 O 3 |
||
Свойство |
Р |
Р |
Р |
Р |
Р |
||
Значение, мг/см2ч |
4,06 |
0,14 |
0,15 |
0,77 |
2,44 |
Таблица 2. Разрушаемость (Р) и осыпаемость (Ос) образцов анода
Без покрытия |
||||||||||||
№ образца |
1 |
2 |
3 |
|||||||||
Среда |
СО 2 |
СО 2 + AlF 3 |
СО 2 + AlF 3 |
|||||||||
Свойство |
Р |
Ос |
Р |
Ос |
Р |
Ос |
||||||
Значение, мг/см2ч |
32,0 |
3,5 |
48,1 |
13,2 |
41,5 |
9,3 |
||||||
Покрытие из Н3ВО3 |
||||||||||||
№ образца |
4 |
5 |
||||||||||
Среда |
СО 2 |
СО 2 + AlF 3 |
||||||||||
Свойство |
Р |
Р |
||||||||||
Значение, мг/см2ч |
9,0 |
12,0 |
||||||||||
Покрытие из смеси Н 3 ВО 3 и Al 2 O 3 |
||||||||||||
№ образца |
6 |
7 |
8 |
9 |
10 |
|||||||
Покрытие |
91% Н 3 ВО 3 + 9% Al 2 O 3 |
83% Н 3 ВО 3 + 17% Al 2 O 3 |
||||||||||
Среда |
СО 2 |
СО 2 + AlF 3 |
СО 2 |
СО 2 |
СО 2 + AlF 3 |
|||||||
Свойство |
Р |
Р |
Р |
Р |
Р |
|||||||
Значение, мг/см2 час |
12,5 |
17,0 |
18,1 |
12,3 |
18,9 |
Таблица 3. Результаты микроскопического анализа
№ изображения |
Образец 1 |
Образец 2 |
Образец 3 |
1 |
95,7 |
36,8 |
85,5 |
2 |
94,2 |
33,9 |
88,7 |
3 |
86,4 |
33,2 |
89,4 |
4 |
92,2 |
44,5 |
88,1 |
5 |
90,1 |
32,6 |
89,3 |
6 |
94,8 |
38,9 |
85,6 |
7 |
89,7 |
31,1 |
90,7 |
8 |
81,8 |
23,9 |
88,1 |
Средняя площадь коксовой части, % |
90,6 |
34,4 |
88,2 |
Средняя площадь пор, % |
9,4 |
65,6 |
11,8 |
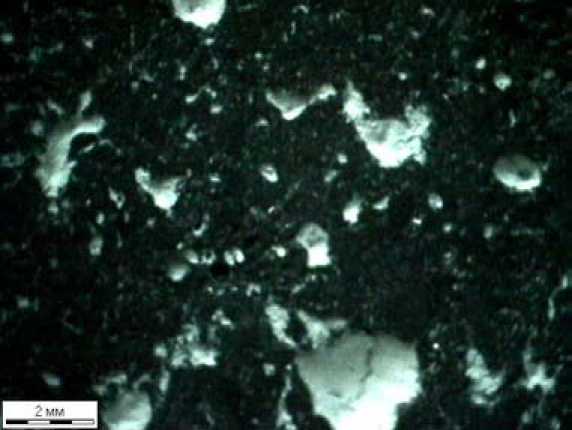
Рис. 5. Микроструктура образца 3
Защитное покрытие из борной кислоты обеспечивает снижение разрушаемости примерно в четыре раза, при этом осыпаемость исключается полностью. Результаты последней серии опытов показали возможность использования в качестве защитного покрытия композиционого материала из смеси борсодержащего вещества (борной кислоты) и глинозёма.
Целью микроскопического анализа являлось определение площади пор, выходящих на поверхность образца после его обработки в токе СО2. Для этого образец покрывали наполнителем белого цвета, затем наполнитель сошлифовывали. На такой поверхности поры представлены «белыми» участками, а твёрдая коксовая часть – «чёрными». Отношение площадей «черных» и «белых» участков позволило определить пористость, выходящую на поверхность образца, а значит оценить его взаимодействие с углекислым газом. Для проведения микроскопического анализа выбраны три образца из коксовой части анода: исходный материал (1), образец без покрытия, обработанный в токе углекислого газа (2), и образец с защитным покрытием, обработанный в токе СО 2 (3).
Микрофотосъёмку производили на лабораторном микроскопе МБС-10. Для оцифровки изображения применяли программу Image Scope-S, площадь «черных» и «белых» областей измеряли в автоматическом режиме. На каждом образце анализировали 8 изображений. В результате измерений получена относительная площадь черных (коксовой части) и белых областей (пор) в % к общей площади.
В табл. 3 приведены результаты измерений, а на фотографии (рис. 5) - одно из изображений для образца с защитным покрытием, обработанного в токе СО2.
Из табл. 3 видно, что относительная площадь пор, выходящих на поверхность, практически одинакова для образцов 1 и 3. Результаты для образца без покрытия, обработанного в токе углекислого газа, показывают существенное (примерно в 6 раз) увеличение пористости.
Заключение
Исследованы защитные свойства материалов защитных покрытий на основе борсодержащих химических соединений с добавками глинозёма. Показано, что как сами исходные вещества – борная кислота и оксид бора, так и их смеси с глинозёмом являются эффективной защитой от окисления угольных материалов в среде углекислого газа.
Рентгенофазовым анализом материала покрытия показано, что после его взаимодействия с агрессивной газовой средой не образуются новые химические соединения.
Сравнительный микроскопический анализ подтвердил эффективность защитных свойств покрытий из борсодержащих материалов.
Статья опубликована при поддержке Программы развития Сибирского федерального университета.