Жаростойкий бетон для электроизоляции блюмсов алюминиевых электролизеров
Автор: Шахрай С.Г., Архипов Г.В., Поляков П.В., Михалев Ю.Г., Иванова А.М., Калиновская Т.Г., Шайдулин Е.Р., Авдеев Ю.О.
Журнал: Журнал Сибирского федерального университета. Серия: Техника и технологии @technologies-sfu
Статья в выпуске: 6 т.9, 2016 года.
Бесплатный доступ
При производстве алюминия снизить удельный расход электроэнергии и повысить выход по току возможно за счет уменьшения расстояния между анодом и катодом МПР с одновременным снижением горизонтальных токов в расплавленном алюминии. Снижение горизонтальных токов может быть достигнуто размещением электроизоляции между катодным угольным блоком и блюмсом на участке «граница настыли - проекция периферии анода на подину». В качестве электроизоляционного материала наиболее технологично и экономично использовать жаростойкий бетон, имеющий хорошую адгезию к стали и химическую стойкость к воздействию криолит-глиноземного расплава, достаточно малую прочность на сжатие, что исключит разрушение катодного угольного блока в случае увеличения объема электроизоляционной вставки под воздействием электролита. В статье приводятся результаты исследований свойств некоторых жаростойких бетонов с целью выбора оптимального состава материала для электроизоляции блюмсов алюминиевого электролизера.
Алюминиевый электролизер, жаростойкий бетон, горизонтальные токи, прочность, модуль упругости, электрическое сопротивление, энергоэффективность
Короткий адрес: https://sciup.org/146115885
IDR: 146115885 | DOI: 10.17516/1999-494X-2016-9-6-918-927
Текст научной статьи Жаростойкий бетон для электроизоляции блюмсов алюминиевых электролизеров
Рис. 1. Схема электроизоляции блюмса бетоном (поперечный разрез): 1 – подовый блок; 2 – бетонная вкладка; 3 – блюмс материале с низкой прочностью и жесткостью обусловлена тем, что в процессе эксплуатации под воздействием электролита происходит объемное расширение бетона и существует риск образования трещин в угольном катодном блоке. Композиции для электроизоляционных вставок содержат помимо тонкомолотого наполнителя, связующего и отвердителя еще и заполнитель-разрыхлитель, или так называемый вспучиватель, снижающий прочность на сжатие.
В настоящее время для электроизоляции блюмсов зачастую используется бетон, включающий заполнитель шамотный ЗБШ кл. 4 в качестве наполнителя; вермикулит вспученный средний (Марка 150) в качестве материала, снижающего прочность на сжатие, жидкое стекло с плотностью 1,30÷1,36 г/см3 в качестве связующего и кремнефторид натрия – как отвердитель для ускорения схватывания бетона. Этот состав не обладает достаточной химической стойкостью, поскольку в процессе эксплуатации электролизера оксиды кремния и алюминия, входящие в состав жаростойкого бетона, а также пары натрия и тетрафторалюмината натрия, проникающие сквозь тело бетона к блюмсу, контактируют с оксидами железа, покрывающими блюмс, и с самим железом. В результате на границе бетон – блюмс и в теле бетона могут об- разовываться интерметаллиды, например, по следующим реакциям:
1,5Fe 2 O 3 + SiO 2 + 13Na(г) + 4,333NaAlF 4 (г) =
= 17,333NaF + 2,167Al2O3 + Fe3Si,(1)
Fe 2 O 3 + 2SiO 2 + 14Na(г) + 4,667NaAlF 4 (г) =
= 18,667NaF + 2,333Al2O3 + 2FeSi,(2)
4,5Fe + 1,5SiO2 + 6Na(г) + 2NaAlF4(г) = 8NaF + Al2O3 + 1,5Fe3Si,(3)
1,5Fe + 1,5SiO2 + 6Na(г) + 2NaAlF4(г) = 8NaF + Al2O3 + 1,5FeSi,(4)
изменения стандартной энергии Гиббса ∆Gо в результате протекания которых при 900 °С – рабочей температуре бетона, равны соответственно, кДж: – 2108,47; – 1978,544; – 708,466; – 667,273.
Такие интерметаллиды, обладающие металлической проводимостью и снижающие электроизоляционные свойства бетонной вставки, действительно обнаруживаются в составе бетона, используемого для электроизоляции блюмсов, в электролизерах, проработавших достаточно долгое время (25 месяцев) [3]. По-видимому, могут проходить и другие реакции, при-– 920 – водящие к росту электропроводности, например, с образованием интерметаллидов железа с алюминием, таких как Fe3Al, FeAl, Fe2Al3, FeAl2, FeAl3, Fe2Al5 [4].
Цель работы – рекомендовать бетон, обладающий большой химической стойкостью и не уступающий по другим показателям бетону, используемому в настоящее время для электроизоляции блюмсов.
Обоснование состава бетона
Для снижения риска образования интерметаллидов целесообразным представляется использование магнезитового бетона, в котором наполнителем является магнезитовый порошок с высоким содержанием MgO (около 80 %), а отвердителем – нефелиновый шлам. Оксид магния устойчив к действию пара натрия. Изменение стандартной энергии Гиббса реакции
MgO + 2Na(r) = Na 2 O + Mg (5)
при 900 °С равно 216,024 кДж. Но даже если магний будет образовываться в результате более сложных реакций, например,
3MgO + 6Na(g) + 2NaAlF 4 (g) = 8NaF + Al 2 O 3 + 3Mg, ( 6 )
∆Gо которой при 900 °С равно 185,801 кДж, опасаться образования интерметаллидов с металлической проводимостью не следует, поскольку железо практически не взаимодействует с магнием [4]. Магний же, будучи сильным восстановителем, не будет находиться в свободном виде.
Замена кремнефторида натрия на нефелиновый шлам снижает количество вносимого в футеровку электролизера натрия при неизменном количестве вносимого кремния. При этом взаимодействие оксидов магния и кальция, содержащихся в нефелиновом шламе, с паром натрия при 900 °С по реакции
CaO + 2MgO + 6Na(g) = 3Na 2 O + Mg 2 Ca (7)
термодинамически маловероятно (∆Gо = 656,224 кДж) и не приводит к образованию интерме-таллида Mg2Ca [4], который является сильным восстановителем.
В новом составе в качестве связующего можно использовать жидкое стекло, а в качестве материала, снижающего прочность, – вспученный вермикулит.
Подготовка и методика испытаний образцов бетона
Были подготовлены и испытаны четыре состава бетона (составы 1–4), приведенные в табл. 1, свойства которых сравнивали со свойствами образцов бетона с шамотным наполнителем (состав 0), используемого в настоящее время алюминиевыми заводами.
Подготовка образцов бетона осуществлялась предварительным смешиванием сухих компонентов в течение 8–10 мин с помощью мешалки для сухих смесей, приводимой в действие электродрелью, до получения однородной массы. После добавления связующего (жидкого стекла) перемешивание велось в течение 10–15 мин до получения гомогенной смеси, которая заливалась в цилиндрические формы диаметром от 40 до 50 мм и высотой от 50 до 80 мм. Предварительная сушка и твердение бетона происходили при комнатной температуре в те- – 921 –
Таблица 1. Составы образцов испытуемого электроизоляционного бетона (% об.)
Компоненты |
Содержание компонентов в образцах, % об. |
||||
№ 0 |
№ 1 |
№ 2 |
№ 3 |
№ 4 |
|
Порошок магнезитовый (периклазовый) кл. 4 ППЭ-88 ГОСТ 24862-81 |
- |
48 |
34 |
43 |
32 |
Заполнитель шамотный ЗБШ кл. 4, ГОСТ23037-99 |
34 |
– |
– |
– |
11 |
Вермикулит вспученный средний, Марка 150, ГОСТ12865-67 |
34 |
20 |
34 |
25 |
25 |
Жидкое стекло, плотность 1,30÷1,36 г/см3, ГОСТ 13078-81 |
27 |
27 |
27 |
27 |
27 |
Кремнефтористый натрий, ТУ 113-08-587-86 |
5 |
5 |
5 |
– |
– |
Шлам нефелиновый , ТУ 1789-067-00196368-2000 |
– |
– |
– |
5 |
5 |
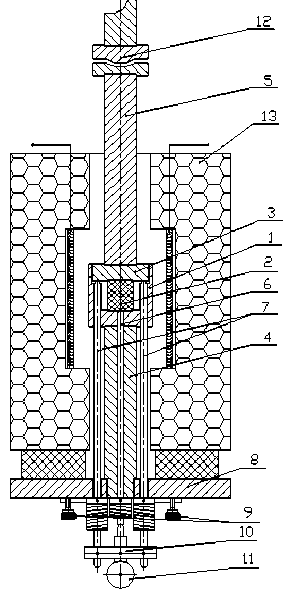
Рис. 2. Устройство для определения прочности и модуля упругости: 1 – стакан; 2 – образец; 3 – опорная площадка; 4 – нижняя опора; 5 – нагрузочный стержень; 6 – опорный стержень; 7 – измерительные стержни; 8 – опорная плита; 9 – опорные пружины с винтами-фиксаторами; 10 – держатель датчика; 11 – датчик; 12 – цилиндр с выступом; 13 – печь чение 48 ч. Затем образцы извлекались из форм и при температуре (120±10) °С подвергались окончательной сушке в электродуговой печи в течение 3 ч.
В настоящей работе выбор приемлемого состава бетона определялся механическими характеристиками (модулем упругости и пределом прочности на сжатие) и электроизоляционной способностью. Последняя оценивалась после пропитки образцов при 970 °С в течение 48 ч электролитом с криолитовым отношением (КО) 2,7 с добавкой 3 мас.% глинозема.
Определение модуля упругости и предела прочности на сжатие производили на специальной установке ИК-4 [5] в устройстве, представленном на рис. 2. Оснастка для испытания изготовлена из стали марки 12Х18Н10Т.
Испытания образцов производили в интервале температур от 20 до 950 °С. Относительную линейную деформацию сжатия ε , %, определяли по формуле
£ = ^•100 = (п — п0) "ЮО, (8)
о о где Ah - абсолютное изменение высоты образца, мм; h0 - начальная высота образца, мм; п0 - показание датчика перемещения при отсутствии нагрузки; n – показание датчика перемещения при сжатии; М – коэффициент градуировки (калибровки) датчиков.
Напряжение сжатия σ, МПа, определяли по формуле
F
° = А , где F - усилие сжатия образца, Н; А - площадь поперечного сечения образца, мм2.
Модуль упругости бетона Е, МПа, определяли по тангенсу угла наклона прямолинейного участка диаграммы сжатия образца к оси деформаций д^-
^ = tya = -.
Предел прочности на сжатие вычисляли по формуле
Fmax »„ - л, ( где Fmax – разрушающая нагрузка, Н.
Показателем электроизоляционной способности бетонов служит их удельное сопротивление. Однако измерить этот параметр после пропитки образцов бетона электролитом не удалось вследствие их разрушения и невозможности определить падение напряжения на фрагментах. Поэтому оценка электроизоляционной способности фрагментов образцов характеризовалась косвенно по силе тока, проходящего при данном напряжении через фрагменты при включении их в цепь постоянного тока.
Результаты и обсуждение
Результаты механических испытаний на сжатие образцов бетонов составов 1-4 и контрольного бетона состава 0 при различных температурах приведены на рис. 3 и 4.
Бетон состава 1 во всем интервале температур имеет более высокие, чем контрольный бетон, значения предела прочности (рис. 3). Прочность бетона состава 2 в интервале температур 200–550 °С ниже, а при 600–700 °С несколько выше, чем у бетона состава 0. Бетон состава 4 в интервале 20–500 °С близок по прочности к бетону состава 0, однако при температурах 500-550 °С его кривая предела прочности имеет резкий скачок, значительно превышая прочность бетона состава 0. Результаты испытаний образцов бетона состава 3 показывают, что его предел прочности имеет более низкие значения, чем у контрольного бетона, практически во всем интервале температур.
Измерения модуля упругости, отражающего сопротивление упругой деформации бетонов при различных температурах, показывает, что жесткость бетонов состава 1 и 2 во всем интер- – 923 –
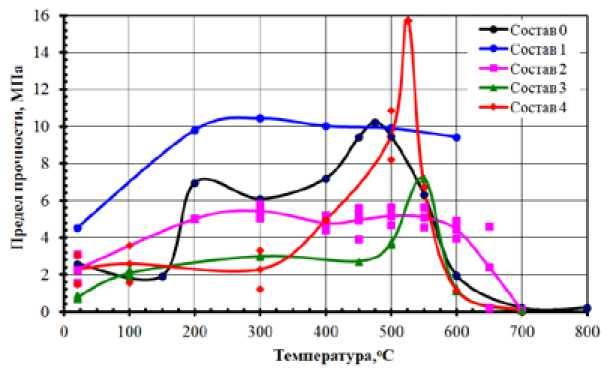
Рис. 3. Зависимость предела прочности на сжатие бетонов от температуры
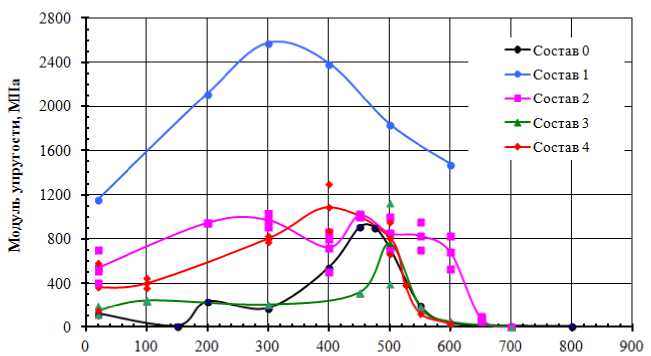
Темпер а тур а,°С
Рис. 4. Зависимость модуля упругости бетонов от температуры вале температур превышает аналогичную характеристику бетона состава 0 (рис. 4). Модуль упругости бетона состава 4 в интервале температур 20–500 °С несколько выше, чем у бетона состава 0, и только при более высоких температурах показатели жесткости экспериментального и контрольного бетонов близки по значениям. Бетон состава 3 практически во всем интервале температур значительно превосходит остальные экспериментальные бетоны по требуемым показателям жесткости (кривая зависимости модуля упругости лежит ниже, чем у бетонов 1, 2 и 4) . В сравнении с контрольным бетоном при температурах 20–300 и 500–950 °С он имеет близкие, а при 300–500 °С более низкие значения модуля упругости, чем у бетона состава 0.
Высокая прочность бетонов составов 0, 1 и 2, содержащих в качестве отвердителя кремнефторид натрия, вероятно, обусловлена тем, что их твердение происходит в результате образования коллоидного клея Si(OH)4 по реакции
Na 2 SiF 6 + 2 (Na 2 О∙2SiO 2 ) + 10Н 2 О = 5Si(ОН) 4 + 6NaF (12)
в отличие от бетонов составов 3 и 4, не содержаших кремнефторида натрия.
Образующийся Si(ОН)4 приобретает максимальную прочность после высушивания и перекристаллизации в SiО 2 с выделением воды. При этом кремнефтористый натрий является сильнодействующим плавнем, понижающим огнеупорные свойства бетонов на жидком стекле при рабочих температурах электролизера [6].
Сравнительный анализ механических характеристик бетонов позволяет сделать вывод, что бетоны составов 1, 2 и 4 как имеющие достаточно высокую жесткость и, как указывалось ранее, создающие опасность повреждения блоков нежелательно использовать для заделки блюмсов. Это связано с тем, что при термическом расширении материалов подины в период прогрева ванны до рабочей температуры и высокого сопротивления сжатию бетонной вкладки существует риск увеличения нагрузки на угольный катодный блок и образования в нем трещин. По результатам механических испытаний наиболее приемлем бетон состава 3, который по показателям жесткости и прочности соответствует требованиям, предъявляемым к бетонам, используемым для электроизоляции блюмсов.
В дальнейших исследованиях бетоны составов 3 и 0 после их пропитки электролитом в одинаковых условиях сравнивали по электроизоляционной способности. Электроизоляционные свойства образца 3 оказались лучше, чем у образца 0, так как сила тока, проходящего через фрагменты образца 3, была практически равна нулю (меньше предела чувствительности амперметра – 0,001А) во всем диапазоне температур от 25 до 900 °С. Иная картина наблюдалась при испытании фрагментов бетона состава 0. При подъеме температуры от 25 до 500 °С сила тока, проходящего через фрагмент, была меньше предела чувствительности амперметра, в интервале температур 500–900 °С зафиксирована величина тока 0,05 А, при температуре выше 900 °С – 0,1 А. Таким образом, бетон состава 0 после пропитки при температуре >900 °С в течение 48 ч проводит ток, следовательно, увеличение времени пропитки в условиях действующего электролизера сделает материал еще более электропроводным. Большая электропроводность бетона состава 0 обусловлена, по-видимому, электропроводящими соединениями, образующимися в этом бетоне, которые отсутствуют в бетоне состава 3. Действительно, ренгенофазовый анализ бетонов после пропитки их электролитом показал (табл. 2), что составы бетонов существенно различаются.
В бетоне состава 0 присутствуют следующие соединения, которые не обнаружены в бетоне состава 3: Na6.65 Al6.24 Si9.76 O32 – алюмосиликат натрия, Na Al11 O17 – β-глинозем и Na5 Al 3 F 14 – хиолит. Согласно [7] два первых соединения являются твердыми электролитами, обладающими ионной проводимостью. Рентгенофазовый анализ не показал присутствия ин-терметаллидов, которые, по-видимому, за столь короткое время испытания, как двое суток, не образуются.
Выводы
Исследованиями свойств жаростойких бетонов установлено, что для использования в условиях действующего электролизера в качестве материала для электроизоляции блюмсов предпочтителен бетон состава 3. Выбор в его пользу обосновывается химическим составом – 925 –
Таблица 2. Фазовый состав образцов бетонов составов 0 и 3 после пропитки их электролитом, мас. %
Формула |
Минерал |
Образец состава 0 |
Образец состава 3 |
Na F |
Виллиомит |
4,13 |
11,8 |
Ca F 2 |
Флюорит |
1,47 |
3,74 |
Na Al 11 O 17 |
0,23 |
0 |
|
C |
Графит |
25 |
17,9 |
Na 6.65 Al 6.24 Si 9.76 O 32 |
Нефелин |
54,8 |
0 |
Al 2 O 3 |
5,22 |
0 |
|
Na 3 Al F 6 |
Криолит |
8,54 |
4,58 |
Na 5 Al 3 F 14 |
Хиолит |
0,47 |
0 |
Mg O |
Периклаз |
0 |
49,2 |
Mg Al 2 O 4 |
0 |
2,77 |
|
Mg Ca Si O4 |
Монтичеллит |
0 |
3,64 |
K Na 3 ( Al Si O 4 ) 4 |
Нефелин |
0 |
3,29 |
Na 1.71 Al 11 O 17 |
0 |
2,89 |
(наполнителем является магнезит – материал, стойкий к воздействию паров натрия), прочностными характеристиками (модулем упругости и прочностью на сжатие менее 0,1 МПа в диапазоне температур 800–900 °С) и электроизоляционной способностью .
Статья подготовлена с использованием результатов работ, выполненных в рамках федеральной целевой программы «Исследования и разработки по приоритетным направлениям развития научно-технологического комплекса России на 2014–2020 годы», по соглашению № 14.579.21.0032 по теме: «Разработка технологии получения алюминия со снижением расхода электроэнергии на действующих электролизерах на 300-1000 кВт*ч/т алюминия». Уникальный идентификатор RFMEF157914X0032.
Список литературы Жаростойкий бетон для электроизоляции блюмсов алюминиевых электролизеров
- Renе von Kaenel, Jacques Antille, Light Metals, 2011, 569.
- Zhou Dongfang, Yang Xiaodong, Liu Wei, Light Metals, 2012, 607.
- Разработка способов снижения потерь тепла, электрического сопротивления и повышения МГД стабильности электролизеров для производства алюминия: отчет о НИР/ФГАОУ ВО «Сиб. федер. ун-т»; рук. Поляков П.В.; исполн.: Михалев Ю.Г. . -Красноярск, 2014. 184 с. № ГР. 114121750014. Инв. № 315041670003.
- Диаграммы состояния двойных металлических систем: справочник в 3Т.: Т.1/Под общей ред. Н.П. Лякишева. М.: Машиностроение. 1996. 992 c.
- Архипов А.Г., Архипов Г.В. Пат. РФ № 2178884. (2002)
- Электронный ресурс: http://www.markmet.ru/ogneupornie-materialy/ogneupornye-betony-na-zhidkom-stekle.
- Бурмакин, Е.И., Степанов Г.К., Шехтман Г.Ш., Тезисы докладов VI Всесоюзной конференции по физической химии ионных расплавов и твердых электролитов. Ч.2. Киев: 1976. С.118