Абразивно-экструзионная обработка алюминиевых сплавов
Бесплатный доступ
Проанализированы конструктивно-технологические особенности деталей летательных аппаратов, изготавливаемых из алюминиевых сплавов, и сделан вывод о целесообразности использования абразивно-экструзионной обработки сложнопрофильных и труднодоступных поверхностей таких деталей. Рассмотрены особенности абразивно-экструзионной обработки и характеристики инструмента для данного вида финишной обработки. Приведена схема опытно-промышленной установки для абразивно-экструзионной обработки. Определены цель и задачи исследования. Описана методика проведения экспериментальных исследований и используемое оборудование. Исследование проведено в два этапа. На первом этапе исследована зависимость глубины царапины от геометрических характеристик и вида абразивного зерна при абразивно-экструзионной обработке деталей из алюминиевых сплавов. Эксперимент проведен на установке, имитирующей процесс микрорезания единичным абразивным зерном. Полученные результаты позволяют определить вид, зернистость абразива на каждом этапе обработке, а также предварительно определить требуемое усилие прижатия единичного абразивного зерна к обрабатываемой поверхности. На втором этапе рассмотрена и экспериментально проверена возможность абразивно-экструзионной обработки деталей из алюминиевых сплавов. Эксперимент проведен на опытно-промышленной установке экструзионного шлифования. В результате определено влияние состава рабочей среды (зернистости и концентрации абразива) на эффективность обработки (интенсивность съема металла), что позволяет выбирать оптимальную зернистость абразива и его концентрацию. Определено количество циклов обработки, необходимое для удаления дефектного слоя с деталей, изготавливаемых литьем по выплавляемым моделям, при использовании различного вида абразива. Даны рекомендации по выбору состава рабочей среды и режимов абразивно-экструзионной обработки деталей из алюминиевых сплавов. Определены дальнейшие направления исследований.
Алюминиевый сплав, абразивно-экструзионная обработка, рабочая среда, активное абразивное зерно, микрорезание
Короткий адрес: https://sciup.org/147151688
IDR: 147151688
Текст научной статьи Абразивно-экструзионная обработка алюминиевых сплавов
При эксплуатации летательных аппаратов (ЛА) преждевременное разрушение деталей (потеря работоспособности) носит усталостный характер, вызванный высокими циклическими напряжениями изгиба и кручения вследствие воздействия газового и гидравлического потоков в условиях высоких температур и агрессивных сред. Подобному воздействию подвергаются фасонные поверхности большинства объемных сложнопрофильных деталей (лопатки турбин, компрессоров и вентиляторов, роторы винтовых компрессоров, крыльчатки насосов) [1].
Частично критерии работоспособности обеспечиваются на этапе разработки конструкции и выбора материала детали. Критерии прочности и надежности связаны с качеством деталей (величиной шероховатости, ее направлением и формой микронеровностей, полученных при механической обработке поверхности) и обеспечивается технологией их изготовления [2].
Существенное влияние шероховатости поверхности на сопротивление усталости связано с тем, что оставшиеся после обработки микронеровности поверхности являются концентраторами напряжений в поверхностном слое и под действием циклических нагрузок приводят к возникновению и развитию усталостных трещин. Анализ конструкций деталей ЛА показал, что требования по шероховатости поверхности варьируются в диапазоне Ra = 1,25^2,5 мкм для деталей сопловых аппаратов до Ra = 0,32^0,63 мкм для поверхностей проточной части турбин [3]. Высокие требования к шероховатости поверхности приводят к необходимости операций финишной обработки.
Формообразование и последующая финишная обработка сложнопрофильных и труднодоступных поверхностей требуют сложных движений инструмента или использования фасонных инструментов. Зачастую формообразование может быть обеспечено только специальными методами литья и последующей электроэрозионной обработкой. Для таких заготовок характерно наличие дефектного слоя с высокими остаточными напряжениями, наклепом и микронеровностями. Например, величина дефектного слоя у деталей после литья по выплавляемым моделям составляет 0,1…0,8 мм, а шероховатость Ra = 20…40 мкм [4].
В ряде работ [1, 3] предложено использовать для обработки подобных деталей метод абразивно-экструзионной обработки (АЭО) и приведены результаты исследований по обработке деталей, изготавливаемых из жаропрочных, коррозионно-стойких легированных сталей. Но анализ конструкций ЛА показал, что велика доля деталей, изготавливаемых из алюминиевых сплавов (крыльчатки и корпуса насосов ТНА, детали автоматики и рулевых машин и др.) [5, 6]. Распространенность алюминия в самолето- и ракетостроении объясняется его физико-механическими свойствами: низкой плотностью и хорошими прочностными характеристиками его сплавов (например, твердость сплава АМг6 составляет 65 НВ, а предел кратковременной прочности σВ = 275…315 МПа при плотности 2640 кг/м3); хорошей коррозионной стойкостью в атмосфере и среде многих органических кислот из-за наличия сплошной тонкой и плотной оксидной пленки Al2O3); высокой тепло- и электропроводностью (удельная теплопроводность АМг6 С = 922 Дж/кг · К).
Исследование проведено с целью рассмотрения возможности использования метода АЭО для обработки деталей из алюминиевых сплавов, имеющих сложнопрофильные и труднодоступные для стандартных методов обработки поверхности.
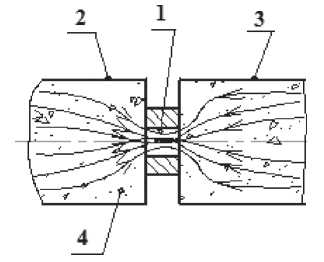
Рис. 1. Схема процесса двухнаправленной абразивно-экструзионной обработки
Суть метода АЭО заключается в экструзии вдоль обрабатываемой поверхности 1 вязкоупругой рабочей среды (РС) 4 наполненной абразивными зернами (АЗ), которая перепрессовывается под давлением при помощи цилиндров 2 и 3 (рис. 1) [7–9].
Под действием давления РС на входе в канал детали формируется сжатый абразивный «жгут», который при движении «отслеживает» контуры канала. На поверхности абразивного жгута находятся активные АЗ, контактирующие с поверхностью канала, вследствие чего при их движении микровыступами снимается определенный слой материала.
В качестве инструмента для АЭО используется рабочая среда (РС), состоящая из полимерной основы и рабочих частиц (например, АЗ) различной зернистости и в различной концентрации с добавлением пластификаторов и модификаторов, позволяющих варьировать физико-механические свойства среды [8, 10].
В отличие от резания закрепленным абразивом процесс АЭО обладает некоторыми особенностями: в контакте с обрабатываемой поверхностью находится часть сжатой под давлением РС, равная площади обрабатываемого канала; геометрическая форма инструмента и параметры резания изменяются в процессе движения абразивного «жгута» вдоль обрабатываемой поверхности вслед- ствие возможного изменения сечения канала и давления среды; активные зерна находятся в длительном контакте с обрабатываемой поверхностью [11]. В процессе обработки РС перепрессовыва-ется, вследствие чего происходит постоянная смена активных АЗ, находящихся в зоне контакта с обрабатываемой поверхностью, и переориентация их микровыступов и т. д. [3]. При этом в отличие от других видов струйной абразивной обработки при АЭО скорости течения РС невысоки, а сила резания определяется реологическими свойствами среды и давлением в системе.
Определение реологических характеристик РС (модуля Юнга, коэффициента Пуассона, эффективной вязкости, измеряемой при сдвиговом течении и пр.) производится в большинстве случаев экспериментально, вследствие сложности многокомпонентной полимерной системы, по методикам, предложенным в ряде работе [12–14].
Для расчета режимов резания необходимо определение нормальной и касательной состав- ляющих силы микрорезания, достаточной для удаления заданного слоя материала или снижения шероховатости (снятия гребешков микронеровностей) [15]. Исследование особенностей контактных взаимодействий при АЭО [16, 17] показало, что глубина царапины и вид взаимодействия (микрорезание, упругое или пластического деформирование) зависит от материала обрабатываемой детали, характеристик его поверхностного слоя, геометрических характеристик АЗ (зернистости, углов при вершине микро- и субмикровыступов, радиусов скруглений) и силы прижатия зерна к обрабатываемой поверхности.
Нами проведено исследование зависимости эффективности обработки от состава РС и режимов резания при АЭО деталей из алюминия и его сплавов. Исследование проводилось в два этапа. На первом этапе имитировался процесс микрорезания единичным АЗ с целью выявления зависимости эффективности резания от геометрических характеристик АЗ и режимов обработки, что позволило определить необходимый вид абразива. Второй этап, выполненный на установке для экструзионного шлифования УЭШ, позволил выявить влияние состава РС (зернистости АЗ и концентрации абразива) на эффективность АЭО.
Имитация контакта при микрорезании единичным АЗ выполнялась на установке МР-2 (рис. 2) со ступенчатым нагружением индентора. Геометрические параметры АЗ моделировались с помощью сменных конических инденторов, изготовленных из сплава Т15К6 с углами заточки, которые при анализе статистических данных [18] были выявлены в качестве наиболее характерных для углов микровыступов АЗ (рис. 3).
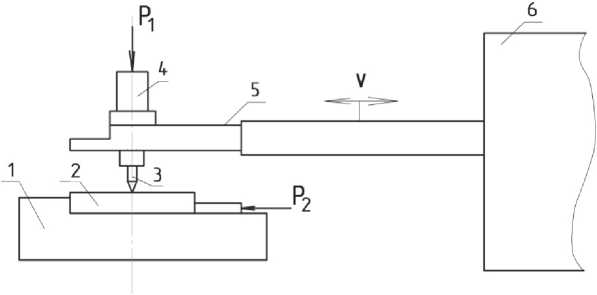
Рис. 2. Установка МР-2: 1 – приспособление; 2 – образец; 3 – индентор; 4 – сменный груз; 5 – шток; 6 –привод
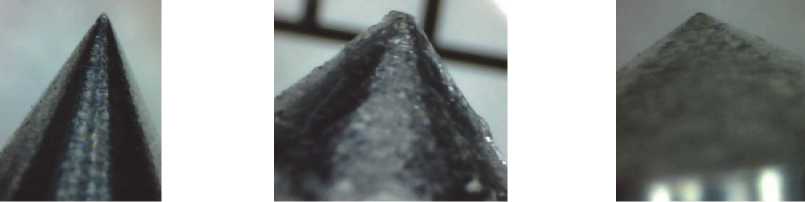
а) б) в)
Рис. 3. Сменные инденторы (×100) с углами заточки: а – 60°; б – 90°; в – 120°
Эксперимент спланирован для двух факторов на трех уровнях варьирования (табл. 1), проведен на катанных образцах из сплава АМг6 твердостью 100 НВ. Эффективность резания оценивалась по глубине царапины h ц .
Расчет глубины царапины h ц проведен по ширине b ц (рис. 4, а) с учетом геометрических характеристик индентора, в том числе его радиуса скругления.
При резании образцов наблюдалось незначительное отделение стружки, зоны врезания в начале и пластического деформирования – в конце, а также навалы по длине царапины (рис. 4, б, в) из-за перераспределения материала вследствие пластического деформирования.
Таблица 1
Факторы, уровни варьирования, матрица полного факторного эксперимента ПФЭ2 и результаты эксперимента
Фактор |
Уровень варьирования |
Шаг λ |
№ опыта |
х 1 |
х 2 |
у |
№ опыта |
х 1 |
х 2 |
у |
||
–1 |
0 |
1 |
||||||||||
х 1 – угол индентора γ, ° |
60 |
90 |
120 |
30 |
1 |
1 |
1 |
0,074 |
6 |
–1 |
0 |
0,157 |
х 2 – нагрузка, Н |
0 |
2,5 |
5,0 |
25 |
2 |
–1 |
1 |
0,263 |
7 |
0 |
1 |
0,116 |
y – глубина царапины h ц , мм |
3 |
1 |
–1 |
0,011 |
8 |
0 |
–1 |
0,095 |
||||
4 |
–1 |
–1 |
0,094 |
9 |
0 |
0 |
0,110 |
|||||
5 |
1 |
0 |
0,051 |
После математической обработки результатов эксперимента получена зависимость эффективности резания алюминиевого сплава от исследуемых параметров:
h ц = 0,535 - 0,84 ⋅ 10 - 2 ⋅γ+ 0,0172 ⋅ Р + 0,4 ⋅ 10 - 4 ⋅γ 2 + 0,64 ⋅ 10 - 2 ⋅ Р 2 - 3,6 ⋅ 10 - 4 ⋅γ⋅ Р , которая позволяет определить зернистость абразива и силу прижатия единичного абразивного зерна Р (нормальную составляющую силы резания).
Эксперимент показал (рис. 5), что глубина царапины при микрорезании возрастает с уменьшением угла заточки индентора и увеличением силы прижатия единичного АЗ к обрабатываемой поверхности. Замечено также, что при резании индентором с острым углом образование царапины происходит за счет микрорезания, а с увеличением угла заточки наблюдается увеличение доли пластического деформирования в объеме контактных взаимодействий.
Аналогичное исследование, проведенное на стальных образцах, и теоретические расчеты [3] показали, что при царапании индентором с углом 60° для образования царапины глубиной 0,01 мм необходима сила 0,4 Н (сталь 45), 0,45 Н (Х18Н10Т) и 0,5 Н (ХН70Ю). При царапании образца из алюминиевого сплава мы наблюдаем образование царапины глубиной на порядок выше.
Следовательно, при обработке алюминиевых сплавов для снятия определенного слоя материала давление в системе должно быть ниже, чем при обработке стальных заготовок. Для уточнения соотношения давления в системе и в зоне обработки при использовании различных составов РС необходимы дополнительные экспериментальные исследования.
В ходе проведенных ранее исследований установлено ориентировочное соотношение величин давления в системе и в зоне обработки для РС, приготовленной на основе каучука СКТ с добавлением мелкодисперсного фторопласта Ф40 и карбида кремния зернистостью F100 в концентрации 60 % [3]. Полученные данные позволяют с учетом этого соотношения построить ориентировочный график зависимости глубины снятого за один цикл (перепрессование РС в прямом и обратном направлении) обработки металла от давления в системе при использовании различного вида абразива (рис. 6). График показывает, что минимальное давление в системе, необходимое для начала обработки с учетом условий обеспечения сдвигового течения РС с указанной концентрацией абразива, должно составлять 4 МПа. Диапазон исследуемых давлений ограничен максимальным давлением, обеспечиваемым гидросистемой установки.
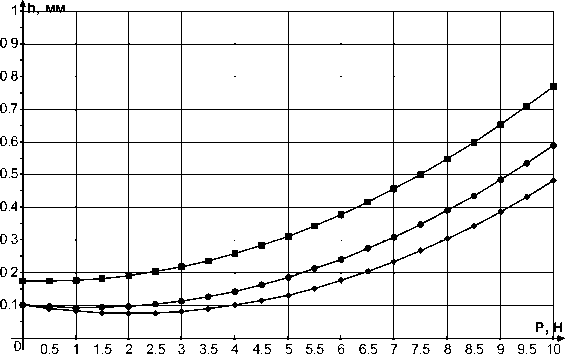
Рис. 5. Зависимость глубины царапины h ц от силы прижатия Р и угла заточки индентора γ: 1 – 60°; 2 – 90°; 3 – 120°
Проведенные расчеты позволяют ориентировочно определить количество циклов обработки необходимых для удаления дефектного слоя с поверхности деталей, изготовленных из алюминиевых сплавов, при обработке различным видом абразива на различных режимах (рис. 7).
В качестве исходных данных для расчетов взята глубина дефектного слоя h = 0,8 и шероховатость Ra = 40 мкм, что соответствует характеристикам поверхностного слоя деталей, изготавливаемых литьем по выплавляемым моделям [19].
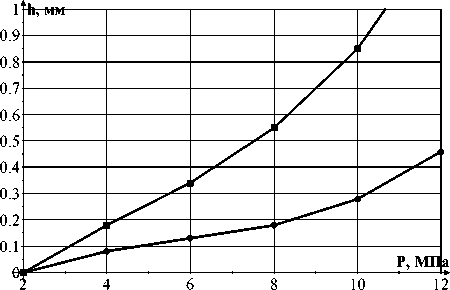
электрокорунд нормальный карбид кремния черный
Рис. 6. Зависимость величины снятого слоя h от управляющего давления в цилиндре на 1 цикл обработки
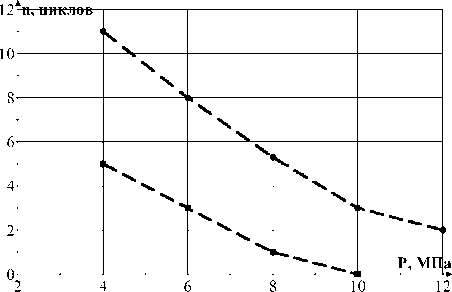
электрокорунд нормальный карбид кремния черный
Рис. 7. Зависимость количества циклов обработки n , необходимых для удаления дефектного слоя от давления масла в управляющем цилиндре
Полученные расчетные данные необходимо подтвердить экспериментальными исследованиями. Необходимо также определить зависимость величины снимаемого за один цикл металла от давления в системе и состава РС (зернистости абразива, концентрации модификатора и рабочих элементов). Проведение подобного исследования необходимо для разработки методики выбора состава РС для различных характеристик поверхностного слоя детали и этапов обработки.
С целью апробации возможности и установления параметров АЭО алюминиевых сплавов проведено исследование влияния состава РС на эффективность обработки.
Эксперименты выполнены на установке УЭШ-100. Опытно-промышленная установка двунаправленного действия УЭШ-100 (рис. 8, 9) имеет два гидроцилиндра с рабочими камерами 2 и 5, между которыми устанавливают приспособление 3, обеспечивающее монтаж и герметичное соединение детали (образца) между рабочими камерами.
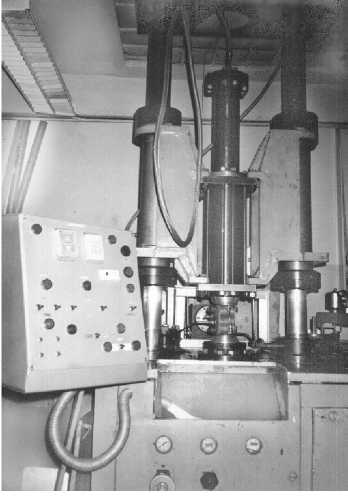
Рис. 8. Общий вид установки УЭШ-100
Верхний гидроцилиндр 5 прикреплен к траве р се 4, которая посредством встроенных гидроблоков 1 имеет возможность перемещаться вверх и вниз по направ л яющим. Установка имеет гидравлическую 10 и электрическую 6 систему управления. Управление возможно в ручном и автоматическом режимах.
Гидравлическая система обеспечивает создание давления масла насосной станцией от 9 до 12 МПа и дистанционную подачу масла в гидроцилин д ры через трубопроводы от гидрозолотников, а электрическая систе м а позволяет управлять элементами гидросистемы и контролировать их срабатывание (включение и выключение н асосной станции, гидр о золотников, конечны х выключателей и др.). Параметры системы контролируют по манометрам, контрольным лампам на панели пу л ьта управления 6 с записью параметров на осциллогр а ф К-115 и самопишущие прибор ы системы измерения 8.
Образцы изготовлены из алюмин и евого сплава АМг6 после фрезерования с шероховатостью пов е рхности Ra = 6,3 мкм. Режимы обработки: управляющее д авление масла в системе Р = 10 МПа; количество циклов n = 10. РС приготовле н а на основе каучука синтетического термостойкого высокомолекулярного СКТ (ТУ 38.103694-89) с добавлением 12 % мелкодисперсного фторопласта Ф40 (ТУ 301-05-17) и карбида кремния ч е рного марки 54С с варьированием зернистости и концентрации абразива с реализацией плана Коно m = 2.
Пульт упр
Измерительный ком п лекс
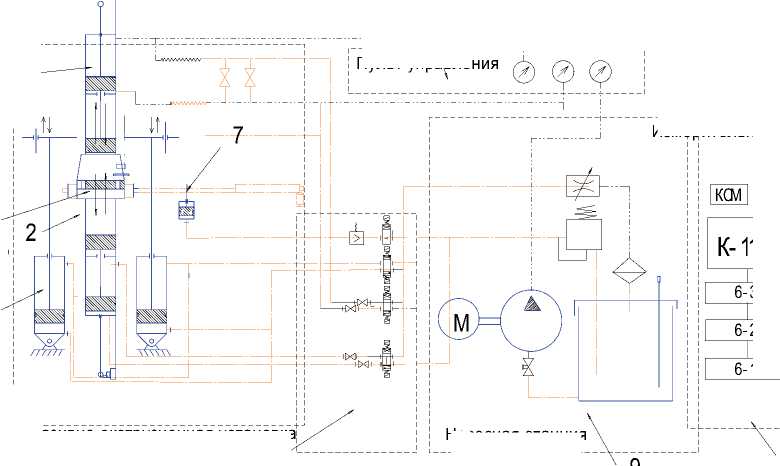
3ZZ
2 zz
Абразивно-экструзионная установка
Насосная станция
УЭШ-100
Шкаф управления
Рис. 9. Схема функциональная установки УЭШ-100
В результате эксперимента было выявлено, что с возрастанием концентрации абразива в РС растет интенсивность съема металла с поверхности (рис. 10, 11).
Увеличение концентрации рабочих частиц приводит к увеличению жесткости РС, и соответственно, к увеличению нормальных напряжений, усилив а ющих прижатие активного зерна к поверхности при постоянном давлении в системе [20]. Помимо этого увеличивается количество активных АЗ – зерен, находящихся в зоне контакта с обрабатыв а емой поверхностью и производя щ их резание. Соответственно, увеличивается производительность снятия материала с поверхности.
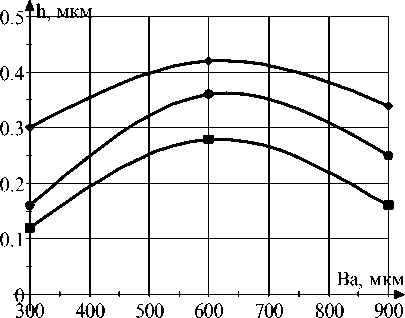
Ka = 50%
Ka = 65%
Ka = 80%
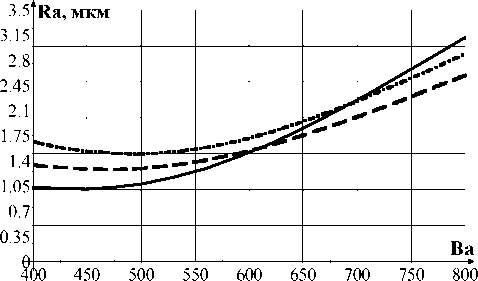
^^^^^^^я Ka = 50%
^^я ^^ Ka = 65%
Ka = 80%
Рис. 11. Зависимость шероховатости Ra от состава РС (зернистости абразива Ва и его концентрации Kа )
Рис. 10. Зависимость интенсивности съема металла по высоте h при АЭО от состава РС (зернистости абразива Ва и его концентрации Kа )
Увеличение зернистости абразива первоначально также приводит к по в ышению интенсивности съема металла. При этом максимальный съем происходит при использовании абразива зернистостью F36. При дальнейшем увеличении зернистости происходит снижение производительности обработки, так как уменьшается площадь контакта единичного зерна с обрабатываемой поверхностью и количество активных зерен в зоне обработки, что обусловлено формой к ристаллов карбокорунда, имеющего небольшое количество режущих кромок (рис. 12). При этом наиболее интенсивный съем металла наблюдается на первых циклах обработки вследствие ударнодинамического характера перемещения зерна между выступами шероховатости, что у в еличивает скорость их перемещения вдоль обрабатываемой поверхности [3]. После у даления м и кронеровностей начинает формироваться направленная шероховатость.
При использовании шлифовального зерна в качестве рабочих элементов и высоком давлении в системе наблюдается увеличение шероховатости с увеличением зернистости и кон ц ентрации абразива в РС. На поверхности образцов после обработки при максимальных значениях факторов наблюдаются царапины и следы внедрения отдельных абразивных зерен (рис. 13). Поэтому при обработке мягких металлов необходимо ограничить концентрацию абразива в РС и использовать шлифпорошки на последних этапах обработки, что позволит исключить возникновение новых царапин после удаления дефектного слоя sY .
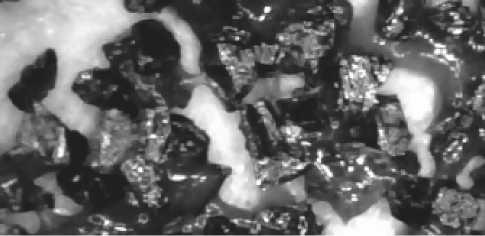
Рис. 12. РС на основе СКТ и карбида кремния черного. Увеличение ×40
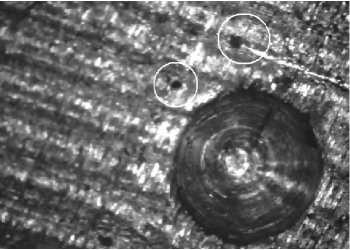
Рис. 13. Следы внедрения отдельных абразивных зерен (отмечены окружностями) в поверхность алюминиевого образца при АЭО. Увеличение ×40
Проведенные исследования позволяют сделать с л едующие выводы:
-
1) при обработке алюминиевых сплавов для уд а ления дефектного сло я необходимо использовать абразив с углами при вершине микровыступ о в менее 90°, что хара к терно, например, для
электрокорунда, а для уменьшения шероховатости поверхности – с углами 90…120° (например, карбид кремния) при силе прижатия единичного АЗ в диапазоне 0,02…0,04 Н, что позволит реализовать пластическое деформирование абразивной обработкой без удаления слоя материала;
-
2) на черновых операциях обработки для снятия основных гребешков микронеровностей после фрезерования, а также удаления дефектного слоя (на заготовках после фрезерования) возможно использование крупнозернистого абразива на умеренных режимах (давление 4…6 МПа). На последующих стадиях обработки зернистость абразива рекомендуется снижать и использовать шлифпорошки и микрошлифпорошки;
-
3) на заключительных стадиях обработки материалов с поверхностной твердостью до 65 НВ необходимо ограничивать содержание абразива в РС пятьюдесятью процентами, так как опыт приготовления РС показывает, что практически невозможно получить высокую концентрацию при использовании мелкозерного абразива (шлифпорошков и микрошлифпорошков). Увеличение концентрации абразива приводит к дополнительному увеличению давления в зоне обработки и вероятности появления дополнительных царапин на поверхности с уже удаленным дефектным слоем.
В настоящее время нами проводятся экспериментальные работы с целью уточнения зависимости сил прижатия АЗ от состава РС и режимов обработки, что позволит при разработке технологии АЭО деталей из алюминиевых сплавов выбирать значения давления в гидросистеме промышленной установки.
Список литературы Абразивно-экструзионная обработка алюминиевых сплавов
- Левко, В.А. Абразивно-экструзионная обработка: современный уровень и теоретические основы процесса: моногр./В.А. Левко; Сиб. гос. аэрокосм. ун-т. -Красноярск, 2007. -228 с.
- Основы расчета и конструирования деталей и механизмов летательных аппаратов: учеб. пособие для втузов/Н.А. Алексеева, Л.А. Бонч-Осмоловский, В.В. Волгин и др.; под ред. В.Н. Кестельмана, Г.И. Рощина. -М.: Машиностроение, 1989. -456 с.
- Сысоев, С.К. Экструзионное хонингование деталей летательных аппаратов: теория, исследования, практика: моногр./С.К. Сысоев, А.С. Сысоев; Сиб. гос. аэрокосм. ун-т. -Красноярск, 2005. -220 с.
- Chokkalingam, B. Analysis of casting defect through defect diagnostic study approach/B. Chokkalingam, S.S. Mohamed Nazirudeen//Journal of Engineering Annals of Faculty of Engineering Hunedoara. -2009. -Vol. 2. -P. 209-212.
- Гахун, Г.Г. Конструкция и проектирование жидкостных ракетных двигателей: учеб. для студентов вузов по специальности «Авиационные двигатели и энергетические установки»/Г.Г. Гахун, В.И. Баулин, В.А. Володин и др.; под общ. ред. Г.Г. Гахуна. -М.: Машиностроение, 1989. -424 с.
- Исследование, разработка и внедрение технологии и оборудования для экструзионного шлифования и полирования сложных каналов в крупногабаритных деталях от 200 до 600 мм (детали типа направляющий аппарат, крыльчатка и др.): отчет о НИР: 0-629-84/рук. С.К. Сысоев; испол.: В.А. Левко, М.А. Лубнин, Д.Б. Скороделов и др. -Красноярск, 1986. -392 с. -Рег. № 01850028567.
- Pat. 3521412 US, ISC B24B 1/00, 19/00. Method of honing by extruding/R.W. McCarty; 05.11.1965; 21.07.1970.
- Pat. US2006205329 US, Method and apparatus for abrading the region of intersection between a branch outlet and a passageway in a body/L.J. Rhoades (US); 14.09.2006; 27.02.2007.
- Pat. 105043 SG ISC B24C 3/00, 3/02, 3/04,7/00, 9/00. Abrasive flow machining apparatus, method and system/Y.M. Wan; 20.02.2009; 27.08.2009.
- Cherian, J. Advances in abrasive flow machining: an overview/J. Cherian, J. Missac//International Journal Metallurgical & Materials Science and Engineering (IJMMSE). -2014. -Vol. 4. -Iss. 1. -P. 15-24.
- Fang, L. Movement patterns of ellipsoidal particle in abrasive flow machining/L. Fang, J. Zhao, B. Li, K. Sun//Journal of Materials Processing Technology. -2009. -Vol. 209, no. 20. -P. 6048-6056.
- Левко, В.А. Особенности реологии рабочей среды при абразивно-экструзионной обработке/В.А. Левко//Вестник Сибир. гос. аэрокосм. ун-та им. акад. М.Ф. Решетнева. -2005. -№ 4. -С. 96-100.
- Снетков, П.А. Экспериментальное определение коэффициентов вязкости, упругости и пластичности рабочей среды при абразивно-экструзионной обработке/П.А. Снетков, В.А. Левко, Е.Б. Пшенко, М.А. Лубнин//Вестник Сибир. гос. аэрокосм. ун-та им. акад. М.Ф. Решетнева. -2009. -№ 4. -С. 134-138.
- Agrawal, A. Experimental determination of viscosity of abrasive flow machining media/A. Agrawal, V.K. Jain, K. Muralidhar//International Journal of Manufacturing Technology and Management. -2005. -Vol. 7, no. 2-4. -P. 142-156.
- Gorana, V.K. Forces prediction during material deformation in abrasive flow machining/V.K. Gorana, V.K. Jain, G.K. Lal//Wear. -2006. -Vol. 260. -P. 128-139.
- Левко, В.А. Контактные процессы при абразивно-экструзионной обработке/В.А. Левко//Металлообработка. -2008. -№ 3 (45). -С. 19-23.
- Anderson, D. Experimental and numerical investigations of single abrasive-grain cutting/D. Anderson, A. Warkentin, R. Bauer//International Journal of Machine Tools and Manufacture. -2011. -Vol. 51, no. 12. -P. 898-910.
- Ефимова, Т.С. Экспериментальное определение геометрических параметров единичной абразивной режущей кромки/Т.С. Ефимова, В.В. Федотов//Труды IV Всерос. конф.-семинара «Научно-техническое творчество: проблемы и перспективы», Сызрань 22 мая 2009 г. -Самара: Изд-во Самар. гос. техн. ун-та, 2009.
- Sysoeva, L.P. Surface-stress reduction in channels after electrospark machining by abrasion and extrusion/L.P. Sysoeva, A.S. Sysoev//Russian Engineering Research. -2013. -Т. 33. № 1. -С. 51-52.
- Левко, В.А. Влияние состава рабочей среды на технологические режимы абразивно-экструзионной обработки сложнопрофильных деталей/В.А. Левко, Е.Б. Пшенко//Вестник Сибир. гос. аэрокосм. ун-та им. акад. М.Ф. Решетнева. -2006. -№ 4. -С. 64-68.