Анализ газогенерирующих систем для автономного энергоснабжения лесных терминалов
Автор: Куницкая Ольга Анатольевна, Помигуев Александр Владимирович, Калита Евгений Георгиевич, Швецова Виктория Викторовна, Тихонов Евгений Андриянович
Журнал: Resources and Technology @rt-petrsu
Рубрика: Полная статья
Статья в выпуске: 3 т.18, 2021 года.
Бесплатный доступ
Одной из наиболее острых проблем лесного комплекса Российской Федерации, в настоящее время, является истощение запасов спелых и перестойных эксплуатационных лесов в экономически доступной удаленности. Ежегодно растет расстояние вывозки заготовленной древесины, особенно в Сибири и на Дальнем Востоке. Рост расстояния вывозки заготовленной древесины приводит к существенному росту себестоимости продукции лесозаготовительного производства, поскольку в себестоимость транспортной составляющей входят не только строительство и содержание лесных дорог, но и горючее, масла, шины, и т.д. для автолесовозов, заработная плата водителей. Для снижения транспортной составляющей себестоимости разработана и успешно используется в Сибири и на Дальнем Востоке технология создания лесных терминалов (непостоянных лесопромышленных складов), производящих, обычно, пиломатериалы, иногда ряд других видов продукции. Это позволяет существенно повысить коэффициент полнодревесности воза автолесовозов. Для эффективной работы лесных терминалов необходимы автономные источники энергоснабжения. В настоящее время, обычно, энергоснабжение мобильных деревообрабатывающих станков производится от вала отбора мощности трактора, или дизельного генератора. Такой вариант энергоснабжения не оптимален, ввиду дороговизны самого горючего и его доставки к лесному терминалу. Использование газогенерирующих систем позволяет существенно снизить расходы на энергоснабжение лесных терминалов. Работа выполнена в рамках научной школы «Инновационные разработки в области лесозаготовительной промышленности и лесного хозяйства» Арктического государственного агротехнологического университета.
Лесные терминалы, газогенерирующие системы, автономное энергоснабжение, мобильные деревообрабатывающие станки
Короткий адрес: https://sciup.org/147236115
IDR: 147236115 | DOI: 10.15393/j2.art.2021.5823
Текст научной статьи Анализ газогенерирующих систем для автономного энергоснабжения лесных терминалов
-
1. Введение
-
2. Материалы и методы
Для выполнения деревообрабатывающих операций на лесных терминалах используют мобильные лесопильные станки (ленточные и дисковые), мобильные рубительные машины, иногда мобильные комплексы по производству прессованного биотоплива (пеллет, брикетов), также возможными потребителями энергии на лесных терминалах могут быть установки по производству биологически активных веществ, по переработке пищевой продукции леса (грибов, ягод). Таким установкам требуется либо только электрическая энергия, либо электрическая и тепловая. Понятно, что уровень энергопотребления зависит от перечня установок на лесном терминале. Для оптимального выбора автономной энергетической установки надо иметь информацию о её возможностях и потребностях оборудования лесного терминала, включая обслуживающие производства — ремонтное оборудование, помещения и оборудование вахтового посёлка, обычно совмещённого с лесным терминалом.
Различные системы автономного энергоснабжения активно используются во многих странах мира для обеспечения работы удалённых объектов сельского хозяйства, лесных плантаций и т. д. [1—5].
Переработка заготовленной древесины на верхних складах и лесных терминалах позволяет получать пиломатериалы, технологическую и топливную щепу, прессованное биотопливо [6— 13] и также требует автономных источников энергии. Очень полезными будут автономные источники энергии и при ликвидации чрезвычайных ситуаций, например лесных пожаров [14].
Развитие государства, его экономики обусловлено наличием соответствующей ресурсной базы, особенно источниками энергоресурсов. В регионах, где отсутствует централизованное теплоснабжение, системы газогенерации могут стать одним из оптимальных решений в короткие сроки при наименьших финансовых затратах [15].
На данном этапе общественного и технологического развития наиболее значимым энергоресурсом является нефть. Больше всего нефтяная зависимость выражена в работе транспортного комплекса.
Расход за год на одно транспортное средство в среднем 2,1—2,3 т бензина (или дизтоплива). Если оценить для всех средств наземного транспорта, то в совокупности это 2,2—2,5 млрд т топлива. Для получения такого количества топлива, в зависимости от условий и задач, необходимо от 6,2 до 8,8 млрд т нефти.
Согласно данным British Petroleum, при таком объёме потребления обеспеченность мировыми запасами нефти составляет 30—35 лет. Данное обстоятельство побуждает всерьёз задаться целью поиска альтернативных энергоресурсов. И во многих странах ведутся интенсивные разработки, обеспечивающие уменьшение расхода топлива и поиск топлив новых видов.
Виды энергоресурсов классифицируются по:
-
• содержанию и составу: углеводороды, водород и производные;
-
• агрегатному состоянию;
-
• форме применения;
-
• сырьевым ресурсам.
-
3. Результаты
Получение новых видов топлив позволяет обеспечить конкурентное развитие государства, его энергетической отрасли и соответствующих компаний-участников. Уже почти половиной мирового рынка производства синтетического газа владеет компания «Эйр Продактс» (США) — 36,5 млн м3 в год. И объёмы производства ею стремительно наращиваются: рост составляет более чем в 10 раз. Понятно, что этот рынок гораздо меньше рынка природного газа, но это направление обладает преимуществом возобновляемости ресурсной базы, поэтому в данные сферы вкладываются значительные инвестиции.
Ещё один пример. Промышленная группа Gas Technology Institute (США) реализовала проект запуска газифаера, обеспечивающего промышленные объёмы производства синтетического газа, причём уже очищенного от примесей [16].
Газификация состоит из несколько последовательных процессов, которые включают: сушку твёрдого вещества, пиролиз твёрдого вещества с образованием газов, смол и полукокса, крекинг и окисление смол (и, в некоторой степени, окисление пиролизных газов) и газификацию полукокса. Вместе с химическим процессом имеют место и испарение влаги, и явления переноса. Продукты газификации могут использоваться в качестве заменителя топлива, получаемого из нефти. В частности газ, получаемый в тепловых газификаторах может использоваться при производстве электрической и тепловой энергии на предприятиях лесного комплекса.
Таким образом, в сфере газификации топлива для получения возобновляемых энергоресурсов произошло качественное изменение ситуации: экономически оправдан резкий переход от единичных пилотных установок к массовой реализации коммерческих проектов.
Ниже приведена рентабельность переработки в России некоторых видов сырья:
-
1. Бурый уголь — от 75 до 90 %.
-
2. Торф (30 %-я влажность) — 45—50 %.
-
3. Древесные и сельскохозяйственные отходы — 70—80 %.
-
4. Бытовые отходы — 50—60 %.
Различные виды древесных отходов имеют разные размеры и форму, а поэтому при конструировании генератора в каждом отдельном случае нужно сообразовываться именно с тем видом отходов, для газификации которых он предназначен. В том случае, если в одном генераторе предположено использовать ряд древесных отходов, конструкция генератора должна удовлетворять специфическим особенностям каждого из отходов.
Для того чтобы произвести полное испарение содержащейся в топливе влаги при помощи физического тепла горячих газов, поступающих из нижней части генератора, и обеспечить устойчивый режим газификации, необходимо иметь большую высоту слоя топлива.
Площадь поперечного сечения верхней части шахты генератора должна быть возможно большей, чтобы не было уноса потоком мелких частиц топлива (например, опилок). Это мероприятие также необходимо для устранения излишней потери давления при применении топлива с малым размером кусков.
С другой стороны, при газификации древесных отходов отсутствуют обычные затруднения, встречающиеся при газификации каменного угля, вроде спекания и шлакования, за исключением разве отдельных случаев, когда растительные отходы содержат различные минеральные загрязнения, и поэтому некоторое шлакообразование может иметь место.
Вообще говоря, можно считать древесные отходы и растительные отбросы одним из наиболее легко газифицируемых видов топлив. Практически всякие отходы и отбросы растительного происхождения могут успешно перерабатываться в газогенераторах.
Энергетическая отрасль России имеет огромные ресурсные возможности для производства синтетических видов топлива из возобновляемых ресурсов. Соответственно, инвестируя в развитие и оптимизацию технологий газификации, РФ надолго может обеспечить лидирующие позиции и в сегменте альтернативной и возобновляемой энергетики.
Основа процесса газификации — термохимическое преобразование твёрдого и жидкого исходного сырья в газовый или жидкий продукт. Получаемый продукт транспортируется и сжигается для извлечения тепловой энергии с целью её механического или электромеханического преобразования, когда конечным результатом становится получение электрической энергии.
Газификация — гетерогенный физико-химический процесс со сложной кинетикой: непрерывно протекают многочисленные последовательные, параллельные, прямые и обратные химические реакции. Процесс реализуется в условиях фильтрационного и диффузионного переноса энергии, импульса и массы вещества в гетерогенной полидисперсной среде. Также характерно наличие фазовых превращений.
Интенсивное освоение альтернативной энергетики произошло в предвоенный период, в частности, в Германии, которая испытывала недостаток нефтяных месторождений, но располагала большими запасами угля. Задача преобразования угля в жидкое топливо была решена, что и было представлено в работе Ф. Фишера и Г. Тропша (1926). Это известный теперь синтезом Фишера — Тропша, направленный на получение углеводородов из монооксида углерода и водорода. В свою очередь, смесь CO и H, именуемую синтез-газом, получают из угля или углеродсодержащего сырья. В годы Второй мировой войны Германия производила авиационный бензин полностью из синтетического топлива. В СССР существовала аналогичная программа газификации твёрдых топлив [17].
Рост добычи газа и нефтедобычи в послевоенные годы обеспечил замещение нефтью остальные энергоресурсы жидких и газовых топлив. Однако в 1973 г. произошёл нефтяной кризис, связанный с резким повышением цен на нефть.
Переход к системам генерации газа на твёрдом топливе — это не возврат к забытому прошлому, а переход к новой спирали развития энергетики. Дальнейшее улучшение качества нефтепродуктов достигло своего предела. В конечном итоге в рабочем объёме цилиндра двигателя внутреннего сгорания образуется газовая смесь, воспламенение которой создаёт механическое движение. По данным российских и зарубежных исследователей, ежегодный прирост биомассы на планете покроет все необходимые энергозатраты человека при рациональном использовании всего 10 % от количества, воспроизводимого природой. Помимо сохранения запасов углеводородов, это улучшит экологическую ситуацию в регионах (отказ от карьерного захоронения отходов производства). Ориентировочная стоимость такого топлива составляет 25 руб. за 1 кг. Этого количества топлива вполне достаточно для выработки 1,2 кВт/ч электроэнергии и 3 кВт/ч тепла в пересчёте на электроэнергию.
Газогенераторные комплексы по назначению используются в двух направлениях. Простейшие генераторы окислительного газа, даже с низким КПД, обеспечивают хорошую энергоэффективность: 750 Вт на 1 кг топлива. Этот предел увеличивается, когда мощность генерации увеличивается до 1 МВт или более. При переработке сельскохозяйственных отходов возникает второе направление, при котором следует применять комбинированные газогенераторы, оборудованные анаэробным компонентом (вторая ступень). В этом случае энергетический потенциал обрабатываемого сырья используется более эффективно. На второй ступени газогенератора можно производить тепло, электрическую энергию, а также синтетическое топливо. Генераторы этого типа имеют наибольший потенциал для использования при переработке отходов животноводства, но обладают некоторыми техническими недостатками в работе отдельных узлов. Эти недостатки препятствуют промышленному использованию газификаторов в настоящее время [18].
Действительно, по сути, газогенератор — это миниатюрная газовая фабрика. В процессе газогенерации твёрдое топливо в ходе ряда термохимических процессов газифицируется, превращаясь в газ-производитель. Генераторный газ содержит основные компоненты: окись углерода (CO), метан (CH 4 ), водород (H 2 ). Можно предположить, что в стационарном режиме работы генератора процесс разложения топлива протекает самосогласованно. Продукты газификации представлены на рисунке 1.
Эффективность альтернативной энергетики с точки зрения усреднённых ценовых показателей представлена в таблице 1.
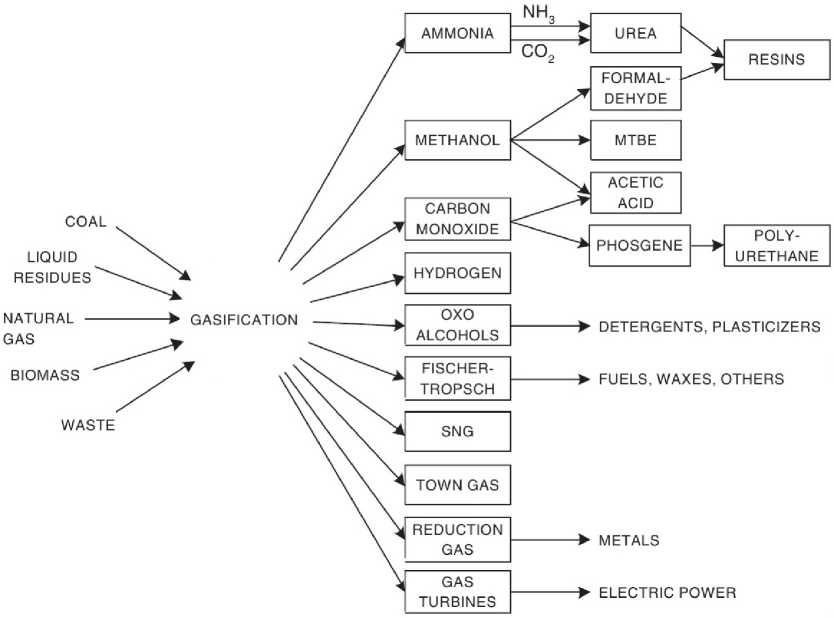
Рисунок 1. Продукты газификации
Figure 1. Gasification products
Таблица 1. Сравнение ценовых показателей альтернативных ресурсов энергии
Table 1. Comparison of price indicators of alternative energy resources
Вид энергоустановки |
Цена энергии за 1 кВт/ч |
|
электрическая |
термическая |
|
Прямое использование солнечного излучения |
от 5 до 40 руб. |
— |
Ветрогенератор |
от 14 руб. |
— |
Биогаз |
1 м3 от 7 руб. |
|
1 м3 — 2,1 кВт/ч |
||
Газогенератор (газификация) |
от 0,90 до 1,50 руб. |
от 0,40 до 1,10 руб. |
Комбинированная |
от 0,40 до 1,50 руб. |
от 0,40 до 1,10 руб. |
Resources and Technology 18 (3): 53-76, 2021 ISSN 2307-0048
Наибольшее распространение в нашей стране и мире получили технологии газификации топлив в потоке, в плотном слое и в «кипящем» слое. В реакторе при повышении температуры химическое равновесие смещается в направлении эндотермических реакций. При этом соотношение СО/СО2, кроме температуры, зависит ещё от избытка воздуха, давления, способа контактирования топлива, наличия катализаторов, концентрации реагентов.
Слоевая газификация в плотном слое представлена: прямого действия (рисунок 2), обратного (рисунок 3). «Горизонтальная» или «поперечная» схема газификации в плотном слое представлена на рисунке 4.
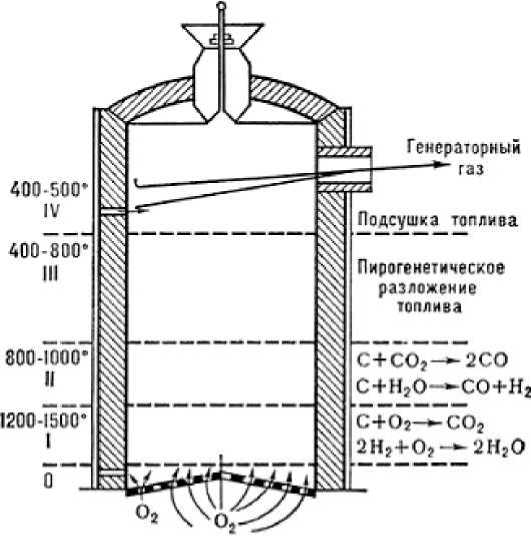
Рисунок 2. Схема прямого процесса газификации
Figure 2. Scheme of the direct gasification process
К настоящему времени освоены различные модификации промышленных процессов газификации конденсированных топлив, наиболее распространёнными из которых являются технологии Лурги (газификация под давлением в псевдостационарном плотном слое кускового топлива), Винклера (газификация в псевдокипящем слое мелкозернистого топлива), «Эксон» (газификация в псевдокипящем слое мелкозернистого топлива в присутствии катализатора), «Ферко Силвагаз» (газификация в псевдокипящем слое мелкозернистой биомассы), Копперса — Тотцека (газификация в потоке пылевидного топлива), «Моултен Солт» (газификация в расплаве соды), «Атгаз» (газификация в расплаве железа), Тексако (газификация водотопливной суспензии), Велмана — Галуши и их различные вариации и комбинации.
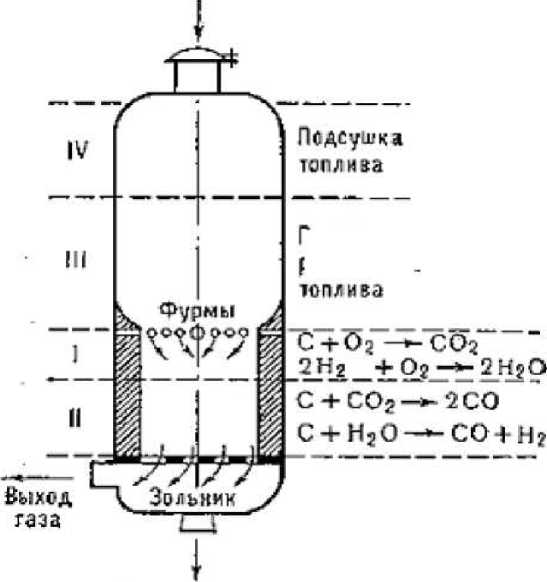
Удаленке золы
Рисунок 3. Схема обращённого процесса газификации
Figure 3. Scheme of the reversed gasification process
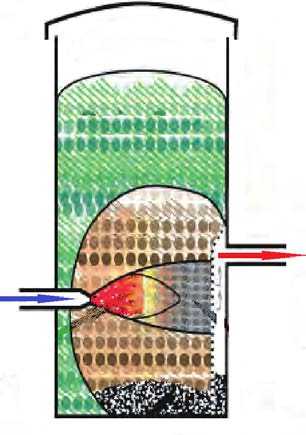
Рисунок 4. Схема поперечного процесса газификации
Figure 4. Diagram of the transverse gasification process
Генераторы прямого процесса не получили широкого распространения, т. к. в условиях работы на влажном и смолистом топливе они требуют сложных дополнительных устройств для тонкой очистки получаемого газа. Поэтому они применяются только в том случае, если их работа ориентируется на бессмольное топливо, как, например, кокс, древесный уголь, антрацит и др.
Генераторы с обращённым процессом получили наибольшее распространение не только вследствие того, что в них возможно газифицировать топлива, содержащие смолы, но и потому, что процесс газообразования отличается гибкостью, загрузка топлива производится на ходу машины и не требует сложных загрузочных приспособлений, устройство шахты просто и, наконец, возможна работа на различных видах топлива. Подача воздуха в различных конструкциях генераторов этого типа производится через щель, фурмы, центральную трубку и, наконец, через центральную трубку и фурмы, а отвод газа — через колосниковую решётку, над колосниковой решёткой и в центре газификатора.
Генераторы с горизонтальным процессом используются преимущественно в целях максимальной экономии места. Единственное отличие их от генераторов прямого процесса заключается в том, что газ проходит через слой топлива по горизонтальному направлению. Также как и генераторы прямого процесса, они пригодны для работы только на топливах, бедных летучими веществами.
При практической реализации процессов газификации используется широкий спектр типов реакторов. Для большинства целей эти типы реакторов могут быть сгруппированы в одну из трёх категорий: газификаторы с подвижным слоем, газификаторы с псевдоожиженным слоем и газификаторы с увлечённым потоком.
Газификаторы с подвижным слоем (иногда называемые газификаторами с неподвижным слоем) характеризуются следующим: слой, в котором топливо медленно движется вниз под действием силы тяжести. При таком противоточном расположении горячий синтез-газ из зоны газификации используется для предварительного нагрева и термообработки нисходящего топлива. Благодаря этому процессу потребление кислорода очень низкое, но в продукте присутствуют синтез-газ и побочные продукты. Температура на выходе синтез-газа обычно низкая, даже если в центре слоя достигаются высокие температуры шлакообразования. Преобразование биомассы в топливный газ, называемое газификацией, является ключевой технологией для производства электроэнергии на основе биомассы. Некоторые примеси, такие как смола, оксиды серы, оксиды азота и аммиак, всегда присутствуют в газе продукта. Однако двигатель внутреннего сгорания может принимать только очень ограниченную концентрацию этих загрязняющих веществ. Он требует обязательной очистки продуктового газа путём удаления загрязнений до определённого минимального уровня. Среди загрязняющих веществ также присутствует смола, которая блокируют проход вещества.
Газификаторы с псевдоожиженным слоем обеспечивают чрезвычайно хорошее перемешивание сырья и окислителя, что способствует тепло- и массообмену. Это обеспечивает равномерное распределение сырья в слое газификации. Работа газификаторов с псевдоожиженным слоем обычно ограничивается температурой, которая ниже точки размягчения золы, т. к. шлакообразование золы нарушает псевдоожижение слоя. Размер частиц имеет решающее значение. Более низкая температура в процессах с псевдоожиженным слоем означает, что такой процесс более подходит для газификации такого сырья, как низкосортный уголь, биомасса, отходы дерево- и сельхозпереработки.
Газификаторы с увлеченным потоком работают с подпиткой и дутьём в прямоточном потоке. Топливо измельчается до размера 100 мкм или менее, чтобы способствовать массопереносу и обеспечить перенос газа. Все газификаторы с увлеченным потоком работают в диапазоне шлакования. Высокотемпературная работа создаёт высокую потребность в кислороде для этого типа процессов. Газификаторы с увлечённым потоком не имеют особых технических ограничений на тип используемого топлива.
Один важный момент, который следует отметить во всём вышесказанном, это важность ошлакованной золы. При температурах выше точки размягчения зола вызывает закупорку технологических отверстий и загрязнение синтез-газа, поэтому приходится чистить или полностью менять ответственные узлы оборудования.
Температура, необходимая для полной термогазификации биомассы, составляет не менее 900 °C, т. е. имеет тот же порядок величины, что и при газификации угля. С другой стороны, имеется ряд существенных различий между газификаций угля и газификацией биомассы, которые напрямую связаны с природой сырья. Во-первых, это качество золы биомассы, которая имеет низкую температуру плавления, но в расплавленном состоянии очень агрессивна. Во-вторых, высокая реакционная способность биомассы. Кроме того, значение имеет волокнистый характер растительной биомассы. Наконец, в низком диапазоне температур газификация биомассы имеет очень высокое содержание смол. Для обработки кусковой древесины применялся ряд процессов с подвижным слоем, но пока рабочая высокопроизводительная технология не получена. Поэтому в большинстве процессов для газификации биомассы используют псевдоожиженные слои и стремятся найти решение проблемы образования отложений смол (дёгтя).
В отличие от газификации воздухом газификация паром требует внешнего источника теплоты, если пар используется в качестве единственного газифицирующего агента. В этом случае получаются преимущественно водород, окись углерода и отчасти углекислота, к которым примешивается водяной пар. Также подачей водяного пара можно существенно снизить температуры в зоне восстановления и повысить теплоту получаемого смешанного газа за счёт образования дополнительного количества СО и Н 2 . Получаемый при этом газ называется водяным генераторным газом.
Реакторы газификации варьируются от процесса к процессу. На первый взгляд, процессы могут выглядеть как простая печь, но на самом деле они часто механически самые сложные. Например, с псевдоожиженным слоем сложность заключается непосредственно в псевдоожижении. В остальном эти реакторы относительно просты. Главное преимущество в том, что рабочая температура ниже температуры плавления золы и давление также ниже, чем у большинства других процессов. Самая простая и недорогая конструкция — реактор с футеровкой из огнеупорного кирпича. В случае одноступенчатых газификаторов с верхним пламенем реактор состоит из одного цилиндра, с отверстием в верхней части для горелки и для подачи сырья, а внизу расположен центральный выход как для продуктового газа, так и для шлака. Наличие одного выхода как для продуктового газа, так и для шлака является преимуществом, т. к. вероятность закупоривания шлакового крана или выхода газа практически отсутствует даже в газогенераторах малой мощности. Дополнительное преимущество теплоизоляционного реактора с кирпичной стенкой в том, что она имеет большую теплоёмкость. Устройство нагрева может быть встроено в основную горелку. Реактор и облицовочная кладка нагреваются вначале пусковой горелкой, затем пусковая горелка заменяется на угольную или масляную горелку, а реактор находится частично под давлением (повышенным или пониженным). Альтернативой огнеупорной футеровке является водоохлаждаемая мембранная стеновая конструкция.
Газы покидают реактор газификации при высоких температурах, которые варьируются от 550 °C для некоторых газификаторов с подвижным слоем сухой золы до 1600 °C для шлаковых газификаторов с увлеченным потоком сухого угля. Синтез-газ из реактора газификации загрязнён различными компонентами, которые необходимо удалить перед его использованием. Это загрязнители, которые могут быть твёрдыми частицами, соединениями серы или хлора, смолами. Процессы очистки газа работают при температурах значительно ниже, чем температура газификации, т. е. всегда существует необходимость охлаждать синтез-газ. Наиболее высокотемпературными процессами газификации являются шлакообразование с увлечённым потоком. При охлаждении газа любые увлеченные частицы золы неизбежно проходят через критический диапазон температур, при котором зола становится липкой. Температура, при которой зола становится сухой, обычно около 900 °C.
Газификаторы топлива с псевдоожиженным слоем обычно имеют температуру на выходе 900—1000 °C. Даже после прохождения циклонов газ содержит некоторое количество летучей золы, и, следовательно, в конструкции охладителя синтез-газа возникает опасность появления эрозии.
Большинство газификаторов биомассы работают при температуре около 900 °C и страдают от одинакового охлаждения синтез-газа. Кроме того, поскольку зола биомассы богата щелочами и карбонатами, то они могут конденсироваться или десублимироваться и вызывать дополнительное загрязнение в интервале температур между 600 и 900 °С. При более низких температурах при достижении точка конденсации смол возникают условия для улавливания частиц золы.
В некоторых случаях топливо проходит стадию предварительной торрефикации. Торрефикация представляет собой мягкий процесс пиролиза и проводится в диапазоне температур от 230 до 300 °C в отсутствие кислорода. Эта предварительная термическая обработка биомассы улучшает её удельную энергию, снижает соотношение кислорода и углерода (O/C) и их гигроскопичность. Во время этого биомасса подсушивается, уменьшается её масса, в значительной степени сохраняя свою энергетическую ценность. Процесс торрефикации удаляет H2O и CO2 из биомассы. В сырой биомассе высокое содержание кислорода вызывает чрезмерное окисление во время газификации, увеличивая термодинамические потери. Торрефикация также увеличивает относительное содержание углерода в биомассе. Свойства обожжённой древесины зависят от температуры и продолжительности обжига, а также от вида самой древесины. Торрефикация также изменяет структуру биомассы, делая её более рыхлой. Это вызвано деполимеризацией гемицеллюлозы. В результате процесс измельчения становится проще, что снижает энергозатраты. Это упрощает сжигание биомассы или её газификацию в реакторе. Особенность торрефикации заключается в том, что она снижает гигроскопичность, поэтому при хранении торкретированной биомассы она поглощает меньше влаги, чем свежая биомасса.
В биомассе гемицеллюлоза подобна цементу в железобетоне, а целлюлоза похожа на стальные стержни. Нити микрофибрилл (целлюлоза) поддерживаются гемицеллюлозой. Разложение гемицеллюлозы при торрефикации происходит как таяние цемента из железобетона. Во время торрефикации происходит снижение веса биомассы, из-за разложения компонентов гемицеллюлозы. Таким образом, после торрефикации биомасса уменьшается в размерах что обеспечивает снижение энергозатрат при её транспортировке. Гемицеллюлоза разлагается, как правило, в диапазоне температур от 150 до 280 °C, что является температурой её торрефикации. Лигнин, связующий компонент биомассы, начинает размягчение выше температуры 130 °C, что способствует уплотнению торрированной биомассы. Таким образом, разложение гемицеллюлозы является основным механизмом торрефакции. При температуре выше 180 °C реакция становится экзотермической с выделением газа.
Использование газогенератора в сочетании с системой обратной связи создаёт значительный экономический эффект. Затраты при использовании брикетов примерно в 15 раз меньше, чем при использовании дизельного топлива. Более того, промышленные отходы могут быть использованы в качестве сырья для производства топливных брикетов, т. е. это решение обладает ресурсом дополнительного «суперэффекта», когда выработка энергии сопровождается утилизацией отходов. Трудно переоценить такую выгоду, поскольку задача поддержания экологического баланса и эффективной глубокой переработки отходов является одной из наиболее актуальных в настоящее время.
По сути, эта технология используется для создания процесса с завершённым циклом переработки отходов производства. Основной особенностью газогенератора является система автоматической оптимизации теплового режима камеры газификации и повышенное содержание водорода и метана в общем объёме генераторного газа. Фурменный пояс камеры газификации в новой конструкции изготовлен методом литья из металлокерамики, в состав которой входят ингибиторы, также инициирующие образование водорода и метана. При этом рабочий ресурс фурменного пояса увеличивается почти в 3 раза. Избыток электрической энергии накапливается в ячейке из топливных элементов.
Система основана на принципе максимального сокращения узлов и агрегатов с механическим и электромеханическим приводом, т. к. их эксплуатация инициирует наибольшее количество отказов в аварийных ситуациях. Вероятность их возникновения возрастает в условиях низких температур. Именно по этой причине из технологической схемы исключаются углеводородные виды топлива, в т. ч. конденсированный природный газ.
Газогенератор может быть использован для утилизации сельскохозяйственных и промышленных отходов, а также шлама очистных сооружений; при замене классического топлива (местный уголь, мазут, торф, природный газ) на синтез-газ, используемый для технологических нужд предприятия и ЖКХ, путём преобразования его в электрическую и тепловую энергию [19].
Сырьевым ресурсом для работы газогенератора на твёрдом топливе являются брикеты, в т. ч. из лесных и сельскохозяйственных отходов с влажностью не более 30 %. Размер брикетов от 10 до 100 мм (без определённой формы) и от 10 × 40 × 100 мм до Ø60 × 100 мм (прессованные).
В комплекте с газогенератором присутствует система очистки газа. Дополнительным оборудованием для работы комплекса является линия измельчения, сушки и брикетирования, газопоршневая установка. Газ, полученный при высокотемпературной газификации, принудительно направляется в зону регенерации, где он превращается в генераторный газ. Затем производятся очистка, охлаждение и транспортировка. Вся агрегатированная конструкция может быть как стационарного, так и мобильного исполнения. Система может работать круглосуточно, в автоматическом режиме и дистанционно обслуживается одним оператором в смену. Управление осуществляется в автоматическом или, при необходимости, ручном режиме. Модельный ряд представлен в таблице 2.
Химический состав генераторного газа: СО = 32—34 %; N 2 = 32—36 %; СН 4 = 5—8 %; CO 2 = 2—5 %; Н 2 = 2—18 %; H 2 S = до 0,01 %; С 2 —С 10 = до 10 %; NO = до 0,015 %.
При преобразовании органических веществ в газ и жидкое топливо реактор газификации может состоять из двух отдельных камер: одна для влагоудаления влаги, другая для газификации, поскольку избыточное содержание влаги на начальном этапе снижает энергоэффективность установки. Конструктивное исполнение реактора обеспечивает увеличение выхода до 90 % продукта, в котором содержание воды снижено до 1—1,5 %, а удельная теплота сгорания увеличена на 15—20 %.
Занимаемая площадь под действующую установку переработки отходов и генерации энергии (тепловой и электрической) приведена в сравнительной таблице 3.
Для каждого типа мощности системы генерации необходим общий склад для топлива из расчёта месячной нагрузки энергопотребления. Площадь склада может варьироваться в пределах от 200 до 1000 м2.
Таблица 2. Технические характеристики газогенерирующих систем отечественного производства
Table 2. Technical characteristics of gas generating systems of domestic production
Параметры |
Марка газогенерирующей системы |
||||
ГТГ-100 |
ГТГ-150 |
ГТГ-200 |
ГТГ-500 |
ГТГ-1000 |
|
Электрическая мощность, кВт/ч |
30 |
45 |
60 |
160 |
330 |
Сумарная тепловая мощность реактора-газификатора, МВт |
0,122 |
0,183 |
0,244 |
0,610 |
1,22 |
Выработка газа, м3/ч с калорийностью, ккал/м3 |
70—85 1250—1000 |
100—130 1250—1000 |
140—170 1250—1000 |
360—430 1250—1000 |
720—860 1250—1000 |
Расход топлива, кг/ч: |
|||||
биомасса |
41 |
62 |
82 |
210 |
380—440 |
лузга подсолнечника и шелуха риса, опил и щепа |
35 |
52 |
70 |
175 |
330—370 |
иловые осадки очистных сооружений |
38 |
57 |
76 |
163 |
350—420 |
торфяные брикеты, бурые угли |
34 |
51 |
68 |
170 |
320—360 |
Габаритные размеры, м |
5 × 1,1 × 3,5 |
6 × 1,4 × 4 |
8,5 × 3,5 × 5,1 |
10,5 × 5 × 6,1 |
12 × 6,5 × 6,1 |
Масса, кг |
3400 |
4950 |
5300 |
6100 |
7500 |
Утилизируемое при охлаждении газа технологическое тепло в виде горячей воды, Гкал/ч |
0,018 |
0,026 |
0,038 |
0,095 |
0,19 |
Утилизируемое тепло в виде горячей воды от работы ГПЭС (газопоршневой электростанции), Гкал/ч |
0,04 |
0,06 |
0,08 |
0,22 |
0,43 |
Усреднённый выход газа из 1 кг топлива, м3/кг |
1,8—2,3 |
1,8—2,3 |
1,8—2,3 |
1,8—2,3 |
1,8—2,3 |
Энергетическая отдача газа из 1 кг топлива, ккал/кг |
1900—2300 |
1900—2450 |
1900—2600 |
1900—2750 |
1900—2750 |
Энергоотдача по технологическому теплу из 1 кг топлива, ккал/кг |
550 |
550 |
550 |
550 |
550 |
Суммарная энергоотдача, ккал/кг |
2450—2850 |
2450—3000 |
2450—3150 |
2450—3300 |
2450—3300 |
Энергетический КПД реактора по газу, % |
65 |
68 |
71 |
75 |
75 |
Таблица 3. Сравнение геометрических параметров газификаторов
Table 3. Comparison of geometric parameters of gas generators
Параметры |
100 кВт |
300 кВт |
500 кВт |
Высота × диаметр газификатора |
3м × 0,6 м |
4м × 0,7 м |
5м × 0,9 м |
Занимаемая площадь вспомогательного оборудования (дробилка, пресс, сушилка, транспортёр загрузки) |
25 м2 |
45 м2 |
90 м2 |
Занимаемая площадь для газотурбинной установки, электрогенератора, пульта управления |
30 м2 |
60 м2 |
120 м2 |
Итого занимаемая площадь |
55 м2 |
105 м2 |
210 м2 |
Основным узлом газогенераторной установки является фурменный пояс. В области фурменного пояса твёрдое топливо разлагается на газообразные компоненты. Материал этого компонента обеспечивает эксплуатацию системы в самых сложных тепловых условиях. По этой причине изготовления можно использовать металлокерамическую конструкцию фурменного пояса. Это обеспечит повышение рабочей температуры и снижение доли вредных веществ, выходящих в атмосферу.
Вводя катализаторы в компоненты материала фурменного пояса, также дополнительно можно увеличить долю водорода в газовом продукте. Во время работы газогенератора диоксины не попадают в атмосферу, т. к. при температуре 1200 °C они полностью разлагаются на фурменном поясе. Это система так называемой «чистой трубы», продуктами которой являются только результат окисления водорода: вода и её производные. В итоге состояние воздуха в районе эксплуатации системы значительно улучшится, т. е. процесс газогенерации является уникальным ещё и с точки зрения экологии [20].
Система газификации биомассы состоит из предварительной обработки биомассы, газификации биомассы, газоочистки и подача горючей газовой смеси в дизельный или газотурбинный двигатель для выработки электроэнергии, как показано на рисунке 5. Продуктовый газ также можно сжигать в котле для производства пара, который может работать как паровая турбина для производства электроэнергии. Неочищенная газовая смесь, выходящая из газогенератора, часто загрязнена смолой, твёрдыми частицами, аммиаком и пр. Самая сложная задача — очистить газ в соответствии со строгими требованиями работы газовой турбины и двигателя. Общая эффективность производства электроэнергии с помощью паровой турбины составляет менее 20 %, в то время как для газовой турбины (двигателя внутреннего сгорания) она может достигать около 50 %.
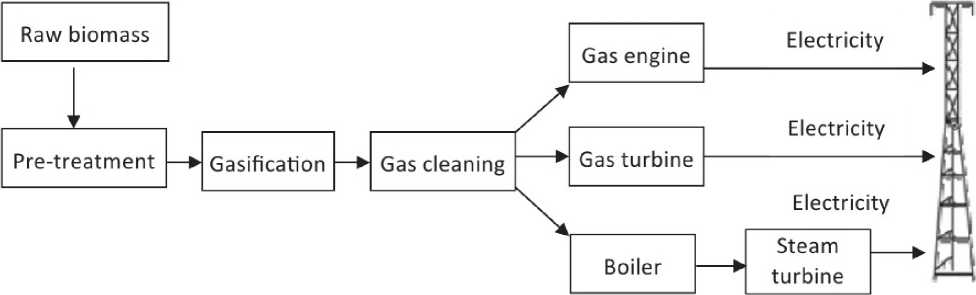
Рисунок 5. Схема получения электрической энергии
-
Fi gure 5. The scheme of power generation
В теории процесс взаимодействия реагентов достигнет равновесия при бесконечной продолжительности. Модель, описывающая выход и состав продукта при этих условиях, называется моделью равновесия. Но в такой модели характер реакции не учитывает геометрических параметров газификатора. На практике реагенту доступно только конечное время, чтобы прореагировать. Для практического применения необходимо использовать кинетическую модель прогнозирования газового продукта. Кинетическая модель прогресс, происходящего в реакторе, позволяет определять состав продукта в различных положениях в реакторе. Она учитывает как геометрию реактора, так и его аэро- и гидродинамику. Если аэро-и гидродинамика реактора хорошо известна, то модель Эйлера обеспечивает очень точное предсказание температуры и выход газа. Относительно новый инструмент моделирования — использовать для моделирования газификации нейронную сеть. В этом случае нейронная сеть самообучается на основе экспериментальных данных.
Как было отмечено выше, основными потребителями электроэнергии в условиях лесных терминалов являются мобильные лесопильные станки, производящие пиломатериалы, и мобильные рубительные машины, перерабатывающие на топливную щепу порубочные остатки, тонкомер, некондиционную древесину и отходы лесопиления. Данная щепа может использоваться и для газогенераторов.
На основе данных сайтов компаний-производителей такого вида оборудования была сделана представительная выборка их технических характеристик. В результате статистической обработки данных выборок получены следующие результаты. Мощность электропривода ленточных пильных станков тесно коррелирует с максимальным диаметром распиливаемых брёвен (коэффициент линейной корреляции r = 0,71), графически связь представлена на рисунке 6.
Энергопотребление вала отбора мощности ориентировочно в 1,0—1,5 раза выше, чем у электропривода; энергопотребление двигателя внутреннего сгорания ориентировочно в 1,5 раза выше, чем у электропривода.
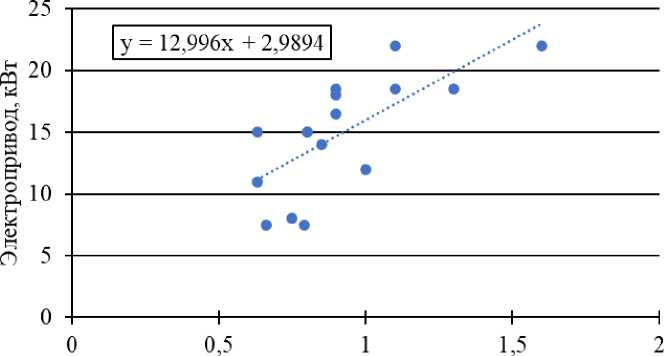
Максимальный диаметр распиливаемых бревен, м
Рисунок 6. Зависимость мощности электропривода лесопильных станков от максимального диаметра распиливаемых брёвен
-
Fi gure 6. Dependence of the sawmill electric drive power on the maximum diameter of processed logs
Площадь сечения загрузочного патрона мобильных рубительных машин связана с максимальным диаметром перерабатываемого сырья (рисунок 7).
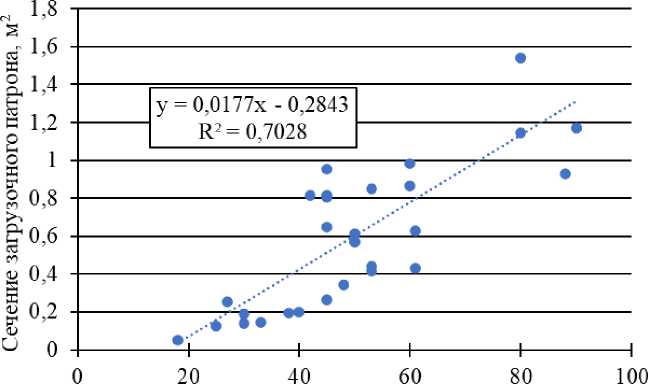
Максимальный диаметр перерабатываемого сырья, см
Рисунок 7. Зависимость площади сечения загрузочного патрона мобильных рубительных машин от максимального диаметра перерабатываемого сырья
-
Fi gure 7. Dependence of the cross-sectional area of the loading cartridge of mobile chopping machines on the maximum diameter of the processed raw materials
Потребляемая мощность мобильных рубительных машин связана с максимальным диаметром перерабатываемого сырья (рисунок 8).
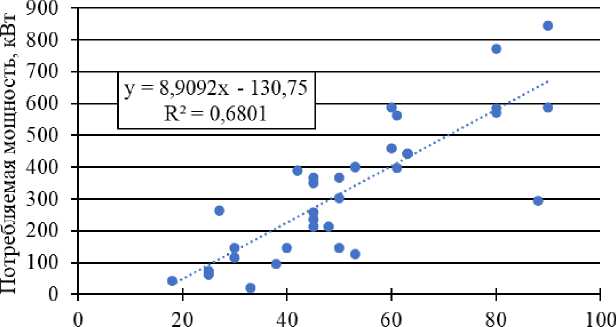
Максимальный диаметр перерабатываемого сырья, см
Рисунок 8. Зависимость мощности электропривода мобильных рубительных машин от максимального диаметра перерабатываемого сырья
-
Fi gure 8. Dependence of the electric drive power of mobile chopping machines on the maximum diameter of the processed raw materials
-
4. Обсуждение и заключение
Газификацию биомассы можно рассматривать как одну из конкурентных стратегий по эффективному способу переработки древесной биомассы в топливный газ для комбинированного производства тепла и электроэнергии, необходимых для энергоснабжения лесных терминалов. Чтобы преодолеть логистические проблемы и удовлетворить потребности в электроэнергии в удалённых районах, распределённая выработка электроэнергии с изобилием газификации древесной биомассы могла бы дать значительный экономический эффект. Для уменьшения технических проблем необходимо использовать газогенераторы небольшой мощности (1—10 МВт). Как показывают данные статистической обработки технических характеристик мобильных лесопильных станков и рубительных машин (рисунки 6 и 8), такой мощности вполне хватит для энергообеспечения основных потребителей на лесных терминалах. Важно предусмотреть использование катализатора для газоочистки, чтобы обеспечить необходимое качество газа для газовых двигателей.
Список литературы Анализ газогенерирующих систем для автономного энергоснабжения лесных терминалов
- Математическая модель выбора системы машин для создания и эксплуатации лесных плантаций / О. Б. Марков, Р. В. Воронов, А. Б. Давтян, И. В. Григорьев, Г. А. Калита // Деревообрабатывающая промышленность. 2021. № 1. С. 16—26.
- Политика социалистической Республики Вьетнам по развитию сельских районов / В. И. Григорьев, В. Л. Нуген, Р. М. Низамов, И. В. Григорьев // Вестник Казанского государственного аграрного университета. 2021. Т. 16, № 1 (61). С. 112—118.
- Григорьев И. В., Григорьева О. И., Вернер Н. Н. Системы машин для создания и эксплуатации лесных плантаций // Актуальные направления научных исследований XXI века: теория и практика. 2017. Т. 5, № 5 (31). С. 438—443.
- Математическая модель модульного принципа подбора системы машин для создания и эксплуатации лесных плантаций / Р. В. Воронов, О. Б. Марков, И. В. Григорьев, А. Б. Давтян // Известия высших учебных заведений. Лесной журнал. 2019. № 5 (371). С. 125—134.
- Григорьев В. И. Лесные плантации в Азиатско-Тихоокеанском регионе // Наука и инновации: векторы развития. Материалы Междунар. научно-практич. конф. молодых учёных: Сб. науч. ст.: В 2 кн. Барнаул, 2018. С. 75—78.
- Технологическая интеграция лесопромышленных предприятий / А. А. Тамби, И. В. Григорьев, А. Б. Давтян, А. В. Помигуев, О. Н. Калита, В. И. Григорьев // Деревообрабатывающая промышленность. 2021. № 1. С. 26—37.
- Improving the quality of sorting wood chips by scanning and machine vision technology / I. Grigorev, A. Shadrin, S. Katkov, V. Borisov, N. Kaznacheeva, D. Levushkin, V. Druzyanova, I. Gnatovskaya, R. Diev, D. Akinin // Journal of Forest Science. 2021. Vol. 67, no 5. P. 212—218.
- Improving the efficiency of wood chipping operations / I. Grigorev, A. Shadrin, N. Kostyukevich, D. Levushkin, V. Borisov, R. Diev, A. Voronova // INMATEH — Agricultural Engineering. 2020. Vol. 61, no 2. P. 217—224.
- Григорьев И. В. Технологические процессы лесосечных работ с углублённой обработкой древесины // Февральские чтения: Сб. материалов научно-практич. конф. профессорско-преподавательского состава Сыктывкарского лесного института по итогам научно-исследовательской работы в 2015 году. Сыктывкар, 2016. С. 121—126.
- Развитие циркулярной экономики в России: рынок биотоплива / А. А. Тамби, С. С. Морковина, И. В. Григорьев, В. И. Григорьев // Лесотехнический журнал. 2019. Т. 9, № 4 (36). С. 173—185.
- Тамби А. А., Григорьев И. В., Куницкая О. А. Обоснование необходимости внедрения процессов промышленного лесопиления в структуру лесозаготовительной отрасли // Известия высших учебных заведений. Лесной журнал. 2017. № 6 (360). С. 76—88.
- Григорьев И. В., Григорьева О. И., Куницкая О. А. Переработка древесины на лесосеке: перспективы развития // Энергия: экономика, техника, экология. 2017. № 2. С. 27—33.
- Перспективные направления развития технологических процессов лесосечных работ / И. В. Григорьев, О. И. Григорьева, А. И. Никифорова, В. М. Глуховский // Труды БГТУ. № 2: Лесная и деревообрабатывающая промышленность. 2016. № 2 (184). С. 109—116.
- Технология получения воды в лесу при помощи иглофильтров / О. И. Григорьева, О. И. Гринько, А. Б. Давтян, И. В. Григорьев // Повышение эффективности управления устойчивым развитием лесопромышленного комплекса: Материалы Всерос. науч. конф., посвящённой 90-летию Воронежского государственного лесотехнического университета им. Г. Ф. Морозова / [Редколлегия: Е. А. Яковлева и др.]. Воронеж, 2020. С. 444—449.
- Asadullah M. Barriers of commercial power generation using biomass gasification gas: A review // Renewable& Sustainable Energy Reviews. 2014. Vol. 29. P. 201—215.
- Gas Technology Institute campus generating on-site power // Power Engineering. 2003. Vol. 107, no 1. P. 50—50.
- Molino A., Chianese S., Musmarra D. Biomass gasification technology: The state of the art overview // Journal of Energy Chemistry. 2016. Vol. 25, no 1. P. 10—25.
- Panwar N. L., Kaushik S. C., Kothari S. Role of renewable energy sources in environmental protection: A review // Renewable & Sustainable Energy Reviews. 2011. Vol. 15, no 3. P. 1513—1524.
- Springmann H. High pressure gasification of coal using nitrogen dilution of waste gas from steam generator // Book High pressure gasification of coal using nitrogen dilution of waste gas from steam generator. EditorGoogle Patents, 1977.
- Frewer H., Muller R., Schiffers U. Gas turbine and steam power-generating plant with integrated coal gasification plant // Book Gas turbine and steam power-generating plant with integrated coal gasification plant. EditorGoogle Patents, 1986.