Анализ теплофизических свойств полимеров с целью выбора оптимального композиционного материала теплозащитного покрытия летательного аппарата
Автор: Койтов Станислав Анатольевич, Мельников Владимир Николаевич
Рубрика: Контроль и испытания
Статья в выпуске: 12 (271), 2012 года.
Бесплатный доступ
Приводятся итоги исследований композиционных материалов на термогравиметрическом анализаторе и выбор наиболее эффективного теплозащитного покрытия, способного решить проблему защиты металлического корпуса летательного аппарата от высокотемпературного нагрева, возникающего в процессе движения в плотных слоях атмосферы.
Теплозащитный материал, испытания материалов, полимеры
Короткий адрес: https://sciup.org/147151551
IDR: 147151551
Текст научной статьи Анализ теплофизических свойств полимеров с целью выбора оптимального композиционного материала теплозащитного покрытия летательного аппарата
В результате увеличения требований к срокам эксплуатации ракет до 15 лет стала актуальной задача по созданию теплозащитного материала, отвечающего поставленным условиям. В качестве альтернатив хорошо зарекомендовавшего себя теплозащитного покрытия (ТЗП) ТЗМКТ-8 выступили материалы ТЗМКТ-8В-ТЭАТ и ТЗМКТ-8В-МФД, обладающие высокими эксплуатационными характеристиками. Ранее проведенные физико-механические исследования этих материалов показали удовлетворительные результаты. Но теплофизические свойства были изучены только теоретически путем математического вычисления теплоемкости и теплопроводности через определенную на приборе ИТА-4 тепловую активность. Для выбора оптимального композиционного материала требовалось провести практическое изучение свойств теплозащитных материалов ТЗМКТ-8В-ТЭАТ и ТЗМКТ-8В-МФД на термогравиметрическом анализаторе TGA/DSC1 под воздействием высоких температур. Композит ТЗМКТ-8В-МФД создан на основе нового эпоксидного компаунда и армирующего кремнеземного наполнителя.
Испытания образцов материалов в виде стружки проводили в диапазоне температур от 30 до 1500 ° С со скоростями нагрева 10, 150 ° С/мин и скоростью расхода газа 100 мл/мин. Для испытаний материалов использовался алюмосиликатный тигель 70 мкл. Все испытания проводились в среде воздуха.
Количественная оценка потери массы образцом в мг и % в процессе испытаний производилась по интегральной термогравиметрической кривой (ТГА), температурный диапазон деструкции материалов определялся с помощью дифференциальных термогравиметрических кривых (ДТГ), так как на ДТГ можно более достоверно определить начало и конец ступеней разложения материала. Пик на кривой ДТГ означает максимальную скорость разложения материала на конкретной ступени процесса термической деструкции материала. Согласно литературным источникам ступени (начало, конец) процесса деструкции материала оценивают по разным критериям. Это может быть точка начала отклонения кривой от прямолинейного участка на ТГА (или ДТГ)
или точка пересечения касательных к точке перегиба на ТГА. При этом полученные кривые для всех образцов должны оцениваться по одному и тому же критерию. Определение точки начала процесса разложения материала часто является субъективным показателем. В данных исследованиях начало процесса разложения материала оценивалось по точке начала отклонения кривой ТГА от прямолинейного участка. Температура пика – это менее субъективная характеристика. Этот показатель указывается в столбцах оценки каждой ступени превращения материала на термограммах.
Термограммы процессов деструкции материала ТЗМКТ-8В-ТЭАТ при температурах до 1500 °С и скоростях нагрева образца 10 и 150 ° С/мин представлены на рис. 1. Как видно (рис. 1, а), процесс деструкции материала двухступенчатый. При скорости нагрева образца материала 10 °С/мин в интервале температур от 30 до ~200 °С происходит постепенное удаление из образца материала сорбированной образцом атмосферной влаги, содержащихся в образце непрореагировавших компонентов связующего и легколетучих фракций композита материала. С увеличением температуры нагрева образца происходит термическое разложение материала с распадом химических связей и образованием низкомолекулярных продуктов деструкции материала.
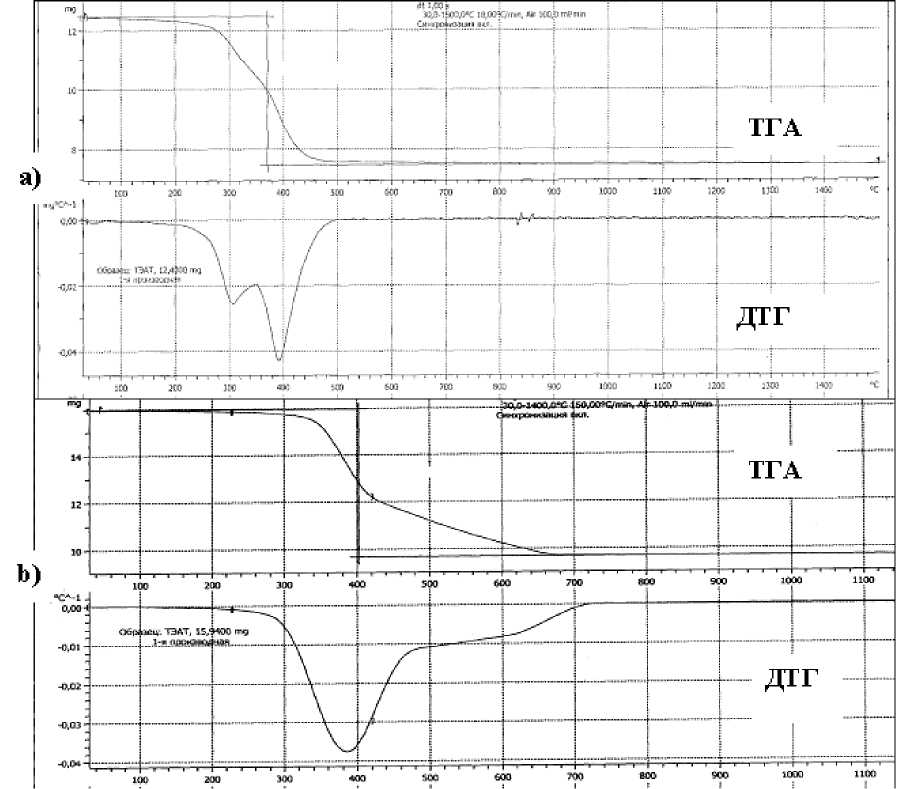
Рис. 1. Кривые ТГА и ДТГ для образцов из материала ТЗМКТ-8В-ТЭАТ: a – скорость нагрева 10 °С/мин; b – скорость нагрева 150 °С/мин
Согласно кривой ТГА потеря массы образцом происходит в интервале температур от ~220 до ~500 °С. Максимальная скорость разложения образца материала, как видно по пику на кривой ДТГ, происходит при температуре ~395 °С. Процесс деструкции материала практически заканчивается при температуре ~500 °С, при этом суммарные потери массы образца ТЗМКТ-8В-ТЭАТ при нагреве составили ~40 %, или 4,99 мг, от навески образца материала массой 12,43 мг.
При скорости нагрева образца материала ТЗМКТ-8В-ТЭАТ 150 °С/мин (рис. 1, b) процесс термической деструкции материала смещается в сторону более высоких температур и его начало зафиксировано при температуре ~290 °С, пик максимальной скорости потери массы образцом – при температуре ~390 °С, процесс деструкции композита материала заканчивается при температуре ~720 °С, потери массы образцом при этом составили ~40,1 % (6,39 мг) от навески материала образца массой 15,94 мг.
Термограммы процессов деструкции материала ТЗМКТ-8В-МФД при температурах до ~1500 °С представлены на рис. 2. Как видно по кривой ДТГ (рис. 2, а), процесс термической деструкции материала ТЗМКТ-8В-МФД при скорости нагрева образца материала 10 °С/мин в интервале температур от 30 до ~1500 °С двухступенчатый. На первой ступени термодеструкции материала происходит удаление сорбированной материалом атмосферной влаги и непрореагировавших компонентов композита, затем постепенное удаление легколетучей фракции из материала и при температуре ~245 °С начинается процесс интенсивного разложения материала с максимумом при температуре ~295 °С, при этом потери массы образцом составили ~17 % (1,78 мг) от навески материала. На второй ступени деструкции материала в интервале температур от ~380 до ~620 °С происходит дальнейшее разложение материала с формированием коксового остатка (максимум пика при температуре ~510 °С) и практически заканчивается при температуре ~640 °С, суммарная потеря массы образцом при этом составила ~35 % (3,64 мг) от исходной массы образца 10,58 мг.
При скорости нагрева образца ТЗМКТ-8В-МФД 150 °С/мин (рис. 2, b) процесс разложения материала двухступенчатый и смещается в сторону более высоких температур. Так, первая ступень разложения материала заканчивается при температуре ~460 °С с максимумом при температуре ~370 °С и потерей массы ~20 % (2,42 мг) от навески материала. На второй ступени деструкции материала в интервале температур от ~460 до ~750 °С происходит дальнейшее разложение материала с формированием коксового остатка (максимум скорости потери массы при температуре ~580 °С). Процесс разложения материала практически заканчивается при температуре ~780 °С, суммарная потеря массы образцом составила ~35 % (4,16 мг) от исходной массы образца 11,92 мг.
Анализ сравнения кинетических параметров материалов ТЗМКТ-8В-ТЭАТ и ТЗМКТ-8В-МФД на термогравиметрическом анализаторе TGA/DSC1 позволяет заключить, что термическая деструкция материала ТЗМКТ-8В-МФД происходит в более широком температурном диапазоне, чем разложение материала ТЗМКТ-8В-ТЭАТ, и, следовательно, выделение газообразных продуктов материала ТЗМКТ-8В-МФД происходит в более длительном интервале времени, что в условиях работы материала в составе изделия будет определяющим фактором значительного уноса тепла с поверхности набегающим тепловым потоком при полете в плотных слоях атмосферы.
Сравнение кривых ДТГ показало, что потеря массы образца ТЗМКТ-8В-МФД происходит с меньшей скоростью и приводит к большему количеству остаточного кокса материала ТЗМКТ-8В-МФД в отличие от ТЗМКТ-8В-ТЭАТ.
Можно заключить, что склонность к коксообразованию и выход коксового остатка у ТЗМКТ-8В-МФД выше, чем у ТЗМКТ-8В-ТЭАТ. Из практических и теоретических исследований известно, что помимо поглощения тепла в процессах химического разложения и физических превращений, таких как испарение, плавление, особенно важными являются потери тепла на излучение с обуглившейся поверхности выгоревшего материала. В связи с этим образование большего количества механически устойчивого обуглившегося слоя является одним из важных критериев определяющих выбор абляционных теплозащитных материалов.
Из анализа кривых, снятых при скоростях нагревания ~10 и 150 °С/мин, видно, что термические эффекты обоих материалов, выраженные при малых скоростях нагревания, изменяют свое поведение при высоких скоростях и практически сливаются в единый тепловой эффект. Температуры диапазона начала и окончания основной фазы потери массы при высоких темпах нагрева смещаются в область более высоких температур по сравнению с опытами при скоростях нагревания образца ~10 °С/мин. Термическая деструкция полимеров при низкой скорости нагрева может трактоваться как своеобразный процесс физико-химической релаксации, а смещение температурно-временных характеристик при высоких скоростях нагрева в сторону высоких температур объясняется ограничением подвижности релаксирующих элементов (элементов молекулярной и надмолекулярной структуры).
Ранее было показано [1], что при темпах нагрева образцов материала ТЗМКТ-8, изготовленных пропиткой под давлением и имеющих у ~1,65 г/см3, В ~2 %, С ~36 %, более 300 °С/мин, все пики на кривой ДТГ сливаются в один. Характер протекания термической деструкции для материалов ТЗМКТ-8 и ТЗМКТ-8В одинаков. Было показано, что при термической деструкции материала ТЗМКТ-8 затрачивается 2125,72 Дж/г. При этом кажущаяся (эффективная) энергия активации процесса равняется при скорости нагревания 10 °С/мин 135,65 кДж/моль, порядок реакции -0,93, а при скорости нагрева 470 °С/мин - 8,75 кДж/моль, порядок реакции - 0,15 [2]. Определенные кинетические параметры процессов термической деструкции исследуемых материалов: эффективная энергия активации и порядок процесса показывают, что при темпах нагрева образцов 300-500 °С/мин кинетические параметры резко снижаются по сравнению с кинетическими параметрами, определенными при темпах нагрева образцов ~10 °С/мин. Это можно объяснить снижением активационного барьера пиролиза материалов и повышением роли физических процессов, таких как диффузия, испарение, сублимация и т. п. [2].
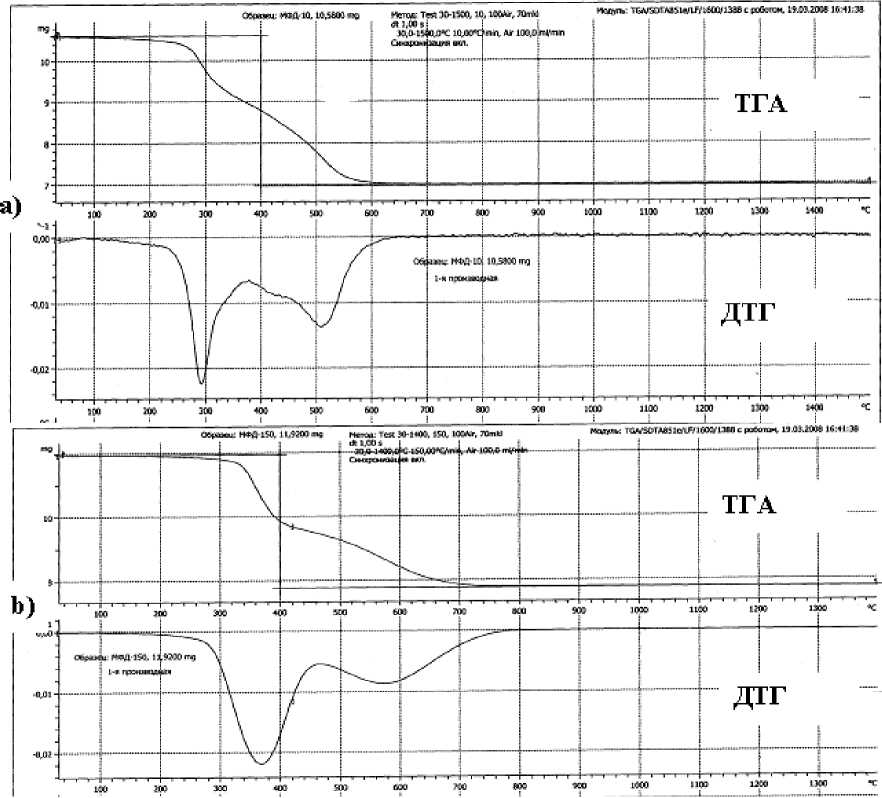
Рис. 2. Кривые ТГА и ДТГ для образцов из материала ТЗМКТ-8В-МФД: a - скорость нагрева 10°С/мин; b - скорость нагрева 150°С/мин
Изучение кинетики термического превращения подтвердило, что материал ТЗМКТ-8В-МВД наиболее эффективен в тепловых потоках и его можно использовать в качестве тепловой защиты, аналогичной материалу ТЗМКТ-8. Хотя методы ТГА, ДТГ, ДТА и ДСК позволяют получить обширную информацию о реакциях термического разложения в материалах, их нужно рассматривать только как предварительные, поскольку они не содержат никаких прямых доказательств, касающихся природы протекающих химических реакций. В связи с этим необходимо проведение подробного анализа материалов с использованием одного или нескольких аналитических методов, как, например, ИК-спектроскопия, хроматография.
Для подтверждения работоспособности материала ТЗМКТ-8В-МВД, нанесенного методом вакуумного формования, проведены натурные испытания материала ТЗМКТ-8В при работе изделия в течение ~6 мин. Результаты удовлетворительные.
Список литературы Анализ теплофизических свойств полимеров с целью выбора оптимального композиционного материала теплозащитного покрытия летательного аппарата
- Мельников, В.Н. Исследование термической деструкции теплозащитных материалов/В.Н. Мельников//Механика и процессы управления: тр. XXXVI Урал. семинара. -Екатеринбург: УрО РАН, 2006. -Т. 2. -С. 123-128.
- Мельников, В.Н. Исследование термической деструкции теплозащитных материалов/В.Н. Мельников; ОАО «ОКБ „Новатор»//Тез. докл. 5-й Междунар. конф. «Авиация и космонавтика -2006», 23-26 окт. -М.: МАИ, 2006. -С. 77-82.