Автоматизация технологических объектов цеха добычи нефти и газа
Автор: Зеленский Владимир Анатольевич, Коннов Вадим Петрович
Журнал: Известия Самарского научного центра Российской академии наук @izvestiya-ssc
Рубрика: Современные наукоемкие инновационные технологии
Статья в выпуске: 4-3 т.16, 2014 года.
Бесплатный доступ
Рассматриваются вопросы автоматизации технологических объектов цехов добычи нефти и газа ЦДНГ-4 ОАО «Оренбургнефть», обеспечивающей их работу в нормальных условиях эксплуатации без постоянного присутствия обслуживающего персонала непосредственно у технологических объектов управления, а также аварийную и технологическую сигнализацию. Пуск технологического оборудования и вывод его на режим, в том числе после ликвидации аварий, осуществляется вручную. Система реализует информационную технологию в виде определённой последовательности информационно связанных функций, задач или процедур, выполняемых в автоматизированном режиме. Система обеспечивает оперативный контроль технологических параметров объектов ЦДНГ-4, включая сбор, накопление, обработку и отображение информации о ходе технологического процесса, поддержание оптимальных технологических режимов, аналитический контроль, предупредительную и аварийную сигнализацию.
Автоматизация, технологический объект, сигнализация, контроль, технологический параметр
Короткий адрес: https://sciup.org/148203247
IDR: 148203247
Текст научной статьи Автоматизация технологических объектов цеха добычи нефти и газа
Система телемеханики ЦДНГ-4 «Оренбургнефть» обеспечивает централизованный контроль за работой технологического оборудования, формирование и печать отчётных документов. Объектами автоматизации в системе являются: блоки напорной гребенки (БНГ) в количестве 3 штук, водораспределительные пункты (ВРП) в количестве 8 штук, скважины нагнетательные в количестве 74 штук и скважины водозаборные в количестве 35 штук. На перечисленных объектах производятся следующие технологические операции: измерение линейного давления, измерение расхода, контроль открытия двери блока механики и автоматики (БМА), контроль открытия двери шкафа телемеханики, измерение температуры в БМА, измерение температуры в шкафу телемеханики, извещение о пожаре в БМА, управление вентиляцией БМА, управление обогревом БМА. Взаимное расположение БМА и блока напорной гребёнки, а также структура блока напорной гребёнки 1 показаны на рис. 1. Взаимное расположение ВРП-2 и блока напорной гребёнки, а также структура блока напорной гребёнки, показаны на рис. 2.
Для контроля технологических процессов на объектах ЦДНГ-4 предусмотрено аттоматизи-
Коннов Вадим Петрович, аспирант рованное рабочее место (АРМ) для диспетчера, устанавливаемое на блочной кустовой насосной станции БКНС-1, БКНС-2 Росташинского месторождения и БКНС Зайкинского месторождения. Для обслуживания системы, выполнения работ по конфигурированию АРМ «Диспетчер» имеет инженерные функции. Изменения в конфигурацию, например, отключение системы контроля технологических параметров, изменение заданий и настроечных параметров контроллеров и т.д., вносит сменный инженер (начальник смены), относящийся к технологическому персоналу. Для обеспечения нормального функционирования системы и предотвращения несанкционированного доступа в ход технологического процесса предусмотрена защита информации. Система обеспечивает оперативный контроль за состоянием объектов управления, расчёт технологических параметров и показателей, архивирование информации, предупредительную сигнализацию отклонений технологических параметров от нормы, формирование и печать отчётных документов о работе технологических объектов ЦДНГ-4 ОАО «Оренбургнефть» [1].
Система обеспечивает решение следующих задач:
-
- сбор информации об измеряемых параметрах всего фонда нагнетательных скважин, таких как давление и расход;
-
- учёт закачки по объектам разработки и выявление дисбаланса отбор-закачка в режиме реального времени;
-
- выдачу сообщений об авариях;
-
- подготовку и передачу информации в системы управления разработкой месторождений и оперативного управления предприятием.
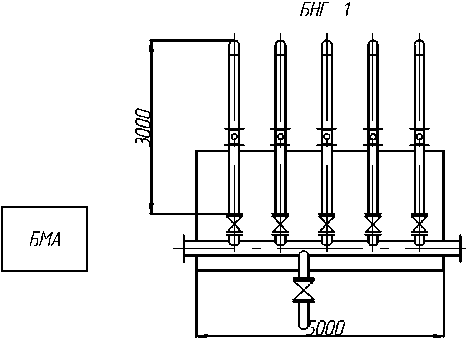
Рис. 1. Взаимное расположение БМА и БНГ-1 и структура блока напорной гребёнки
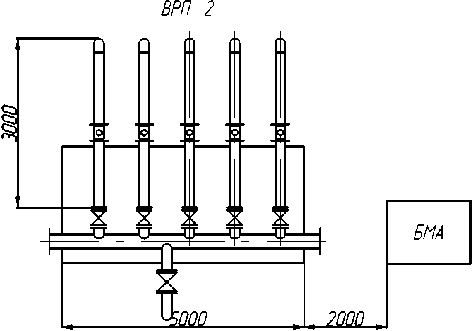
Рис. 2. Взаимное расположение БМА и водораспределительного пункта
Комплекс технических средств организован в виде функционально распределённой системы, представляющей собой распределённую вычислительную сеть. Абонентами распределённой сети являются:
-
- существующий сервер базы данных;
-
- автоматизированное рабочее место диспетчера (АРМ «Диспетчер»);
-
- шкафы узлового контроллера сбора данных (УКСД), оснащённые Historian-сервером, для хранения технологических параметров;
-
- контроллеры телемеханики КТС.5-02, КТС.8-04.
Система построена по иерархическому многоуровневому принципу (рис. 3). На каждом уровне имеются аппаратно-программные средства, взаимоувязанные для обеспечения сквозного обмена информацией между верхним (1), средним (2) и нижним (3) уровнем.
1 |
Интеграция и оптимизация |
Моделирующие и интегрирующие информационные системы реального режима времени |
2 |
Дистанционное диспетчерское управление |
Удалённое управление через АСУ ТП |
3 |
Базовый процесс управления |
Сбор данных с автономных датчиков |
Рис. 3. Уровни иерархии системы автоматизации
Система телемеханики работает в двух режимах: автоматическом и автоматизированном. В автоматическом режиме выполняются: сбор и первичная обработка информации с датчиков, защита технологического процесса и оборудования, формирование отчётных документов, формирование и хранение базы данных. В автоматизированном режиме выполняются: отображение оперативной и архивной информации о ходе технологического процесса и состоянии оборудования, вывод отчётных документов на печать. Структура комплекса технических средств (КТС) АСУ ТП соответствует магистрально-модульному принципу построения с сетевой организацией обмена информацией между устройствами и имеет трёхуровневую структуру [2].
К нижнему уровню системы автоматизации относятся: датчики расхода; датчики давления. К среднему уровню системы автоматизации относятся: контроллеры, historian-серверы, коммутаторы, радиомодемы, станции ШПД, станции РРЛ, барьеры искрозащиты, источники питания. К верхнему уровню системы автоматизации относятся: сервер хранения базы данных, АРМ оператора и специалистов. Для системы автоматизации используются датчики и приборы, серийно изготавливаемые отечественными и зарубежными компаниями и имеющие все необходимые разрешения и сертификаты для применения в системах управления технологическим процессом на предприятиях нефтегазового комплекса [3]. При использовании средства измерения во взрывоопасной зоне используется оборудование взрывозащищённого исполнения. Все датчики и приборы, монтируемые непосредственно на технологических площадках, имеют соответствующее исполнение по условиям окружающей среды. Средства автоматизации в части устойчивости к воздействию климатических факторов внешней среды по исполнению для различных климатических районов и категорий размещения соответствуют требованиям ГОСТ 15150-69. Все приборы, эксплуатирующиеся на открытом воздухе, имеют исполнение не ниже условий эксплуатации и сохраняют работоспособность при температурах от -40°С до +40°С.
Аппаратура нижнего уровня размещается на технологическом оборудовании и в аппаратных шкафах, устанавливаемых в местах измерения и контроля технологических параметров. Установка датчиков, прокладка электрической проводки и кабельной эстакады уточняется при монтаже. Присоединение к приборам внешних трубных проводок должно осуществляться в соответствии с требованиями ГОСТ 25164-96 и ГОСТ 25165-82, а электрических проводок – в соответствии с требованиями ГОСТ 10434-82, ГОСТ 25154-82, ГОСТ 19104-88, ТУ16-526.492-81. Для контроля и сигнализации давления применяются малогабаритные датчики давления Метран-55-Ex-ДИ со следующими характеристиками: максимальное давление – 250 кгс/см2; предельные значения температур: -42...70°С; вид взрывозащиты - ЕхiaIICT5X; приведённая погрешность: 0,5. Датчики давления устанавливаются строго вертикально согласно монтажным схемам. Связь датчика с контроллером осуществляется через токовую петлю 4...20 мА с использованием барьеров искробезопасности фирмы Pepperl-Fuchs. Для контроля и сигнализации расхода применяются расходомеры ГС-СРВУ-Т-485 со следующими характеристиками: максимальный расход 25 (50, 200) м3/час (в зависимости от расхода, см. 02.55-1116.4.НФ-АК); максимальное давление 25 МПа; приведённая погрешность: 0,5. В состав счётчиков-расходомеров входят: преобразователь расхода типа ПР-25 (ПР-50, ПР-200); счётчик расхода ГС-СРВУ-Т-485. Обмен информации с контроллером А812-01 осуществляется с помощью интерфейса RS485 по протоколу ModBus RTU с использованием барьеров искробезопасности фирмы Pepperl-Fuchs. Преобразователь расхода устанавливается на трубопроводе с помощью фланцевого соединения согласно монтажным схемам. Для контроля температуры внутри БМА устанавливается датчик температуры ATM2-I. В БМА предусмотрен конвектор для поддержания температуры не ниже 10°С в холодное время года. Управление вентиляцией осуществляется от шкафа УКСД.
Структура системы среднего уровня включает шкафы системы телемеханизации, обеспечивающие контроль технологических параметров в составе системы. Вся оперативная информация от датчиков и других средств автоматизации на технологических площадках поступает в шкафы системы телемеханизации. В состав оборудования среднего уровня системы входит: шкаф контроллера телемеханики, шкаф коммуникационный, шкафы связи. В качестве технологического контроллера применяется контроллер КСБ1 фирмы «Интротест» и Historian-сервер AdvantiX ER-400 фирмы Fastwel. В качестве вспомогательного контрол- лера используется А812-01 фирмы «Интротест», установленный в шкафу. Информационный обмен между контроллером А812-01 и Historian-сервером осуществляться с помощью интерфейса RS-485 и Ethernet c использованием преобразователя интерфейса Moxa NPort IA 5450A.
Контроллер обеспечивает:
-
- сбор информации от датчиков, устанавливаемых по месту;
-
- обработку и передачу информации о состоянии объектов на верхний уровень системы автоматизации.
Historian-сервер обеспечивает:
-
- сбор информации от датчиков, устанавливаемых по месту;
-
- обработку и хранение полученной информации;
-
- передачу информации о состоянии объектов на верхний уровень системы;
Система укомплектована активными искробезопасными барьерами фирмы
Pepperl+Fuchs. Конструкция шкафов телемеханики обеспечивает возможность внешних связей и взаимодействие со шкафами других систем. Вся поступающая информация собирается и хранится на главном сервере хранения базы данных.
Оборудование верхнего уровня (АРМы) располагается в помещениях АБК операторной БКНС и обеспечивает непрерывный контроль технологического процесса с визуализацией режимов работы и технологических параметров на дисплее АРМа оператора. Верхний уровень системы автоматизации обеспечивает информационный обмен между АРМ, Historian-серверами и сервером хранения базы данных. Это может осуществляться через существующую технологическую сеть ОАО «Оренбургнефть».
Ввод системы в эксплуатацию состоит из следующих этапов:
-
- проведение предварительных испытаний, выдача отчета, корректировка;
-
- проведение опытной эксплуатации;
-
- проведение приемочных испытаний;
-
- обучение производственного персонала работе с системой;
-
- сопровождение и гарантийное обслуживание системы;
-
- мониторинг технологического процесса и получение трендов измеряемых технологических параметров;
-
- формирование и печать отчетных документов;
-
- прием информации о состоянии объектов;
-
- архивацию событий;
-
- формирование базы данных.
Выводы: результатом проектной работы явилось создание системы автоматизации технологических объектов добычи нефти и газа ЦДНГ-4 ОАО «Оренбургнефть». Для нормального функционирования системы управления необходимо создание подразделения по ее обслуживанию, включающего в свой состав специалистов по техническому и программному обеспечениям.
Список литературы Автоматизация технологических объектов цеха добычи нефти и газа
- Зеленский, В.А. Выбор парадигмы, математического аппарата и инструментов моделирования технологических процессов в машиностроении и нефтегазовой промышленности/В.А. Зеленский, В.П. Коннов, А.И. Щодро//Математическое моделирование, численные методы и информационные системы: Мат-лы IV Всеросс. научно-практ. конф. с меж. участием. -Самара: Изд-во СМИУ, 2012. С. 113-120.
- Зеленский, В.А. Моделирование технологических процессов с помощью сетей Петри/В.А. Зеленский, В.П. Коннов, А.И. Щодро//Актуальные проблемы радиоэлектроники и телекоммуникаций: Мат-лы Всеросс. научно-техн. конф. -Самара: Изд-во СГАУ, 2012. С. 286-290.
- Голубятников, И.В. Системы мониторинга сложных объектов/И.В. Голубятников, В.А. Зеленский, В.Е. Шатерников. -М.: Машиностроение, 2009. 172 с.