By hydrogen reduction from a-FeOOH hydroxide compound under isothermal conditions
Автор: Tien Hiep Nguyen, Nguyen Van Minh, Tang Viet Phuong, Tang Xuan Duong, Le Hong Quan
Журнал: Вестник Южно-Уральского государственного университета. Серия: Металлургия @vestnik-susu-metallurgy
Рубрика: Нанотехнологии и наноматериалы
Статья в выпуске: 1 т.21, 2021 года.
Бесплатный доступ
In this work, the process of obtaining magnetite nanopowder Fe3O4 by hydrogen reduction from α-FeOOH hydroxide compound under isothermal conditions was studied. The α-FeOOH nanopowder was prepared in advance by chemical precipitation from aqueous solutions of iron nitrate Fe(NO3)3 (10 wt. %) and alkali NaOH (10 wt. %) at room temperature, pH = 11, under the condition of continuous stirring. The hydrogen reduction process of α-FeOOH powder under isothermal conditions was carried out in a tube furnace in the temperature range from 310 to 375 °С. The study of the crystal structure and phase composition of the powder samples was performed by XRD phase analysis. The specific surface area S of the samples was measured using BET method by low-temperature nitrogen adsorption. The average particle size D of powders was calculated using the data of measuring the specific surface area S. The size and morphology characteristics of the particles were investigated by scanning and transmission electron microscopy method. The calculation of the kinetic parameters of the process of obtaining the Fe3O4 nanopowder under isothermal conditions was carried out using the Gray-Weddington model and the Arrhenius equation. It was found that the reduction process of the α-FeOOH nanopowder begins to accelerate strongly in the temperature range from 340 to 375 °С. The reduction rate constant at 375 °С is about 2 times that of the reduction at 310 °С. The value of the activation energy for the process of obtaining Fe3O4 nanopowder under isothermal conditions was ~ 36 kJ/mol, which indicates a mixed mode of limiting the kinetics of the process. It has been shown that the time-temperature regime of the reduction of the α-FeOOH hydroxide compound with holding at 340 °С for 3 h makes it possible to obtain a nanosized magnetite powder Fe3O4 with high purity at an increased rate of the process. The obtained Fe3O4 nanoparticles have a crystalline structure and generally have a polygonal or irregular shape, the size of which ranges from 30-80 nm with an average value of 65 nm, each of them being connected to several neighboring particles by isthmuses.
Kinetics, magnetite nanopowder, hydrogen reduction, isothermal conditions, reduction degree, rate constant, activation energy
Короткий адрес: https://sciup.org/147233978
IDR: 147233978 | DOI: 10.14529/met210107
Текст научной статьи By hydrogen reduction from a-FeOOH hydroxide compound under isothermal conditions
Currently, magnetite Fe3O4 nanopowders (NP) have found wide application in various fields of science, technology, and medicine [1–4]. Fe3O4 nanoparticles (NPs) functionalized with biomolecules can be used as materials for targeted drug delivery in order to recognize or treat biological systems. Due to their magnetic properties, Fe3O4 NPs are also often used in magnetic hyperthermia to destroy tumor cells, in magnetic reso- nance imaging (MRI) as contrast agents, to create actively antitoxic adsorbents in the field of nanotoxicology. In addition, dispersion, non-toxicity, and superparamagnetic properties make Fe3O4 NPs interesting for use in other fields, for example, in the manufacture of effective catalysts, biosensors, ferromagnetic liquids, as a feedstock for the synthesis of Fe NP by reduction [2, 3, 5–13].
The production of metals and oxides NP, including Fe3O4 NP, is carried out in various ways, most of which are characterized by a number of disadvantages, such as high energy consumption, reduced productivity, and environmentally uncleanness [5, 6, 9, 14]. Chemical-metallurgy method, which includes the stage of hydrogen reduction of oxygen-containing compounds, is a highly efficient method from a technology and economic point of view, because the method is quite simple in equipment, environmentally friendly and makes it possible to use industrial waste as a raw material, to regulate the dimensional characteristics of oxides and metals NPs in the course of their production [6, 15–17].
A big disadvantage of chemical-metallurgy method for producing oxides and metals NP is low productivity due to the low speed of the reduction process under conditions of holding at low temperatures. At that time, an excessive increase in the reduction temperature is not recommended because it leads to intensive processes of aggregation and sintering of NPs, respectively, to the formation of particles with a particle size outside the nanoscale range [13, 18].
Thus, the study of the kinetic characteristics of synthesizing process of Fe 3 O 4 NP in order to find a way to accelerate it while guaranteeing the required properties of the obtained products is an important scientific-practical problem.
In this regard, the aim of this work is to study the kinetics of synthesizing process of Fe 3 O 4 NP by hydrogen reduction from α-FeOOH NPs under isothermal conditions, as well as to analyze the structural and dimensional properties of the obtained magnetite nanoparticles.
Materials and methods
As materials for the preparation of Fe 3 O 4 NP was used iron hydroxide (III) α-FeOOH NP, synthesized by chemical precipitation from aqueous solutions of iron nitrate Fe(NO 3 ) 3 (10 wt. %) and alkali NaOH (10 wt. %) at room temperature, pH = 11, and continuous stirring. Getting iron hydroxide proceeds by the reaction:
Fe(NO 3 ) 3 + 3NaOH =
= FeOOН↓ + 3NaNO 3 + Н 2 О. (1)
The pH was monitored with an “Expert-001” pH meter; the measurement error was ±0.03. Using a Buchner funnel, the obtained α-FeOOH precipitate was washed until the ions of the dissolved salt were completely washed off, which was controlled by the pH of the solution over the precipitate. Then the precipitate was dried at 40 °C for 48 h, the thickness of the filling of the hydroxide paste in the plates was no more than 10 mm. The time-temperature regime of drying was determined experimentally for the complete removal of the precipitate of adsorbed water molecules from the sample while ensuring a high dispersion of α-FeOOH particles. Thereafter, the dried α-FeOOH was milled using a laboratory mill “Fritsch Pulverisette 2”. The obtained α-FeOOH powder was analyzed for structural and dispersed properties and was used for further research.
The study of the kinetics of the process of obtaining Fe 3 O 4 NP was carried out in a tubular furnace “SNOL 0.2/1250” in a hydrogen atmosphere at various temperatures. During the process, the following reaction took place:
6FeOOН + H 2 = 2Fe 3 O 4 + 4H 2 O. (2)
The hydrogen generator “CAM-1” was used as a source of hydrogen; the relative humidity of the obtained hydrogen did not exceed 1%. To prevent the ignition of the resulting powders in air, after reduction, their surface was passivated in a stream of nitrogen taken from the dewar of liquid nitrogen.
The calculation of the degree of conversion (α) (u.fr.) (the ratio of the amount of the reagent that entered the reaction to its initial amount) was carried out according to the formula:
a_ m0 - mt 6Ma-FeOOH _ m о "(3 M H2o + Mo)
= 7.6 , m m- , (3) m 0
where m 0 is the initial weight of the sample, kg; m t is the mass of the sample over time t , kg; M H O is the molar mass of water; M O is the molar mass of atomic oxygen.
The kinetics of synthesizing process of Fe 3 O 4 NP by hydrogen reduction was studied using the model of Gray–Weddington [19]. The use of this model makes it possible to determine the values of the rate constant by the formula:
k ■ t = 1 - (1 -a )1/3, (4) where k is the rate constant, s–1; t is the reaction time, s.
The calculation of the activation energy ( E a ) (J/mol) was carried out according to the experimental data obtained under isothermal conditions using the integral form of the Arrhenius equation:
ln k = - Ea- • 1 + ln A, (5) RТ where A is a constant (pre-exponential factor); T is temperature, K; R is gas constant, J/(mol·K).
The phase composit ion o f powde r sa mple s was deter mine d by X R D p ha se a naly sis on a di f fractometer “Difrey-4 01” ( R ussi a ) ( C r -K α radiation) at room temperature. T he s ize a nd shape o f t he ob ta i ne d na n opar t ic l e s we r e inv e st ig a te d on s c a nn ing a nd tr ansmissio n e lec t r on mic r o sc op e s “T ES CAN V EGA 3B ” (S EM) ( C ze c h R epubl ic) and “ LEO 912 A B OMEG A” (T EM ) ( Ger ma ny ) .
The spec i f i c su r fa c e a rea ( S ) (m2/kg) of the samples was me a sure d by the B E T me thod based on low-t e mpe r a ture nit r og e n a dso r p tion on a “ NOV A 1200e” a n a ly ze r ( US A) . T he a v e r a g e p a r t icle size o f the powders wa s c al c u la t e d f r om t he me a su r e me nt data of the S value using the formula:
D = 6 , ρ⋅ S
where ρ is the pycnome tr ic de nsi ty of th e ma t erial, kg/m3; D i s a v e r a g e par t ic l e s ize , m .
Results and discussion
The XRD and SEM results for the NP sample of the initial α-FeOOH are shown in Fig. 1.
The result of XRD (Fig. 1a) showed that the initial sample is single-phase, containing only the hydroxide α-FeOOH phase. Analysis of the SEM image (Fig. 1b) revealed that α-FeOOH NPs mainly have an acicular shape with a length of up to 200 nm. The specific surface area S of α-FeOOH NP is 39.5 m2/g, respectively, the average size D of α-FeOOH NP is 44 nm.
In order to study the kinetic characteristics of synthesizing process of Fe 3 O 4 NP under isothermal conditions, the dependences of the degree of conversion α on time t were obtained at different temperatures: 310, 325, 340, 355, 375 °С. These temperatures are in the range of intensive course of the reduction process, which was shown by the TG data in the work [18]. In Fig. 2 shows the curves of the dependence α( t ) at different temperatures.
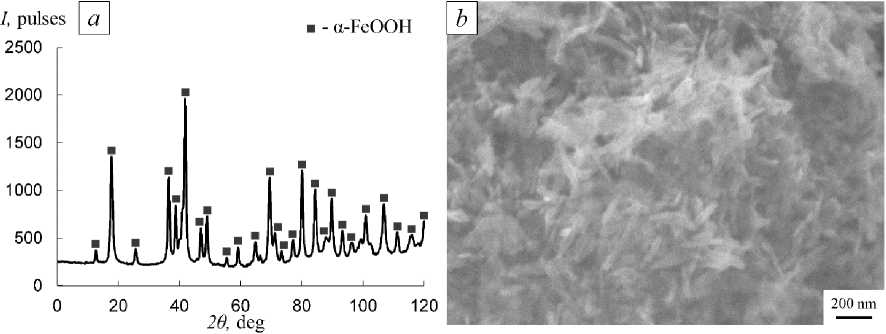
Fig. 1. XRD pattern (a) and SEM image (b) of the α-FeOOН NP sample
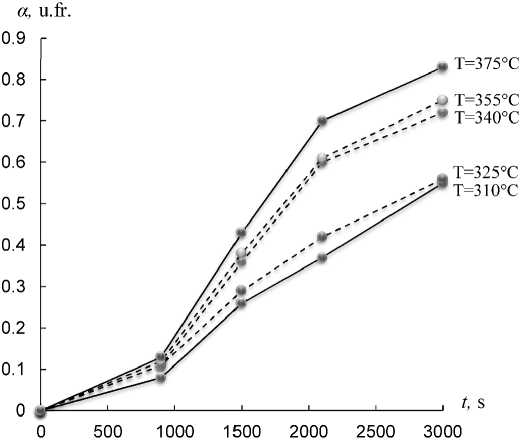
Fig. 2. Dependence α( t ) at different temperatures
I t c a n be se e n th a t the re d uc t ion p r oce ss of α-FeO OH NP be g ins to a c c eler a t e st r ong ly in the tempe r a tu r e ra ng e f rom 340 to 375 °С. At temperature Т = 375 °С for 50 min of r e du c t ion, the v a lue of α wa s 8 3% , whic h is a pp r oxi mate ly mor e tha n 1. 5 time s c ompa r e d to the c ase at 310 °С (for the same time).
The rate constant k o f synt he s izing pr oc ess of Fe 3 O 4 NP wa s ca lc ulate d us ing the Gr a y– We dd ing ton e quatio n ( 4) . T he re su lt of c alc u lating the values of k ( T ) is pre se n ted i n T abl e 1.
Acc or d ing to th e d a ta in t he t a bl e , it c an b e s e e n th a t th e ra t e cons ta n t of r e du c t ion a t 375 °С is about 2 times higher than the v a lue obt a in e d in the case of reduction at 310 °С.
To deter mine th e a ctiv a t i on e ner g y E a of synthesizing process of Fe 3 O 4 NP by hy dr og e n reduction from α-F eO O H under i sot he rma l c o n d it ions, the g r a phs of th e de pe ndenc e of t he loga ri thm of the r ate c ons ta n t on th e r ec ip r oca l tem p e r ature wer e p lot te d ( Fig . 3) a cc ording t o the Arrhenius equation (5).
The calculated E a value was ~ 36 kJ/mol. Comparison of the obtained E a value with the limiting values in the literature [20], it can be concluded that the synthesizing process of Fe 3 O 4 NP by hydrogen reduction from α-FeOOH proceeds in a mixed mode of kinetics limiting. In this case, the rate of the general process of obtaining Fe 3 O 4 NP is determined both by the rate of its own chemical reaction and by the rate of diffusion of reagents and reduction products through the powder layers; accordingly, an expedient way to accelerate the process can be both an increase in temperature and the elimination of diffusion layers by intensive mixing.
The next part of the work presents the results of study on the structural-dispersed characteristics of the reduction product of α-FeOOH NP at 340 °C, the holding time was 3 h (Fig. 4). On the one hand, this temperature is in the range of intensive acceleration of the process, and on the other hand, it is not too high, which, without
Table 1
The result of calculation of the rate constant k at different temperatures
Т reduction , °С |
310 |
325 |
340 |
355 |
375 |
|
α, u.fr. |
||||||
t , min |
15 |
0.08 |
0.11 |
0.11 |
0.12 |
0.13 |
25 |
0.26 |
0.29 |
0.36 |
0.38 |
0.43 |
|
35 |
0.37 |
0.42 |
0.60 |
0.61 |
0.70 |
|
50 |
0.55 |
0.56 |
0.72 |
0.75 |
0.83 |
|
k ·104, s–1 |
0. 6947 |
0.7669 |
1.1121 |
1.1745 |
1.4143 |
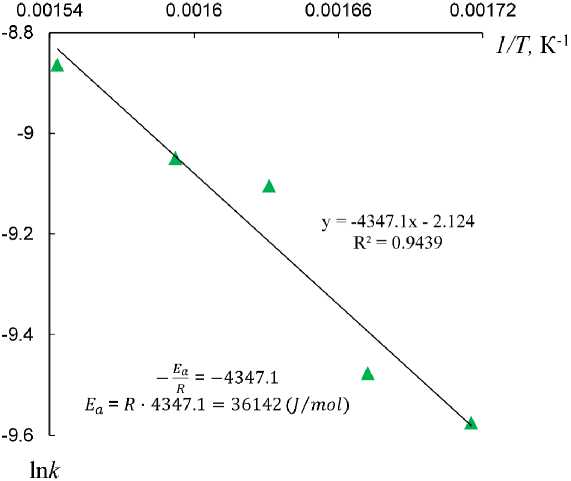
Fig. 3. Calculation of the activation energy in coordinates of the Arrhenius equation
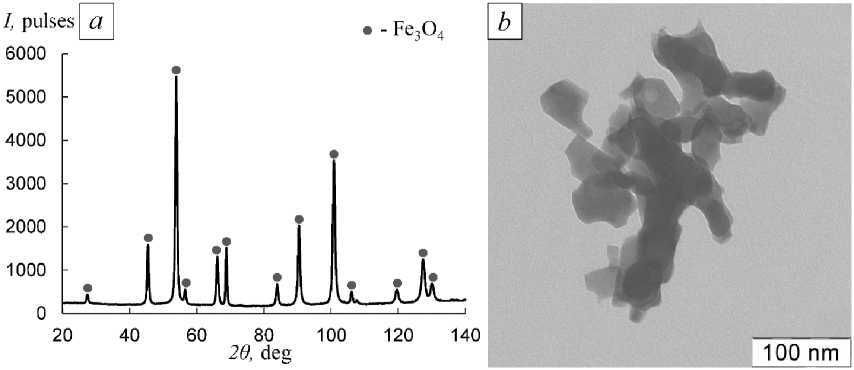
Fig. 4. XRD pattern (a) and TEM image (b) of the Fe 3 O 4 NPs obtained by hydrogen reduction from α-FeOOH NP at 340 °C, holding for 3 h
l e a d ing to in te n siv e p r oc es se s of a g g r e g a tion a n d s in te ring of the o btained m a g ne ti te NP s, ma k e s it p ossi bl e t o ob tain a reduc t ion pr od uc t wi th an in c r ea se d quali ty . Ne ve r th e l e ss, in pra cti c e, d e pe nd ing on the ta sk , i n or der to ac c eler a t e the reduction proce ss whi le e nsu r ing th e re qu ir ed p r oper t ie s o f the obt a in e d p r oducts, i t i s de s ira bl e t o var y th e r e du c t ion te mpe r ature in the c on sid e red range from 340 to 375 °С.
The XRD result (Fig. 4a ) r e v e ale d that t he composit ion o f t he s a mple unde r st udy i s single- p ha se , c ons is ting on ly of the F e 3 O 4 phase wi th a c ub ic cr y stal latt ic e . T he p r onou nc ed peaks on the XRD d iff ra ct i on pa t ter n of the s a mp le sh ow the h ig h c r y stall ine natu r e of the obt a i ne d ma g ne tit e par t icle s. Ana ly sis o f the TE M image (Fig. 4b) of the sample s how ed t hat F e 3 O 4 NP s m ainly ha v e a polyg o na l or irr e g ula r s ha pe, t he s ize of which r a ng e s from 30 –80 nm, each of t he m is c onne cte d t o se v e r a l neighboring par ticle s by ist hmuse s. T h e mea sure me nt r e su lt S of Fe 3 O 4 NP s is i n good agre eme nt with the r e su lt o f microscopic analysis, the S v a l ue is 18. 3 m2/g, w h i ch co rres p o n ds t o t h e av erage s i z e o f Fe 3 O 4 NPs D = 65 n m . Thu s , t he s e l e c t ed time tem p er a t ure regi m e for t h e redu c ti o n of t he h ydroxide compound α- F eO O H m a kes i t po ss ib le t o ob ta i n n ano si z ed c r ys tallin e m agn etit e p o wd e r wi th hi gh p urit y a t an in c r eased r a t e o f th e process.
Conclusion
The kinetics of synthesizing process of Fe 3 O 4 NP by hydrogen reduction from α-FeOOH under isothermal conditions at temperatures from 310 to 375 °С were studied. It was found that the reduction process of α-FeOOH NP begins to accelerate strongly in the temperature range from 340 to 375 °С. The reduction rate constant at 375 °С is about 2 times that of the reduction at 310 °С.
The value of the activation energy of synthesizing process of Fe 3 O 4 NP was ~ 36 kJ/mol, which indicates a mixed mode of limiting the kinetics of the process. In this case, the rate of the general process is limited both by the rate of its own chemical reaction and by the rate of diffusion of reagents and reduction products through the layers of powders, respectively, an expedient way to accelerate the process is to increase the temperature or eliminate diffusion layers in the bulk of the powder sample by intensive mixing.
It has been established that the time-temperature regime of reduction of α-FeOOH with exposure at 340 °С for 3 h makes it possible to obtain a nanosized crystalline magnetite powder with high purity at an increased rate of the process. The obtained Fe 3 O 4 NPs generally have a polygonal or irregular shape, the size of which ranges from 30–80 nm with an average value of 65 nm, and each of them is connected to several neighboring particles by isthmuses.
Список литературы By hydrogen reduction from a-FeOOH hydroxide compound under isothermal conditions
- Bhushan B. (Ed.). Springer Handbook of Nanotechnology. Heidelberg, 2017. 1500 p.
- Ortega G., Reguera E. Biomedical applications of magnetite nanoparticles. Chapter 13. In book: Materials for Biomedical Engineering. Nanomaterials-Based Drug Delivery. Elsevier, 2019, pp. 397–434. DOI: 10.1016/b978-0-12-816913- 3. Rudakovskaya P.G., Beloglazkina E.K., Mazhuga A.G., Klyachko N.L., Kabanov A.V., Zyk N.V. Synthesis of magnetite-gold nanoparticles with core-shell structure. Moscow University Chemistry Bulletin, 2015, vol. 56, no. 3, pp. 181–189. (in Russ.) DOI: 10.3103/S0027131415030104
- Dahman Y. Nanotechnology and Functional Materials for Engineers. Elsevier, Health Sciences Division, 2017. 282 p.
- Morel M., Martínez F., Mosquer E. Synthesis and characterization of magnetite nanoparticles from mineral magnetite. Journal of Magnetism and Magnetic Materials, 2013, vol. 343, pp. 76–81. DOI: 10.1016/j.jmmm.2013.04.075
- Pei W., Kumada H., Natusme T., Saito H., Ishio S. Study on magnetite nanoparticles synthesized by chemical method. Journal of Magnetism and Magnetic Materials, 2007, vol. 310, iss. 2, pp. 2375–2377. DOI: 10.1016/j.jmmm.2006.10.837
- Klekotka U., Satula D., Nordblad P., Kalska-Szostko B. Layered magnetite nanoparticles modification – synthesis, structure, and magnetic characterization. Arabian Journal of Chemistry, 2020, vol. 13, iss. 1, pp. 1323–1334. DOI: 10.1016/j.arabjc.2017.11.002
- Wei Y., Han B., Hu X., Lin Y., Wang X., Deng X. Synthesis of Fe3O4 Nanoparticles and their Magnetic Properties. Procedia Engineering, 2012, vol. 27, pp. 632–637. DOI: 10.1016/j.proeng.2011.12.498
- Wen X., Yang J., He B., Gu Z. Preparation of monodisperse magnetite nanoparticles under mild conditions. Current Applied Physics, 2008, vol. 8, iss. 5, pp. 535–541. DOI: 10.1016/j.cap.2007.09.003
- Martínez-Mera I., Espinosa-Pesqueira M.E., Pérez-Hernández R., Arenas-Alatorre J. Synthesis of magnetite (Fe3O4) nanoparticles without surfactants at room temperature. Materials Letters, 2007, vol. 61, iss. 23–24, pp. 4447–4451. DOI: 10.1016/j.matlet.2007.02.018
- Rashdan S., Selva Roselin L., Selvin R., Lemine O.M., Bououdina M. Nanoparticles for biomedical applications: Current status, trends and future challenges. In book: Biomaterials and Medical Tribology. Elsevier, Woodhead Publishing, 2013, pp. 1–132. DOI: 10.1533/9780857092205.1
- Wallyn J., Anton N., Vandamme T.F. Synthesis, Principles, and Properties of Magnetite Nanoparticles for In Vivo Imaging Applications-A Review. Pharmaceutics, 2019, vol. 11 (11), 601. DOI: 10.3390/pharmaceutics11110601
- Ryzhonkov D.I., Konyukhov Y.V., Nguyen V.M. Kinetic regularities and mechanisms of hydrogen reduction of nanosized oxide materials in thin layers. Nanotechnologies in Russia, 2017, vol. 12, no. 11–12, pp. 620–626. (in Russ.) DOI: 10.1134/s1995078017060076
- Kargin D.B., Mukhambetov D.G., Konyukhov Y.V., Altynov E.A., Aznabakiev K.R. Magnetic properties of iron and iron oxide nanopowders produced from rolling mill scale. XXII International conference about permanent magnets, 2019, p. 107.
- Filatov S.V., Zagainov S.A., Gileva L.Yu., Pykhteeva K.B. Development of the analysis of iron oxide reduction processes. Izvestiya. Ferrous Metallurgy, 2015, vol. 58, no. 9, pp. 658–661. (in Russ.) DOI: 10.17073/0368-0797-2015-9-658-661
- Berdnikov V.I., Gudim Yu.A. Chemical reactions at reduction of iron from oxides by natural gas. Izvestiya. Ferrous Metallurgy, 2020, vol. 63, no. 1, pp. 84–86. (in Russ.) DOI: 10.17073/0368-0797-2020-1-84-86
- Roshchin V.E., Roshchin A.V. General electron theory of reduction and oxidation of metals. Izvestiya. Ferrous Metallurgy, 2020, vol. 63, no. 3–4, pp. 271–285. (in Russ.) DOI: 10.17073/0368-0797-2020-3-4-271-285
- Konyukhov Yu.V. [Development of scientific and technology foundations for synthesizing nanopowders from industrial raw materials and materials modification using energy-mechanical treatment. Dissertation of Dr. Sci. (Tech.)]. Moscow, NUST “MISiS”, 2018. 303 p. (in Russ.)
- Kolpakova N.A., Romanenko S.V., Kolpakov V.A. [Collection of problems in chemical kinetics]. Tomsk, TPU Publ., 2008. 280 p. (in Russ.)
- Schmalzried H. Chemical kinetics of solids. Weinheim, VCH, 1995. 433 p.1.00013-1