Compressibility of the composite material with fiber filler and nanodimensional polyurethane matrix for road and hydro engineering construction
Автор: Victor G. Nazarov, Alexander V. Dedov, Elena S. Bokova
Журнал: Nanotechnologies in Construction: A Scientific Internet-Journal @nanobuild-en
Рубрика: Technologies for production of construction materials and products
Статья в выпуске: 1 Vol.15, 2023 года.
Бесплатный доступ
Introduction. The aim of the research is to study the compressibility of composite materials obtained by varying the degree of impregnation of a non-woven needle-punched cloth with an aqueous dispersion of polyurethane. Materials and research methods. Non-woven needle-punched cloth made of polyethylene terephthalate fibers (TU 6-13-0204077-95-91) with a linear density of 0.33 tex (diameter 20–25 microns) was used as objects of research. For impregnation, an aqueous dispersion of anionic stabilized aliphatic polyethiruretane of the brand IMPRANIL DL 1380 (PRC) with a dry residue of 40% was used. The compressibility of canvases and composite materials was established using the ICH indicator according to GOST 577-68 with an accuracy of measuring the thickness of ± 0.001 mm. Results and discussion. An approach is proposed to establish the relationship between the degree of compressibility of composite materials and the load and to obtain an equation for predicting the degree of compressibility of composite materials from the degree of impregnation and load. Optimal loading conditions of the composite material with a minimum degree of compressibility has been established. Conclusion. The optimal degree of impregnation of a non-woven needlepunched fabric made of polyethylene terephthalate fibers with a diameter of 20–25 microns with polyurethane dispersion is 0.5.
Non-woven needle-punched cloth, polyurethane dispersion, impregnation, composite material, compressibility
Короткий адрес: https://sciup.org/142235806
IDR: 142235806 | DOI: 10.15828/2075-8545-2023-15-1-53-58
Текст научной статьи Compressibility of the composite material with fiber filler and nanodimensional polyurethane matrix for road and hydro engineering construction
Original article
H ighly porous non-woven needle-punched fabrics made of synthetic fibers with a porosity coefficient of more than 0.8 [1–5] are used in road [6–9] and hydraulic engineering [10–13] construction and water drainage systems [14–17]. The general requirement for fabrics is high water permeability, which depends on the change in the porous structure when compressed by a layer of soil or road surface. The consequence of compression is a decrease in porosity and the permeability of the cloths [3–5].
When using composite materials obtained by impregnating fabrics with polymer dispersions [18], the compressibility decreases. The mechanical properties and permeability of composite materials depend on the degree of impregnation and on the distribution of polymer particles
in the cloth. The formation of a nanoscale thickness coating of polymer particles on the fibers surface increases the fibers rigidity, the connection of the fibers by “bridges” of polymer particles limits the movement of the fibers in the direction of the exposure direction [18, 19]. Moreover, with the predominant formation of the nanoscale coating on the fibers surface and connecting bridges, the macroscopic degree of fabric porosity does not change and the relatively high water permeability remains.
The condition for the coating formation on the fibers is their wetting with water and a high affinity between the dispersion polymer and the fiber-forming polymer, which is not achieved when synthetic rubbers are used to impregnate latex fabrics [19]. Water dispersions of polyurethanes have been proposed [20–22], which have a high affinity for polyethylene terephthalate [23–26]. However, the technological problems of obtaining composite mate-
TECHNOLOGY OF PRODUCTION OF BUILDING MATERIALS AND PRODUCTS rials with a given compressibility remain unsolved. Therefore, the aim of the work is to study the dependence of the composite material compressibility on the impregnation degree of fabrics made of polyethylene terephthalate fibers with a polyurethane dispersion.
METHODS AND MATERIALS
The fabrics compressibility degree was determined as the result of five measurements averaging. Under the compression strength of 20 kPa the maximum relative error was ±7%. And the relative measurement error decreased with the compression strength growing.
RESULTS AND DISCUSSION
The objects of the study are the non-woven needle-punched fabrics made of polyethylene terephthalate fibers (TU 6-13-0204077-95-91) with a linear density of 0.33 tex and 20–25 µm diameter. The fibrous cloths were obtained with the mechanical formation technique [12] and were strengthened with needle-punching density of 180 cm–2 [27]. The thickness, the surface and the bulk density of the fabric were 2.5±0.1 mm, 0.25±0.02 kg/m2 and 95±5 kg/m3 respectively. The experimental samples’ mass was determined using electronic scales with a weighing accuracy of ±0.002 g. The samples’ thickness was determined according to GOST 12023-93 using a thickness gauge with a division value of 0.01 mm according to GOST 11358-70.
We used for impregnation a water dispersion of an anionic stabilized aliphatic polyetherurethane (IMPRA-NIL DL 1380 (China)) with a dry residue of 40%. The samples were immersed in a dispersion filled container and rolled for 3–5 min at room temperature. Then the samples were removed from the container, kept on a metal mesh until the dispersion completely drained and rolled between the rollers with a half of the cloth thickness gap. The impregnation degree was varied by diluting dispersion with different dry residue using the distilled water. The heat treatment of the impregnated cloths was carried out at a temperature of 90оC. The composite materials’ impregnation degree (CM, rel. units) was calculated from the expression:
The effect of pressure on the compressibility of composite materials of various degrees of impregnation.
Dependences of ε on P are shown in Fig. 1.
The obtained dependences of ε on P (Fig. 1) are described by equation:
ε = a–bР 2 +cР 3. (3)
A significant number of variables (a, b, kPa–2 and c, kPa–3) reduces the criterion value of Equation 3. We have found that in the coordinate system ε-Р0.5, the dependences of ε on Р are transformed into linear ones (Fig. 2) and are described as:
ε = kP × Р 0.5 ε < 1,
where kP is the dimension coefficient, kPa–1, which corresponds to the compressibility degree of the composite material at 1 kPa pressure. The smaller the kP coefficient, the higher the compressive resistance of the composite material.
The dependence of kP on CM was obtained using two assumptions. Firstly, the greater the impregnation degree, the lower the compressibility degree of the composite
с
M
m 1
- m
m
where m1 and m (kg) are the samples’ mass after and before the impregnation.
The compressibility of the fabrics was determined using a dial indicator according to GOST 577-68 with a thickness measurement accuracy of ±0.001 mm. The composite material compressibility degree (ε) was calculated as:
d - dP
Г =----— d,
where d (m) is the thickness of the composite material; dP (m) is the thickness of the composite material under pressure P (kPa).
It follows from (2) that at the ultimate strain of the cloth and composite material (or when the condition dР→0), ε→1.
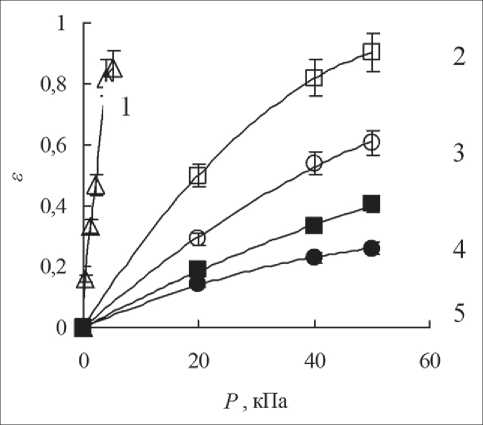
Fig. 1. Dependences of the compressibility degree on pressure for the fabric (1) and the composite material with the degree of impregnation 0,18 (2), 0,27 (3), 0,87 (4) and 1.16 (5)
TECHNOLOGY OF PRODUCTION OF BUILDING MATERIALS AND PRODUCTS
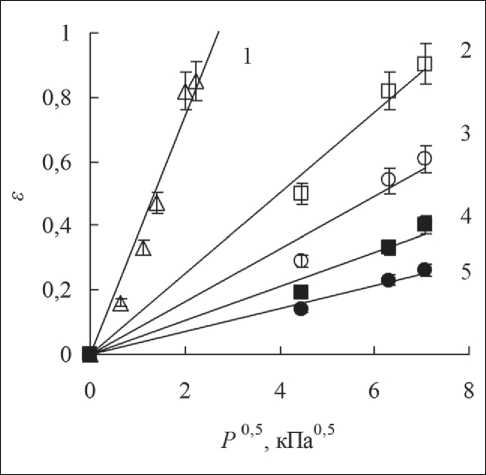
Fig. 2. Dependences of the compressibility degree on the nominal pressure for the fiber (1) and the composite material with the degree of impregnation 0,18 (2), 0,27 (3), 0,87 (4) and 1.16 (5)
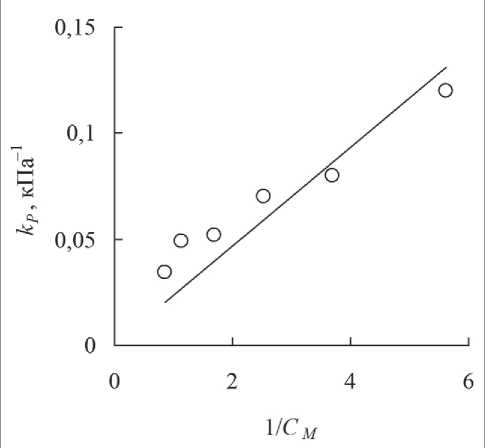
Fig. 3. Dependence of the k P coefficient on the inverse value of the impregnation degree
material, which leads to an i inverse proportionality between kP and CM . Secondly, with the impregnation degree tending to the limit value when all the fiber pores are filled with polymer, the obtained material’s, compressibility degree tends to zero.
The influence of the degree of impregnation on the compressibility of composite materials.
The dependence of kP on 1/ CM is shown in Fig. 3.
The dependence kP on 1/ СМ has a linear form (Fig. 3) and with a correlation coefficient of 0.9 is described by the equation:
kP = 0.023(1/ СМ ). (5)
Replacing the coefficient kP in equation 4 with equation 5, we obtained an equation for predicting the compressibility degree of a composite material with a given impregnation degree and known pressure:
ε = (0.023/ СМ ) P 0.5. (6)
The influence of the degree of impregnation and pressure on the compressibility of composite materials.
The graphical solution of Equation 5 for the given СМ from 0.01 to 1 and P from 1 to 100 kPa is shown in Fig. 4.
A significant decrease in the compressibility degree of the composite material is observed with an increase in the impregnation degree from 0 to 0.5. With the impregnation degree from 0.5 to 1.0, the compressibility degree practically does not depend on the polyurethane content in the composite material. So, for a composite material with the impregnation degree of 0.01, in comparison with a material with the impregnation degree of 0.5 with a pressure of 1 kPa, the compressibility degree decreases from 0.9 to 0.05, and with a pressure of 100 kPa – from 1 to 0.55, respectively (Fig. 4).
Porous structure of composite materials.
Micrographs of a composite material with an impregnation degree of less than 0,5 are shown in Fig. 5.
Visual analysis shows that with the impregnation degree less than 0.5, bridges between the fibers don’t not form. The polyurethane particles form coating on the fibers surface, the thickness and defectiveness of which depend on the impregnation degree. At the impregnation degree of 0.18 the coating has a thickness of approximately 200–500 nm with a high defectiveness (Fig. 5a). With an increase in the coating thickness up to 1000 nm for materials with an impregnation degree of 0.27 the coating defectiveness decreases (Fig. 5b), and for a material with an impregnation degree of 0.48, a monolithic coating is obtained (Fig. 5c). However, compared to the fabric, the composite materials compressibility with an impregnation degree of less than 0.5 decreases slightly.
The decrease in the composite materials compressibility with an impregnation degree of more than 0.5 is a consequence of the formation of bridges between the fibers (Fig. 6, a and b).
TECHNOLOGY OF PRODUCTION OF BUILDING MATERIALS AND PRODUCTS

Fig. 4. Dependences of the compressibility degree of composite materials on the impregnation degree and pressure
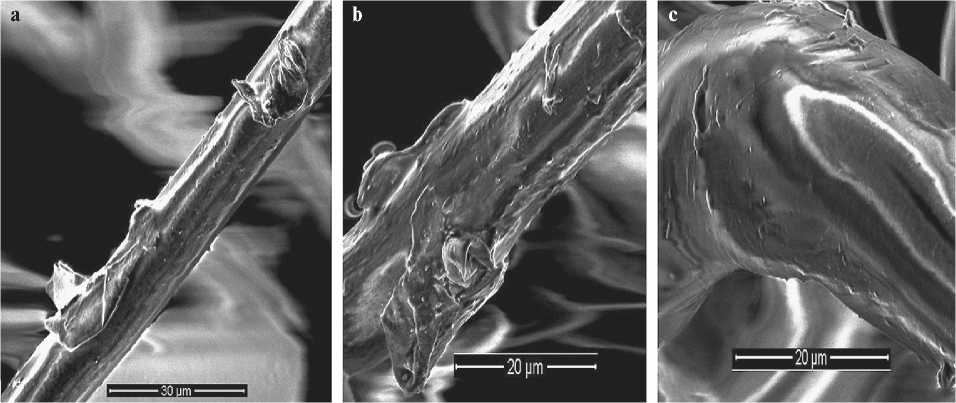
Fig. 5. Micrographs of the fibers surface of composite materials with a impregnation degree of 0,18 (a), 0,27 (b) and 0,48 (c)
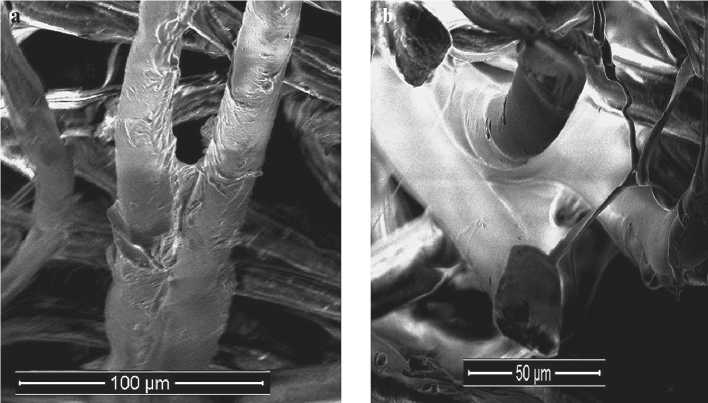
Fig. 6. Micrographs of the fiber surface of composite materials with an impregnation degree of 0,87 (a) and 1,16 (b)
TECHNOLOGY OF PRODUCTION OF BUILDING MATERIALS AND PRODUCTS
At the impregnation degree of 0.87, bridges connect adjacent fibers (Fig. 6a), and at the impregnation degree of 1.16, several fibers are connected (Fig. 6b).
CONCLUSION
– Сomposite materials with compressibility sufficient for practical use in road and hydraulic engineering construction equal to 0.5 are obtained at the impregnation degree with water dispersion of polyurethane of a non-woven needle-punched fabric made
of polyethylene terephthalate fibers with a diameter of 20–25 microns;
Сomposite materials with an impregnation degree of 0.5 are recommended for use in road and hydraulic engineering construction at a pressure of less than 36 kPa, at which the material compressibility degree is not more than 0.2;
Сomposite materials compressibility decreases when connecting fibers with bridges of polymer particles, whereas the polymer coating formation on the fibers surface practically does not affect compressibility.
Список литературы Compressibility of the composite material with fiber filler and nanodimensional polyurethane matrix for road and hydro engineering construction
- Dubrovski P. D., Brezocnik M. The modelling of porous properties regarding PES/CV-blended nonwoven wipes. Fibers and Polymers. 2012; 13 (4): 363–370.
- Thirumurugan V., Kumar M. R. Design of an Instrument to Determine the Acoustic Characteristics of Non Wovens Made from Recycled Polyester, Jute and Flax. Fibers and Polymers. 2020; 21(12): 3009–3015.
- Nazarov V.G., Dedov A.V. Influence of the processing mode of nonwoven needle-punched materials on air filtration. Fibre Chemistry. 2021; 53(2): 143–148.
- Nazarov V.G., Dedov A.V. Influence of the processing of non-woven needle-punched materials on the air flow mode. Fibre Chemistry. 2022; 53(5): 317–320.
- Nazarov V.G., Dedov A.V. Application of the linear filtration law for predicting air permeability of non-woven needle-punched fabrics. Fibre Chemistry. 2022; 53(5): 321–325.
- Nithin S., Rajagopal K., Veeraragavan A. State-of-the Art Summary of Geosynthetic Interlayer Systems for Retarding the Reflective Cracking. Indian Geotechnical J. 2015; 45(4): 472–487.
- Al Qurishee M. Application of geosynthetics in pavement design. Int. Res. J. Eng. Technol. 2017; 4(7):1–7.
- Alimohammadi H., Schaefer V. R., Zheng J., Li H. Performance evaluation of geosynthetic reinforced flexible pavement: a review of full-scale field studies. Inter. J. Pavement Res. Technol. 2021; 14(1): 30–42.
- Anusudha V., Sunitha V., Mathew S. Performance of coir geotextile reinforced subgrade for low volume roads. Inter. J. Pavement Res. Technol. 2021; 14.(2): 213–221.
- Makarov A. G., Pereborova N. V., Vagner V. I., Egorova M. A., Klimova N. S. Spectral Analysis of Viscoelastic Creep of Nonwoven Geotextiles. Fibre Chem. 2018; 50(5): 378–382.
- Tian D., Xie Q., Fu X., Zhang J. Experimental study on the effect of fine contents on internal erosion in natural soil deposits. Bulletin of Engineering Geology and the Environment. 2020; 79(8): 4135–4150.
- Esinovskiy V. A., Medvedkina I. R., Muravyov A. V., Fedotov A. A. Application of Incomat® Concrete-Filled Shells in the Construction and Repair of the Fastening of Slopes of Navigable Rivers and Channels on Inland Waterways. Power Technology and Engineering. 2021; 55. №4. Р.360–366.
- Kumar S., Roy L. B. Rainfall Induced Geotextile Reinforced Model Slope Embankment Subjected to Surcharge Loading: A Review Study. Archives of Computational Methods in Engineering. 2022; 29(4). 3203–3221.
- Tavangarrad A. Н., Mohebbi В., Hassanizadeh S. M., Rosati R., Claussen J., Blümich B. Continuum-Scale Modeling of Liquid Redistribution in a Stack of Thin Hydrophilic Fibrous Layers. Transport in Porous Media. 2018; 122(9): 203–219.
- Vieira da Silva J., Lodi P. C. Evaluation of Superficial and Internal Clogging of Geotextiles. Inter. J. Civil Engineering. 2020; 18(1): 1125–1137.
- Roy R., Chatterjee M., Ishtiaque S. M. Low Velocity Impact Performance and Puncture Resistance of Nonwoven Geotextiles with the Change of Process Parameters. Fibers and Polym. 2020; 21(1):188–195.
- Lysova M. A., Gruzintseva N. A., Gusev B. N. Establishment of Quality Indicators for Nonwoven Geosynthetic Fabrics According to Their Operational Functions. Russian J. General Chem. 2021; 91(7) 1213–1217.
- Nazarov V.G., Dedov A.V. Рermeability of composition fiber materials//Inorganic Materials: Applied Research. 2022. V.13. №1. P. 111–115.
- Dedov A. V., Nazarov V. G. Mechanical Properties of Composite Materials Based on Latex-Impregnated Needle-Punched Nonwoven Fabrics from Fibers of Different Nature. Inorganic Materials: Applied Research January. 2018; 9(1) 47–51.
- Lokhande G. P., Chambhare S. U., Jagtap R. N. Anionic water-based polyurethane dispersions for antimicrobial coating application. Polym. Bulletin. 2017; 74(11): 4781–4798.
- Zhang F., Wei X. Study of ionic/nonionic polyurethane dispersions with high solid content and low viscosity using a complex hydrophilic chain-extending agent. J. Coatings Technol. Research. 2018; 15(1): 141–148.
- Mestry S. U., Khuntia S. P., Mhaske S. T. Correction to: Development of waterborne polyurethane dispersions (WPUDs) from novel cardanol based reactive dispersing agent. Polym. Bulletin. 2021; 78(1): 6835–6840.
- Herbort A. F. Sturm M. T., Schuhen K. A new approach for the agglomeration and subsequent removal of polyethylene, polypropylene, and mixtures of both from freshwater systems – a case study. Environmental Sci. and Pollution Res. 2018; 25(1-3): 15226–15234.
- Nazmul Islam G. M., Ali A., Collie S. Textile sensors for wearable applications: a comprehensive review. Cellulose. 2020; 27(8): 6103–6131.
- Dedov A.V., Babushkin S.V., Platonov A.V., Kondratov A.P., Nazarov V.G. Sorptive properties of nonwoven materials. Fibre Chem. 2001; 33(5): 56–58.
- Dedov A.V., Nazarov V.G. Processed Nonwoven Needlepunched Materials with Increased Strength. Fibre Chem. 2015; 47(2): 121–125.
- Nega B. F., Pierce R. S., Yi X., Liu X. Characterization of Mechanical and Damping Properties of Carbon. Jute Fibre Hybrid SMC Composites. Appl. Composite Materials. 2022; 29(10): 1637–1651.